
21 minute read
VOICEBOX
from AMT AUG/SEPT 2020
by AMTIL
Change is inevitable. Your progress is optional
The current economic dislocation is as much a challenge as any before it, but also will not last forever, and it will present opportunities for Australian manufacturers who are prepared to adapt to accelerated change in the emerging post-COVID-19 world, writes Brent Whyte.
Never has the axiom ‘Change is inevitable’ been more relevant to manufacturers than in the emerging post-COVID era, when Australian industry is being reshaped by tectonic events. We already know supply chains will change, automate and truncate to become more rapidly responsive to domestic and international events. The way we work, communicate and engineer the future will also change. The degree to which countries must be more self-sufficient in key areas may emerge as a national priority. Technologies focused on flexible manufacturing, health, hygiene, energy, infrastructure, defence, construction, sustainability and environmental risk management will all be among the winners from change. Some of the changes will be new; some will be an acceleration of trends that were already underway; and some will kill off old practices that were already on life support before COVID-19 struck. And while no-one has a clear chart to the future (that would be like having tomorrow’s race results or share prices) we do know there will be challenges and opportunities; and there will be winners and losers, depending on how they see the future. So, while most of us right new are focused on survival – and rightly so – it might also be time to look over the parapet to the world ahead and position ourselves for change. Ask yourself, is it time now to get out and get your abilities known? To position yourself early as a master of change in the area in which you operate? To present yourself as an authority with a vision of the future – as someone who sees challenges and change as a time of opportunity, a positive thinker? Or do you do nothing and believe your old reputation will carry you through? That might work for some, if their corporate vision is clearly understood by the people who sit down to make choices about who gets considered for work, or who is selected for tender lists. But it can be a risk to presume that everyone knows your company and the full extent of your capabilities. The fact is they often don’t. Based on our decades of experience in the B2B business here at Whyte PR, we find it mostly falls into three categories: • Some customers will have a strong idea of who you are and what you do, because they deal with you frequently. • Others will have a less clear idea – they may know that you do one thing well, but they may not understand that you are good at other things as well. • And others just won’t have a clue, because some reputations are rooted firmly in the past and will die out with their old customer base, or they depend too much on one sector – even one large customer – and tie their fortunes to them. Failure to communicate your business’ advantages is surrendering your future to someone else – because business is based on constant renewal and clear and systematic communication of who you are and what you do. It is fundamental to understand that all businesses have a reputation in the marketplace. Your choice, really, is not whether you have a reputation, but whether you choose to define that reputation – or choose to let others do it for you (often competitors). So how do you get yourself known without paying a fortune (before you have generated a fortune)?
My first tip would be to join in some of the forums and events sponsored by AMTIL, to help find out from your peers who is a dud and who can actually understand what you are talking about. Have a chat with the people at AMTIL – about membership, editorial, advertising, events – and with the same cohort of people in other print and electronic media that are respected in the vertical markets you focus upon. These are the people working on the front line, sorting fact from fiction and credibility from waffle. Some of the tales they will tell you will be well worth learning in advance, because there are traps for new players (and indeed for some big companies whose heads are so elevated into marketing clichés, they may be alienating the down-to-earth, engineering-oriented audience that forms their key audience). Above all, they have to be self-starters – after all, you don’t buy a working dog and bark too. And when you do find the right people to talk to (naturally our company is happy to talk), enter a discussion that should Brent be without obligation, and with an eye Whyte to a shared future. It is not the strongest or the most intelligent who will survive, but those who can best manage change.
Brent Whyte is Managing Director of Whyte Public Relations, working alongside Senior Consultant Jack Mallen-Cooper, who joined the company in 2012. Whyte Public Relations works with local and international companies operating throughout Australasia, South Asia, Europe, America and China. www.whytepr.com.au
Jack MallenCooper
Manufacturing an edge in safety
The Federal Government estimates that COVID-19 closures have cost the national economy $4bn a week. This has long-term implications for the financial wellbeing of all Australians. But as we’ve seen from other nations that have relaxed their restrictions, this is a dangerous time because everywhere is now a high-risk environment. Alistair Venn explains how manufacturers can make safety their edge in a post-COVID world.
For most manufacturers, COVID-19 has been one of the most challenging periods, with organisations having had to navigate large hits to the bottom line. The crisis saw shifts in labour, supply and demand critically affect the entire industry. Manufacturers have had to deal with a sharp decline in consumer spending, disrupted supply chains, and facility shutdowns — often, all at once. As the world gets back to business, the key challenge for manufacturers lies in normalising safety procedures, ramping up operations as demand for goods return to normal levels, and minimising the risk of COVID-19 being contracted and spread throughout their facilities — resulting in halted operations and putting local communities at risk. The businesses who will come out on top are those who implement an early warning system — a set of procedures to guide the organisation as restrictions loosen, but to also enable leaders to react quickly if another outbreak occurs. These early warning processes will help manufacturers build long-term immunity to risk and disruption. SafetyCulture is one of the world’s leading platforms for workplace safety and efficiency. Working with more than 27,000 companies around the world, we have witnessed how COVID-19 has exposed the failings of a top-down business compliance model, where traditionally, safety has been the responsibility of a compliance officer. This is true in the manufacturing industry too. To stay ahead in today’s environment, managing a business’ health & safety obligations can no longer simply be a box-ticking exercise to meet compliance requirements. Safety is the responsibility of everybody. Democratising safety by empowering teams to act appropriately, reporting issues, and taking action to solve problems is how the manufacturing world can get safely back to business. As we look to life post COVID-19, it’s the people on the frontline of every industry who have the visibility to build a culture of safety from the ground up. It’s down to each and every member of your team to ensure procedures and guidelines are followed. Here’s how manufacturers can take action to ramp up operations and inspire confidence in employees and suppliers: Make safety the #1 priority Consistently high standards in managing hygiene, exposure and traceability have always been important in the industry, but they are now imperative. Reduce opportunities for contamination by removing unnecessary processes that involve human interaction and implement strict safety protocols for all – including staff and visitors to facilities. Make sure everyone knows they are responsible for ensuring strict cleaning regimens are being applied to all touchpoints throughout factories and warehouses – and reporting when they are not. Create an early warning system A huge priority will be establishing an early warning system that provides real-time data and the transparency required for staff to trust the new factory environment. Increasing the frequency of checks is critical as you get back to business. Empower front-line staff with simple, digitised checklists and inspection processes that give you real-time insights and turn issues into actions while creating an audit trail to keep track of everything. Get rid of inefficient paperbased safety inspections. Make safety everyone’s responsibility Employees are looking for confidence to sustainably get back to work. Communication is going to be critical. Everyone needs to take responsibility to create a genuine culture of safety, from the frontline to senior management, putting the safety of their colleagues and customers first. Compliance alone won’t cut it. Use checklists to cover areas including correct personal protective equipment (PPE), social distancing and hygiene processes. Lead by example Manufacturing has always been a risky industry. Use your years of experience to lead by example and become a sector that others look to for tips and guidance. A digital approach Using SafetyCulture’s iAuditor app, thousands of businesses worldwide have been able to simplify the auditing process and gain visibility and insights to help raise safety and quality standards across their organisations during COVID-19. Acting as an inspection management software, iAuditor is an easy-to-use application that enables your team on the frontline collect consistent data, standardise operations, send reports, identify failed areas and get problems resolved fast To support Australia’s manufacturing industry, SafetyCulture has digitised hundreds of the world’s COVID-19 reopening guidelines into simple mobile checklists in an inspection app that any team member can use in minutes. The ‘Return to Work’ templates, based on policies and procedures recommended by the Chief Medical Officer Brendan Murphy, and guidelines from health organisations like the WHO, can be relied upon to guide organisations through this challenging time.
Alistair Venn is the Chief Operating Officer at SafetyCulture. www.safetyculture.com.au
AMTIL DIGITAL BANNERS 60,000 ONLINE AD IMPRESSIONS 7,000 VISITORS 25,000 PAGE VIEWS
Figures quoted are average monthly statistics. Package dependent
Call Anne Samuelsson for your FREE 2021 AMTIL Digital Media Kit on 0400 115 525 or email asamuelsson@amtil.com.au
1510AMTIL/V3
COVID-19: How can the manufacturing supply chain respond? This year has presented a steep learning curve for global supply chain sites, as typified by the dramatic disruptions to supply chains caused by the COVID-19 crisis. By Danielle Dadello.
In March, metalwork manufacturers across Australia who rely on overseas suppliers for their materials saw drastic supply shortages, and many manufacturers waiting on materials or ingredients have had to make the difficult decision to put their businesses on hold. As a result, this places enormous pressure on the supply chain. Globalised supply chains require globalised visibility Manufacturers and suppliers providing services and stock to businesses such as food processors face a lot of pressure and responsibility, propping up the smooth running of producers’ ability to provide goods for end-of-the-line consumers. For example, food manufacturers utterly depend on the smooth running of the supply chain, but all too often relationships with suppliers can be problematically complex and unclear. Globalisation and complicated supply lines mean that some manufacturers and supply chain sites might be in risky and unreliable supply chain relationships without even knowing it. This can mean supply chain sites tasked with receiving and delivering goods and services can unexpectedly become affected by international crises, much like COVID-19, without the means to properly address and overcome this. Even in the case of less dramatic but nonetheless critical issues like product recalls, manufacturers can be held accountable for any improper product handling and poor management performed by the suppliers of materials and components earlier on in the supply chain. Enhanced insight into supply chains from the very first source is essential for manufacturers to have greater visibility into all ingredients sourced and used in production, to significantly minimise recalls due to incorrect or missing labelling, and on a greater scale, get ahead of international crises, and safeguard business performance against supply chain issues. Many manufacturers are using cloud-based technology to gain this critical, business-bolstering insight. Having complete visibility over your suppliers, materials, and all points of production means you can know where your goods are at all times, and ensure nothing gets changed or compromised along the way. It also means the goods you pass along to your customers will be the highest quality they can be. Bolster yourself against risks With enhanced visibility into suppliers, it’s essential you identify supply chain characteristics that seem risky and address them head on. With healthier supply chains, manufacturers can be better supported and far more resilient in times of uncertainty, or when supply chain sites fail. Building strong relationships with your suppliers is essential to abate risk, and establish productive systems of trust – trusted relationships where you can truly rely on your suppliers to provide quality goods, so you can then do your best work. Strong relationships are also critical in multi-supplier strategies, which manufacturers should consider exploring for trusted back-ups and support when primary suppliers can’t provide. Establishing supplier relationships in different countries and regions means that if one supplier falls due to political, economic or environmental events, you can draw on unaffected suppliers to keep business running. It’s also best to identify risky supply chain characteristics and cut them as soon as you can. For example, relying on suppliers in low-cost countries can leave manufacturers at a higher chance of receiving low-quality goods, forced to wait out delays, or seriously affected if that supplier goes under. It’s essential to review any suppliers’ track record too, and ensure they’ve consistently met demands and quality standards with their customers. In today’s globalised and digitised world, best supply chain practice comes down to implementing technology. Technology tools like cloud software is the only way suppliers and manufacturers can gain truly accurate, real-time visibility across all their stock and goods. Customer communication For companies in metalworks and production, keeping customers happy is a must. In uncertain, challenging times like this, it’s more important than ever that your customers understand that, as much as they rely on smooth running supply chain processes and product deliveries, so do you. When product recalls or unexpected events like COVID-19 strike, suppliers need to communicate clearly and openly with customers. Customers will appreciate you conveying the reality of hold-ups and offering more realistic timeframes around when services and products will be available, so they’re not left in the dark and can make decisions about their own business operations. It’s important that these timeframes are based on datadriven, real-time insights gleaned from smart technology, so they’re accurate and legitimate. Talking to key stakeholders in your customer base can also help you better communicate next steps and showcase that you’re invested in each customer’s wellbeing. Chatting to heads of finance, growth, or product can help you tailor communications to each part of customers’ companies, and keep specific sectors informed. Customers will appreciate this comprehensive approach. Moreover, if stock and goods are held up, see how else you can support customers. Perhaps there are other services or products that you can provide at this time instead. This works to keep customers satisfied, before they start searching for different products. Whether it be metalwork, food production or other manufacturing sectors, manufacturers are facing significant supply chain challenges as disruptions leave goods and resources held up overseas. It’s critical that in crises like this, manufacturers can continue to cater to their customers, and work on strengthening their supply chain relationships and practices to ensure best practice in the future. A globalised and highly complex line, the supply chain can be vulnerable at the best of times. Now more than ever, manufacturers of all kinds need to prioritise supply chain technology, gain visibility into their goods and protect themselves.
Danielle Dadello is a Country Manager at Unleashed Software www.unleashedsoftware.com
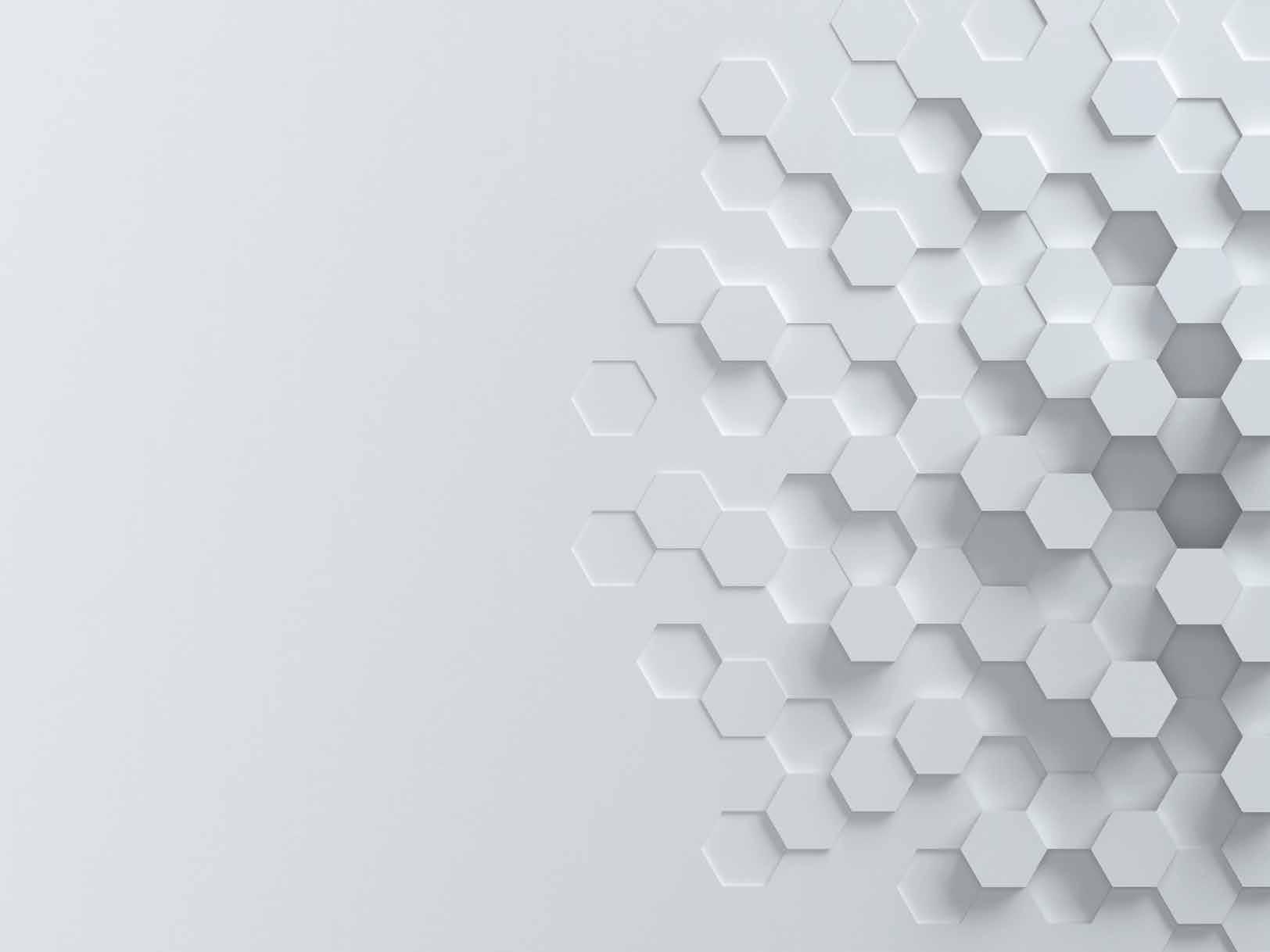
Australia: Using electricity to clean up toxic water
University of Sydney engineers have developed an electrochemical oxidation process to clean up heavily polluted industrial wastewater. The process involved treating wastewater with electricity using specialised electrodes. After discharging electricity, oxidation reactions near the electrode surfaces were driven, transforming the organic contaminants into harmless gasses, ions or minerals. The powerful process eliminates even the most persistent nonbiodegradable pollutants, such as pharmaceuticals and pesticides, as well as various classes of organic compounds that can be found in many industrial effluents. The process is relatively simple, does not require the addition of chemicals or severe operation conditions, and does not produce additional waste streams. Worldwide, researchers are investigating methods for the development of biofuels from algae. Developing alternatives for the treatment and reuse of this industrial effluent is a hot research topic and can bring opportunities for energy and resource recovery within a circular bio-economy framework. A UNESCO report found that the opportunities from exploiting wastewater were vast, and that safely managed wastewater is an affordable and sustainable source of water, energy, nutrients and other recoverable materials.
University of Sydney
The water before, during and after treatment.
Hong Kong: High strength steel with unprecedented fracture resistance
In the latest breakthrough in “super D&P” steel (a novel super-steel) scientists attained an unprecedented strength-toughness combination for ultra-high fracture toughness. This changes the conventional view that attaining high strength will be at the expense of deteriorating toughness. The team also made an important scientific discovery: It has a unique fracture feature in which multiple micro-cracks are formed below the main fracture surface, through a novel “highstrength induced multi-delamination” toughening mechanism. These micro-cracks can effectively absorb energy from externally applied forces, resulting in the steel’s much higher toughness resistance compared to existing steel materials. The cost of raw materials of the D&P steel is only 20% of the cost of maraging steel, and can be produced by conventional rolling and annealing processes, so no complex fabrication and special equipment are required.
University of Hong Kong USA: Expandable foam for 3D printing of large objects
It’s a frustrating limitation of 3D printing: Printed objects must be smaller than the machine making them. Now, a new material can be used to 3D print small objects that expand upon heating. Testing many different resin formulations, researchers 3D printed a hollow, latticed sphere. Heating the sphere in an oven caused a volatile component of the resin to bubble out as a gas. This created a porous, polystyrene foam-like material that was up to 40 times larger in volume than the original printed object. With this method, the team also 3D printed many other shapes, including a boat, which could carry about 20 times more weight at its expanded
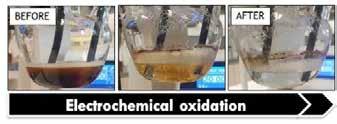
size, and a wind turbine that could produce a small amount of electricity at its larger size. The new material isn’t as strong as polystyrene foam, but could be used for cushioning, airfoils, buoyancy aids or expandable habitats for astronauts.
American Chemical Society
Australia: New QLD-designed rocket system boosts Australian space industry
Australian rocket company Gilmour Space and the University of Queensland have partnered to develop new technologies for an Australian-made rocket that will be launching small satellites into low Earth orbits from 2022. Gilmour is pioneering the development of next-generation hybrid rocket technologies that are safer and more cost-effective than traditional chemical-propulsion rockets. The company reached a milestone with a successful hot-fire of its upperstage hybrid rocket engine last June - a key demonstration of its ability to produce repeatable, stable, high-performance combustion over a long duration burn. The engine will have the capability to power the upper stage of the Eris orbital launch vehicle, and deliver customer payloads. More recently, Gilmour achieved one of the longest hybrid rocket engine test firings in the world: a 110-second mission duration burn of its upper stage engine. 110 seconds is the time period expected for the final stage to deliver customer payloads into their specific orbit. This proved many of the technologies needed for the company’s larger engines.
Gilmour Space and mixed

USA: Technology to remedy 3D printing's 'weak spot'
Plastics are commonly used for extrusion 3D printing and finding a way to remedy the inadequate bonding between 3D-printed layers has been an ongoing quest. A sophisticated technology has been developed that can bolster welding between layers all while printing the 3D part. To promote inter-layer bonding, the surface of each printed layer was coated with carbon nanotubes which were heated using electric currents. To overcome inadvertent damage to the part, the team generated plasma which could carry an electrical charge to the surface of the printed part. This technique allowed electric currents to pass through the printed part, heating the nanotubes and welding the layers together. When the researchers tested the strength of 3D printed parts, their strength was comparable to injection-moulded part.
Texas A&M University
USA: Far-UVC light safely kills airborne coronaviruses
More than 99.9% of seasonal coronaviruses present in airborne droplets were killed when exposed to a particular wavelength of ultraviolet light that is safe to use around humans. Conventional germicidal UVC light (254nm wavelength) can be used to disinfect unoccupied spaces such as empty hospital rooms, but direct exposure to these conventional UV lamps is not possible in occupied public spaces, as this could be a health hazard. To continuously and safely disinfect occupied indoor areas, researchers have been investigating far-UVC light (222nm wavelength). Far-UVC light
cannot penetrate the tear layer of the eye or the outer dead-cell layer of skin and so it cannot damage living cells in the body. Researchers estimate that continuous exposure to far-UVC light at the current regulatory limit would kill 90% of airborne viruses in about 8minutes, 95% in about 11 minutes, 99% in about 16minutes, and 99.9% in about 25minutes. The sensitivity of the coronaviruses to far-UVC light suggests that it may be feasible and safe to use overhead farUVC lamps in occupied indoor public places.
Columbia University Irving Medical Center
Australia: World-first thermal coating
A new lightweight, fire-resistant cladding that can withstand temperatures of more than 1000°C developed by the CSIRO, is set to change the face of ships around the world, creating advanced manufacturing jobs in Tasmania and reducing carbon emissions. The material, developed in collaboration with Tasmanian small business, CBG Systems, has already been installed on two new ships and used to replace cladding on another. The prototype paneling, called Rapid Access Composite (RAC) Plus, is the first of its kind in the world, withstanding temperatures of over 1000°C and remain structurally stronger than conventional fire protection coatings and weighing half as much.
CSIRO

Germany: Clean without scrubbing or using chemicals
Scientists have developed a self-cleaning metallic surface by structuring an aluminium plate with a laser process in such a way that water droplets no longer adhere and dirt particles can be removed from the surface - completely without chemical cleaning agents or additional effort. For several years, scientists have been developing functionalised surfaces by means of laser-based manufacturing processes. Now, they have created a periodic surface structure that is not only water and ice-repellent, but also removes dirt particles solely by rolling water drops. In this context, they particularly focussed on the material aluminium. In particular, the scientists studied the function of self-cleaning laser-structured aluminium.
Technische Universität Dresden
Switzerland: Transparent, breathable face masks
Researchers have devised a transparent design for face masks. Over the past few months, the prototypes for see-through masks mostly involved replacing a part of a mask with clear plastic panels which reduce breathability and often quickly fog up. Researchers from the EPFL and Empa in Switzerland have spent the past two years developing a better alternative that offers near full transparency while still being breathable and protective. The result is the HelloMasks, which are made from organic biomass-based materials – rendering them transparent and also recyclable and biodegradable. Using a manufacturing process called electrospinning where an electrical charge is used to create ultra-thin threads, the new polymer features fibres spaced just 100 nanometres apart which is the same as conventional disposable masks that allow air particles to pass through but block bacteria and viruses. They may be available by early 2021.
Gizmodo

Australia: Record-breaking heavy-lifting
Australian-based heavy lifting tower crane specialists, MARR Contracting P/L was awarded the contract to deliver specialised heavy-lifting crane services on the construction of an earthquake-prone bridge and motorway project in Turkey (the 1915 Çanakkale Project). This bridge will cut a 90min. boat trip to a 6min. car ride. The record-breaking construction feat saw one of MARR’s M2480D Heavy Lift Luffers - the world’s largest capacity tower crane - undertake the world’s heaviest (155 tonnes) craneage lift at a height of 318m, on what will be the world’s longest spanning suspension bridge. The bridge will join the towns of Gallipoli in Turkey to Lapseki in Asia. The feats of engineering required to complete the construction are “staggering” and could be a game changer for the future of bridge construction. A milestone development was the installation of the centre section of the upper cross beam (UCB) on the Asian side of the bridge on 7 June. The European side was completed 24 hours later, with the final centrepieces installed on both sides of the Bridge on 8 June. Key to the plan was using the heavy lift tower crane’s ability to carry heavy modular sections, instead of lifting and welding small pieces of steel at height. Fully assembled in a dry dock, the cranes, each weighing 600 tonnes, were lifted by a floating crane and transported 1 km to the caisson in the middle of the Canakkale Strait. The bridge is due to open in March 2022.
Marr/mixed

Record-breaking 155-tonne lift of a section of the UCB, 318m above sea level