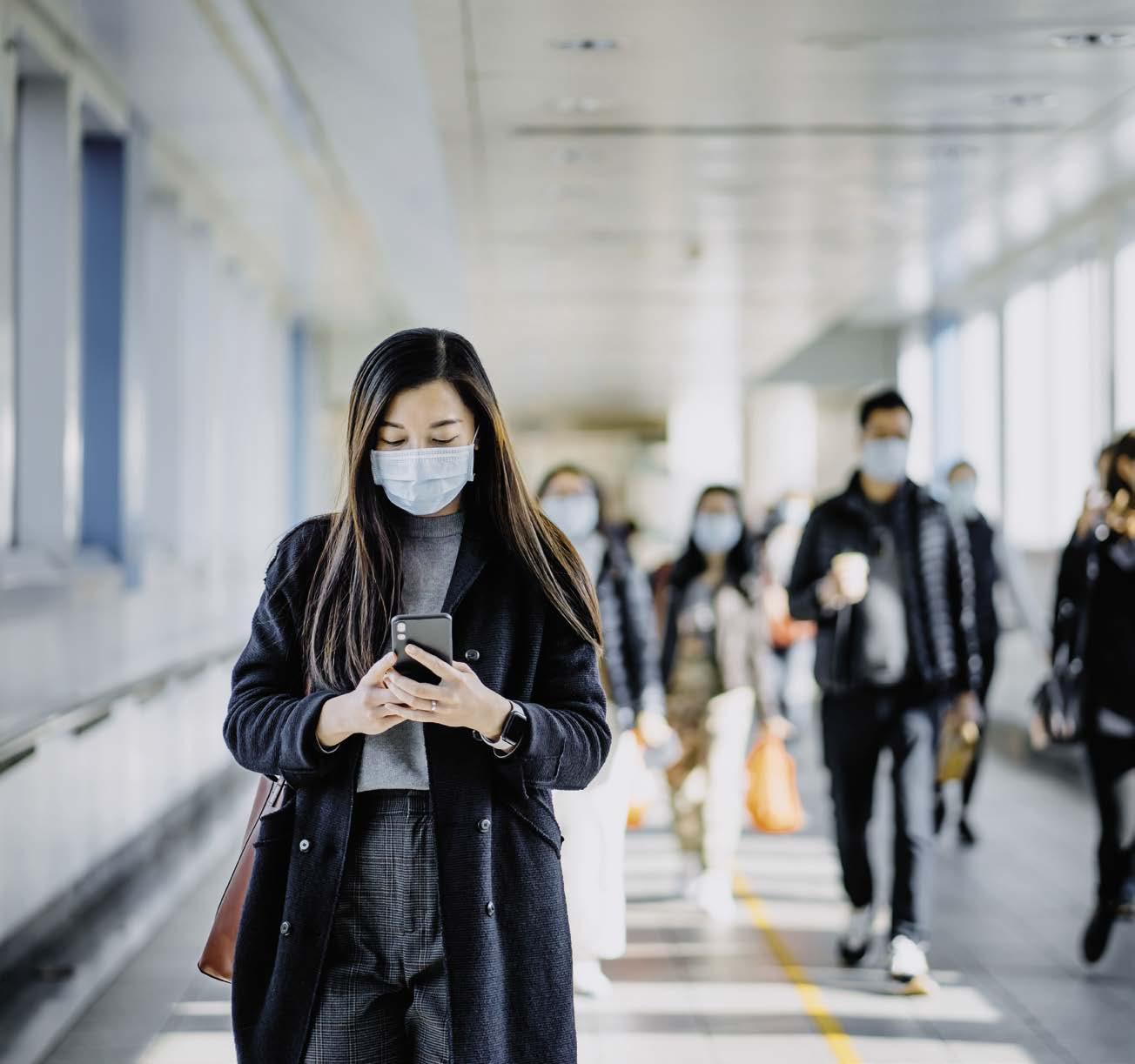
11 minute read
FUNDAMENTALS OF WATER FLOW
from HVACR News June-July 2023
by AIRAH
This Skills Workshop provides an overview of the theory and fundamentals of the science water flow as it relates to fluid flow in a hydronic distribution system. To solve any flow problem, a basic knowledge of the physical properties of the fluid is required.
The objective of most HVAC&R pumping applications is to either circulate liquid around a piping system (e.g., chilled or heated water coils) or to transfer a liquid from a source to a final destination (e.g., header tank).
Advertisement
Pressure is required to overcome the system losses and make the liquid flow. Losses can be due to friction of pipe, fittings and components or static pressure differences due to differences in height between the source and the destination, or to overcome the existing pressure in a vessel into which a liquid is being pumped.
The following factors enable conversion between the various metric units and from imperial to kPa:
Static or velocity pressure
Pressure within a pumped system is split into static pressure and velocity pressure.
Static pressure ( ps) is the pressure developed by the difference in height of the liquid source and destination, or is the pressure of the vessel into which the liquid is being discharged. In closed loop systems that are not open to atmosphere, the static pressure is often zero, unless a header tank or pressurisation unit is included in the system, where the static pressure will then be set by the make up pressure.
Velocity pressure ( pv) is the pressure needed to overcome the frictional resistance of the system, including pipes, fittings and components.
Total pressure
The sum of the system static pressure and velocity pressure is called the total pressure ( pt ): pt = ps + pv
Where: pt = Total pressure (Pa) ps = Static pressure (Pa)
Gauge or absolute pressure
Pressure is usually expressed in “gauge pressure”, which is the pressure above or below atmospheric pressure. Sometimes, pressure is expressed as “absolute pressure”, which is relative to a perfect vacuum.
Absolute pressure = gauge pressure + atmospheric pressure
Note that the atmospheric pressure exerted by air at sea level will generate 101.325kPa; this is reduced to only 89.9kPa at an altitude of 1,000m. Canberra, for example, has an elevation of 243.84m (800 feet), equivalent to 98.44kPa.
pv = Velocity pressure (Pa).
Velocity pressure can be transformed to static pressure and static pressure can be transformed to velocity pressure. Static pressure is measured with a pressure gauge, and must always be measured in a static liquid or through a pressure tap mounted perpendicular to the flow direction.
Total pressure can be measured through a pressure tap with the opening facing the flow direction. The velocity pressure can be found by measuring the pressure difference between total pressure and static pressure. Such a combined pressure measurement can be performed using an annular flow device.
Annular flow device tubes measure ps and pt and can be used to calculate pv (see Figure 1).
Velocity pressure ( pv) is a function of the liquid velocity. The velocity pressure can be calculated with the following equation, where the velocity (V ) is measured and the liquid density ( ρ) is known: pv = ½ρ V²
Where: pv = Velocity pressure (Pa) ρ = Density of liquid being pumped (kg/m³)
V = Velocity of liquid being pumped (m/s).
Head
Definition of head
Head is the term used to define the energy supplied to the liquid by the pump. The increase in pressure between the inlet and outlet of a pump (i.e., the pressure increase imposed on the piping system by the pump) is due to the momentum imparted by the impeller. This in turn is a function of the velocity at the tip of the impeller. Similar to total pressure, total head is made up of static head (Hs) and dynamic head (Hd ).
If two identical pumps, operating in identical conditions, are pumping different liquids, the head (H), which is the height of a column of the liquid at the pump discharge that each pump can sustain, will be (if the effects of pipe friction are ignored) identical. The pressure developed by each pump will also be the same unless the densities of the liquids being pumped differ. The head, also known as the liquid column, is a function of the impeller velocity and pump construction, it is entirely independent of the liquid being pumped.
Converting head to pressure
Pressure can be calculated from a known head as follows: p = g x H x ρ 1000
Where: p = pressure (kPa) g = acceleration due to gravity (m²)
H = head (m) ρ = density of liquid being pumped (kg/m³).
Example
Both pumps in Figure 3 will produce a liquid column of H metres. However, if Pump 1 handles water and Pump 2 handles mercury, pressure gauge P1 will register a pressure equal to:
9.8 × H × 1000/1000 = 9.8 × H (kPa).
The density of mercury is 13,600 kg/m³ and hence pressure gauge P2 will register a pressure equal to:
9.8 × H × 13,600/1000 = 133.3 × H (Pa).
Note that, although the head is the same, the pressures are very different.
The power required for pumping any liquid is proportional to the product of the density of the liquid and the height it has to be elevated. Therefore, if Pump 1 requires 10kW, then Pump 2 would require 13.6 x 10 = 136kW. Hence, the difference with Pump 2 is that the discharge pressure and the power consumption will be 13.6 times that of Pump 1. Since both pumps have the same physical dimensions, they will deliver the same volumes of different liquids so long as the viscosities are the same.
In summary
• Regardless of the density of the liquid, the centrifugal pump will always produce the same head if operating conditions and speed are maintained constant.
• The pressure (read from a gauge at the discharge) will be increased in direct proportion to the ratio of the density of the liquid to that of water at 15°C; i.e., the specific gravity of the liquid.
• The power required by the pump will also be increased in proportion to the ratio of the density of the liquid to that of water at 15°C; i.e., the specific gravity of the liquid.
Terminology – pressure or head
When working with pumps, the word head is often used to define pressure.
Note: The terms head and pressure are often mistakenly used interchangeably. Pump manufacturers have traditionally preferred to use head when specifying pump performance. The main reason for this is that a particular pump always sustains a given head regardless of the liquid it is pumping.
The HVAC&R industry uses both terms, with a slight preference for pressure. This is simply because air conditioning system designers generally work with pressure when calculating piping system performance; i.e., they use pipe pressure loss charts, fitting losses based on pressure rather than head and pressure losses through coils, chillers, etc., all expressed in kPa. There is little problem with this while the liquid being pumped is water at the normal temperatures encountered in air conditioning systems (typically 8–10°C for chilled water and 45–85°C for heating water). The density of water varies little from 1,000kg/m³ within these temperature ranges.
Another reason for using pressure terminology instead of head is that, in an actual HVAC&R installation, the gauges on the pump suction and discharge normally display pressure, not head.
Pump head terminology
When the hydraulic fluid flows continuously between the pump, plant and the terminal units (serving a coil) without going to the reservoir, then the system is called a closed loop hydraulic system. When the system is open to atmospheric pressure it is called an open system.
Pascal’s law states that any pressure applied to a fluid inside a closed system will transmit that pressure equally everywhere and in all directions, which in turn ensures the pump operating pressure will not allow the possibility of cavitation of the pump. For an open loop system, a height of the make up tank must be sufficient to ensure that cavitation cannot be present.
The following covers some common terms and quantities relating to pump or system head (see Figure 4).
• Dynamic discharge head is equal to static discharge head plus friction head plus velocity head.
• Dynamic suction head is equal to positive static suction head minus friction head minus velocity head.
• Dynamic suction lift is the sum of suction lift and velocity head at the pump suction (when the source is below the pump centreline).
Friction head is the height of liquid (metres) that represents system resistance caused by flow.
• Static head is the hydrostatic height of a fluid. In a closed system, the static head has no effect on performance apart from the pump casing being able to handle the static head within the system.
• Static suction head is the positive vertical height in metres from the pump centreline to the free surface of the fluid.
Static suction lift is the distance in metres from the pump centreline to the free surface of the fluid (below the pump centreline). Suction head is the height of fluid above the centreline of the pump on the suction side of the pump.
In order to size a pump, the following would apply (for an open system only):
• Static pressure minus suction head equals actual static head pressure loss Suction lift is the height the fluid must be lifted within an open type system on the suction side of the pump to reach the centreline of the pump
Total dynamic head is the dynamic discharge head plus dynamic suction lift, or dynamic discharge head minus dynamic suction head Dynamic discharge head equals static discharge head plus friction head plus velocity head
• Velocity head is the height of fluid corresponding to the kinetic energy per unit mass of fluid divided by gravitational acceleration.
Flow rate
Flow velocity
Flow velocities are usually determined during the design stage.
Flow-rate tolerance
Flow rate tolerances will be designated by the design engineer in the TAB specifications, typically as stated in CIBSE Code W.
The heating water flow rate should be between ±10% of design, even though hot water systems can normally tolerate a wider flow deviation because of the larger temperature differential between supply and return.
The ±10% tolerance is economically achievable and can eliminate side effects caused by low water velocity, air purge problems, etc.. However, terminals using low temperature hot water as found in heat recovery systems may require the tolerance to be within ±5% of design flow rate.
Varying pump flow
In some hydronic systems, the flow rate is changed by either varying the pump speed or by the sequencing constant speed multiple pumps on and off (see Figure 5).
Varying pump speed is preferred because of the significantly reduced energy cost brought about by the reduction in pump pressure and water flow rate. For a constant speed pumped system, as the flow is reduced due to the load requirements, the pump pressure is increased with no resultant energy savings. Most of the control valves would be closed or near closed at times of low load. For variable speed pumps, as the load diminishes, the water flow rate is reduced and at the same time the pressure on the pump is reduced, leading to lower power required and less energy consumed by the pump.
It should be noted that the use of a variable‑speed pump will not overcome or even help in any way the problems associated with a system that is poorly balanced. If the flow rate is incorrect initially or at full flow, it will stay that way as the pump pressure is varied. Hence there is still the need to perform a water balance regardless of a variable speed pump being installed.
The terminal units in most variable volume systems have individual two way control valves that allow full diversity or random loading (0–100%).
A minimum pressure differential must be allowed for in the design stage to ensure that all terminals receive the design flow rate at all times.
Hydronic pressure losses
Hydronic systems are subject to the same types of frictional losses and dynamic losses through fittings as experienced in air distribution systems. Pressure loss data for piping system components are supplied by the manufacturers and are expressed in one of the following terms:
• Equivalent metres of pipe Kilopascals (kPa)
• Metres of water.
The Kv value describes the amount of water that flows through the valve at a pressure loss of 1 bar. The Kvs value describes the Kv value when the valve is fully open.
This is a measured characteristic of the valve body against an actual pressure drop. For a known flow rate, all valves have a measurable pressure drop across them: p = ( m³/hr )² × 100 kv = ( 3.6 × L/s )² × 100 kv
Frictional losses in pipes may vary due to:
• The condition of the piping
• The ageing process of the piping
• Chemical treatment of the system
Changes in the pH level of the system.
A closed system will remain relatively clean due to the fact that minimal water is added to the system apart from water that has been lost through leakage (gland packings), hence there will be small variation in the system pressure loss.
On the other hand, any system open to atmosphere and the dust therein (e.g., a condenser water system) will over time accumulate debris and suffer corrosion, which will generate a higher pressure loss per metre of piping than an equivalent closed system. Appropriate water treatment and filtration and straining can help to keep open systems clean.
Control valve authority
Control valve authority is a term used to describe how the control valve is selected and sized to ensure that the valve and the coil will perform correctly, and the valve has controllability over the circuit (or coil) through the whole valve stroke.
The valve authority is generally defined as a ratio of the pressure drop against the fully opened valve compared to the pressure drop of the entire circuit (valve included) at the design flow rate conditions. In terms of control, the valve authority works in conjunction with the valve, actuator and terminal characteristics (see Figure 6).
If the control valve is oversized, this will impact on the performance of the system and the life span and reliability of the valve.
When sizing a control valve, the most common approach is to calculate the flow coefficient known as Kv
Where: kv = control valve flow coefficient
Q= flow rate p = pressure drop.
Example
A control valve is to be selected for a flow of 20.17L/s with a maximum pressure drop of 53kPa. Determine the required Kv of the valve:
Kv = m³/hr × 10
√Δp = 3.6 × 20.17 × 10
√53 = 99.74 (say 100)
The combined characteristic will be considered linear from the controller’s point of view (see Figure 7). The lower the authority, the larger the pressure shift will be.
System curves
The frictional losses throughout the piping system will depend on the actual flow rate achieved (see Figure 8).
If only one set of friction pressure/flow rate data is available, a system curve can be obtained by using the principle that pressure varies directly as the square of the flow rate. When two values are known, the new flow rate or pressure can be calculated by the following equation:
Where: p₂ = ( L/s2 )² p1 = L/s1 p = pressure (kPa)
L/s = flow rate (L/s).
Example:
A system has a pressure of 100kPa with a flow rate of 1.6 L/s. Determine the new pressure at 2.0L/s:
Pressure p2 = p1 × ( L/s2 )² L/s1
Pressure p2 = 100 × ( 2.0 )² 1.6
Pressure p2 = 156kPa
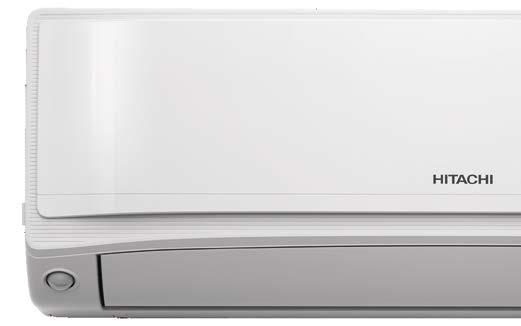
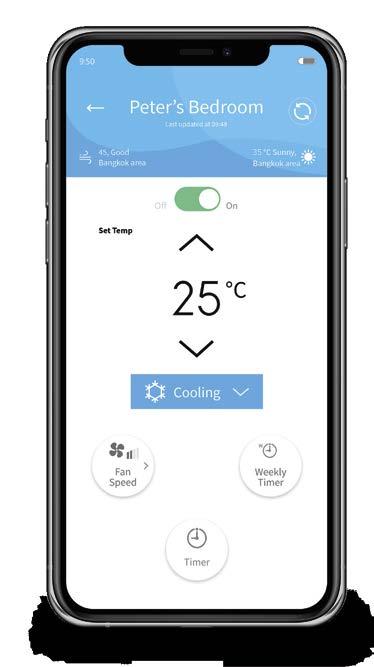