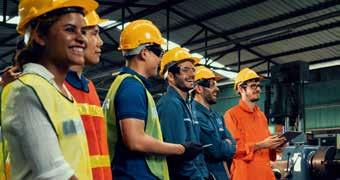
27 minute read
VOICEBOX Opinions from across the manufacturing industry
from AMT APR/MAY 2022
by AMTIL
In the last issue of AMT, Jack Parr examined the history and evolution of manufacturing leadership. Now he looks at what the future holds and how manufacturing leaders can face the challenges to come.
My previous article described the development of leadership principles in the 20th Century, ending with the question “What are the new principles to drive Australian Manufacturing to 2030?” With help and advice from several industry colleagues, I have sought to answer that question. First, howevever, it is important to contextualise today’s conditions compared with earlier halcyon times. While onshore manufacturing is currently front of mind, the sector is no longer the driver of Australia’s economic prosperity, accounting for just 6% of GDP. Neither political party seems to have the determination to create a more progressive industrial landscape to underpin and accelerate a decade-long rejuvenation plan. Technology has changed industry. Automation and technological integration are driving the replacement of manual work with ‘knowledge work’. Technological change has outpaced our education system, particularly tertiary. STEM is struggling for priority in an increasingly crowded school curriculum. Despite technology, peoples’ pace of life has increased – counterintuitively with longer working hours. Societal standards have also changed. Work-life balance is a growing factor in career choices, with service industries offering greater appeal, to manufacturing’s detriment. Harassment and bullying are no longer tolerated, and triggers for anxiety are much lower, demanding an innovative approach to people management and ‘social responsibility’. There are existential environmental and ecological threats to the planet. The net effect of these pressures means manufacturing can no longer be inert, insular and individualistic. Companies must become progressive, innovative, and more attractive. Management must evolve from controllers to people motivators and skill- and knowledge-providers. Companies must become collective and collaborative, while acting as advocates for the industry itself! Within that context, I offer four key principles for the future of manufacturing leadership:
• Principle 1: Transition to ‘Collegiate Management’.
Management needs to take a fresh approach to divisions of work; inflexible rules; fixed hours, salary or wages, on-site or off site working, differing ‘hygiene’ standards – all should be up for transition. It is time for a collegiate approach to people management. Enterprise bargaining agreements (EBAs) epitomise the issue. A bargain is “agreement between two groups”. Should a company not be one team with benefit for all? This is not an analogue transition, but the place to start is with existing employees who demonstrate the attitude and skills the company values. Such people are also marketable, so they need be fully engaged by using a ‘flexibility toolkit’ – including, of course, total remuneration. The other issue is to recruit well. Several colleagues expressed the view that HR’s role in recruitment needs rethinking. The new social compliance processes can lead to ‘appropriate choice’ but ‘inappropriate fit’ to actual need. • Principle 2: Capability is now your responsibility. The industry faces both manufacturing and engineering skills gaps.
To meet technology-driven skills demands, some enlightened (and frustrated) companies have set up their own apprenticetraining schools or joint training ventures. One such visionary said “We send them for one day (for the TAFE Certificate) and the other four days, we retrain them!” Capability is a driver of productivity; innovation is the key, so the onus is now with the company to provide people with tomorrow’s skills and capabilities. The new question is how to train and develop.
One colleague rightly pointed out that ‘attention spans are lower today’, so learning methods must adapt and utilise practical workplace applications. The challenge is to identify these capabilities, develop learning protocols and delivery methods, and integrate capability development into normal company practices. • Principle 3: Everything is about innovation. It has always been my belief that manufacturing is like “walking up a down escalator – stand still and you go backwards!” Today, you must be looking to innovate, to use technology and people’s capability to maximise productivity. But innovation is not about invention! It is about continuous improvement, the use of the latest technologies and integrated computer systems to automate processes and provide better data to measure and manage. It is about the paperless factory. Electronic integration with the customer will become the service innovation for both process and product management. One colleague is already using electronic condition monitoring to improve product servicing. Industry 4.0 and even 5.0, while having high entry costs, will become ubiquitous. Innovation is also about empowerment of people; the distribution of information to aid capability, leading to distributed authority and more task autonomy for individuals or teams. Management should no longer be about control, but about motivational support and leading continuous improvement. • Principle 4: Advocacy for the industry. Manufacturing encompasses a range of industries who all use things made from metal, supplied by manufacturing SMEs who provide everything from components to capital goods. Yet this sector and these companies lack a ‘collective voice’ – let alone a ‘collective mind’! Manufacturing is not only an essential economic sector, but one that can offer rewarding, challenging careers. The sector can only grow if more people appreciate its value and choose it as a career. The industry needs to advocate as both a collective body top-down, and at an individual company level upwards. It has to start ‘marketing’ itself to graduates, school students and the general public.
How many companies offer open days to the local community, or even employees’ families? How many promote themselves and the industry to local schools? Do industry bodies really promote the attraction of manufacturing? How visible is their advocacy and how are they building the ‘collective voice’? Leadership and management over the next decade should be through a collegiate relationship rather than a subordinate one. It must be looking to use capability and empowerment as a driver of productivity. It should look to develop collective innovation through collaborative knowledge sharing. Finally, leaders must have a collective and individual purpose to ensure a growing and sustained future for the manufacturing sector. Jack Parr is the Coordinator for the Vernier Foundation, a charity aimed at funding and supporting, STEM education in schools. The Foundation is the charitable arm of the Vernier Society, an organisation that for nearly 80 years has worked to support Victorian Manufacturing. www.vernier.org.au
Attract and retain talent during a labour shortage
With global headlines reminding employers of the ‘tight’ labour market, businesses are faced with a difficult question: ‘How best to retain and attract staff in a competitive labour environment?’ By Andrew Nicola.
It is more important than ever for employers to have an effective and cost-efficient strategy to attract and retain key staff. In the current environment, this means offering competitive remuneration packages potentially applying a number of ‘levers’ to achieve the best result for the employee and the employer, this may include: • Short term incentives • Salary packaging • Equity incentives, including ‘phantom share schemes’ • Communication of total remuneration Short-term incentives
Examples of short-term incentives include cash bonuses and payrises. These incentives are simple to implement and quite flexible, however the potential downsides include: • The employee’s bonus is subject to tax at their marginal rate • There are various employer on-costs (i.e. payroll tax,
WorkCover, etc.) • Do the bonuses incentivise the employee or align the employee interests with the employer? • Is there an expectation the bonuses will continue? Salary packaging
Salary packaging is broadly where an employee arranges to receive less cash salary in return for certain benefits. The types of benefits that can be effectively packaged will depend on the employer, the industry and certain individual circumstances. Common benefits salary packaged include: • Motor vehicles. • Computers and other devices. • Tools of trade. • Car parking. Due to the concessional tax treatment of certain benefits, salary packaging can often provide employees with a greater after-tax cash position, while not costing the employer any more. Furthermore, employment on-costs such as payroll tax, workers compensation and superannuation guarantee can sometimes be reduced. Equity incentives
Equity incentives are a component of an employee’s remuneration package that provide employees an opportunity to owning a portion of the business, usually via shares and options. Equity incentives can: • Help the business attract and retain talent. • Promote the company’s long-term success by aligning interests between owners and employees. • Improve an employee’s remuneration package without impacting the business’ short-term cash flow. While used extensively by public companies, equity incentives can be more difficult to implement for private businesses. For example, it may be that a private business owner is uncomfortable to offer ownership to a non-family member or the structure does not facilitate this – ie the operating entity is a Discretionary Trust. A recent trend within private businesses are ‘Phantom Share Plans’, which aim to replicate the benefits of share ownership without granting actual ownership to the employee. These plans seek to deliver a cash bonus to a participating employee, linked to the increase in the value of the business and/or other key business metrics. A Phantom Share Plan can be administratively simple to establish, is flexible with how the award is calculated and does not have the Corporations Act obligations of a normal equity plan. Another option gaining attraction are loan-funded share plans. These arrangements generally involve the employer providing an interest-free limited recourse loan to enable certain employees to acquire shares in the business at market value. The limited recourse feature of the loan means that the employee is protected from downside risk if the value of the shares falls below the outstanding loan balance. When implemented correctly, these arrangements should not have adverse tax outcomes to the employee or employer. However, these arrangements are complex, and it is critical that appropriate documentation be prepared otherwise unintended tax outcomes can arise. Total remuneration approach
Another trend is communicating ‘total remuneration’ benefits to employees, where financial and non-financial benefits are quantified and made visible to employees. Quantifying the total remuneration will better inform employees of their current package. The following components may be included in the ‘total remuneration’ approach: • Fixed salary. • Variable performance incentives – both short- and long-term. • Equity holdings (if provided). • Other non-financial benefits, which may include: - Flexibility to work between the office and home - Training and development initiatives - Parental leave - Income protection insurance - Non-cash benefits (e.g. phone, carparking, free gym membership etc). Research indicates that employers who adopt a ‘total remuneration’ approach can see an increase to employee engagement, decrease in staff turnover and a boost to the employer’s brand. Australian businesses are faced with labour shortages in a time of continued economic uncertainty. This is forcing many to think outside the box and implement financial and non-financial incentives to attract and retain staff. With many options available there’s no one-size-fits-all approach. It’s important to talk to your trusted tax advisor if you are considering any of the above options, to identify and implement the most suitable and effective remuneration strategy for your business.
Andrew Nicola is a Tax Director at William Buck www.williambuck.com
Rubbish in rubbish out: the importance of documenting: performance vs operational
Whether your business is expanding, automating, or recently established and is embarking on the design and construction of a new facility, countless hours will have been spent planning the benefits and commercial drivers of your new project. Failure to communicate and articulate your project’s specifications in accordance with the relevant performance criteria can be catastrophic. By Victor Borzillo.
Most well-drafted construction contracts will provide mechanisms to administer contractual disputes by providing clear and structured frameworks as to how you (as the owner/principal) and the contractor should respond to common issues including warranties, variations, delays, performance requirements and testing and commissioning expectations. However, these provisions will be of little value to you in circumstances where the specifications: • Have not been appropriately or correctly identified or referenced to form part of the overarching contract. • Are outdated (commonly caused by referencing superseded design revisions or iterations). • Have been developed without reference to, or contemplation of, relevant performance requirements of the proposed facility. • Are otherwise incorrect. Deficient specifications often mean that contractors can rely upon otherwise clearly drafted contractual provisions to justify additional variation costs and delayed project completion. Negotiated risk allocation can provide a false sense of security
Contractual risk allocation and responsibility aside, deficient design briefs or unclear contractual specifications can be extremely costly to overcome. Even if your contract terms afford you the protection of consequential loss (which is becoming increasingly less common and will most certainly increase construction costs to provide “contingency” for contractor risk), delayed commencement of operations at your new facility can cause irreparable harm to your company’s reputation and revenue. Further still, an election to accept an increased project price (reflecting contingency risk) to obtain additional protection from your contractor will not always achieve the intended outcome. Reliance upon contractors’ indemnities and insurance coverage can often lead to a false sense of security, for example, in circumstances where: • The contractor’s financial position may not withstand a claim for loss and damage by your company. • The contractor’s insurance does not respond to the category of loss claimed, or worse, is otherwise voided due to warranties or commitments proffered by the builder which are specifically prohibited. In these situations, the contractual security you have relied upon (and paid a premium for) may ultimately prove to be worthless. Risk mitigation as a stitch in time
The commercial benefits of building a new or upgraded facility will have already been considered by the time you are ready to progress to project design and delivery phases. The real question at this juncture is, how can you mitigate identified risks? As is the case with most commercial endeavours and transactions, the devil is in the detail. The old adage “measure twice, cut once” rings true from the simplest task to the most complex of major projects. There is absolutely no substitute for careful and informed planning to ensure the comprehensive documentation of your project’s specifications and operational requirements.
Assisting you in developing specifications for your project
Some recommendations to assist you in developing and documenting specifications that align with relevant operational and performance requirements are as follows: • Establish an internal steering committee comprising key stakeholders/representatives from within your business. • Minute steering committee meetings to record key commercial, operational and practical considerations. • Develop a risk assessment matrix which contemplates relevant issues including: - key operational considerations; - commercial/contractual obligations to your customers; - operation and maintenance risks; - operational cost expectations and requirements; - environmental impacts and requirements; - funding and grant requirements; - approval pathways and requirements; - legislative requirements; - project planning considerations; and - project delivery issues. • Engage experts and consultants with appropriate qualifications and industry experience. • Engage lawyers with practical project delivery experience to compliment your own project team. • If your own in-house team does not include someone with practical experience in delivering construction projects, engage a project management consultant to work with your legal advisers and your own project delivery team. • Ensure your planning and design phase is adequately resourced commensurately with the size, complexity, and value of the project and/or the expected commercial output of your completed facility. When preparing specifications and inputs, ensure your design team understands the expected commercial outputs of your product or service, along with all other key requirements that arise from or incidental to your project. These considerations often include your own customers’ expectations, feedstock parameters and limitations, finance terms, grants, facility design life, environmental obligations and ongoing operational and maintenance expectations. If not considered from the outset, any one of these issues can result in project failure and protracted (and expensive) rectification and dispute resolution processes. All of these potential risks are unnecessary and can be avoided or significantly reduced by implementing appropriate and comprehensive project planning procedures. If you remember one thing
‘Rubbish in rubbish out’ should serve as a simple prompt to remind you of this key message: there is absolutely no substitute for careful and informed planning to ensure the comprehensive documentation of your project’s specifications align with the relevant performance and operational requirements of your business.
Victor Borzillo is a Principal And National Head of Group at Macpherson Kelley. www.mk.com.au
How global demand and pricing are impacting Australian aluminium suppliers
The COVID-19 pandemic continues to cause profound disruption to global supply chains across a range of industrial sectors. One area experiencing turbulence is in the supply of aluminium, writes Tony Dragicevich of Capral Limited.
If you’d sat behind the desks of the CEOs of Australia’s leading industrial fabrication, transport and marine businesses in March 2020 as the first wave of COVID-19 restrictions rolled out, you’d never have predicted the turn of events these industries would experience over the coming 24 months. Many were forecasting reduced demand, industry downturns, staff reductions and operational stand-downs. Fast forward two years and as an industry we are riding a collective wave of strong demand. Local manufacturers are benefiting from the reduced presence of imported aluminium products, spurring increased demand for locally fabricated aluminium products. The strong growth in demand has created a different type of challenge for local businesses that use aluminium, who are now faced with supply challenges due to material shortages and supplier capacity, while subject to unprecedented aluminium pricing pressures. In fact, capacity to supply aluminium products within Australia has never been pushed so hard, with pricing impacts and supply shortages affecting everything from beer cans to car parts, not to mention plate and rolled products. Capral Aluminium is Australia’s largest producer and distributor of aluminium products, supplying to a wide range of industrial sectors as well as commercial and residential building. It is also Australia’s largest aluminium supplier to the transport, marine and general aluminium fabrication sectors. Capral has seen a significant change in requirements for local aluminium supply over the past 18 months – we are noticing growing market share against import products. Of course, the Australian industrial, transport and marine sectors are currently very buoyant, and our customers supplying these industries are under pressure to meet the strong demand. Australia is not the only country where the economy has been boosted by government stimulus. In addition to supply pressures there has been a significant lift in global commodity demand and prices, including aluminium. Aluminium pricing can be complicated to understand for those of us who don’t delve into the world of commodity markets. However, there are three core elements impacting on the price of aluminium, all of which are experiencing record highs and ultimately impacting on price of fabricated aluminium products. 1. LME. LME is the market-traded price of aluminium on the
London Metal Exchange and is used globally (outside China) as the primary cost of aluminium. LME prices reached $4.40/kg in early February, their highest since 2008, up a massive 60% from the start of 2021. 2. Billet Premiums. Aluminium extrusion manufacturers, including Capral, extrude the aluminium profiles from a billet, being the base material extruders use for production. Billet is purchased from primary aluminium smelters both in Australia and internationally, where smelters add a number of base premiums for extrusion billet supply. Over the past decade base billet premiums have been stable due to a reasonable supply/ demand balance for billet across the globe. The situation has changed dramatically for 2022. Global demand for billet in 2022 has outstripped supply and has led to up to 350% increases in premiums for 2022 smelter supply contracts. 3. Extrusion Supply. With record levels of local extrusion supply, and many extruders operating a full capacity, it is likely that
Australian industrial, transport and marine fabricators will see the cost increases of aluminium raw materials experienced by the local extruders passed on through the supply chain. No doubt this will also place pricing pressures on these businesses with the cost of materials set to rise over the coming year. So what is the forecast for 2022? Industry experts expect the cost of aluminium to remain relatively high throughout 2022. Global factors play a large part in this scenario, not least the impact of government directives in China and Russia, who have traditionally been strong suppliers of aluminium to the global market. In August 2021, Russia imposed at 15% export tax on aluminium. This further increased regional market premiums and presents an upside risk on prices. As China decarbonises, increasing smelting cuts have been taken to meet regional energy consumption and energy intensity targets under China’s five-year plan to reduce emissions. China aluminium cuts are now around 2.3MT/year with risk of further cuts in coming months. Combined with other factors already described, this has driven up LME metal prices to multi-year highs Finally, freight costs and availability continue to place pressure on the local supply of imported billet, with spot prices for containers increasing by more than 200% in 2021, and the shortage of containers is expected to persist in 2022. Costs for importers to ship to Australia will also increase significantly. Therefore, from a profitability perspective, aluminium smelters may be able to generate higher margins in alternative markets, such as the EU and US, relative to Australia with strong product and market premiums. To maintain the flow of billets in Australia, the product premiums have substantially increase. From a local perspective, this is a double-edged sword for Australian extruders. We have excellent demand, but costs continue to rise. At Capral we are working very hard to ensure our plants are operating at full capacity and maximum efficiency so we can mitigate any unnecessary cost increases for our customers and meet their expectations around timely supply. We are committed to supporting our customers in these areas and have worked very hard to establish the additional capacity needed to supply local manufacturers. Throughout 2021 we made a number of capital improvements and have even brought an additional extrusion press online to meet demand. There are few industries who are not facing unprecedented times in response to COVID-19 and the changes it has brought to our economy. The industrial, transport and marine sectors are no different. I hope they will continue to support our local manufacturers well into the future.
Tony Dragicevich is the Managing Director of Capral Limited. www.capral.com.au
Australia: Decarbonisation tech instantly converts CO2 to solid carbon
Researchers have developed a smart and super-efficient new way of capturing CO2 and converting it to solid carbon, to help advance the decarbonisation of heavy industries. Designed to be smoothly integrated into existing industrial processes, the new, modified tech is radically more efficient and can break down CO2 to carbon in an instant. The work is built on an earlier experimental approach that used liquid metals as a catalyst. The “bubble column” method starts with liquid metal being heated to about 100-120°C. CO2 is injected into the liquid metal, with the gas bubbles rising. As the bubbles move through the liquid metal, the gas molecule splits up to form flakes of solid carbon, taking just a split second. It’s the extraordinary speed of this chemical reaction vs alternative methods that makes this technology commercially viable.
RMIT
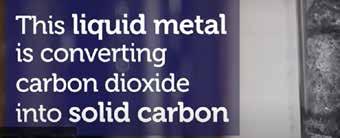
USA: Creating the “impossible”: Lightweight material stronger than steel
A new substance is the result of a feat thought to be impossible: polymerising a material in two dimensions. Using a novel process, chemical engineers have created a new material that is stronger than steel and as light as plastic, and can be easily manufactured in large quantities. The new material is a 2D polymer called a polyaramide that self-assembles into sheets, unlike all other polymers, which form one-dimensional chains. Until now, scientists had believed it was impossible to induce polymers to form 2D sheets. For the monomer building blocks, melamine is used. Under the right conditions, these can grow in two dimensions, forming disks. These disks are stacked, held together by hydrogen bonds between the layers, which makes the structure very stable and strong.
MIT
Australia: Lotus effect: Self-cleaning bioplastics
Inspired by the always immaculate lotus leaf, researchers have developed a self-cleaning bioplastic that is strong, sustainable and compostable. Easily integrated with industrial manufacturing processes, the bioplastic is made from cheap and widelyavailable starch and cellulose. Most compostable plastics require complicated industrial processes and high temperatures; this one does not. The secret lies in the lotus leaf’s surface structure, which is composed of tiny pillars topped with a waxy layer. Any water that lands on the leaf remains a droplet, simply rolling off. Researchers synthetically engineered a plastic made of starch and cellulosic nanoparticles. The surface of this bioplastic was imprinted with a pattern that mimics the structure of lotus leaves, then coated with a protective layer of PDMS, a siliconbased organic polymer. The bioplastic not only repels liquids and dirt effectively, but also retains its self-cleaning properties after being scratched with abrasives and exposed to heat, acid and ethanol.
RMIT
Magnified 2000 times, the pillared structure of a lotus leaf (left) and the new bioplastic.
USA: Is 3D printing ready for the factory floor?
Metal 3D printing start-up Seurat Technologies has raised another $21m to help accelerate the roll-out of its proprietary Area Printing technology - a process in which a laser containing over 2.3 million pixels, is used to ‘micro-weld’ metal powders into thin layers on a print bed. According to Seurat, its approach is unique, as it ‘decouples’ print rate and resolution, allowing it to overcome 3D printing’s “speed, quality, scale and cost trade-offs.” It is said to be “infinitely scalable,” and potentially offers cost savings compared to traditional die-casting processes for manufacturers operating in all industries. Seurat says that its system will offer users major speed and cost efficiency, especially compared to traditional production methods. At launch, the machine will be capable of 3D printing at a cost of $300/kg, but the firm intends to lower this to $150/kg by 2025, giving it casting-level capabilities.
3D Printing Industry
China: Biggest amphibious aircraft in the world
The size of a 737, China’s AG600 will be the biggest amphibious aircraft in the world after testing of its prototype is completed. Designed by AVIC (Aviation Industry Corp. of China), previous iterations were trialled in 2017 and 2020. This craft will increase China’s maritime coverage to the entire South China Sea. China, however, claims it will be used in maritime patrols and search and rescue operations. It can take off and land in 2m waves, can cruise at speeds of 500kph with an endurance up to 12 hours. While not combat-ready, it can carry personnel and equipment and can ferry up to 50 passengers. When arriving on land, the aircraft swings out the rear wheels that are lined up along the fuselage, while the nose wheel emerges from the keel of the boat.
Interesting Engineering
The AG600 during a previous test
USA: Creating a better plastic
Thermoplastics which are melted down, weaken with each reuse which is a barrier to recycling. But a group of chemists has discovered a method to break down plastics to create a new material that is stronger and tougher than the original. The stability of carbon-hydrogen bonds makes it difficult to turn natural products into medicines and challenging to recycle plastics. But by modifying these bonds, the life span of polymers could be expanded beyond single-use plastic. With a newly identified reagent that could strip hydrogen atoms off medicinal compounds and polymers, the chemists made new bonds in places previously considered unreactive, enabling many valuable transformations on a wide range of important compounds. “It could change the way we look at plastic”.
University of North Carolina at Chapel Hill.
USA: New soft robot material: Reversible plasticity
Researchers have discovered a new approach for shape-changing using rubber, metal, and temperature to morph materials and fix them into place with no motors or pulleys. By observing the strength of kirigami patterns, the team created a material architecture of a repeating geometric pattern. Next, they needed a material that would hold shape but allow for it to be erased. Here they introduced an endoskeleton made of a low melting point alloy embedded inside a rubber skin. Normally, when a metal is stretched too far, the metal is bent, cracked, or stretched. However, when stretched, this composite would hold a desired shape rapidly, perfect for soft morphing materials that can become instantly load-bearing. Finally,
the material had to return the structure back to its original shape. Heaters were incorporated next to the mesh which cause the metal to be converted. The applications for this technology are only starting to unfold. By combining this material with onboard power, control, and motors, the team created a functional drone that autonomously morphs from a ground to air vehicle.
Virginia Tech
Ground-based robot morphs into flying drone

Australia: Technology increases detection of wound infection
A new study has found fluorescence imaging technology, an advanced diagnostic device which allows clinicians to see into a wound, can increase the detection of infection by 11-fold. Developed by MolecuLight, the device is poised to change post-surgical wound management. The study shows that pathogenic bacterial burden is present in most surgical wounds, but is largely asymptomatic and therefore goes undetected. This device quickly and reliably detects bacterial burden at the point-of-care. This is the first study reporting the use of an advanced diagnostic device for the visualisation and diagnosis of infection in surgical wounds.
University of WA
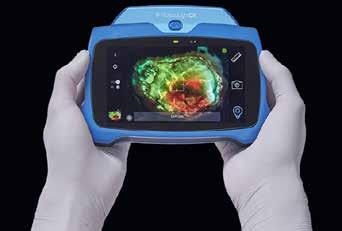
Moleculight's advanced diagnostic device which allows clinicians to see into the wound. The laser beam is positioned at the joint between the two sheet edges to be welded, and a filler metal is inserted in front, resulting in a high-quality welded seam.
Australia: Fighting fire with nuclear science
At the Lucas Heights nuclear facility, a team of scientists is building the firefighting uniform of the future - specifically for Australian conditions. They have fashioned an ultra-light fireproof material that could revolutionise firefighting gear and protect household items with a simple coating, and after six years of research are ready to commercialise it. The scientists investigated a family of two-dimensional transition metal carbides: carbonites and nitrides, known as MXenes. Protective suits made with traditional retardant use as much as 40% carbon compounds, making them heavy. Because this material uses very low concentrations of the material, it comprises only about 1-5% of the total weight. And because it can be applied as a post-treatment, it doesn’t complicate the manufacturing process. The maximum fire reduction is 50-70%. The versatile material could also potentially be used in energy storage devices.
The Age/ANSTO
Germany: Revolutionising steel construction with laser welding
An alternative for conventional steel construction has been developed which facilitates gentler machining of high-strength materials, and significantly reducing energy consumption and costs while greatly increasing process speed. The energy input required can be reduced by up to 80% and subsequent straightening of the component is eliminated entirely. A large proportion of the energy expended in conventional gas or arc welding is lost in the form of heat. Researchers have developed an energy-efficient alternative – the laser multi-pass narrow-gap welding (MPNG), uses a commercially available high-power laser and reduced number of layers with drastically reduced seam volume. The high intensity of the laser beam guarantees that the energy input is highly localised at the welding point, whereas the surrounding areas remain comparatively cold. The new process also excels in terms of weld seam quality – the seams are significantly slimmer and the edges are virtually parallel, whereas in conventional welding processes the seams are V-shaped.
Fraunhofer
“If you can do it in Australia, you can probably do it on the moon” Dr Brad Tucker from the ANU Research School of Astronomy and Astrophysics citing Australia’s “world class” mining sector as being instrumental in the acquiring of a NASA Rover deal. Included in Australia’s expertise is working in harsh and remote environments (Australia has the longest autonomous train in the world, in the Pilbara). Australia also leads the world in soil extraction and sample analysis. The new home-bred built Rover will pick up and transfer lunar samples to NASA’s in-situ resource utilisation system on a commercial lunar lander.
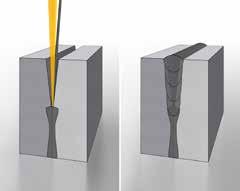