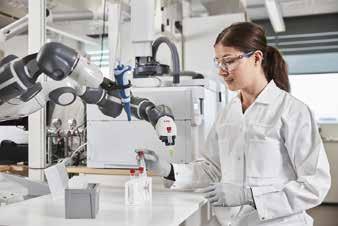
6 minute read
Robots in labs: Making healthcare more productive
from AMT AUG/SEPT 2020
by AMTIL
Robot helpers in laboratories worldwide make healthcare more productive Healthcare has never been more in the spotlight than it is right now. From pharmaceutical and medical device production to medical and research laboratories, the latest robotic solutions can support the human workforce and transform the quality, capacity and cost of operations.
Pharmaceutical and medical device manufacturers are under more pressure than ever before, and need creative solutions that can improve the efficiency and quality of their operations, control costs and speed up research & development (R&D) times to launch products more quickly, while coping with a worldwide shortage of skilled professionals to accomplish these tasks. Automation can help overcome these challenges and improve staff safety, with robots able to complete repetitive tasks up to 50% faster than current manual processes, enhancing productivity and enabling highly skilled manufacturing, medical and laboratory staff to undertake more valuable activities. Accurate, fast, flexible, tireless and able to work 24 hours a day, robots are well suited to repetitive tasks, while also being flexible enough to switch between jobs, as needed. Recent technological advancements have brought robots a long way from their big, heavy-duty predecessors, designed primarily for the automotive industry. Today, robots have smaller footprints, far greater flexibility and integrated vision. Selective Compliance Articulated Robot Arm (SCARA) robots are a good example. Tabletop mountable and with a small footprint, SCARA robots fit well into the confined spaces typical of pharmaceutical manufacturing facilities. Whether they are dealing with tablets, test tubes, or syringes, SCARA robots are fast and accurate, performing articulate point-to-point movements, such as picking and placing, parts transfer, and parts handling. The development of collaborative technologies means robots are also increasingly well suited to laboratories and medical facilities, as they don’t require safety fences to operate safely and efficiently alongside people. Collaboration enables people and robots to safely work together for maximum flexibility and efficiency, sharing the same workspaces and even co-operating on the same tasks, without jeopardising speed and safety. Laboratory and healthcare applications Modern robots are not just found in manufacturing environments or logistic centres, they are increasingly incorporated as components of medical devices in laboratory environments, supporting anything from R&D in the pharmaceutical industry or universities, to healthcare testing in medical facilities. Today’s robots can perform multiple tasks, are easy to program, and may even be able to manage other laboratory equipment. When it comes to general lab work, ABB’s YuMi collaborative robot may be integrated into a device to undertake a range of repetitive, delicate and time-consuming laboratory activities, such as dosing, mixing and pipetting tasks, sterile instrument kitting and centrifuge loading and unloading. Devices integrated with robots may also be able to support temperature-controlled processes by automatically inserting and removing samples to and from special ovens to ensure they are incubated under the correct conditions. While YuMi is the fastest fully collaborative robotic component currently on the market, it is inherently safe in design. With padded arms, collision-detection and no pinch points, YuMi is able to operate safely among its human colleagues in relatively unstructured environments with no need for added safety measures, such as fencing. This enables it to take on a range of repetitive, high-volume tasks, even when they require human-like dexterity or might change at short notice. For example, YuMi can support process tasks such as device tending, collection and storage, sample transportation and filing alongside human lab workers. In one notable application, a YuMi has been integrated by researchers from the European Institute of Oncology, to help staff manage an immuno-assay preparation process used to quantify the presence of virus antibodies. The assay preparation is extremely time-consuming, previously requiring lab staff to perform several repetitive operations, including the washing of well-plates, and YuMi has successfully taken over the washing process. Meanwhile Copan Diagnostics in the USA is using YuMi-based HEPA (high-efficiency particulate air)-filtered bio-safety workstations to manage tissues, bone, and sterile fluid samples, as well as transporting traditional swabs and blood cultures. After the technologist scans a barcode, the robot automatically presents a sequence of plates and materials for sample inoculation. The robot then streaks the plates and transfers them to a system that completes the transportation process. The next step Word is spreading about the advantages of robots in healthcarerelated applications. According to internal ABB research, the global market is estimated to reach nearly 60,000 non-surgical medical robots by 2025, which is a four-fold increase from 2018. In October 2019, ABB opened a new research centre at the Texas Medical Center (TMC) in the US to work alongside the best minds in academia, science and medicine to advance on new robotic and automation concepts for hospitals and medical facilities, laboratories, the pharmaceutical industry and medical device manufacturers. TMC is the largest medical hub in the world, treating 10 million patients a year, and is at the forefront of life science innovation. “With robots now available in a growing range of hygienic designs and able to handle an expanding range of tasks, robotic automation is already making production, testing and R&D more efficient and productive across the healthcare and pharmaceutical industry,” said Marc Segura, ABB’s Managing Director – Consumer Segments & Service Robotics. “The ABB team in our healthcare research centre in Houston is researching new applications and supporting development of new cutting-edge robotics solutions with our partners. Our aim is to reduce the number of manual procedures that need to be performed by people and improve the cost and
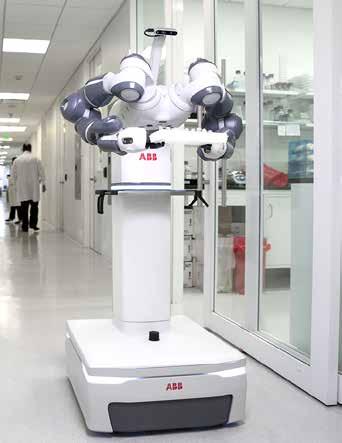

The name to remember ...for all your linear motion needs
accuracy of laboratory work, which will enhance patient satisfaction and ultimately patient safety.” Prototype technologies showcased by ABB at the Healthcare Research Hub since it opened include YuMi robots that may be able to aid in centrifuge tending and test tube handling systems, and an IRB 1200 robot that could execute liquid transfers in a pipetting application. Another prototype concept under development for ABB Healthcare Robots is a mobile dual-arm YuMi robot. Designed to assist medical and laboratory staff with laboratory and logistics tasks in hospitals, it may be able to sense and navigate its way around its human coworkers autonomously, while learning to find different routes from one location to another. It has the potential to undertake a wide range of repetitive and time-consuming activities, including preparation of medicines, loading and unloading of medical devices, pipetting and handling liquids and picking up and sorting test tubes. The mobile YuMi could also be developed to be used in hospitals for a wide variety of logistics roles, including dispensing medicines, transporting them to where they are needed in hospitals, bringing medical supplies to hospital staff and bed linen direct to patients’ bedrooms. All prototype activities are focused on future technologies that apply to common medical laboratory tasks that robotic automation may be able to support, by combining consistent performance with a level of flexibility and continuous operation that may increase throughput and quality while also minimising costs. As prototypes, they are not medical devices and are not yet available for sale. While YuMi and other ABB robotic components have broad potential in medical applications, each medical device must undergo a robust design and testing process to assess if the device can safely perform its intended use for each unique medical application before being commercialised. It is the sole responsibility of the medical device manufacturers to conform to all applicable laws, standards, and guidelines.
www.abb.com/au
With over 35 years of experience, Linear Technik has gained an enviable reputation as Australia’s leading supplier of Linear Components.
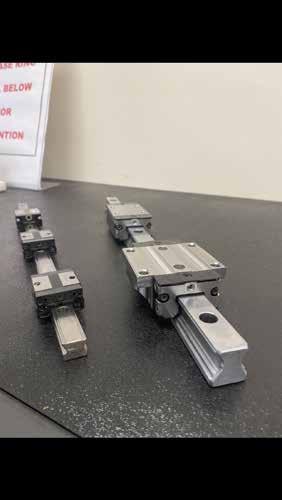
Our product and industry knowledge is second to none and our range covers all aspects of Linear Motion Technology.
• Expert Product Knowledge • Huge Stock Holdings • Fast Access to all Brands • 24/7 Breakdown Service • Fully equipped Workshop facilities • Same Day Despatch to all States on Stocked Products
Linear Technik has a solution for all Linear applications!
LINEAR BEARINGS
LINEAR SETS
ALUMINIUM PROFILES
PROFILE RAIL GUIDES