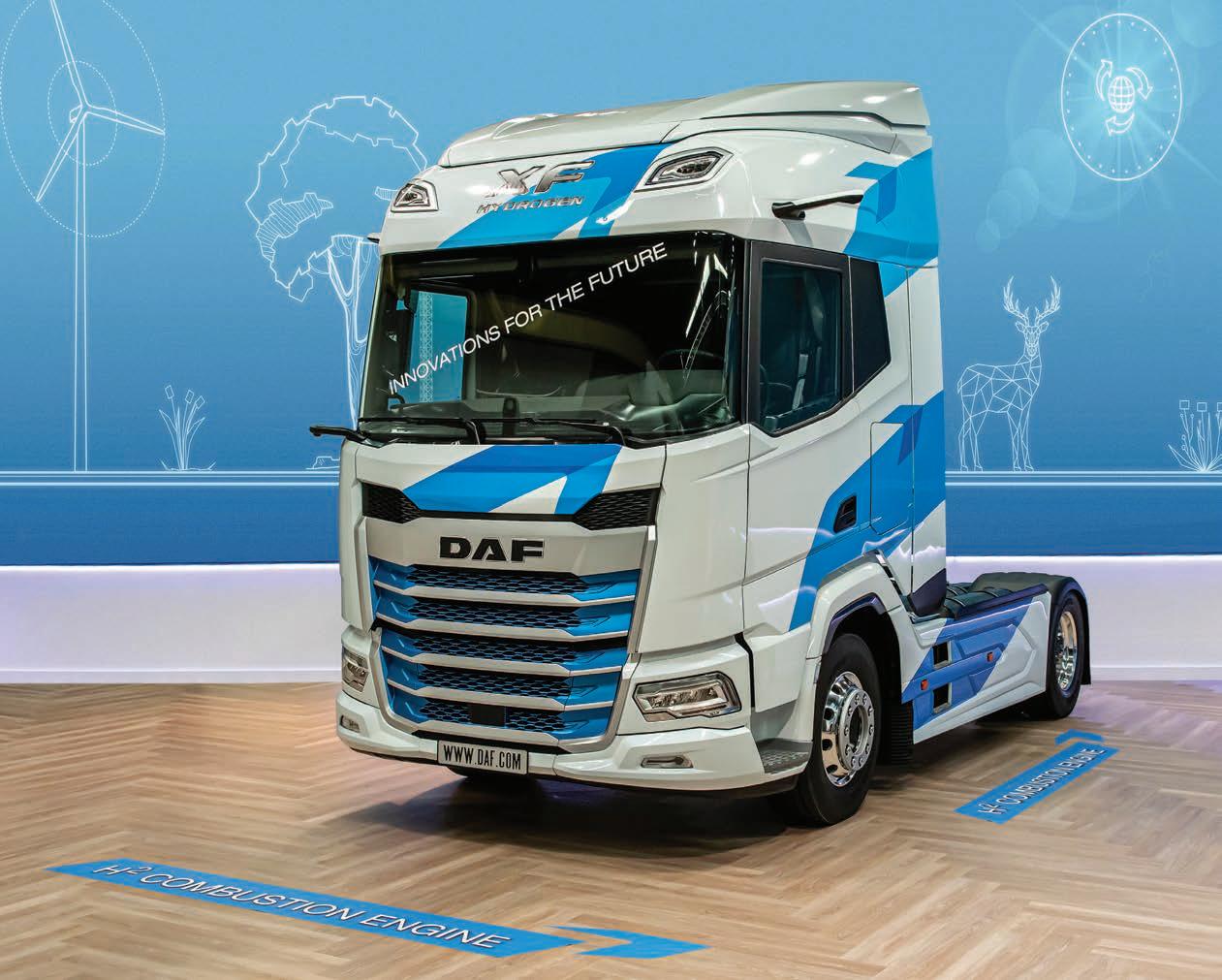
6 minute read
Hydrogen Drive
DAF is developing the XF H2 Innovation Truck which features a hydrogen fuelled internal combustion engine.
A Cleaner
Burn By Brian Cowan
IF YOU LOOK AT IT SIMPLISTICALLY, THE HYDROGEN FUEL
cell is shaping up as the primary path towards a carbon-free future for transportation. For light vehicles, battery electric looks secure as well, but recharging time and range limitation present huge challenges for long-distance goods cartage using pure electric drivetrains.
Huge, but not insurmountable. One alternative is the use of a quick-swap battery module, able to be fully charged off-vehicle – though in a long-distance, heavy-transport application such modules would need to offer at least five times the 100kWh capacity of the likes of the Tesla Model S car. Which calls for a dedicated vehicle design, quite unlike any current truck.
The point being there’s no single-best solution with each approach having its good and bad points. Despite the burningeyed fervour of some adherents for their pet concept, there are more shades of grey than a shelf of sado-erotic novels.
And now, into this mix, comes a return of the idea of burning hydrogen directly in an internal combustion engine – on the face of it a grand scheme, for when you burn hydrogen (in other words, combine it with oxygen) the end product is simply water.
Some 20 years ago, several engine makers looked seriously at the concept, chief among them being BMW. The company even got a 750i model running acceptably well, but eventually flagged the project for offering too many hurdles.
Among them were very high combustion temperatures when using an ideal fuel/air ratio, leading to an excess of oxides of nitrogen (NOx) in the exhaust, and the need for aggressive
Liebherr and MAHLE are collaborating on hydrogen combustion engines and have developed a pre-chamber ignition system to suit hydrogen on its H966 and H964 engine. positive crankcase ventilation to avoid blown-by fuel igniting in that space, since hydrogen is much easier to ignite from a stray spark or hot spot than petrol or diesel.
On the other hand, it is much more tolerant of lean mixtures (though at the cost, obviously, of power output), which reduce peak combustion temperatures and consequently NOx production. It also works best at high compression ratios.
Hmm...high compression ratio, integrated SCR and EGR systems to reduce NOx, sounds like a modern (Euro 5 or 6) diesel engine, eh? And that’s the development path that several groups are taking, mixing hydrogen with diesel in a dual-fuel approach. And it’s about to be trialled in New Zealand.
Conventional compression ignition using hydrogen alone doesn’t work, alas, for despite igniting easily when triggered by an outside source, it has a very high auto-ignition temperature (around 580degC compared with the 180-320degC of diesel). You just couldn’t build an engine with a compression ratio high enough to produce these sorts of temperatures.
However, mixed with diesel in about a 40:60 hydrogen: diesel ratio, the gas works very well. Its extreme diffusability (the reason why it’s a devil to keep contained at anything like normal pressures and temperatures) promotes excellent mixing of the two fuels prior to combustion, and its greater energy density than the diesel ensures peak power output can be maintained.
The real beauty of the approach is that a modern diesel engine already carries NOx-reducing kit in the shape of its SCR and EGR systems, meaning a dual-fuel conversion requires
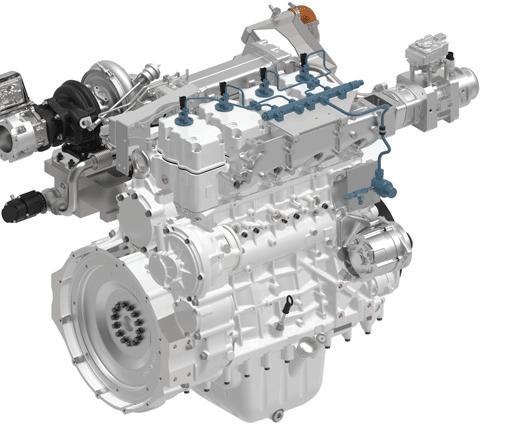

Wiri |5 Aerovista Place |09 279 7351 Otahuhu |20 Kahu Street |09 276 7206 Palmerston North |76 Campbell Street |06 358 2571 Christchurch |108-A Hayton Road, Sockburn |03 343 2001 Christchurch |Treffers Road, Wigram |03 348 3758 Invercargill |90 Preston Street, Prestonville |03 215 8584 Invercargill |53 River Street, Prestonville |03 215 9955

H2 GAS
engine modifications little more complex than that of an LPG/ petrol spark ignition engine project. The payoff is the zerocarbon exhaust emissions of the hydrogen component – not the full Monty, sure, but a simple and cost-effective first step towards the phasing out of fossil fuels.
A leading player in the development of this technology is ULEMCo, a Liverpool-based British firm. And it’s ULEMCo’s H2ICED technology that a local start-up, KiwiH2, has adopted for a trial scheduled to begin soon involving units from local trucking companies.
KiwiH2 is one of several recent recipients of funding from the Government’s Low Emission Transport Fund (LETF) administered by EECA (Energy Efficiency and Conservation Authority). In the first instance the trial will involve two units.
Sarah Barnett, senior communications advisor with EECA, sees the plan as an important first step towards a zero-carbon future, using existing vehicles: “KiwiH2 will be offering customers a bundled leasing and fuel package that will, for a monthly fee, include the lease of the conversion unit and all fuel (both diesel and hydrogen),” she says.
Cummins reveals hydrogen engine
CUMMINS UNVEILED ITS 15-LITRE HYDROGEN ENGINE AT THE
Advanced Clean Transportation (ACT) Expo held in Long Beach, California in early May. The engine is built on Cummins’ new fuel-agnostic platform that allows a base engine to be adapted to suit diesel, natural gas and hydrogen fuel types.
Below the head gasket each fuel type’s engine has largely similar components, and above the head gasket, each has different components to optimise its performance.
Full production is expected in 2027. Zero-carbon hydrogen fuel is a key enabler of Cummins’ strategy to help customers reduce greenhouse gas (GHG) emissions.
“We’ve established significant goals as part of our PLANET 2050 sustainability strategy, including a target of zero emissions,” says Srikanth Padmanabhan, President, Engine Business, Cummins Inc.
“Reducing well-to-wheels carbon emissions requires innovation of both energy sources and power solutions. While use cases for battery electric and fuel cell electric powertrains are promising, the pairing of green hydrogen in the proven technology of internal combustion engines provides an important complement to future zero emissions solutions.”
Cummins announced the testing of hydrogen internal combustion (ICE) technology in July 2021, and has made impressive early results, already achieving production power and torque targets (over 810 ft-lbs torque and 290 hp from the medium-duty engine).
Additional testing on more advanced prototypes will begin soon. With Cummins’ significant global manufacturing footprint, the company can quickly scale production.
Cummins says the industry needs multiple solutions to meet the needs of all on- and off-highway customers and all applications considering the variation in duty cycles and operating environments.
The engine will be a zero-carbon fuelled solution for multiple markets. Cummins intends to produce hydrogen internal combustion engines in both the 15-litre and 6.7-litre displacements.
Hydrogen internal combustion engines use zero-carbon fuel at a lower initial price of a fuel cell or battery electric vehicle with little modification to today’s vehicles. Accelerated market adoption of hydrogen engine powered vehicles is driven by the technology’s high technology maturity, low initial cost, extended vehicle range, fast fuelling, powertrain installation commonality, and end-user familiarity.
“Heavy-duty trucking is critical to the global economy and is one of the hard-to-abate sectors of the economy,” said Daryl Wilson, Executive Director of the Hydrogen Council.
“We are encouraged by progress at Cummins in the development of hydrogen-fuelled internal combustion engines and look forward to continued advancements that can help us reach cost-effective decarbonisation of economies worldwide.”
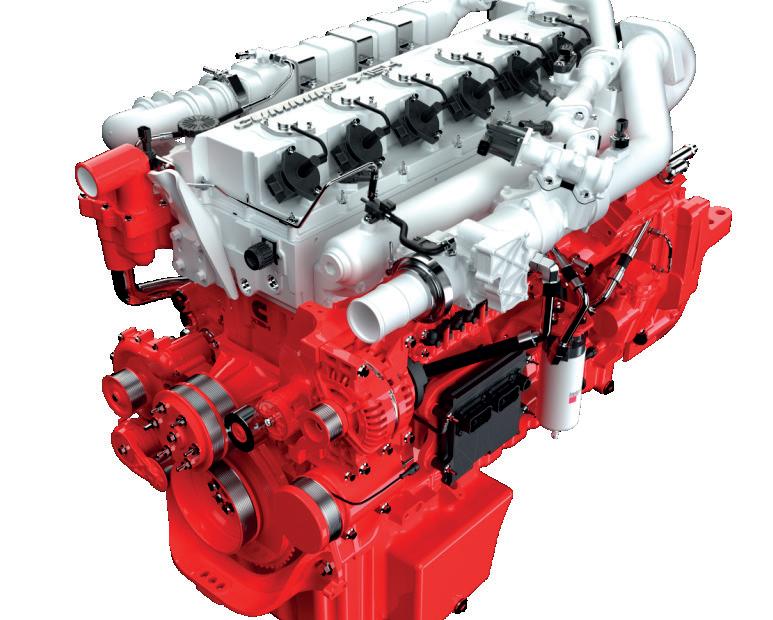