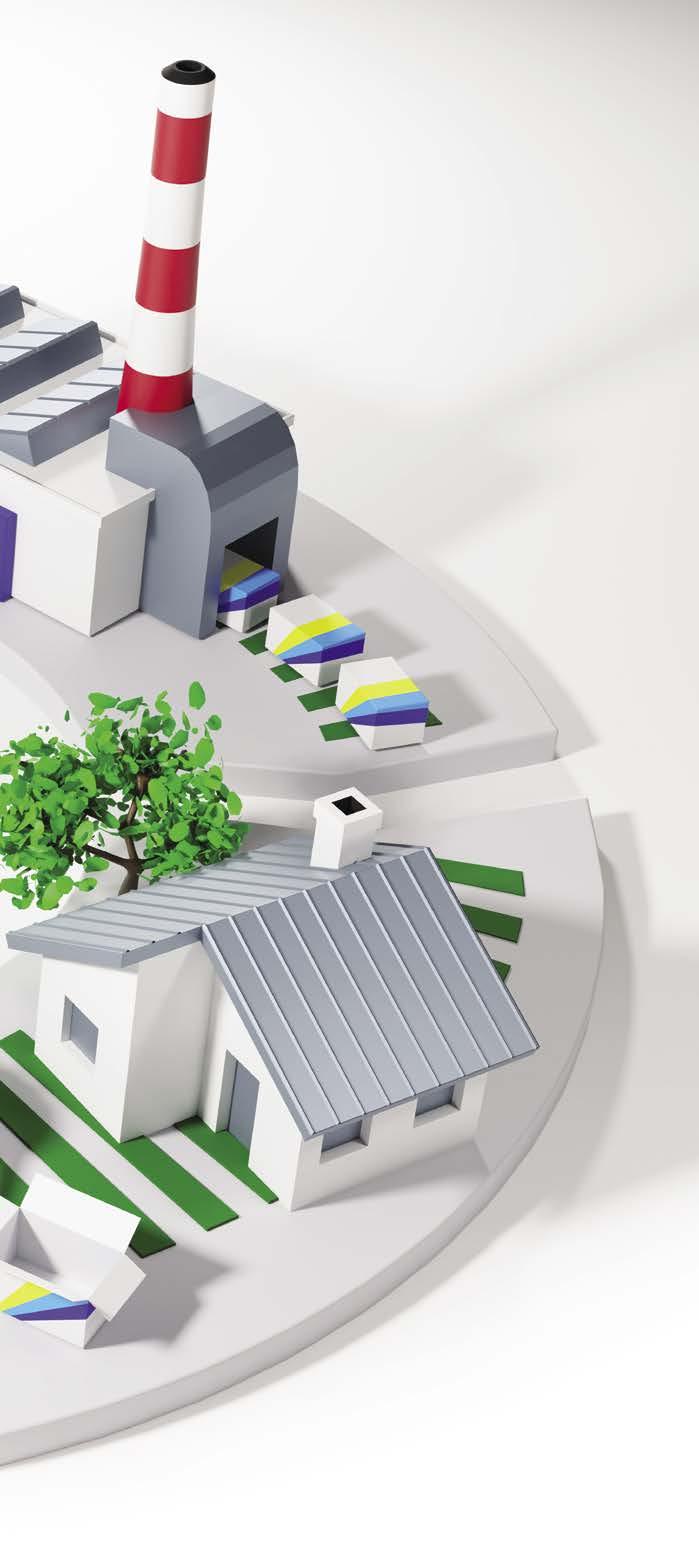
2 minute read
MECLA
from HVACR News June-July 2023
by AIRAH
The Materials and Embodied Carbon Leaders’ Alliance (MECLA) is a collaboration between the NSW Government and more than 100 founding members driving reductions in embodied carbon in the building and construction industry.
When MECLA began in 2021, it focused on addressing emissions from the most common and highest volume building materials: steel, cement and aluminium, which MECLA says produce about 7–9 per cent of annual global greenhouse emissions each.
Advertisement
In 2022, MECLA members established a new working group, to look at building services. Reducing embodied carbon in building services is particularly challenging because there is less control over the emissions from the manufacture of the materials that make up these services. With many supply chains in the mix, part of the solution is to demonstrate demand for low‑embodied‑carbon products to the entire supply chain.
AIRAH is co chairing the building services working group. ■ and how much the product is really needed in its current form, or at all, is a scary concept to consider in a world where the linear economy prevails.
“We have traditionally taken materials from the earth, made products to sell to a market, used the products, and then disposed of products in landfills. But with some 100 billion tonnes of materials extracted from the planet globally every year, the time is coming, and in some cases is already here, when materials will not be available in their current abundance and we will have to think differently.
“We must see value in all materials, both virgin and secondary, and we have to design for durability, repairability, and disassembly. We must have an economic system – a circular economic system –that enables these practices and business models. Our resource availability will simply demand it.”
So, what does all this mean for HVAC&R systems?
Different components in a building have different life‑cycles, and these are either technical or economic.
According to one major building services contractor, the air distribution system and some parts of it like AHUs and ductwork may have a life exceeding 50 years. Other elements such as FCUs and VAVs and the componentry inside perhaps have a life of 15–20 years. Chillers and chilled water system elements (coils, valves, pumps etc.) will have an effective life of 15–25 years depending on maintenance and type of building use.
Beyond life cycle replacement there is the change of use/building refurbishment trigger point and a reuse or replace decision around fitness for the new purpose. One contractor offers the example of a 40 plus‑storey city building that was refurbished around 18 years ago, and decisions were made about what to reuse and what to replace based on cost –with subsequent negative life cycle cost implications. Now, the same building is being refurbished, and the same decisions are being made around a different set of lifecycle‑focused criteria and embodied carbon. This is indicative of a general trend toward recycling of ductwork, pipework, cabling and more, with refrigerant being reclaimed and casing sold for scrap.
ONE PERSON’S TRASH …
Christopher Pol discovered first hand the riches that can come out of old systems. The Western Australia fridgie has had some great returns from the systems he collects.
“It’s a great way to recycle the materials, and make some decent money,” Pol says.
“The missus wasn’t enjoying looking out of the kitchen window at the Great Wall of aircon units I was accumulating, so I’ve had my apprentice busy chipping away at them: 78 down, 130 to go.
“So far we’ve had three skip bins of just light steel, then the first trailer load of coils and half the scrap copper was ready to cash in.”
It’s definitely worthwhile scrapping, Pol says.
“The trailer load of coils scored a cool $7k cheque. It has also been bloody handy having a good selection of second hand parts sitting around to get people out of trouble.”
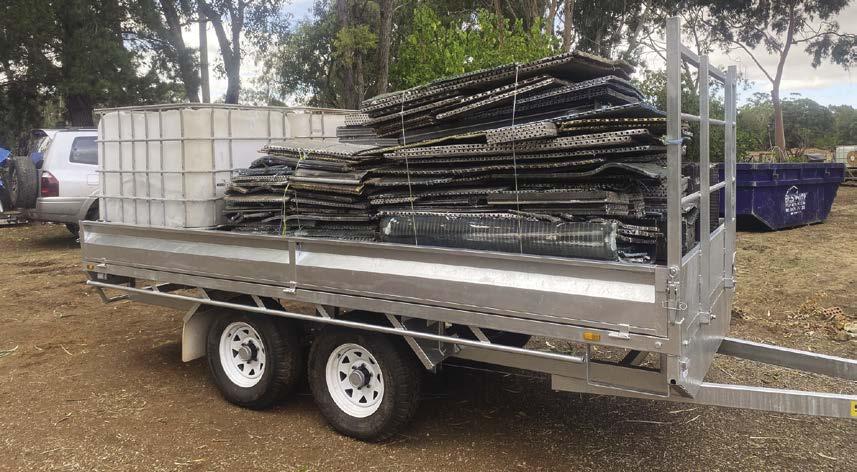