
12 minute read
Securing the Future
By Colin Smith
T FIRST GLANCE THIS PAIR OF NINE-AXLE KENWORTH
K200s doesn’t look a lot different to other rigs in the familiar Rotorua Forest Haulage (RFH) green and white colours. But look a bit closer and they usher in a new generation of automation and safety for Kiwi logging trucks.
What makes the duo special can be demonstrated in a few moments of hydraulic choreography that will likely grab the attention of anyone who has thrown chains over the top of logging trucks and trailers.
Both RFH K200s are equipped with the Swedish developed ExTe Com 90 log securing system. The system has been used in Sweden’s forest industries for about 20 years and the design is covered by three patents.
Local refinement has been carried out by Evans Engineering in Tokoroa with three trucks completed and a fourth now in build.
With extendable bolsters, integrated lashing arms and a hydraulic tensioning system, ExTe Com 90 automates a significant part of the log securing process. And it also monitors the tension holding the logs in place while the truck is moving and allows in-cab or remote operation.
It’s technology that has already allowed RFH to speed up loading and unloading times on its two units.
But the primary reason behind putting the Com 90 system into use is to reduce the risk of shoulder injuries which logging truck drivers can sustain in the process of throwing chains over their loads.
Evans Engineering design engineer Sam Haines has led the local testing and adaptation of Com 90 to suit New Zealand conditions. He started work on the project in 2018, visited Sweden the following year and developed the first Kiwi unit as a trial at Port of Tauranga for ISO Ltd starting in December 2019.
“When we introduced the system on the first ISO truck moving logs around the streets near Port of Tauranga, I followed it for the afternoon and timed everything. That truck went from 10 shuttles in a day to 22.
“After that successful initial trial at the Port of Tauranga for ISO, RFH approached us with the backing of Timberlands Ltd about implementing the Com 90 system into a HPMV highway unit,” says Haines.
“Timberlands are very safety focused and are proactive about implementing concepts to reduce risk and harm.”
The Com 90 system offers several advantages to logging truck operators.
“Throughout the years the logging industry has relied on chains and wire ropes to secure the logs to the vehicle when transporting,” says Haines.
“These have to be thrown over the packet of logs and manually tightened with twitches or other tensioning tools. The chains can
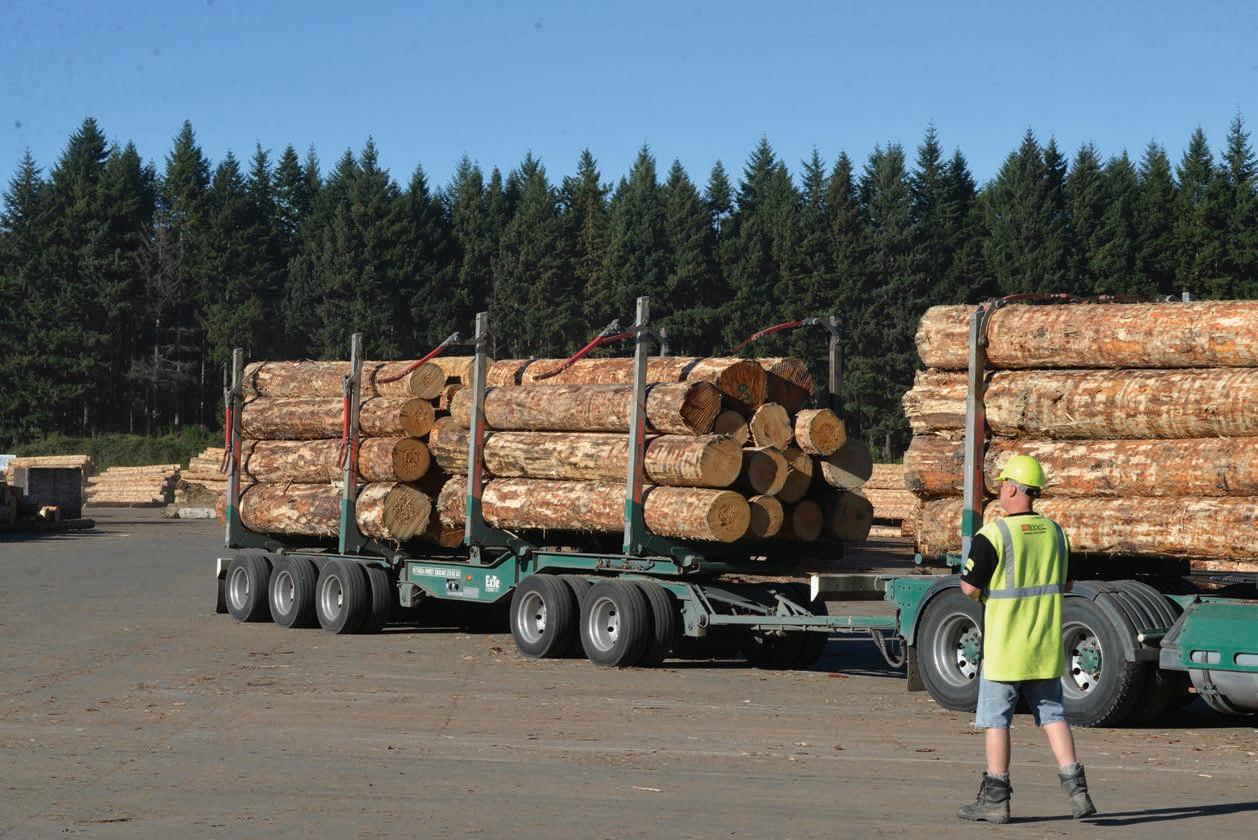
Greg Hose uses the remote to lash down a load of logs with the ExTe Com 90 system.
be quite heavy depending on the size and length. This in turn has caused many injuries to workers over the years.”
The ExTe Com 90 system is a logging bolster that can extend and secure the logs simply by pushing a few buttons.
“The system consists of hydraulics and integrated lashing arms to extend above the height of the packet and then pull down to secure the load with 1.7 tonnes of force. That’s almost two and a half times what a man can do with a twitch and extender bar,” says Haines.
The lashings comprise a nylon webbing strap encased in a durable nylon/rubber outer covering. The bolsters are high tensile steel.
“The system is controlled via a touch screen display in the cab where you can monitor system pressures all the time the truck is moving. An alarm lets you know if the system needs to be retightened,” says Haines.
On the RFH Kenworth’s that simply means stopping the truck briefly and re-tensioning the Com 90 without leaving the cab.
“On some trucks fitted with a continuous PTO you can have the system automatically retighten itself while it’s moving,” says Haines.
“When arriving at a loading site you push a few buttons in the cab and the bolsters will open automatically.
“Once the logs are loaded, you can use the Com90 remote control to close the lashing arms and pull down on the logs.
“When arriving at the unloading site, without leaving the cab you can open the lashings ready to be unloaded from the safety of the cab.”
RFH now has the second and third Kiwi units completed by Evans Engineering. They’re out in the bush and also working from the Kaingaroa Processing Plant (KPP) to destinations including the Red Stag Mill, Kinleith, Kawerau and Port of Tauranga.
At the moment Timberlands regulations require them to also use belly chains but Com 90 is still easing the workload for drivers and saving time. Securing the three belly chains takes only a third the amount time as the nine chains used on a standard three-packet load.
RFH Operations Manager Sam Sargison says the early experience with Com 90 has been positive.
“It’s a learning curve and there have only been a few technical issues,” he says.
Sargison says the system is of greatest benefit where trucks are running shorter (50-80km) shuttle trips.
“However, the benefit isn’t just time. The technology will tell you if your load has shifted slightly and needs re-tensioning but the biggest thing for us is learning about new ways to protect drivers from injury.”
Sargison says there is an awareness the average age of drivers is increasing and reducing the amount of chain throwing – and potentially eliminating it completely – would be beneficial.
“The Com 90 system is something than can help to keep drivers healthy and working in the industry for longer. This system may also make the log transport industry more attractive to a wider range of people.”
Sargison says testing that included five repeated 0.8g emergency braking stops that saw Com 90 easily met the Land Transport safety requirements.
“We had the truck come to a complete stop from 70kph and nothing moved,” he says.
Being able to run without belly chains is a possibility but isn’t considered a priority for the immediate future.
“The goal for the moment is to reduce as much of the manual labour and injury risk as possible and make things more efficient. Beyond that who knows,” says Haines.

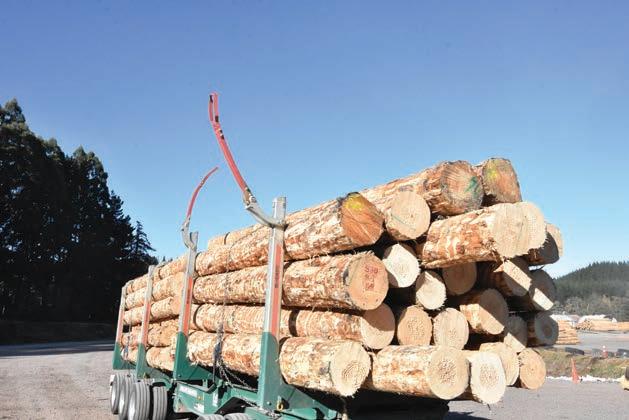
To get the driver’s viewpoint on Com 90 NZ Truck & Driver spoke with RFH drivers Greg Hose and Jeff “Skippy” Hennell.
“It’s definitely a cool system, I really like it,” says Hose who has driven logging trucks for about 25 years.
“It’s a lot quicker than nine chains and you’ll often move up the queue in the chaining zone.
“The loaders do have to be a bit more careful with the bolsters and how it’s loaded is important. The diggers are good because they can place the logs really carefully.”
The 70km round trip from KPP to Red Stag Mill was with `Skippy’, who he began since driving a Com 90 equipped K200 has earned a second nickname.
“They’ve started calling me ‘Watch My Bolsters’,” he says.
That’s because Skippy has been protective of his new Com 90 gear and keen to impress on loader drivers that slightly different loading and unloading techniques are required.
“It’s expensive and I’ve been really careful. I treat the gear like it’s mine,” says Skippy.
“When I first started with it, I wasn’t saving much time because I was asking the loader if they had loaded us before and explaining you can’t push like you normally do.
“The first week took a bit longer but now everyone has got the hang of it and it’s really fast. It can easily save 10 minutes of chaining at both loading and unloading if everything goes to plan.
“I try to get loaded in more of a pyramid shape because of the way the lashings latch together,” he says.
Skippy is driving a 525hp Cummins X15 powered K200 with an 18-speed Road Ranger transmission. He says Com 90 makes no difference to how the truck drives and performs.
The two-month-old K200 runs on a 58-tonne permit. The Com 90 system and the hydraulics that run it have added about 1-tonne to the tare weight.
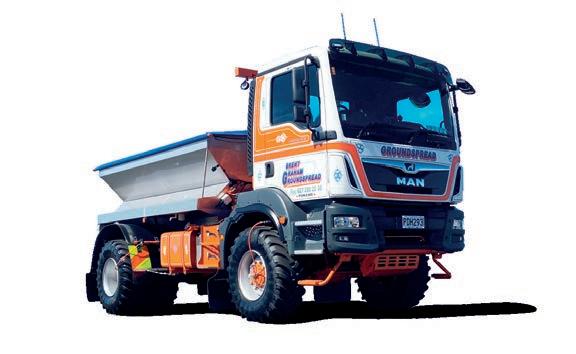
With a Bigfoot With a Bigfoot onboard you’ll onboard you’ll monster any monster any surface Make light work of any surface using the surface OptiTraction footprint with a Bigfoot Central
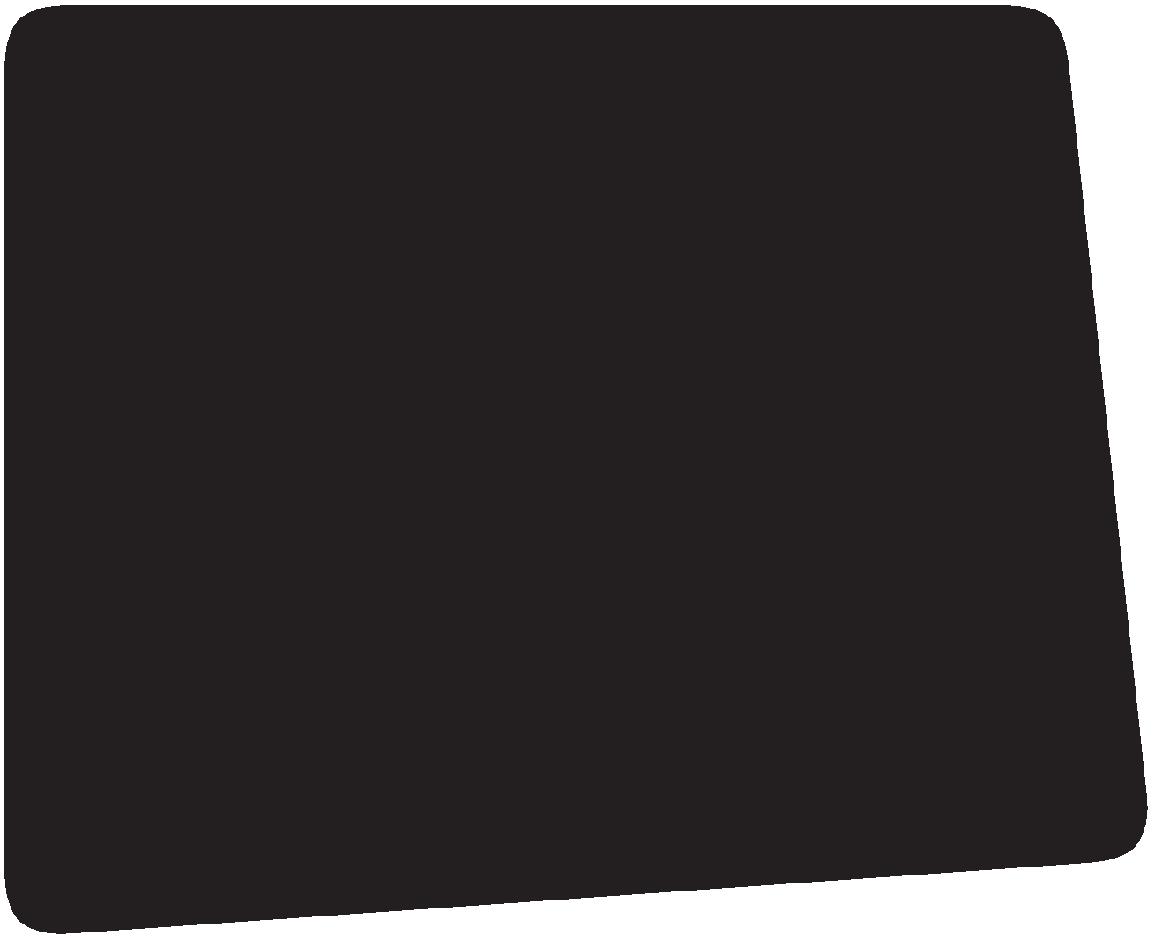
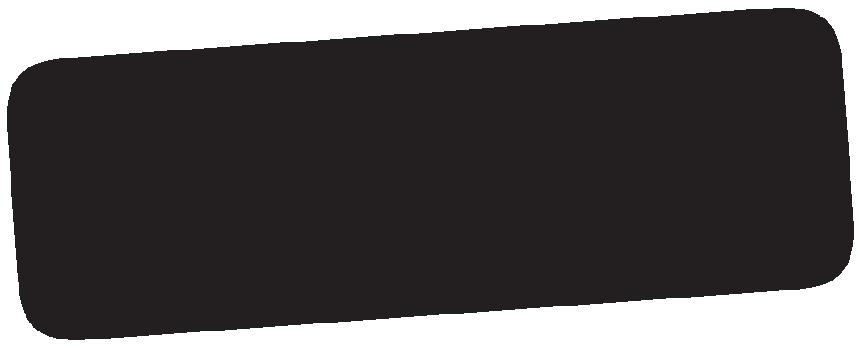
Features of the Bigfoot Features of the Bigfoot Central Inflation Tyre System Central Inflation Tyre System
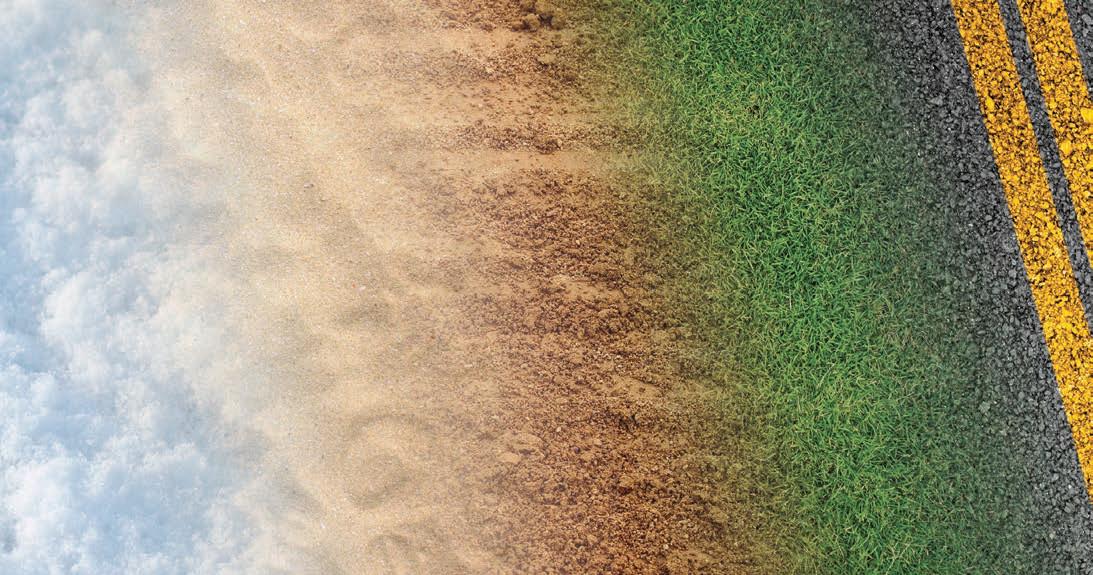
● ● Designed and tested in some of the worlds harshest conditions Designed and tested in some of the worlds harshest conditions
● ● ● ● Easy to use in-cab control unit Easy to use in-cab control unit Lor● Built in safety features prevent operating outside safeLor● Built in safety features prevent operating outside safe em limits for selected tyre pressureem limits for selected tyre pressure ipsu ● Precision manufactured in New Zealand using onlyipsu ● Precision manufactured in New Zealand using only ● ● Full after sales service and parts network Full after sales service and parts network ● ● Full manufacturers warranty Full manufacturers warranty
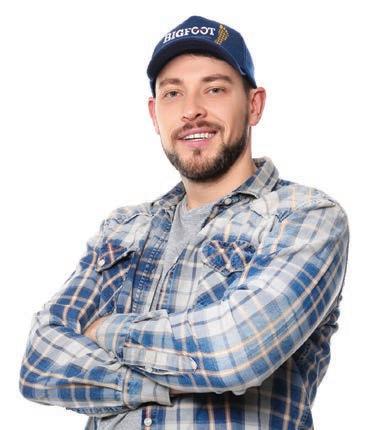


Lore Lore m m BRENT GRAHAM CONTRACTING
TM TM
TD32531
The brain behind the Bigfoot system is The brain behind the Bigfoot system is the Bigfoot OptiTractionthe Bigfoot OptiTraction control module. control module. and makes monitoring and adjusting tyre and makes monitoring and adjusting tyre pressures simple. The display also provides pressures simple. The display also provides visual and audible alarms. visual and audible alarms.
The ExTe Com90 system with a log load fully lashed down (far left), in the process of opening (left) and fully open (right) ready to be unloaded.
Skippy says that training gave him a basic understanding of the Com 90 system, but it was first two weeks or so in use where he became familiar with its operation.
“It was a bit like getting a new TV remote or a new controller for a Playstation or something. You can be shown how to use it, but it takes a little while to fully understand it.
“At first I was a bit apprehensive of all the buttons and technology but after a bit of time using it, it’s been really good,” says Skippy.
“All of the drivers in these trucks talk to each other quite often about the little glitches they’ve had, and we bounce ideas off each other.
“We’ll ring each other as ask “have you had this happen before?’ It’s all part of the learning curve.”
“The monitoring is excellent, and the system warns you
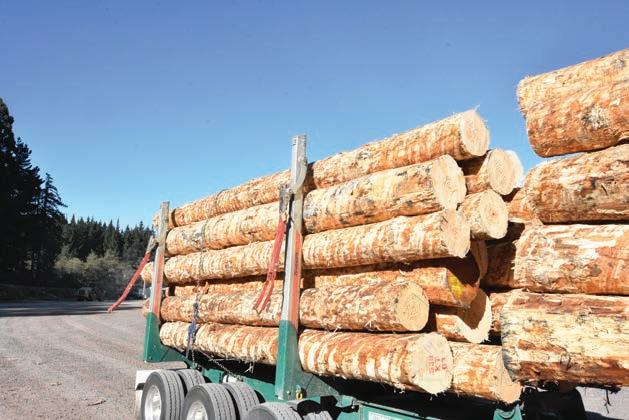

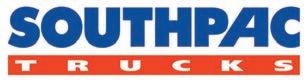
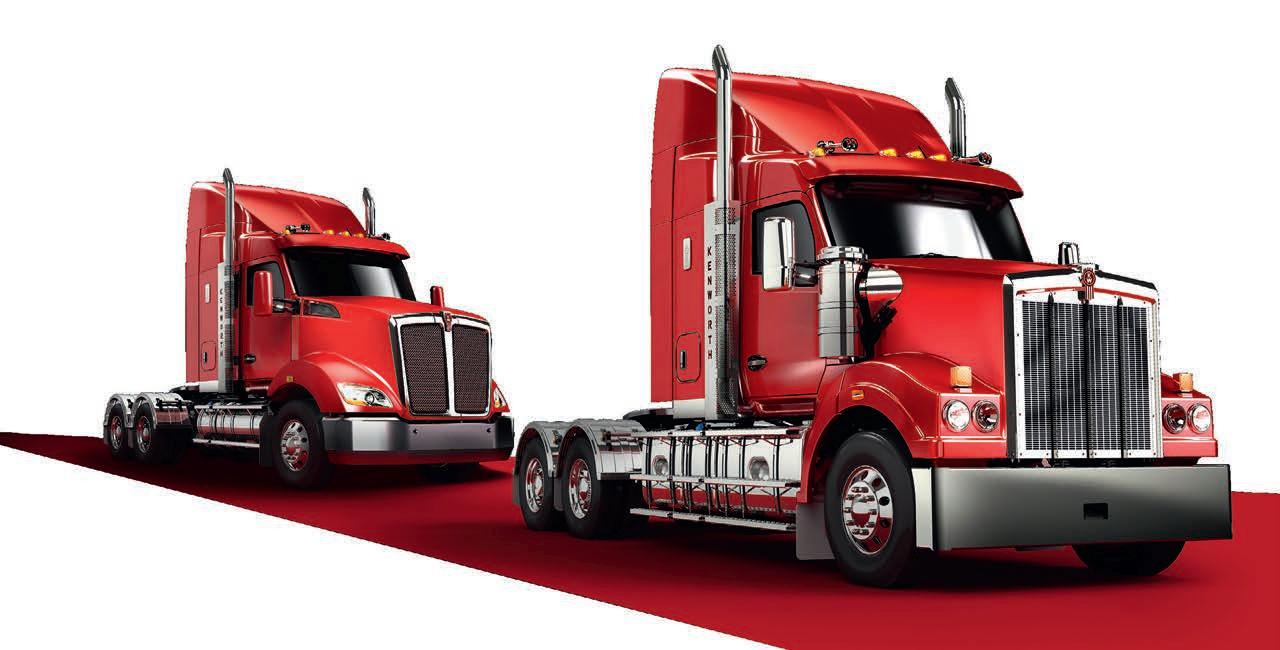
96-98 Wiri Station Road PO Box 76463 Manukau City, Auckland, NZ PHONE (09) 262 3181 FAX (09) 278 5643
NORTHLAND
Mitchell Redington 021 555 326
AUCKLAND
Steve Willcocks 027 525 0015 Mitchell Redington 021 555 326
WAIKATO
Adam McIntosh 027 603 1023 Tim Finlay 021 452 805
BAY OF PLENTY - GISBORNE
Tim Finlay 021 452 805
T610/T610SAR
TARANAKI
Adam McIntosh 027 603 1023
HAWKE’S BAY – MANAWATU – WANGANUI – WELLINGTON
Mark O’Hara 027 2466 954
SOUTH ISLAND
Mike Gillespie 027 4322 491 Chris Gray 027 2816 840 Steve Herring 021 377 661 FIND OUT MORE WWW.SPT.CO.NZ TD31842
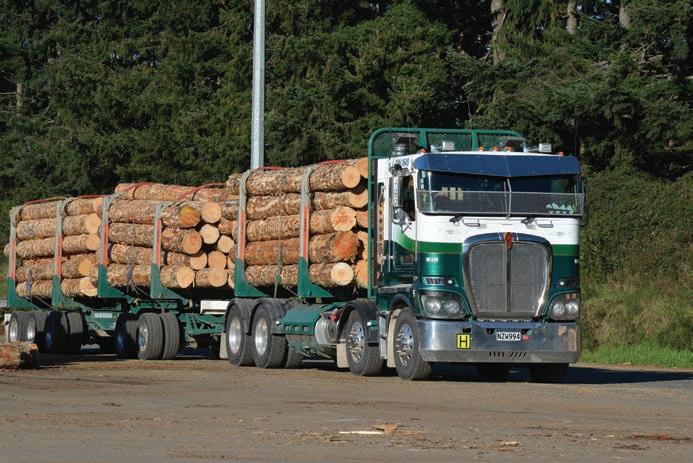

Top Left: RFH has two Kenworth K200s equipped with the Com 90 system. Lower Left: The tablet display in the cab shows the lashing pressures and provides a warning if tension falls below 1200kg. Right: “Skippy” Hennell only has three belly chains to fasten and unfasten on a three packet load.
if the tension ever goes below 1200kg.”
It also identifies on the touchscreen which lashing needs to be re-tensioned.
Skippy says there’s been plenty of interest from other drivers.
“I’ve been getting a lot of questions about it from other drivers and some of them come and have a good close look at it. One of my mates was watching me use the remote control and called me a lazy bastard.
“You still have the belly chains but you’re only throwing three chains rather than nine. It takes about a third of the time and that’s great when it’s raining.”
The K200 doesn’t run `empty trailer-up’ on this short run back to KPP but when it does, on other runs, Skippy says it’s important to make sure the gantry hook is sitting a little higher than where it’s usually left to ensure it doesn’t make contact with the lashings.
A few modifications have been made to suit New Zealand conditions.
“At the same time as adding the Com 90 system to the trucks we made use of the hydraulic system and added cylinders to the truck bolsters so they can be laid over and stood up by pushing buttons,” says Haines.
Evans Engineering have also shortened the bolsters and rams to suit local conditions.
Scandinavian log trucks typically carry a larger number of logs which tend to be smaller diameter and lighter but stacked higher than in New Zealand. Fully loading the RFH trucks to the original 1900mm bolster heights would have put them overweight.
That led to the bolsters and the rams inside them being shortened by 250mm on the first RFH truck and once proven the same dimensions were installed for the second truck.
There have been a few teething problems and improvements made along the way.
“It’s working well but we are still improving,” says Sam Haines.
“Originally the software was in Swedish but now we have an English language tablet in the cab.”
And a minor wiring glitch on the second truck meant the system didn’t recognise the trailer was attached.
The log industry has worked hard on procedures and new technology to improve safety. ExTe Com 90 fits the bill by reducing the risk physical injury for drivers as well as providing a monitored log securing system.
Sam Haines can see more automation being introduced to the logging industry that will further improve safety and efficiency gains.
“I don’t think it will be long until we are building fully automated units that are completely controlled from the cab of the truck – all of the load securing and even the trailer lifting,” he says. T&D
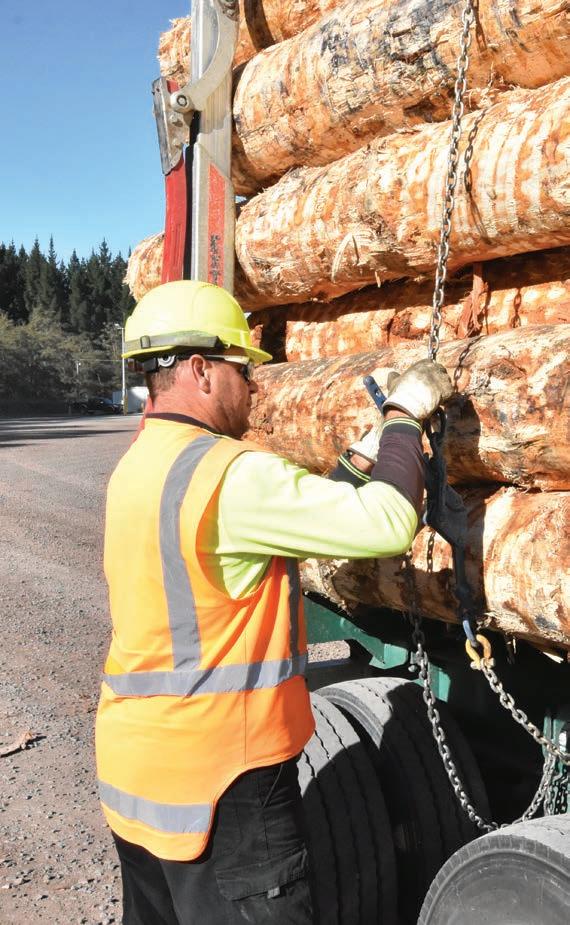
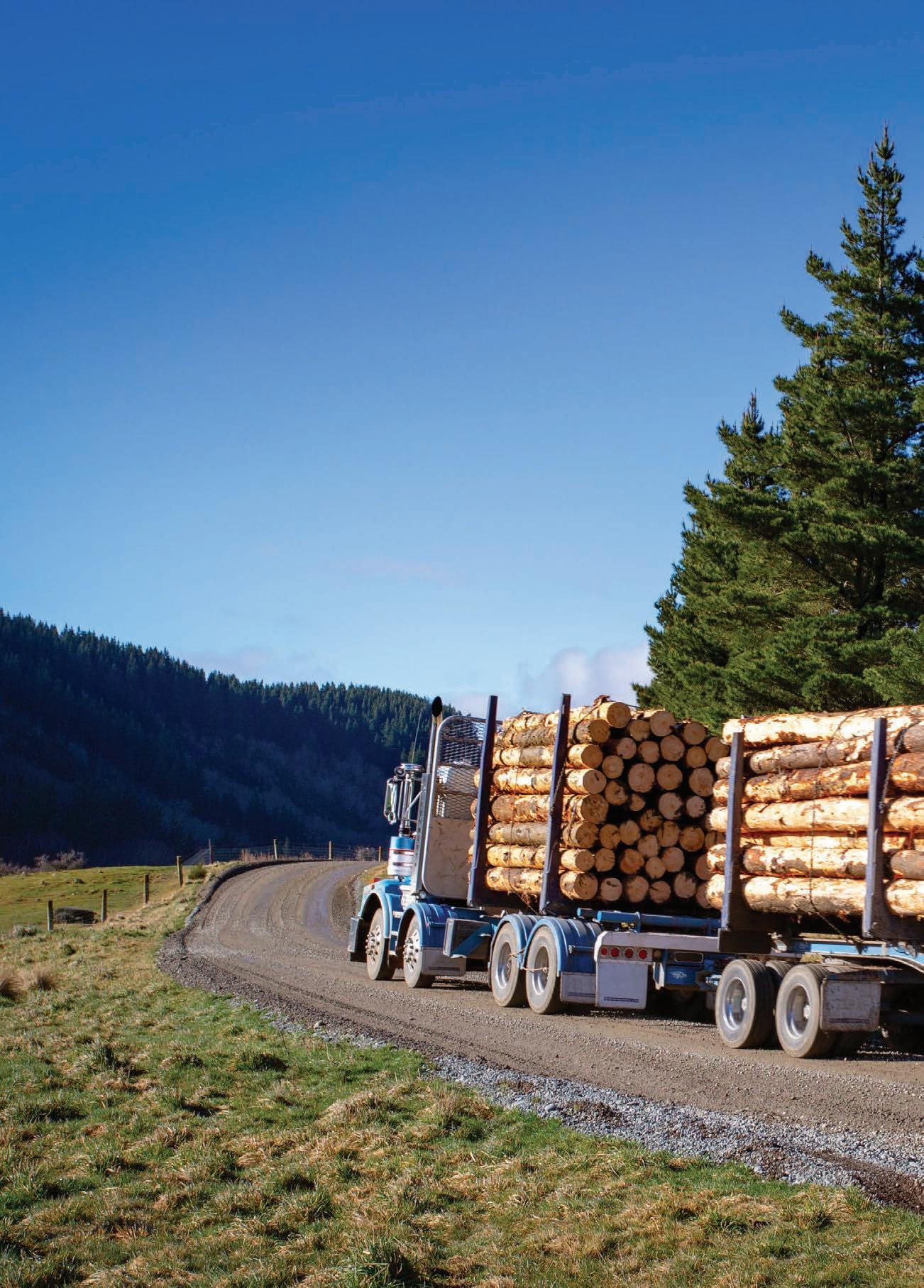