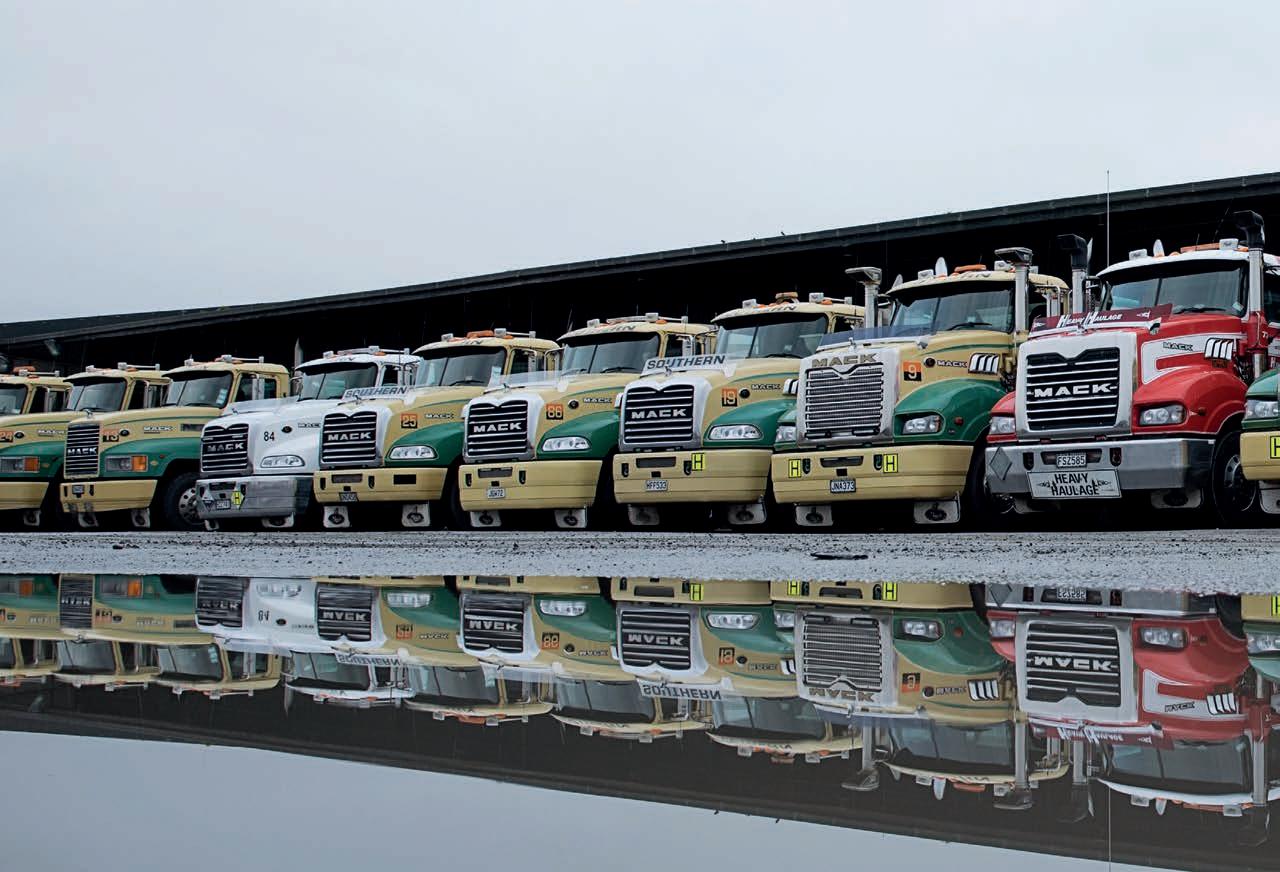
28 minute read
News
HWR Group ready for hydrogen move
SOUTHLAND-BASED TRANSPORT GIANT H.W. RICHARDSON
Group (HWR) is poised to lead New Zealand’s adoption of hydrogen to reduce emissions from heavy vehicles.
Group CEO Anthony Jones confirms HWR has been trialling a hydrogen dual-fuel truck since the last half of 2021 and is now committed to a fleet of 10 dual-fuel trucks which are scheduled to go on the road in the second quarter of 2023.
The trucks are fitted with pressurised hydrogen tanks behind the cab. With modifications to the intake system, the existing diesel engines run on a dual-fuel mix that replaces up to 40% of the diesel fuel consumption with an equivalent amount of hydrogen. The result is a 40% reduction in exhaust emissions.
“Based on our reviews, the key factors to a sustainable fuels transition will be managing the existing capital base deployed today in the heavy transport industry. That is why we chose dual-fuel in the first instance. It’s a way to transition the industry sustainably to hydrogen. Over time we see our fleet moving to 100% hydrogen fuel cells in the future, but not just yet,” says Jones.
HWR Group has worked closely with Christchurch’s AF Cryo, part of Fabrum Solutions. AF Cryo has partnered with UK-based Clean Power Hydrogen (CPH2) and supplies the cryogenic cooling system for the CPH2 membrane free electrolyser.
“I would say they are the leaders in this technology, and they have perfected the IP and technology around the liquification of hydrogen and its storage,” says Jones
“We have committed to our first 1.1-Megawatt (MW) electrolyser and storage system with options to buy further. It will be delivered in August and commissioned by March or April next year.”
The system is scalable and produces the hydrogen onsite. The 1.1MW CPH2 electrolyser is capable of producing 450kg of high purity hydrogen per day from water.
“The first one will be in Southland. There are reasons for that, including the access to green power, water, coupled with our existing fuels and transport network ,” Jones says.
The first trucks are new units which will be fitted with the storage tanks and modifications to the intake system in Europe as well as here in NZ.
“We are working with a European supplier that has perfected dual-fuel technology.”
There are also plans to locally retro-fit existing trucks in the HWR fleets.
HWR plans to have 10 trucks on the road in the second quarter of next year to coincide with the first hydrogen plant being commissioned.
The medium-term roll-out of more hydrogen refuelling locations is tied to HWR Group’s Allied Petroleum network which stretches from the Bay of Islands to Stewart Island.
HWR Group has a fleet of 470 trucks in the South Island and more than 1300 nationwide.
“We will roll out the 1.1MW electrolysers into the existing network where it makes the most sense,” says Jones.
Jones says the dual fuel solution is an ideal course to transition the industry towards zero-emissions.
“The capital investment needed to go 100% hydrogen is astronomical compared to the existing internal combustion engine. Dual fuel technology allows any modern truck to be converted although the design and the tuning will be slightly different depending on brands and roles,” he says.
“I’m in no way against hydrogen fuel-cell vehicles but the capital cost is still very high compared to retro-fitting existing vehicles with a dual-fuel system. This will allow meaningful change to the whole industry.
“But the cost of fuel cells will come down and more efficient ways of storing hydrogen will be developed. Dual-fuel is a way to establish the infrastructure that’s needed to support fuel cells in the future.”
HWR already has some local dual-fuel experience.
“We have had a truck on trial since August last year. We’re not seeing any drop in power at all. We’re not seeing any downsides and we have already learnt a lot.”
Another benefit is the dual-fuel trucks can run on diesel alone if they need to travel beyond the available hydrogen network.
“If you run out of hydrogen, you’re not going to end up with a truck stranded somewhere,” says Jones.
Jones says figures indicate that a single dual-fuel truck running an average of 384km per day can eliminate 102kg of carbon emissions per day.
“We have a fleet of 470 trucks just in the South Island so that would equate to 12.5 million kg of CO2 per year,” he says.
“It’s still a drop in the ocean but it’s a first step to reducing carbon emissions and we need to move now. We know this is going to make a difference.
“For the HWR Group and for Allied Petroleum this represents a big HWR Group CEO Anthony Jones says the company aims to be a leader in the roll-out of hydrogen in New Zealand.

step in our sustainability strategy. We aim to be the leader, but the entire industry can benefit from that,” says Jones.
More hydrogen coverage: NZ Truck & Driver Associate Editor Brian Cowan looks at another New Zealand dual fuel project and the science behind hydrogen combustion engines starting on Page 69. T&D
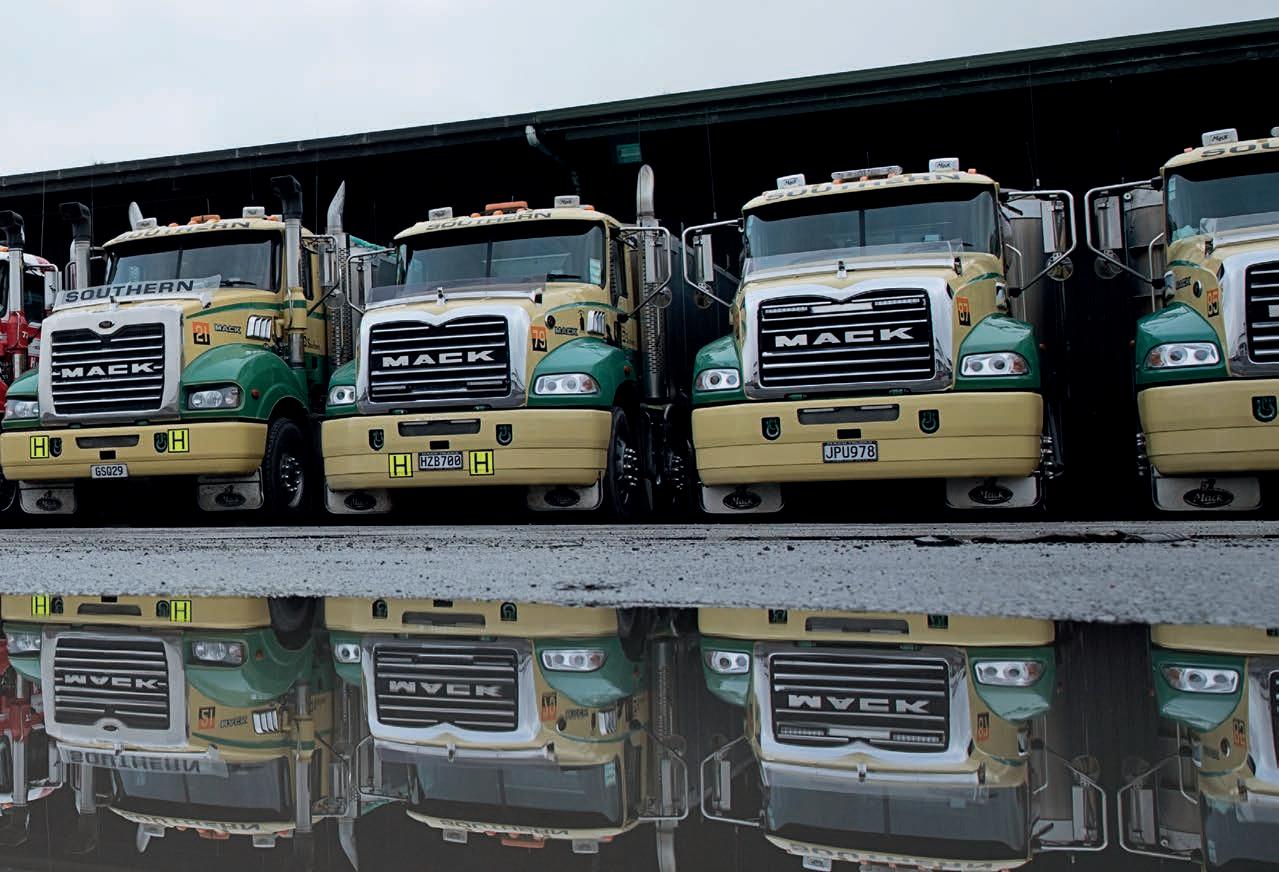
Kirstin Turvey is a trainee in the Transporting New Zealand Te ara ki tua Road to Success programme which will is being extended with the transTasman diversity programme.
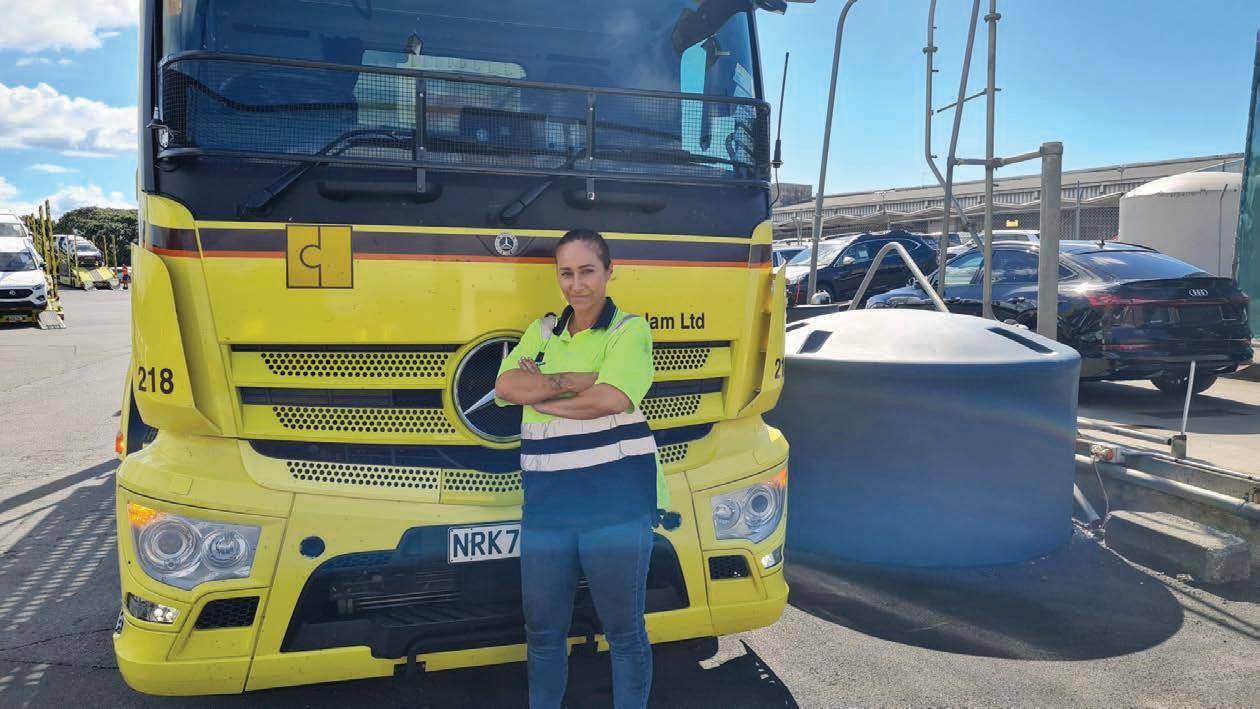
New trans-Tasman diversity scheme
A NEW INITIATIVE TO DRIVE DIVERSITY IN THE ROAD
transport industry has been launched by Ia Ara Aotearoa Transporting New Zealand and Teletrac Navman.
The 2022 Driving Change Diversity Programme will develop a group of diversity champions, nominated from within the transport industry, teaching them how to create change and facilitate diversity in their workplace and community. It is based on a similar successful programme run by the Australian Trucking Association (ATA) across the Tasman.
Falling under the banner of Transporting New Zealand’s Te ara ki tua Road to Success traineeship, it will be the first trans-Tasman programme of its kind in the industry, focusing on attracting talent to the industry by making it more inclusive.
“With the support of Teletrac Navman, the 2022 Driving Change Diversity Programme will showcase diversity champions to the New Zealand trucking industry and wider community, and help promote a positive view of the careers available in road freight transport to encourage more people into the sector’s workforce,” says Transporting NZ chief executive Nick Leggett.
Participants in the 2022 Teletrac Navman Driving Change Diversity Programme will be provided professional development coaching to become mentors, be supported to become spokespeople for diversity and inclusion in the industry, and develop a strong professional network with like-minded individuals.
“There’s no doubt our industry will benefit from this. There have long been concerns about driver shortages, so we need to create an environment where both local and overseas drivers feel welcome,” Leggett says.
“Diversity in the workplace has proven benefits such as increased productivity, access to a greater talent pool, competitive advantages, and the development of more inclusive, attractive workplaces. There are many opportunities available to people with an interest in road transport, logistics, and heavy-vehicle mechanics,” Leggett says.
Transporting NZ says the trucking industry is vital to New Zealand’s productivity and economic growth, with trucks transporting 93% of New Zealand’s freight.
“During the two years that the programme has been running in Australia, we’ve seen positive changes in the transport industry,” says Teletrac Navman marketing director Megan Duncan.
“Interest in the programme is increasing and the participants are creating a strong diverse network of people who will help shape the future of the industry. We’re looking forward to bringing New Zealand into the programme in 2022 and growing diversity in the sector on both sides of the Tasman.”
ATA Chair David Smith says the programme had received overwhelming support from industry members since its Australian launch.
“We are so thrilled to welcome our New Zealand counterparts to the programme. They are demonstrating the leadership and innovative thinking that is crucial to building a viable and sustainable industry,” Smith says.
Nominations for the Teletrac Navman Driving Change Diversity Programme can be made until 3 June 2022. Participants must be involved as an owner or employee in a trucking business in New Zealand.
The programme begins with a workshop in September and participants will attend the Transporting NZ Conference in Invercargill.
For information on how to participate contact Fiona McDonagh at Transporting New Zealand, fiona@transporting.nz T&D
From left: Cathy Clennett, co-founder and chair of Hiringa Energy, Jimmy Ormsby, Managing Director Waitomo Group, Dan Khan, co-founder and CTO Hiringa Energy, Simon Parham, COO Waitomo Group, and Andrew Clennett, co-founder and CEO of Hiringa Energy.
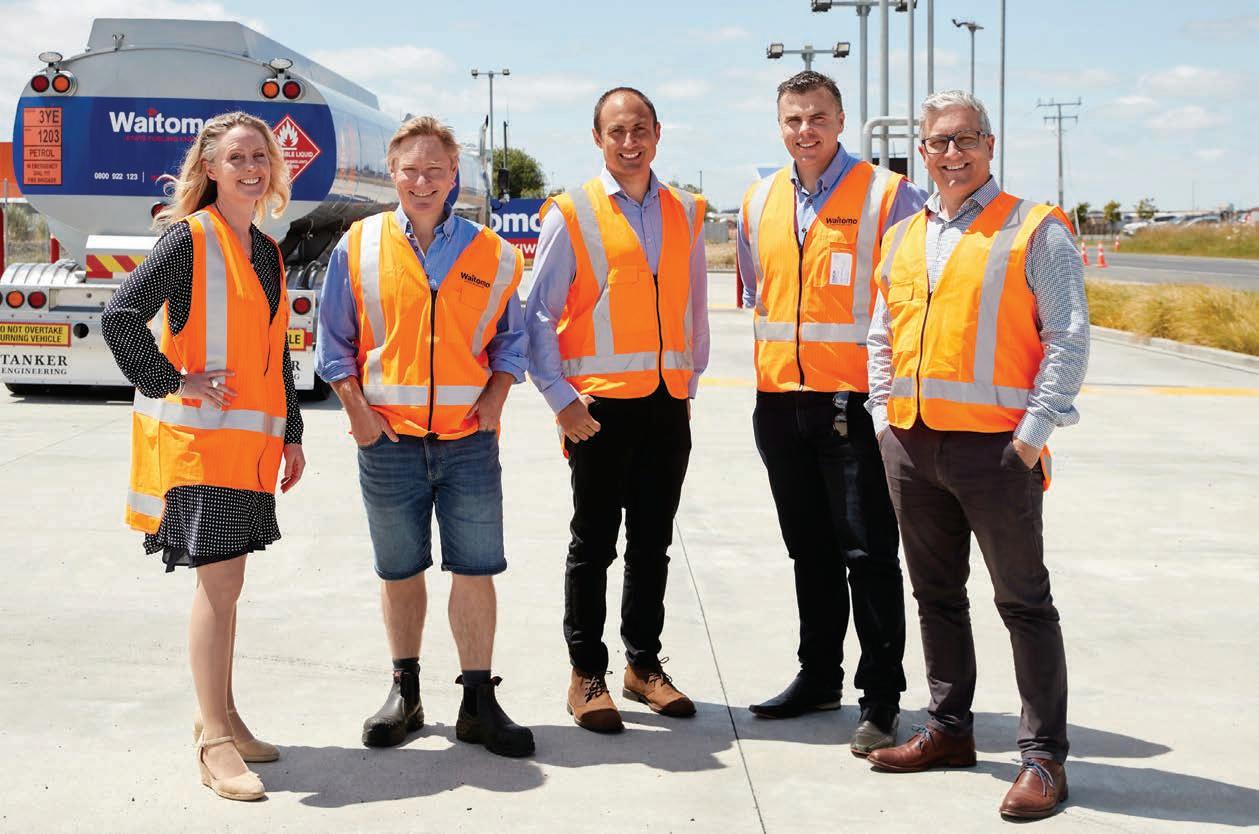
Hydrogen project underway
PALMERSTON NORTH WILL BE HOME TO NEW
Zealand’s first high-capacity green hydrogen refuelling station.
Construction at the site, adjacent to Palmerston North Airport, began in the first week of May with the site planned to be in operation in September. It’s the first of four hydrogen refuelling stations being developed by innovative Kiwi energy companies Hiringa Energy and Waitomo Group to establish New Zealand’s first nationwide hydrogen refuelling network.
Andrew Clennett, CEO of Hiringa Energy, says this is one of the first refuelling networks for heavy transport in the world.
Financial backing for the project has been provided through investment from Hiringa’s Strategic Alliance partners, Mitsui and Co (Asia-Pacific), Government funding from EECA and the COVID-19 Recovery Fund, and growth capital from key investors including Sir Stephen Tindall’s K One W One and international funders.
Waitomo Group is self-funding its investment in the project because the Kiwi business sees hydrogen as an important step in the transition to lower emission fuels.
Waitomo Group Managing Director Jimmy Ormsby says breaking ground at the Palmerston North site marks a major milestone for the partnership.
“What began as a discussion between two innovative, future-focused Kiwi companies about developing hydrogen on our existing and new Waitomo Fuel Stops, is now becoming a reality for future Kiwi generations,” Mr Ormsby says.
“Seeing this vision come to life is particularly poignant for me as the third-generation owner of Waitomo, given Waitomo celebrates its 75th anniversary this year. What a way to cement in the transition to a lowemissions fuel future for the fourth generation.
“Adding low-emission alternative fuel solutions to our network is a nobrainer. We want to leave a legacy for the next generation of Ormsby’s to continue in our footsteps. The exciting opportunities that green hydrogen technology offers allows us to deliver on that,” Mr Ormsby says.
Mr Clennett says heavy transport makes up only 4% of New Zealand’s vehicles, but accounts for more than 25% of total vehicle emissions.
“Green hydrogen is the key technology that will allow these fleets to stay on the road. It is a mass-market, clean energy solution that can have a real impact on reducing our transport emissions,” he says.
Specialist hydrogen equipment for the station has been sourced from Europe. The station will be built next to a Waitomo Group Fuel Stop, servicing petrol and diesel customers. Once operational, hydrogen-powered heavy transport vehicles will be able refuel at the station in similar time to what they are used to.
The partners say another three hydrogen refuelling stations are due to begin construction later this year, in Hamilton, Tauranga and Auckland.
More than NZ$50m has been invested in the first phase of the project and detailed engineering and compliance work has been completed. Resource consent has been granted for both the Palmerston North and Hamilton sites, and applications are in for the Tauranga and Auckland sites.
Expansion of the refuelling network into the South Island will begin in 2023, with 24 high-capacity refuelling stations due to come online across New Zealand in the next 4-5 years to support a growing fleet of hydrogenpowered vehicles.
An initial fleet of 20 zero-emission Hyzon hydrogen-powered trucks to support the network has been purchased by TR Group. Built to meet New Zealand regulations, the trucks will be capable of over 600km between refuelling stops. T&D
Iveco restructures NZ sales

IVECO GROUP IS MAKING SIGNIFICANT CHANGES TO
its New Zealand operations.
In an announcement from Australia, Iveco says it is taking full responsibility for sales in New Zealand and ending agreements with its three independent dealers. Iveco Group’s local vehicle sales operation is to be consolidated at its Wiri facility in South Auckland.
The decision is the latest restructuring in the supply and distribution of Iveco vehicles. Late last year it was announced the Iveco plant in Dandenong, Victoria would close from mid-2022 and the brand would transition to a fully imported vehicle range supported by a customisation facility for Australasia.
Iveco Group says the sales decision is based on the desire to form even closer relationships with its New Zealand customer base, with a view to better servicing its needs. It estimates the Auckland site already accounts for 86% of vehicle sales in New Zealand, meaning most buyers will be unaffected by the move.
The operational change will mean that three existing dealerships will cease sales of Iveco vehicles in October. Iveco Group has invited the affected dealerships to remain part of the network in service and/or parts capacities. It is also in the process of appointing additional service and parts dealers to expand its capabilities in these areas.
There are currently 21 Iveco service and parts outlets in New Zealand.
Iveco Trucks Australia Head of Network, Product and Marketing, Ella Letiagina, said that New Zealand was an important and growing market for the brand.
“In recent years Iveco has experienced strong growth in New Zealand, especially since the opening of our flagship sales service and parts facility in Wiri, Auckland during early 2019,” Ms Letiagina said.
“We believe that by concentrating sales efforts at this location we can further streamline our processes leading to greater efficiencies, while also benefiting future buyers who will enjoy a more engaging and seamless customer journey.”
Ms Letiagina acknowledged the contribution that the three impacted dealerships – AdvanceQuip (Auckland), Star Trucks International (Nelson) and Waikato Iveco (Hamilton) – had made during their tenure as Iveco sales dealerships.
“I would like to thank our outgoing dealerships for their dedication to our brand and Iveco customers over the years,” she said.
“And for existing and prospective New Zealand Iveco owners, I reassure them that our new direction will see even more engagement with them and that they’ll be well catered to, not only from a sales perspective, but from a total ownership experience.”
Iveco will be directly responsible for all sales and is expanding its sales team in several regions.
“We are increasing our footprint by adding new sales staff in different regions of the country. It’s a sales model that has proved to be globally successful,” says Iveco dealer principal Barry Woods.
Star Trucks International director Dale Greaves has enjoyed success with the Iveco line-up and hopes his Nelson-based firm can remain involved with the brand.
“My first thought was maybe it’s time to take retirement and get on with enjoying life. But I have two issues with that – my customers and my staff,” says Dale.
“My customers have been extremely loyal to me. Iveco has been good to me and it’s a good brand. I’m confident that Star Trucks will be able to continue to represent the Iveco brand under a new arrangement.
“I want to support my customers with the trucks I have delivered and the ones I have sold that are waiting to be delivered.”
Iveco plans to introduce several new products to the New Zealand market later this year, including the new S-Way model which replaces the Australian-built Stralis. T&D

NEWS
Royans expands again
ROYANS TRANSPORT ACCIDENT REPAIRS HAVE made another move to expand its network in New Zealand with the acquisition of Sievwright Auto and Powderline in Invercargill.
Sievwright Auto is an industry leader supplying abrasive blasting, panel beating, and paint services for heavy commercial vehicles and equipment.
Powderline are also the local market leader in large scale powder coating with the second biggest powder coating oven in the country. They also offer Thermoplastic coating, a product that offers excellent protection against corrosion, wear and tear and chemical attack.
Operating from multiple facilities in Invercargill, the Sievwright Auto team has over 22 years’ experience in commercial and industrial work in the region.
John Sievwright will be staying on for a short transition period before embarking on new endeavours with Naomi Sinclair being appointed as Branch Manager.
Founded in 1944, Royans has grown to become the largest commercial vehicle repair specialists in Australia and New Zealand.
Sievwright Auto and Powderline operation will be Royans 28th branch and its sixth in New Zealand. Its recent expansion in the New Zealand market now sees it represented with two branches in Auckland, two in Christchurch, plus Palmerston North and Invercargill. T&D Sievwright Auto in Invercargill has become part of the Royans network.
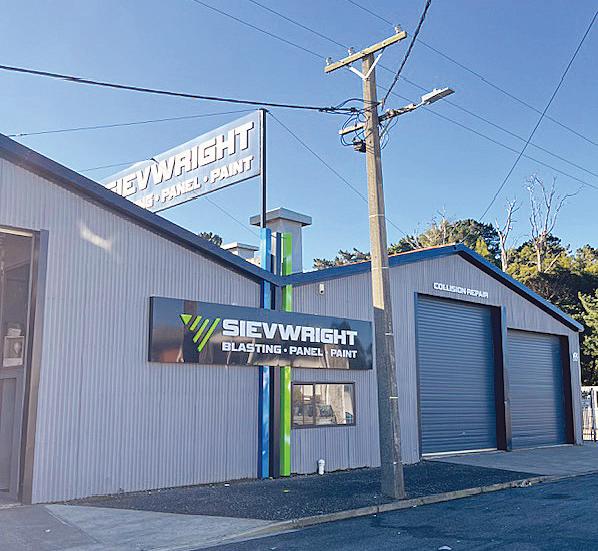
FULL SAFETY SYSTEMS STANDARD ACROSS THE RANGE
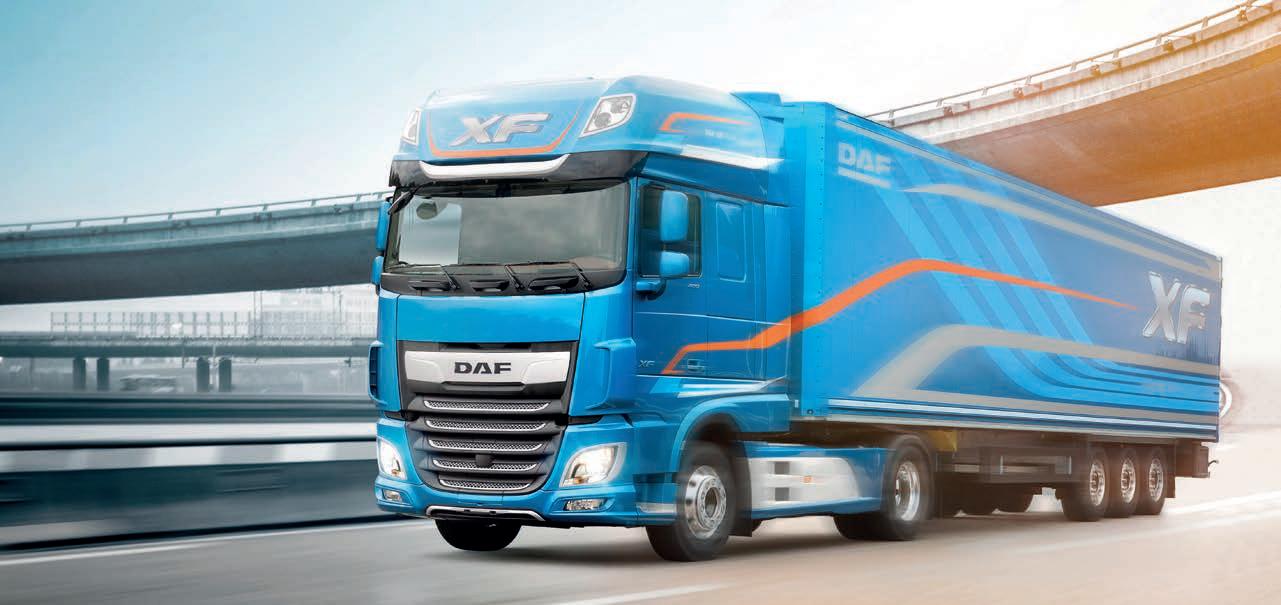
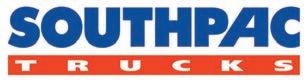
96-98 Wiri Station Road PO Box 76463 Manukau City, Auckland, NZ PHONE (09) 262 3181 FAX (09) 278 5643
NORTHLAND
Mitchell Redington 021 555 326
AUCKLAND
Steve Willcocks 027 525 0015 Mitchell Redington 021 555 326
WAIKATO
Adam McIntosh 027 603 1023 Tim Finlay 021 452 805
BAY OF PLENTY - GISBORNE
Tim Finlay 021 452 805
EURO 6 DAF XF
TARANAKI
Adam McIntosh 027 603 1023
HAWKE’S BAY – MANAWATU – WANGANUI – WELLINGTON
Mark O’Hara 027 2466 954
SOUTH ISLAND
Mike Gillespie 027 4322 491 Chris Gray 027 2816 840 Steve Herring 021 377 661 FIND OUT MORE WWW.SPT.CO.NZ TD31844
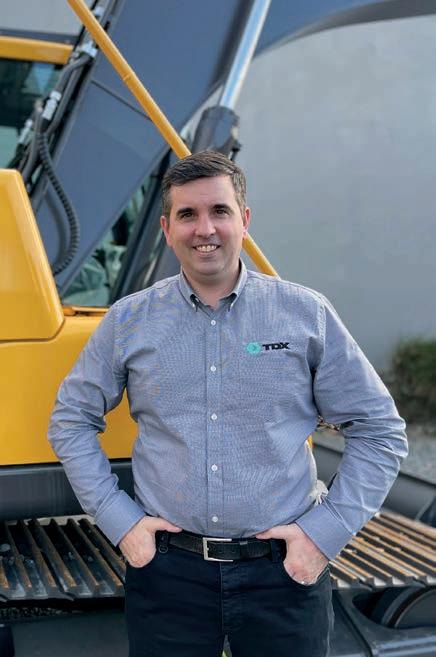
Left: TDX directors and TransDiesel founders Alister McLaughlin (left) and Steve Wooff. Above: Newly appointed TDX CEO Colm Hamrogue.
TDX - a new name in heavy machinery
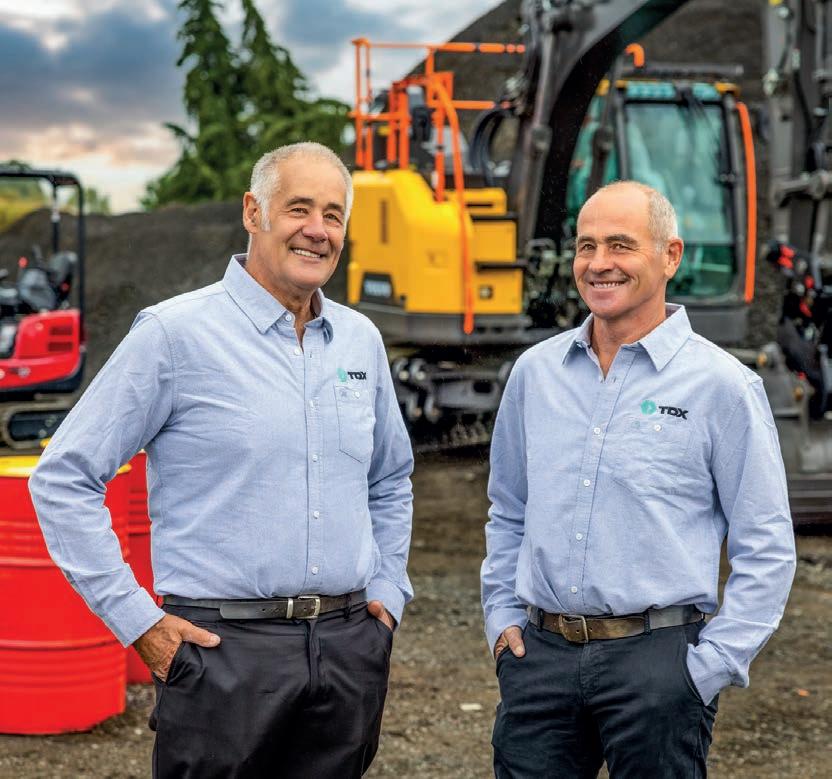
THERE’S A NEW NAME BACKED BY 40 YEARS OF
experience in the local heavy machinery industry.
TransDiesel, a leading supplier of construction equipment, diesel engines, transmissions and lubricants products has rebranded as TDX as the company looks to continue expanding its nationwide operation.
“Our continued goal of delivering exceptional customer experiences as well as a focus on technology, innovation and sustainability are key drivers for this update to TDX,” says Colm Hamrogue, CEO.
“It marks an exciting opportunity to develop the business and prepare the brand for opportunities over the coming decades.”
TDX employs almost 300 people across a nationwide network of 18 branches and has grown from small beginnings in the early 1980’s to an annual turnover of over $200m. It began the rebranding exercise 10 months ago and launched to the public on May 19.
“The evolution to TDX reflects our maturing as a company, one which had an initial focus on diesel engines and transmissions, to one which now partners with some of the world’s biggest and most recognisable names, including Volvo and Yanmar construction equipment, Shell lubricants as well as Perkins, Sennebogen, Kohler and Allison Transmissions,” Hamrogue says.
One consideration which remains very much front of mind for the TDX team is an overwhelming desire to retain a Kiwi-centric focus. The TDX name and logo is accompanied by the tag-line: `World Class Experience. Local Know-how.’
“We recognise and respect 40-years of heritage and are enthusiastic to build on this legacy for the next 40. Above all else, we want to reinforce that TDX is local,” says Hamrogue.
“We’re locally owned, assist locals and want locals to succeed. Our customers know and trust us, that’s something that is never going to change.”
The fresh identity was spearheaded from within the company and involved consultation with staff, customers and suppliers.
“The new name and logo is a nod to the foundations of our brand, a promise to customers and commitment to add value to our partners,” said Marc Warr, Marketing Manager.
“We’re confident that we are remaining true to our heritage, at the same time making a positive and future-focused statement that will stand us in good stead for decades to come.”
The design of the new logo also holds particular significance.
“The arrow illustrates moving forward together with our customers and the hexagon demonstrates the importance of partnership between our people, customers and suppliers,” says Warr.
“As for the ‘X,’ it represents the special customer-focused difference we’re renowned for, a world-class service experience we’ve made our own and will continue to deliver into the future.”
The new branding is being progressively introduced on all sites through to December as well as on vehicles and uniforms. T&D
New technology for Actros

THE LATEST MERCEDES-BENZ ACTROS MODELS WILL
introduce Kiwi customers to Level 2 autonomous driving technology.
Mercedes-Benz Trucks new Active Drive Assist enables SAE Level 2 partially automated driving capability; a first for New Zealand heavy trucks.
The innovative driver assistance technology becomes an optional feature following a 1.2-million-kilometre validation programme that involved 15 trucks in Australia and five in New Zealand.
Active Drive Assist helps to actively steer the truck and keep it in the centre of its lane, although the driver is still required to hold the steering wheel.
It is one step ahead of some current systems that can push a truck back into the lane should it wander out. Active Drive Assist actually helps to steer the truck in the first place and aims to prevent it getting out to the edge of the lane. The Lane Keeping Assist system is proactive rather than reactive.
It does this by using cameras to monitor lane markings and uses that data to help operate the electro-hydraulic steering system. Drivers can overrule Lane Keeping Assist at any time and also turn off the system.
Active Drive Assist uses an electric motor located on the steering box to provide assistance in addition to the standard hydraulic power steering. It not only helps keep the truck in the lane, but also provides more assistance to the driver and improving manoeuvrability, especially at lower speeds.
Mercedes-Benz Trucks Australia Pacific Director, Andrew Assimo, says drivers will appreciate Active Drive Assist technology.
“Mercedes-Benz Trucks’ Level 2 automation makes life easier for drivers and boosts safety by helping reduce fatigue,” Assimo says.
“The feedback from our validation programme has been overwhelmingly positive from drivers who can really appreciate the benefits of the system after experiencing it first-hand.”
Mr Assimo says the Level 2 Automation system is not taking control away from drivers as they are required to hold the steering wheel at all times and must be prepared to take over at any stage.
“This is a driver assistance feature, not a driver replacement feature,” he says.
“Mercedes-Benz is always advancing new technology to boost safety, reduce fuel consumption and emissions and improve the experience of the driver, which is why we have introduced Active Drive Assist as an optional feature,” he says.
While Mercedes-Benz Trucks offers features such as its Level 2 Automation and innovative Mirror Cam feature as options, a suite of advanced safety features is standard on every truck its sells.
Active Brake Assist 5 includes an Advanced Emergency Braking System (AEBS), adaptive cruise control and lane departure warning.
“Mercedes-Benz has long been leading the pack when it comes to fullyintegrated active safety systems in Australia and New Zealand and we intend to continue this leadership with features such as Active Drive Assist,” Assimo says.
Other key technology introduced by Mercedes-Benz Trucks includes high resolution Multimedia Cockpit tablet screens and Predictive Powertrain Control, which uses GPS and topographic information to optimise gearshifts and maximise coasting to save as much fuel as possible. T&D
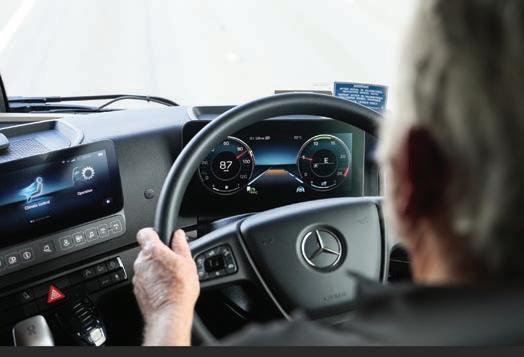
Firth goes electric
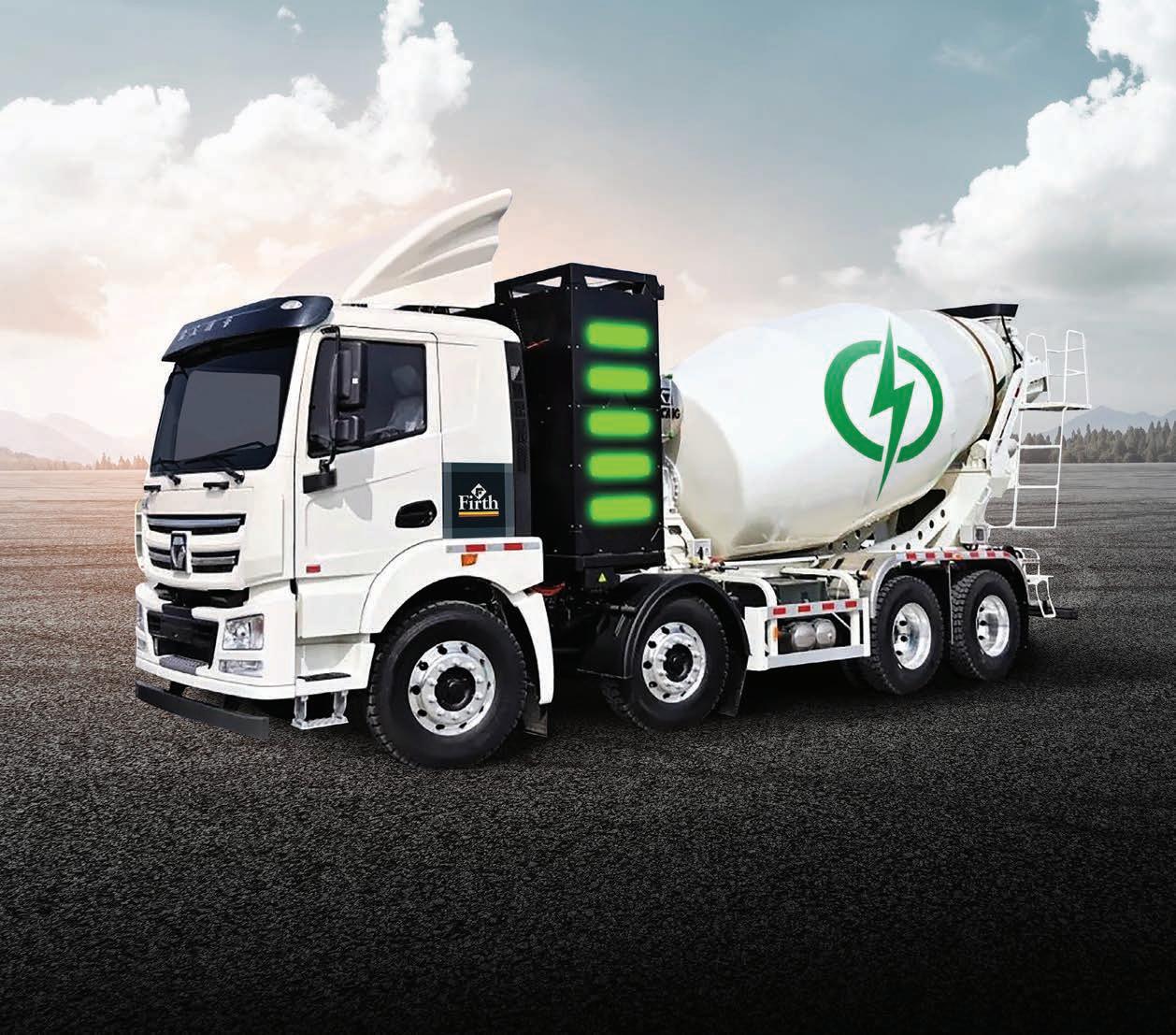
NEW ZEALAND’S FIRST EV
concrete mixer will go to work with Firth near the end of this year.
Based on a XCMG E700 8x4 battery-electric truck supplied by Auckland importer Etrucks, the concrete truck will operate from Firth’s Manukau plant and make deliveries around the Auckland region in a trial to evaluate its potential.
The truck is partially funded by a grant from the Low Emission Transport Fund (LETF) administered by the Energy Efficiency and Conservation Authority (EECA).
It’s part of the same round of LETF grants announced earlier this year that will also see Fonterra trial a similar 8x4 XCMG E700 as a milk tanker while Mainfreight will use a 6x4 E700 on an Auckland-Hamilton inter-city transport project.
The fund supports the demonstration and adoption of low emission transport technology, innovation and infrastructure to accelerate the decarbonisation of the New Zealand transport sector.
“EV vehicles are the future of motor vehicle transport and we have seen great innovation in cars, and trucks are the next logical step as the technology is catching up to bigger chassis sizes,” says Cameron Lee, Firth General Manager.
“We are making great strides in our decarbonisation of the industry and current diesel engines are a significant contributor, and as a result for us to be able to remove the diesel component we are contributing to our sustainability goals.”
The XCMG truck is equipped with a 5 cubic-metre mixer bowl and is forecast to have an operating range of about 160km on a fully charged battery.
“We are always keen to give things a go and have an open mind towards testing and trying all sorts of systems, processes and equipment as well as being committed to continually improving and innovating in all forms,” says Lee.
“There will be internal analysis of performance, capacity, and availability with the next step to look to expand the trial further to other metro centres.”
Lee says Firth’s customers are increasingly requesting more sustainable options
“This is increasing month on month in all forms, whether vehicle, concrete trucks, or footprint,” Lee says.
Firth says the truck is scheduled to arrive in New Zealand in October.
Among the goals of the trial is gathering information on the potential for EVs in specialised transport roles and for Firth to understand the intricacies of operating EV trucks to maximise fuel and carbon savings.
The EV concrete mixer trial will also see potential challenges in the areas of scheduling, operation, and possibly legislative requirements. T&D
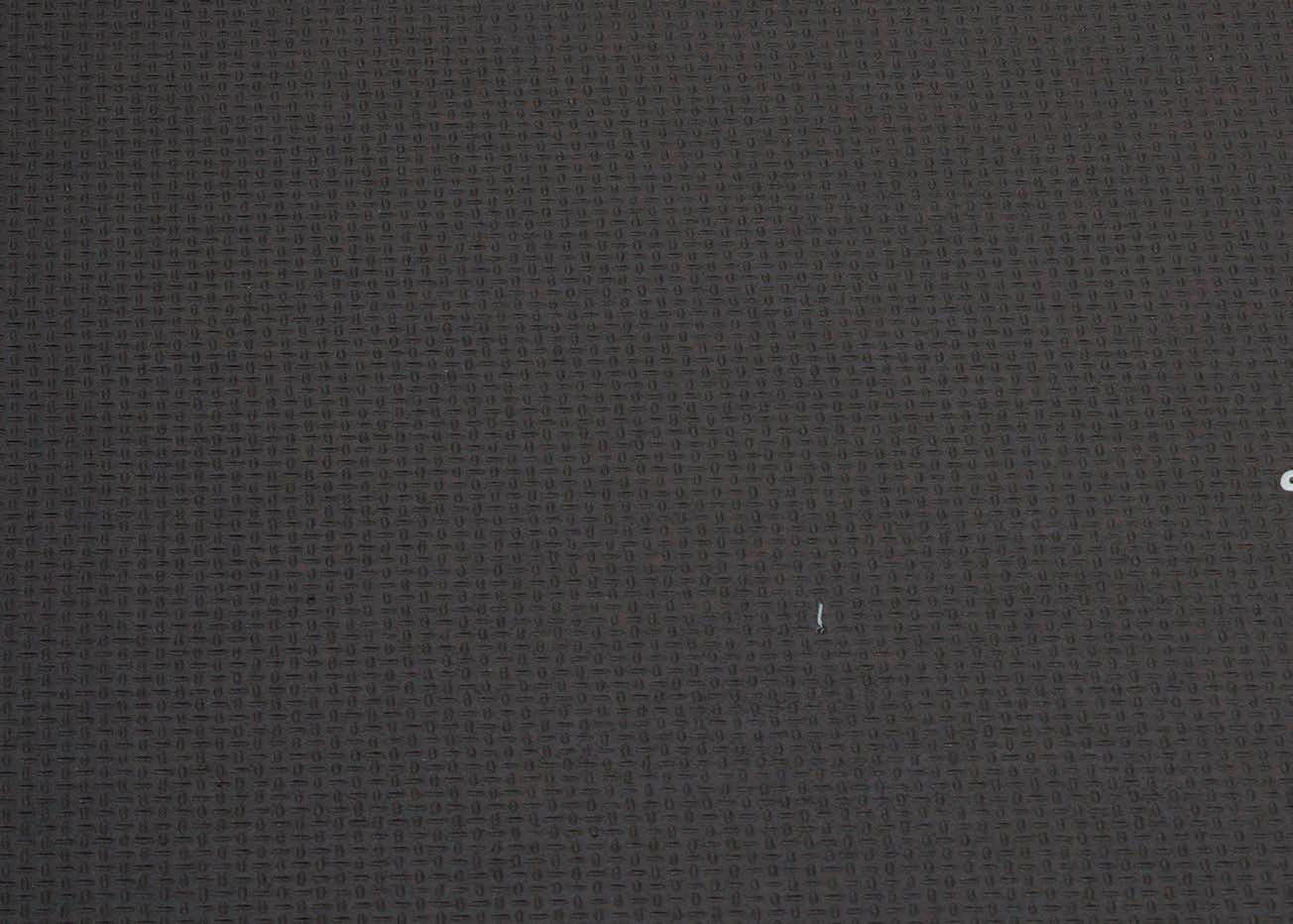
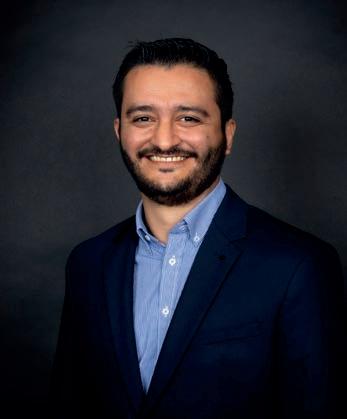
Scania Assistance expanded
SCANIA NEW ZEALAND HAS
upgraded its nationwide Scania Assistance programme.
The bespoke emergency assistance service –which began operating here in a limited capacity last year - now has the support, resources and expertise of the global community of Scania Assistance.
Rafael Alvarenga, Scania New Zealand managing director, says this upgraded service will make roadside servicing more efficient and effective.
“A significant feature is that workshop teams now have access to the Scania Assistance app, Scania On Scene (SOS), which gathers information about customers and cases on a single digital platform.
“For the customers this means one, clear point of contact direct with the workshop with SOS providing a better communication platform with technicians in the field. The app is also used to secure technicians’ wellbeing and safety during what are often remote and afterdark roadside missions.”
Alvarenga says Scania experienced a 110% increase in local truck sales last year, so its commitment to service and support must reflect the growing market share, which has increased from 6% to 16% in the last two years.
“We’ve also worked hard to increase our national network of service centres with more than 30 regional workshops providing fantastic round the clock service. However, given the many remote and rural routes our trucks service 24/7, Scania Assistance is a very important complement to the workshop service and our customers’ peace of mind,” Alvarenga says.
Project Manager for the Scania Assistance launch in New Zealand, Colin Bowden, says the service is staffed by a strong team who understand the local industry and customer needs.
“We’ve trained nearly 70 technicians and service-minded professionals who now have access to these very comprehensive Scania systems and vehicle diagnostics,” says Bowden.
“Wherever any of our customers are, Scania Assistance will be available 24/7 year-round. With one call they will be in touch with a professional service coordinator who knows their Scania vehicle and can make things happen faster, maximising the customer’s up-time,” says Bowden.
Scania’s national spare parts warehouse currently stocks more than 13,000 individual parts contributing to an impressive 94% parts availability of all customer needs. T&D
Rafael Alvarenga
TRANS-TEX 220 NEW ZEALAND’s TRUSTED TRUCK and trailer DECKING
EUROPEAN BIRCH PLYWOOD - Certified to withstand the most demanding applications
12mm / 9 ply 2440 x 1220 2440 x 1525 2440 x 1850 3050 x 1525 3650 x 1850
18mm / 13 ply
2400 x 1200 2440 x 1220 2440 x 1525 2440 x 1850 2600 x 1900 3050 x 1525 3650 x 2000
21mm / 15 ply
2400 x 1200 2440 x 1220 2500 x 1500 4000 x 1500 3650 x 2000
15mm / 11 ply
2440 x 1220 2440 x 1850 3050 x 1525 At Roadmaster, we only use Plytech Trans-Tex 220. It’s simply the best product available in the country. It gives us peace of mind, adds great value, and the service and support we get from the guys at Plytech is first-class.
Colin Patchell CEO Roadmaster
Australian eCanter trial
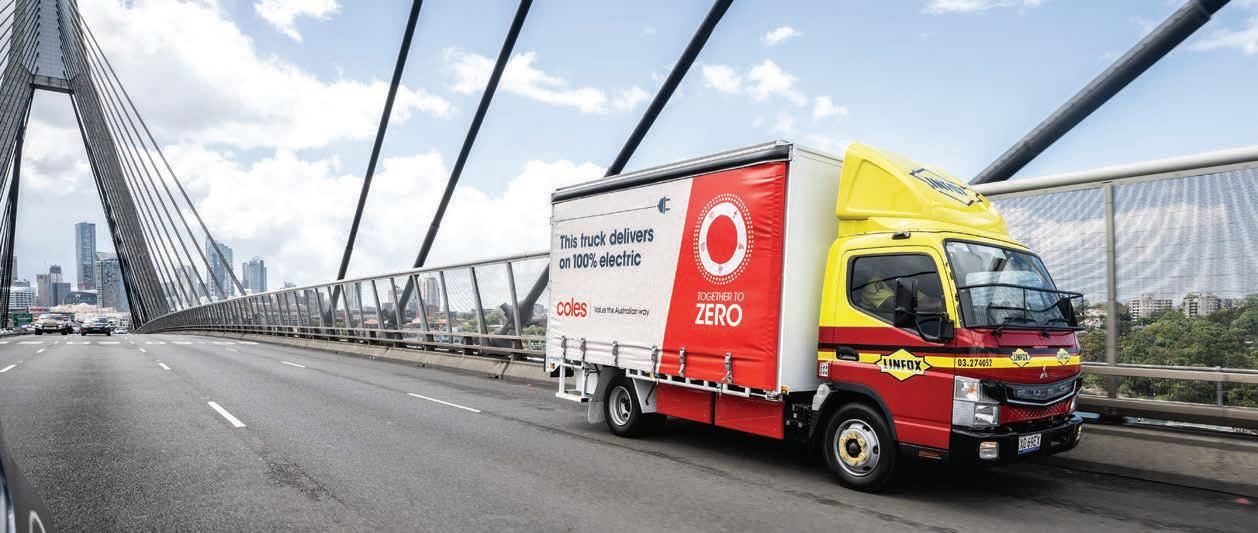
AUSTRALIAN SUPPLY CHAIN LEADER LINFOX LOGISTICS
now has six electric trucks in operation with major customers.
A Fuso eCanter is the latest addition to the Linfox Logistics EV fleet in partnership with iconic Australian retailer, Coles.
The eCanter is servicing several Coles stores in New South Wales, loading products from the Eastern Creek Distribution Centre for delivery to Coles supermarkets and new format Coles Local stores.
Based on anticipated usage, at least 60 tonnes of carbon dioxide equivalent emissions (CO2) will be avoided annually with this vehicle compared to the same size Euro 6 diesel powered truck. The emission-free Fuso eCanter is powered by 100 per cent renewable electricity.
The electric vehicle is an important step towards Linfox and Coles’ shared sustainability goals, highlighted by Linfox’s ‘Act Sustainably’ strategic promise, along with Coles’ ‘Together to Zero’ strategy.
“As a leading logistics provider that has traditionally relied on fossil fuels to transport goods, Linfox has made a commitment to find alternative sources of energy to power our customers’ supply chains,” said Linfox Executive Chairman, Peter Fox.
“Working in partnership with a trusted Australian retailer such as Coles, that connects customers with products from thousands of farmers and suppliers, is where the switch to electric vehicles can make the biggest difference.”
Linfox will use findings from this trial and its other electric vehicle trials to better understand how further scalable solutions can be integrated across the distribution network in Australia. T&D
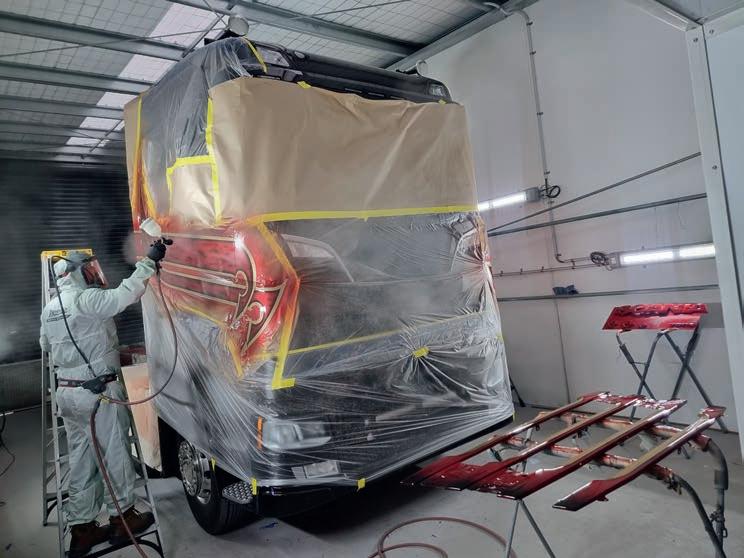
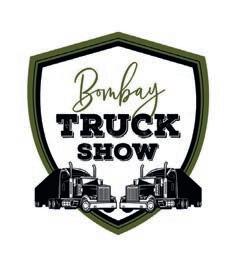
Growth plans at Booth’s Group
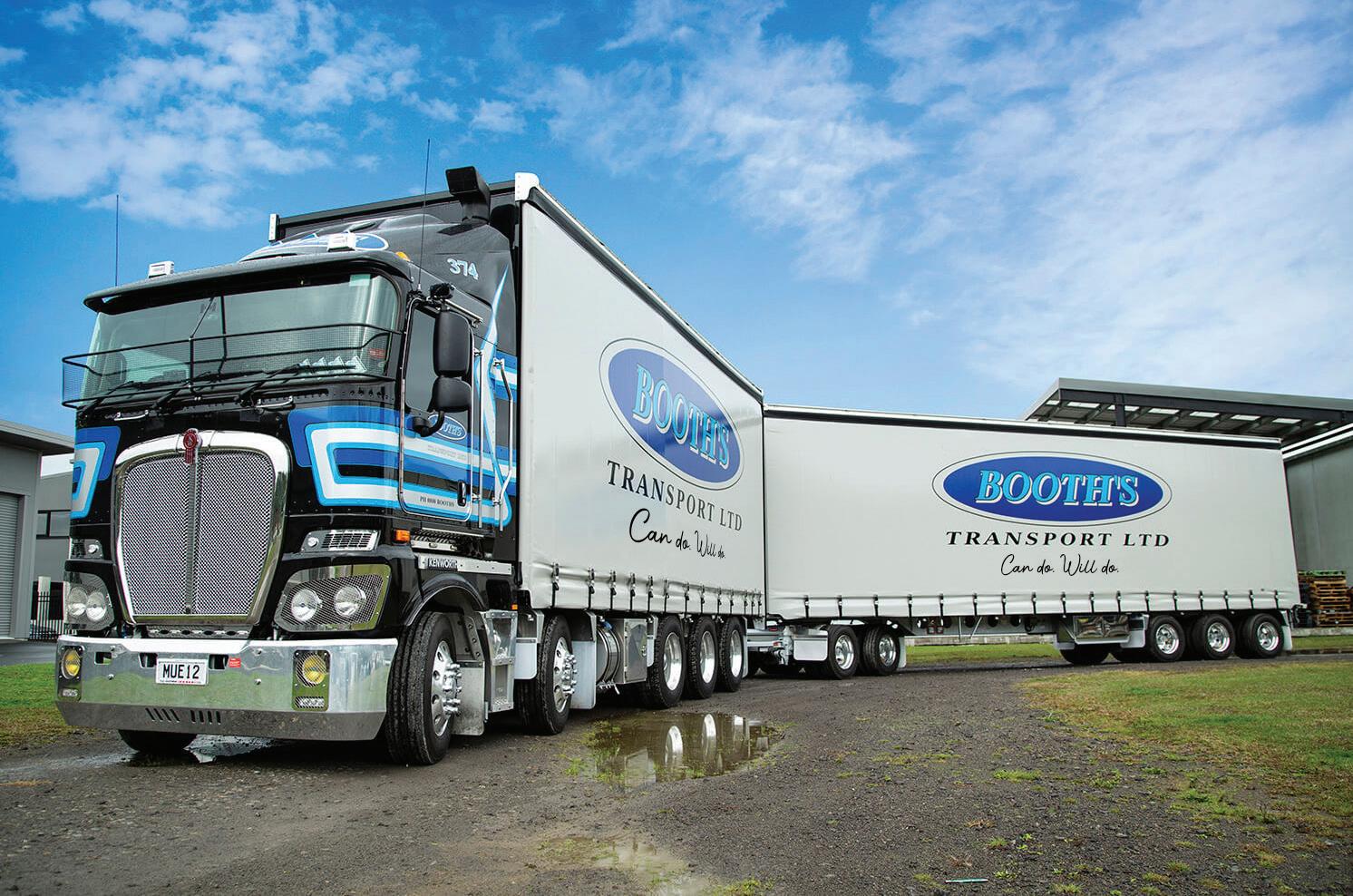
RECENT GROWTH AND AMBITIOUS
goals at the Booth’s Group of companies (Booth’s Transport, Tomoana Warehousing and The Produce Connection), has led to three senior management appointments.
Newly appointed Group Chief Executive Officer (CEO), Dallas Vince, joined Booth’s earlier this year bringing with him extensive experience in the freight sector both in New Zealand and abroad. Prior to taking on the Group CEO position, Vince held a number of senior leadership roles within Goodman Fielder, Halls Transport, and TIL/Move.
Scheduled to join Booth’s Group in July is Clive Jones, current General Manager of MTD Trucks, New Zealand’s sole distributor for Volvo trucks and buses, as well as Mack trucks.
Jones has over 30 years’ experience in the sector, having had roles including sales, driver development, national sales management and more recently as General Manager at MTD. He has served the Volvo Group of brands in various roles for 20 years.
Jones’ role at Booth’s will be Group Commercial Manager, with responsibilities for aspects of fleet procurement and organisation, as well as management of a team focused on safety and efficiency.
“We are delighted we have been able to secure Clive to join our team and he will add enormous value, particularly with his experience in the industry and the relationships he has forged along the way”, says Dallas Vince.
The third appointment sees Dean Aldred in the newly created role of Chief Information Officer (CIO) for the group. With more than 25 years in IT management, Dean joined following eight years with the Sime Darby Commercial Group, New Zealand’s importer for heavy truck brands Hino, UD, Mack, and Volvo. Prior to that has worked with leading companies including Dell, Canon, and Unisys.
“Dean has both the IT experience and systems knowledge we need, alongside a practical skill set relating to the heavy transport sector in general. We are excited to have Dean round out our leadership team and drive one of our key focus points for the coming year being investing in our data and customer interface technology,” says Vince.
Booth’s owners and Executive Directors Craig and Trevor Booth made a joint comment on the new appointments.
“We have ambitious goals ahead of us, both within our existing companies but more broadly with our focus to disrupt and lead the market with an even more compelling customer offer.
“Our heritage dates back to the late 1980’s when our father and founding Director, Graham Booth, branched out from carrying his own produce from a farm in Opiki, Manawatu to a quality and diverse fleet working for a broad range of customers. From there it just kept on growing and that’s always been our vision also.” T&D
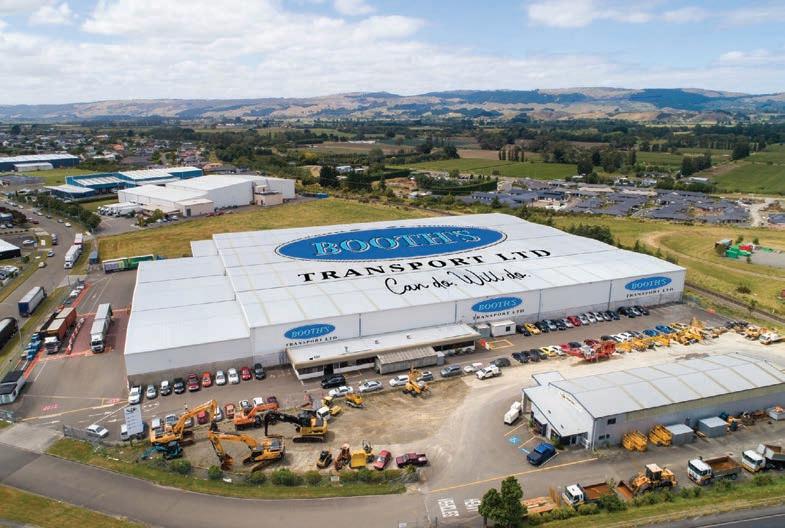