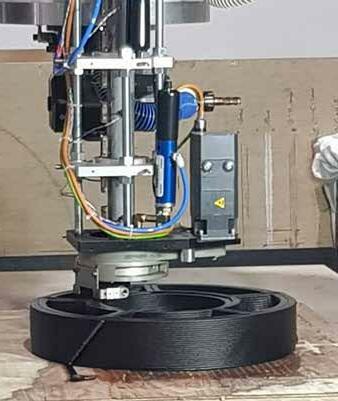
7 minute read
CNC Design – Inside the Virtual Smart Factory
from AMT FEB/MAR 2022
by AMTIL
Designing and building some of the biggest 3D printing machines in the Southern Hemisphere, CNC Design has now established its Virtual Smart Factory (VSF): a versatile gantry-based additive manufacturing system to produce large parts for industries such as construction, mining, entertainment, aerospace and defence.
Founded in 1984, CNC Design is a leader in motion control and drive-based solutions throughout Australia, New Zealand and South-East Asia, and has established itself as one of the world’s foremost specialists in developing and retrofitting CNC machinery. CNC Design is based in Nunawading, Victoria, and in the last few years the company has been building and supplying very large volume 3D printing and machining systems for thermoplastics, concrete, and wax. In addition, CNC Design is the exclusive representative for Siemens machine tool products in Australia and South-East Asia, and has partnerships with Güdel and Comau. The company has an extensive service, sales and engineering network in the Asia-Pacific region, with more than 175 people located in its offices in Australia, New Zealand, Indonesia, Thailand, Malaysia and Singapore. The team at CNC Design has completed more 2,500 projects in 30 countries. Big area additive manufacturing
Drawing on its extensive experience in CNC systems and gantryrobot technologies, CNC Design developed its Virtual Smart Factory (VSF) range of big area additive manufacturing (BAAM) machines at its R&D centre for additive and machining technologies in Melbourne, with the machines assembled in its Thailand facility. CNC Design has already supplied some of the largest additive manufacturing machines in the world, making parts up to 30m in length. The VSF is a flexible solution for the additive manufacturing of large parts that are commonly used in construction, aerospace, mining, defence, and other industries. Applications that CNC Design’s technology has been involved with to date have included: • Printing of moulds for thermoforming. • Printing and machining of moulds for the leisure sector, including for recreational vehicles (RVs), sculptures and art pieces for theme parks. • Moulds for pre-casting concrete and glass-reinforced concrete (GRC) parts for the architectural and construction industry. • Making tools for composite and fibreglass industries, covering different types of resin transfer moulding (RTM) and infusion moulding, with the potential to be used in several other industries. Process and materials
CNC Design’s giant VSF Composite printer boasts a number of advanced features, including: • Multi-temperature zone extruder (patented) for melting and extrusion with servo motor control for high dynamic performance and throughputs up to 220kg/hr • Nozzle rotation unit with temperature-controlled roller to flatten and compress print bead for maximum bonding strength. • Vacuum pellet drying and conveying system with high performance and energy efficiency for continuous printing. • Axis print speeds up to 20m/min with rapid axis speeds of up to 60m/min. • Changeable nozzles from 3mm to 30mm in diameter. • Thermal control of the print process for optimum print speed and quality The VSF pellet-based 3D printer is currently available in three sizes: the smallest model comes with a 19mm screw diameter print head, which deposits up to 12kg per hour (based on reinforced
CNC Design’s Virtual Smart Factory (VSF) can print in a wide range of thermoplastic fibre reinforced materials.
ABS material). The next level up is the 30mm screw diameter print head which puts out up to 70kg per hour of material with a typical bead that is 16mm by 4.5mm. The biggest print head comes with a 60mm screw diameter, which gives it an output capacity of 220kg per hour with the bead width of 50mm and height of 15mm. In between sizes can be manufactured depending on the customer application requirement. CNC Design’s VSF system is compatible with a wide range of printing materials, covering amorphous and semi crystalline polymers, with melting temperatures up to 400 degrees Celsius. Depending on the application, there are a wide range of reinforcement fibres available including glass, carbon, Kevlar and basalt fibre, plus hemp and other bio-based fibres. Printing nano composites will be the next area that the R&D team at CNC design are focusing on, which will be thermoplastic composites with additives/fillers like graphene, clay, carbon nanotubes and other nano materials with interesting and unique properties. Some of the materials that have been used by customers to date include: • ABS reinforced with 30% glass fibre. This material offers light weight coupled with various useful mechanical properties such as impact resistance, toughness, rigidity when compared with other common polymers, and high dimensional stability. • ABS reinforced with 20% carbon fibre. This material is lightweight and has good mechanical properties including impact resistance, toughness, rigidity compared with other common polymers, and high dimensional stability. • Polycarbonate reinforced with glass or carbon fibre at 20%.
This offers temperature resistance and is intrinsically flame retardant, with high impact resistance, dimensional stability, and abrasion resistance.
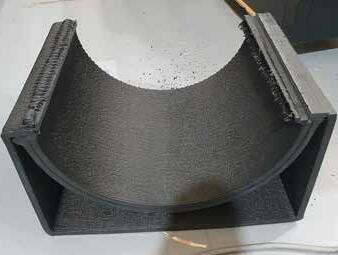
Composite moulds made with 3D printing and five-axis high-speed milling in the VSF Composite cell.
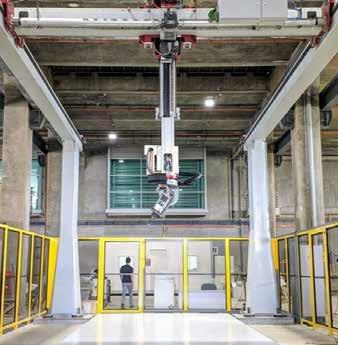
In 2019, Witteveen+Bos used CNC Design’s VSF Prefab Concrete Printer to set up an apartment module printing station at the Singapore Housing & Development Board (HDB)’s Centre of Building Research.
• Thermoplastic vulcanisate (TPV). Combining the characteristics of vulcanised rubber with the processing properties of thermoplastics, this also offers good sealing and resistance to heat and fluids. • Ethylene vinyl acetate (EVA). This features good lowtemperature properties, good clarity and gloss, lowtemperature toughness, stress-crack resistance, and resistance to UV radiation. CNC Design continues to undertake research into a range of other materials for future applications. Projects
Siam Cement Group (SCG) is one of the largest cement and building materials companies in South-East Asia. In late 2020, SCG 3D printed a 102sqm building in Thailand using CNC Design’s VSF Onsite Concrete printer. The VSF Onsite Concrete printer is designed to be easily relocatable while retaining high speed and precision for printing. This allowed SCG to print intricate textured surfaces on the walls of structures it was constructing. Using conventional methods, this would have required complex moulds and formwork to achieve a similar design. Additionally, the construction of the wall took around five days and required five operators, which amounted to a significant saving in time and labour. Another unique feature of this building was that a tenth of the printed material consists of recycled materials. Another client of CNC Design is Witteveen+Bos, which is a frontrunner in the implementation of concrete 3D printing in the architecture, engineering and construction (AEC) industry and a pioneer in the development, design and engineering of 3D printed concrete structures. Singapore Housing & Development Board (HDB) is a public housing authority and is responsible for the development of 81% of the housing in Singapore. In 2019, Witteveen+Bos used CNC Design’s VSF Prefab Concrete Printer to set up an apartment module printing station at the HDB Centre of Building Research in Singapore. For Witteveen+Bos, this milestone proved the viability of its efforts in the field of 3D printing for construction. The VSF Concrete Printing System enables printing of unique concrete elements up to 9m long, 3.5m wide and 3.8m tall. Globally, there is a great demand for housing, and concrete 3D printing could help to meet these demands. Currently, the design and fabrication of concrete building elements using the conventional method of precast production is timeconsuming and requires high labour content. Besides, the moulds used in the construction will be discarded, resulting in material wastage. Construction using 3D printing, on the other hand, combines digital building information modelling (BIM) technology with additive manufacturing techniques to allow free-form construction without the need for moulds or forms, thereby reducing the environmental burden of material waste. The method also opens new opportunities for creating geometric forms that would be near impossible to create with traditional methods. The VSF concept has been applied to machining, handling and additive manufacturing not only for concrete, but also for wax, foam, high-temperature plastics and composites. The VSF system uses the Sinumerik One CNC controller, which is the flagship control system from Siemens, with its ability to handle multiple technologies and multiple operations from a single system. Coupling the Sinumerik One with Güdel three-axis cartesian gantry modules as the mechanical platform allows CNC Design to make VSF machines that can be scaled up to 70m in the X axis, 6m in the Y axis, and up to 3.2m in the Z axis. The VSF system is also available in the form of 6-axis industrial robots combined with linear track motion for smaller print volumes.
www.cncdesign.com.au www.virtualsmartfactory.com
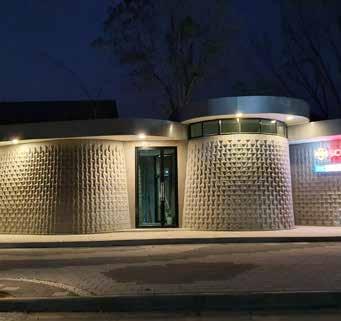
Construction using 3D printing combines digital building information modelling (BIM) technology with additive manufacturing techniques to allow free-form construction.