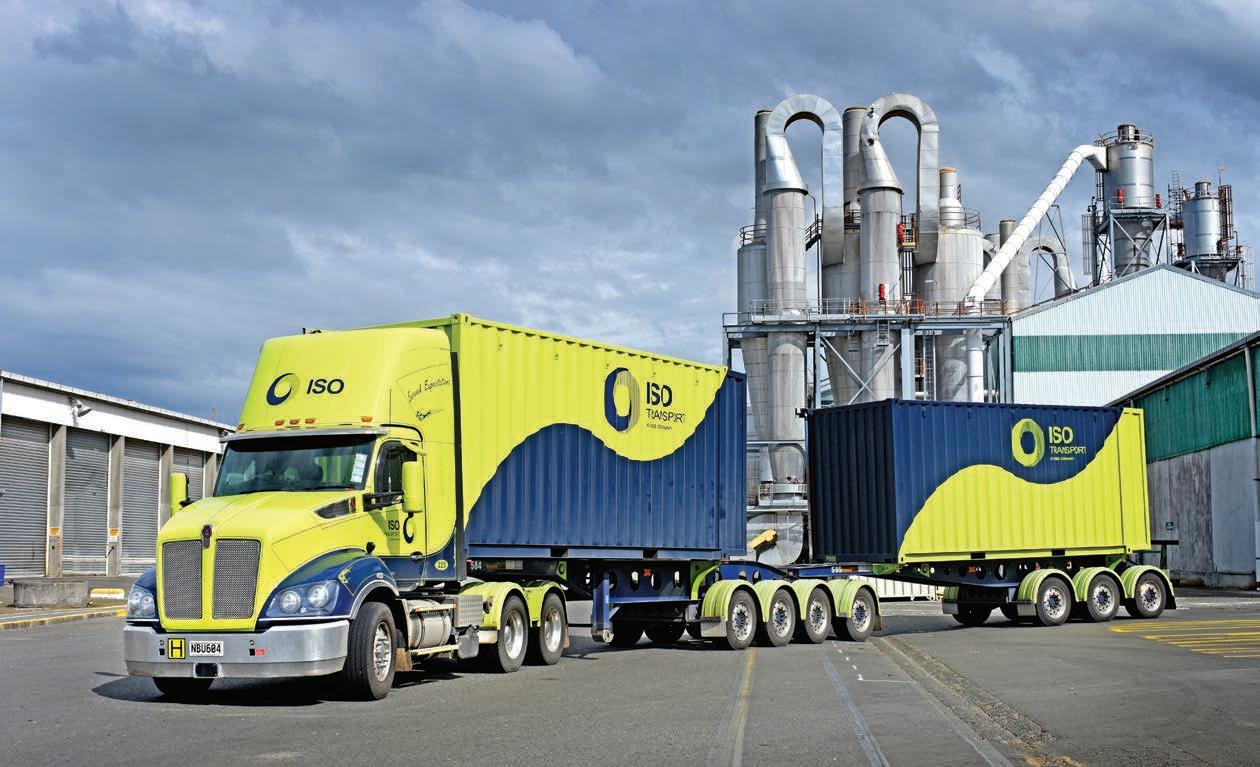
19 minute read
Teletrac Navman Fleet Focus
A load of containerised pulp leaves the PanPac plant near Napier in one of ISO’s versatile Kenworth T410 10-axle units.
SO’S FLEET OF FLUORESCENT GREEN TRUCKS stand out like a beacon and the firm’s profile at New Zealand log export ports is equally prominent. Trucking is one of many cogs in the machine of ISO’s operations in New Zealand, which handles around 60 per cent of New Zealand’s export log trade. It loads over 500 log vessels a year, around 11 vessels a week. While logs — more than 25 million of them a year — feature prominently, ISO also handles a large portion of New Zealand’s kiwifruit exports, around 25% of the country’s pulp exports as well as container, breakbulk and all manner of other import and export operations.
ISO was founded in 1995 as a stevedoring company, which fundamentally is the process of loading or unloading ships. Since then, the company has diversified into other businesses where it has seen opportunities to add value for customers. More often though, it needed to ramp up efficiency in these other operations to keep up with its ability to load ships. It is now a multi-faceted logistics company focused on port operations.
In the good old days loading ships was done with a lot of labour. Crated goods were loaded into cargo nets which the ships’ cranes then hauled aboard. Stevedores then manually stacked them in the hold.
Of course, containerisation transformed much of the business of shipping, and of shipside handling operations. However, if you watch logs being loaded at most ports around the world it won’t look much different to the old-style cargo net process, except they are loading logs rather than boxes.
Logs still arrive at the ship’s side by loader or on a trailer. The ship’s crane lowers strops which are manually wrapped around the logs and the crane hauls them aboard. On the ship they are unhooked, then the stevedoring crew on deck use small diggers with log grapples to line them up neatly in the hold or up against stanchions lining the ships deck, stacking the load height 12 to 15 metres above deck level.
Having to attach strops around logs every few minutes is hard physical work, not to mention hazardous. Releasing the strops, which could easily be under tension, can be even more hazardous, even if the closest workers are reasonably well protected in a machine cab.
Another log loading operator still uses this process in Tauranga. Not ISO. It has revolutionised the loading process for its customers at this port, and in Gisborne, so that it now takes more than 50% fewer people and less time to load the ship and send it on its way. More on this later.
A phrase like “It’s the way we’ve always done it,” stands as an open challenge to ISO whose track record of innovation shows it to be pretty relentless in finding safer, smarter, and faster ways of doing things. That is better for the customers, it is clearly paying off in winning market share, but especially as it is safer, it also benefits staff.
ISO’s business development manager, Neil Weber, says that safety issue drove one of the innovations he introduced when he joined in 2014. In 2013 ISO won its first big contract in Tauranga for marshalling 2.5 million
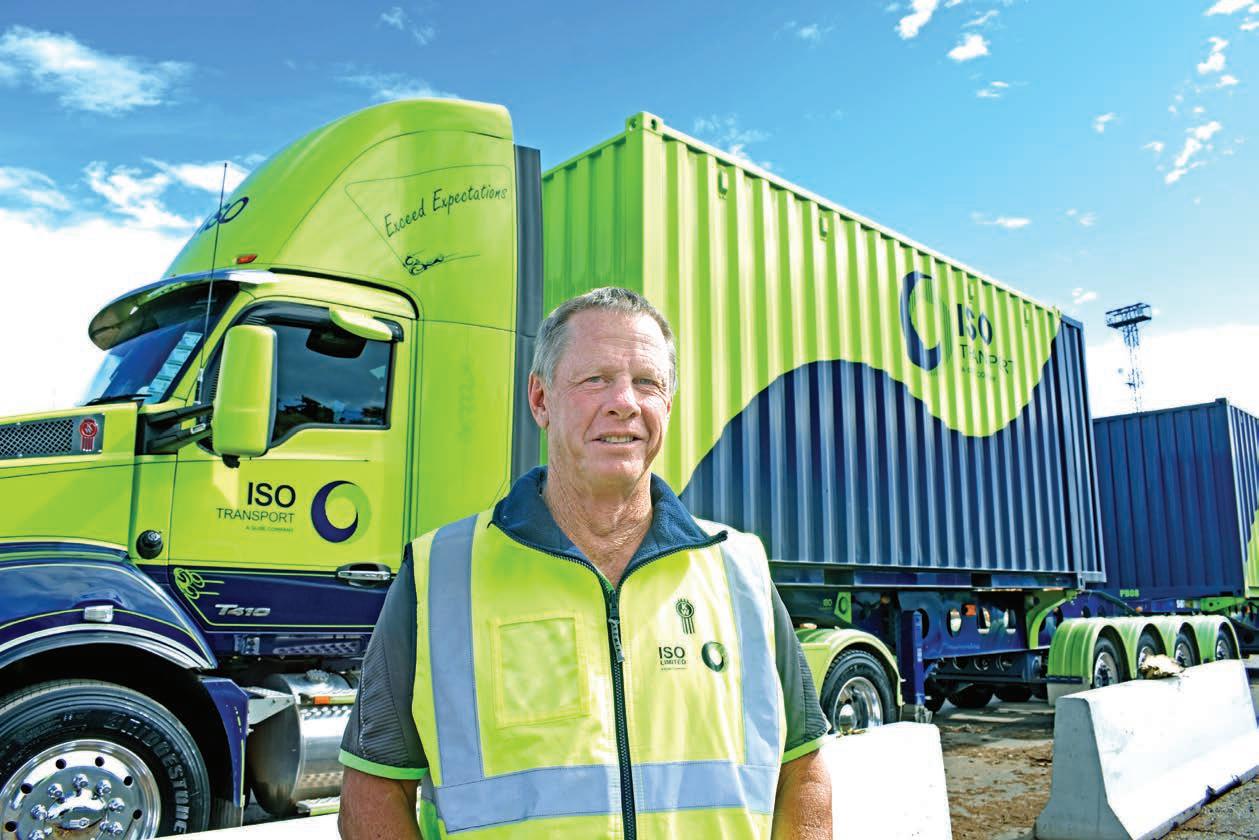
Neil Weber has overseen many of the innovations introduced to the ISO operation in recent years.
tonnes a year of logs — basically compiling ship loads of logs. It had started marshalling in Napier in 2011 but the Tauranga contract was of a different order of magnitude and really got under way just as Weber joined.
The size of the new contract at Tauranga quickly highlighted a problem. Most of the logs are marshalled on the wharves but the client company had to store some logs just over the road in an offport log yard. That meant double-handling and it’s a straight additional cost. At the time ISO was using conventional looking trailers, triaxle ‘bailey bridges’.
However, Weber says, the big issue was the need to repeatedly fling chains over packets of logs and unchain them again after a short shuttle from the off-port yard. It was hard physical and frankly hazardous work.
“We’re a very, very safety-focused company and we don’t want people exposed to hazards or repetitive strain type injury and with throwing chains — there’s always that possibility.”
Even keeping staff prepared to do that job repeatedly was a serious challenge. Finding a solution was a priority as the Tauranga business increased from almost zero short haul logs to around 250,000 tonnes a year.
Weber had made several industry trips to Australia, so he knew that there, as in some other countries, backboards were sometimes fitted to logging trailer units. It wasn’t a big leap from there to modifying a triaxle skel and making use of the container twist locks to install cage sides at either end. The change effectively created log bins, which hold the logs safely for their short journeys. With the logs caged the sides could remain open in the centre for easy loader access. The bin design did away with the use of chains entirely, in one fell swoop solving drivers’ biggest issue and again, it saved time and money.
It seems so obvious now. It’s one of those ideas that make you wonder why no-one thought of this before. Few ports do log shuttles and ISO was so successful in winning business with this operation it now has seven of the nine customers who use the off-port storage in Tauranga.
The trailers were built by Patchell Trailers, and Weber remains a big fan of their work. Clearly the bins are more enclosed than conventional trailers and although it may seem like it would be a solution for longer distance log haulage, it’s not. Weber explains the bin units are heavier than conventional trailers, so they would reduce the payload, and the empty trailers couldn’t be loaded onto the trucks, which is necessary to give the trucks enough
traction on forestry roads.
ISO operates six log bins, two per B-train trailer set, with more coming later in the year. However, even now, that short haul business is not full time, so the trailers can also be swapped out for curtain-sided bins. They are actually modified containers with a curtain on one side, for handling bulk pulp, effectively creating bins suitable for packaged pulp.
New Zealand exports over one million tonnes of pulp each year through the Tauranga and Napier ports, in both containers and in bulk. The pulp is all baled, but the bulk cargo is shifted by clamp forklifts which grab bundles of pulp bales using paddles at each side of the machine.
As Napier is the other port that needs log shuttles the log bins and bulk bins combo is in use there. They can be exchanged in just a few minutes. ISO handles 250,000 tonnes of pulp a year in Napier. Weber says the Super-B units mean they can run 60-tonne gross weight loads of logs and pulp 24 hours a day, five and a half days a week in Napier.
And that’s not the end of the innovation with these trailers. Not all logs are of the same length. While the current bins are fine for logs of 3.9 to 5.9m they have room and payload capacity to handle more 3.9m logs per load. So now Weber and Patchells are developing a sliding mechanism making the back end of the bin moveable to allow two packets to be carried per bin.
ISO started out as a family business initially by the late Les Dickson and then later on by his son, Greg Dickson, and then his son, Liam Dickson. The family run business branched out into trucking in the early 2000s when they won a contract from Carter Holt Harvey to handle 500,000 tonnes of pulp that all came into Tauranga on the rail.
Weber says the 10-truck fleet was an aging “fruit salad” of second-hand trucks in the early years: Mitsubishis, Scanias, Sterlings, bought first for pulp handling (bulk and containers) and then for some container transport between Auckland and Tauranga. A couple of leased Isuzus were bought in around 2015. The first new trucks were two Freightliners mainly for line haul, which are still part of the fleet.
That fleet was also servicing the ISO warehousing and container packing operation in Tauranga, mostly timber into 40ft containers — again mostly short haul, around 5000 to 10,000 containers a year.
The pulp side was around 20,000 containers a year plus 12 to 18 ships a year of bulk pulp.
As the innovations that have transformed the business started to stack up, I asked Weber if he could name a top 10. “Easy,” he said. “This is a shipping business, so they are nearly all three-letter acronyms.”
He rattled them off: “RSMs, ATS, MHC, Pre-Advice, Com 90, MLS, LMS, ShipSys, Log bins and pulp bins, Super-Bs, debarkers… how are we doing?”
More than enough.
One of them was ISO’s move to a fleet upgrade focused on running at HPMV loads.
At the time Weber says there were not a lot of options but the Australian-built Kenworth T410 fitted the bill. They opted for four 6x4s and four 8x4s for container haulage. Weber says a lot of drivers prefer having a bonnet in front of them rather than the cab-over design favoured in Europe, partly for looks and partly for perceived safety, along with easier access, important when you are getting in and out frequently each day. Top: Logs are checked through an ATS (auto tally station) before being loaded onto a ship. Below: ISO ISO manages all of Tauranga’s bulk ship kiwifruit exports on behalf of Tauranga Kiwifruit Logistics and Zespri. Bottom: One of the 550-tonne Liebherr Mobile Harbour Cranes in action at Tauranga.

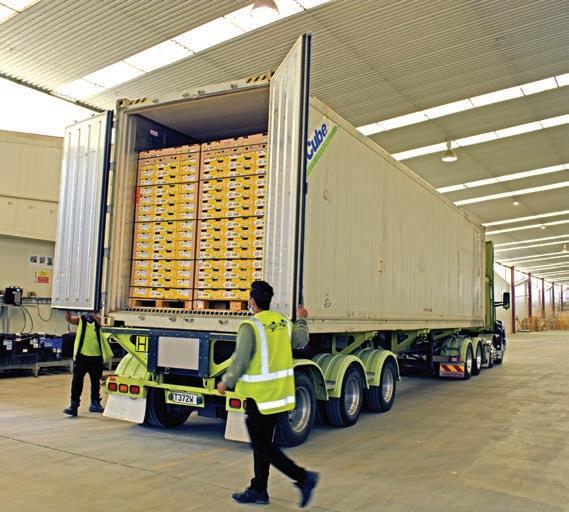
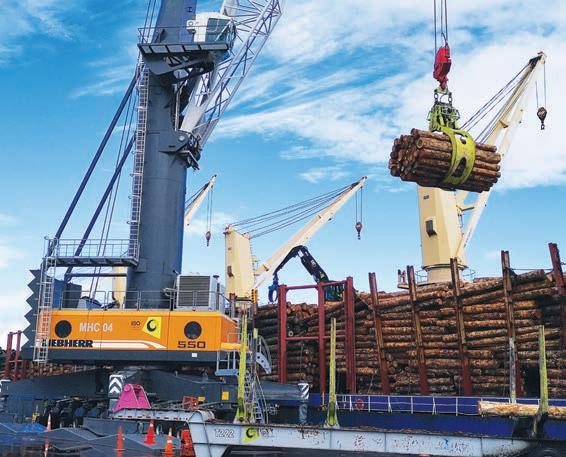
Loading pulp into a ISOI Kenworth at the PanPac plant in Napier.
ISO completed the order in March 2020 and the new trucks were all on the road by the end of November 2020. Weber says the Super-B configuration is a smart move for New Zealand and it reduces the number of loads on our roads for the given freight. The distribution over more axles avoids any increased loading on the road but the extra capacity reduces the number of truck journeys.
“The focus on axle loadings here is much greater than just about anywhere else,” he says.
The fleet upgrade gave ISO a new look on the road, but the company was also making another move to expand its truck business significantly. This change was much less visible.
In January 2021 ISO completed a deal to take over Gisborne-based Williams & Wilshier/Pacific Haulage Limited which runs 100 logging trucks, mostly Kenworths. They will remain branded in Pacific Haulage livery as the company has such a strong legacy in the region. So, with the fleet sorted, ISO got back to looking at other ways to improve the business. Most of the innovations are home grown, but some have simply been ordered and shipped in, like the massive Liebherr MHCs, or mobile harbour cranes that dominate the skyline at Mt Maunganui, their jibs reaching 75m in height.
It takes a company with serious backing — which ISO got when it became part of the Qube group in 2017 — to fund the purchase of not one but six of these 550-tonne monsters, 18 months ago, each of which travels on 80 wheels. Three cranes are in operation in Tauranga and three in Gisborne.
The 12-tonne safe working load capacity cranes are equipped with the world’s largest grapples, specified by ISO, which lift an entire trailer’s log packet at a time. No log wires are involved and there’s no-one around on the loading berth. Queried as to why the largest grapples are found here in New Zealand, Weber says it’s all a question of scale. “We handle a lot of logs here.”
At Tauranga and Gisborne there’s the volume to justify the massive investment in the cranes. The economics only work if there is more cargo to move and the shipping available to take it when the extra speed increases the throughput.
The MHCs can load a ship with over 35,000 tonnes of cargo of logs, faster than the ship’s own cranes — that’s when they are even working. Weber says the frequency of shipboard cranes being inoperative is increasing due to a number of factors, including that they’ve been used for years on all sorts of bulk cargoes and operated by people in ports all around the world with widely differing levels of skill. This is a prime example of ISO taking control of a new area which benefits everyone involved in the process.
The new mobile cranes highlighted the need for another innovation. Traditionally the 30- tonne max ships’ cranes hoisted tracked machines — diggers — aboard to distribute the logs evenly. Typically, being the smaller 16–20 tonne machines, they struggle to keep up with the capacity of the mobile cranes.
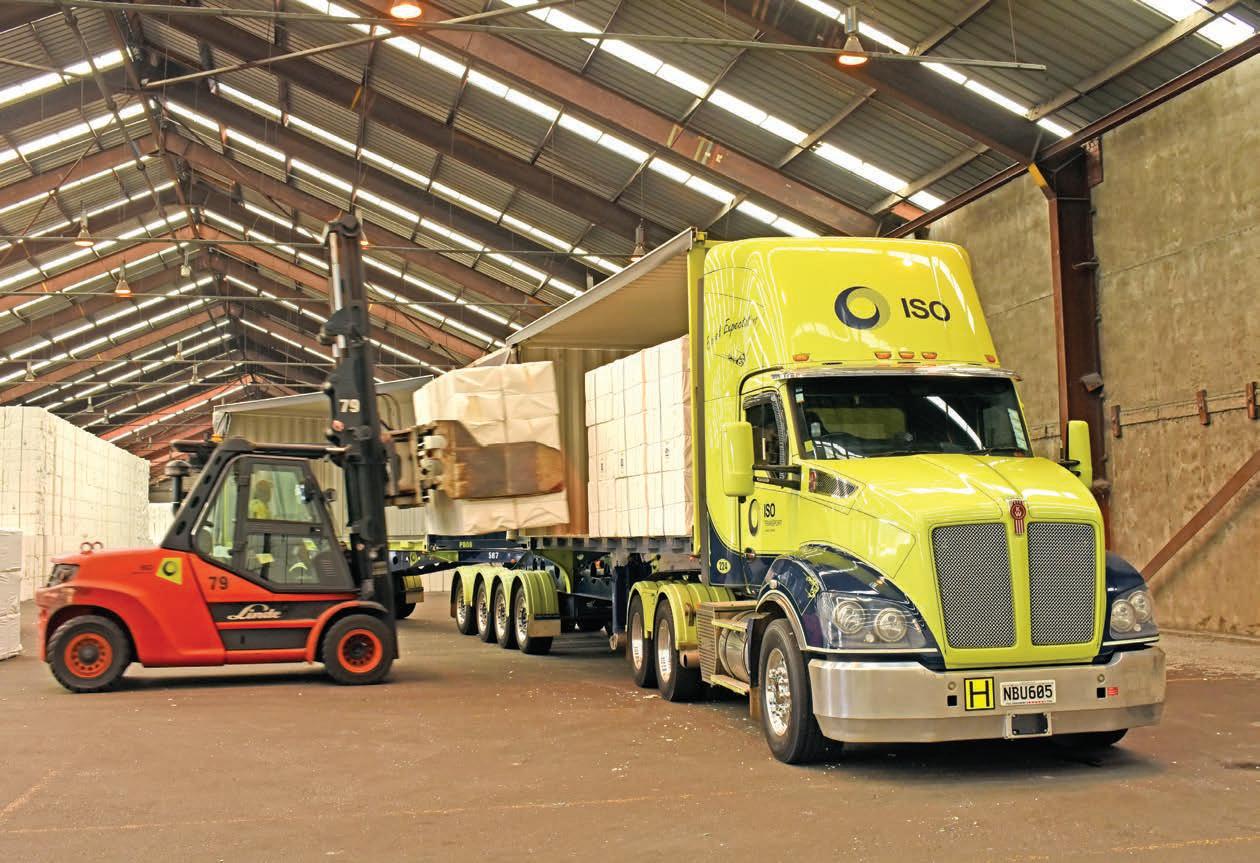
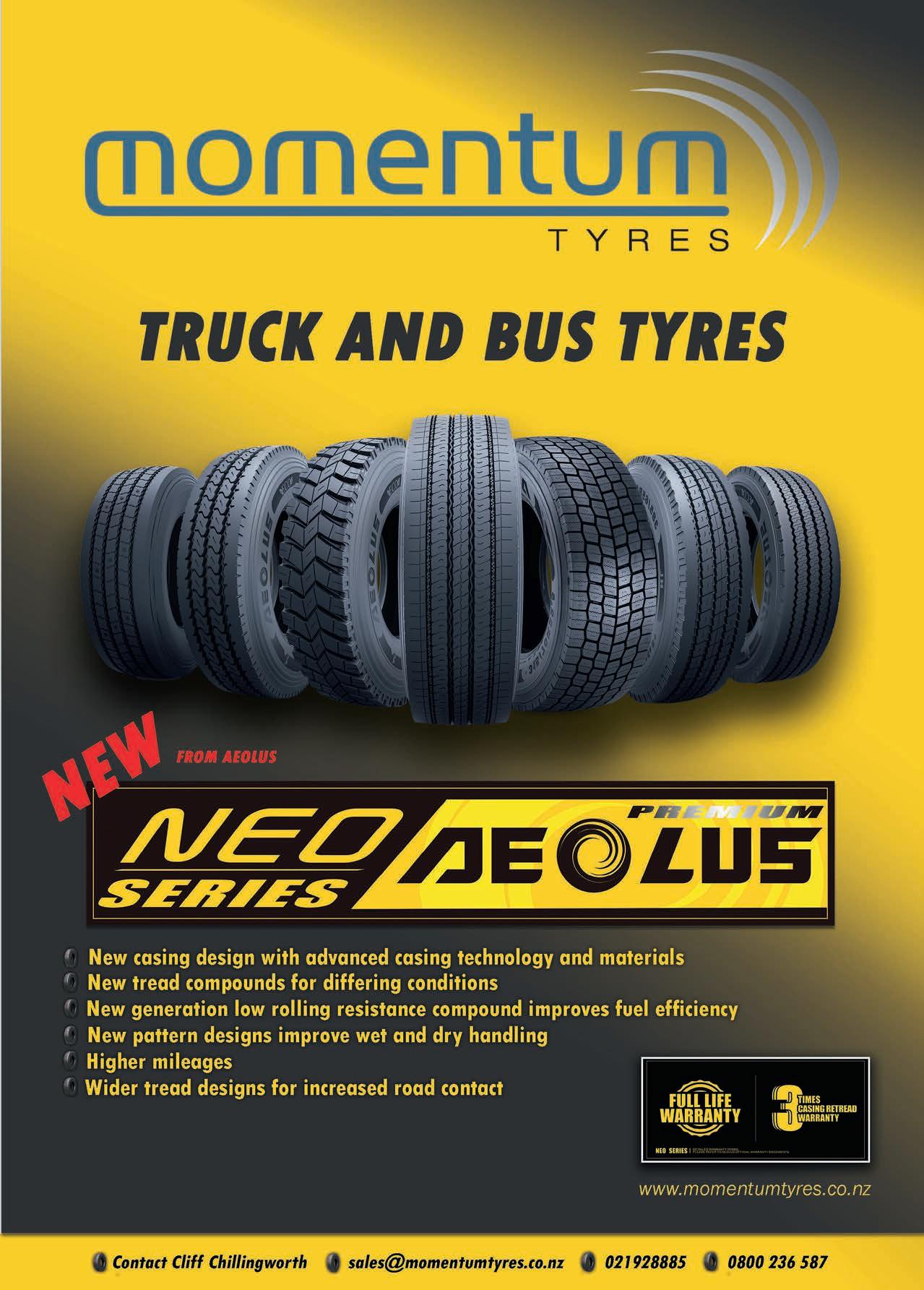
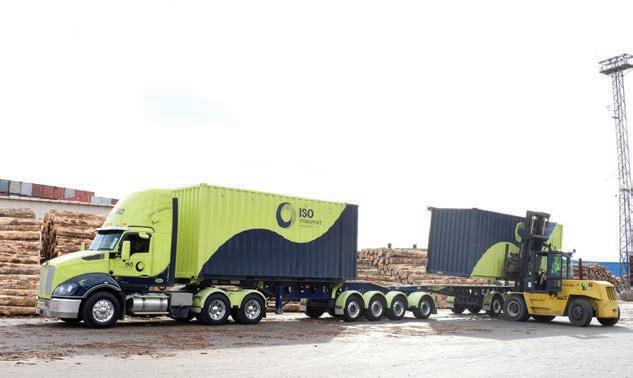


Above: ISO trucks can be quickly converted from carrying containers to having the innovative log cages fitted for short-haul loading work. Far right: Driver Levi Rahui checks the twist locks after the log cages have been fitted into place.
As the mobile cranes can also hoist heavier diggers aboard, ISO is moving to using a 30-35-tonne machine which can handle a bigger grapple and reposition many more logs at a time. Weber also says ISO is also developing a remote-control digger, which a driver can operate from the safety of a room onshore, anywhere.
“That’s really one of the drivers of innovation. We are always looking at the safety of staff and if we think we can find a way of doing the job while making it safer for staff, we’ll do it. Or we’ll take a look at a completely different way of doing things.”
Another bought-in innovation are the Com 90 devices developed in Sweden, another solution to the perennial problem of chaining logs. The Com 90 unit, the first in New Zealand, has both hydraulics and a worm gear built into each stanchion of a log trailer. The hydraulics fling a pair of arms mounted at the top of each stanchion across the load of logs and they grab each other with a simple hook and loop arrangement. The worm gear then pulls the arms down tight, and it keeps up the pressure, hugging the logs even tighter if they settle.
Weber says at around $100,000 per unit they are not cheap, and they have to be mounted on trucks with hydraulics to the trailer. The one unit ISO is running is currently under evaluation.
Other innovations have been developed in house or in association with a partnering company. Robotics Plus is one such partner and one of the
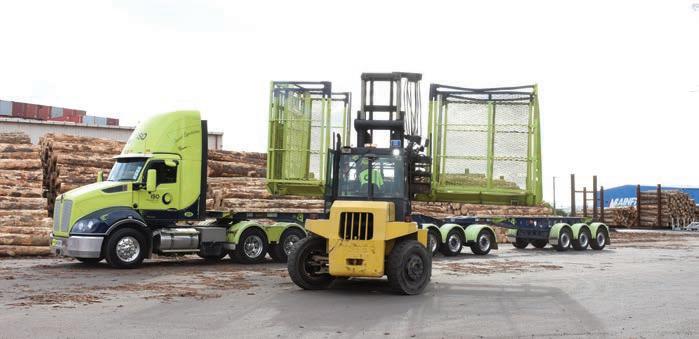
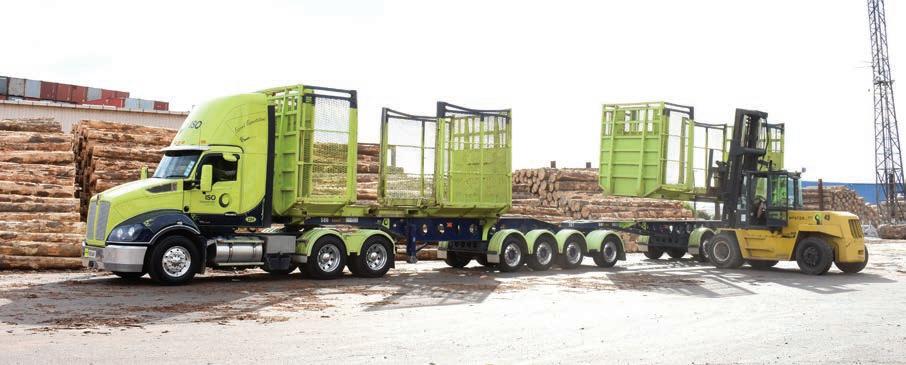

Today every log is digitally scanned for measurements and identification.
big breakthroughs it has been involved with are the RSMs or robotic scaling machines. Three have been installed in Mt Maunganui. There are now 14 machines working in ISO operations with others due to be installed at other log ports soon.
They are an integral part of ISO’s LMS or log management system. Today, every log has to be measured and tracked. When logs are loaded in the forest the driver is supposed to count every log, which is harder than it sounds, says Weber. It was a constant headache, trying to reconcile packets of logs when they arrived at the port.
Now drivers send ‘pre-advice information’ to ISO when they pick up a load of logs in the forest. The logs are graded there, and the large end of all logs receive a painted mark. The driver sends photos of each load to ISO’s pre-advice system, which is unique to ISO, so it knows what’s coming.
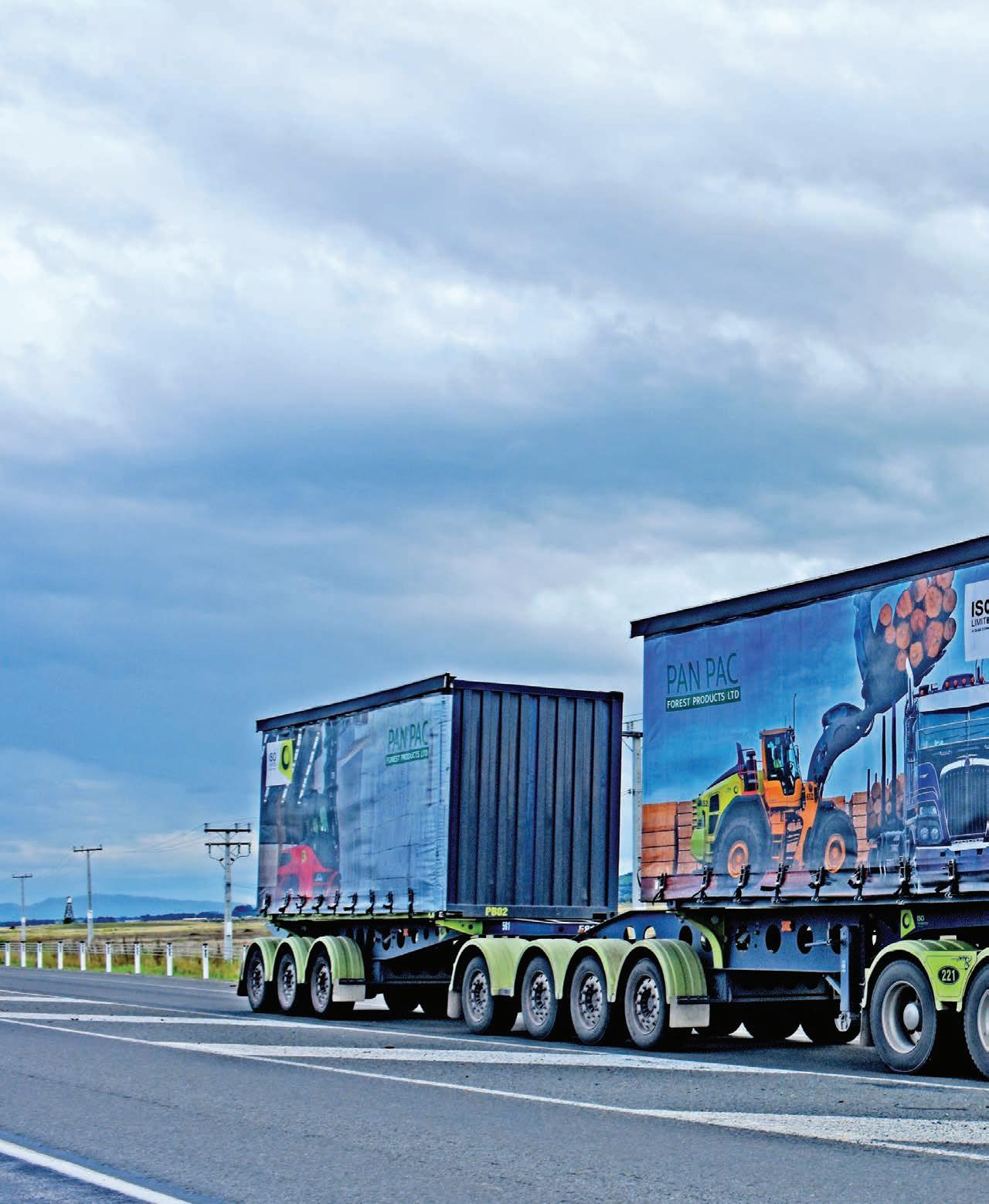
Above: Loading logs in cages hauled by a Freightliner Columbia. Below: Pulp on the move from PanPac near Napier.
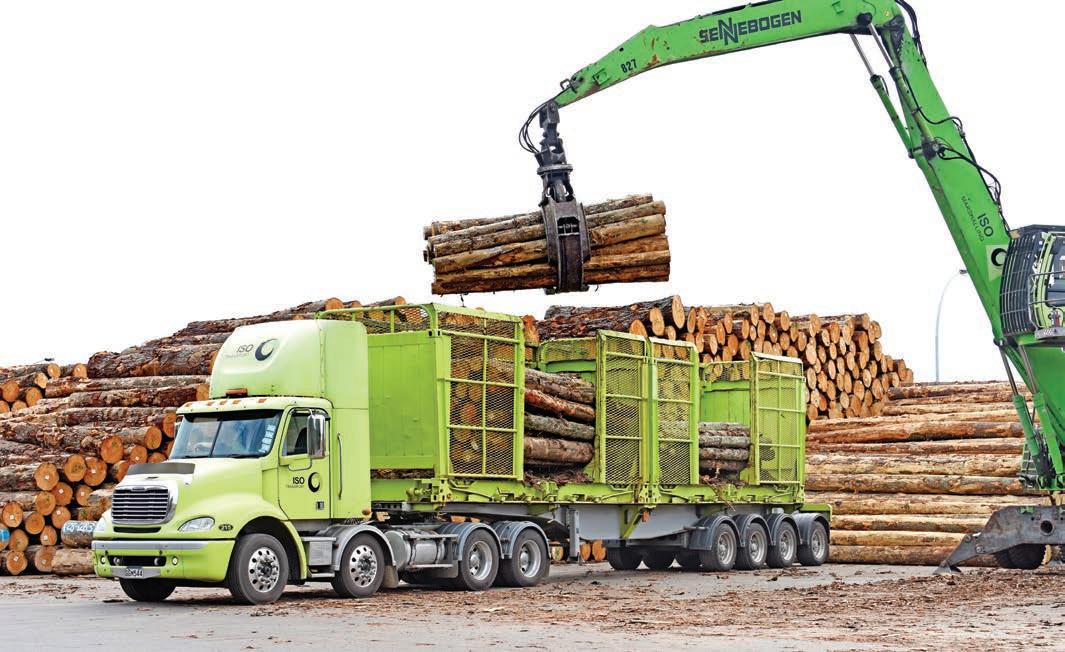

Loading cages at the Napier log yard.
In the past the load would be manually checked when it arrived at the port, and the logs ‘scaled’, that is the small end diameter of all logs would be measured with a ruler and a scanner would record the measurement. The amount of millable timber in each log is obviously important, and that has to be measured at the smaller end.
“In the past it was a process that could see drivers hanging around in a queue at the port for an hour or more depending on a number of factors.”
The first process when a truck arrives at the port is for each log to have a barcode ticket stapled to its small end, a key ingredient of the LMS or log management system. Then the drivers simply drive into the back of a large shed containing the RSMs. They stop under a caged gantry and the RSM’s powered boom laden with cameras rolls down and up between each packet of timber. It scans and photographs all the logs and tickets on both truck and trailer for the scaling software to process every piece.
On the control screen you can see the RSM has automatically measured the dimensions of every ticketed log. In a few minutes the driver is through and heading onto the port to unload. With three lanes in operation, the RSM shed can handle more than 300 loads a day, so there’s virtually no waiting. ISO’s 14 machines are currently processing 1200 loads a day through Marsden Point, Gisborne, Napier, Timaru, and Bluff.
“It’s been a real boon to the transport companies — not that they would ever admit that,” says Weber. “They love coming to ISO; it’s four minutes for scaling every time.”
The E-scaler operator, Midas Te Kakara, who comes from one of several families with more than one member working at ISO, is also happy to admit it was good for him too. A job in a nice warm office beats scrambling about in the rain, measuring logs with a ruler and a scanner.
Some RSM images also came in handy when one of ISO’s customers, a log exporter, received a query from an overseas customer who complained its order of logs of a certain volume turned up about 10 per cent less than ordered. They wanted a substantial discount. As the data tracking is so comprehensive the exporter simply asked ISO for the scans that showed every log in the customer’s order. The complaint was hastily withdrawn. “It must have been some other supplier,” says Weber, with a grin.
ISO also receives 40-50 per cent of the logs it exports through the port of Tauranga by train.
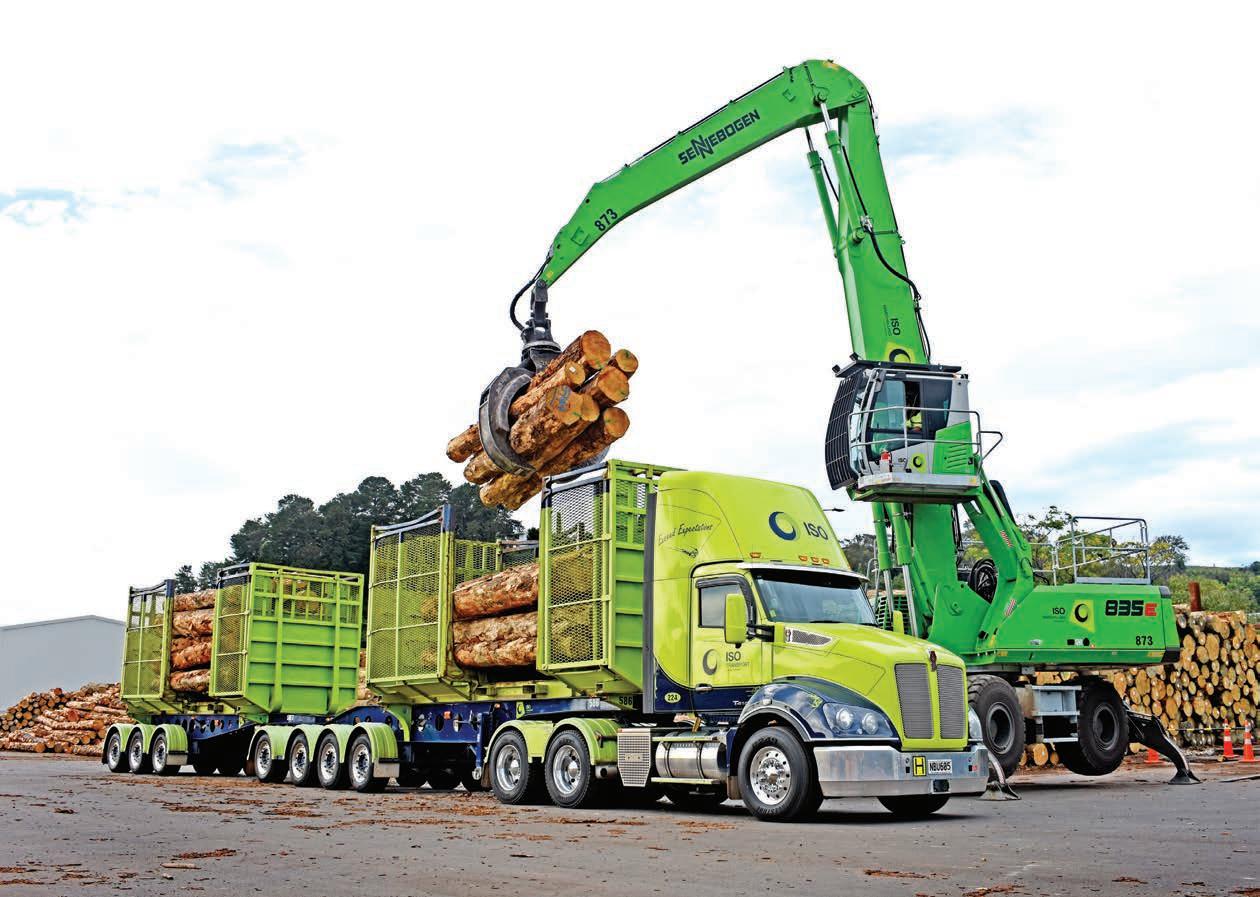
ISO has been trialling a Swedish Com 90 log securing system on this Isuzu at Port of Tauranga.
The track terminates at the edge of the log yards. The train can’t go through the RSM bays, so the measuring process is still done manually, as described above — but not for long. Again, working with Robotics Plus, ISO has developed a mobile log scaler, the MLS. This fully automated driverless machine, which looks like a big square letter ‘n’ on wheels can find the train, straddle the carriages, and roll along the length of the train scanning as it goes.
The space given over to log marshalling yards, and of course the off-port yards, indicate the scale of the marshalling operation required to keep sending a log ship out every day. That’s where another piece of ISO innovation comes in. Shipsys is the ship side equivalent of the LMS.
As the LMS tracks and accounts for every log coming into marshalling from the forest, Shipsys manages the packaging and loading of logs onto ships, ensuring the right consignments go on the right ships to the right ports. And it has a simpler version of the RSM, the ATS. The ATS or auto tally station is a shed containing a drive through scanner which checks every log into a consignment going aboard a ship, again replacing people having to scramble around a trailer with handheld scanners.
At the beginning we mentioned how in the good old days the wharves were swarming with people manually handling cargo. Advances in freight handling have removed much of the physical labour and ISO’s innovations have reduced much of the risk in the tasks that remain. But this doesn’t necessarily reduce jobs; the raw numbers say otherwise. By increasing efficiency and moving into other operations and making them work well too, ISO has increased its staff from around 600 in 2014 to 1100 now. The jobs have changed and become much safer.
It’s almost an afterthought when it takes minutes to drive past the log operation at just this one port, but we end up at TKL’s (Tauranga Kiwifruit Logistics) cool store, run by ISO, where consignments of kiwifruit are marshalled. Here ISO manages all of Tauranga’s bulk ship kiwifruit exports on behalf of TKL and Zespri — scanning pallets into the cool store for night loading and, during the day also loading directly onto the vessel.
As we left the port gates, Weber got a scheduled call to meet a contractor at another large shed sitting on a large yard just outside of the port. It was being upgraded to further refine another part of the loghandling process.
It’s clear there’s always something on the go at ISO. “I’d never get bored,” says Weber. “There’s always something new to do. We’re never satisfied with what we are doing today.
“I personally get a lot of satisfaction from helping make people’s lives better and especially safer. That’s always a big motivation.” T&D
