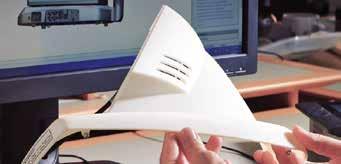
7 minute read
Better prototyping: Nidek cuts time-to-market with 3D printing
from AMT AUG/SEPT 2020
by AMTIL
A vision for better prototyping: Nidek boosts clinical trials, cuts time-to-market with 3D printing Nidek Technologies (Nidek), located in Padova, Italy, specialises in the development and prototyping of high-technology ophthalmological diagnostic systems.
With all of its products having direct contact with patients, it’s crucial that Nidek produces fully functional prototypes that precisely replicate the final product. This enables a comprehensive evaluation of the fit, form and function of new devices before investing in expensive clinical trials and moving to final production. As this process often proved costly in terms of lead time and capital, Nidek turned to Stratasys 3D printing in a bid to optimise its prototyping process and, as a result, accelerate its clinical validation. This was demonstrated in a recent project that saw Nidek produce a new automatic Gonioscope, a device designed to observe the space between the iris and cornea. Typically, the R&D team would create the prototypes using traditional manufacturing, requiring expensive injection moulds or using CNC machines to create the individual device components. This led to escalating lead times and, should iterations be required, substantially increased prototyping costs. To overcome these barriers, Nidek invested in a Stratasys Objet500 Connex3 3D printer. “Our prototyping process has become much more streamlined since incorporating Stratasys 3D printing into our workflow,” says Cesare Tanassi, CEO at Nidek. “The technology enables us to develop complex parts with intricate geometries on demand. The ability to validate designs early in the product development cycle helps us eliminate costly iterations during manufacturing, as well as significantly reducing our time-to-market compared to traditional prototyping methods.” Deploying 3D printed devices into clinical trials According to Tanassi, waiting for production parts to conduct clinical evaluations creates costly delays. “Previously we were constrained by the time restrictions associated with traditional manufacturing,” he explains. “3D printing overcomes these bottlenecks and permits us to quickly enter our devices into clinical trials. As you can imagine, fully verifying our products is crucial to ensuring that premium healthcare is maintained. “In the case of the Gonioscope, the quality of the Stratasys 3D-printed components saw the device pass a year-long clinical trial where eight global medical centres examined it. It will soon be utilised by clinics and hospitals around the globe, contributing to a novel way to diagnose glaucoma.” Beyond the Gonioscope, the benefits of 3D printing are impacting numerous other products. According to Federico Carraro, Mechanical Division Manager at Nidek, this occurred when developing the company’s micro-perimeter, a device used to determine the level of light perceived by specific areas of the retina. Previously Nidek used metal fabrication for this device, which took around two months to create and dramatically delayed the prototyping cycle.
The external case of the prototype Gonioscope was built on a Connex3 3D printer. The assembled Gonioscope prototype, built with 3D-printed parts.
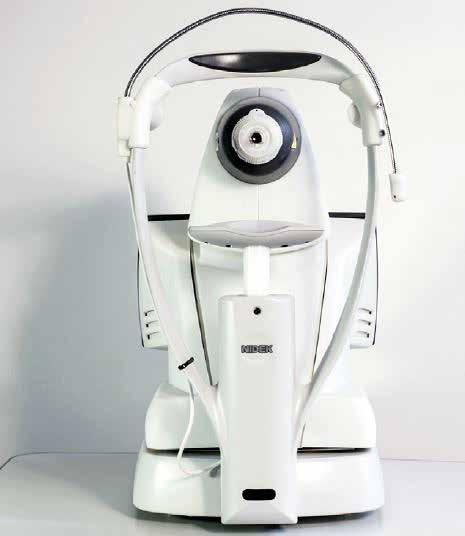
“With our Stratasys Objet500 Connex3, we can combine a wide range of 3D printed materials with contrasting mechanical characteristics,” explains Carraro. “This allows us to accurately emulate final parts, including threads, seals, rubber and transparent components. In this case, we achieved the same functional result within 24 hours by replacing metal parts with robust 3D printed components.” Tanassi adds: “In the case of the Gonioscope, utilising the tough flexibility and snap-fit characteristic of the Stratasys Rigur 3D-printing material, we could replace several aluminium parts with a single 3D-printed component. The ability to quickly 3D-print high-quality parts that require no post-processing has proven instrumental in cutting our iterations and directly reducing our product development cycle. In fact, since introducing Stratasys 3D printing, we have slashed our prototyping costs by 75% and accelerated our development time by 50%.” A clear case for transparent 3D-printed parts Nidek is now pioneering a new proprietary polishing process for its prototype illumination lenses. Traditionally the development of lenses requires several months of build time and costs thousands of euros per lens. “In the future, with the VeroClear material, we may quickly 3D print prototype lenses with high clarity and smooth surface finish devoted to our illumination optics,” says Tanassi. “We used a proprietary robotic polishing process for our 3D-printed lenses.” The versatility of Connex3 PolyJet materials gives Nidek the tools to quickly overcome multiple challenges throughout the product development process. From ideation, to iterating prototypes, to clinical evaluation, 3D printing drives innovation, improves product design, saves cost and reduces product development time.
www.objective3d.com.au
World-first in 3D printing gives personal touch to keep the blood flowing Researchers from CSIRO have made it possible to 3D print tailor-made stents, a critical biomedical device used to treat narrow or blocked arteries.
The breakthrough, made in metallurgists around the world. The partnership with Wollongong-based team of scientists at CSIRO’s Lab22 Medical Innovation Hub, represents in Melbourne cracked the problem a paradigm shift in the production using selective laser melting (SLM). of self-expanding nitinol stents for CSIRO Principal Research Scientist Peripheral Arterial Disease (PAD), Dr Sri Lathabai said the process which afflicts more than 10% of allowed them to create complex Australians. PAD is a condition in products with high geometric which fatty deposits collect and accuracy that are patient-specific. reduce blood flow in arteries outside “Nitinol is a shape-memory alloy the heart — most commonly in with superelastic properties,” Dr the legs. People with PAD typically Lathabai said. “It’s a tricky alloy to experience pain when walking The proof-of-concept stents offer the potential for work with in 3D printing conditions, and in severe cases may develop customisation to individual patient requirements, due to its sensitivity to stress and gangrene. but are equally as suitable for mass production. heat. We had to select the right Minister for Industry, Science and 3D-printing parameters to get the Technology, Karen Andrews, said the home-grown technology had ultra-fine mesh structure needed for an endovascular stent, as well the potential to revolutionise the $16bn global stent manufacturing as carefully manage heat treatments so the finished product can industry. expand as needed, once inside the body.” “This is a great example of industry working with our researchers to develop an innovative product that addresses a global need and builds on our sovereign capability,” Minister Andrews said. Until now, surgeons have been restricted to accessing ‘off-theshelf’ stents for operations. The ability to 3D print stents is expected to improve sizing options, preserve essential anatomy, and enable diameters and shapes to suit individual patient requirements. The process could also allow for individual stents to be made on-site, under the surgeon’s direction, reducing inventory and saving money. Finding a way to 3D print a self-expandable nitinol stent without compromising the metal’s unique properties has challenged overseas reliance The process of developing a swab that not only collects the mucus but also allows for the mucus to be transferred for testing has taken several weeks to develop. “We tried several different 3D-printed designs obtained from Harvard Medical School and finally came up with a simple design that is flocked with a safe nylon material,” said Howard Wood & Stuart Grover, joint-CEOs and founders of 3D Printing Studios. “The design, coupled with the EOS P 396 industrial 3D printer for plastic parts will allow us to produce thousands of these medical swabs per day.” South Australian Pathology has tested the latest 3D printed swabs and has given the green light on their use. This makes 3D Printing Studios the only Australian company to manufacture medical nasal swabs, essential products in the fight against COVID-19. This will reduce the need to import these vital products while bringing manufacturing back to Australia. Chief Executive of Medical Innovation Hub Dr Arthur Stanton is a vascular surgeon who has treated thousands of patients and saw a
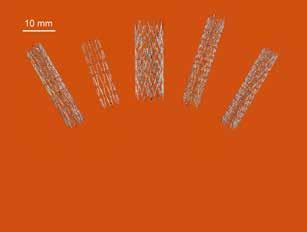
need for an improved treatment. “We believe our new 3D-printed self-expanding nitinol stents offer an improved patient experience through better fitting devices, better conformity to blood vessel and improved recovery times,” Dr Stanton said. “There is also the opportunity for the technology to be used for mass production of stents, potentially at lower cost.” A new company, Flex Memory Ventures, has been established to
www.csiro.au www.flexmemoryventures.com
Locally-made COVID swabs end Australian
Melbourne-based 3D Printing Studios has been working with state governments and health departments to produce medical nasal and throat swabs used in COVID-19 test kits.
drive commercialisation of the technology.
www.johnhart.com.au www.3dprintingstudios.com
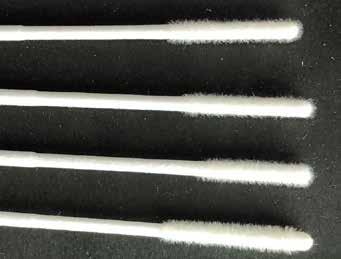