
5 minute read
Robovoid: Using AM to support construction innovation
from AMT AUG/SEPT 2020
by AMTIL
Robovoid: Using additive manufacturing to support construction innovation
When Victorian start-up Robovoid Pty Ltd needed to develop sophisticated new tooling for its innovative new concrete construction system, it turned to 3D printing – and AMTIL’s Additive Manufacturing Hub – to find a solution.
Robovoid Pty Ltd was established in July 2018 by Dr John Stehle and Scott Olding for the specific purpose to research, develop and commercialise Stehle’s Robovoid Invention. The Robovoid Invention is a patent-pending recycled plastic void former for concrete construction applications. The Robovoid Invention has drawn on Stehle’s previous experience developing new and innovative precast construction solutions, an example being the innovative dowel connection system adopted in the flooring system implemented for the Leadenhall Building (aka the “Cheesegrater”) in London. On the back of Stehle’s 25-year career in the construction industry, and with a strong desire by Stehle and Olding to introduce new solutions to the industry that reduce the environmental impact of new construction, the Robovoid Invention commenced its development journey. The Robovoid Invention involves multiple research & development (R&D) components but one of the key areas identified at the beginning of the project was how to make the Robovoid recycled plastic components, or Robovoid Components. Of course, a key criterion in determining how to make the Robovoid Components was the anticipated cost per unit – the production process had to be efficient! It had to be a production process that could produce Robovoid Components in large volumes at a low cost. The challenge Robovoid’s product design heavily involved the application of DfMA (Design for Manufacturing and Assembly) principles, of which Stehle had extensive experience from the construction industry. In going down the path to research, design and develop an injection moulding tool to produce the Robovoid Components, the Robovoid team met and spoke with many suppliers to the industry about the complexity of its mould design (which continued to evolve), and the ability to achieve a suitable cycle time to make the process as efficient as possible. Two of the reasons for the complexity of Robovoid’s mould design were the complex part geometry itself, and the configuration of the cooling channels within the mould. The design complexity and the observed limitations of traditional toolmaking techniques resulted in Stehle and Olding considering metal 3D printing for some elements of the injection moulding tool. During this phase of the project they met with Amiga Engineering and discussed their mould design with Managing Director Michael Bourchier and his team. At this stage they also met with John Croft, Manager of the Additive Manufacturing Hub (AM Hub) at AMTIL, and to hear about the Hub’s voucher programme to promote and support additive manufacturing. The experience and expertise of the Amiga team coupled with the support of the AM Hub enabled Robovoid to continue exploring the process and benefits of metal 3D printing components of the overall injection moulding tool. “We had to think about things such as: plastic flow (as defined by rheology), thermal shrinkage, support conditions during the 3D build process, how to incorporate cooling channels in the mould, and the part ejection method and mould draw requirements,” says Stehle. Robovoid, its toolmaker Geetha Engineering and the team at Amiga agreed that the moulding tool would utilise H13 tool steel, which is a very tough, high-strength steel. This material is commonly used in injection moulding applications to deal with the high stress and repeat loading environment. However, to the best of the team’s collective knowledge, H13 tool steel had never been used before
Dr John Stehle developed the Robovoid Invention.
to 3D print an application this large and complex (approximately 200mm by 200mm by 170mm high). Indeed, Amiga was advised by experts in Germany that it could not be done. This, of course, was the motivation the team needed to get it done! The solution It goes without saying that 3D printing requires 3D modelling to happen first, which included parametric modelling, and basic mould flow and finite element analysis. Before committing to part geometry and steel mould investment for a prototype mould, the Robovoid team wisely tested its part geometry using 3D printing methods via a selective laser sintering (SLS) method and nylon material. 3D Systems Asia Pacific provided an excellent service with this part of the process (which was also financially supported by the AM Hub voucher). In particular, Robovoid was able to physically test and evaluate multiple versions of the ‘click together connection’ design developed by Stehle.
Since injection moulding involves the flow of hot plastic in its liquid state, it can easily escape from any gaps, so Robovoid needed a tool to be produced within a tolerance of +/-0.05mm. While the complex analyses carried out by Amiga indicated that this was theoretically possible, there remained a very real technical risk that it may not be feasible. As it turned out, this was not a straightforward assignment and there were unforeseen technical challenges and some delays. However, with a lot of hard work and persistence, Amiga was (to their great credit) able to produce all the pieces requested and supplied them to Geetha to be incorporated into the wider injection moulding tool. Key developments that Amiga pioneered on this R&D journey included bespoke cooling and air filtering and extraction systems. Amiga also implemented state-of-the art build analysis so that thermal distortions caused by the high-temperature lasers required to melt the metallic powder could be predicted and compensated via an iterative nonlinear time-history optimisation routine. Geetha, which predominantly uses traditional mould-making techniques, was very pleased with the accuracy eventually achieved from the 3D printing process and the toughness of the material. Geetha did have to manually polish the mould and make a number of manual adjustments over a period of time as Robovoid tested (and continues to test) the performance of the mould in a trial production environment. The financial support provided by the AM Hub voucher program was a key enabler for Robovoid to consider and pursue metal 3D printing as part of our overall project. The AM Hub voucher also provided financial support for the testing of part geometry in collaboration with 3D Systems Asia Pacific.
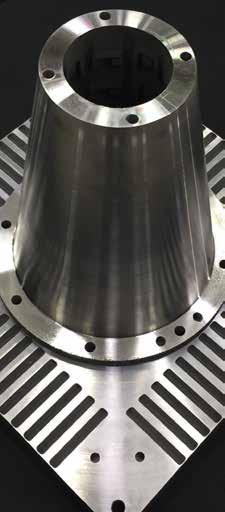
The outcome The Robovoid team was aware of the limitations of traditional toolmaking techniques and the impact that this would likely have on the performance of its injection moulding tool. Despite the new challenges and uncertainty faced from opting to use metal 3D printing as part of the overall process to produce the mould, the desired design outcomes could not have been achieved by solely adopting traditional mould-making techniques. In recent times Robovoid has successfully produced Robovoid Components in small batches using this prototype injection moulding tool. At the end of the day, Stehle and Olding believe they now have a better tool design and production process to move forward with, and to take the learnings from their wider R&D program to produce version two of the tool in the near future.
www.amhub.net.au www.robovoid.com
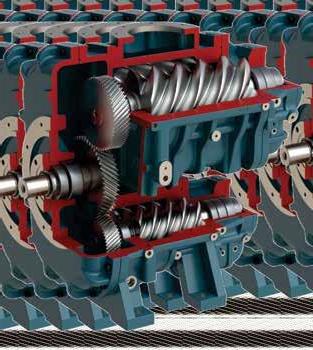
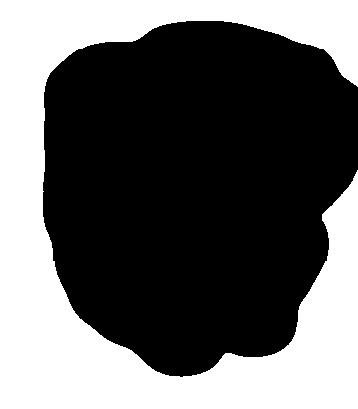