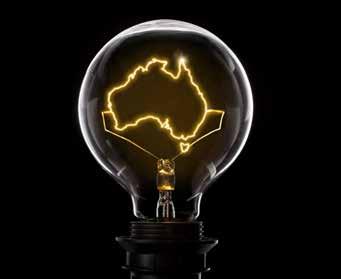
27 minute read
VOICEBOX: Opinions from the manufacturing industry
from AMT FEB/MAR 2022
by AMTIL
CSIRO: Every dollar invested in R&D creates $3.50 in benefits for Australia
Each dollar invested in research & development (R&D) would earn an average of A$3.50 in economy-wide benefits for Australia, according to evidence compiled in a new report from CSIRO. By Katherine Wynn, Jasmine Cohen and Mingji Liu.
Many Australians know research & development drives economic growth and improves our well-being and prosperity. However, few could describe the size of the relationship between Australia’s research & development spending and economic growth, or compare this to performance on other typical investment returns. Examples of future industries that could be unlocked by research & development in Australia include the quantum technology and hydrogen industries. Examples of emerging technologies that could change the way Australians work and live include artificial intelligence and robotics. This is significant, given that recent figures from the Australian Bureau of Statistics show that business spending on research & development as a proportion of GDP is just half the OECD average, and the lowest it has been since 2003. We hope our analysis will raise awareness of the value of this kind of spending, and its importance for Australia’s economic recovery and long-term resilience. Investing in innovation now is crucial for the future. In consultation with government and academic stakeholders, our team at CSIRO Futures, the strategic and economic advisory arm of Australia’s national science agency, used a new yet simple economic approach to quantify the return on investment in overall research & development spending for Australia. By adapting a method originally developed in the US, we calculated return on investment by defining the relationship between domestic gross spending on research & development, and the growth in per capita gross domestic product (GDP) that follows as a result. This method encompasses both successful and unsuccessful research & development investments, and quantifies only monetary benefits (excluding non-monetary social and environmental benefits). Our approach also accounts for delays between research & development investments and payoffs, and for the capital costs of integrating research & development into the economy. For example, an innovation of new computer software must be built into existing computer systems, and might therefore take a decade before its use becomes widespread. Overall, we calculate that one dollar of research & development investment creates an average of $3.50 in economy-wide benefits in today’s dollars, and a 10% average annual return for Australia. By removing the considerations of delays and capital costs, we can also calculate an upper boundary on our estimate – that is, the maximum theoretical return on investment barring any hurdles along the way. This unadjusted result, which does not account for the additional time and costs associated with integrating research & development into the economy, is estimated as creating $20.80 in economy-wide benefits, and a 104% average annual return for every dollar spent on research & development in Australia. Even with our conservative estimate of $3.50 return on the dollar, the expected benefits of investing in innovation are high compared with many other types of investments. For example, Australia’s 10year government bond returns have historically averaged around 7% per year. Private investments in the ASX200 stock index have typically yielded around 10% annually. “We hope our analysis will raise awareness of the value of this kind of spending, and its importance for Australia’s economic recovery and long-term resilience. Investing in innovation now is crucial for the future.”
Perhaps even more significantly, even our conservative estimate of $3.50 return on investment suggests research & development has a cost/benefit ratio well in excess of $1 to $1. This means there is a strong economic case for this kind of spending. But research & development investment is risky, right? This may be much less of a problem at a national level. While cost or time overruns are never favourable for any investment, building this uncertainty into our findings shows that research & development investment remains economically viable even if this happens. Results from sensitivity analysis demonstrate that if the costs of research & development spending or delays of payoffs increase by 20%, the most conservative (combined adjustment) results only fall to $3.30 return on investment, with annual yields of 9.5% (at lowest). These are still strong returns. Our findings imply that so far, Australian innovation investments – whether they be in new products and services or in creating new industries – have been well worthwhile, and that increasing future investment could capture substantial economy-wide returns. As our estimates only capture the economic benefits of innovation, actual returns are likely to be much higher when also considering the broader social and environmental benefits of Australian research & development.
Dr Katherine Wynn is Lead Economist at CSIRO Futures, the strategic advisory arm of Australia's national science agency, CSIRO. Jasmine Cohen is an Economic Consultant at CSIRO Futures. Mingji Liu is a Senior Economic Consultant at CSIRO Futures. This article was originally published by The Conversation. www.theconversation.com www.csiro.au
Jasmine Cohen Mingji Liu
The evolution of manufacturing leadership
Australian manufacturing may be facing a resurgence, but it must learn from the past to face the challenges of the future. In the first of a two-part series, Jack Parr looks at the history and evolution of manufacturing leadership.
In 1990, manufacturing companies drove the world economy, yet in just three decades, service companies have come to dominate – companies with well-defined leadership principles. In this time Australian manufacturing has gone from 14% to 6% of GDP. Technological change, globalisation and political inaction were driving Australian manufacturing to near extinction. The COVID-19 pandemic has created an opportunity for resurgence, but we cannot repeat history. Manufacturing must now be a sector that can manage the economic, environmental and social challenges of the next 30 years. Manufacturing must evolve again through new leadership, new management and new principles. It is said one must learn from the past to prepare for the future. The Industrial Revolution of the 18th century created the mechanised manufacturing company and initiated an economic and technological transformation. It saw the rise of the owner-manager, who exploited workers of all ages in the drive for production and profit. It took over a century for Frederick Winslow Taylor to establish a new relationship between workers and management. His 1911 book ‘The Principles of Scientific Management’ has been declared one of the most influential books of the 20th century, laying out scientific methods to improve the efficiency of labour. Taylor stated: “In future it will be appreciated that our leaders must be trained right as well as born right”. In 1916, a French mine manager, Henri Fayol, complemented Taylor’s work through his concise ‘14 Principles of Management’. The subsequent decades saw the study of worker motivation, the ‘Psychology of Work’, become the focus for productivity improvement. Elton Mayo’s famous ‘Hawthorne Experiments’ of the 1920s, demonstrated how increased attention to the worker and their environment could have a positive effect on productivity. The work of socio-psychologists like Hertzberg, McGregor, and Maslow with his famous Hierarchy of Needs, all contributed to understanding employees’ motivation to improve business performance. The late 1960s and early 1970s saw the rise of computerisation, which increased the efficiencies of both the shop floor and office. A new generation of managers implemented ‘Modern Management’ techniques through the writings of Peter Drucker, lifting management thinking to the strategic level. Regarded as the founder of modern management, Drucker encouraged managers to think about the purpose of an organisation and define it through the Mission Statement. Strategic Management now analysed the business in terms of goals, processes and objectives. George Doran proposed that these objectives needed to be ‘SMART’ – Specific, Measurable, Achievable, Relevant and Timely. Business was competitive and business schools recommended ancient texts like Sun Tzu’s ‘Art of War’ and Machiavelli’s ‘The Prince’ to endorse this competitiveness. In 1976, Hewlett Packard implemented the Japanese strategic tool ‘Hoshin Kanri’, prompting other organisations to implement such tools. Organisations started to focus their goals and objectives into a set of strategic principles – unique propositions covering products, people and customers. In the 1980s, two international organisations – one Japanese, one American – built their enduring success on two unique but different sets of business principles. In Japan, over the course of 20 years, Taiichi Ohno, the pioneer of the Toyota Production System and the inspiration behind Lean Manufacturing, changed the manufacturing process from ‘scientific’ to ‘systematic’ – with standardisation and continuous improvement at its core. While this was Toyota’s specific strategy, they were surprisingly willing to share it with the world. Their reasoning lay in the core principle of continuous improvement: “By the time others get to understand and apply it, we will have moved further forward.” Jack Welch became CEO of General Electric in 1981, having joined the company straight from university in 1960. One of his main principles was “Don’t manage – lead change before you have to!”, demonstrated by the fact that over the next 20 years, he transformed GE from a US$25bn appliance manufacturing company into a US$130bn conglomerate offering products and services. Welch also had strong principles on strategic positioning, with “If you don’t have a competitive advantage – don’t compete”. If GE were not one of the top two companies in a product sector, he pulled out. Welch’s principles on people, however, were controversial. He believed the bottom 10% of employees each year were nonperforming and should be publicly identified and fired. Welch explained that “Public hangings are teaching moments … worth a thousand CEO speeches.” ‘In Search of Excellence’ became the seminal book on leadership in the 1980s. Written by Tom Peters and Robert Waterman, it was based on distilling the performance of 43 successful US companies down to eight high-performance principles. Peters’ message was that leaders should focus on action, customers and people. He said “Management is about arranging and telling – leadership is about nurturing and enhancing”, and “Allow people to make mistakes, learn and grow”. Leadership was also based on communication “The best leaders … almost without exception and at every level are master users of stories and symbols!” In the 1990s Rosabeth Moss Kanter prophetically questioned “Could giants learn to dance?” The answer would certainly appear to be ‘No’ if the previous giants of Australian manufacturing are to be the guide. This is not the article to debate the reasons for the decline of our manufacturing sector, but it is fair to say that a focus on minerals rather than manufacturing, a lack of government foresight, and archaic industrial relations all played a part. The pandemic has created a new opportunity for Australian manufacturing. The industry can build a new citadel, a new light on the economic hill. But it must be founded on a new set of business principles, not repeating the past but now based on innovation, agility and co-operation. The challenge going forward is for all in manufacturing to develop, advocate and implement these principles!
Jack Parr is the Coordinator for the Vernier Foundation, a charity aimed at funding and supporting, STEM education in schools. The Foundation is the charitable arm of the Vernier Society, an organisation that for nearly 80 years has worked to support Victorian Manufacturing. www.vernier.org.au
Saving through smarter energy use
Manufacturers are constantly challenged to do more with less, but one area leaving the handbrake on in terms of progress is the industry’s reliance on fossil fuels. They stand to benefit from smarter energy use. By Jordan Griffiths.
Australia’s manufacturing industry spent $5.3bn on electricity in 2019, more than the combined spend of mining, transport, utilities and construction. Of this consumption, 45% of energy consumed by manufacturing is derived from natural gas and 22% comes from coal, while renewables only account for 28%. The writing’s been on the wall for fossil fuels for a considerable time now. Continuing to rely on natural resources to maintain growth exposes a business to serious risks, not just to its public image, but also exposes its tangible and intangible value. If the environmental arguments alone aren’t rousing enough, the price of renewable energy now rivaling those of fossil fuels means that manufacturers can make huge financial savings by getting a handle on their energy usage. There are two ways manufacturers can go about saving with smarter energy use: they can switch to renewable energy; or they can find ways to cut down on the amount of energy they need to continue operations. These aren’t mutually exclusive strategies, and there are multiple factors to consider when finalising an approach. Electrification is growing in popularity, and as the cost of carbon rises, renewable energy costs drop – driven by the introduction of global emissions reduction targets. It’s not necessarily feasible for every operation to be electrified, but as technology matures, we’ll see more processes adopt that approach, especially those with low CO2 emissions. For example, 28% of steel globally is produced using electric furnaces, which require as little as a fifth of the energy required for a traditional blast furnace. Our north star for sustainability transformation is a ‘Triple Zero’ concept, focusing on zero loss, zero harm and zero waste. In Australia, significant industries are increasingly applying this strategy when it comes to smarter energy use. Australia’s mining sector has long been a vital part of the country’s economy; however, the environmental damage caused by large-scale mining is threatening the sector’s future. The Granny Smith gold mine in Western Australia is a standout example of the industry addressing this issue, by installing one of the world’s largest renewable energy microgrids to support extraction and smelting processes. Powered by more than 20,000 solar panels and supported by a 2 MW/1 MWh battery system, the innovative system reduces the mine’s fuel consumption by 13%. Elsewhere, South Australia is driving green hydrogen innovation, following up its recent Hydrogen Export Prospectus with an announcement from State Premier Steven Marshall, to provide $37m in state funding for upgrades to the $240m Eyre Peninsula Gateway Hydrogen Project, which features a 75 MW electrolysis plant. The project will ultimately increase sovereignty in Australian domestic markets reliant on green hydrogen and ammonia, as well as expanding green export opportunities. Aspiring to adopt green energy is a good starting point; however, most businesses are struggling to get a foothold. In Australia, businesses can buy renewable energy directly from a solar or wind farm using a Power Purchase Agreement (PPA). These agreements allow businesses to buy renewable energy on a long-term contract, often at a cheaper rate. The other strategy, cutting down on existing energy usage, can be trickier to facilitate in an existing business. Energy will always be needed in manufacturing, and the nature of some processes are more energy-intensive than others. It’s up to every industry to encourage more energy efficiency and demand for carbon offsets, which then drives investment into renewables. Manufacturers can aid this cause by re-evaluating the product itself through a triplezero lens, in order to futureproof operations; as well as reviewing the time of day operations can take place, in order to efficiently tap into lower energy market prices. In the long term, manufacturers can look to the Circular Economy mode for guidance, which aims to decouple business growth from the use of scarce resources. The core theme within this model is the concept of resource recovery, or a more succinct way of putting it: recycle and upcycle. Resource recovery sees businesses recover embedded value at the end of the production cycle, in order to become a supplier for another production cycle. To understand and capture the full business opportunity of the Circular Economy, manufacturers need to embed recycling into processes as early as the design stage. In this new environment the unit cost of resources becomes less of a factor because instead of using additional resources to manufacture new goods, companies and customers use what’s already in the market. Focus shifts from producing things from virgin resources to transferring existing products between users and transforming used products into new ones. A perfect example in the Australian manufacturing sector is the partnership between Cleanaway, Pact Group and Asahi Beverages to build a $45m polyethylene terephthalate (PET) plastic bottle manufacturing plant in Albury – the largest in Australia. Once it’s fully operational and online, the plant is slated to process the equivalent of one billion bottles a year, producing recycled PET pellets that will be used to manufacture new recycled packaging material. Not every manufacturer is in a position to invest so significantly in reforming its byproducts, but every business can start adopting green energy in some way or form. It can seem intimidating but once you start thinking about how to separate your business’s growth and goals from reliance on fossil fuels, incorporating sustainability into your business processes will become second nature. Not only will the environment thank you for it, but so will your bottom line.
Jordan Griffiths is Managing Director – Operations at Accenture. www.accenture.com
Why artificial intelligence will be key to unlocking success in 2022
The last two years have inflicted major disruption for Australian manufacturers. Data intelligence will be critical as businesses look to rebuild , and those that don’t put artificial intelligence (AI) at the core of their strategies will fall behind in 2022, writes Haley Glasgow.
The pandemic has upended the manufacturing sector and put the spotlight on Australia’s reliance on global supply chains. Lockdowns made it impossible for many manufacturers to access the staff, sites and equipment necessary for maintaining operations and filling orders, according to the Australian Manufacturing Growth Centre. At the same time, the pandemic highlights the need to build a local manufacturing sector as the nation looks toward COVID-19 recovery. So much so, that one in two manufacturers intend to bring operations back to Australia within the next three years. Following market volatility caused by COVID-19, reshoring is a step in the right direction for Australia’s manufacturing sector. However, four in five (82%) senior employees in the sector are underprepared to compete in a digital economy. Businesses need to fast-track e-commerce channels to overcome competition from imports and online sources. Leveraging technologies like artificial intelligence (AI) and digital selling is one way to achieve exactly that. As companies look to build resilience and effectively reshore operations, here are three reasons why Australia’s manufacturing sector should harness AI in 2022: Reduce customer exposure to market volatility
COVID-19 has resulted in a shortage of goods, and consequently higher prices. In addition, many manufacturing companies experienced logistical challenges as a result of restrictions on the movement of people. With increased supply chain disruption comes increased market volatility, which is set to be a challenge into 2022. But customers don’t want to feel this instability. Understanding how the supply chain will impact both inflation and the end-to-end components of a company will put manufacturers in the position to solve volatility earlier, ultimately reducing customer exposure and providing a more predictable experience. For example, COVID-19 disrupted the oil & gas industry two-fold, first due to failed agreements on production cuts, and second because of slowed demand from travel restrictions. By leveraging dynamic pricing and data-driven insights to predict how the oil & gas market might fluctuate over the course of a year, companies can set their prices accordingly to account for those fluctuations. The same principal applies to manufacturing. By calibrating between peaks and troughs, prices – already set in the middle – will remain stable, while the company remains smart and profitable. This will have a knock-on effect. Having less volatility to worry about means customers will have a better experience. They will feel more engaged with the company. And as a result, customers lean toward repeat engagement with a brand based on that positive experience. Maximising opportunities around reshoring operations
During the pandemic, Australian manufacturers struggled to manage their supply chains, with full lockdowns in many countries from which materials are typically sourced, including China and the UK. This exposed Australia’s dependence on offshore supply chains. But the more positive side of this is that there has been a significant shift in confidence toward onshore capacity in Australia. As a result, we can expect to see more companies reshore operations in the next couple of years, as manufacturers look to gain greater company agility, diversify revenue streams and riskproof their supply chains. One in two Australian manufacturers (55%) have indicated they intend to reshore their operations to Australia by 2023, while almost one-quarter (22%) have already made the move and reshored at least part of their operations. This is according to PROS’ Australian Manufacturing Outlook Survey. Surprisingly the biggest appetite for reshoring has been from Western Australia, the Northern Territory and South Australia, as these regions focus on creating local jobs and growing priority sectors such as downstream lithium processing, defence and space. As Australian manufacturers look to reshore, it’s imperative they lead with a digital strategy. Now is the time to leverage technologies like AI and digital selling to support the local industry boom. This will help overcome one of the primary constraints for Australian business leaders – competition from imports and online sources – to drive company growth. Overcome pressure of pandemic pricing
COVID-19 has driven supply chain and freight disruptions, as well as inflation, resulting in market and pricing volatility across the board. Manufacturers can no longer rely on their typical pricing structures and manual practices, which can lead to lagging, unreliable and error-prone pricing, to maximise revenue. Beyond that, how manufacturers price a product has a knock-on effect on customer experience. While increasing prices by 10% to optimise margins might sound good in theory – especially during COVID-19 recovery – this could lose a potential customer to a competitor offering the same product at a lower price. On the other hand, manufacturers that don’t account for rising costs experience undue margin leakage. Instead, manufacturers must embrace a digital mindset and leverage AI-based price optimisation and management to deliver profitable prices informed by market conditions and co-ordinated across all sales channels. These capabilities will allow manufacturers to deliver tailored, market-relevant prices in real time, ensuring personalised buying experiences and creating a streamlined pricing strategy in 2022 and beyond. Manufacturing always involves an element of risk. This is especially true in the context of the pandemic where we’ve seen supply chain shortages heavily impact pricing and material availability. But with investment in innovative tools like AI, and collaboration with the government and industry, manufacturers will be one step closer to recovering operations and improving the buying experience for customers.
Haley Glasgowis Head of Strategic Consulting & Alliances, APAC at PROS. www.pros.com
Canada: Unbreakable glass inspired by seashells
Scientists have developed stronger and tougher glass (a glass and acrylic composite material that mimics nacre/mother of pearl). Instead of shattering upon impact, the new material has the resiliency of plastic and could be used to improve cell phone screens, among other applications. The new material is three times stronger than normal glass, and more than five times more fracture-resistant. The scientists took the architecture of nacre and replicated it with layers of glass flakes and acrylic, yielding an exceptionally strong yet opaque material that can be produced easily and inexpensively. They then made the composite optically transparent. By tuning the refractive index of the acrylic, it seamlessly blended with the glass to make a truly transparent composite. It is planned to improve it by incorporating smart technology, allowing the glass to change its properties, such as colour, mechanics, and conductivity.
McGill University
Engineers have demonstrated a way to help 3D printed plastic heal itself at room temperature using only standard LED lights via the addition of special powder to the liquid resin. Full healing takes approx. one hour and the process actually makes the repaired plastic even stronger than it was before it was damaged. The powdered additive is a trithiocarbonate, known as a reversible addition fragmentation chain transfer (RAFT) agent which was originally developed by CSIRO. There are other processes like this, but they rely on thermal chemistry and typically it takes around 24 hours and multiple heating cycles. And an oven is required which is heated to high temperature – preventing the repair of the plastic material in situ (it would need to be disassembled). With this system, the broken plastic can be left in place and the light shone on the entire component. Only the additives at the surface of the material are affected.
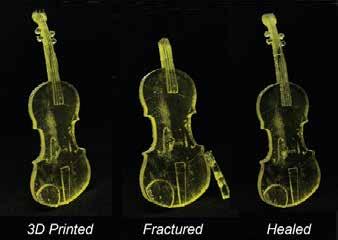
3D printed items treated with a trithiocarbonate, such as this violin, can self-heal when placed under UV light.
UNSW School of Chemical Engineering
UK: World record flight powered by synthetic fuel
The RAF and Zero Petroleum have won a Guinness World Record for the world’s first successful flight using only synthetic fuel. In a world-first, an Ikarus C42 microlight aircraft completed a short flight powered by synthetic gasoline at Cotswold Airport late last year. Zero Petroleum’s synthetic UL91 fuel is manufactured by extracting hydrogen from water and carbon from atmospheric carbon dioxide using energy generated from renewable sources. This innovation is part of the RAF’s Project MARTIN and has the potential to save 8090% of carbon per flight, supporting the RAF’s vision that synthetic fuels will have a major role in powering the fast jets of the future. The high-grade aviation gasoline ZERO® SynAvGas was developed in just five months and ran successfully in the aircraft without any modification to the aircraft or the engine. The engine manufacturer Rotax’s measurements and the test pilot’s observations showed no difference in power or general performance compared to standard fossil fuel.
UK Govt
Australia: Australia's largest rocket engine test
Rocket engineers at Gilmour Space Technologies have greeted the new year with a successful 110-kilonewton test fire of the most powerful rocket engine ever developed in Australia. The 75-second test was a major milestone for Gilmour Space, which is developing Australian Made rockets that will, over the next five years, be capable of launching 300 to 4,000kg satellites and payloads into low earth and other orbits. Such satellites could be used to detect bushfires, help fertilise crops, and improve phone or internet coverage. The company is in talks with the Canadian government and the Australian Space Agency about bushfire-detection satellites.

Gilmour Space/ABC
Japan: New tool detects precursor combustion instability
Combustion engines remain at risk of fatal damage by a phenomenon called "combustion oscillations," where pressure fluctuations inside the engine become large. Now, researchers have developed a novel tool to detect a precursor to combustion oscillations using machine learning and a dynamical systemsbased approach, opening doors to the prediction and prevention of related fatal engine damage. The team conducted combustion experiments with varying fuel flow rates in a staged multisector combustor and used the data from these experiments to train a machine learning algorithm called 'support vector machine’. This allowed them to classify the combustion into three states-stable, transitional, and combustion oscillations.
Tokyo University of Science
USA: A robotic hand with a gecko-inspired grip
A robotic gripper - “farmHand” – has been created that can grasp with delicate strength. Combining adhesives based on gecko toes with a customised robotic hand, the manipulators are both dexterous and strong and capable of handling a wide variety of items, from raw eggs to an angle grinder. The adhesive creates a strong hold via microscopic flaps. These flaps create a Van der Waals force, so the adhesives can grip strongly but require little actual force. It is not sticky nor leave a residue. The finger pads are made of a collapsible rib structure that buckles with little force,
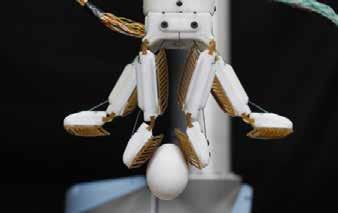
A close-up of the hand performing a highly hyperextended pinch on only the top of an egg.
no matter the location or angle of contact. The hand’s tendons are crucial as well because they enable a hyperextended pinch. While many robotic hands and clamps will pinch objects in a “C” shape, farmHand pinches with the end of its fingers pressed pad to pad. This gives the adhesives more surface area to work with.
Stanford
USA: Drilling through undrillable rock
A semi-autonomous tunnelling robot called Swifty, created by a San Francisco start-up Petra, has demonstrated through a test that it can drill through the hardest rocks on Earth by boring a 61cm tunnel through 6.1m of Sioux Quartzite using super-heated gas. This attempt would normally destroy drilling equipment. The company previously used plasma to melt the rocks but the extreme heat turned the rocks into lava. This made Petra turn to colder options. Its robot has sensors attached to small rods which touch the rock, but the excavation is carried out by applying heat and gas. It can create 46-152 cm diameter tunnels through the hardest geologies with a non-contact thermal drill that melts any type of rock by heating a mixture of gas to apply heat above 982° C. The company claims that no method has been able to tunnel through this kind of hard rock until now and that the cost of tunneling through bedrock to bury underground lines is reduced by 50-80%.
Interesting Engineering
The robot’s progress through Sioux Quartzite at a rate of 2.5cm per minute, uses machine vision and can reverse out of the tunnel it drilled.
USA: Polymer discovery gives 3D-printed sand super strength
Researchers have designed a novel polymer to bind and strengthen silica sand for binder jet additive manufacturing. The printable polymer enables sand structures with intricate geometries and exceptional strength – and is also water soluble. It is cheaper and faster than other 3D-printing methods and enables the creation of 3D structures from a variety of powdered materials. Instead of ink, the printer head uses a liquid polymer to bind a powdered material, such as sand. The binding polymer is what gives the printed sand its strength. The team tailored a PEI binder that doubled the strength of sand parts compared with conventional binders. Parts printed via binder jetting are initially porous when removed from the print bed. They can be strengthened by infiltrating the design with an additional material. This second step provided an eight-fold strength increase, making a polymer sand composite stronger than any known building materials, including masonry. Few polymers are suited to serve as a binder. The key finding was the unique molecular structure of this PEI binder.
DOE/Oak Ridge National Laboratory
Australia: Vaccine needle-free
Vaxxas, a Queensland biotechnology company is using its HDMAP High Density Microarray Patch technology - a patch with thousands of vaccine-coated microprojections that is applied to the skin for a few seconds - to efficiently deliver vaccine to the abundant immune cells immediately below the skin surface. The microprojections also trigger natural immuno-cellular alarms that cause vaccine components to be rapidly trafficked to lymph nodes eliciting a robust immune response. The company uses proprietary dry-coating technology that can eliminate or significantly reduce the need for vaccine refrigeration during storage and transportation - easing the resource and logistics burden of maintaining the vaccine "cold chain".
Vaxxas
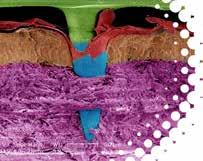
axxas' HD-MAP is readily fabricated by injection moulding to produce small patches each with thousands of very short (~0.25mm) microprojections.
USA/International: New ultrahard diamond glass synthesised
An international research team has synthesised a new ultrahard form of carbon glass with a wealth of potential practical applications for devices and electronics. The type of bond holding a carbonbased material together determines its hardness. For example, soft graphite has two-dimensional bonds and hard diamond has three-dimensional bonds. The synthesis of an amorphous carbon material with three-dimensional bonds has been a long-standing goal. Because of its extremely high melting point, it’s impossible to use diamond as the starting point to synthesise diamond-like glass. However, the research team made their breakthrough by using a form of carbon composed of 60 molecules arranged to form a hollow ball (buckyball) which was heated just enough to collapse its soccer-ball-like structure to induce disorder before turning the carbon to crystalline diamond under pressure. The team used a large-volume multi-anvil press to synthesise the diamond-like glass.
Carnegie Institution for Science
“We averaged an astounding one inch per minute in a geology usually excavated by dynamite … no tunneling method has been able to tunnel through this kind of hard rock until now.” Silicon Valley startup Petra’s CTO and Tesla co-founder Ian Wright. “Our non-contact method is the next evolution of tunneling and will usher in a new age of undergrounding utilities.” Petra CEO and co-founder Kim Abrams. Petra recruited Wright to help improve the thermal spallation drilling technology it was working on. The result is “Swifty,” a semiautonomous boring robot.