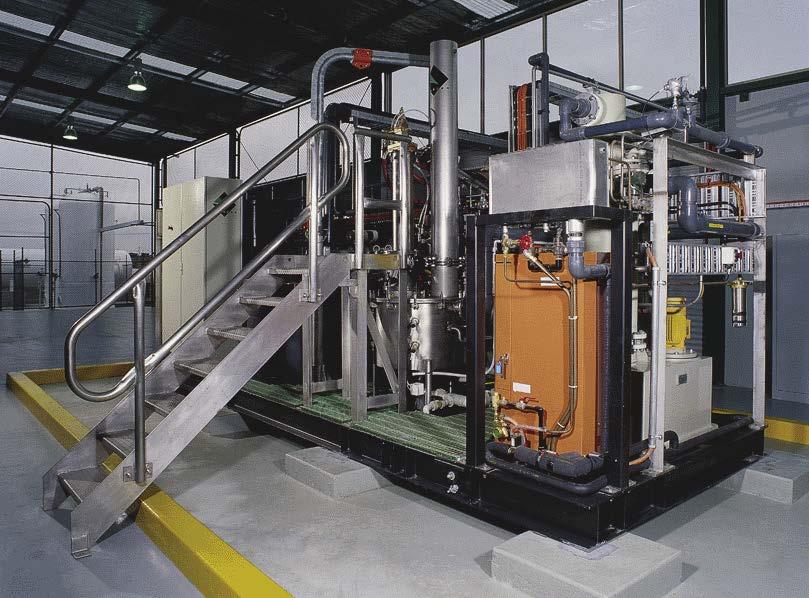
3 minute read
MEASURING EMBODIED CARBON
from HVACR News June-July 2023
by AIRAH
The National Australian Built Environment Rating System (NABERS) and Green Star, the rating system developed by the Green Building Council of Australia (GBCA), are now incorporating embodied carbon into their ratings.
Before we can land on an accurate rating for embodied carbon, however, we need to be able to accurately measure it.
Advertisement
One way is by using an environmental product declaration (EPD). An EPD is an independently verified and registered document that communicates transparent and comparable data and other relevant environmental information about the life‑cycle environmental impact of a product.
But although a wide variety of building products already have EPDs, many products in the HVAC&R space do not.
To fill this gap, a methodology called TM65 was developed in the UK, and has been adapted to Australia and New Zealand by the GBCA and CIBSE, with assistance from AIRAH. This has been incorporated into the Green Star credit system for star ratings. ■
Pol’s situation corresponds with Greg Picker’s view of recycling in the HVAC&R industry. As General Manager of the Air conditioning and Refrigeration Equipment Manufacturers Association of Australia (AREMA), feedback he receives about recycling levels for air conditioning systems suggests it is very high in Australia, particularly compared to other countries.
“There are three main things that come out of most air conditioners: metals, refrigerants, and plastics,” Picker says.
“Figures from KPMG, for example, show that more than 85 per cent of metals from split systems at end of life were being recycled, with bigger systems likely yielding an even higher recycling rate.”
When it comes to refrigerants, our level of refrigerant recovery in Australia is also indicative of good practice globally; however, Picker believes more gas could be recovered from systems at end of life, particularly in smaller residential systems.
“Another bit that worries me though, is that if a system is on top of a building that is being demolished, how efficient are the demolition people going to be at getting the metals and gas out?” he says.
Plastics are another matter. According to Picker, most of it goes to landfill as shredder flock. So how do we change this?
“Certainly, governments have talked about stewardship,” says Picker. “We’re among the best in the world when it comes to metals and refrigerant recovery, and we have to deal with a whole range of other issues – such as ensuring maintenance in existing kit – but over time we will need to address plastics as well.
“However, this is a live conversation in policy circles so we will have to wait and see – the future may be soon.
“The good news from a manufacturing perspective is that our recycling efforts are world leading. [But] we reckon there are still improvements to be made, and we need to address these.”
Circularity And Refrigerants
One reason for Australia’s world leading recycling reputation are our mandatory laws around refrigerants. Without them, we could be in a far worse environmental position.
“In Australia, it is a legal requirement that refrigerant is recovered, and it is actually illegal to vent the product into the atmosphere,” says Kylie Farrelley, general manager of Refrigerant Reclaim Australia (RRA), the product stewardship organisation for the Australian refrigerants industry.
“Just one kilo of a common refrigerant used commercial refrigeration is equivalent to four tonnes of CO2. You only need a little bit to be released to atmosphere to do a lot of environmental damage.”
Intentionally venting is illegal under the Ozone Protection and Synthetic Greenhouse Gas Management Act, and good maintenance by licenced technicians is essential so the gas is not inadvertently released into atmosphere.
Recovered refrigerant is either retained for reclamation (recycled) by specialised equipment or safely disposed of by RRA. It is recovered by licenced technicians who return it to their wholesaler, and the wholesaler issues a rebate to the contractor. RRA then collects it from the wholesaler and re imburses the wholesaler for the rebate paid to the contractor.
RRA has two methods for destroying refrigerants. The first is an argon plasma arc which transforms refrigerant into a salty water waste. With the other, the refrigerant is processed through a modified cement kiln where the acidy gases created from the breakdown of fluorinated gases are neutralised by the alkaline lime in the cement clinker.
“Both those processes are approved by the United Nations Environmental Program and they’re at least 99.99 per cent efficient,” says Farrelley.