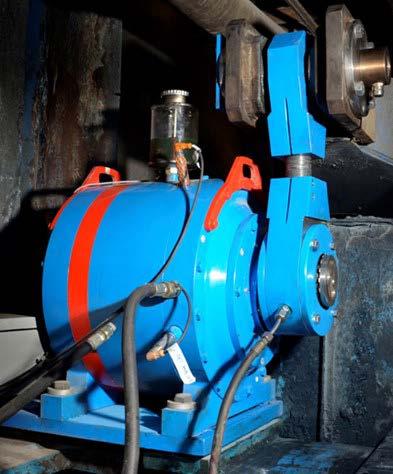
15 minute read
edited by:M. Abram, P. Nolli, M. Meier, P. Rivetti, Q. Chen.................................................................. pag
Technologies in billets and bloom continuous casters supplied by SMS concast in recent projects in China
P. Nolli, M. Abram, M. Meier, P. Rivetti, Q. Chen
The Chinese steel industry has been put under pressure by the Government strategy to decrease energy use, pollutant emission and use of water. This clean-up process has been accompanied by the push for relocation of large steelmaking complexes farther away from urban areas. The relocation of steel plants not only gives the opportunity to build them with more modern technologies for environmental purposes, but it also gives the chance to build plants with capabilities of producing higher quality products. To satisfy this trend toward higher quality, in the casters commissioned recently or under commissioning in China, SMS Concast has supplied various technologies available from its portofolio, such as CONDRIVE technology for mould oscillation, flow control by stopper, mould and final stirrer, advanced L1 automation for control of the machine and of the process, Level 2 quality control system, on-line solidification models and for bloom casters metallurgical soft reduction (MSR). These technologies are outlined in the present paper.
KEYWORDS: CONTINUOUS CASTING, SOFT REDUCTION, MOULD OSCILLATION, SOLIDIFICATION MODEL, ELECTROMAGNETIC STIRRING, SECONDARY COOLING, AUTOMATION, FLOW CONTROL, QUALITY MANAGEMENT, LEVEL 2
INTRODUCTION In recent years SMS Concast has been awarded contracts for the supply of various billet and bloom casters in China. While some of these projects have already been commissioned, others are still under commissioning or through the engineering or erection stage, with commissioning expected by the end of 2020. Several of these continuous caster projects are part of relocations plans, in which large steel-making complexes are moved away from urban areas and from the cities that over time have engulfed the original plants. Alongside this trend, what is clear is the increasing focus of Chinese steel plants toward the production of higher quality products. This puts the top OEM suppliers of continuous casting equipment like SMS Concast, with their wide and complete portfolio of technologies and their know-how, in the lead position for being awarded new projects. Of the many technologies in SMS Concast portfolio, the following will be outlined: CONDRIVE electromechanical oscillation drive, CONFLOW stopper flow control, Metallurgical Soft Reduction, Dynamic Soft Reduction and Dynamic Spray
Paolo Nolli, Marcel Meier, Marco Abram, Pierpaolo Rivetti, Qiwen Chen
SMS Concast AG, Switzerland
Cooling enabled by COOL on-line solidification model, CONSTIR electromagnetic stirring, Level 2 automation and quality management.
MOULD OSCILLATION - CONDRIVE In order to achieve full flexibility of changing stroke and/or frequency parameters on-line and to achieve better oscillation quality, hydraulic has been the drive of choice over the traditional electromechanical drives with eccentric. Hydraulic drives however have some disadvantages, such as higher investment costs, need for hydraulic unit and piping, and more complex maintenance with higher costs. In recent years SMS Concast has develop a new electromechanical drive system, namely CONDRIVE (figure 1), that combines the benefits of hydraulic drives with those of traditional electromechanical ones: it allows changing stroke and frequency on-line and has simple maintenance with low costs. Additional benefits are a compact design, which in combination with a quasi-plug&play approach allows for a quick and smooth installation, and need for only electrical power and water. The CONDRIVE working principle has been described elsewhere (1); here we can briefly say that it is based on a torque motor connected to an eccentric shaft that rotates between angle +α and –α. The angular movement of the shaft is transferred to the oscillation mechanism through a connecting rod.
Fig.1 - One of the installations of CONDRIVE
Through a servo drive and a powerful controller, the oscillation parameters can be changed on-line through the software, by changing the angle α (change of stroke) and the cycle period (change of frequency). In terms of quality for the cast product, beside the on-line change of oscillation parameters, CONDRIVE provides a greater quality of oscillation. Figure 2 shows examples of measurements of oscillation for hydraulic and traditional electromechanical drives compared to CONDRIVE. It is clear how much smoother the oscillation for CONDRIVE is, having almost perfectly sinusoidal curves for displacement, velocity and acceleration as well.
Electromechanical with eccentric Hydraulic CONDRIVE
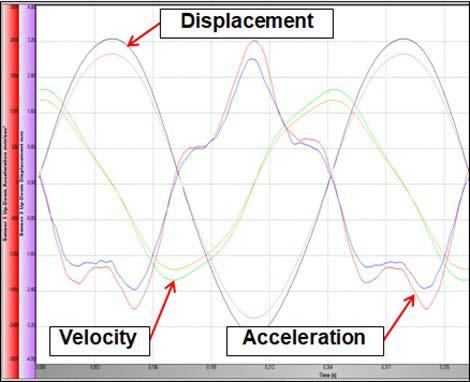
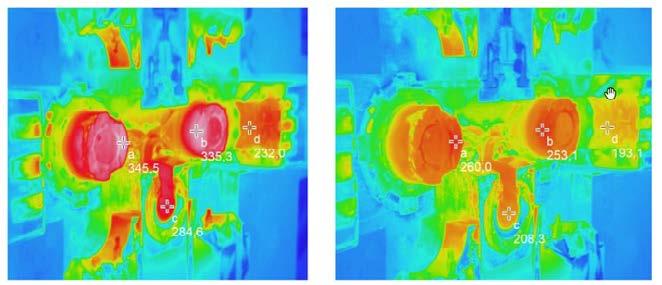
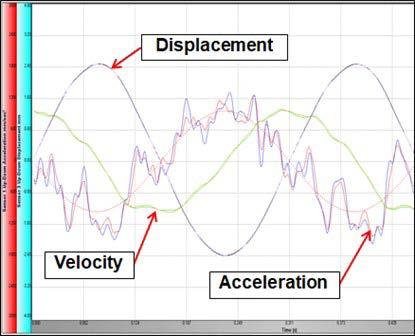
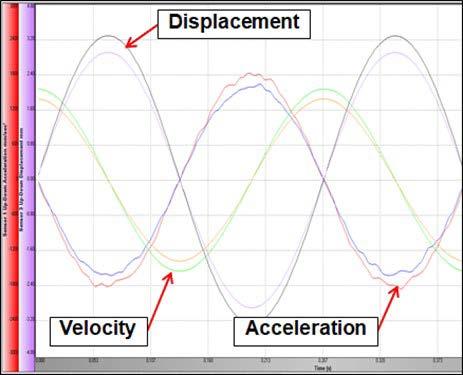
Fig.2 - Example of quality of oscillation for traditional electromechanical and hydraulic drives compared to CONDRIVE.
In China 10 strands (two 5-strand billet casters) in 2019 and 15 strands (one 7-strand billet caster, one 8-strand billet caster and one 5-strand bloom caster) in 2021 were equipped with CONDRIVE and we expect that many more future caster projects will follow suit.
FLOW CONTROL – CONFLOW For billet casters the move to production of higher quality steel grade means that the control of flow of liquid steel from the tundish to the mould cannot be done through metering nozzles, but through other systems, such as stopper or tundish slide gate. For the highest levels of quality, stopper control together with a Submerged Entry Nozzle is the combination of choice. In flow control technology, SMS Concast has a solid track record with more than 2000 strands supplied with the proprietary CONFLOW stopper system. Figure 3 shows pictures of CONFLOW and its main components.
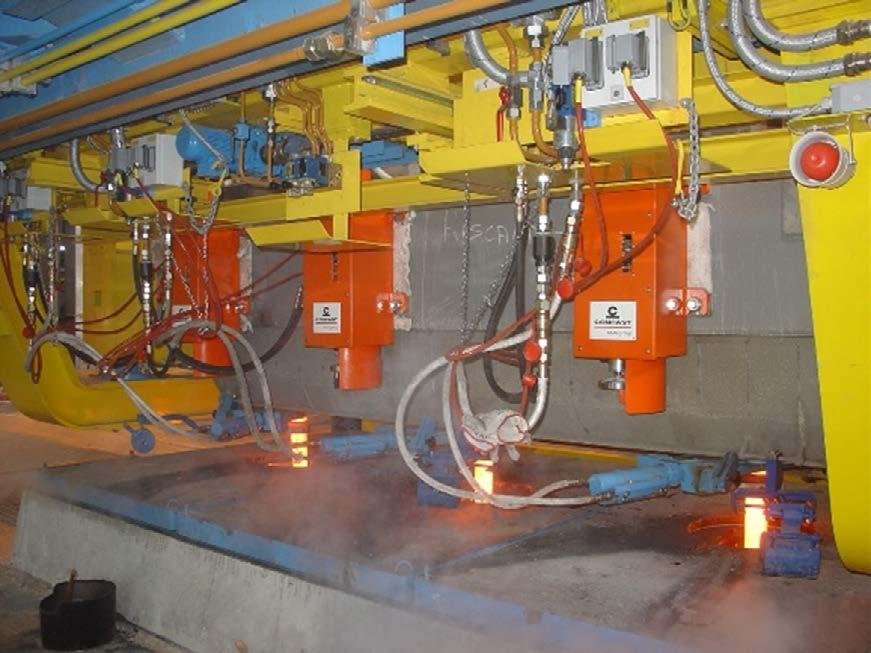
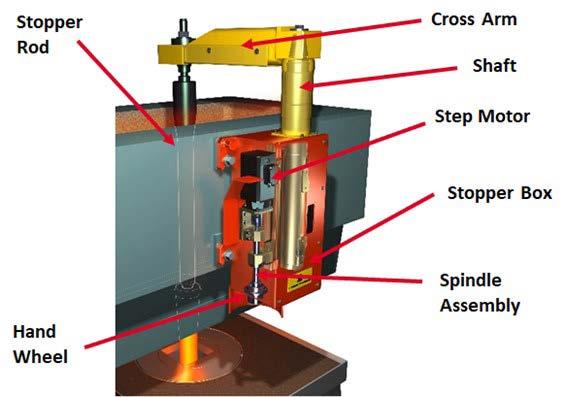
Fig.3 - CONFLOW stopper control system and its main components.
The main features of CONFLOW are: • tight mechanical tolerances that allow excellent control of the stopper lift • electric drive through a step motor • spindle assembly for manual movements • adaptable mounting points for installation on any tundish • full automation integration • full automatic start of casting • clogging monitoring, automatic self-cleaning cycle, stopper dithering (figure 4) • break-out and overflow detection and protection
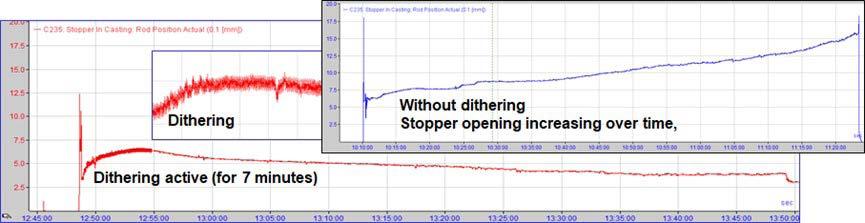
Fig.4 - Example of the implementation of stopper dithering and its effect on stopper behavior.
METALLURGICAL SOFT REDUCTION For the best quality in terms of center porosity, void and segregation, MSR (Metallurgical Soft Reduction) is the most effective technology. MSR consists in the application of a small controlled reduction to the strand in the zone where the cone at the final stage of solidification closes up. The reduction is applied in a progressive series of steps by mean of Pinch Roll modules with small reduction carried out at each roll. The deformation must be sufficient to counteract porosity and segregation, while at the same time avoiding internal cracks. The application of reduction after complete solidification is called Hard Reduction (MHR) and helps reducing center porosity and variability in segregation. Figure 5 shows examples of MSR installations and modules.
Fig.5 - Examples of MSR installations and modules.
Figure 6 shows a schematic of MSR. As the risk of cracks is higher when the bloom is farther from complete solidification, i.e. when the solid fraction at the center is lower (between 0.3 and 0.6), it is essential to estimate the solidification pattern for the given casting process conditions (steel grade, casting speed, superheat, mould and secondary cooling) and to select the corresponding reduction pattern. Reduction applied too early or too strong when the solid fraction is not high enough will cause cracks; too low reduction close and after complete solidification will not give benefits of the compacting and closing of center porosity, void and cracks.
Fig.6 - Schematic of the MSR reduction pattern and corresponding risks.
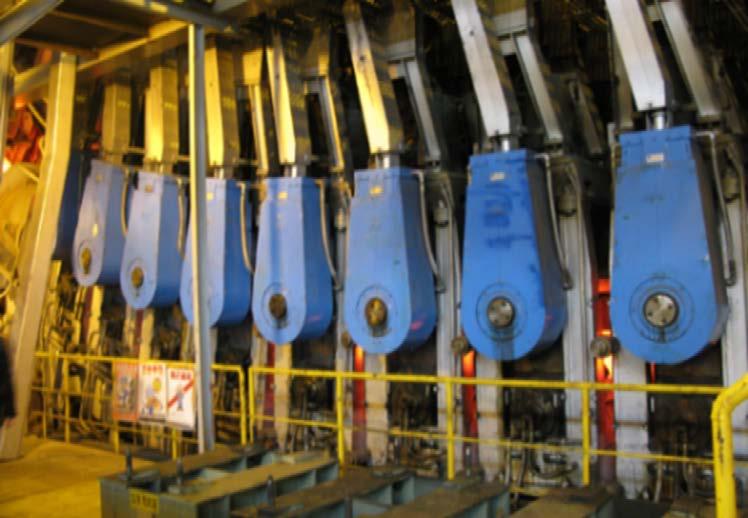
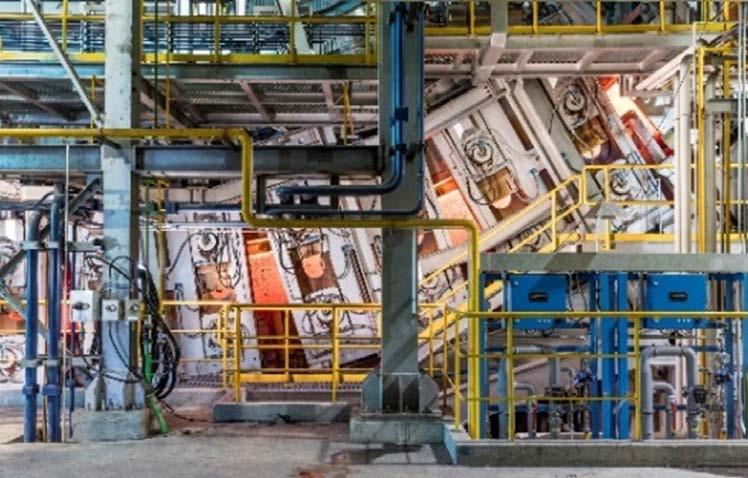
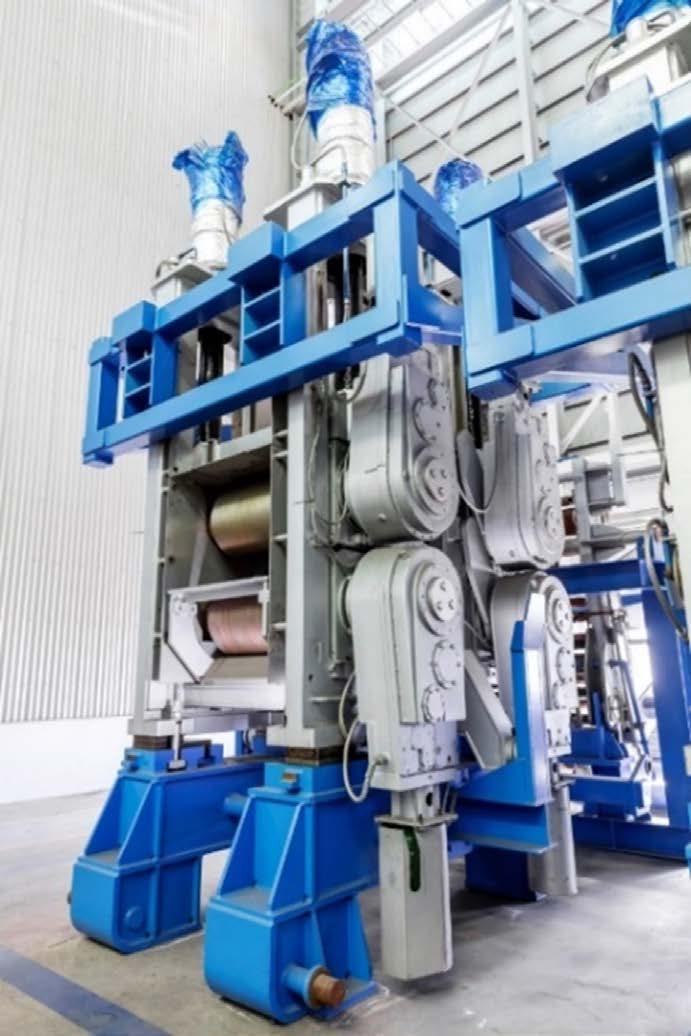
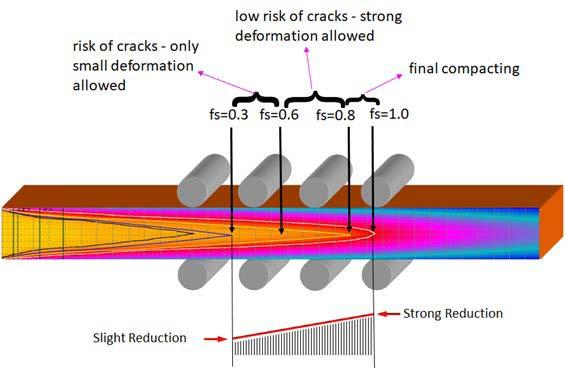
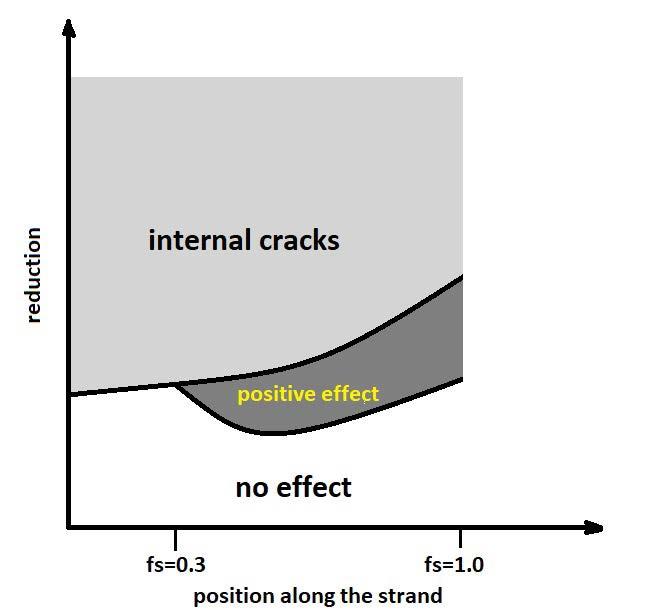
Knowing the evolution of the solid fraction at the center of the bloom/billet is therefore essential to establish the reduction pattern for the exact conditions in which the caster is being operated. In SMS Concast continuous casters this is achieved through an on-line solidification model, which will be described in more details in the next section. The extent of the benefits that can be achieved with MSR in terms of reduction or elimination of center void and porosity and in terms of reduction of Carbon segregation, are significant. Examples (2) of the difference in center soundness and segregation achieved with and without MSR are shown in figure 7 and 8.
Fig.7 - Difference in center soundness achieved with and without MSR.
Fig.8 - Difference in carbon segregation achieved with and without MSR.
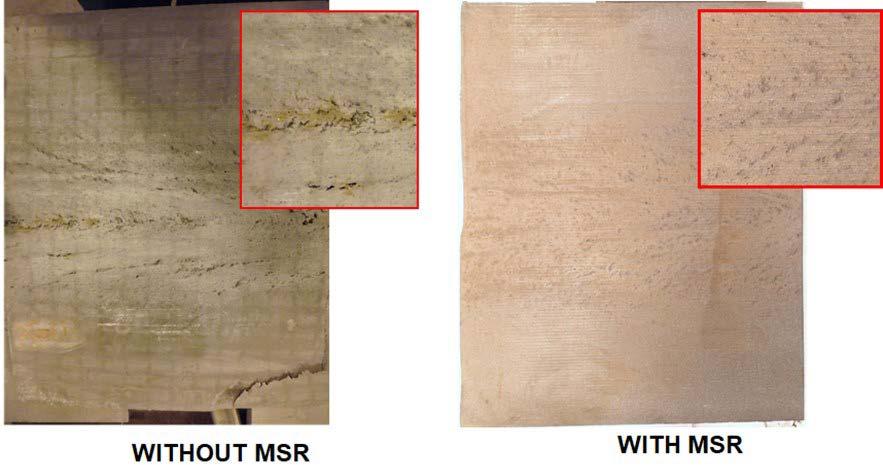

COOL – ON-LINE SOLIDIFICATION MODEL for DYNAMIC CONTROL OF THE PROCESS For an effective application of MSR technology it is vital to know how solidification develops along the strand for the current casting conditions. When used for this application (figure 9), COOL, the solidification model developed by SMS Concast,
• takes inputs from the L1 and L2 systems, such as steel grade, section size, casting speed, superheat, mould cooling water flow rate and ΔT, secondary cooling water flow rates; • takes information from a database describing the configuration of the caster (e.g., mould length, spray nozzles layout, guiding and segment rollers position, MSR modules positions; the same database has information of the steel grades thermo-physical properties and values of other parameters such as ambient temperature); • calculates the solid fraction along the strand. The reduction or force to be applied at each MSR module is then determined from recipes that are relations specific for each steel grade between the solid fraction fs and the reduction/force. The values of reduction/forces are then passed to L1, which controls all the necessary actuators to achieve those values of reduction or force. The use of COOL therefore allows implementing so-called Dynamic MSR, which is the adjustment of the MSR conditions to the current casting conditions on-line.
Fig.9 - Application of the on-line solidification model COOL to Dynamic Soft Reduction.
A similar type of dynamic control of process parameters is Dynamic Spray Cooling (DSC), in which secondary cooling flow rates are adjusted based on the actual casting conditions and on the actual thermal history of the billet/ bloom still within the cooling chamber, in order to achieve preset targets of temperatures at specific points along the strand (figure 10). The secondary cooling adjustment through Dynamic Spray Cooling achieves proper distributions of flows among the zones, avoiding re-heating in between them and thus limiting the occurrence of intermediate cracks. Ultimately each secondary cooling zone is operated not simply based on the casting speed, as it is common practice, but on the history of the section of billet/bloom passing through each zone at a given moment (more important for blooms than for billets given the lower casting speed).
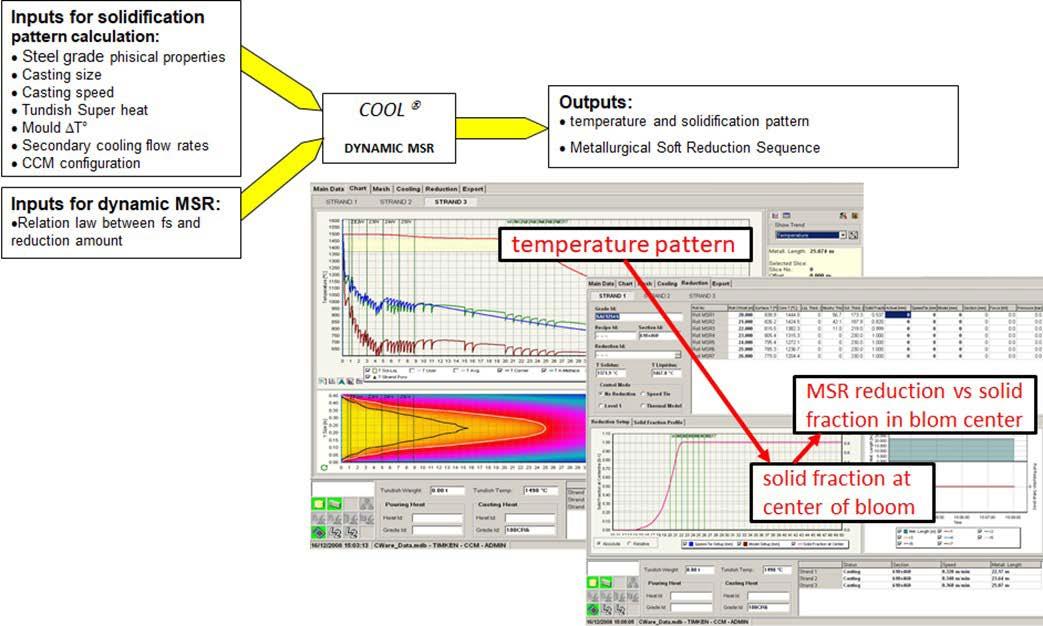
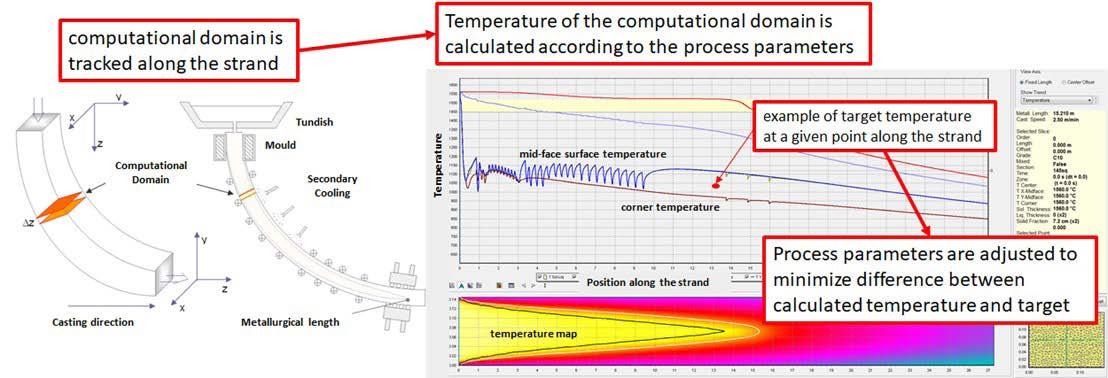
Fig.10 - Schematic of Dynamic Spray Cooling.
CONSTIR - ELECTROMAGNETIC STIRRING Both Mould and Final EMS are standard features in all SMS Concast recent projects in China, both in blooms casters and billet casters for higher quality steel grades. The benefits of electromagnetic stirring are well known: reduction of center segregation and porosity, increase of equiaxed zone, reduction of internal cracks, and reduction of subsurface inclusions. SMS Concast advantage in EMS lay in the extensive know-how based on more than 1000 units installed, in the capabilities of full customization, and in the optimization of settings based on simulations. Further advantages are the following. • Simulation tools for optimization of the position of the Final EMS – COOL solidification model described above is used to calculate the solidification pattern. The position of the final stirrer is then determined by considering the proper solid fraction at which to apply stirring and so that a wide enough portion of the bloom is still partially liquid that its structure can be affected by the EMS (figure 11). • Modulated Wave Stirring (MWS) – This technology (figure 12) is based on the modulation of both frequency and current, which has the effect of generating more vortexes, which in turns creates a more uniform temperature and chemical distribution and a more efficient breaking of the growing dendrites (3). Other benefits are 30% power savings and a correspondingly longer EMS lifetime, and longer SEN life because of the lower wear due to the lower angular velocity. Modulated Wave Stirring has been supplied and will be supplied in all SMS Concast bloom caster projects in China.
Fig.11 - Determination of the FEMS position from a solidification profile calculated with COOL.



CONVENTIONAL STIRRING MODULATED WAVE STIRRING
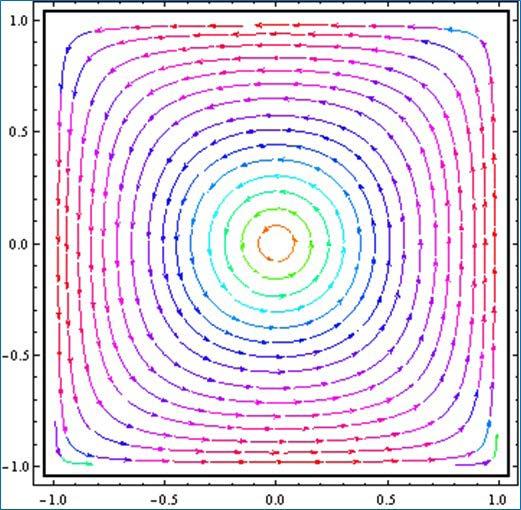
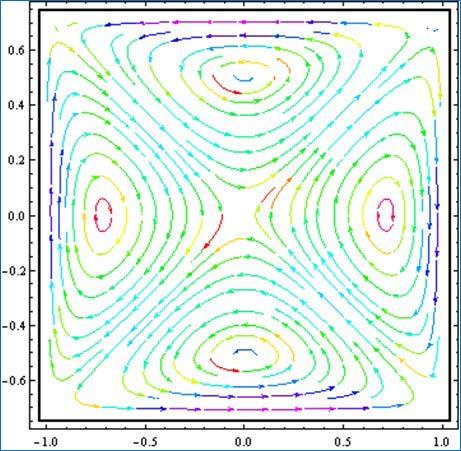
Fig.12 - Modulated Wave Stirring: left) example of modulation for current; center and right) comparison of stream lines in conventional and MWS stirring.
ELECTRICS AND AUTOMATION – LEVEL 2 SOLUTIONS One of the strength of SMS Concast is the capability to offer packages of Level 1 and Level 2 systems for the control of the operations of the caster and for full integration with the Level 3/4 systems of the steel plants. At the base of all is the established know-how for engineering and manufacturing of electrical boards and the cooperation with the major international suppliers of drives, PLCs and automation equipment (Level 0). In terms of Level 1, SMS Concast know-how offering ranges from design of the automation system architecture, from sensors and remote I/O modules, to PLCs, network design, programming of the automation software and HMI design. Beside L1, in all recent projects in China SMS Concast is also supplying the Level 2 system (figure 13).
Fig.13 - Level 2 by SMS Concast.
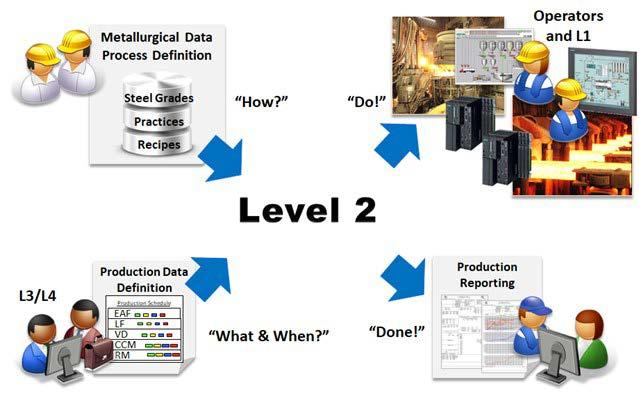
The logic on which SMS Concast Level 2 system has been designed, is to provide the caster pulpit operators with tools that allow them to drive the production according to standard operating practices that are steel grade-dependent and pre-defined by the process engineer. The ultimate goal is the complete standardization of the production practices. Other features, such as metallurgical models (e.g. COOL solidification model described above) and reporting, allow dynamical adjustment of process parameters to match changes in casting conditions and review and analysis of production or process data. The L2 systems in the recent Chinese projects include the following features: • equipment life tracking • production scheduling and management • billet/bloom tracking • quality management, with metallurgical data management (steel grades, process parameters), process control and quality control with real-time evaluation of quality events and tracking of the material affected by such events Of particular relevance in the projects in China are the quality management features. Figure 14 shows a schematic of how this is implemented: • a quality event is detected at a certain point along the strand; this is a deviation of the process conditions from the optimal ones based on predefined quality rules • the position of the material affected by the quality event is tracked along the process; at cutting the billet/bloom containing this portion of material is identified and tracked further in discharge and storage • quality reports show the affected billet/bloom, the position of the possible quality defect within the billet/ bloom and the type of quality event with the corresponding actions to be taken.
Fig.14 - Quality management by SMS Concast Level 2.
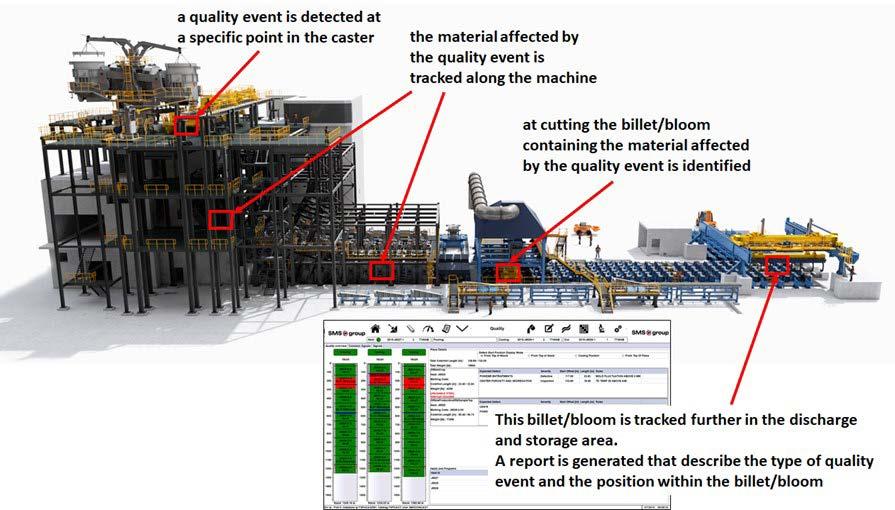
CONCLUSIONS The pressure by the Chinese government on the steel industry to reduce its impact on the environment and on the population has led to several relocation projects in which steelmaking complexes are moved farther away from urban areas. The trend for environmental improvements has met with the other trend seen in Chinese steel industry, which is the drive toward an increased percentage of production volume devoted to higher quality steel grades. In the relocation process, Chinese steelmakers are taking the opportunity to build the new continuous casters with more sophisticated technologies that enable them to produce such higher quality products. SMS Concast, with its know-how, expertise, established references and portfolio of technologies, is therefore particularly suited to be elected as continuous casting equipment supplier in those new projects having higher quality as one of the goals. Of all the technologies that SMS Concast can offer, only a few have been described here: CONDRIVE mould oscillation drive, CONFLOW stopper control, CONSTIR electromagnetic stirring and Modulated Wave Stirring, Metallurgical Soft Reduction, COOL solidification model for dynamic adjustment of soft reduction and spray cooling, Level 2 with quality management. These technologies have improved billet/bloom quality as one of their main objectives and have therefore become standard features in the casters that SMS Concast has commissioned or is commissioning in China. As Chinese market remains the most active steel market and as this trend to higher quality products will continue to get stronger and stronger, we expect that these technologies will be employed in many more projects in the country, making SMS Concast a key supplier of continuous casting equipment in China.
REFERENCES
[1] Kabosch D, Saegesser M, Chittaro E, Feldhaus S, Meier M. New electrical oscillation drive with adjustable stroke and frequency during operation. European Continuous Casting Conference 2017. 2017 June 26-29; Vienna, Austria. Vienna: Asmet; 2017. p. 96-102 [2] Zani F, Grundy A N, Feldhaus S, Sanders J, Valentine N, Eastman C. Vertical Continuous Casting Machine for large blooms. European Steel Technology and Applications Days 2015. 2015 June 15-19; Düsseldorf, Germany. Düsseldorf: Wirtschaftsvereinigung Stahl; 2015 [3] Feldmann M, Neri L, Lesin S, Kapusta A, Khavkin M, Tilman B. Current and Frequency Modulation - A New Way to Improve Electromagnetic Stirring. European Steel Technology and Applications Days 2015. 2015 June 15-19; Düsseldorf, Germany. Düsseldorf: Wirtschaftsvereinigung Stahl; 2015