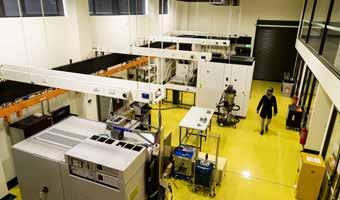
26 minute read
INDUSTRY NEWS: Current news from the Industry
from AMT FEB/MAR 2022
by AMTIL
Sydney’s “factory of the future” ready to drive innovation
A $25m facility has been launched to drive innovation and foster industrial output in the heart of Sydney’s Tech Central. The facility is a foundational node for complementary facilities that support the NSW Government’s projects at Western Sydney Aerotropolis and Western Sydney parklands.
Located in the Engineering precinct of the University of Sydney’s Darlington campus, the Sydney Manufacturing Hub is a new manufacturing-focused research facility that will work alongside industry to deliver cutting-edge R&D in additive manufacturing and materials processing. It is geared to enable concept-to-production demonstration capabilities, including advanced pre- and postprocessing of materials for faculty, students, small and mediumsized companies, and, if needed, larger companies to experience and leverage metal 3D printing and advanced manufacturing. The Hub provides capabilities for design; topological optimisation; 3D printing of metals, ceramics and polymers; as well as postprocessing heat treatment, advanced characterisation and more, paving the way for new technology in industries like aerospace, autonomous vehicles, biomedical, defence, maritime, and robotics. University of Sydney Vice-Chancellor Professor Mark Scott AO said the University has continued to demonstrate its capability as a R&D leader in the region by working closely with both the public and private sector: “The Sydney Manufacturing Hub is a key demonstrator for what’s ultimately possible when government, industry and higher education work together on high-impact technologies. This is evidenced not only through the establishment of this new research facility, but also via our collaborative projects in Greater Sydney, particularly the Western Sydney Parklands and Aerotropolis.” Director of the University of Sydney’s Core Research Facilities Professor Simon Ringer said the Sydney Manufacturing Hub would drive the state’s ‘Industry 5.0’ revolution: “Advanced manufacturing is making the previously impossible possible. Key industries will benefit from these technologies through the reduction of material waste, simplified supply chains, and an independent capacity to create materials, components and even whole machines – all of which weren't possible using traditional manufacturing. Using these technologies we could soon see Australian-designed and built space rocket engines, hypersonic vehicles, satellites, eco-active building and construction, and fast tracking of the electrification revolution in propulsion. It will even be transformative for areas like health – our team has recently leveraged additive manufacturing in the production of custom orthopaedic implants to help with patientspecific needs. We are witnessing a dramatic disruption in how materials are made that’s driving research breakthroughs.' “On one hand, we are looking at the periodic table with fresh eyes – additive manufacturing lets us combine elements to make new materials with entirely new combinations of properties at scale. On the other hand, additive and advanced manufacturing has made manufacturing more accessible, with digital workflows making it easier for local companies to enter competitive global markets.” The research facility places Sydney at the centre of a new skills based development and puts the gears in motion for the state’s advanced Industry 5.0 output. The facility will provide specialised consulting, fabrication activation and training to its industrial partners, providing both guided and autonomous access to the facilities for the purposes of testing, research and fabrication.
www.sydney.edu.au
BAE Systems lands new $80m F-35 contract
BAE Systems Australia in December was awarded a new F-35 Air Vehicle Support Services (AVSS) contract to establish sovereign maintenance and supply-chain support for the Australian fleet at RAAF Bases Williamtown in New South Wales and Tindal in the Northern Territory.
“We are delighted to build on our contribution to the global F-35 program with this additional support for the RAAF,” said Andrew Gresham, BAE Systems Australia Managing Director, Defence Delivery. “We will be leveraging our years of experience in fast jet sustainment working side by side with the RAAF to deliver aircraft availability and capability requirements.” Maintaining and sustaining the global F-35 capability will create around 360 new direct jobs at BAE Systems Australia over the next 10 years and develop a specialist supply chain across Australia of more than 70 SMEs by 2025. BAE Systems has provided fast jet maintenance and upgrades to RAAF aircraft from its Williamtown facility for almost three decades and employs nearly 460 people in the precinct. The new AVSS contract will employ 46 BAE Systems Australia staff, providing direct, on-theground support to RAAF personnel sustaining the F-35. The company will have around 130 people working to support F-35 aircraft maintenance by the end of the year, having also recruited 25 former Jetstar technicians during the downturn in commercial aviation caused by COVID-19. As a key partner and integral part of the industry team with Lockheed Martin, BAE Systems delivers up to 15% of each fifth generation aircraft globally. This includes the advanced manufacture of the aft fuselage, empennage, and crucial components from our facilities in the UK and Australia, and advanced electronic warfare capability from our US business. Parts of the vertical tail, corrosion prognostics and avionics are manufactured by BAE Systems in South Australia.
www.baesystems.com
CSIRO, Boeing launch new five-year $41m R&D partnership
Improving sustainability and using digital technologies to boost productivity are among the focus areas of a new five-year research program launched by CSIRO and Boeing, the world’s largest aerospace company.
Building on 32 years of joint research, the new agreement will see the partners invest up to $41m across areas of mutual interest. CSIRO Chief Executive Dr Larry Marshall said the Boeing relationship represented a success story of science partnering with industry to create impact. “CSIRO has existed for more than 100 years to help industry solve its greatest challenges and create a prosperous society,” Dr Marshall said. “Our partnership with Boeing is a shining example of that, science delivering real solutions for aviation and aerospace industries and creating economic benefits for Australia and jobs for Australians that we know from our history will continue to deliver value for decades. “The next five years will see our science really move the needle on innovation to create sustainable solutions that deliver the great challenge of lowering emissions while expanding our economy at the same time – but that’s what science does.” CSIRO has been named Boeing’s Supplier of the year on four occasions: 2011, 2016, 2017 and 2018 in the Environmental category. The parties have made numerous breakthroughs since first partnering in 1989. These include CSIRO’s ‘Paintbond’ technology, which has been applied to more than a thousand Boeing aeroplanes around the world, saving millions of dollars in maintenance costs. Greg Hyslop, Chief Engineer of The Boeing Company and executive vice president of Boeing Engineering, Test & Technology welcomed the partnership: “Years of research and development is at the core of every critical innovation in aerospace. Our new multiyear agreement with CSIRO will lead to a more sustainable aviation industry, building upon our decades-long partnership that has already produced so many significant advancements for Boeing and our customers.” Over the years CSIRO and Boeing have invested more than $200m on joint research projects. The strong relationship with CSIRO was a key factor in Boeing choosing Australia as the location for its largest research & development operation outside the United States. CSIRO’s Chief Technical Advisor to Boeing Shravan Singh said the next few years would see the organisations ramp up projects focused on using AI, machine learning and creating digital twins to improve efficiency and lower costs. “There is also huge potential to use CSIRO’s deep expertise in sustainability to reduce environmental impacts right across the value chain from airplane manufacturing, right through to optimising times around flight operations,” said Singh.
www.csiro.au www.boeing.com.au
David Pook, BR&T-A Melbourne Centre Manager, and Shravan Singh, CSIRO Senior Technical Adviser to Boeing.
A proud Australian manufacturer of diverse bespoke metal products for 68 years.
EXTENSION TORSION COMPRESSION



Get in touch today…
T +61 7 3271 3500 E sales@marshalliance.com.au W marshalliance.com.au
Toyota opens state-of-the-art product centre in Altona
Toyota Australia has opened a state-of-the-art Product Centre at its Centre of Excellence (CoE) facility in Altona, Victoria.
The new Product Centre brings together all of Toyota’s local planning, design, engineering and evaluation teams in the same facility, ensuring the world-class Australian teams will continue to design and develop unique products for the Australian and global markets. These teams were behind such models as the HiLux Rugged X and HiLux Rogue. The new facility will allow for an unmatched level of collaboration across departments. Mike Rausa, Vice President Product, Guest and Aftersales Operations at Toyota Australia, said the new facility would give the product design, engineering and evaluation teams even more opportunities to create exciting products. “We’ve already seen what our planning and development teams are capable of, with vehicles like the HiLux Rugged X and HiLux Rogue proving to be popular here in Australia and creating accessories that are adopted in markets around the world,” Rausa said. “We wanted to retain and build on the capability developed during our long history of vehicle manufacturing, providing a highly collaborative environment that would allow Australian design and engineering expertise and know-how to be utilised within the broad Toyota family. The new Product Centre delivers just that, keeping jobs, skills and career paths grounded in Australia.” The Product Centre is housed inside the former powertrain manufacturing building that produced over 2.5 million locally built engines from 1978 to 2017, ensuring that Toyota’s positive impact on the local economy will continue. It reflects the desire of Toyota Motor Company global President Akio Toyoda, who stated that he wanted to leave a legacy at the Altona manufacturing site, and of former Toyota Australia President and Chairman Max Yasuda, who had a vision to create a centre that built better ways of working – with highly skilled people creating excellent products. Toyota Australia Product Planning and Development General Manager Rod Ferguson said the new Product Centre would foster an environment for Australia to spearhead exciting new projects for the local market and beyond. “Our design and engineering teams are highly utilised by Toyota affiliates around the world, thanks to their exceptional ability to create products that resonate with customers across the globe,” Ferguson said. “Having previously been based at multiple facilities around Melbourne, consolidating the product teams on one site in a state-of-the art facility, alongside other business functions, will foster a level of collaboration that hasn’t been possible before. The new Toyota Product Centre ensures Toyota’s legacy of locally developed products will continue for decades to come.” Toyota has invested about $40m in the construction of the Product Centre, forming part of the $150m overall investment in the CoE. The CoE also houses the industry-leading Hydrogen Centre and hydrogen production, storage and re-fuelling facility, which will help in the creation of sustainable mobility solutions, with the capacity to produce up to 80kg of hydrogen per day while serving as a commercial-grade refuelling outlet for commercial and passenger fuel cell electric vehicles (FCEVs).
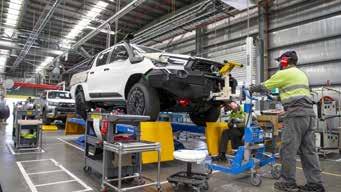
Weld Australia has called on governments to have confidence in Australian manufacturing in the wake of several faults in New South Wales’ trams and ferries.
All 12 trams that normally run on the Central to Dulwich Hill line were decommissioned in November. Major cracking was found in the trams, which were manufactured in Spain. The trams only came into service in 2014 and are already out of warranty, which means New South Wales taxpayers could be liable to foot the repair bill. This was quickly followed by the suspension of the Newcastle light rail after a mechanical issue was identified in the trams, which were built by the same Spanish manufacturer behind the Dulwich Hill fleet. A number of cracks were also recently discovered in the hull of one Sydney’s new Manly ferries. An independent report identified several welding defects onboard the Balmoral—one of the Emerald-class ferries, which were built in Indonesia and China. Weld Australia CEO Geoff Crittenden said: “Australian manufacturing, fabrication and welding companies are globally competitive and more than capable of delivering infrastructure like Sydney’s trams and ferries on time and, more importantly, in accordance with all relevant international Standards. “We need a commitment from our governments to increase levels of local content for all procurement decisions. We need to bring home the manufacture of goods like trams and ferries. There really is no reason for our Governments not to onshore this manufacturing work—Australian manufacturers are ready, willing and more than capable.” Manufacturing is a key contributor to the Australian economy. According to the Federal Government’s Australian Manufacturing Performance Report, manufacturing contributes $100bn to the Australian GDP every year, employs around 1 million people, and is responsible for an astounding 26% of all business expenditure on R&D in Australia. “Australian manufacturing is world-class,” said Crittenden. “We need our Governments to recognise that local manufacturers, fabricators and welders have the capability and capacity to deliver their local asset and infrastructure needs. Government procurement decisions must prioritise Australian manufacturing.”
www.weldaustralia.com.au
USQ, Wagners breaking new ground
Engineering makes things easier, accessible, innovative, and cost-effective. This concept is key to the partnership between the University of Southern Queensland (USQ), Wagners Composite Fibre Technologies (CFT) and Allnex Composites
The partnership started in 2019 through a $10m Cooperative Research Centres program, to produce cutting-edge innovation in composite manufacturing. Their newest innovation has reimagined a fundamental production process from concept design and now mass production. Historically Wagners CFT bonded two square profiles to produce rectangular sections for use as joists in structures such as bridges and boardwalks. However, sanding and bonding was an expensive and time-consuming process. After years of research & development (R&D), Wagners CFT is now able to produce high-performing large, hollow rectangular composite profiles through a novel pull-winding process at its composite manufacturing facility in Toowoomba. This technology will also be replicated for manufacture in their new facility in Texas, USA. These composite profiles are an alternative to steel, aluminium and timber due to their non-corrosive, resilient, lightweight, high strength and neutral electromagnetic nature. Michael Kemp, General Manager – New Generation Building Materials (NGBM) at Wagners CFT, said through R&D, the partnership with USQ and Allnex had produced a cost-effective and efficient solution. “This is an innovation that took our pultrusion technology to the next level, ensuring we are at the forefront of global composite manufacturing,” he said. “The new process not only saves time, money and environmental waste but also, by optimising the joist and shape, improves flexural performance by approximately 35%. “This project demonstrates our commitment to research and development. We continue to invest in new product lines and production efficiencies to ensure the continued growth and expansion of our Composite Fibre Technologies business.” USQ’s Professor Peter Schubel, Executive Director of the Institute for Advanced Engineering and Space Sciences, said the University’s long-standing relationship with Wagners held great potential for industry. “Our interests are well aligned and the ongoing collaboration means that we will continue to contribute to the civil composites sector, as well as other high growth areas of composite pultrusion such as telecommunications,” he said.
www.usq.edu.au www.wagner.com.au
Sustainability could be the major focus of Australia’s post-pandemic recovery, with new research revealing Australian businesses, on average, will put 57% more budget, time and people towards environmental initiatives.
The findings come from the 2021 Australian Business Assurance Report by risk management consiltancy SAI Global, based on a survey of 328 Australian executives. The report found that 85% of businesses are already taking measures to reduce their environmental impact. Waste management seems to be the leading, and most manageable concern: 57% of executives say their organisations are reducing waste management processes including reusing, refurbishing, recycling and disposal. Businesses are also focused on reducing their emissions. Almost half (48% of businesses) are reducing their energy consumption, 24% are increasing local sourcing and 23% are reducing travel and product transportation. Large organisations (more than 501 employees) seem to be taking charge in reducing emissions, with two thirds (66%) focusing on reducing their energy consumption, compared with 41% of small businesses (fewer than 50 employees). More than a quarter (29%) are reducing their travel and transportation emissions, compared with 21% of small businesses. Saeid Nikdel, environmental management systems expert at SAI Global, believes the COVID-19 crisis has caused a fundamental shift in the current trajectory and presented an opportunity for businesses to rebuild more sustainably. “The global pandemic has presented many challenges to businesses, but the silver lining of the crisis is that it allows us to rethink our future and build resilience to other challenges such as climate change,” says Nikdel. “The pandemic also hastened the transition to a hybrid working model, which has resulted in employees avoiding unnecessary face-to-face meetings as well as domestic and global travel, in turn, reducing fossil fuel depletion and the associated impacts on climate change. As we emerge from the pandemic, it’s imperative that businesses looking to put more resources toward environmental sustainability create a multi-faceted approach that focuses on a range of measures.” Less common are taking measures to improve efficiency of resource-heavy processes, which only 17% of businesses are acting on, and improving end-of-life treatment of products, chosen by 14%. “While many businesses say they are taking strides to reduce their waste management, energy consumption and emissions, not enough businesses are taking a holistic approach to environmental sustainability to also look at the lifecycle of their products, better uses of raw materials and natural resources, and better utilisation of space. The end-of-life treatment of products, how they are stored and how raw materials are acquired and extracted all have an impact on a company’s environmental impact and should be considered when developing an environmental strategy.” To help them with this strategy, almost a third (31%) of businesses said they will review their environmental policy. However, Nikdel believes this is not enough: “An environmental policy is simply a statement that outlines an organisation’s commitments to sustainability. Whereas, adopting an environmental management system, such as the ISO 14001 standard, will improve an organisation’s ability to develop and implement policies, objectives, procedures, and governances to deliver environmentally responsible and sustainable business practices. “When an organisation successfully certifies to a management system, they don’t just focus on their own people and their own organisation. To properly address sustainability, businesses are best to look across their entire operations, to their suppliers and partners, to ensure there is environmental consideration in the production, design, transportation and disposal – the full lifecycle – of their products or services.”
Dan Grant steps down at MTPConnect
After more than three years as Managing Director and CEO of MTPConnect, Dr Dan Grant is leaving the organisation and Stuart Dignam has been appointed to the interim CEO role.
Dr Grant was appointed as CEO of MTPConnect, the Growth Centre for Australia’s Medical Technology, Biotechnology and Pharmaceutical sector, in July 2018 when the organisation was responsible for the $15.6m Growth Centre Project Fund and a $10m granting program from the Medical Research Future Fund (MRFF) with a team of six. MTPConnect today has more than $180m in project funds under management, including five programs delivered for the MRFF, and a team of 24. MTPConnect’s six strategic funding programs have so far seen $95m committed to 145 projects across Australia. These investments have yielded an additional $566m in industry contributions and flowon external investment. MTPConnect has also assisted research institutes and SMEs with their translational and industry-focused grant applications, with 64 MTPConnect-assisted projects securing grants worth $307m. Dr Grant says the time is right for a change: “I am so proud of our team at MTPConnect. Together, we’ve built the organisation to be a significant player in Australia’s medical products landscape. When you look at the funding allocated through our granting programs, the additional contributions provided by industry, the flow-on external investments and the money secured through grant reviews, MTPConnect has contributed to $968m flowing into Australia’s medical products sector. With such strong outcomes secured, along with longer-term certainty for MTPConnect, the time is right for me to pursue new opportunities and spend more time with my family.” MTPConnect Chair Sue MacLeman thanked Dr Grant for his contribution to MTPConnect and the growth of the sector: “When Dan was appointed, he was tasked with taking our organisation to the next level, a challenge he’s met and exceeded. Due in no small part to Dan’s contribution, MTPConnect is making a real difference to Australia’s medical products sector, supporting innovative projects across the country with funding, driving enhanced collaboration between research and industry and boosting commercialisation outcomes. On behalf of the Board, I sincerely thank Dan for his leadership, passion for the sector and hard work and wish him all the very best for the future. “In recognition of our success to date, the Government has approved an additional one year of operation for MTPConnect, and other Growth Centres, through until 30 June 2023. This means our MTPConnect team can continue its fantastic work in supporting the development, manufacturing, translation and commercialisation of medical products and innovations, and the workforce skills needed to drive those outcomes.” The MTPConnect Board will undertake a search for a new CEO. MTPConnect’s Chief Operating Officer, Stuart Dignam, has accepted the role of interim CEO. www.mtpconnect.org.au
It’s what you can’t see that is the biggest risk to your growth.
Get the visibility you need to efficiently control everything from bill of materials to production planning and inventory.
BusinessHub specialises in delivering MYOB Advanced: a cloud ERP (Enterprise Resource Planning) tool for manufacturing businesses like yours. Our expertise allows us to tailor a business solution to give you full control. With ongoing support and clarity, we’ll improve the efficiencies of all your key business areas: Inventory, Accounts, Customers and Production. Visit the BusinessHub exhibition during Australian Manufacturing Week at the The International Convention Centre Sydney (ICC Sydney) from 7-10 June 2022.
We’re here to set you up for success. phone 1300 733 071 � businesshub.com.au/AMTIL
Elexon Electronics named Moreton Bay Region’s Business of the Year
AMTIL member Elexon Electronics has proudly accepted the inaugural Advanced Manufacturing Excellence Award and has been named Business of the Year in the 2021 Moreton Bay Region Business Excellence and Innowvation Awards.
Operating for more than 15 years, Brendalebased Elexon Electronics has continually evolved in response to both changing customer needs and developments within the mining, medical and defence industries, while also being a passionate contributor to the Moreton Bay regional community. It received its award in a ceremony delivered by Moreton Bay Region Industry and Tourism (MBRIT) in partnership with Moreton Bay Regional Council. “Being recognised in the sector of Advanced Manufacturing is quite an achievement especially during this challenging year,” said Frank Faller, CEO of Elexon Electronics. “It recognises our outstanding performance and is our testament to our continuous development. It also marks an important return of customer confidence, shifting from a dependence on overseas suppliers to homegrown manufacturing talent and capability once again.” The event featured 58 finalists across 12 categories, after a record number of businesses from a diverse range of sectors were nominated. The winners were decided via a judging process involving 40 expert judges, who evaluated nominations based on industry world best-practice. Taking out the top award, Elexon Electronics said it was honoured to stand alongside the other highly acclaimed local participating businesses. It also praised the collaborative atmosphere in the region, which promotes healthy competition and inspires excellence.
www.elexonelectronics.com

IMCRC catalyses over $230m to advance Australian manufacturing
The Innovative Manufacturing Cooperative Research Centre (IMCRC) announced in December that it has catalysed to date more than $230m investment in manufacturing innovation, research and development (R&D) across Australia.
The announcement coincided with the release of IMCRC’s Annual Highlights Report, which summarises the CRC’s achievements for the 2020-21 financial year and includes interviews and case studies with executives from leading manufacturing businesses, startups and small and medium enterprises (SMEs). IMCRC has established a unique manufacturing investment portfolio of 70 industry-led R&D projects that delivers a seven-fold multiple on the Commonwealth cash invested. To date, eight projects have been successfully completed, already furthering the collective research outcomes that will bring substantial economic value and high value jobs to Australia’s manufacturing industry. IMCRC CEO and Managing Director, David Chuter, said the achievements highlighted the CRC’s unwavering commitment to the transformation of Australian manufacturing. “As an industry-led CRC, we incentivise and enable forward-thinking businesses to collaborate with Australian universities and the CSIRO to develop, scale up and realise new ideas, products and services,” said Chuter. “Our business model is designed to catalyse manufacturing innovation and R&D projects of strategic importance to our industry and research partners. It centres around safeguarding government and industry funding by requiring partners to set clear strategic and commercial outcomes from the outset and by putting in place processes to overcome barriers to collaborative success. “As more IMCRC projects reach completion, I am optimistic about what could be achieved using the IMCRC business model at scale to drive further Australian manufacturing innovation and transformation, particularly with Australian SMEs, who represent around 80% of our industry project partners.” One of the projects completed in 2021 is the Urban Art Project (UAP) Design Robotics Project. Since receiving $1.2m in project cash funding from IMCRC to develop visionenabled, agile and adaptable robots, UAP founder and Managing Director Matt Tobin said UAP had been adopting advanced manufacturing techniques and robotics, enabling the company to re-shore much of its production to Australia. “The IMCRC has been a catalyst for fundamental change in our business. Industry 4.0 technologies, such as the robotics we are integrating into our processes, are changing manufacturing,” Tobin said. “Without investment in these types of research partnerships, Australian industry will lose all ability to transform, and the impact on our global competitiveness will be devastating.” The research collaboration with UAP, the Queensland University of Technology and RMIT University also directly led to the $18m Advanced Robotics for Manufacturing (ARM) Hub in Brisbane. Ian Macfarlane, IMCRC Chair, said success stories like UAP were a testament to the efforts of the industry and research partners and the IMCRC team’s ability to rally organisations together and develop collaborative solutions at pace.
www.imcrc.org/annual_highlights
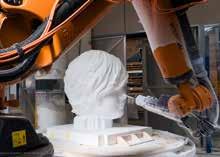
SA establishes Australian Space Park
A pipeline of exciting local jobs for both now and the future have been further secured amid the massive announcement that South Australia will be the site for the nation’s first dedicated space manufacturing hub.
The establishment of Australian Space Park aims to cement South Australia as the nation’s Space State and provide a vital manufacturing link to the local space industry value chain. Four companies are partnering with the South Australian Government to develop the space sector in South Australia through the purposebuilt facility: Fleet Space Technologies, Q-CTRL, ATSpace and Alauda Aeronautics. With the Australian Space Agency and Mission Control already based in Adelaide, the Australian Space Park will boost space manufacturing capability and capacity by initially co-locating four space manufacturing companies in a purpose-built facility with a focus on collaboration and production of small satellites and their payloads, rockets, electrical vertical take-off and landing vehicles (eVTOL), and supporting componentry and technical systems. Premier Steven Marshall announced the State Liberal Government would be contributing a $20m investment in the Australian Space Park, which is anticipated to create approximately 220 highly skilled space industry roles within the first two years of operation, further building out the Space ecosystem in South Australia as the national centre for this emerging industry. Discussions with the Adelaide Airport are ongoing as a potential location for the Park. “The creation of the Australian Space Park signals our commitment to the South Australian and Australian space sector by bridging the gap between research and development and prototyping to production at scale,” Premier Marshall said. “The Hub aligns with Australia’s space strategy that aims to triple the space sector’s contribution to GDP to over $12bn per annum and create up to an additional 20,000 jobs by 2030. It is fantastic to have four amazing companies partner with the South Australian Government on this initiative.” Adelaide Airport has been identified by the industry consortium as an ideal location for the Australian Space Park due to its proximity to traditional aerospace companies and the central business district and innovation precinct, Lot Fourteen, which is home to a growing community of space companies. Adelaide Airport Managing Director, Mark Young, said the Airport Business District offered excellent connectivity with national and international users. “We’re excited to be identified as the potential site of the Australian Space Park,” Young said. “In addition to our central location, we offer suitable land opportunities both for the hub as well as room for growth and to attract like-minded businesses keen to play a role in the growing space sector.” As the centrepiece of the nation’s space endeavours and building upon South Australia’s strong starting position in the New Space economy, the state is presently targeting an annual growth rate in the space sector of 5.8% over the next decade.
www.invest.sa.gov.au/australianspacepark
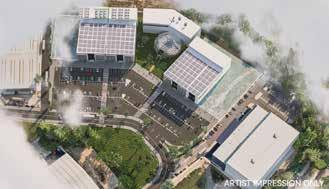
ReMade in Australia tackles waste
The Federal Government has launched ReMade in Australia – a national campaign urging Australians to recycle more, and show how they can help create jobs and protect our environment.
Prime Minister Scott Morrison announced ReMade in Australia on 6 December, saying it was a critical step in giving Australians the confidence to recycle more and to buy products manufactured with recycled content. “We are taking responsibility for our waste, we put a stop to it being shipped overseas as someone else’s problem and we have made recycling one of six national manufacturing priorities,” said Morrison. “Australians are doing the right thing and they want to be assured that the efforts they make in recycling at their homes and workplaces are delivering real outcomes, from the roads they drive on to the sunglasses they choose to wear. “We need to recycle even more and this campaign will help consumers and business understand the benefits that recycling can deliver for our environment and for jobs. ReMade in Australia builds on the pride we all have in Australian made and the pride we take in doing the right thing for our environment.” Minister for the Environment Sussan Ley said that recycling can reduce pressure on our environment and create Australian manufacturing jobs: “The Morrison Government is driving a billion dollar transformation of Australia’s waste and recycling industry, through the Recycling Modernisation Fund. We are seeing governments and industry investing in the commissioning of new plant and equipment, and our waste export bans are driving fundamental change. ReMade in Australia will help Australians understand the ways they are contributing through both recycling and the choices they make at the checkout.” Assistant Minister for Waste Reduction and Environmental Management Trevor Evans said that now was the right time for Australian businesses and consumers to think ReMade Australia: “This campaign taps into the pride Australians have in doing the right thing for the environment. At a time of year when people are buying gifts and unwrapping tonnes of packaging, it is all the more important to have recycling front of mind.”
www.awe.gov.au/remadeinaustralia
