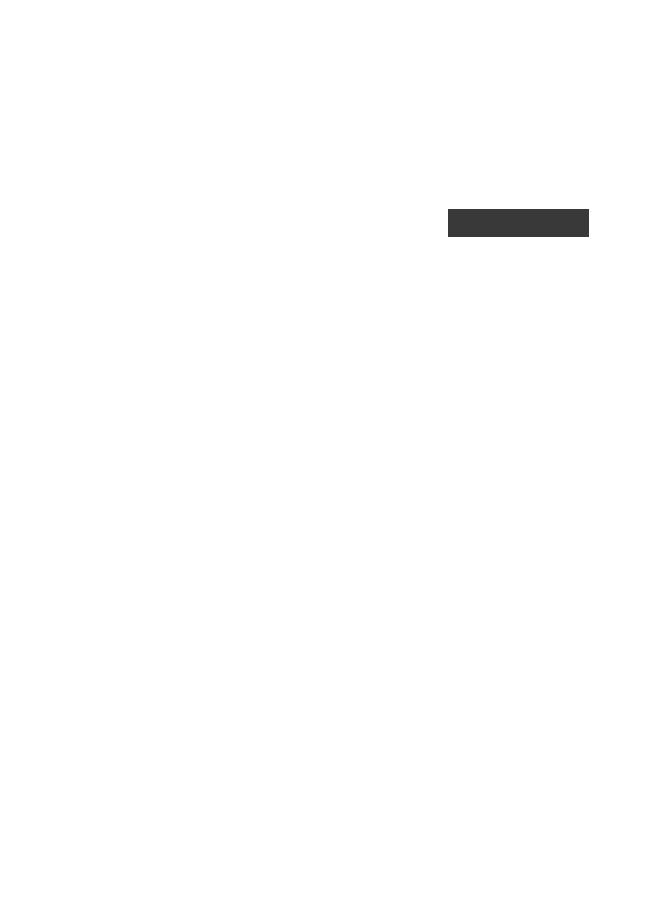
6 minute read
REMARKABLE RIESLINGS
from HVACR News June-July 2023
by AIRAH
2015 The Florita Riesling Cellar Release
Spanish for “little flower”, the Florita riesling was first released in 2004 by Jim Barry Wines. This micro batch riesling is made from grapes hand selected from individual rows. Its best fruit comes from vines planted in shallow loamy soils. The vineyard also has good air drainage, which alleviates the risk of frost.
Advertisement
2022 SINGLE VINEYARD Mc KAY’S RIESLING
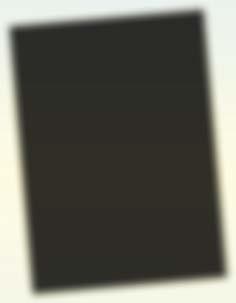
Each year, Jim Barry Wines identifies distinctive parcels of fruit that reflect the vineyard in which they are grown. This small‑batch project allows it to create unique, vintage specific wines that highlight the best fruit from vineyards owned by the Barry family.
sun and alkaline siltstone below loamy topsoil combine to create an ideal environment for growing intensely flavoured, finely structured rieslings. These vineyards have produced numerous award‑winning vintages, including the 2022 Florita and Lodge Hill Riesling vintages. The family’s dedication to the development and promotion of the variety also led to it being
This riesling was sourced from the McKay’s Vineyard at Watervale and picked slightly later than usual to deliver a more generous and opulent style. A small parcel underwent cool fermentation in aged French barrels to enhance the texture of the wine.
2022 Watervale Riesling
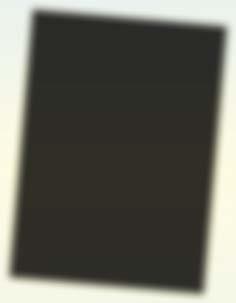
Located 15km south of the Clare township, the tiny village of Watervale is nestled in South Australia’s Clare Valley and is internationally renowned for the quality of its rieslings.
A consistently awarded wine since its first release in 1974, the Watervale riesling is picked from select parcels of vines that achieve ripeness with naturally high acid levels. ■
Source: www.jimbarry.com recognised with the Wolf Blass AM BVK Award at the 21st Canberra International Riesling Challenge in 2022.
“Making riesling in the Clare Valley is an incredible privilege,” says third generation winemaker and general manager Tom Barry.
“I am grateful to my parents and grandparents for their hard work and foresight, which has afforded us the opportunity to make this wonderful variety.”
Natural Growth
As well as the soil in which the variety is grown, temperature control is a critical parameter in quality wine production. This is especially so for South Australian wineries, where the climate varies from cool to hot, depending on the season.
Refrigeration addresses some of these challenges, but creates a set of others. Refrigeration is typically the largest consumer of electricity in Australian wineries –accounting for 50 to 70 per cent of total electricity use.
So when it foresaw a rise in the demand of its famed riesling, Jim Barry Wines sought a holistic solution to the upgrade of its refrigeration plant that recognised the importance of energy efficiency and environmental sustainability.
This led to Jim Barry Wines approaching refrigeration specialist Cold Logic.
The South Australian based company has serviced some of the biggest names in the Australian wine industry for nearly 40 years. Cold Logic says its installations have chilled 13.5 million tonnes of crushed grapes – the equivalent of 870 million cases of wine.
“Cold Logic is passionate about helping our clients improve their efficiencies and environmental impact,” says Cold Logic partner Eddie Lane.
“We aspire to minimise the impact of refrigeration on the environment through actively promoting national refrigerants and minimising the electrical energy consumed by the system.”
After a careful assessment that considered the existing unreliable and ageing refrigeration plant, and the future goals and growth of Jim Barry Wines, Cold Logic determined that an ammonia (NH3) refrigeration plant would best suit the long term aspirations of the winemaker.
A cost comparison analysis against alternatives followed, which considered the use of synthetic refrigerants and whole of life cost.
Ammonia emerged as the most appropriate option.
“Ammonia refrigeration is the most efficient refrigerant in industrial applications, with a very high COP (coefficient of performance) efficiency factor,” says Lane.
“Ammonia is a natural refrigerant, is 100 per cent environmentally friendly with zero global warming potential (GWP) and zero ozone depleting potential (ODP). In short, it represented Jim Barry Wines with both the most energy efficient system and environmentally friendly option.”
The Plant
The brief from Jim Barry Wines called for a refrigeration system designed to meet the capacities of 4,000 tonnes of crushed grapes, and whole bunch pressing of 15 tonnes of riesling per day during vintage – when grapes are harvested from the vineyards and prepared to be made into wine.
The system would also need to provide for chilling of 200 tonnes of must (raw crushed grapes) and 500kL cold stabilisation from 20˚C to 2˚C.
This equated to a total capacity demand of approximately 450kWr.
“Experience in wineries and knowledge of these processes was pivotal in getting the right total heat loads and allowing for future growth targets to be achieved,” says Lane.
The ammonia refrigeration plant was designed and assembled at Cold Logic’s Port Adelaide factory. Meanwhile, minor earth moving works were carried out at the Clare winery to accommodate the evaporative condenser.
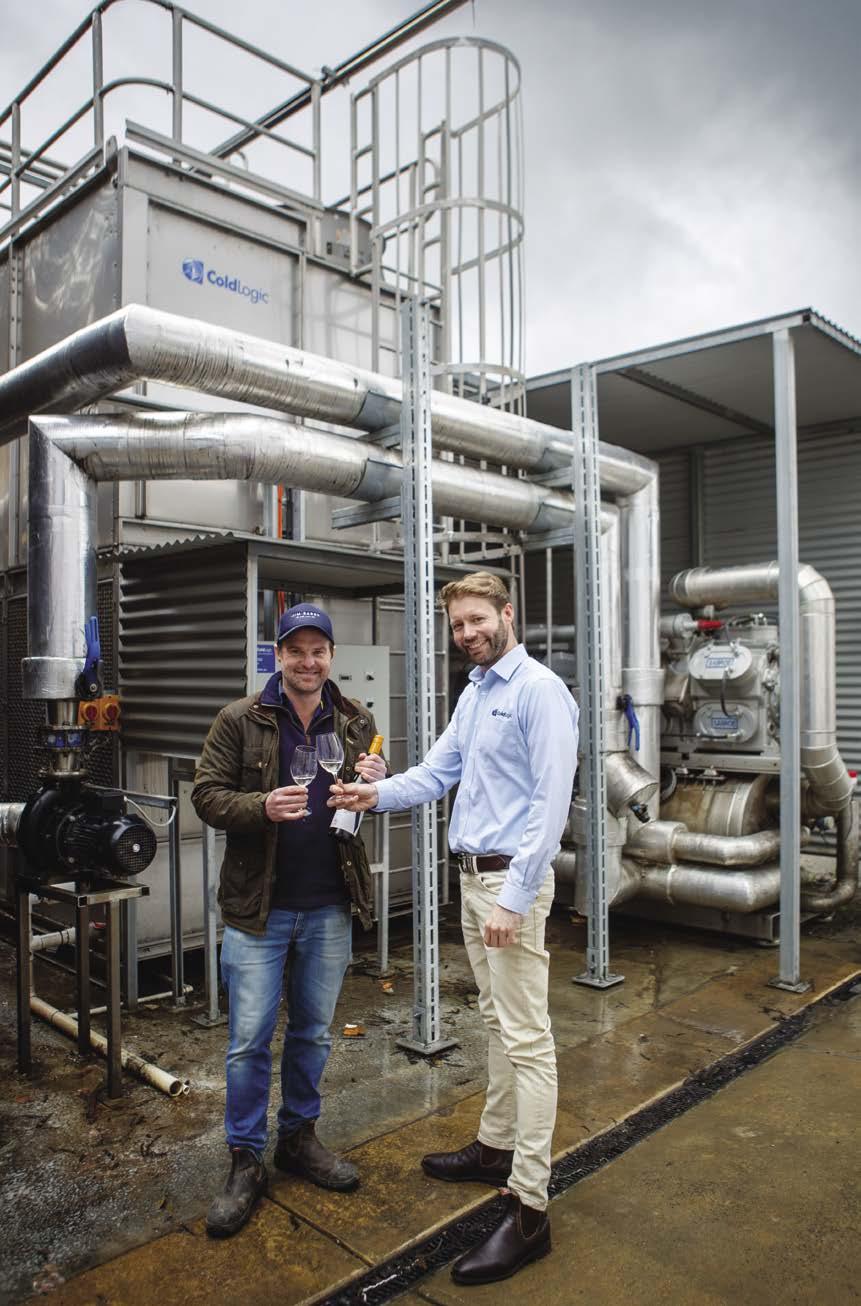
With the COVID 19 pandemic creating a number of supply chain challenges, including longer than‑normal lead times, strong project management by the Cold Logic team was critical.
Once pre assembled, the refrigeration system was transported via road from Port Adelaide to Clare. A large pull down on the existing glycol tank was also completed to allow for a thermal buffer to cater for a week long shutdown.
The existing chiller was then removed to allow for positioning of the new ammonia package and condenser, while the existing brine pumps were reconfigured so that the new refrigeration plant could handle the large “lumps” in load during vintage.
The existing hot and cold glycol tanks were also retained.
This changeover, including site installation and commissioning, was completed in just one week and well before vintage.
Standard ammonia safety systems were installed, including breathing apparatus, wind socks and regulatory signage.
Lane explains that the plant at Jim Barry Wines is controlled via a proprietary control system that works on the glycol tank temperature.
The new RadiCal 2 Impeller the best in its class
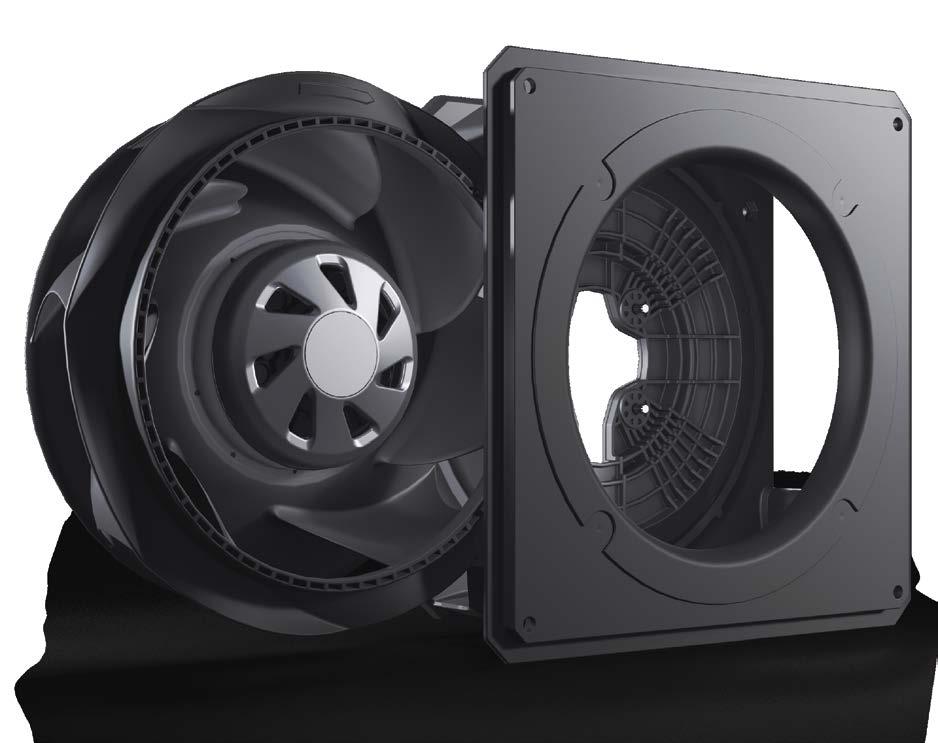
Unbeatably powerful, quiet, compact, and efficient. The new RadiCal 2 impeller from ebm-papst is better than its predecessors in every respect.
Scan the QR Code for our product brochure!
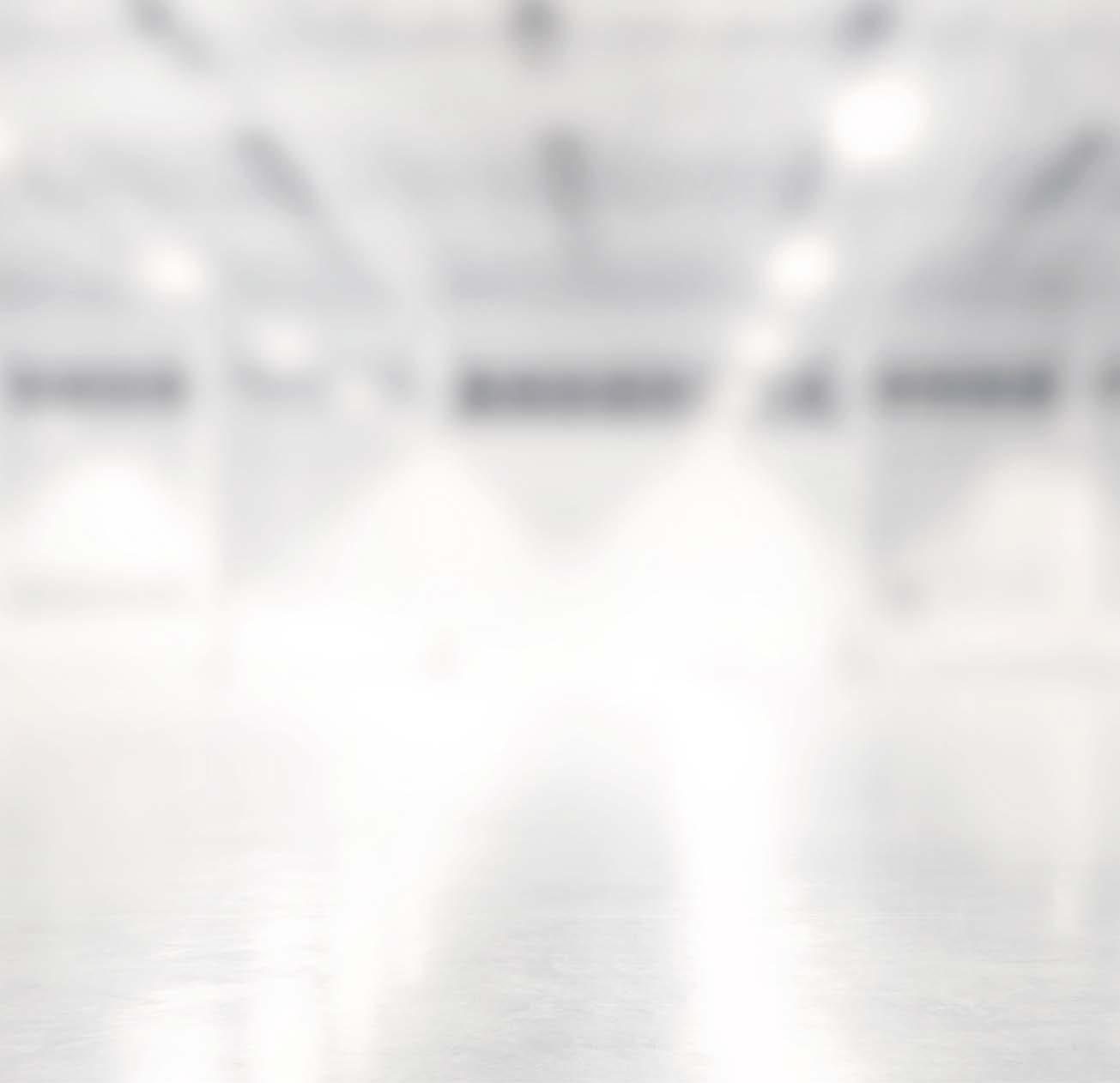
New Vintage
The new ammonia refrigeration system at Jim Barry Wines has been in operation since reaching completion in 2021. Since then, it has delivered an energy cost reduction of 30 per cent compared to previous annualised costs associated with the former air cooled chiller.
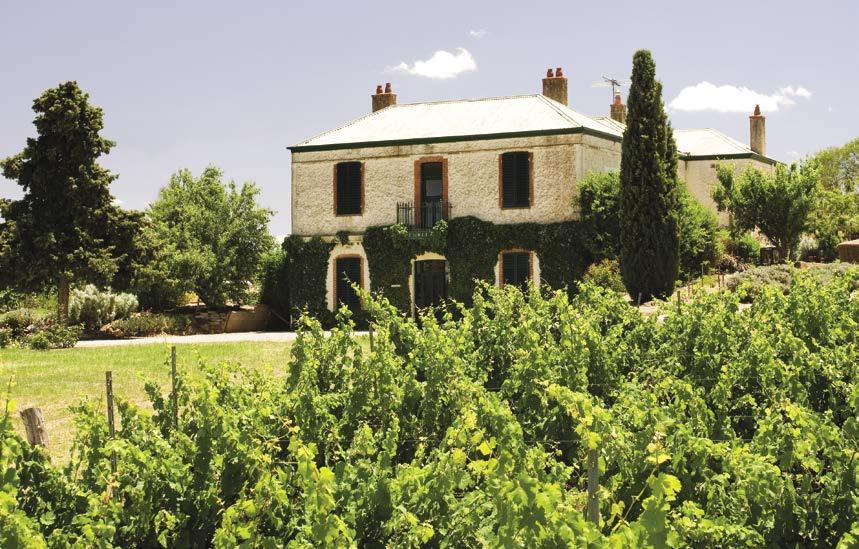
“Jim Barry Wines is very concerned about climate change and we feel a responsibility to act immediately,” says Barry.
“The new ammonia refrigeration plant will help guarantee the long term supply of high quality riesling, will offer significant environmental benefits and substantial energy savings.”
To this end, Barry hopes that sharing the energy savings from the refrigeration upgrade will provide fellow viticulturists and wineries with the confidence and encouragement to consider ammonia based refrigeration.
Internally, the adoption of a natural refrigerant with zero GWP has been well received by the winemaker’s employees, who have acknowledged the positive contribution the company is making to the environment.
The new refrigeration plant represents a significant step on the winemaker’s journey to becoming a carbon neutral company.
“For most companies, having a sustainability plan is no longer a differentiator but an expectation from customers and employees,” says Lane.
“Cold Logic is buoyed to be playing an important role in making net zero carbon emissions a reality, and we love being a part of the most innovative winemaking industry in the world.” ■
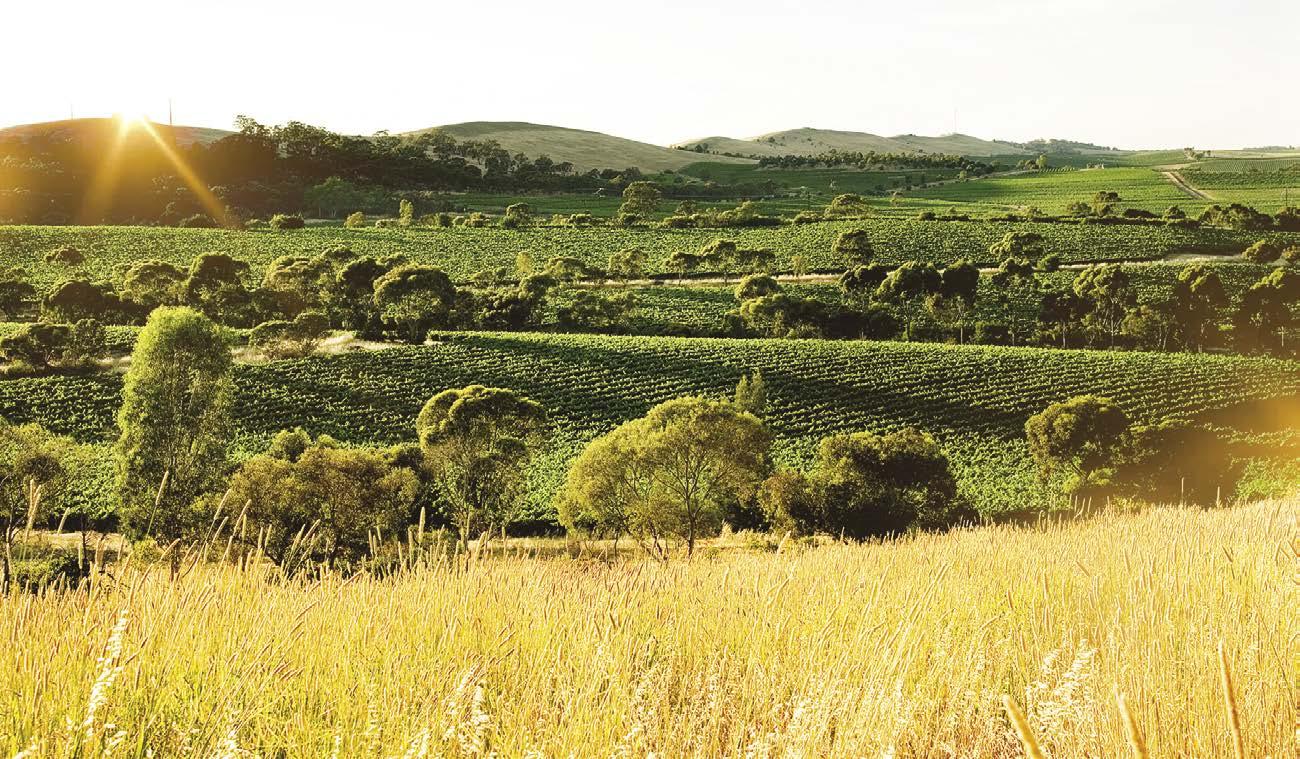
Project At A Glance
The Personnel
▲ Client: Jim Barry Wines
▲ Controls: Sabroe (proprietary)
▲ Refrigeration design: Cold Logic
▲ Refrigeration contractor: Cold Logic
The Equipment
▲ Chillers: Johnson Controls/Sabroe
▲ Compressors: Johnson Controls/Sabroe
▲ Condensers: Bao Feng
▲ Controls: Johnson Controls/UNISAB
▲ Pumps: Grundfos
▲ Sensors: ifm
▲ Valves: Danfoss
▲ VSDs: Danfoss
Skills summary
■ What?
A guide to the fundamentals of water flow in HVAC systems.
■ Who?
Relevant for anyone involved in the process of testing, adjusting and balancing water systems within the HVAC&R industry.
Pressure
Definition and units
Pressure (p) is a measure of the effect of a force, expressed by dividing the force by the area it is acting on:
p = Force/Area = F/A
Pressure (p) is defined in Newton per square metre (N/m²). The SI unit ‘Pascal’ was created to take the place of Newton/m².
1 Pascal (Pa) is the pressure (or stress) exerted by a force of 1 Newton acting on an area of 1m², 1 Pa = 1 N/m². Therefore:
p = h × ρ × g (Pa)
Other units have been used to express pressure as follows:
Bar (bar) 1 barometric pressure = 101.3kPa ~ 100,000Pa
Millibar (mbar) 1000mbar = 1 bar
Pound per square inch (psi) Imperial measure (lb/in² or psi), 1psi = 6.9kPa
Feet head of water Imperial equivalent to metres head
Inches Water Gauge ("WG) Same as feet head of water, but expressed in inches
Inches or mm of Mercury. Similar to a water column, but using mercury