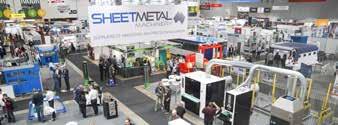
30 minute read
INDUSTRY NEWS Current news from the Industry
from AMT APR/MAY 2022
by AMTIL
Visitor registrations open for AMW 2022
Online registrations are open now for visitors to the inaugural Australian Manufacturing Week exhibition, taking place in Sydney in June 2022.
Owned and operated by AMTIL, AMW is Australia’s premier manufacturing solutions event. Under the theme ‘Where technology meets innovation’, AMW 2022 will take place at the International Convention Centre Sydney (ICC Sydney) in Darling Harbour from 7-10 June 2022. The opening of registrations marks a major milestone in the build-up to the exhibition. Preparations for AMW 2022 have been marked by high levels of early interest, with the floor space almost entirely booked out well before the end of last year. “It’s great to finally have opened up registrations for visitors to AMW,” says Kim Banks, Head of Events at AMTIL. “We’ve had an incredible response from exhibitors, with stands getting booked faster than any of us had anticipated. There’s clearly a really strong appetite across the industry for an exhibition like AMW. Now we’re just concentrating on welcoming as many visitors to the show as we can.” AMW will occupy more than 9,000 sqm of floor space at the ICC Sydney, with more than 155 organisations taking stands to exhibit some of the very latest manufacturing technologies, processes and support services. AMTIL will be making regular announcements between now and the start of the event about its plans for the show, so it’s worth keeping an eye on the AMW website as well as its social media channels for the latest updates. The AMW exhibition will consist of six dedicated zones offering a comprehensive view of the modern manufacturing landscape. The Austech Machine Tools & Ancillary Equipment Zone will host an extensive range of metalworking and machine tool technology, including the latest state-of-the-art cutting tools from Iscar Australia. Exhibitors such as Automated Solutions Australia and Epicor Software will be displaying their products in the Robotics & Automation Zone, while the Weld Solutions Zone will feature the latest cutting-edge welding technology. The Additive Manufacturing Zone will feature the latest innovations from the fast-evolving world of 3D printing, from companies such as RAM3D, while the Australian Manufacturers Pavillion will showcase some of the most innovative manufacturing businesses operating today, including Marand Precision Engineering and Marsh Alliance. Finally, the Manufacturing Solutions Zone will offer optimised solutions to the most common challenges experienced by manufacturers. “We’re thrilled to be open for online registrations for AMW 2022,” said Shane Infanti, CEO of AMTIL. “AMW is a brand new exhibion from AMTIL and it’s been a long road getting to this point. Now we’re really into the final stages of making sure we put on the best show possible for the Australian manufacturing industry.” Australian Manufacturing Week 2022 will take place at the International Convention Centre Sydney (ICC Sydney) in Darling Harbour from 7-10 June 2022. For more information and to register your intention to attend, visit the AMW website at:
www.australianmanufacturingweek.com.au
Australia to become EV-manufacturing powerhouse
A unique combination of advantages has handed Australia an historic chance to become a sustainable global manufacturer of electric vehicles (EVs) – provided the Federal Government acts swiftly and decisively, according to new research by the Australia Institute’s Carmichael Centre.
The new report, Rebuilding Vehicle Manufacturing in Australia: Industrial Opportunities in an Electrified Future, has found Australia is uniquely blessed with advantages to attract and retain EV manufacturing and rebuild the nation’s car-making capacity. This potential, however, will not be met without major government action. “When it comes to creating an EV manufacturing sector, Australia enjoys advantages other nations would die for: rich reserves of lithium and rare earths, strong industrial infrastructure, a highly skilled workforce, powerful training capacity, abundant renewable energy options, and untapped consumer potential,” said Dr Mark Dean, the report’s lead author. “And contrary to popular belief, we wouldn’t be starting from scratch. Thanks to the resilience of our remaining automotive manufacturing supply chain, a surprising amount of auto manufacturing work – including components, specialty vehicles, and engineering – still exists here.” However, Dr Dean said his research found Australia’s advantages would count for little without significant government support. The report makes a range of recommendations including: • Using tax incentives to encourage firms involved in the extraction of key minerals – primarily lithium and rare earths – with local manufacturing capabilities, especially emerging
Australian EV battery industries. • Introducing a long-term strategy for vocational training, ensuring the establishment of skills to service major EV manufacturers looking to set up operations Australia. • Offering major global manufacturers incentives (tax incentives, access to infrastructure, potential public capital participation, etc) to global manufacturers to set up – especially in Australian regions undergoing transition from carbon-intensive industries. • Introducing local procurement laws for the rapid electrification of government vehicle fleets. “No nation builds a major industry without its government taking a proactive role. Our new research shows there’s no excuse for inaction, because there are a huge range of powerful levers our government could be pulling,” Dr Dean said. “If we capture the moment we’ll capture abundant benefits: creating tens of thousands of regional manufacturing jobs, reducing our dependence on raw resource extraction, reinforcing our accelerating transition toward non-polluting energy sources, and spurring innovation, research, and engineering activity in Australia. We just need our government to act.”
www.carmichaelcentre.org.au/rebuilding_vehicle_ manufacture_in_australia
New defence centre brings manufacturing jobs to Geelong
Avalon will soon be home to a major defence manufacturing facility, bringing more than 300 new jobs to the Geelong region, with support from the Victorian State Government.
Minister for Industry Support and Recovery Martin Pakula on 22 February welcomed Hanwha Defense Australia’s announcement that its $170m Armoured Vehicle Centre of Excellence will be established at the Avalon Airport Industrial Precinct. “We’re backing Hanwha to make the Geelong region its home because we know it will grow the economy for years to come,” said Pakula. “Victoria continues to lead the way in advanced manufacturing and this state-of-the-art facility in Avalon will create hundreds of jobs and deliver major benefits for local businesses in the supply chain.” Hanwha will use the new Avalon facility to build self-propelled howitzers to deliver the Commonwealth’s approximately $1bn LAND 8116 program. The investment will strengthen the state’s defence capabilities and create hundreds of highly skilled local jobs in design, engineering and advanced manufacturing. Construction of the 32,000sqm state-of-the-art facility is expected to start later this year and take two years to complete – creating more than 100 jobs during construction. Richard Cho, Managing Director of Hanwha Defense Australia, commented: “The Hanwha Armoured Vehicle Centre of Excellence will become the home of Hanwha tracked vehicle operations in Australia and, if successful under the Land 400 phase 3 program, the home of our Redback family of vehicles for both the Australian Defence Force and global markets.” Victoria’s supply chain will directly benefit from Hanwha setting up in the Geelong region with businesses expected to generate $200m in flow-on investment, more local jobs and export opportunities. Hanwha Corporation is South Korea’s largest defence company and also operates in other sectors including aerospace, fintech, mining and clean energy. Hanwha Defense Australia was established in 2019 and is headquartered in Melbourne. In January 2021, the Victorian Government signed a Memorandum of Understanding with Hanwha to formalise a long-term partnership to support the establishment of Hanwha’s defence manufacturing operations in the state. Hanwha is also one of the final two bidders to deliver the Federal Government’s multibillion LAND 400 Phase 3 Infantry Fighting Vehicle program. If successful, Hanwha will create more than 1,000 jobs in the Geelong region over the next 12 years and an estimated $5.7bn for Victoria’s economy. www.hanwhadefense-intl.com
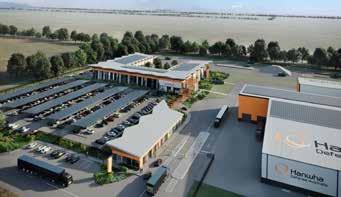
Camfil Kaire Unit named AIRAH Product of the Year
Camfil’s Kaire Unit has been named AIRAH 2021 Product of the Year
Camfil’s Kaire Unit has been named AIRAH (Australian Institute of Refrigeration, Air Conditioning and Heating) 2021 Product of the Year - a prestigious, peer reviewed award recognising excellence in product manufacture within the Australian HVAC&R (Heating, Ventilation, Air Conditioning, and Refrigeration) industry. This Australian designed and manufactured multi-staged, combination filtration system was designed to control light to heavy kitchen exhaust emissions (smoke, grease and cooking odours) for all types of commercial cooking applications. Kaire Unit incorporates three stages of particulate filtration using custom designed mechanical filters to deliver effective filtration of kitchen exhaust emissions with increasing efficiency through each stage at a minimal cost. A final gaseous filtration stage uses activated carbon media to remove odours. With restricted space in buildings, it is preferred to horizontally discharge kitchen exhaust instead of vertically above the roof line. Horizontally discharged kitchen effluent requires an engineered solution to remove particulates and odour, as per Australian Standards (NCC, AS 1668.1:2012 and AS 1668.2:2012). The Kaire unit achieves this with staged particulate filters and activated carbon media. Designed to operate at 1.85m/s, the Kaire Unit delivers a minimum 0.3 micron particulate removal efficiency of 95%+ (EN 1822- 5:2009) and an initial contact efficiency of 98%+ with odours. The Kaire Unit stands out from alternative HVAC industry offerings such as filter frames mounted in ductwork due to its build quality, customisability, range of sizes and purpose-built filters for kitchen effluent - grease, smoke and odour. This system is a relatively low CAPEX expense and reduces OPEX. Maintenance costs and time is reduced as the filters can be quickly changed rather than spending a significant amount on labour and time cleaning ESP cells. An optional range of integrated inline fan systems that match perfectly with the Kaire Unit also reduce installation time and eliminates the need for separate fan selections by clients. Since its product launch in 2016, the Kaire Unit has gone through several revisions and improvements to become the go-to, deemed as a solution for the economical filtration of commercial kitchen exhaust to Australian standards. www.camfil.com
ICS vulnerability disclosures grows 110%
A biannual Industrial Control System Risk & Vulnerability Report from Claroty finds that Industrial Control System vulnerabilities are expanding beyond Operational Technology to the Extended Internet of Things.
Industrial control system (ICS) vulnerability disclosures grew a staggering 110% over the last four years, with a 25% increase in the second half of 2021 compared to the previous six months, according to new research released by Claroty, the security company for cyber-physical systems across industrial, healthcare, and enterprise environments. The fourth Biannual ICS Risk & Vulnerability Report also found that ICS vulnerabilities are expanding beyond operational technology (OT) to the Extended Internet of Things (XIoT), with 34% affecting IoT, medical devices and IT assets in the second half of 2021. “As more cyber-physical systems become connected, accessibility to these networks from the internet and the cloud requires defenders to have timely, useful vulnerability information to inform risk decisions,” said Amir Preminger, Vice President of research at Claroty. “The increase in digital transformation, combined with converged ICS and IT infrastructure, enables researchers to expand their work beyond operational technology (OT), to the Extended IoT (XIoT). Highprofile cyber incidents in the second half of 2021 such as the Tardigrade malware, the Log4j vulnerability and the ransomware attack on NEW Cooperative show the fragility of these networks, stressing the need for security research community collaboration to discover and disclose new vulnerabilities.” Key Findings
• ICS vulnerability disclosures grew 110% over the last four years, demonstrating heightened awareness of this issue and the growing involvement of security researchers shifting toward OT environments. 797 vulnerabilities were published in the second half of 2021, representing a 25% increase from 637 in the first half of 2021. • 34% of vulnerabilities disclosed affect IoT, medical devices and IT assets, showing that organisations will merge
OT, IT, and IoT under converged security management.
Therefore, asset owners and operators must have a
thorough snapshot of their environments in order to manage vulnerabilities and reduce their exposure. • 50% of the vulnerabilities were disclosed by third-party companies and a majority of these were discovered by researchers at cybersecurity companies, shifting their focus to include ICS alongside IT and IoT security research.
In addition, 55 new researchers reported vulnerabilities during the second half of 2021. • Vulnerabilities disclosed by internal vendor research grew 76% over the last four years. This demonstrates a maturing industry and discipline around vulnerability research, as vendors are allocating more resources to the security of their products. • 87% of vulnerabilities are low complexity, meaning they don’t require special conditions and an attacker can expect repeatable success every time. 70% don’t require special privileges before successfully exploiting a vulnerability, and 64% of vulnerabilities require no user interaction. • 63% of the vulnerabilities disclosed may be exploited remotely through a network attack vector, indicating that the need for secure remote access solutions, which accelerated due to the COVID-19 pandemic, is here to stay. • Claroty’s Team82 continues to lead the way in ICS vulnerability research, having disclosed 110 vulnerabilities in the second half of 2021 and more than 260 vulnerabilities to date. • The leading potential impact is remote code execution (prevalent in 53% of vulnerabilities), followed by denial-of-service conditions (42%), bypassing protection mechanisms (37%), and allowing the adversary to read application data (33%). • The top mitigation step is network segmentation (recommended in 21% of vulnerability disclosures), followed by ransomware, phishing and spam protection (15%) and traffic restriction (13%). www.claroty.com
Charging into the US market
An Australian electric battery manufacturer has charged into the US market.
US President Joe Biden announced in February that Brisbanebased EV charging company Tritium will build a manufacturing facility in Tennessee, while reiterating his commitment to electrify the US government's car fleet. The new plant will produce up to 30,000 EV chargers per year and create 500 local US jobs over the next five years. The facility is expected to house up to six production lines for Tritium’s DC fast chargers, including its award-winning RTM and PKM150 models. Production is scheduled to start in the third quarter of 2022. Tritium CEO Jane Hunter appeared alongside Mr Biden at the White House and said Pres. Biden's policies "have contributed to enormous demand" for Tritium products in the US. "This directly led us to pivot and change our global manufacturing strategy. Tritium’s investment in a US-based, cutting-edge facility for manufacturing is part of our strong push toward global growth in support of the e-mobility industry. We are thrilled to work with the US Federal government and the State of Tennessee on this initiative. With the help of the hard-working residents of Tennessee, we expect to double or even triple our charger production capacity to further our product distribution throughout the US” added Hunter. “I welcome Tritium to Tennessee and thank the company for its commitment to create more than 500 new jobs in Wilson County,” said Tennessee Governor Bill Lee. The news was also welcomed in Australia by Dr Jake Whitehead, Head of Policy at the Electric Vehicle Council in Australia. "It's such exciting news for Tritium, which is a Brisbane-based company, founded out of a backyard shed 20 years ago. I've known this team for a long time, they've been working super hard and now,
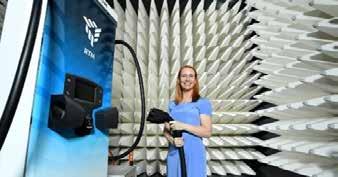
Jane Hunter, CEO of Tritium, inside the Tritium Electric Vehicle Charging Test Facility in Brisbane.
“Tritium could be the most important Australian company most Australians have never heard of — an example of a successful homegrown business that's exporting a high-tech clean-energy product, rather than shiploads of ore,
sheep or gas” (ABC Science News).
they've gone from strength to strength, recently being listed on the NASDAQ and today taking the stage with the President of the United States."
Planet Innovation and Lumos Diagnostics establish local RAT manufacturing facility
A Victorian Rapid Diagnostics Manufacturing Facility and Innovation Hub to manufacture RATs and other diagnostic tests is set to be established.
Planet Innovation - Australia’s leading healthtech innovation and commercialisation company - and Lumos Diagnostics, a rapid point-of-care diagnostics company, with support from the Victorian State Government, will establish a $17.2m Rapid Diagnostics Manufacturing Facility and Innovation Hub in Victoria to locally manufacture RATs. Subject to necessary approvals, including those from the Therapeutic Goods Administration (TGA), the facility will produce one million tests in April 2022 and scale up to three million per month by July 2022. At full capacity, the facility will be able to make 50 million RATs each year. Beyond COVID, the facility will be able to produce a variety of diagnostic tests including those for tropical diseases, flu/ influenza, reproductive health, and chronic disease management, ensuring its long-term viability. Planet Innovation Co-CEO Stuart Elliott says the business is delighted to collaborate with Lumos Diagnostics in support of the Victorian Government’s initiative to establish a strong, sovereign capability for the manufacture of rapid diagnostics. “PIanet Innovation will bring its breadth of medtech expertise to create a world-class operation that will support Victoria through the current COVID pandemic and into the future, with the capabilities to produce a range of diagnostic tests,” he said. “In conjunction with Lumos and the Victorian Government, Planet Innovation will also initiate steps for building a powerful innovation ecosystem in rapid diagnostics that will engage a range of local organisations in the advancement of Victoria’s medtech manufacturing sector.” In addition, the project will create approximately 70 ongoing jobs, adding to Victoria’s thriving medical technology manufacturing sector that already employs thousands of Victorians across the state. Premier Daniel Andrews said of the agreement: “Manufacturing rapid antigen tests in Victoria will protect and secure the state’s supply chain and create local jobs. “Being able to scale up production so quickly shows the strength of Victoria’s advanced manufacturing capabilities.” Lumos’ COVID-19 RAT test CoviDx™ will be manufactured at an existing space provided to Lumos via Planet Innovation, its founding shareholder. Lumos Diagnostics Executive Chair Sam Lanyon said of the deal: “As a global leader in rapid point-of-care (POC) diagnostic technologies, we’re proud to work with Planet Innovation and support the Victorian Government, to manufacture and deliver critical, rapid diagnostic tests. “Lumos will leverage its global experience, that has seen it create critical infrastructure and world-class technology in North America, to support the establishment of a Victorian manufacturing hub for rapid diagnostics.
www.planetinnovation.com
SPEE3D named inaugural winner of US Military Expeditionary Manufacturing Award
AMTIL member SPEE3D has won the inaugural Expeditionary & Tactical 3D Printing Excellence Award from the US Defense Strategies Institute for deployable additive manufacturing.
The outstanding contribution SPEE3D’s technology has made to furthering the manufacturing capability of Defense was recognised by the US Defense Strategies Institute (DSI) at their 6th Military Additive Manufacturing Summit, which took place in Tampa, Florida. At the summit, SPEE3D was announced as the inaugural winner of the Defense Strategies Institute’s Award for Expeditionary & Tactical 3D Printing Excellence. The Defense Strategies Institute (DSI) is a non-partisan Institute designed to assist in advancing the mission critical goals of the United States' Military and Government. They are also the organisers of the Annual Military Additive Manufacturing Summit event which enables thought leaders and key policymakers across military services, Defense agencies, and civilian organisations to come together for actionable discussions and debate. The 2022 Military Additive Manufacturing Summit focused on advancements made in the 3D printing space, as well as how the DoD is working to quickly integrate AM technologies in order to supply durable, affordable equipment and parts to the Warfighter in the battlespace. “We had an incredible number of entries this year from various esteemed government, Defense industry and Defense prime organisations based in the US, and internationally,” states Richard Giordano, Director of Programs at the Defense Strategies Institute. “The 3D Printing Awards is dedicated to recognising individuals, or groups, that have exemplified an outstanding achievement in 3D printing in support of DoD mission priorities. We would like to congratulate all of the recipients making waves in the Advanced Manufacturing space to improve Defense sovereign capability.” Since 2020, SPEE3D, and the Australian Army, have conducted several field trials, taking their WarpSPEE3D tactical printer far out into the rugged bushland of Mount Bundey, and Bradshaw Training Areas. At these locations, the Australian Army’s Additive Manufacturing Cell (AMC) technicians manufactured dozens of case studies, proving that it is possible to 3D print, replace, validate, certify, and put to use metal applications in the field. Steven Camilleri, CEO of SPEE3D, remarked: “SPEE3D is very proud and humbled to be recognized in the US for our work with Defense. We must acknowledge that the Australian Army’s dedication to pursuing new innovation with us has been the backbone of our success. Their commitment to this project helped develop the groundwork for a better sovereign manufacturing future for Defense forces worldwide”. Developed in Australia, SPEE3D’s metal 3D printing technology offers the world’s fastest and most economical additive manufacturing capability. It is also the world’s only proven capability that is able to be successfully deployed, and instantaneously 3D manufacture and supply metal parts on demand in remote, harsh environments. www.spee3d.com
Clearly the best Clearly the best
Industrial Door Solutions
NEW 36pp brochure now available. Contact us to get your FREE copy.
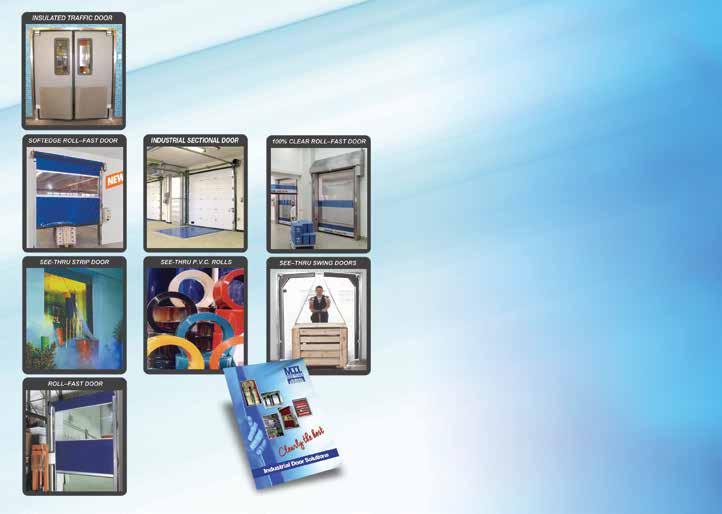
M.T.I. Qualos Pty. Ltd. are leaders in the manufacturing and service of Industrial Transparent Flexible Doors, Insulated Traffic Doors, and Roll-Fast Doors. We produce to the highest quality standard within a full range of industrial doors to suit any door application.
Contact our team today to find a solution for you.
M.T.I. Qualos Pty. Ltd. 55 Northern Road, West Heidelberg, Vic. 3081 Tel: 1300 135 539 E: sales@mtiqualos.com.au W: www.mtiqualos.com.au
Lithgow marks a new era of precision manufacturing for regional NSW
Thales Australia’s Lithgow Arms business on 21 February marked the beginning of a new industrial era for its Lithgow facility and 140-strong workforce, with a sod turning ceremony to commence construction of a new $6.5m building, the first phase of an industrial plan to transform the Lithgow Arms facility in regional New South Wales.
Building on $70m of investment by Thales Australia in the Lithgow facility that has included new equipment and product development over the past decade, Phase 1 of this new industrial plan will establish a modern manufacturing and integration hub for the design, development and precision manufacture of next generation weapons systems for the Australian Defence Force, industrial partners and export customers. The ceremony was attended by leaders from local, state and federal governments including: Paul Toole MP, Deputy Premier of NSW and Member for Bathurst. Toole said: “This is a momentous occasion for both Thales and Lithgow today. The $6.5m investment by Thales in a new facility here in Lithgow shows that Thales is going to be in Lithgow for a long, long time. Today marks the future, and a new era that not only secures existing advanced manufacturing jobs here in Lithgow, but will continue to create new jobs into the future.” Since 1912, the Lithgow small arms factory has proudly supported Australia’s soldiers in every major conflict, and employed over five generations of local workers. This industrial transformation plan will harmonise the steadfast traditional precision manufacturing of yesteryear with the introduction of new digital technologies, and globally benchmarked high precision manu-facturing techniques. A necessary step in achieving the company’s Industry 4.0 ambitions. New technologies will include 3D printing, as well as the installation of automated electro-plating and other metal treatment capabilities. A new purpose-built live firing test and evalua-tion capability will support systems integration of existing and new technologies for developmental advanced weapons systems such as the Digital Battle Rifle, and the acceleration of research and technology development of other digitised small-arms and weapon system platforms. Corry Roberts, Vice President – Land at Thales Australia & New Zealand, said: “We are a company that loves to make complex stuff, and we take our stewardship of this strategic manufacturing facility very seriously. This factory doesn’t only have a great history – it has a great future as well. We are excited today to be celebrating the commencement of a new era for the Lithgow factory, and the continuation of delivering truly Australian, truly sovereign weapons and weapons systems capabilities now, and into the future.” The new development will expand the capability of Lithgow Arms to also support new sovereign manufacturing partnerships for strategic ADF programs, including the recently announced partnership with Rheinmetall Defence Australia. Coupled with the company’s recent announcement to expand its partnership with Fuller Global and Outdoor Sporting Agencies (OSA) to help grow its export markets by 300% in the next two years, Lithgow Arms will create a possible 4050 new jobs in regional NSW. The precinct will also provide facilities to enable collaboration across research institutions, SME partners, and key industrial partners to create the soldier systems and small arms of the future, and secure the next generation of manufacturing and engineering skills in Lithgow and across the Central West.
www.thalesgroup.com.au
NSW to power local manufacturing with locally built electric buses
The New South Wales (NSW) Government is supporting the creation of local manufacturing jobs in Western Sydney with a $70m investment to transition the state’s bus fleet to zero-emissions technology.
Western Sydney-based company Custom Denning has been awarded a contract to design, manufacture and assemble 79 new electric buses. Premier Dominic Perrottet and Minister for Transport and Veterans David Elliott toured the St Mary’s factory on 14 February to inspect the production line and meet workers. “This is a true Western Sydney success story and our government is proud to have played a part in this business producing the first locally-built electric bus,” Perrottet said. “Custom Denning employs 160 workers at their St Mary’s factory and this investment will now provide more jobs to ensure our buses are built to the highest standard. “Our government is getting closer to securing a cleaner, healthier future for the people of NSW and at the same time this electric bus transition will generate hundreds of local manufacturing jobs, which is an amazing outcome for our state.” Elliott added that the $70m investment takes the number of bus orders placed with Custom Denning past 100, which will help drive a post-pandemic jobs recovery and a boost for local manufacturing. “The NSW Government’s commitment to transition the entire 8,000-plus bus fleet is super-charging jobs and manufacturing in Western Sydney,” Elliott said. “Bus customers are already experiencing the benefits of electric buses from Penrith to Bondi, and we will continue to back local manufacturing. I’m committed to exploring opportunities to secure more local manufacturing, component supply and workforce skills development to boost our economy.” Once built, the 79 buses will operate services in Sydney’s inner west. Transport for NSW, in collaboration with its contracted bus operators, have ordered 101 electric buses from Custom Denning. www.custombus.com.au www.nsw.gov.au
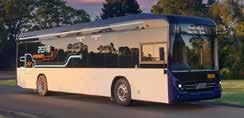
Economic Accelerator – Transforming research into world-leading business
A new $1.6bn economic accelerator will turn Australia’s leading research into world-beating businesses as part of the Morrison Government’s focus on building the country’s resilience.
Australia’s Economic Accelerator (AEA) features as part of a $2.2bn package to focus the commercialisation of the six national manufacturing priority areas – Resources and Critical Minerals, Food and Beverage, Medical Products, Recycling and Clean Energy, Defence and Space – bringing the country’s brightest business and academic minds together. Together with a new $150m expansion of CSIRO’s Main Sequence Ventures, the AEA will reshape research funding to emphasise projects with high potential for commercialisation that are directed at National Manufacturing Priorities and industry engagement. The Prime Minister said the AEA would invest in projects as they progressed through the stages of their development. “Stronger commercialisation of research and ideas will mean a stronger economy and a stronger future for Australia,” the Prime Minister said. “This is about funding projects to bridge the ‘valley of death’ where early-stage research is often not progressed due to higher levels of risk and uncertainty. “The AEA will drive our universities and businesses to work hand-in-glove through the stages to prove projects’ viability and potential. “Expanding the CSIRO’s Main Sequence Ventures program then takes this further, incentivising the additional venture capital investment support needed to progress innovative new products and technologies through to market to become the new businesses and employers of the future.” Acting Minister for Education and Youth Stuart Robert said the AEA would boost investment in two critical stages of experimental development: proof of concept and proof of scale. “The AEA will become a critical source of competitive funding support for innovating new projects with high commercial potential, and will take a lot of the risk and uncertainty for universities out of the equation,” Minister Robert said. “We will start with a big range of contenders – a contest of ideas. “But as we progress to stage two, the number of applicants will diminish and the value of the funding to each will increase. “For example, stage one will involve nearly 100 grants a year of up to $500,000. Recipients will be required to engage industry through in-kind support or even co-location. “In order to be one of the 36 recipients attracting up to $5m in funding as part of ‘stage two’ projects, industry will need to put more skin in the game with a 50% co-investment. “At stage three, up to 50 companies will be supported through the Main Sequence Venture, where we are providing $150m in two successive co-investment funds. “This investment is about new jobs, increased wages, and creating products that make life easier, more efficient or even more interesting,” Minister Robert said. Minister for Industry, Energy and Emissions Reduction Angus Taylor said the grants were an investment in Australia’s future industries and smart manufacturing within the Morrison Government’s National Manufacturing Priorities. “By working with industry and researchers, the government is helping to ensure our economy benefits from our world-class research, both now and well into the future,” Minister Taylor said. Minister for Science and Technology Melissa Price said the $150m expansion of the CSIRO Main Sequence Ventures program would back start-up companies and help create commercial opportunities from Australian research.
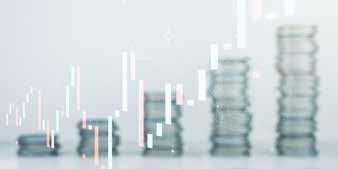
“The Morrison Government is prioritising investment in research and action to turn Australia’s best ideas into new industries and strengthen our future prosperity,” Minister Price said. “The expansion of the Main Sequence Ventures will further support the development of spin-off and start-up companies with high commercial potential arising from local research. “Over the past four years, Main Sequence Ventures has invested in 39 companies that are commercialising deep tech opportunities that have created more than 1,200 technology-related jobs. “Our new investment in this program will ensure it can play a bigger role in our economy and help develop the next generation of great Aussie companies and products.” Minister Robert said the Morrison Government would also invest $296m in industry-focused PhDs and fellowships to support its research commercialisation goals and drive greater universityindustry collaboration. “This new scheme will generate 1,800 industry PhDs and over 800 industry fellows over 10 years to fundamentally reshape the workforce of Australia’s universities,” Minister Robert said. “PhD students will benefit from the experience of undertaking research within industry settings, creating employment pathways beyond academic roles. “Industry will benefit from the opportunities to host PhD students, bolstering their ability to harness ideas and concepts for innovation, as well as to open the pathway to the recruitment of high-calibre graduates. This will be further enhanced by a new suite of ARC Fellowships that will recognise and reward our academics who collaborate with industry, helping to drive the translation of their research, creating new pathways for their work. “These initiatives will change the culture and the focus of research across Australia’s universities – building greater engagement with industry and ensuring that innovation is at the core of our economic future as a nation.” www.pm.gov.au/media
Victoria’s new Local Jobs First Commissioner will champion local businesses and workers getting roles in the state’s big infrastructure, manufacturing and services projects.
Moana Weir started as Victoria’s new Local Jobs First Commissioner in January and brings a wealth of experience to the role. She has been a senior officer at companies including SEEK, REA Group, and an executive at Bupa. An experienced lawyer, she is currently Chair of the Victorian Equal Opportunity and Human Rights Commission. The Local Jobs First Commissioner advocates on behalf of Victorian small and medium-sized enterprises and promotes the employment of Victorian apprentices, trainees and cadets on government construction projects. The role also oversees compliance with local content commitments that maximise opportunities for local industry. Ms Weir replaces the inaugural commissioner Don Matthews, who retired in 2021. The Victorian Government is the largest procurer of goods, services and construction works in the state and helps to develop local industries, create jobs and boost economic activity. Under its Local Jobs First policy, the Victorian Government has set local content requirements for 227 strategic projects since December 2014.
Minister for Industry Support and Recovery Martin Pakula
Victoria’s Local Jobs First Act 2003 is Australia’s oldest legislation on mandatory local content, requiring all Government departments and agencies to apply local content for contracts valued at $1m or more in regional Victoria, or $3m or more in metropolitan Melbourne. It also requires job opportunities to be created for Victorian apprentices, trainees and cadets on projects worth over $20m.
www.localjobsfirst.vic.gov.au
Cairns manufacturing sector boosted with Hub funding
The future of far north Queensland manufacturing gets a boost with the Palaszczuk Government announcing permanent funding for the Cairns Manufacturing Hub, as part of a $17m state-wide boost for manufacturing.
Minister for Regional Development and Manufacturing and Minister for Water, Glenn Butcher, said the Palaszczuk Government’s investment in Manufacturing Hubs and Made in Queensland Grants has created and supported nearly 6,000 jobs to date. “The work done at these hubs is vital to building and strengthening Queensland’s booming manufacturing sector. “Manufacturing already contributes $20bn a year, to the state’s economy and employees and we want to see that grow even further,” Minister Butcher said. Minister Butcher was joined by his far north government colleagues at Status Signs, in Portsmith, to make the funding announcement. Cairns MP Michael Healy said the Cairns Manufacturing Hub has already shown great results. “I know the team at the Cairns Manufacturing Hub has worked really hard to get support for local business and working with a group like Status Signs brings many rewards.” Barron River MP Craig Crawford said the Cairns manufacturing sector contributed about $780m annually to the state’s economy and employed more than 6,000 workers locally. “We cannot underestimate the value of manufacturing in the Cairns region,’’ Mr Crawford said. “It is one of our most important sectors and we want to see manufacturing continue to thrive.’’ Speaker and Mulgrave MP Curtis Pitt is confident the ongoing Hub funding and associated grants will help far north businesses be recognised as global leaders. “This funding will ensure Queensland manufacturers continue to receive the services offered by the Hubs, remain nationally and internationally competitive, and are in a position to take advantage of growth opportunities,” Mr Pitt said. Status Signs Director Rhys Carmady said the Manufacturing Hub and the team had been very helpful in securing a grant that has increased the capability of the business. “With the help of the great team at the Cairns Manufacturing Hub we have secured a grant of more than $130,000 which we have been able to use to buy a CNC routing machine, which cuts objects into 3D shapes, a 3D UV printer, a CNC laser cutter and some automated software. “It’s going to be absolutely vital in helping our business grow.” Mr Carmady said the team had helped with training and courses for his staff and this has been vital for not only adding skills to the business but also helpful with staff retention. “The courses and training have been exactly what we’ve needed and the Manufacturing Hub team, Andrew and Sandra, have been fantastic to deal with,” he said. Funding of $17.75m will enable the Hubs, including Cairns, to continue to support regional manufacturers to grow their businesses and create local jobs. Each Hub has established itself to build on the current economic strengths of their regions. “The Manufacturing Hubs are bringing together the industry partners, state and local governments, local businesses and educational institutions to collaborate and grow regional manufacturing,” Mr Butcher said. The Manufacturing Hubs build stronger and sustainable regional businesses and develop connected industry ecosystems to increase national and international competitiveness, lift productivity, stimulate sustainable job growth, and attract private sector investment.
www.qld.gov.au
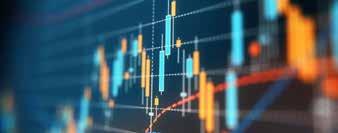