
18 minute read
edited by: S. Six, L. Fischer, T. Gusarova, S. Schulze, R. J. van den Bogert, A. A. Kamperman............. pag
Advanced cast product quality testing
S. Six, L. Fischer, T. Gusarova, S. Schulze, R. J. van den Bogert, A. A. Kamperman
Nowadays, most steel casting plants worldwide are familiar with the HD scan testing system from SMS group. It is based on a well-established ultrasonic measuring technique that is specially designed for defect distribution images in a coarse cast structure. The first industrial reference installation of the HD scan system was performed by Tata Steel in the Netherlands in December 2018. Since then, Tata Steel and SMS have been working in close collaboration on the progress of the HD scan system and its benefits in terms of casting process optimization. New evaluation results will be presented and compared with the results of sulphur prints and APS etching. As we all move towards Industry 4.0 solutions, digital data evaluation is set to overcome the disadvantages of subjective operator assessments. As a result, new concepts for evaluating typical casting defects, such as segregations and cracks, are being devised. These concepts are independent of defect distribution imaging (HD scan or macro-etching / sulphur printing), have greater informative value with regard to the cast product quality and ensure objective comparison of evaluation results of different steel plants or producers. The huge interest shown by SMS customers led to various models of HD scan being established for different customer demands – from industrial machines with high throughput down to small-scale lab equipment for research activities, e.g. for implementing new casting technologies and steel grades.
KEYWORDS: HD SCAN, ULTRASONIC, CAST PRODUCT, QUALITY, SEGREGATIONS, CRACKS, INCLUSIONS
INTRODUCTION In the modern world of advanced technologies and digital solutions, which are becoming a reality of everyday life, we have to accept technological advances and adapt quickly in order to keep moving forward into the future. Some of the well-known, old-school processes need to be replaced with new modern ones, not necessarily because they are worse, but because they sometimes cannot go hand in hand with industrial progress. One such old-school technique is macro-etching. It is traditionally used in cast steel plants to verify the internal quality of the finished product. For this purpose, a piece of slab, bloom, billet, or other cast product is cut out of the product or strand during casting. The piece is reduced in size and surface-treated to eliminate the effects of cutting (torch burning or other methods), and to ensure an appropriate steel surface smoothness for further processing stages. Finally, the surface is chemically treated with an acid solution in accordance with in-house requirements. After etching, the distribution of internal defects becomes visible on the sample surface. Normally, a photo of the S. Six, T. Gusarova, S. Schulze
SMS group GmbH, Germany
Tata Steel Netherlands
steel sample is taken in order to digitalize and store the results (as sample storing is too laborious). The distribution of defects is evaluated by an expert, who manually assesses and records the segregation class, crack statistics, and geometrical parameters (the latter is used for corner transverse samples). The whole procedure is understandably long from a human factor perspective, including the subjective evaluation and high probability of human error when recording the results. To overcome this, a number of sophisticated software programs were developed. With software, the evaluation of quality parameters becomes objective, and results can be recorded quickly and reliably. However, there is still a need for the etching procedure itself, which means that the steel plant must provide the appropriate space, equipment, and budget (acid purchasing, waste disposal, etc.). Moreover, dealing with hazardous substances is always associated with concerns about the danger to employees and property, as well as with measures that need to be taken in this regard. As an alternative to all of the disadvantages of the aforementioned etching method, SMS group developed a new and safe technology (1-3). The product is called HD scan and consists of ultrasonic scanning equipment, specially designed for cast product tasks, with sophisticated software for evaluating the results; incidentally, it can also objectively evaluate macro-etch images. The sample preparation for the ultrasonic method is the same as for macro-etching, not counting the time-consuming surface treatment that is not required for ultrasonic flaw detection. The samples are placed in a water bath and scanned automatically. At the same time, the sensors move in water above the steel sample without coming into contact with it, so there is no wear. On completion of the analysis, the sample can be easily replaced. As only normal tap water without any chemical additions is used, the method is non-hazardous and does not involve any additional purchasing/waste disposal expenditure. This method also gained the attention of other producers. The results, which were presented at ESTAD 2019, proved the system’s far better sensitivity to non-metallic inclusions in very similar ultrasonic investigations compared to the results of macro-etching (4). TKS also presented the results from their ultrasonic equipment, scanning an entire slab from above with no need for sampling, though with detection limits of only 5-10 mm (5). Some lines, not the whole slab, are scanned to give a 2D assessment of the cast slab quality. The method was initially introduced for quick tests on cracks in the cast product. TKS now also evaluates the severity of segregations in the centre of the slab. Nevertheless, reliable results cannot be ensured by scanning a cast product from above, as a dense segregation zone may hide the defects underneath, in the second half of the cast product thickness. It was only possible, therefore, to make an approximate internal quality evaluation. Over the last six years of HD scan development, different steel grades (carbon and low carbon steel, stainless steel, Si steel and others), some samples of cast aluminium and copper material, and also many different samples from the latest research work for various steel making processes, have been investigated on our pilot system at SMS group in Düsseldorf. In some cases, HD scan was requested to help with particular problems or to solve special tasks being undertaken by SMS customers for their process routes. In most cases, the information concerning the material, process parameters, and other data was not disclosed by the customer. HD scan was therefore working ‘blind’, with no precognitive input. Consequently, in spite of the extensive knowledge gained of different materials and process routes, the related know-how could not be fully expanded. Hence, SMS started looking for a customer who was willing to cooperate on the further development of HD scan. In December 2018, the first industrial HD scan instrument was installed by Tata Steel in Ijmuiden, the Netherlands. Since then, it has been used for the quality control of samples from CC21 and CC22, which were cross-checked by sulphur print and APS etch. Following the commissioning of CC23, the company plans to use HD scan to perform internal quality examinations of the entire production output from the new casting machine. In 2021 two other SMS customers have ordered the HD scan machines in different sizes according to the desired sample throughput. After METEC 2019, many requests for a smaller, laboratory version of HD scan were received from customers who wanted to test the method first and/or utilize its benefits
for research purposes. As a result, a new mobile version of the instrument, called HD scan LAB, was designed and built for transport and installation in a container. It is now placed at SMS Hilchenbach for customer measurements and is available for leasing as it can be easily transported to any plant. For some of our customers, the primary inhibiting factor for introducing HD scan into their plant routines is the fact that the new technique lacks a normative basis. In this context, it should be noted that the normative basis for macro-etching is also still very limited. The best-known “standard” method, referred to as the Mannesmann scale, was used by most steel producers in their own way: there was no normed etching procedure. In Germany, for example, the first standard came out in 2018 (6), after almost 40 years of steel plants continually using the macro-etching technique. SMS group is working on introducing ultrasonic testing as a standard method of internal quality control for cast products. However, it is clear that it will take some years before there is a normative basis for the new method. Tata Steel supports SMS’s intention to develop the ultrasonic technique for the internal quality analysis of cast products. The next section describes the internal quality parameters to be elaborated for HD scan evaluation and taken into account in the collaborative efforts of Tata Steel and SMS.
INTERNAL QUALITY PARAMETERS – HD SCAN EVALUATION Segregations The evaluation of segregations as a two-dimensional distribution was implemented on the basis of the testing and documentation guideline SEP 1611, which is recognized by leading steel producers in Germany and in some neighbouring countries (6). The main difference, however, is that the segregation classes are not restricted to integers. Decimal classification is also realized, as it is well known that integer classification is often not sufficient for an appropriate internal quality comparison of two samples/casting lines/production parameters, etc. Additionally, a three dimensional approach should be tested in order to exploit the full potential of ultrasonic testing. HD scan provides not only the 2D information (from one layer, as with macro-etching) but also 3D data (multiple layers in a sample volume). The extent and variety of benefits won from this extended evaluation is to be clarified in the collaboration work between Tata Steel and SMS. At the moment, a fully automatic evaluation of the segregation class is performed in HD scan evaluation software in three different ways: similar to Mannesmann charts, according to SEP1611 rules in integers and according to SEP1611 rules but with decimal notes. Another customer-specific evaluation may be carried out in parallel based on individual specifications, for example the sum of segregation areas normalized to a sample width, or a comparison with internal scales. SMS has also started implementation of further international standards, e.g., Russian GOST R 58228-2018 and American ASTM E381-20.
Cracks Despite the existing crack evaluation provided by HD scan software, a more sophisticated approach is being tested in collaboration with Tata Steel. The 3D information is included for better automatic detection of cracks. The evaluated statistical parameters are approximately the same: crack length, distance to the product surface, distance between the cracks, etc. Distinctions are made between several types of cracks: transversal, longitudinal, narrow face, corner, centreline, triple point cracks etc according to different reasons of cracks formation in cast product. In addition, the system for evaluating the crack quality class is developed, ensuring that clear decisions about the product quality and its further processing can be quickly made.
Inclusions/pores The system for detecting macro inclusions and pores with HD scan is very sensitive as there are clear material borders for ultrasonic reflection. However, so far it has not been possible to distinguish between these two defect types. Additional investigations are being carried out at SMS group. At the same time, the effect of ultrasonic impedance changes by transition steel/inclusions and steel/ gas (pores) on various ultrasonic response parameters is being studied. The automatic evaluation of inclusions and pores should therefore be enabled separately. Until then,
the combined automatic evaluation of inclusions and pores will be performed. The differentiation of the chemical composition is not possible with ultrasound. The aim of the current investigation is to enable a distinction between filled and unfilled defects, such as pores and inclusions, filled and unfilled cracks, etc. Various statistics are evaluated automatically, giving a quick and clear overview over the defected sample area. Therefore, conclusions about defect formation reasons and responsible segments in the casting machine can be done faster.
Ratio of equiaxed zone (REZ) and other structure-related results In the early days of HD scan development, it was shown that ultrasound can map the macrostructure of samples in many different ways. One of the views allows an evaluation of the ratio of equiaxed zone (REZ), the effect of magnetic stirring, etc. Another view gives an idea of the symmetrical process workflow, cooling effects, etc. The potential offered by this high volume of information has still not fully exploited, in the first instance due to the refusal of customers to give detailed information on the samples (steel compositions, process parameters, casting machine, etc.). For more accurate results, detailed investigations of this should be performed which, although not a top priority, are also planned for the collaboration work with Tata Steel. Geometrical parameters The definition of the geometrical parameters of the sample are not part of the planned cooperation, as this has already been completed and includes the calculation of the width and height of the sample (i.e. cast product thickness), as well as the diagonal ratio (especially important for billet and bloom samples), bulging, depression etc. (of special interest for transversal corner slab samples as an evaluation of the slab geometry parameters). Any geometrical evaluation additionally requested by a customer can be added to the existing software.
DISCUSSION OF RESULTS Originally, new commissioning results from Tata Steel new casting machine were planned for this paper. However, the first commissioning results are not available yet and can be presented first at the conference in autumn 2021. Consequently, the results presented at the ESTAD/METEC 2019, though not published so far, will be discussed here. These results were obtained by comparing the APS etching method with the HD scan technique for three common carbon steel samples. These samples were tested by APS etching, whereby no defects were detected (example of a corner sample in Fig. 1 left). Afterwards, the samples were analysed in HD scan. Crack-like defects were found all over the slab surface (Fig. 1 right).
Fig.1 - Example of a corner carbon steel sample, investigated with APS etching (left), and HD scan (right).
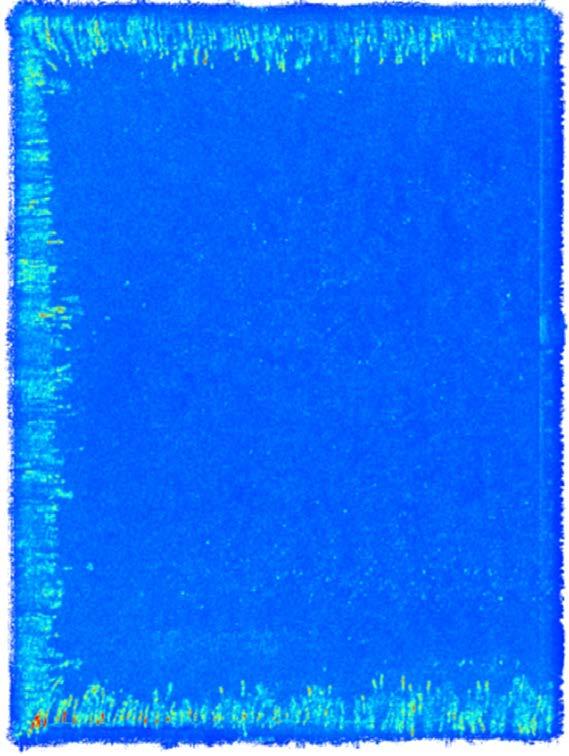
In order to verify the HD scan results, small pieces were cut out of the samples (Fig. 2a), milled down to the sample depth of the HD scan analysis, and polished for microscopic examination. Already after cutting, the crack-like holes were visible on the sample surface, which became partly smudged by further polishing (Fig. 2b). Microscopic investigations showed no sharp defect edges that are characteristic of cracks. The smooth pattern inside the defect indicates defect formation prior to solidification – most probably from carbon monoxide, as the customer confirmed the increased concentration of oxygen in the steel due to the lack of aluminium addition.
a b c

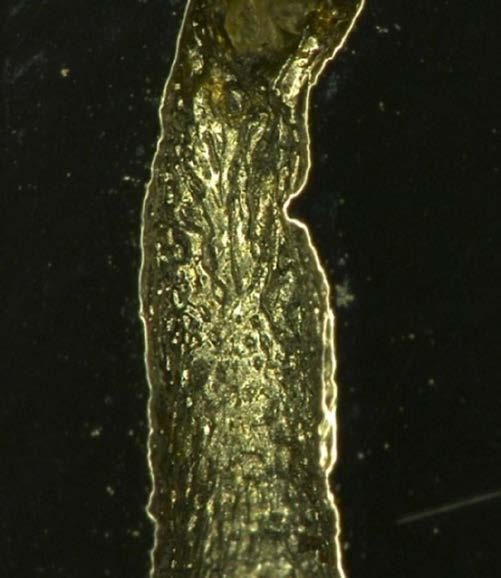
Fig.2 - Microscopic investigations: a – position of the sample; b – photo of the sample after polishing; c – microscopic images of a characteristic defect.
In conclusion, the results provided by HD scan were proven to show the real sample and thus the cast prod-uct quality, in contrast to traditional macro-etching techniques. HD scan showed similar results on examples for other international customers, rising the interest of new this technology. As every customer has its own demand on sample throughput in the plant, SMS provide three instrument sizes with various configurations from very simple to extensive. But if less than 10 samples per day need to be tested – HD scan LAB would be the best choice.
HD SCAN LAB Last year, a small laboratory version of the instrument was developed and built at the learning workshop of SMS group in Hilchenbach, Germany. This instrument can analyse only a sample of a maximum area of 300 x 300 mm2 . This version has been slimmed down to a minimum and therefore costs less: short scanning distances, no water preparation system – just a water-filled plastic tray, in which the sample is placed (Fig. 3 left). The HD scan LAB does not take up much space and can be installed as a mobile instrument in a laboratory or even in a container. The first HD scan LAB was built to assist with the commissioning of the new casting line at ArcelorMittal in Aviles. It was placed in a container so that it can be transported more easily and can also function as a mobile laboratory (Fig. 3 right). In this way, no special space in the customer’s laboratory was required – the container was set up in the factory premises. Only electrical and water connections were needed to operate it. The container with HD scan LAB can be transported subsequently to the next commissioning location of SMS group, providing quick information about the casting quality and shortening the startup process for new casters.
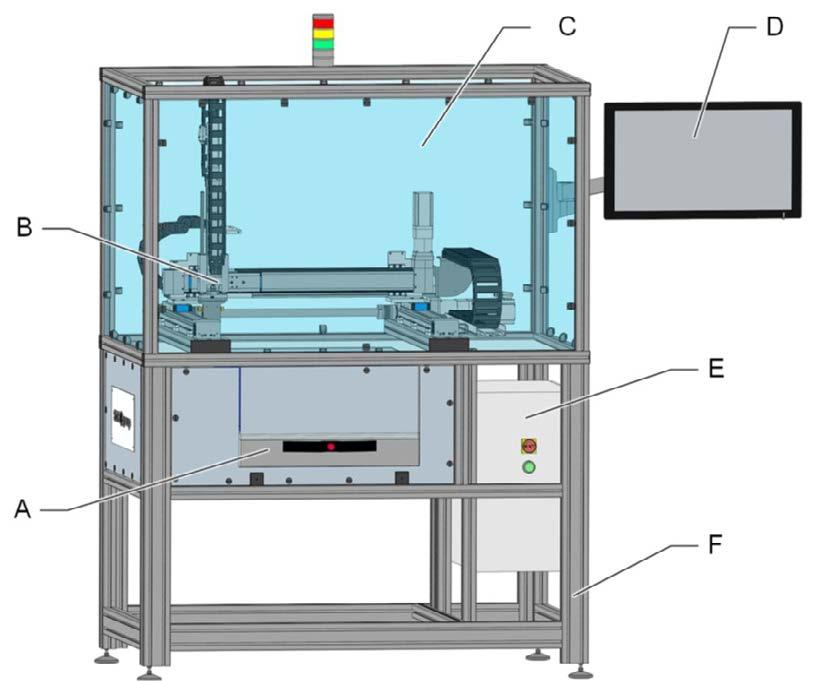
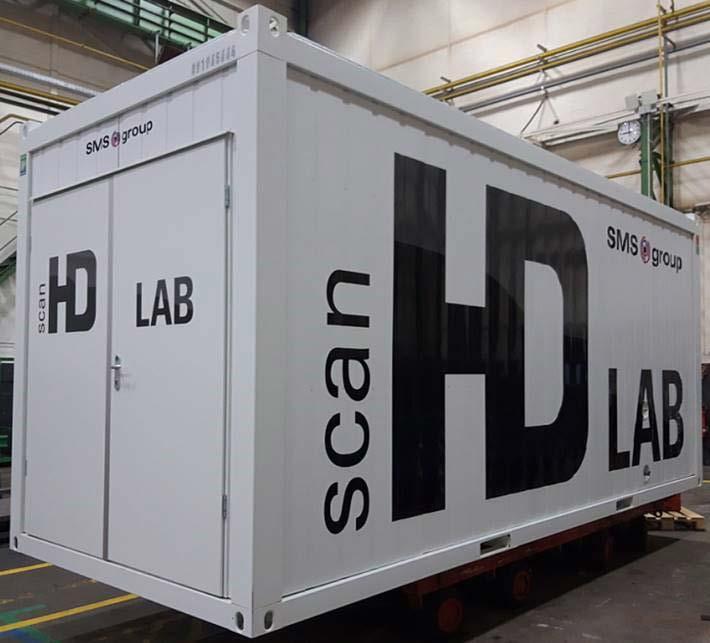
Fig.3 - Layout of an HD scan LAB instrument (left) and photo of a container with HD scan LAB (right). Description of the layout: A – extendible drawer with plastic tray; B – scanning axes with ultrasonic sensors; C – safety covering, D – monitor; E – control cabinet, F – construction frame.
The HD scan LAB instrument is designed for easy handling and operation by all commissioning personnel, with no special skills required. A sample is placed straight into the water-filled plastic tray in the extendible drawer, which acts as an ultrasonic bath. The system is ready to scan when the drawer is closed. The sample name and number are entered in the software. The scanning process is initiated by pressing the start button. Scanning is performed fully automatically. The results are stored on the hard drive, where they can be used for evaluation via a remote access connection. The analysis of the results should be performed either automatically using the HD scan evaluation software or by an expert, who has access to the data and the software. After scanning, the sample can be easily replaced with a new one. The system is specially designed to be as user-friendly as possible for busy commissioning staff.
CONCLUSIONS The new ultrasonic technique for examining the internal quality of cast products – HD scan – is slowly but surely winning over conservative minds in the steel community. It will be some time before this system finds its way into everyday practice. However, the first important steps have been taken: the first industrial HD scan instrument has been in operation at Tata Steel for over two years, another two instruments will be installed at customers in 2022. A laboratory version HD scan LAB has been built for smaller customer needs and can be used as mobile version in a container for commissioning the new casting machines; and discussions on the distribution of further instruments are underway. Tata Steel and SMS are collaborating with a view to expanding the evaluation capability using HD scan software. The results from everyday practice show how well suited the ultrasonic technique is for the internal quality characterization of cast products.
REFERENCES
[1] Gusarova T, Schulze S, Moors M, Klein M, Six S, Kamperman AA, van den Bogert RJ, van der Wal s. HD scan – the digital link between cast quality and process data, METEC & 4thESTAD Conference Proceedings. 2019 [2] Klein M, Gusarova T, Schulze S. Ultrasound scans slab quality. 9th ECCC Conerence Proceedings. 2017 [3] Gusarova T, Schulze S, Runge A, Reifferscheid M. Ultrasonic testing for the internal quality evaluation of cast steel products. METEC & 2ndESTAD Conference Proceedings. 2015 [4] Choi W. Comparison and utilization of evaluation method for internal quality of slab. METEC & 4thESTAD Conference Proceedings. 2019 [5] Rieß S, Weber W, Petry S, Herrmann H-G, Rabe U, Pudovikov S. Evaluation of Internal Slab Quality by an Advanced Ultrasonic Testing System. METEC & 4thESTAD Conference Proceedings. 2019 [6] SEP 1611. Evaluation of Centerline Segregation of Continuously Cast Slabs. 2018
8a EDIZIONE CORSO
Metallurgia per non Metallurgisti
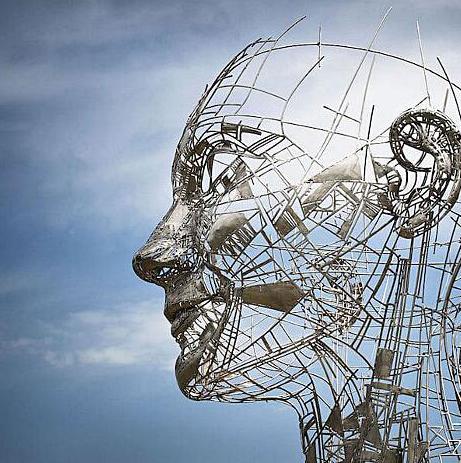
8,9,15,16,22,23, 29,30 MARZO - 5,6,12 APRILE 2022
Il Corso - proposto dall’Associazione Italiana di Metallurgia in modalità webinar - è stato rimodulato in undici mezze giornate per favorire la fruizione da remoto. I docenti, di estrazione sia accademica che industriale, assicurano un mix di competenze difficilmente raggiungibili in altra sede. Il programma fornisce sia pure succintamente, e lezione per lezione, le principali indicazioni riguardanti i diversi argomenti trattati nel Corso. Le lezioni, si susseguiranno tra loro in modo da fornire al partecipante una conoscenza panoramica a trecentosessanta gradi dell’ampio settore metallurgico.
Target Il Corso è dedicato a persone non coinvolte in attività che richiedono una preparazione avanzata nei vari settori metallurgici, ma alle quali è sufficiente la conoscenza, l’interpretazione e la spiegazione della metallurgia nei più svariati settori tecnologici, applicativi, selettivi, ispettivi e di collaudo. “Metallurgia per non metallurgisti”, con un linguaggio per “non addetti ai lavori”, è rivolto a manager, personale di vendita e di acquisto, progettisti, ispettori e in generale a tutti coloro che devono lavorare e utilizzare materiali metallici, senza avere necessariamente una preparazione universitaria.
Coordinamento: Prof. Carlo Mapelli
Docenti del Corso
Paolo Albertelli - Politecnico Di Milano Silvia Barella - Politecnico Di Milano Francesca Bisaglia - RTM Breda, Cormano Matteo Bosatra – Fondinox, Sergnano Giovanni Maria Caironi – F.I.A.S., Gorla Minore Riccardo Casati - Politecnico Di Milano Enrique Mariano Catrodeza – Politecnico Di Milano Mario Cusolito – Consulente, Lecco Marco De Marco – IIS, Genova Ezio Debernardi - Consulente, Torino Elisabetta Gariboldi - Politecnico Di Milano Andrea Gruttadauria - Politecnico Di Milano Marina La Vecchia - Università Di Brescia Nora Lecis - Politecnico Di Milano Vincenzo Loconsolo - Consulente, Milano Carlo Mapelli - Politecnico Di Milano Livio Marietti - A. Benevenuta & C., Forno Canavese Alberto Morini - Fondinox, Sergnano Tommaso Pastore - Università Di Bergamo Ilaria Rampin – Pometon, Maerne Dario Ripamonti – CNR Icmate, Milano Elisabeth Sfameli – RTM Breda, Cormano Andrea Tavasci – Tenarsidalmine Luigi Varalda - Consulente, Torino Valentina Vicario – Soliveri, Caravaggio
8,9,15,16,22,23, 29,30 marzo 5,6,12 aprile 2022
totale ore: 44
Da remoto:
in modalita sincrona
(diretta streaming su piattaforma Zoom)
in modalità asincrona
(registrazioni su area riservata)
Segreteria organizzativa
Associazione Italiana di Metallurgia
Evento patrocinato da