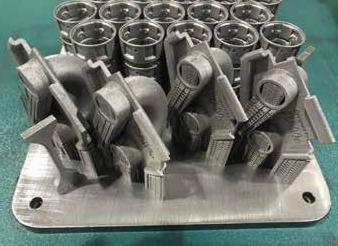
5 minute read
RAM3D – Bringing additive manufacturing to medical
from AMT AUG/SEPT 2020
by AMTIL
RAM3D – Bringing additive manufacturing to medical Additive manufacturing has the potential to become a game-changer for the medical industry. From its base in Tauranga, New Zealand, 3D metal printing service provider RAM3D has worked on a number of different projects in the sector that demonstrate the techology’s potential. By Gilly Hawker.
Printing ventilator parts for COVID-19 RAM3D became an essential supplier to the medical industry during the lockdown period. This project was a combined effort involving RAM3D, Doctor Andrew Robinson of Lakes District Health Board, and Kilwell Fibretube Engineering, who have been involved in reverse engineering and prototyping. The parts RAM3D were asked to 3D print were for an anaesthesia machine that was being converted to an intensive care ventilator for COVID-19. RAM3D successfully redesigned the valve (bridge) and will be full-scale manufacturing the part. The key aspects of the design were that it had to be simple to install and needed to have limited risk of failure; it was imperative there was no leakage through the seals during operation. RAM3D was sent the original CAD file of the part; it was made up of two pieces and had been designed for CNC manufacturing. After several failed attempts to 3D print the functional parts, the team at RAM3D decided to redesign the part as a single piece that required no further assembly. The successful prototype had a simpler design and required very little post-processing. The bridge parts were printed in Titanium 64 (medical-grade alloy) as this is RAM3D’s choice of powder for medical projects. They were quick to install and conversion only took two minutes, including testing. The Maquet Flow-i anaesthesia machines from Gettinge Group are underutilised in many hospitals world-wide. Consequently this project could potentially increase the number of ventilated beds in intensive care units (ICU). There are 7,000 of these Maquet Flow-i anaesthesia units installed globally and most of the machines are in Europe. Asked about the project, Dr Andrew Robinson remarked: “In this instance 3D printing provides a simple, quick to innovate and costeffective method of manufacture. It is very important to note that fused deposition modeling (FDM)-style printers (the most common around the world) are not well suited for this device.” Custom titanium implants for veterinary surgery Since 2013 RAM3D has been metal 3D printing surgical instruments, prosthetic limbs, sleep apnoea parts, and human and animal implants. RAM3D trialled its first artificial dog jawbone in mid-2013, working with a design company Axia and Massey University vet surgeons to save the life of a boxer dog with aggressive mouth cancer.
The RAM3D ventilator adapter.

The vets take the CT scans of the animal and send them to the design company to create a 3D CAD model, and this is sent to RAM3D to be printed. The turnaround time is quick, and the implant is then sent back to the vets at Massey to complete the surgery. The titanium jawbone was printed on a Tuesday, fitted to the dog on a Wednesday, and 12 hours later the animal was eating happily. RAM3D prints in Grade 5 Titanium 64 because it is the most widely used titanium alloy in biomedical implants, where high strength is required. Titanium is the perfect metal to make human and animal body parts because it physically bonds with the bone. Once the implant is inserted, natural tissue and bone form over the titanium replica. Because of its durability, titanium implants can last up to 20 years inside the human body. Titanium is not magnetic and does not interfere with magnetic resonance imaging (MRI) equipment. It also has a higher strength-to-weight ratio – it is stronger and lighter than stainless steel. RAM3D have printed hundreds of dog and cat implants, including leg and hip bones. More recently it provided an implant for Kora, a Land Search & Rescue (LANDSAR) dog in training. Kora was getting close to becoming certified when Nick (Kora’s handler and operational field member with LANDSAR) noticed her performance had dropped off and she was a bit lame. In Nick’s own words, “like any performance athlete, injury for a working dog is a high probability”. After a visit to the vet, Nick was told she would need some surgery on her lower back; the damage was done between the last disc of her spine and sacrum. The surgery was a success; Nick was surprised she walked out of the clinic straight after her operation, and even though she was a bit sad and heavily medicated, he knew it wouldn’t be long until she was back to her normal self. She is now fully mobile and raring to go. Production potential RAM3D knows that metal 3D printing is a competitive production technology with an unprecedented potential for industry. The team at RAM3D work with companies to improve the design of production parts, and 3D printing them makes them more efficient and costeffective. The diversity of parts RAM3D manufactures ranges from titanium knives used by the Team NZ America’s Cup crew, to customised handlebar extensions for the New Zealand Olympics Cycling Team, as well as Oceania Defence’s Inconel and titanium suppressors for military operations.
RAM3D recently provided an implant for Kora, a Land Search & Rescue (LANDSAR) dog in training.

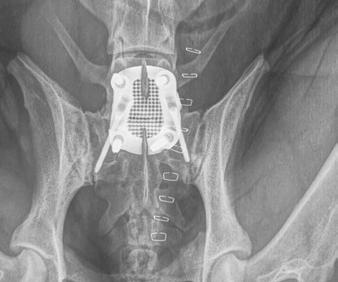
Kora needed an implant on her lower back between the last disc of her spine and sacrum.
Over the last three years, the company has seen a big shift from prototyping to full production work. To keep up with customer demand, it now has a total of seven printers in its growing facility. The team have seen an unprecedented increase in both large and smaller companies interested in trying 3D metal printing as an alternative to other forms of manufacturing. This is possibly because of having time to work on projects during the COVID-19 lockdown. RAM3D has more than 10 years’ experience in the additive manufacturing industry. Its services includes metal 3D printing, and consultation on design for additive manufacturing. It can print in stainless steel 15-5ph and 316L, titanium 64, Inconel 718 (high temp alloy) and aluminium (AISi10Mg).
www.ram3D.co.nz
066BMS ACLR8
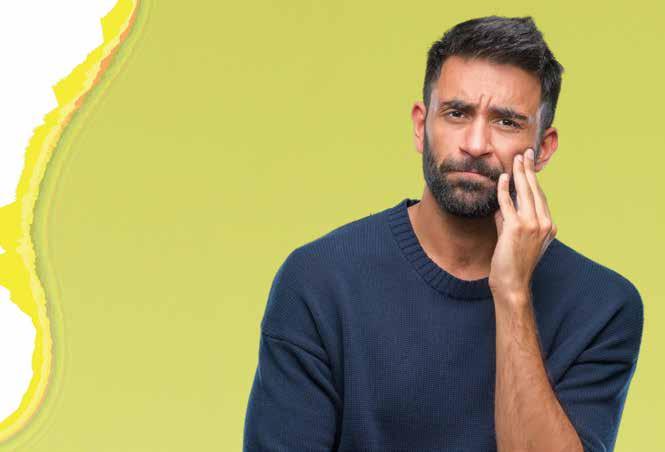