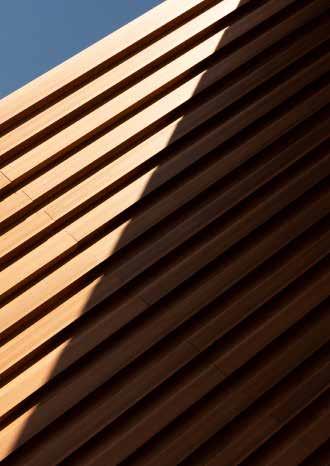
The text pages of this publication have been printed on paper manufactured in Australia and produced from responsibly managed forests.
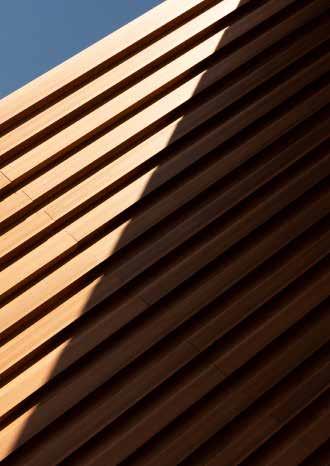
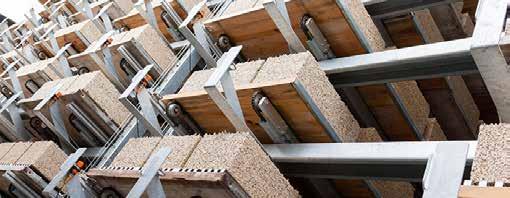
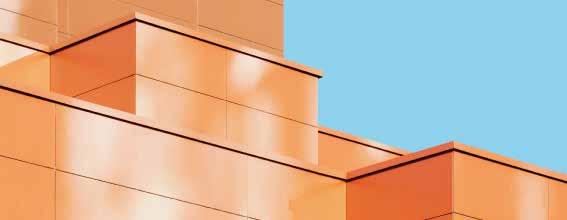

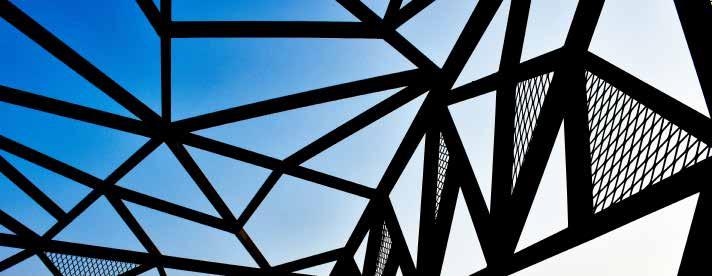
The text pages of this publication have been printed on paper manufactured in Australia and produced from responsibly managed forests.
The increase in infrastructure work in Australia over recent years has resulted in a lack of resources, poorly applied lessons learned from previous projects of a similar nature, and a lack of consistent benchmarks to validate projects. The scale, complexity, value of projects, and significant interfaces between contract packages and stakeholders create the need for joint ventures, attracting complications on which systems to use, multiple reviews, how to resource, and the many different management styles among the many variables which add cost and complexity to infrastructure projects.
Presently, there is a lack of skilled professionals in Australia to deliver many components of infrastructure projects. It is often on the system/ software side where infrastructure projects come undone. When budgets are established, the risks are often underestimated, and understating the final cost is partially due to a lack of experience.
The common misconception that the traditional approach of transferring the risk costs the client less money is not well-founded and incorrect. Neither
the client nor the contractor, during the development of the budget and project bid phase, can understand the extent of risk. Passing the risk to a contractor adds cost to the project, and ultimately when the project goes off the rails, the client will need to step in and help sort it out. Risk needs to be allocated to the party best placed to manage that risk, and some inherent risks need to be retained by the project owner. The construction industry cannot be expected to take on risks that are often too difficult to quantify at the tender stage.
is often agnostic of contractual risk (varying from project to project with non-standard contracts), latent conditions, and risk allocation. If a standard risk allocation matrix was prepared at the project's inception with cost and time considerations and applied to the project budget, a more robust budget would be achieved, thereby preventing project delays when the contractor submits their offer.
Traditionally, government agencies have engaged the industry through lump sum contracts or re-measurable rates contracts transferring a range of risks to the contractor. The other more common form of contract is the Public-PrivatePartnership (PPP). These contracts often contain performance components that may include patronage or long-term maintenance provisions.
There is a disconnect between the initial project budget and what contractors include in their tenders. The standard approach in establishing a budget
Most infrastructure contracts are bespoke or utilise a standard form contract that has been significantly amended, resulting in most risks being pushed onto the contractor (who is often not the entity best placed to manage the risk). There is much greater use of standard contracts with known and more equitable risk allocations in other countries. Complicating the process is a client who is unwilling to accept a nonconforming tender with qualifications. The size and value of the projects require Tier 1 contractors to compete against one another to provide the client with several submissions. However, this is being hindered when the proposed risk apportionment is not fair and equitable during the tender stage due to Tier 1 contractors stepping back, resulting in fewer options for the government.
There are strategies available to manage some of the risks including a geotechnical baseline to be provided to the contractors during the tender period. If there is a difference from the baseline, then an adjustment will be made. It all starts with developing a standard risk pro-forma for each infrastructure sector (i.e. road, rail, water). Identification and management of the risks, incorporating lessons learned, is the foundation for mitigating risk.
Improved understanding of risk can be achieved through early contractor involvement, leveraging the industry's experience in executing similar work. Furthermore, data collection on outturn costs and analysis could be used to benchmark contingencies required in the business case.
AIQS proposes that project risk allocated to the contractor should be managed through an appropriate reimbursable mechanism. We are undertaking further work with the Australian Construction Industry Forum (ACIF) concerning the allocation of risks on construction projects.
GRANT WARNER CEO Australian Institute of Quantity Surveyors"Focusing on derisking the project as early as possible would also lower the overall cost and build confidence within the industry."
5 JANUARY 1949 TO 11 FEBRUARY 2023 (AGE 74)
By Anthony Mills FAIQS, CQSDennis Lenard's passing on the 11th of February 2023 is a huge loss to the quantity surveying industry. Dennis joined the AIQS NSW Chapter in 1973 and worked his way up to become president of the institute in 1995. Many people were familiar with Dennis as an industry innovator and thought leader.
Dennis and I met in 2001 while travelling to the United States in preparation for the ICEC/PAQS World Congress in Melbourne. He asked if I wanted to tour the University of Pittsburgh campus the night before to talk about what might be required
to manage the conference papers. We discussed the need for high-quality papers on quantity surveying topics in academia and practice, and Dennis offered to assist me. Dennis was a mentor to me and many others, and his advice and support were greatly appreciated.
Dennis was the first Australian president of the International Cost Engineering Council (ICEC) and the first president of the Pacific Association of Quantity Surveyors (PAQS), making him the only person in the world to hold both positions. He was a strong supporter of international
organisations and the relationships they foster. He was particularly convinced that the AIQS had a duty to assist other quantity surveying associations in developing educational and competency standards. He was a visionary who wanted to promote the value of quantity surveying at all levels, from local to global.
Dennis graduated with a Bachelor of Applied Science (with Honours) degree from the University of Technology, Sydney. He later earned a Master’s degree from UTS and a PhD in construction innovation from the University of Newcastle; a
theme that grew into a lifelong passion and later found expression in many of the roles he took on throughout his career.
Dennis began his career in the 1970s with a variety of construction firms that worked in both the building and civil industries. He founded a highly successful housing company before launching his own private development firm. He was well-versed in the construction industry, having faced many of its challenges firsthand.
In the late 1980s, he changed careers and became a senior academic, taking a role at the University of Technology, Sydney as Professor and Head of School. He immediately began looking for ways to broaden its horizons. He spent two years in Shanghai and one year in Hong Kong, making valuable contacts and expanding his understanding of how to improve and reform the global construction industry. During this time, he also became a Director of the Construction Industry Institute of Australia, a group that brought together industry and universities to solve difficult and entrenched problems.
Dennis was appointed Director of the Centre for Construction Innovation in Manchester, United Kingdom, in 2000, while also serving as a Professor of International Construction at Salford University in the United Kingdom. At that point, he began to understand the issues confronting the construction industry in the United Kingdom, which has one of the world's most sophisticated construction markets.
Dennis returned to Australia in 2002 as the Director of the Business and Industry Development Research Program at the Australian National Cooperative Research Centre for Construction Innovation - a government-sponsored research centre tasked with studying industry dynamics and developing guidelines to improve industry practices.
Dennis was approached in 2003 to become the Chief Executive of Constructing Excellence in the United Kingdom. The position was regarded as the most senior government position in the UK construction industry, and after accepting the appointment, it was ratified and formally announced by the UK construction minister. Dennis's role was to work strategically to accelerate change and build sustainable businesses across the entire supply chain and the UK construction sector.
When Dennis was interviewed for the influential, "Building" magazine, the reporter began, "Trust an antipodean to want to turn everything upside down. But the new CEO of Constructing Excellence believes that's what we need to do to improve the industry's image - and he's starting with a fundamental review of his own company.” His opinions were frequently challenged and often politically charged, but he handled the role with the professionalism and integrity that he was known for.
Dennis returned to Australia in 2007 and took on many advisory and consultancy roles. He led many government reform initiatives at both state and federal levels. This included major players like the Strategic Industry Leaders Group and the Design Value Working Group.
Dennis was, "someone who could talk to the contractors but also be convincing in a more academic role," according to Peter Rogers, chairman of Constructing Excellence, UK. He was a quantity surveyor with a broad worldview who understood the stresses of the construction industry. He was generous with his time and cared for many people along the way. Dennis received numerous awards from various organisations, including ICEC and PAQS, and was named a Life Fellow of AIQS in 2003.
Dennis is survived by his wife, Frances, and two children, a son, John, and daughter, Andrea. He was a lifelong sports fan and avid golfer. "My rugby teammates used to call me ‘twinkle toes,’ because I had a real burst of speed for a prop forward," he said in a 2003 article in Building magazine. Dennis was a successful quantity surveyor who valued and nurtured many people he met during his productive career.
Vale Dennis Lenard LFAIQS
More often than not, claimants derive prolongation costs by determining an average daily rate taken from the preliminaries and/or indirect costs listed in the contract and multiplying that rate by the number of days of delay.
A claimant must first identify the actual days of delay a respondent is culpable. The appropriate method to identify actual days of delay is to complete a cause-andeffect delay analysis. Next, the claimant's actual days of delay need to be identified to quantify the costs incurred on those days. Finally, the claimant should then analyse its cost records relating to the periods of delay, which are the respondent's responsibility.
Prolongation costs must reflect the actual losses incurred by a claimant unless otherwise stated in the contract.
To demonstrate a causal link and substantiate the cost claimed, the claimant should reconcile records of the indirect and direct costs such as daily reports and/or timesheets to the days claimed. In addition, the claimant can put forward other records such as invoices, if they can be proven that they are recoverable.
Assuming actual days of delay have been identified and the actual costs have been quantified and separated into indirect and direct costs; the claimant is also required to evidence that the costs claimed were on the project. Substantiation in the form of (but not limited to) daily progress reports, daily diaries and sign-in/out registers is required. Without this type of
contemporaneous evidence, it would be difficult for a claimant to prove the costs they are claiming were related to the delay event(s).
Generally, the claimant can claim only time-related indirect costs incurred during the period(s) of delay identified and costs can only be claimed for the days that are not the claimant's culpability. These costs typically include staff salaries, insurance costs, bank guarantees and reoccurring site running costs. The claimant cannot include purchase costs or capital costs such as vehicles, plant and office equipment.
Direct costs that the claimant can claim are those direct costs that naturally flow from the identified delay events. It is reasonably straightforward to work out the direct cost by reviewing an as-built program that demonstrates what direct costs were on the critical path at the time of the delay. Records such as timesheets, sign-in sheets and payroll data will provide evidence the direct costs were incurred during the delay period.
A general example of a claim for direct costs is when a three-day respondent delay event occurs and therefore delays the critical electrical commissioning team on a power station. The commissioning personnel and associated plant and equipment could not carry out any work on the project and the costs could not be mitigated by demobilisation and remobilisation. This means the cost for the personnel, plant and equipment would be increased by a further three days as there would be an additional three days spent on the project to complete the electrical commissioning works. The claimant would be able to demonstrate that the electrical commissioning work is on the critical path by way of a CPM programme and would need to prove by way of daily reports, daily timesheets and sign-in/
out registers that the personnel and equipment were on site when the delay occurred.
Generally, unless stated otherwise in the contract, profit cannot be claimed as part of a prolongation claim as it is not a ‘cost’. Profit would need to be claimed separately as a loss of profit claim (depending on the jurisdiction).
The key points to remember when quantifying prolongation costs are as follows:
1. Identify the actual days of nonculpable delays
2. Only quantify reoccurring indirect actual costs incurred (unless the contract allows for pre-agreed rates to be used)
3. When claiming direct costs, demonstrate these costs are on the critical path and only claim the actual costs incurred (unless the contract allows pre-agreed rates to be used)
4. Maintain records of the actual personnel, labour, plant and equipment affected by the delay event
5. Do not determine prolongation costs by using an average daily rate determined by the preliminaries contained within the contract (unless expressly allowed under the contract)
6. Do not divide the total loss incurred by the number of days of delay as this is at best a total loss or global claim approach.
This article was written by Paul McArd MAIQS, CQS and first published via Accura Consulting LinkedIn (linkedin.com/pulse/how-quantifyprolongation-costs-non-globalapproach-/).
Climate change is a severe environmental threat faced by the world. Scientists have evidenced the impact of global warming and its effects on climate change as caused by the release of Green House Gases (GHGs) into the atmosphere. The report, issued by the Intergovernmental Panel on Climate Change (IPCC), declared that GHG emissions should be reduced by 45% by 2030 compared to 2010 to achieve a 100% reduction by 2050¹. Regarding GHG emissions, the construction industry is one of the worst offenders due to its continued heavy fossil fuel consumption. Therefore, a higher percentage of carbon-related emissions is recorded to be from the construction industry. Compared to other industries, the construction industry plays a critical role in response to climate change by accounting for around 39% of energyrelated emissions globally². The Building sector, a significant component of the construction industry, has become the world’s largest contributor to GHG emissions. Therefore, minimising the carbon emissions of buildings is one of the important concerns in the present context. The need to fulfil this commitment of reducing carbon emissions in the built environment is changing the industry’s behaviour towards the awareness of carbon accounting. The Quantity Surveyor has the specific role of quantifying construction works and as the
accountant in construction is thus well placed in counting carbon emissions. Embodied Carbon (EC) and Operational Carbon (OC) are the two types of carbon emissions generated during the construction life cycle. OC is the emissions (CO2 and CO2 equivalent gases) generated from the operational activities of the building, such as lighting, heating, cooling, etc.
EC is the carbon-related emissions (CO2 and CO2 equivalent gases) due to non-operational works of a building such as material extraction, production, transportation, and construction, together with the downstream works like maintenance, and demolition. The term embodied is important to distinguish from embedded as carbon emissions are not embedded in construction materials and components but accounted as
emitted during the process of production and or construction. Since 86% of the GHGs constitute Carbon Dioxide (CO2) and a unit namely, Carbon Dioxide Equivalent (CO2e) has been developed for the remaining 14% consisting of Methane (CH4), Nitrous Oxide (N2O), and refrigerant gases to gain the uniformity of measurement³. EC accounts for approximately 20-30% of a conventional building, while OC contributes around 70-80% of the overall carbon emissions of the building life cycle⁴.
In contrast to OC, EC emissions are connected with various stages of the building life cycle. Therefore, it is essential to identify the phases of the building life cycle to estimate the EC of a product precisely. These phases are collectively known as system boundaries as given in Figure 1.
¹Chen, S., Teng, Y., Zhang, Y., Leung, C.K.Y. & Pan, W. 2023, 'Reducing EC in concrete materials: A state-of-the-art review', Resources, Conservation and Recycling, vol. 188, DOI 10.1016/j.resconrec.2022.106653. ²Ibid.
³Du, Q., Bao, T., Li, Y., Huang, Y. & Shao, L. 2019, 'Impact of prefabrication technology on the cradle-to-site CO2 emissions of residential buildings', Clean Technologies and Environmental Policy, vol. 21, no. 7, pp. 1499-514, DOI 10.1007/s10098-019-01723-y.
⁴Ashworth, A. & Perera, S. 2015, Cost studies of buildings, sixth edition, Routledge. ⁵Ibid.
To address the issue of climate change, the construction industry has concentrated more on decreasing the OC of buildings. As a result, new buildings are becoming more and more energy efficient and even zero OC. Therefore, the OC component of new buildings is significantly lower and the EC component has become the focal point for reduction of emissions. Figure 2 portrays the variations of OC and EC due to the energyefficient improvements in buildings.
By 2050, EC is predicted to be responsible for around 50% of total carbon emissions from new construction projects⁷. Further, EC is emitted within a shorter period, leading to more intensive annual impacts than OC. Unlike OC, EC estimation is still unregulated, and therefore more attention needs to be paid to evaluating EC in construction projects.
EC estimating can be conducted using first principles starting from raw material extraction to the end of the life cycle, by considering every step. Nevertheless, scrutinizing each step of the life cycle of a product, from its raw material mining to the final step (within the selected system boundary), is comprehensive and consumes a lot of time. EC estimating is facilitated through databases and software tools which use many EC factors to enhance efficiency and to reduce the difficulties in EC estimating. The databases and tools, frequently adopted in EC estimating are shown in Table 1.
When a product moves from its raw material extraction to the final step of the selected system boundary, it should be transported from one place to another. For instance, from the place of raw material mining to product manufacturing and then from product manufacturing to the construction site, and so forth. Therefore, transportation distances would change from one case to another, and many variations can happen for two selected cases even for the same material (e.g., brick). Similarly, changes in transportation mode (e.g., dump truck, flatbed truck) can also happen frequently for two selected cases of the same material. Therefore, changes in transportation distances and modes may affect variations in fossil fuel consumption for a particular task. Since the emission factors are available within static databases, these need to be adjusted to suit the specific case, transportation distances, location, and transportation modes of that case.
These result in inaccuracies and bias in estimating. These changes and inaccuracies can have a compounding effect on a full-scale project estimate.
Many construction materials include a comprehensive process from the mining of raw materials to the end product. The fossil fuel usage for the manufacturing process will change due to various factors such as variations in types of machines, changes in power usage of machines, changes in power mode of machines (e.g., petrol, diesel, or electricity), shifting from manual to an automated process and vice versa, and whether the machines are new or old (the efficiency factors). Since these changes are case sensitive, EC estimates carried out with the use of static databases can be significantly different from estimates using first principle-based methods.
Even when considering the same electrically operated machinery used for the production of a building component,
ICE
Book/excel Cradle to Gate UK
Blackbook Book Cradle to Gate UK
AusLCI Excel sheets Cradle to Gate Australia
EPiC Book Cradle to Gate Australia
Ecoinvent Web application Cradle to Gate Switzerland
GaBi Software Cradle to Grave Germany
SimaPro
Software Cradle to Grave Netherland
eToolLCD Web application Cradle to Grave Australia
ECE Tool Web application Cradle to Gate Australia
Athena estimator Software Cradle to Grave USA
OneClickLCA Software Cradle to Cradle Finland, UK, USA, France
Embodied Carbon in Construction Calculator (EC3)
The FOOTPRINT Calculator
Software Cradle to Gate/Grave USA
Software Cradle to Grave Australia
Asset Impact Software Cradle to Gate/Grave Australia
there could be significant differences in the carbon emission profiles of two different production plants in two different states (or countries). This happens because of changes in the power generation profile of two different electricity suppliers. For example, an electricity supplier with a power generation profile of 20% renewable and 80% fossil fuel-based generation is significantly different from one with 60% renewable and 40% fossil fuel-based generation. As such, the use of static databases with carbon emissions for primary material based on a given power factor will not be accurate.
Most EC databases are based on static data derived from one location. Due to
volatility and rapidly changing energy profiles of power generators worldwide, the use of such static factors results in creating inaccurate estimates for EC. These errors identified have a compounding effect on EC estimates derived from static databases. Even with identical components, origins, and technologies, estimates carried out using GaBi and SimaPro showed different outcomes.⁸ In another comparison, EC estimates which were carried out for seven work items by adapting Blackbook and eToolLCD had significant variations from 8% to 402% compared to first principle-based mechanism⁹. Considering all the above, it is quite evident that static datasets are no longer suited for preparing accurate EC estimates and it is necessary to move towards a mechanism that can capture dynamic datasets.
A construction project consists of numerous supply chains and each supply chain includes different stakeholders (miners, manufacturers, subcontractors, contractors, etc.). If we have the capacity to capture the real-time data from these stakeholders directly, it will enable us to estimate EC accurately. Then the issue is how we can capture those data. Fortunately, we now have technologies such as Blockchain that potentially can solve this issue due to its salient features. The Centre for Smart Modern Construction has developed a dynamic way of estimating EC using a blockchain platform for construction supply chains.¹⁰ Despite blockchain, any other technology that can capture dynamic EC datasets is suitable for reaching a dynamic way of estimating EC. As a way of addressing this, it is essential to access the production data, power profiles, and location data among others, and collect the real-time data within the construction supply chains. This will help to develop a bottom-up EC estimation. The future of this might be in automating the capturing process of data. Stage by stage, we need to remove the manual intervention and enable auto-capture of data. Therefore, in moving from static datasets to dynamic datasets, every stakeholder in the construction industry has a specific role to play. Future Quantity Surveyors need to be equipped with new technologies to deal with these estimates.
This article was written by Srinath Perera MAIQS and Namal Anuradha
from the Centre for Smart Modern Construction, Western Sydney University, Australia
⁸Sinha, R., Lennartsson, M. & Frostell, B. 2016, ‘Environmental footprint assessment of building structures: A comparative study’, Building Environment, vol. 104, pp. 162–171.
⁹Rodrigo, M.N.N., Perera, S., Senaratne, S. & Jin, X. 2021, 'Review of Supply Chain Based EC Estimating Method: A Case Study Based Analysis', Sustainability, vol. 13, no. 16, DOI 10.3390/su13169171. ¹⁰Ibid.
Economic uncertainty was cited as the top challenge for Australian construction businesses, the latest research from Deloitte and Autodesk found. In fact, 61% of construction businesses reported that rising material and labour costs were having significant impact on their financial viability. KPMG research also shows just 31% of projects come within 10% of the original budget, indicating that budget control is more crucial than ever in this uncertain economic climate. There are three vital steps construction professionals can take to contain and optimise costs in their projects.
To know how to address cost overruns, it’s important to understand the root of the problem. In most cases, a project’s overrun is a result of inaccurate analysis or planning before building even starts. In parallel with better planning, technology can help to reduce the common problems or elements that contribute to cost overruns, ensuring you can maximise efficiency and profits.
Below are some of the most common cost overruns to mitigate.
While many of a project’s stakeholders are eager to get the project’s building started, if you begin with faulty schedules and budgets, your project is headed for an overrun from day one. Due to the competitive nature of the tendering process, estimates may suffer from wrongful expectations of the scope of work included in the project. In many cases, some projects will also be estimated on a one size fits all basis, with chances of exceeding that initial estimate high. Therefore it’s vital
to your project’s success to do your due diligence in the preconstruction phase and be accurate and realistic about project deadlines and cost from architects and contractors.
Estimating the project accurately can get started in the RFP process. This is the opportunity where project stakeholders can express their concerns over budget and timelines. If any of the parties appear to be unrealistic about timing or budget, this should be an immediate red flag.
Unfortunately, design deficiencies are too common. Sometimes these could be incomplete or incorrect plans resulting in substandard work. These issues can be mitigated with software that ensures everyone is on the same page, reducing the risk of errors or incomplete designs. During construction, if the project experiences an unexpected change in its scope, for example, it is much easier to plug those design changes into a dynamic digital model than to redraw them on paper.
Alternatively, to enable contractors and subcontractors to build according to the design specifications, owners and contractors should agree on the specific Scope of Work and performance duties in the contract phase. This documentation should include clear references to:
• All project specifications on design documents
• Warranties of the exact work to be completed by contractors
• A risk allocation chart or definition
• A process for unforeseen issues
• A dispute resolution and/or mediation process
Change order requests added after the budget has been set often result in cost overruns. The additional time, labour and materials required to complete the change may also be classified as a cost overrun if it affects other aspects of the project. Consequently, changes can usually be best addressed in the contract phase, when a Change Order Provision can be added to specify procedures and budget needed should a change occur. If it isn’t addressed ahead of time, contractors might increase their total cost of a contract up front in anticipation of changes.
Stakeholders on construction sites have different interests, which can add to instability when any site changes occur. Site changes need to be communicated effectively and quickly, especially across large sites.
With software, calculations and designs can be referred to digitally for accurate reading, and different scenarios can be tested to see which will result in the better outcome. Because digital calculations are assured to be precise (accurate inputs are needed) and software designs can be trusted to accurately depict on-site descriptions, decisions can be made quickly based on solid information, not differing interests. Online access to designs and scenarios allows for greater communication from remote locations. Decisions can be made while project leaders are on site, looking at an issue directly. Faster communication also leads to better decisions, as real-time insight can address a situation before it snowballs into a bigger issue which impacts the budget.
Overruns can be the result of subpar work. Less experienced subcontractors
can cause costly mistakes, delays and errors, even with the most impeccable designs and plans. Subcontractors are often chosen on cost, rather than proper qualification. Using the wrong teams exposes contractors to risk. Contractors who go through the extra steps to ensure subcontractor qualification will reduce the probability of experiencing significant cost overruns on construction projects.
Construction firms often face financial risks from client disputes. The global average value of construction disputes was $52.6 million, according to Arcadis’ 2022 Global Construction Disputes Report. Disputes can cause disruptions during construction projects, resulting in project delays, broken contracts and even litigation.
Here are some risks that can be reduced using construction software:
Technology lowers the risk of defects from failure to perform a repair or remodel properly. By arming contractors with better data and access to key information, construction teams can avoid mistakes that lead to injuries and claims.
Contractors have often found it difficult to defend or clarify their actions when a problem occurs. Software that improves documentation and provides all information accurately could help the contractor avoid litigation.
If property damage is not the contractor’s fault, centrally stored data or activity logs can help prove this to key stakeholders and authorities.
Software can help address contract compliance by ensuring accuracy and fostering clarity of scope throughout the entire project lifecycle, avoiding potential disputes downstream. Using software to create a collaborative environment and enabling information sharing between all project stakeholders, rework and coordination issues are much less likely to arise.
Safety issues and incidents can raise your insurance costs. With a welldocumented safety record, your firm will pay less in premiums. A strong safety culture and qualified subcontractors are foundational for reducing overall safety risks and issues. Technology can further solidify the success of safety programs and new innovations can even proactively reduce risk.
The best way to gain control over your construction finances is to have a central cost management system that provides flexibility and customisation to meet changing and unique project needs. Here are the key attributes of a solid construction cost management system that keeps your projects running on time and within budget.
• Connected and centralised cost management. It is critical that the system that you’re using to record, calculate, and forecast costs is connected to any other related applications being used. Doing so keeps multiple moving parts in sync, eliminates the need for double-entry, and helps teams be more efficient.
When you centralise the management of all cost activities, you ensure that your construction data is connected and auto-updates across the platform to offer an accurate view of the project’s financial health. A centralised system also provides a single source of truth, so stakeholders can have one reliable hub for data. Finally, a tightly connected cost management system can offer a real-time view of your project’s financial health, so you can make better decisions and forecast costs more accurately.
• Customisable structures and terminology. You want a construction cost management solution that adjusts to your unique processes, so equip your team with a solution that lets you customise structures and terminology.
A robust cost management tool will allow you to rename tabs, set up custom budget structures that work
with any accounting system, and create custom calculated budget columns.
• Automated workflows. Ideally, you want a cost management solution that can help automate manual tasks like elevating an RFI to a potential change order, moving change orders through the approval process, and generating contracts and payment applications easily. It’s even better if the solution allows you to improve consistency and transparency of company-defined processes across projects by creating custom approval workflows. Utilising a decision-based workflow engine, teams can automate the routing of internal approvals for Owner Change Orders, Supplier Change Orders, and Contracts based on specific conditions.
The greater accuracy and consistency of your cost-related workflows, the more likely a project will be delivered on schedule and within budget – a win-win for all parties involved.
For more complimentary resources on how to improve the financial health of your projects, download the Autodesk Cost Management Toolkit (https:// getconstructioncloud.autodesk.com/ apac-cost-management-toolkit).
Needless to mention, quantity surveyors are key players in the modern construction industry, providing expert advice to the client in cost and commercial management, contract administration, dispute resolution, etc., right from the feasibility stage through to the completion of a construction project.
Although quantity surveyors are pivotal, it is indeed a question of whether they receive the due recognition they deserve in markets like India and the Middle East, as they are perceived as only basic measurement takers. Moreover, a significant number of quantity surveyors who work here generally do not have relevant undergraduate qualifications in quantity surveying or professional memberships, despite years of industry experience.
Quantity surveyors’ effective contribution to the industry will offer them a level playing field to climb corporate ladders and secure strategic positions. The higher the skill set of a quantity surveyor, the greater the benefits to the employer, and certainly this will keep the professional engaged to the fullest extent with comprehensive responsibilities.
To achieve that, quantity surveyors need to enhance their qualifications and obtain professional memberships, in addition to developing their communication and interpersonal skills. They have to learn BIM and other software to use it appropriately. They have to also set higher professional and ethical standards to set themselves apart from other professionals.
Unless the quantity surveyors focus on the above factors, obtaining due recognition will be highly challenging in this tough environment.
Fresh Slattery research suggests tackling this hidden water footprint – known as ‘embodied water’ = can save our most precious natural resource and drive down emissions.
Although around 70% of the Earth’s surface is covered in water, just 2.5% of that is fresh water – and of that, just a fraction is easily accessible and available for use. The rest is locked away in glaciers, ice caps, permafrost or underground aquifers.
We are left with less than 0.5% of the Earth’s fresh surface water, and that is distributed unevenly across the globe. Australia, the world’s driest inhabited continent, has always been a land of droughts and flooding rains. But our variable climate patterns are becoming harder and harder to predict, with extreme droughts and floods no longer ‘once in a 100 year’ events.
As our population grows, so does our water consumption. Australia’s water usage increased by 25% between 2019 and 2021 alone¹. A massive 85% of that water was supplied to industry.
Large quantities of water are consumed during the process of growing and extracting raw materials, to manufacture and transport products, and during construction. This water is known as embodied water.
Until recently, the sustainability narrative was focused on the operations story. Green Star has rewarded water-wise design for two decades, and the Green Building Council of Australia estimates a Green Star building consumes 51% less water than the average Australian building². Architects and engineers routinely integrate rainwater harvesting, greywater systems, and water-efficient fixtures and fittings into designs. Similarly, facility management teams continue to focus on water-efficient operations. The average NABERS Water rating has risen from 3.4 stars in 2010 to 4.8 stars in 2022 as consumption is measured and managed, and equipment optimised³. Building users are being educated to turn off taps and report leaks. While these efforts are laudable, little attention has been paid to the water used at other stages of the building lifecycle. This is reflected in the scant data and lack of peer-reviewed research papers that could help us understand the size of the challenge – and the size of the opportunity. One full lifecycle assessment of an Australian residence, conducted in 2014, determined that 38.2% of water was consumed before operations⁴. As green
design and smart management drives down water consumption during the operational phase, our attention turns to the water used at other stages of the lifecycle.
Recent and rapid developments across the industry to tackle embodied carbon demonstrate how the issue of embodied water could evolve in just a few short years. Embodied water could become a spotlight issue even faster as the industry looks to reduce emissions at speed and scale.
As Australia’s property and construction industry continues its collective decarbonisation journey, the concept of embodied carbon is gaining traction. Some property and construction leaders are beginning to quantify their hidden carbon footprint – and as they do, they have an opportunity to look at water through a new lens.
¹ Australian Bureau of Statistics 2022, Water Account, Australia 2020-21, ABS, accessed 20 February 2023, <https://www.abs.gov.au/statistics/ environment/environmental-management/wateraccount-australia/latest-release>.
² Green Building Council of Australia 2019, Green Star in focus: The business case, GBCA, accessed 20 February 2023, <https://gbca-web. s3.amazonaws.com/media/documents/gbca-green-star-infocus-the-business-case-v1-r6-digitalspreads-reduced-size.pdf>.
³ NABERS 2022, Annual report 2021-2022, Program Statistics Office – Water, Australian Government, accessed 20 February 2023, <https://nabers. info/annual-report/2021-2022/office-water/>.
⁴ Stephan, A. & Crawford, R.H. 2014, ‘A comprehensive life cycle water analysis framework for residential buildings’, Building Research & Information, vol. 42, no. 6, pp. 685–695, doi: https://doi.org/10.1080/09613218.2014.921764.
“Up to 38% of a building’s lifecycle water consumption can occur before anyone ever turns on a tap.’’
“Slattery analysis finds that, on average, 92% of embodied water is consumed during the product stage – and that the materials with the highest embodied water are also the highest in embodied carbon.”
To understand the untapped potential of embodied water, Slattery’s Carbon Planning team benchmarked and compared the embodied water and embodied carbon of common building materials to understand the association between the two. Here’s what we found…
The Australian Life Cycle Inventory Database (AusLCI) provides industryaveraged data on the environmental impacts of a wide range of Australian products and services. Using AusLCI data, our analysis found that common building materials – especially concrete, glass, aluminium and steel – are the most water-intensive materials, and also those with the highest embodied carbon. Note: A logarithmic scale is used to reflect the wide variation between low and high embodied water and carbon materials.
Large quantities of concrete and glazed curtain walls are common in new builds. The process of making glass involves melting raw materials at high temperatures – which generates significant carbon emissions – and water is used for cooling, cleaning, mixing, quenching and waste treatment. Depending on the glass being manufactured, up to 32.2 litres of water can be consumed per kilogram of glass produced⁵.
Cement, an essential ingredient of concrete, is produced at extremely high heats, generating around 7% of global emissions⁶. Cement production generates emissions through the chemical process of calcination, which breaks down limestone through extreme heat. Cement production is also water intensive. One study found concrete production was responsible for 9% of global industrial water withdrawals in 2012⁷.
If materials that are high in embodied water are also high in embodied carbon, this means that specifying low carbon materials has an additional advantage of reducing embodied water.
To drill down further, we compared the embodied water of two Boral concrete products: the normal general purpose blend and Envisia, a lower carbon concrete that uses 50% less cement. We found Envisia is not only lower in embodied carbon, but also reduces embodied water by around 10%. We suggest this is because Boral Envisia uses less cement, and therefore less water, in production.
Not all materials that are high in embodied carbon are high in embodied water. Slattery’s research finds a correlation, rather than a causal relationship between embodied carbon and water.
Not all data can be used with 100% confidence either. There are still some
⁵ Crawford, R. 2022, ‘Embodied water in construction, Acumen Practice Notes’, Australian Institute of Architects, 1 December, accessed 20 February 2023, <https://acumen.architecture.com.au/environment/water/embodied-waterinconstruction/>.
⁶ Heincke, S., Maksimainen, J. & Reiter, S. 2023, ‘Decarbonizing cement and concrete value chains: Takeaways from Davos’, McKinsey & Company, 3 February, accessed 20 February 2023, <https://www.mckinsey.com/industries/engineering-construction-and-buildingmaterials/our-insights/ decarbonizing-cement-and-concrete-value-chainstakeaways-from-davos>.
⁷ Miller, S.A., Horvath, A. & Monteiro, P.J.M. 2018, ‘Impacts of booming concrete production on water resources worldwide’, Nature Sustainability, vol. 1, pp. 69–76, doi: 10.1038/s41893-017-0009-5.
“Not all materials that are high in embodied carbon are high in embodied water. Slattery’s research finds a correlation, rather than a causal relationship between embodied carbon and water.”
gaps in carbon data, and even larger gaps in the data needed to make sound decisions about embodied water.
When it comes to quantity surveying, the devil is always in the detail. It is important to understand how different materials, required in vastly different quantities, can influence the embodied water outcome. For example, while one unit of a particular material may be considerably lower in embodied carbon or water than an alternative, the quantity required may reduce its appeal and sustainability impact.
Note: The embodied water (y-axis) and upfront embodied carbon (x-axis) of Boral Normal GP Blend on Figure 2 and Low-carbon Envisia embodied water product, based on Boral Victoria Region Environmental Product Declaration (EPD), for LCA Stages A1-A3.
Life Cycle Assessments, or LCAs, assess the environmental impact of materials, products and services across their entire lifecycle. While LCAs are primarily used as a tool to measure and offset carbon emissions, fresh water usage is calculated in this analysis.
We found most embodied water can be attributed to LCA stages A1-3 (product stage) with minimal contributions from A4 (transport stage) and A5 (construction stage).
Across our benchmarks, an average of 92% of embodied water is used during raw materials extraction and product manufacturing (Figure 3). Despite this, the construction industry’s focus has been on sustainable water use on construction sites (A5) and on the use stage (B7).
We also analysed benchmarking data from a selection of 30 diverse new builds and refurbishments. This analysis, illustrated in Figure 5, found commercial,
residential and health buildings have the largest embodied water footprints per square metre of gross floor area (GFA). On some projects this can be the equivalent to the water held in 114 Olympic-sized swimming pools.
To standardise the results and compare projects of varying sizes, we divide the total embodied water by the GFA. A typical new build project has large quantities of concrete, steel reinforcement, structural steel, aluminium and glazing. This explains why the health, commercial and residential sector benchmarks have relatively high embodied water.
Fitouts and refurbishments have lower embodied water, highlighting the embodied water saving opportunities that can be achieved by repurposing existing structures.
There is a notable void in available data to accurately benchmark embodied water.
Crawford analysed common building materials in Australia and demonstrated, through a residential case study, that concrete and timber products have the largest embodied water footprints.⁸ Concrete, as mentioned earlier, uses vast quantities of water during manufacture. Timber, on the other hand, is used in large quantities in residential construction, and therefore has a larger embodied water footprint.
Crawford’s case study considered the lifecycle of the house over a 50year period, finding that the frequent replacement of internal finishes such as paint and carpet contributed the largest overall proportion of embodied water. This highlights the opportunity to reduce recurrent embodied water impacts by opting for longer-lasting products and materials.
Research undertaken by Deakin University of 17 non-residential buildings in Australia⁹ suggests that the embodied water impact is greater than the volume of water used throughout the building’s operational life. Materials selection plays a major role in a building’s embodied water, the research found. But this study, while valuable, did not calculate services, fixtures and fitments due to a lack of data availability. Large, high-rise buildings contain high quantities of service equipment, as well as fixtures and fitments in amenities and end-of-trip areas.
There is substantial variation between AusLCI embodied water figures and datasets employed in the academic studies to date. As mentioned earlier, there
⁸ Crawford, R. 2022, ‘Embodied water in construction, Acumen Practice Notes’, Australian Institute of Architects, 1 December, accessed 20 February 2023, <https://acumen.architecture.com.au/environment/water/embodied-waterinconstruction/>.
⁹ McCormack, M., Treloar, G.J., Palmowski, L. and Crawford, R. 2007, ‘Modelling direct and indirect water requirements of construction’, Building Research & Information, vol. 35, no. 2, pp.156–162, doi: 10.1080/09613210601125383.
“...this can be the equivalent to the water held in 114 Olympicsized swimming pools.”
are also few peer-reviewed papers to draw upon. This highlights an opportunity to develop a nationally consistent framework to measure industry-averaged embodied water impacts.
With no nationally accepted methodology for conducting LCAs, outcomes and data quality can vary substantially. This is an impediment to accurate and comprehensive carbon emissions data, and also prevents us from quantifying and comparing embodied water impacts.
NABERS and the Green Building Council of Australia are currently collaborating with industry experts, including Slattery, to develop a national framework for embodied carbon emissions. This will set a common method to measure, benchmark and certify the upfront embodied carbon emissions of construction and building materials. Industry has identified an opportunity to extend this scope of work to capture other environmental impacts, such as water.
Slattery’s recommended approach is aligned with the ethos of our Carbon Planning Service – and that is to measure embodied carbon throughout the design process to identify and address those with the emissions-reduction potential. By modelling and measuring embodied carbon impacts early in the project lifecycle – and then by making informed adjustments to a building’s design – an embodied carbon reduction of around 10% can be achieved without an additional cost. By reducing embodied carbon, we believe there is likely to be a corresponding reduction in embodied water.
Sizeable opportunities to drive down emissions and reduce embodied carbon are found at the earliest stages of design, as core building components such as the substructure, structure and façade are locked in. The same is true for embodied water. For example:
Build less
• Dematerialise: Efficient design can reduce the volume and quantity of materials, like concrete and steel, without compromising building utility or value.
• Minimise: Consider minimising basements and excavation, and reuse what you can from buildings that may already exist on your site.
With a clear correlation between high embodied carbon and water materials, strategies to reduce one environmental impact are likely to have a positive influence on the other.
• Eliminate: Choose raw finishes, such as polished concrete, instead of layers of materials, or offer ‘cold shell’ fitouts, rather than ‘warm shells’ that tenants may demolish and discard in landfill.
Build smart
• Prefabricate: Build offsite to reduce the amount of material needed and the amount of waste generated.
• Specify: Drive demand for lower carbon material alternatives (A1-3 emissions), such as lower carbon concrete mixes and carbon neutral certified materials. Procure innovative materials, like cross-laminated timber instead of reinforced concrete for structures.
• Verify: Look for materials that have third-party verified Environmental Product Declarations.
• Recycle: Use circular economy, closed loop principles to reuse, recover and recondition materials.
• Repurpose: Maximise future flexibility by designing for disassembly, so products and materials can be reused as the asset evolves.
Build together
• Collaborate: Work with others across the industry to champion the issue of embodied water. Developers, owners and tenants can leverage their purchasing power to advance the sustainability of supply chains by prioritising low embodied water and carbon materials.
• Share: Improve access to data to inform material choices, design strategies and changes to building regulations and government policies.
The enormous challenge of climate change has sharpened the world’s focus on carbon emissions. Measuring carbon has challenged the property and construction industry to look for the hidden costs – and hidden value –throughout the entire building lifecycle. With deep expertise in construction quantities and a cast resource of
“There is an opportunity to reduce recurrent embodied water impacts by opting for longerlasting products and materials.”
benchmarking data at our disposal, Slattery’s team is well placed to measure embodied water to guide design, specification and construction decision-making.
Australian Bureau of Statistics 2022, Water Account, Australia 2020-21, ABS, accessed 20 February 2023, <https:// www.abs.gov.au/statistics/environment/ environmental-management/wateraccount-australia/latest-release>.
Crawford, R. 2022, ‘Embodied water in construction, Acumen Practice Notes’, Australian Institute of Architects, 1 December, accessed 20 February 2023, <https://acumen.architecture.com.au/ environment/water/embodied-water-inconstruction/>.
Green Building Council of Australia 2019, Green Star in focus: The business case, GBCA, accessed 20 February 2023, < https://gbca-web.s3.amazonaws.com/ media/documents/gbca-green-star-infocus-the-business-case-v1-r6-digitalspreads-reduced-size.pdf>.
Heincke, S., Maksimainen, J. & Reiter, S. 2023, ‘Decarbonizing cement and concrete value chains: Takeaways from Davos’, McKinsey & Company, 3 February, accessed 20 February 2023, <https://www.mckinsey.com/industries/ engineering-construction-and-buildingmaterials/our-insights/decarbonizingcement-and-concrete-value-chainstakeaways-from-davos>.
McCormack, M., Treloar, G.J., Palmowski, L. and Crawford, R. 2007, ‘Modelling direct and indirect water requirements of construction’, Building Research & Information, vol. 35, no. 2, pp.156–162, doi: 10.1080/09613210601125383.
Miller, S.A., Horvath, A. & Monteiro, P.J.M. 2018, ‘Impacts of booming concrete production on water resources worldwide’, Nature Sustainability, vol. 1, pp. 69–76, doi: 10.1038/s41893-017-0009-5.
NABERS 2021, NABERS Embodied emissions initiative, Australian Government, accessed 20 February 2023, <https://www.nabers.gov. au/publications/nabers-embodiedemissions-initiative>.
NABERS 2022, Annual report 20212022, Program Statistics Office – Water, Australian Government, accessed 20 February 2023, < https://nabers.info/ annual-report/2021-2022/office-water/>.
Ritchie, H. & Roser, M. 2017, ‘Water Use and Stress’, Our World in Data, accessed 20 February 2023, <https:// ourworldindata.org/water-use-stress>.
Overbey, D. 2021, ‘LCA Stages Matter When Tracking Embodied Carbon’, Building Enclosure, accessed 20 February 2023.
Stephan, A. & Crawford, R.H. 2014, ‘A comprehensive life cycle water analysis framework for residential buildings’, Building Research & Information, vol. 42, no. 6, pp. 685–695, doi: https://doi.org/10. 1080/09613218.2014.921764.
U.S. Geological Survey 2018, ‘Where is Earth’s Water? U.S. Geological Survey’, US Government, accessed 20 February 2023, <https://www.usgs.gov/specialtopics/water-science-school/science/ where-earths-water#:~:text=really%20 is%20true.-,Earth's%20water%20is%20 (almost)%20everywhere%3A%20 above%20the%20Earth%20in,few%20 miles%20of%20the%20ground.>.
Vickers, J., Sullivan, N., Davies, A., Kogileru, T. & Wouters, T. 2022,
‘Embodied Emissions Technical Report’, Thinkstep ANZ, on behalf of NABERS, accessed 20 February 2023, <https:// www.nabers.gov.au/sites/default/ files/2022-12/NABERS%20-%20 Embodied%20Emissions%20-%20 Technical%20Report.pdf>.
I’ve been a practising Quantity Surveyor for over 40 years and have seen firsthand the gradual evolution of the profession. When I first started out, we worked off architectural plans on paper coupled with manual cost estimation. The introduction of CAD and computer calculations, and later BIM, made life easier by reducing error rates and improving efficiency.
Now, our team at Donald Cant Watts Corke are noticing the exponential growth and positive impact that AI will have on the construction industry. The next generation of leadership at DCWC, such as Mark Freestone FAIQS, CQS, and Irena Kuzman FAIQS, CQS, both previous AIQS State Presidents, are part of DCWC’s progressive executive team who are continuously looking at technologies that help us work smarter and more efficiently for our valued clients. One such technology on our radar is Machine Learning (ML) which uses historical data and machine learning algorithms to learn from experience to continuously increase efficiency and reduce costs. Another technology that we’ll hear more of is Blockchain, which is essentially a secure online ledger of transactions that allows streamlined information sharing across a network. This technology is in its infancy within the construction industry but has the potential to greatly impact the way Quantity Surveyors do business.
The DCWC leadership team also believe legislation is critical for the survival of quantity surveying. Whilst professional associations, such as AQIS, provide ethical and professional standards to protect the industry and public alike, quantity surveying is not legally mandated on construction projects in Australia. There is also no mandatory licencing of practitioners, except within Victoria where quantity surveyors must be registered with
the VBA. This contrasts dramatically with other countries, such as Malaysia where legislation and regulatory frameworks offer comprehensive protection and recognition of the profession. The quantity surveying cohort here in Australia must follow Malaysia’s lead and come together to lobby for mandatory regulatory frameworks to be introduced at a federal level. This will future-proof the profession and ensure we keep pace with the rest of the construction industry.
What is the fourth industrial revolution?
In his book The Fourth Industrial Revolution, Klaus Schwab, Founder and the Executive Chairman of the World Economic Forum says “We stand on the brink of a technological revolution that will fundamentally alter the way we live, work and relate to one another… the response to it must be integrated and comprehensive involving all stakeholders on the global polity from the public and private sectors, academia, and the civil society… It will be a new chapter in human development enabled by the merging of the Physical, Digital and Technological worlds and fashion in technologies in ways that create both ’Promise and Peril’”. As digitalisation continues to advance rapidly, the pressure on stakeholders in the Architecture, Engineering, Construction, and Operation (AECO) sector to revamp and restructure their activities and outputs becomes increasingly important. Built environment professionals will have to work with tools such as Artificial Intelligence, Augmented Reality, Big Data, Building Information Modelling, Biomimicry, Blockchain, Cryptocurrency, Cyber Security, Drone Gamification, Internet of Things, Machine Learning, Nanotechnology, Robotics, and Virtual
Reality. In working towards a sustainable construction industry, the fourth industrial revolution brings technologies to assist and accelerate construction sustainability. The fourth industrial revolution has accelerated the use of digital technologies due to Covid-19. In the past two years, new norms in the workplace have evolved such as remote working, outsourcing, and many other skills that embrace digitalisation. As the construction industry is constantly evolving, quantity surveyors should be open to and embrace innovation and new ideas. This includes exploring new construction methods, materials, and technologies that can improve project efficiency, sustainability, and costeffectiveness. Quantity surveyors should stay up-to-date if they are to be at the forefront of the fourth industrial revolution, They should be aware of new technologies, learn how to streamline their processes to improve accuracy and communication with stakeholders, enhance their skills in data analysis and management, analyse cost data, project schedules and performance metrics to make informed decisions.
With growing awareness of sustainability, quantity surveyors should be knowledgeable about green building practices, including energy-efficient design, new materials identification, and waste management. A carbon counting circular economy should be considered when whole-of-life costs are considered in cost-benefit analysis and sustainable options incorporated.
Quantity surveyors should stay up-to-date with the latest regulations, standards, and best practices in the construction industry to ensure compliance and in turn provide accurate cost advice to clients.
In addition to technical skills, quantity surveyors should develop soft skills such as communication, negotiation, and leadership. As the construction industry becomes more collaborative, quantity surveyors need to effectively communicate and negotiate with stakeholders, lead teams, and manage conflicts to achieve successful project outcomes.
The quantity surveyor has a vital role to play in the development and improvement in productivity of the Australian construction industry and is able and expected to make a contribution informed by the current state of the industry from time to time.
The role of the quantity surveyor in the Australian construction industry is particularly valuable in that the quantity surveyor has the accepted and traditional role of being independent, professional, and able to discharge their duties to the client in an honest, transparent, and disciplined manner. They occupy a unique role in the construction industry where their work is valuable to a number of participants, notwithstanding that they have been retained by only one participant, usually either the principal or the principal’s financier.
Quantity surveyors are required to act in an ethical manner consistent with the general standards of their profession and the expectations of the industry and the public. Further, the quantity surveyor is respected by their client as an independent source of disciplined, rational and practical expertise in the cost of works and all of its related aspects, and external stakeholders (subcontractors, suppliers, builders and other professionals), who will respect the construction cost that has been carried out by a senior, experienced and qualified quantity surveyor.
Inflation is currently a concern for all in Australia and particularly in the construction industry, which has experienced substantial and unexpected
cost increases in recent times and particularly over the last year. Industry must now operate in an unpredictable global environment – war in Ukraine, tensions in the Pacific and supply disruptions due to Covid have stressed the world economy and the world’s communities.
The recent budget outlined the government’s expectation that the housing crisis with a shortage of housing stock and escalation in house prices would be addressed by government investment and tax incentives.
Locally, there has been a high rate of insolvency in the construction industry. Quantity surveyors have a particular perspective on such events as the insolvency of a subcontractor or a main contractor leads to a cascading effect throughout all participants in the projects affected.
The quantity surveyor has a particular and accurate insight into the culture of contracts in the Australian construction industry. While there are a wide variety of contracts, the basic classification of contracts categorises:
1. Hard-dollar lump sum contracts
2. Cost-plus contracts
3. Contracts with rise and fall.
The quantity surveyor has the responsibility and role to recommend
"It is that background of volatility and uncertainty that the quantity surveyor can, and does often, make a significant contribution.
"
which of those particular contract forms are suitable for a particular project. It is necessary to assess the suitability of those contract forms accurately to prevent unexpected and unnecessary damage to the contractor or the principal in the case that the contractor is thrown into financial difficulty in the execution of the contract.
Accordingly, the quantity surveyor can be a “force for good” by recommending fair contracts that properly deliver a competitive and quality output for the principal but also do not expose the contractor and his subcontractors to unacceptable risks that may lead to insolvency. That insolvency necessarily entails gross waste in the destruction of productivity and technical innovation in the industry. Additionally, each insolvency usually means that the life savings of the personal participants is substantially reduced if not completely lost.
The quantity surveyor can ensure that the implementation of those contracts can be successfully achieved. They are often involved in costing projects progressively over the duration of the construction, from pre-feasibility to its final completion. Accordingly, the quantity surveyor is able to ensure that the contracts and their contractual risks are sensibly administered to the preservation of the industry and its capacity as well as the successful completion of a project. The quantity surveyor is often in a unique position to advise an owner or financier on appropriate adjustments, concessions, or arrangements that might alleviate some of the uncertainties which would otherwise fall to the other participants.
The quantity surveyor has the opportunity to be a powerful advocate for change improvement in the industry. The need in these circumstances for most contracts, if not all, to have suitable and sensible rise and fall provisions is obvious.
The present ills of the industry are almost directly traceable to the fact that a contractor has given a lump sum price for the work, where the costs that are going to be involved in those works are not able to be properly estimated and may rise by significant percentages during the course of the works.
Re-adjustment of those risks between the participants can lead to better and more successful projects for both parties. The quantity surveyor is, and should be, an advocate for fair and reasonable contracts for the industry to be productive and efficient and no participant is subject to the overwhelming risks of recent times.
The advocacy will need to be directed to:
• The financiers, who are expecting to protect their return and the investment they have made
• The principal and the expectations they have for the prompt delivery of a quality building and its efficient utilisation
• The contractor for making a sustainable contract that protects their employees and subcontractors and develops and maintains effective productive units that can deliver future projects competently.
Of course, the quantity surveyor must also advocate for the industry to ensure that those who would seek to retain the benefit of a rise and fall contract pass the benefits of the rise and fall to their
subcontractors and suppliers so that the whole industry is sustained.
The quantity surveyor could also advocate for the government to change the nature and rigidity of price provisions in government contracts to promote sensible contracting practices and more effective delivery of the industry’s outputs.
Quantity surveyors should realise and revel in the established and respected role that they have in the industry and also accept that they can be a force for good. There is much benefit to society as a whole with a construction industry that is better designed and able to deliver the productivity and efficiency which the community expects.
This article was written by the team at Doyles Construction Lawyers www.doylesconstructionlawyers.com
"The quantity surveyor has the opportunity to be a powerful advocate for change and improvement in the industry. "
Seminars, articles, and LinkedIn posts have become saturated with discussions of rise and fall clauses – the contractual mechanism to adjust a contract price when the costs of labour and materials fluctuate. This clause is by no means new, and we are experiencing its latest renaissance.
However, can an examination of this clause’s past tell us anything new?
Set out in this article is the simple and uncontroversial story of the history of rise and fall clauses in Australia. Like clockwork, they emerge in response to periods of high inflation and price uncertainty, often driven by war. As inflation falls and the market stabilises, rise and fall clauses fade into disuse.
But in researching this history, a second story emerged. History reveals our industry’s repeated struggle with the transition from low to high inflation periods and back again. This story, what it means, and what we can do about it is discussed below.
The takeaway message - plan for the transition phase.
The first reference to rise and fall clauses can be found unsurprisingly after the First World War and the subsequent housing boom. This boom was driven by the introduction of the War Homes Act, designed to assist returning servicemen build affordable homes. The instability of prices and the emergence of the clause is reported in the Cessnock Eagle and
South Maitland paper, which records: The uncertainty as to the future price makes it almost impossible to quote in any industry, but more especially in the iron and steel trade, without a sliding clause authorising the sellers to increase their prices if the cost of coal (or other raw materials) are increased on them.
And that:
An acute stage has been reached in the shortage of artisans in the building and construction trade, and this position is felt at Cessnock, as well as in the cities. Men in Sydney, it is stated, who have spent years in acquiring their craftsmanship, walk out of the building trade, and take jobs on the wharf or in other occupations where bodily strength is their main asset because the wages are better. On account of the future uncertainty of the markets and labour shortages and conditions, builders and contractors are not disposed to tender for work without certain conditions in the contract. These conditions include a rise or fall.¹
The Second World War saw this pattern repeat with another significant housing boom emerging after its end. Evidenced in a report by Hobart's Mercury Newspaper from the 13th of February 1947, the Tasmanian State Government opted to include rise and fall clauses as a means of encouraging tendering, its justification being that, "it is impossible to secure tenders for large works as contractors found it difficult to assess their future costs with the obscurity of the labour market".²
¹ ‘Building and construction jottings’, The Cessnock Eagle and South Maitland Recorder (NSW: 1913-1954), 5 December 1919, p. 2 accessed 3 February 2023, <https://nla.gov.au/nla.newsarticle99444713>.
² ‘State contracts to allow for cost rises’, The Mercury (Hobart, Tas: 1860-1954), 13 February 1947, p. 8, accessed 3 February 2023, <http://nla.gov.au/nla.news-article26396384>.
³ ‘A.C.T. builders cost changes in contracts’, The Canberra Times (ACT: 1926-1995), 3 May 1974, p. 9, accessed 3 February 2023, <http://nla.gov.au/nla.news-article110776449>.
It would be remiss to leave our history lesson here and suggest that only the exceptional conflicts of the first half of the twentieth century could drive such change. A similar result emerged from the 1970s oil crisis. Western oil production had peaked the decade prior, most notably in the United States in 1960, and there was a general decline in global per capita oil production. This left the Western world more reliant on oil from the Middle East and susceptible to disruptions to that supply, including the OAPEC embargo relating to the Yom Kippur War and changes in oil exports after the Iranian Revolution. These events led to massive petroleum shortages and rapid oil price inflation. This contributed to a decade of stagnant economic growth and price inflation. This unsurprisingly drove the re-emergence of rise and fall clauses, with The Canberra Times reporting on 3 May 1974 that "many Canberra builders are inserting rise and full clauses in contracts for building private houses, the move undertaken because of what the builders consider to be increasing uncertainty about future rises in the price of materials and wages".³
These examples clearly illustrate that instability in the prevailing state of the labour and materials markets leads to the construction industry demanding that rise and fall clauses are included in contracts.
But this does not paint the full picture.
There is an enlightening example from 1954. Now a decade after the disruptions caused by the Second World War, lump sum contracts were again returning as the primary means of contracting. A credit restriction policy, introduced by the commonwealth government as a means of lowering housing demand, occurred in tandem with a recession that had begun in June 1952.⁴ State and local governments began to act. The Western Australia State Housing Commission dropped the clause in late 1952⁵, closely followed by the Hobart City Council, which removed such clauses from its contracts in March of the following year.⁶ Simultaneously, the construction industry was locked in debate about the future of the clause.
In one corner was the Royal Australian Institute of Architects (RAIA), championing the owner’s position, the removal of rise and fall contracts. Opposite them was the Master Builders Federation of Australia (MBFA), defending the clause and the benefits it provided.
The RAIA’s arguments were well summarised by then president of the NSW chapter, Mr Moline, who stated, "Nothing did more harm to the building industry than contracts under which a client did not know the extent of his commitment".⁷ The position of the MBFA was well articulated by their resolution on the subject, from the 1954 MBFA Convention in Hobart, that "tenders for new works should be submitted only with the proviso that a rise and fall clause be included in the building contract".⁸ The MBFA argued that builders have two choices to cover themselves as a means of dealing with the risk of cost increases: the inclusion of a rise and fall clause; or, the loss of the tender. They questioned why the builder should be asked to gamble with their contracts, stating:
The gambler harms his client, the industry, and his fellow builders, because he destroys the stable basis of tenders and, to that extent, makes it impossible for architects to estimate the cost of a building. Every architect and building owner should aim to eliminate the gambler from the building industry.⁹
Unfortunately, the MBFA's protestations weren't sufficient, and rise and fall clauses faded amidst market stability and builders’ willingness to take on this risk again.
⁴ ‘Homes and building firm contracts are returning’, The Sydney Morning Herald, 16 December 1952, p. 7, accessed 3 February 2023, <http://nla.gov. au/nla.news-article18295140>.
⁵ ‘Rise and fall clause banned’, The Daily News, 9 January 1953, p. 8, accessed 3 February 2023, <http://nla.gov.au/nla.news-article266059045>.
⁶ ‘Fall Clauses for Council Contracts’, The Mercury, 22 April 1954, p. 17, accessed 3 February 2023, from <http://nla.gov.au/nla.newsarticle27209805>.
⁷ ‘Homes and building’, The Sydney Morning Herald, 2 November 1954, p. 10, accessed 3 February 2023, from <http://nla.gov.au/nla.newsarticle184545690>.
⁸ ‘Homes and building’, The Sydney Morning Herald, 7 December 1954, p. 11, accessed 3 February 2023, from <http://nla.gov.au/nla.newsarticle18458390>.
⁹ Ibid
If we are to accept history, whether a rise and fall clause is present in a contract depends mainly on the inflationary pressure at the time of contracting. In periods of stability, there will be no rise and fall clause; there will be in times of high instability.
This means that our contracts contain an implicit assumption that inflation will behave consistently from the time the contract is written.
The consequence of this assumption is that our contracts fail to handle inflation risk during a time when the market is transitioning from low to high inflation markets, or vice versa.
For the most part, our contracts do not plan for the transition phase and our industry consistently suffers for it.
This requires us to consider strategies that can effectively navigate these transition states.
Here are four possible strategies presented in increasing levels of effectiveness:
1. Build structures into your contract that identify and manage risks early to resolve those issues without a formal dispute. This is commonly seen in early warning notices and dispute avoidance boards, such as those found in the NEC and FIDIC suites. This does not actually remove the risk but can at least create a pathway for its identification and resolution.
2. Owners can choose to be first movers on the issue and provide relief when circumstances change. The Australian Department of Defence exemplified this through the introduction of a pandemic relief clause into its Head Works contract, HC-1 2003, in 2020. While owners legally have the benefit of a lump sum price, they are still
faced, in the absence of action, with the substantial risk of claims from the contractor who must find some means of recovering loss. Or worse still, the owner faces the possibility of an incomplete project if the builder becomes insolvent.
3. Always include a rise and fall clause within the contract. The argument for this is the same as that of the MBFA conclusion in 1954 – the owner pays one way or another. It is beyond the scope of this article to discuss the drafting of these clauses, however, it is worth noting that such clauses are found in most industry standard contract suites, including NEC, GC21, and the FIDIC Yellow Book.
4. Use collaborative contracting models. These models contain more nuanced approaches to risk identification, management and mitigation, and the financial models can treat the risk in more sophisticatedly through the pain share/gain share and adjustment event mechanisms.
Rise and fall contracts have proven necessary at times of high inflationary risk. As inflation stabilises, these clauses slowly fade away.
What we don’t manage well is this risk when the market shifts between stability and instability and our contracts become incompatible with the prevailing market. Have you got a plan for the transition phase?
This article is based on a presentation given by Kiri Parr on 16 February 2023 for the Australian Institute of Quantity Surveyors and sponsored by Bond University.
When considering who owns the float, one first must understand the various definitions of 'float' typically associated with construction projects. Secondly, one must understand the applicable contractual clause relating to claiming an extension of time.
Most people will associate float with the CPM (critical path method) of scheduling. The critical path is determined by the sequence of activities within a program that dictates the overall program duration, i.e., the 'critical path' has zero total floats.
However, there are several other applicable definitions of float, namely:
• Free float: the amount of time an activity can be delayed without impacting upon the start time of its immediate successive activities.
• Interfering float: the difference between the total float and free float.
• Internal float: built-in float between the planned start and completion dates within the program (time contingency).
• External float: float between the Date for Completion and the Date of Completion.
The consideration of 'external float' raises the question of 'who owns the float?'.
The contractor may argue that it 'owns' the float because they plan how the work should be carried out and in what sequence. They may also allow a 'buffer' or contingency between its likely Date of Completion and the Date for Completion.
Suppose, therefore, there is a delay to the contractor's progress for which the contractor is not responsible¹ and the
¹ And three-part chain of causation is satisfied.
time contingency has not been fully exhausted. In this case, the contractor may contend that they are entitled to an extension of time, even if the delay to progress did not result in the Date for Completion being impacted. Rather, the delay merely 'eroded' its planned time contingency. In this scenario, the contractor is asserting ownership of the float.
On the other hand, the employer may consider that the contractor has no contractual relief for being prevented from completing the works before the contractual Date for Completion. Meaning, the contractor is not entitled to an extension of time unless the excusable delay results in the Date for Completion being impacted. In this scenario, the project (i.e., the employer) is claiming ownership of the float.
The expression 'float' is rarely, if ever, defined in the conditions of the contract. Where the wording of the extension of time clause is such that an extension of time is only to be granted if the employer delays completion beyond the Date for Completion, then the likely effect of that wording is that all external float must be 'consumed' before an extension of time will be due.
Suppose the wording of the extension of time clause is such that an extension of time will be due whenever the employer delay event adversely impacts the Date for Completion date. In that case, the external float will not be available for the benefit of the employer in the event of an employer related delay.
The SCL Protocol maintains the following regarding float ‘ownership’:
"Unless there is express provision to the contrary in the contract, where there is remaining total float in the program at the time of an Employer Risk Event, an EOT should only be granted to the extent that the Employer Delay is predicted to reduce to below zero the total float on the critical path affected by the Employer Delay to Completion".²
In other words, unless the contract says otherwise, the float is owned by the project. The following unamended (Australian) standard forms of contract demonstrate the specific wording regarding (external) float 'ownership'. All three examples deem the contractor to 'own the float'.
In respect of an extension of time claim, in determining whether the contractor is or will be delayed in reaching Practical Completion regard shall not be had to:
1. Whether the contractor can reach Practical Completion by the Date for Practical Completion without an extension of time; Whether the contractor can, by committing extra resources or incurring extra expenditure, make up the time lost.
In assessing each EOT, the superintendent shall disregard questions of whether:
1. WUC can nevertheless reach Practical Completion without an EOT; or
2. The contractor can accelerate, but shall have regard to what prevention and mitigation of the delay has not been affected by the contractor.
In determining whether the contractor is or will be delayed in reaching Practical Completion, regard shall not be had to:
1. Whether the contractor can reach Practical Completion by the Date for Practical Completion without an extension of time; or
2. Whether the contractor can, by committing extra resources or incurring extra expenditure, make up the time lost. The three examples of time clauses entitle the contractor to claim for an extension of time to the Date for Completion regardless of the status of the works at the time of the delaying event.
For example, a contractor is contracted to a November Date for Completion. However, the works are progressing quicker than planned and an earlier Date of Completion of some three months sooner is reported, in August. The employer has accepted the contractor's progress and approved the updated contractor's program. A variation direction has been demonstrated to have impacted the program by a month, meaning the Date of Completion is likely to be September.
Is the contractor entitled to an extension of time to the Date for PC?
Yes. The contractor 'owns' the float. The contractor has made the time and is entitled to use the time, i.e., what if a subsequent contractor delay event meant that all that float was subsequently consumed?
1. Read and fully understand the contract.
2. A claim for an extension of time (and its proximate impact) should be made at the time the delay event occurs.
3. Program float can sometimes be misinterpreted as a method of planning contingency into a project. However, since there is some ambiguity between who actually ‘owns’ the float, it is best practice to determine program contingency and delay allowances and drawdown on the allowances as the pre-determined delays, such as the effects of weather, are realised. This can be facilitated by extending planned discrete activity durations or having a pre-determined delay allowance between the forecast Date of Completion and the Date for Completion.
4. Avoid using internal ‘target’ programs in parallel with the project program. This is unnecessary, even if the project ‘owns’ the float, if proper delay allowances and contingencies have been ‘built’ into the program (internal float). This practice also makes it difficult to prove causation, as only the approved project program can be used to demonstrate entitlement to an extension of time.
"The float is the contractor's opportunity."
Adjudication is intended to be a nonbinding determination of a progress payment dispute, but unfortunately, that intent has not translated well into the various Security of Payment (SOP) Acts and the statutory adjudication regime as a whole.
The SOP Acts are reasonably consistent in describing the object of the legislation. The primary objective is to provide an effective and fair process for securing payments, to help people working in building and construction be paid for the work they do, and to ensure they receive, and can recover, progress payments.
If the process was genuinely straightforward, effective, and fair; then, of all the professions, it is the quantity surveyor who would be best suited to carry out the role of adjudicator. However, that is not the case, and effectiveness and fairness have been overtaken by increasingly onerous legal and administrative complexities which may serve the purposes of the adjudication industry, but not the small subcontractor trying to get paid.
On a general note, adjudication is just an example of how legal-based complexity has infiltrated the otherwise very straightforward quantity surveying/ commercial function, to the point where the complex now seems to be preferred to the simple and straightforward.
Getting back to adjudication, let’s consider for a moment the adjudicator’s jurisdiction, i.e., the adjudicator’s power and authority. Over the years, the individual SOP Acts have been
augmented by numerous case decisions and clarifications, to the point now where it places quite arduous constraints on what an adjudicator can and can't do.
To overcome this problem, some legislators have granted the adjudicator the power to rule on their own jurisdiction. But, whilst well-meaning, it has unfortunately made the situation worse. Most adjudicators will say that more than 50% of their time is taken up dealing with jurisdictional matters because of the numerous and varied issues that have developed. This can result in the failure of an otherwise meritorious payment claim, because the small subcontractor claimant has no knowledge of this, and why should they? The failure rate because of jurisdictional issues is very high.
In my humble opinion, the whole sorry mess needs to be scrapped and started again with a blank canvas. Alternatively, a regime for small disputes should be considered (based on a value ceiling), which would strip away all this overly complex legal/administrative jargon, to reengage the small subcontractor.
Unfortunately, the realist (some call cynic) in me knows the chances of that are very remote because there’s too much vested interest in maintaining the status quo. I often liken myself to the small child in the fable of 'The Emperor’s New Clothes', but with a different ending! In the meantime, all that we as a profession can do is try to assist the small subcontractor to first manage their commercial/contractual issues to hopefully avoid escalation to dispute, and secondly, if unavoidable, assist them to navigate the adjudication process.
In preparing this guide, I’ve tried to condense and simplify the numerous issues. But, due to their very nature, that’s not an easy task, especially as each dispute is unique when considering the contractual and factual issues and their interface.
• Prior to an adjudication application, either of the following must occur:
a) the due date for payment has passed with no payment, or
b) the payment schedule indicates a lesser amount.
• If the payment claim or adjudication application is deficient, or the calculation of dates is flawed, the application risks failure regardless of its merits.
• If in doubt, I recommend to:
a) wait until after the due date for payment
b) utilise SOP Act time periods to calculate dates
c) base calculations on business days, not calendar days.
• The application must be consistent with the payment claim, do not add additional items.
• An adjudicator decides a payment dispute based only on the parties’ submissions.
• An adjudicator is not required to enquire, nor consider what may or may not be fair.
• If there is no valid payment schedule, do not assume that an adjudicator will determine that the payment claim will be paid in full.
• There is no such thing as too much information.
• Demonstrate with evidence that the work has been completed (e.g., photographs).
• Provide details of how each figure has been calculated, keeping in mind any original quotes, and provide all applicable receipts/timesheets.
• For changes/variations, describe the date and manner by which it was requested/instructed (e.g., verbally, email).
• Some states require the applicable SOP Act to be written on the claim.
• This is a prime example of unnecessary complexity.
• It marks the day when one is allowed to claim payment and is usually the end of the month.
• Once a reference date has been ‘used’ on a previous claim, it ‘expires’, and any subsequent claim based on the same date is likely void for the purposes of adjudication.
• Respond quickly, do not delay.
• State how much one is prepared to pay on an itemised basis and detail the reasons why it is less than claimed. The above merely scratches the surface and therefore I reluctantly recommend that one should seek specialist advice if one is contemplating adjudication. However, this information may aid the small subcontractor in posing more focused questions about their dispute, and thereby retain some control over the costs of such advice.
As the global community confronts the repercussions of climate change, the construction sector is increasingly urged to adopt sustainable and environmentally conscious practices. Green building certification systems are crucial in establishing industry benchmarks, but selecting the most appropriate standard for a specific region or project can be challenging due to the variety of international options. In this commentary, we compare three key green building certification standards relevant to Australia, New Zealand, the Middle East, and Southeast Asia: Green Star, Green Mark, and Estidama. Our goal is to discuss the advantages and disadvantages of each system and advocate for a harmonisation pathway that benefits the construction industry in these regions.
Introduced by the Green Building Council of Australia (GBCA) in 2003, Green Star is a voluntary certification system that evaluates the environmental impact of buildings and communities in Australia and New Zealand. The system encompasses nine categories: management, indoor environment quality,
energy, transport, water, materials, land use and ecology, emissions, and innovation.¹ Green Star's regional focus ensures criteria are tailored to the distinctive environmental challenges faced by Australia and New Zealand, such as water scarcity and extreme weather events.²
However, Green Star's regional focus can also be viewed as a limitation, since it may not be as applicable to projects in other parts of the world, including the Middle East and Southeast Asia. Moreover, it has been criticised for its complexity and high compliance costs.³ While Green Star has significantly contributed to promoting sustainability in the Australian and New Zealand construction industry, there is potential for improvement in its accessibility and applicability to other regions.
Initiated in 2005 by the Building and Construction Authority (BCA) of Singapore, the Green Mark certification system promotes sustainable design and construction practices in Southeast Asia.⁴ The system evaluates buildings based on five key criteria: energy efficiency, water efficiency, environmental protection, indoor environmental quality, and innovation.⁵ Green Mark's adaptability to the region's tropical climate and its
¹GBCA 2021, Green Star, Green Building Council of Australia, accessed 1 March 2023, <https:// new.gbca.org.au/green-star/>.
²Szokolay, S.V. 2008, Introduction to Architectural Science: The Basis of Sustainable Design, Architectural Press, Oxford.
³Sargent, P., Brophy, V., Cohen, B. & Enright, B. 2012, ‘Green building rating tools: Comparative analysis’, Building Research & Information, vol. 40, no. 3, pp. 260-270.
⁴BCA 2021, BCA Green Mark, Building and Construction Authority, accessed 2023, <https://www. bca.gov.sg/greenmark/>.
⁵BCA 2021, BCA Green Mark, Building and Construction Authority, accessed 2023, <https://www. bca.gov.sg/greenmark/>.
focus on energy and water conservation are especially relevant in Southeast Asia, where rapid urbanisation and limited resources have led to increased environmental pressures.⁶
On the other hand, Green Mark has faced some critiques for not being quite as all-encompassing as other certification systems like Green Star or LEED.⁷ Moreover, its strong focus on the Southeast Asian market may not be suitable for application in other regions like the Middle East, Australia, or New Zealand.
Green Mark has undoubtedly played a key role in tackling the distinctive climate-related challenges faced by Southeast Asian nations. However, by adopting a more comprehensive approach that encompasses various aspects of sustainability, its impact could be significantly amplified.
Estidama, meaning “sustainability” in Arabic, is a green building certification system developed by the Abu Dhabi Urban Planning Council in 2010.⁸
Designed to address the distinct environmental and cultural context of the Middle East and North Africa (MENA) region, Estidama focuses on four pillars:
environmental, economic, social, and cultural sustainability.⁹ Its strengths lie in its comprehensive approach, which includes not only the physical aspects of a building but also the well-being of its occupants and the surrounding community.¹⁰ Furthermore, Estidama places significant emphasis on water conservation and energy efficiency, which are particularly relevant in the water-scarce and energy-intensive MENA region.¹¹
However, Estidama's regional focus may limit its applicability to projects outside the MENA region, including those in Australia, New Zealand, and Southeast Asia. Additionally, its relatively recent development means it may not be as widely recognised or understood as other, more established certification systems. Despite these limitations, Estidama presents a unique and comprehensive approach to sustainable construction in the Middle East, and greater efforts should be made to raise awareness and promote its adoption in other regions.
While each of these green building certification systems has its strengths and weaknesses, their proliferation has led to a fragmented landscape that
can be confusing and challenging for construction professionals and project owners.¹² To ensure that sustainable construction practices are adopted more widely in Australia, New Zealand, the Middle East, and Southeast Asia, a harmonised approach that combines the best elements of each system is recommended.
This harmonisation could take the form of a regional certification system that addresses the specific environmental and cultural challenges of each area while incorporating international best practices. For example, a certification system for Southeast Asia could combine elements of Green Star's comprehensive assessment framework with Green Mark's focus on tropical climate adaptations. Similarly, a certification system for the Middle East could integrate Estidama's holistic approach to sustainability with best practices from Green Star and Green Mark in areas such as energy efficiency and materials selection.
Alternatively, existing certification systems could collaborate to create a unified set of criteria and assessment methodologies that are globally recognised and applicable across different regions. This approach would involve identifying commonalities and best practices from Green Star, Green
⁶Sovacool, B. K. & D'Agostino, A. L. 2012, ‘The socio-technical barriers to Solar Home Systems (SHS) in Papua New Guinea: "Choosing pigs, prostitutes, and poker chips over panels"’, Energy Policy, vol. 47, pp. 200-210.
⁷Chen, Y., Burnett, J. & Chau, C. K. 2010, ‘Analysis of the design approach for green building certification in Hong Kong’, Facilities, vol. 28, no. 13/14, pp. 657-670.
⁸Department of Municipalities and Transport 2023, ‘Estidama Program’, Abu Dhabi Government, accessed 3 May 2023, <https://pages.dmt.gov.ae/ en/Urban-Planning/Estidama-Program>.
⁹Department of Municipalities and Transport 2023, ‘Estidama Program’, Abu Dhabi Government, accessed 3 May 2023, <https://pages.dmt.gov.ae/ en/Urban-Planning/Estidama-Program>.
¹⁰AlWaer, H. & Sibley, M. 2013, ‘An overview of the Estidama system and its applications’, Intelligent Buildings International, vol. 5, no. 3, pp. 142-155. ¹¹Elsheshtawy, Y. 2016, ‘Sustainable development and urban growth in the Gulf States’, In Sustainable Development and Planning VIII, vol. 206, pp. 605-616.
¹²Fowler, K. M. & Rauch, E. M. 2006, Sustainable Building Rating Systems Summary, Pacific Northwest National Laboratory (PNNL), Richland, WA.
Mark, and Estidama, and incorporating them into a shared framework that can be adapted to the specific needs of each region. Such a framework would not only streamline the certification process, but also facilitate knowledge sharing and collaboration among construction professionals, ultimately driving greater adoption of sustainable practices.
In conclusion, the global community must address the urgent need for sustainable and environmentally responsible practices in the construction industry. Green building certification systems such as Green Star, Green Mark, and Estidama provide valuable benchmarks for sustainable construction in their respective regions. However, the construction industry in Australia, New Zealand, the Middle East, and Southeast Asia would benefit from a harmonised approach that combines the strengths of each system while addressing the unique challenges faced by each region. By working towards a unified certification framework, we can collectively promote a more sustainable future for the built environment and contribute to global efforts to mitigate the impacts of climate change.
AlWaer, H. & Sibley, M. 2013, ‘An overview of the Estidama system and its applications’, Intelligent Buildings International, vol. 5, no.3, pp. 142-155.
BCA 2021, BCA Green Mark, Building and Construction Authority, accessed 2023, <https://www.bca.gov.sg/greenmark/>.
Chen, Y., Burnett, J. & Chau, C. K. 2010, ‘Analysis of the design approach for green building certification in Hong Kong’, Facilities, vol. 28, no. 13/14, pp. 657-670.
Department of Municipalities and Transport 2023, ‘Estidama Program’, Abu Dhabi Government, accessed 3 May 2023, <https://pages.dmt.gov.ae/en/ Urban-Planning/Estidama-Program>.
Elsheshtawy, Y. 2016, ‘Sustainable development and urban growth in the Gulf States’, In Sustainable Development and Planning VIII, vol. 206, pp. 605-616.
Fowler, K. M. & Rauch, E. M. 2006, Sustainable Building Rating Systems Summary, Pacific Northwest National Laboratory (PNNL), Richland, Washington, USA.
GBCA 2021, Green Star, Green Building Council of Australia, accessed 1 March 2023, <https://new.gbca.org.au/greenstar/>.
Sargent, P., Brophy, V., Cohen, B. & Enright, B. 2012, ‘Green building rating tools: Comparative analysis’, Building Research & Information, vol. 40, no. 3, pp. 260-270.
Sovacool, B. K. & D'Agostino, A. L. 2012, ‘The socio-technical barriers to Solar Home Systems (SHS) in Papua New Guinea: "Choosing pigs, prostitutes, and poker chips over panels"’, Energy Policy, vol. 47, pp. 200-210.
Szokolay, S.V. 2008, Introduction to Architectural Science: The Basis of Sustainable Design, Architectural Press, Oxford.
This article was written by Loc Tri Nguyen
The use of risk estimating statistical packages is a common method of avoiding the many weaknesses of single value estimating. Many quantity surveyors find themselves participating in risk workshops where risks and occasional opportunities are evaluated. Workshop leaders and participants share the responsibility for creating a mathematical risk model that closely reflects the scale and extent of the anticipated risks and uncertainties. While participants share the responsibility, they are usually at a disadvantage, being unable to control the direction of the workshop and perhaps unable to interrogate the legitimacy of the values being adopted. To address this issue and “level the playing field”, I have prepared a risk estimating Excel workbook (“BasicRiskModel”) with a suite of User Defined Functions for the commonly used triangular and PERT distributions and the ability to handle multiple iterations of a risk model. This is available to download via the link at the end of this article.
Risk modelling typically uses three-point estimating and a probability profile to calculate the range of possible final outturn costs, and from this determines the risk contingency that should be applied at any probability level. My experience in reviewing risk models had lead me to the conclusion that a number of modellers have not correctly understood the nature of certain types of risk events.
One example is the failure to distinguish between the risk treatment of events such as “discovering asbestos during demolition,” and “finding rock during excavation”. At first sight they appear to be similar, but while the first is a “normal” event risk where likelihood and consequence are assessed independently, the rock risk is an example of a cost which occurs when a potential threat (the possible rock depth) crosses a particular threshold (the bottom of the excavation).
To better understand the nature of the rock and similar risks it is probably simpler to consider a more easily analysed situation, and for this I chose the risk of a critical piece of equipment not being delivered in time. Making the example concrete, suppose that the manufacturer has given a range of possible dates spanning a 10week period with the expected date somewhere in the middle of the range and the latest possible delivery date 15 days past our deadline. Since we have decided that the risk profile of the delivery time is unskewed, we may calculate the most likely arrival time as 20 days prior to the deadline. (70 days / 2) – 15 days and the earliest date is 55 days prior (15 days – 70 days). A risk profile of this uncertainty could be modelled with a minimum (Min) -55 days, most likely (ML) -20 days and maximum (Max) +15 days. If delays cost $10,000 per day, then, using a Beta PERT risk profile, this risk could take the form = RiskPert(-550,000, -200,000, +150,000). Clearly this formula would frequently return invalid negative values, but when modified to =MAX(0, RiskPert(-550,000, -200,000, +150,000)) the formula will replace all negative results with zeros.
The distinguishing feature of this risk is that it does not require a separately estimated likelihood since the frequency of occurrence will equal the frequency of positive values. It is this feature that requires “Threshold” risks to be treated differently from “normal” risks. Given the maximum cost and the skew of the threat distribution (commonly unskewed), there is a direct relationship between the most likely value, the minimum value and the likelihood. It is therefore possible to create the risk profile based on the maximum value, the skew and either the assessed percentage likelihood or the assessed positive ML value.
The rock risk is similar as the cost occurs only when the risk profile of the rock depth extends above the lowest excavation depth. Another example is the risk of flooding when a river breaches a levee. The risk occurs only when an underlying threat passes a certain threshold.
In these cases, the risk may be represented in the model, in the normal format, with a percentage likelihood and the three values, but truncated at zero. The calculation for this is based on an iterative solution which is cumbersome in the context of a risk workshop. The “BasicRiskModel” contains a worksheet which calculates the values automatically using the Max, Skew and either the assessed percentage likelihood or the positive ML value.
Estimate items are often ranged as a percentage either side of the ML value. One commonly recommended technique to assess these percentages, which avoids the need to determine the extreme values at which possibility fades into impossibility, is to allow the workshop to instead assess upper and lower limits where there is still a 10% chance that higher or lower values are possible. This can be useful for estimate items with a more or less accurately determined central ML value and where the ranges are typically less than those found with risk events. Even with estimate items, participants may not be able to assess 10% with any accuracy or understand the implications of their choices.
Risk software must use the estimates and the chosen risk profile to calculate the
"...a number of modellers have not correctly understood the nature of certain types of risk events."
actual extremes, and although there may be agreement about the 10% values, that agreement may not survive knowledge of the real minimum and maximum values that they have unknowingly created. This method is frequently promoted as avoiding the discomfort felt by estimators and engineers in assessing real extreme values and, to avoid unsettling them, the actual limits are not revealed. I suspect that most participants are unaware that increasing the P-90 estimate will reduce the extreme minimum that their P-10 estimate produces. In the case of risk events, where ranges are typically quite wide, this method of assessment can lead to unrealistic results. I have seen numerous examples of event risks using P-10 and P-90 values which result in the possibility of clearly invalid negative results. As an example, a PERT risk distribution of Min $100,000; ML $300,000; Max $500,000, with a 10% possibility that the actual cost could be lower or higher resolves into an extreme minimum below negative $94,000. While the possibility of cost savings may be a clear sign of error, other values might also be considered unreasonable were they known. It is for this reason that I consider such techniques unsuitable for event risks. Also, since threshold event risks and many others will require zero or near zero minimums, this method can never be used in association with such risks.
It would be better to allow participants to know what values the risk software will create. The “BasicRiskModel” contains User Defined Functions that allow users to interrogate the assumptions made at
the workshop. It will allow attendees to understand the true range of any costs which are assessed at the P-10 and P-90 or any other percentage values.
distributions are quite strongly positively skewed and it may well be that outputs at all P-values are substantially increased by the use of the triangular profile.
I have the impression that many of the event risks are being assessed by first guessing an ML value and then putting percentages either side of this value. This is generally unsuited to event risks where the extreme values may not have the same dependence on the most likely value. Participants should always be cautious with minimum values and question why they cannot be lower and still be possible. In my opinion, it is more reliable to assess these risks by first assessing the Max value, then the Min value (which is often at or close to zero), and finally deciding where, within this range, the ML value lies, and furthermore not confusing it with the average value as there is a significant difference when distributions are heavily skewed.
Regarding the choice between triangular or beta PERT distributions, triangular is often chosen based on its reduced emphasis on the ML value, but note that the corresponding increased emphasis on the extremes leads to slightly higher P-95 values when distributions are unskewed. This would be an unusual situation as most
Some commercial statistical programs provide a modified beta PERT with a variable “confidence” index. This is also available in the Excel workbook “BasicRiskModel”. Lowering the index when distributions are skewed will result in generally higher P-values. It should also be noted that, when using a modified beta PERT, increasing the “confidence” index has the effect of increasing the difference between the estimated P-10 and P-90 values and the actual extremes of individual items.
To navigate Microsoft’s attempts to protect computers from harmful viruses in .xlsb workbooks created by unknown providers, the following instructions may assist.
The download is a zipped file. Copy it to a folder, right click the file, select Properties and under the General tab, tick “Unblock” then “Apply”. Open the file and click "Enable Macros". Note that your Trust Centre options should be set to “Enable all Macros” and “Allow Trusted Locations”. If you have any difficulties, please email the author on the temporary address, byc.xjk@gmail.com
This article was written by Bary Yeldham AAIQS (Ret.), regarding his developed Excel workbook which can be downloaded via Dropbox (bit.ly/3LoKfj1).
"With a better-informed workshop, many of the errors which creep into risk models may be avoided."
The Australian construction sector adds significantly to the emission of greenhouse gases (GHG), This is primarily due to the release of carbon dioxide from cement-based materials used in construction. Due to the significant impact of the construction sector on the environment, creating new materials with lower environmental impact has become a crucial and pressing matter. One possible approach is to minimise the use of non-renewable resources. For example, in the context of structural concrete, using recycled aggregates from construction and demolition waste has been explored as a potential replacement for natural aggregates.
At present, most constructed spaces utilise concrete, which mainly consists of cement (typically Portland cement), aggregates, and water. In order to produce cement, a binding agent is necessary, which is typically lime-based. There are two major sources of GHGs during the manufacture of cement. Firstly, carbonation happens during the heating of limestone to produce lime, wherein calcium carbonate is transformed into calcium oxide and CO2 is released in the process. This procedure is inevitable and accounts for approximately 55% of greenhouse gas emissions.
The second cause of GHG emissions is the energy required to heat the kiln for producing lime. Most of this energy comes from fossil fuels and accounts for 32% of the total GHG emissions. Together, these procedures contribute to 87% of the GHG emissions produced by the construction sector, which, as mentioned earlier, represents 18% of the total national GHG emissions. Substituting bio-based materials for concrete requires significantly
less lime, typically only up to 21.4%, whereas concrete can contain more than 45% lime. Carbon sequestering materials and technology can be used as a decarbonising technique for the built environment. Bio-based materials improve energy performance in the built environment in comparison to using conventional materials. One such technology is the replacement of existing materials with bio-based alternatives.
Hempcrete is one of these materials. It is a bio-based constructive medium of a mix of hemp shivs, lime, sand, and water. The hemp plant sequesters CO2 during its growth through photosynthesis, and when harvested and processed into hemp shivs and hempcrete, it stores the biogenic carbon. According to the Australian Hemp Masonry Company, hempcrete has a lower carbon footprint
than conventional materials, high sound absorption, high moisture buffer capacity, excellent thermal insulation properties and is fire resistant.
Hempcrete can be used in three different ways: pre-made bricks, a coarse mixture for packing, or a liquid mixture for spraying. Using pre-made bricks is a dry method for building with hempcrete while packing and spraying require mixing the raw materials into a liquid mixture that dries on site. The dry method is suitable for retrofitting existing structures since the blocks are made uniformly and can match traditional masonry techniques. On the other hand, the wet methods are more expensive and less efficient for retrofitting and are better suited for new structures since they are applied on-site and become part of the structure.
However, this novel material is still incompletely researched, especially in the Australian context.
In Australia, most of the current Hempcrete projects use the method of mixing raw materials and tamping. This involves layering the mixed Hempcrete into a formwork and compressing it by hand with mallets. The process is repeated as the lower layers set and the formwork is moved up to add more Hempcrete layers until a wall is formed over several days.
Life cycle assessments (LCAs) are scientific evaluations that measure the environmental impact of products throughout their lifecycles. Previous LCAs have found that to reduce carbon emissions using hempcrete, it is necessary to transition away from lime binders, although research on alternative binders is currently insufficient. LCAs have shown that hempcrete has clear advantages in terms of embodied energy compared to traditional materials and similar thermal properties to concrete with similar densities. Hempcrete also has a net carbon-negative impact as it stores more carbon than it produces during manufacturing. However, due to the lack of industry standardisation, carbon storage levels in hempcrete vary depending on its composition during global production, with current estimates ranging from 35 to 87 kg of carbon per square metre of 250mm thick blocks. Further carbon reduction can be achieved by improving the manufacturing process and reducing the amount of cement used. In-situ carbonation of hydraulic binders can lead to additional carbon sequestration of 13.15 kg of carbon dioxide per square metre of hempcrete. Hempcrete's ability to sequester carbon is impressive and can contribute to carbon-neutral construction by replacing carbon-intensive materials.
Additionally, the hygrothermal properties of hempcrete can potentially reduce building energy consumption. A study in Canada showed that the insulative properties of hempcrete could decrease heating and cooling energy consumption by 10% and 37%, respectively, compared to expanded polystyrene (EPS). This reduction in energy consumption is particularly attractive for the Australian domestic market, where heating and cooling homes account for 20% and 50% of energy consumption, respectively. Reducing electricity consumption for heating and cooling could have significant flow-on effects on the Australian carbon footprint, as the country relies heavily on coal-powered energy.
Hempcrete’s positive attributes contribute to low environmental impacts, healthy indoor living, and energy savings. The thermal regulating properties can reduce heating and cooling requirements, promoting the construction sector to shift to energy-efficient buildings. Limiting the use of energy resources contributes to healthier and more environmentally sustainable buildings throughout their life cycles by positively impacting human health and the environment.
Hempcrete’s positive attributes, as listed in the table below.
Carbon footprint
Similar to other new technologies, there is insufficient long-term information available regarding hempcrete and other bio-based materials. This poses a concern as the lifespan and robustness of in-situ hempcrete are not widely known. However, this is changing as we at UTS are evaluating the performance of hempcrete over time, providing long-term data where degradation owing to age is likely to become apparent.
This will involve conducting experiments to measure indoor environmental quality parameters of scaled-down structures: cast-in-situ hempcrete; and prefabricated hempcrete panels. This will aim to measure and compare the performance of hempcrete production alternatives in terms of indoor environmental quality, to demonstrate the importance of developing panels meeting the desired criteria. To optimise the design considerations of hempcrete production alternatives, we are collecting information regarding the packaging, transportation logistics, installation, and disassembly at the end of the building use. This will contribute to scaling up the production of hempcrete which will promote the abundance of ‘green’ buildings, with the results combined aimed at decarbonising the built environment.
Negative carbon footprint due to biogenic CO2 uptake during hemp growth and to CO2 uptake by carbonation
Sound absorption coefficient of about 0.6 Moisture Buffer Value (MBV) Good moisture buffer 'value (MBV) of 2 g/ (m².%RH)
Acoustic performance
Thermal capacity/Insulation R-1.25 per inch to R-2.3 per inch for low (200 kg/ m³) to medium (400 kg/m³) density wall insulation mixes.
Fire resistance
Good reaction to fire (class “C - s2 - d0”) according to EN 13501-1
Dr Peter Irga is a Senior Lecturer researching the integration of hempcrete and green walls and green roofs into the built environment to maximise their combined effects. Holistically, his work aims to demonstrate that green infrastructure provides our cities with not only natural beauty, but also happier and healthier people.
Professor Sara Wilkinson is a chartered building surveyor and Australia’s first female Professor of Property. Her transdisciplinary research program sits at the intersection of sustainability, urban development and transformation, with a focus on green cities and preparing our urban environments for the challenges of climate change.
Flora Myrto Georgakopoulos is a PhD Candidate in the School of Built Environment at the University of Technology, Sydney. She is conducting research on sustainable construction, including prefabrication, modularity, and the use of renewable materials and greenery. She strives to develop ideas and solutions for healthy living spaces that form circular economy and carbon neutral patterns.
THE BUILDING COST INDEX IS PUBLISHED IN THE PRINT VERSION OF THE BUILDING ENVIRONMENT ECONOMIST.
IT CONTAINS DATA THAT CAN BE USED AS A PREDICTOR FOR THE ESTIMATED TIMES FOR DESIGN AND CONSTRUCTION AND INCLUDES A SUMMARY OF THE PAST, PRESENT AND ESTIMATED FUTURE CONSTRUCTION COSTS.