
10 minute read
A BETTER WAY
fl exo. I need a new die cutter.” How can you possibly be looking a year, year and a half down the road and say, “I need something,” when that’s the kind of lead time you’re getting at the moment? Brewer: I don’t buy it and build the book of business on it. I build the book of business and then buy it to support it. I’m not looking at two years down the road, what do I think I’m going to need. I develop that need and then maybe fi nd a partner—a friend with a boat—and have them take care of it for me until that new machine comes in.
Morelli: Finn, I don’t know if you can speak to this. You’re putting a brand-new, beautiful facility in and, I’m sure, putting new equipment in. What are your thoughts on how you project down the road? MacDonald: My only thought was, 10 or 12 years ago, when we signed a 10-year lease, it wasn’t a 14-year lease. Time just allowed us to get ahead of this tightness that we’re in. Because of that, the one thing that’s kind of interesting is there’s an opportunity for a lot of diff erent folks to be a part of our growth. If you can’t get something new, but you need something, then you might get something used. If you can’t get something used, but you need to retrofi t or refurbish or build up, then you can do it. Th ere’s a lot of options out there. Th ere’s a lot of great options. Th ere’s a lot of ways to get around this. I think if you develop a network of folks who can say, “Listen, let me understand what your end game is, but let me help you move the pieces to get there”—we’ve got partners out there who are that creative. Th ey’re thinking the way I think, and then they come to me, and they bring me that, and it’s very, very refreshing to have those sort of allies. I tell you, if you’re one of the few who do that, then you’re going to be in the mix for a long time. Great opportunity.
Advertisement
Morelli: Does the uncertain time today, over the last couple weeks with everything going on in the world, put any hesitance in your mind right now? Is there any hesitance to the risk level that we might be living in right now? Davis: I think a little bit, for sure, but the encouraging part, we’re blessed to be in this industry, and this industry has been pretty good throughout the pandemic. I do feel that habits have changed. Whether it’s out of fear or convenience, people are ordering stuff online. And it’s kind of “What do you want to do with your Saturday?” and it’s not “Go shop at Target.” Th e two of the three economists that spoke this afternoon, they encouraged us to buy equipment. Th at kind of stuff helps reinforce what we’re doing and gives us some confi dence that the industry is strong and going to continue to be. Even though there is infl ation and some uncertain times ahead, again, we’re blessed to be in this industry. Brewer: Yeah. Hesitancy is not on the table now. Our industry’s doing well. We have our challenges, but we have to just press forward, make the decision, and keep pressing. Th ere’s no bubble out there, in my mind. I’m not worried about that. We’re just on a trajectory. MacDonald: If you think about where they project the ripples, I don’t know if they project that there are going to be fewer problems, and the world is going to slow down, and folks are going to want much, much more of the same and much, much, much less of something unique and diff erent and very focused on their business. And that’s the heart of what we do. Th ere might be some layers above and below that could change, but the heart of what’s going on, I think, still has a bright future. It’s hard to solve labor, but we can throw technology at more quickly, more effi ciently diagnosing a machine problem, get there before it happens so we save the downtime. We can communicate more easily within the plants. We can’t throw people at problems, but we can throw communication and labor and process. I think if we can do that, our little sector of manufacturing can remain bullish.
Morelli: Gentlemen, I just want to thank you personally for helping me out in doing this today and bringing something a little diff erent to this meeting, something that might change the pace a little bit and hopefully brings a bit of value to everybody in this room. Hearing directly from you on things that matter to these people is wha t we were trying to accomplish as a team. So, thank you all very much.
With the steady rise of e-commerce and increasing need for high-graphics printing further fueled by the COVID-19 pandemic, the demand for corrugated production is unprecedented. Yet the market is fragmented, with many corrugated printers and tough competition, making it increasingly important for printers to employ leading-edge technology at every step of the process to achieve optimum results.
With automated plate cleaning, drying, and infrared (IR)/UV curing systems in place, high-graphics corrugated boxmakers can produce works of unmatchable quality at unbeatable speeds in a manner that is safer and more eco-friendly than traditional methods.
The industry’s innovators have historically strived to make the press operator’s job easier and safer. The development of most technologies has been inspired by press operators themselves.
Automated Cleaning Advantages
Plate washing and the removal of print defects can cause significant downtime, and this can happen at all stages of production— at the beginning of the run at setup, within the print run, and at the end of a print run once the printed job is completed.
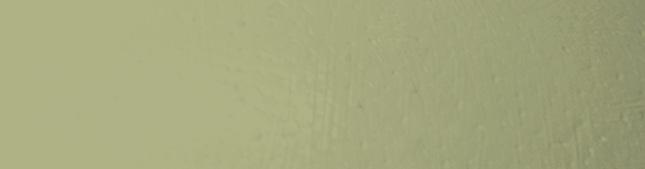

Automated cleaning and IR drying technology push productivity and sustainability boundaries

By Myles Le-Monte Shepherd and Lee Simmonds
Downtime or microstops are not always accounted for by production managers, and huge amounts of time can be lost on each shift for many reasons, such as print defects caused by hickeys, board wraps, premature ink drying, and ink viscosity change, which all lead to the requirement to clean printing plates.
Cleaning also takes place before good boards are printed at the beginning of a print run, especially on multicolor work once the register between the colors is achieved, and at the end of the print run on the fi nal washdown. With automated cleaning technology, the plates can easily be removed from the machine—clean and dry—and be directly stored in a matter of minutes.
Automated cleaning can optimize the productivity, quality, and effi ciency in most print production environments. Technical advancements such as precision spray distribution, automatic plate-thickness adjustment, and high-speed air knife for eliminating moisture on the printing plate mean that hickeys can be cleaned in an instant and that full-plate washing and drying can be achieved in minutes. And printers have the option to clean plates simultaneously or on a selected unit.
Th e cumbersome and costly nature of manual cleaning that was the long- established norm in off set printing led to the development of automatic blanket cleaning. For many years now, almost every off set printing machine has had an automated system to clean printing blankets. It was a game changer in the off set world and has become an essential requirement and standard part of the print process.
With fl exo printing, the same trend toward automation is happening because so much time is being lost through the task of manually cleaning printing plates. Th e requirement for the print quality to be maintained and for the machine to keep producing is essential—more so now than ever due to the demand of printed packaging.
Cleaning has a signifi cant and direct impact on production and waste costs and becomes expensive for companies that are trying to compete without understanding and accounting for how much time they are losing and how much waste they are producing.
Along with the direct labor costs, consequently, time spent manually cleaning restricts output, which ultimately means fewer square meters of board produced from the machine.
Automated systems can eliminate all this wasted time in a very effi cient way and help maintain the print quality. Story after story from printers using the technology demonstrate how attractive the return on investment (ROI) is by reinvesting on other machines once they see the huge savings in time and increased effi ciency with an initial installation. Plate cleaning can also free up muchneeded capacity to produce extra print jobs or additional maintenance time that is sometimes diffi cult to schedule.
IR Drying
IR drying is a critical factor in all high-quality printing processes. Not only does it facilitate a dramatic improvement in image sharpness and quality by reducing absorption into corrugated board, it dramatically enhances color vibrancy and opacity. IR dryers also boost productivity in corrugated printing processes, and the shortwave modular lamphead concept is still the most popular dryer confi guration for corrugated printers today.
Automated drying systems strive to reduce human intervention while maximizing system performance and effi ciency. For example, smart IR sensors measure the temperature diff erential before and after the dryer, automatically adjusting the power level to ensure the minimum amount of energy is used for any given speed, with the maximum drying eff ect achieved.
Prior to this type of system, operators would often have the dryer set for a given job and would not always reduce the power setting for slower run speeds or lower ink-density work. Th is resulted in wasted energy and, in most cases, far too much IR energy to the substrate, which can cause print unit overheating, printing plate drying issues, or, in the worst cases, a safety risk.
Easing Operators’ Burdens
Another consideration to explore in order to fully leverage the advantage of IR drying is whether the segments are modular and can be easily changed without any tools in the event of a lamp failure or other malfunction. Most of today’s solutions require tools and extensive downtime to replace a bulb. Th e most advanced systems ensure that lamp changes have a very minimal impact on the overall effi ciency, which includes ensuring that removing the module from the lamphead is a toolless operation that can be completed in a matter of seconds.
Modular segments have the added advantage of allowing the operator to manually adjust the width of the dryer depending on the board that is being run. In some cases, it is possible to automatically adjust the width of the dryer from the signal from the press, removing another step.
Intelligent control allows operators to go a step further and turn off individual modules where there isn’t any print. All these incremental savings add up to quite signifi cant energy savings and improved overall process effi ciency.
Automation takes away processes from operators where possible to reduce overburdening them. Th ere’s no point in having optimum settings for a given job if the operator is constantly having to manually make adjustments. With an automated drying system, the operator can call up confi gured settings from previous jobs and enable them again to quickly have the best fi nely tuned settings for the conditions.
IoT Advantages
Integrated Internet of Th ings (IoT) is another invaluable feature that facilitates preventive maintenance by issuing prompts and eliminating unplanned downtime. Th is technology allows operators to view a system live to see if there’s anything starting to go wrong with it. It’s like the oil light in a car that comes on quite early, and once the oil is changed, it’s good to go. Without that early indicator, the next sign that the car is in need of oil is when the engine