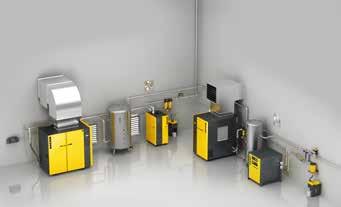
20 minute read
PRODUCT NEWS New and interesting products
from AMT APR/MAY 2022
by AMTIL
Kaeser launches DN 37 C XL booster
Kaeser Compressors has announced the launch of the DN 37 C XL booster. Part of the powerful, energy-efficient turnkey DN C series of boosters, this model is designed for applications that require high air demand up to 25 bar.
Powerful, compact and quiet, DN C boosters from Kaeser Compressors deliver uncompromising performance, dependability and energy efficiency. These innovative complete systems come into their own when, due to technical reasons, specific points in a production process require compressed air at a higher pressure than that supplied by the main compressed air network. They can therefore often be found in PET bottle production, process air applications, nitrogen compression and the provision of high pressure for testing facilities. The recently launched DN 37 C XL model, has been specially designed for high air demand. Kaeser’s largest compressor block, the DN 37 C XL, is the perfect choice for applications with high air demand up to 25 bar, delivering the highest possible flow rate available for this product series. Energy-efficiency comes as standard with these boosters; Premium Efficiency (IE3) drive motors, equipped as standard, contribute to energy-efficient performance, as does the generously dimensioned axial fan, which also ensures reliable temperature control. The DN C series boosters also feature separate cooling air flows for the compressor block, drive motor and control cabinet, which are drawn in through openings in the right-hand side of the enclosure. Once they have been used for cooling, the separate air flows are combined and then discharged upwards through the exhaust air outlet in the top of the enclosure. This clever design reliably prevents cool inlet air from mixing with warm exhaust air – for enhanced efficiency. Thermal overload is therefore kept to a minimum and a separate, energy-consuming cooling system for idling is only necessary under extreme conditions. DN C series boosters are delivered as complete turnkey systems, precisely matched to the upstream compressor. Thanks to the Sigma Control 2 controller, they are ready for connection and selfmonitoring. This is a huge advantage for keeping installation time and costs to a minimum. Kaeser Compressors is the first manufacturer in the booster sector to offer such a user-friendly complete solution, all neatly contained within a single compact enclosure. All maintenance-relevant components, such as cylinders and venting valves, filters, condensate separators, oil drain and filler openings are easily accessible thanks to large maintenance doors. Time-saving features such as these streamline and accelerate maintenance and service work, which translates into lower operating costs and increased availability. These new booster systems are perfectly matched for seamless networking with their “suppliers” – making them fully compatible with Industry 4.0 environments. The DN 37 C XL booster from Kaeser Compressors is available air-cooled or water-cooled, and produces flow rates from 11.54 to 18.9 cubic metres per minute. Initial pressure 7.5 to 13 bar, and final pressure 25 bar.
au.kaeser.com
Cooke Industries upgrades laser cutting capability with SLTL Rapid G
Based in Auckland, New Zealand,
Cooke Industries has brought together excellence in design, engineering, products and support to offer clients true solutions and services in a range of field including air handling, heating, cooling, acoustics, dehumidification, and air diffusion & distribution. To maintain its position as a market leader the company is constantly looking at process improvements. With this in mind, Cooke Industries recently looked to upgrade and enhance its capabilities with the addition of a laser cutting system. The system was needed to meet increased customer demand for high quality and quick turnaround. After extensive research the team settled on a SLTL Rapid G system supplied by Nichol Industries of Melbourne. The Rapid-G is specifically designed to fulfill the varied needs of the heating,

The SLTL Rapid G laser cutting system.
ventilation, & air conditioning (HVAC) duct fabrication industry. It is a perfect solution for sectors that need speed and accuracy. The fibre laser technology provides extensive productivity and speed for the HVAC cutting operations. The new laser cutting system was delivered and installed over the Christmas shutdown and is now further improving Cooke Industries’ capability and service levels. “We have been very impressed with the support and assistance we have received from the supplier, Nichol Industries and the manufacturer, SLTL,” said Andrew Cooke, Managing Director of Cooke Industries.
www.nichol.com.au cookeindustries.co.nz
Walter Supreme thread milling with new DeVibe technology
Unstable conditions and long overhangs often lead to vibration, poor thread surfaces or even fractures during thread milling processes. With the TC630 Supreme orbital thread milling cutter, Walter is presenting the first solid carbide thread milling cutter on the market with DeVibe anti-vibration technology.
Incorporating an antivibration land on the flank face into the design, the tool is stabilised during machining which suppresses vibration. The patent-pending DeVibe technology ensures excellent operational smoothness and enables usable lengths up to 4×DN, which is ideal for small threads, long overhangs, unstable conditions or difficult materials. Also in these difficult areas of machining, creating and maintaining dimensional accuracy is desirable and this is where the cutter’s overall design and geometry deliver exceptional results. With only one row of cutting edges is engaged at a time, tool deflection is addressed and the thread remains cylindrical. The moderate number of teeth also enables a high feed per tooth, enhancing the wear resistance already created by the carefully selected cutter substrate and coating. The Supreme milling cutter for blind-hole and through-hole threads has a broad application range that covers all ISO materials up to 48HRc. Metric thread sizes from M1.6 to M20 are in the standard program, while also in the range are cutters for metric fine pitch threads, UNC, UNF and STI UNF. The latter is primarily suited to aerospace applications. With the TC630 Supreme, users can take advantage of a range of benefits that the thread mill design delivers, such as a high level of process security and reliability in unstable machining operations. This enables it to be applied to lathes with driven tools, long overhang applications or instances where reliable chip removal is required - even in deeper thread applications where the optional internal coolant (from M5) applies. Process stability is also assured for high feed processing and fewer cutter radius corrections are required to deliver time savings and stable, repeatable processes. As well as the cutter design and grade already mentioned, a broad product program and tool shank options ensure that it can be used universally. Areas of application include medical engineering, precision engineering, the aerospace sector as well as electronics and general mechanical engineering.
www.walter-tools.com
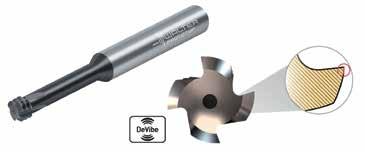
LESS INPUT. MORE OUTPUT.
MITSUBISHI LASER CUTTING
MITSUBISHI‘S 5 YEAR WARRANTY
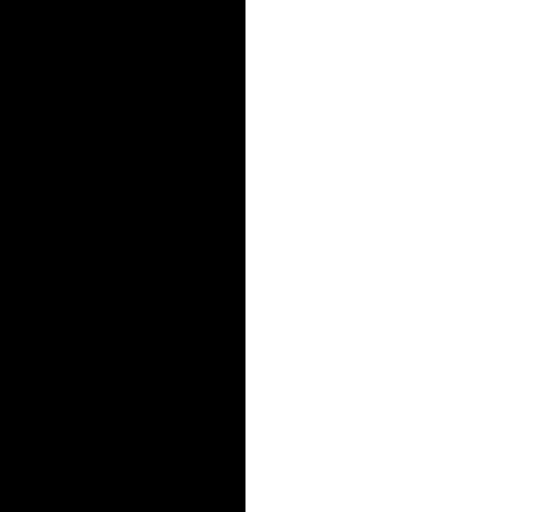
Conventional fiber laser processing systems
Running costs Profit
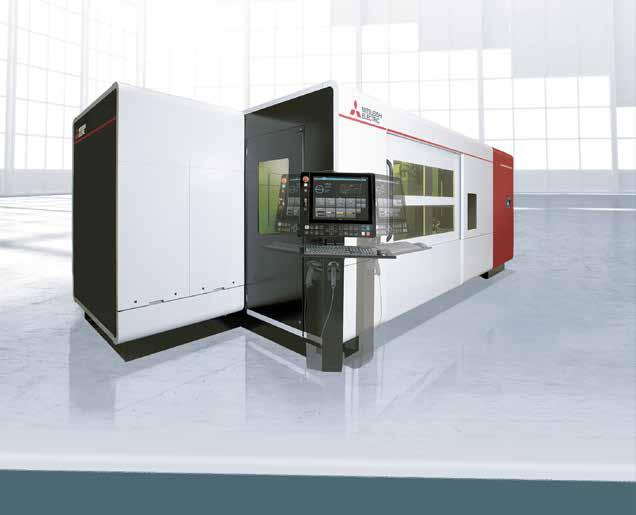
Productivity
Mitsubishi Electric’s GX-F ADVANCED Series
Running costs Profit
Productivity Real-Time Tracking of Electrical and Assist Gas Consumption
Custom Eco Modes
Advanced Gas Reduction (AGR-eco)
AGR-eco
Mitubishi‘s exclusive AGR-eco technology reduces Nitrogen consumption by up to 90%, drastically cutting costs while maintaining processing speeds.
AI Assist Cutting
Mitsubishi’s AI automatically fine-tunes the cut conditions during processing by reading multiple cutting-head sensors, ensuring peak performance with no additional training or operator involvement.
Mitsubishi Bar Code Scanner
The use of a unique job barcode and scanner allows anyone on the factory floor to begin job processing. Minimise additional costs associated with operator training and machine downtime with Mitsubishi.
CALL US TODAY: (03) 9115 1444
sales@kaizenmachinery.com.au www.kaizenmachinery.com.au
Kennametal introduces lightweight version of EV tooling solution
Kennametal has introduced its next-generation 3D-printed stator bore tool for the machining of aluminium engine housings for electric vehicles.
This latest version of the tool features a newly designed arm structure, a larger centre tube made of carbon fibre, and a further weight reduction of more than 20% over the original design. The complex tool is capable of machining three large diameters in just one operation, saving set-up time and machining time for automotive component manufacturers and delivering the highest accuracy and surface qualities. The newly redesigned tool recently won MM MaschinenMarkt’s Best of Industry Award in the Production and Manufacturing category based on votes by readers and industry experts. “As our automotive customers expand their offerings of hybrid and electric vehicles, we continue to respond to their need for lighter weight tooling solutions,” says Ingo Grillenberger, Product Manager at Kennametal. “By leveraging advanced manufacturing techniques like 3D printing, we’ve reduced weight a further 20% over the firstgeneration tool, while improving chip control and increasing tool rigidity—innovations that help our customers machine faster and more efficiently.” Machining three diameters in one operation, the stator bore tool ensures the alignment and concentricity of the machined surfaces while reducing the cycle time significantly. The lightweight 3D-printed combination tool enables a faster tool change and spin-up even on less powerful machines. The surface specifications and component tolerances are achieved without constraints. Hassle-free chip removal is ensured by means of airfoil-shaped arms that are through-coolant-featured to ensure precise and powerful coolant supply to the cutting edges and guide pads. This would be difficult or impossible to economically produce with traditional manufacturing, but 3D printing enables even such complex internal features. Additionally, the Kennametal RIQ reaming system features easy diameter adjustment and a trouble-free setup of new inserts.
www.kennametal.com
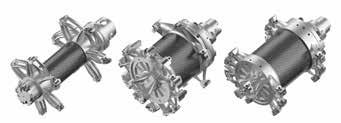
OMAX unveils OptiMAX, its most advanced waterjet ever
OMAX has introduced the OptiMAX, a new generation of waterjet designed to quickly turn prints into parts while relying less on highly experienced operators.
The OptiMAX is OMAX’s most advanced waterjet ever. The culmination of three decades of OMAX engineering expertise and real-world operator experience, it is designed for manufacturers in need of a versatile, easy-to-use cutting system. It offers OMAX’s intuitive software for optimised cutting capability and power, along with improved automation to maximise uptime. Companies can complete a greater range of work, more efficiently, and deliver finished products faster. New and improved features include: • IntelliMAX premium software, designed for incredible ease of use and operation quickly following installation.
Incorporating decades of proprietary waterjet cutting models, no other system can consistently produce parts as rapidly or capably. • IntelliVISOR console with key metrics to optimise operations and complete system monitoring to avoid unplanned downtime. • EnduroMAX pump that automatically sets the correct pressure and minimises fluctuations to improve component life, while offering the most efficient waterjet pump technology in the market. • IntelliTRAX drive system with advanced motion control for further increased system robustness and reliability. Requires virtually no maintenance compared to more conventional ball screw and rack and pinon drive systems. • New garnet delivery system to further minimise downtime. Combined with an optional Tilt-A-JET taper compensation head, the new OptiMAX is the most accurate system on the market. In addition, it provides advanced optional usability features such as water level control, under bridge lighting, and a machine status indicator, along with fast, accurate, and efficient cutting. “The OptiMAX represents the pinnacle in abrasive waterjet cutting,” says Arion Vandergon, Waterjet Product Marketing Manager. “It builds upon everything OMAX has learned during the past three decades to deliver the most capable and efficient waterjet cutting system available today, so our customers are able to easily achieve optimal cutting outcomes.” All OptiMAX products include comprehensive after-sales service, unlimited free training, and software upgrades, as well as a host of efficiency centred resources to maximise uptime and keep customers cutting. www.omax.com
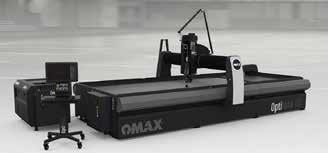
BOGE: Refrigerant compressed air dryer with sustainable, efficient, smart operation
The new refrigerant dryers from BOGE’s DS-2 series are more environmentally friendly than their predecessors, with refrigerant R 513 A as standard, which has much lower global warming potential than the refrigerants previously used.
However it is not just their remarkably low CO2 footprint that gives the new refrigerant dryers the edge; they also offer economic advantages. The smart control perfectly adjusts to the actual demand and reduces power consumption at a constant pressure dew point. Other components also ensure efficient operation. Economical in every detail, BOGE’s new DS-2 refrigerant compressed air dryers feature a smart control that automatically switches off the cooling compressor at partial load as soon as the required dew point has been reached. The cooling temperature is stored in the heat exchanger. This cold reserve cools the incoming compressed air until the dew point rises again. The cooling compressor only starts up again to maintain the required temperature level, and thus only begins consuming energy at this point. This principle allows energy savings of up to 79% compared to a dryer in continuous operation. The new frequency-controlled fan ensures a stable condensation pressure and reduces energy consumption by up to 25%. Furthermore, the patented design of the heat exchanger combined with low differential pressures and a low refrigerant requirement results in lower power consumption. The high-efficiency components reduce pressure losses to a minimum, which prevents over-compression. The new refrigerant compressed air dryers are highly environmentally friendly. With a GWP (Global Warming Potential) of 573, the new devices exceed the requirements of F-Gas Regulation EU 517/2014, which stipulate a significant reduction in emissions of fluorinated greenhouse gases (F-gases) by 2030 to protect the environment. Furthermore, the models of the DS series require a very small amount of refrigerant to begin with. Moreover, thanks to the hermetically sealed refrigerant circuit and a CO2-equivalent less than 10 tons, the entire series is exempt from the leak tightness test stipulated in the F-Gas Regulation. Therefore users save the costs of testing by certified refrigeration technicians. Using refrigerant R 513 A results in a better eco and cost balance with maximum supply reliability. The new control further reduces the consumption and costs of BOGE’s refrigerant compressed air dryer. In this way the control integrated as standard allows perfect adjustment to real operating conditions. It responds to temperature fluctuations immediately, which minimises power consumption. The smart control also offers convenient, intuitive operation via a high-quality 11cm touchscreen. It can even be easily incorporated into an existing infrastructure thanks to various interfaces. Communication takes place by Modbus RTU, USB ports or optionally by Modbus TCP/IP. Other new components such as electronic hot gas bypass valves, in conjunction with the installed scroll compressors, ensure efficient drying and reliable operation. www.boge.com.au
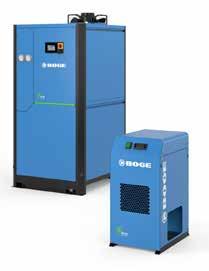
WIDIA introduces its next generation in versatile end milling
WIDIA has announced the launch of the WCE solid end milling platform, delivering affordable performance and reliability for small to medium machine shops.
The initial release of the WCE platform features WCE4, a fourflute geometry which combines advanced, high-performance features with a brand new, versatile grade offered at a highly competitive price. “With its new design, the WCE4 delivers the next generation of versatile end mills to help our customers be more productive and efficient,” said Tamir Sherif, Solid End Milling Global Portfolio Manager at WIDIA. “The WCE4 is an attractively priced tool for small-to-medium shop floors where reliability and consistent tool life are high priorities.” Two key features of the tool are its asymmetrical index and variable helix. The combination of the two reduce vibrations and enable heavy cuts, while the new grade, WU20PE, enables versatility on steel, stainless steel and cast-iron applications. These design features, coupled with the four-flute geometry, deliver an end mill with reliable performance and application versatility – even in demanding operations such as full slots and heavy cuts. The WCE platform includes four-flute, square-end and ball nose end mills with both straight and Weldon shanks and is available in both metric and inch dimensions. The WCE5 five-flute geometry will be released later in 2022. Orders for the WCE4 end mill, as well as other WIDIA metal cutting tooling, can be placed through WIDIA authorised distribution partners. www.widia.com
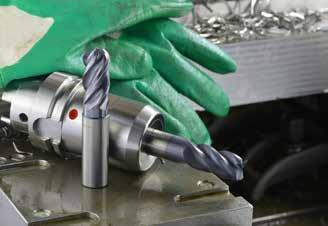
ViscoTec – High-precision uniform material coating of bore holes and internal threads
Combined with different ViscoTec dispensers as a material feeder, the Rotorspray vipro-SPIN enables volumedispensed application of adhesives or viscous greases in bore holes or internal threads.
The desired amount of material to be dispensed is applied in precisely defined quantities and with repeatable accuracy all round. The internal contours are wetted evenly and over a wide area. This is a non-contact application. Due to the conical inner geometry of the spinner head, it is possible to use the Rotorspray in both vertical and horizontal orientation. The vipro-SPIN is suitable, for example, for lubricants, greases and anaerobic or other adhesives – from low to high viscosity. A total of four different spin heads are available. For a flexible coating of interior cylindrical surfaces with a diameter of approximately 16mm to 50mm. A plug-in cable, available in different lengths, allows the Rotorspray to be easily integrated into various control unit systems. The vipro-SPIN is always required when adhesives or other viscous materials are introduced into bore holes, internal threads, or ball bearings. Another possible application is to make a shaft-hub connection. This is of particular interest, for example, in automotive engineering, engine construction or general industries, such as vacuum cleaner manufacturing. A volume-dispensed application is possible with the Rotorspray. This means that the volume can be precisely defined via the dispenser, and the layer thickness of the material application is continuously uniform. Over or under-dispensing is avoided by using a volumetric dispensing system instead of time-pressure systems. This is an advantage over the competition because the dispensing quantity cannot be precisely defined when using ie: simple outlet valves and pressure vessels. The ability to set and spray different volumes on one component offers a further advantage. For example, in an internal combustion engine, there are many bearings and bore holes on which blind caps are placed. These bearings and bore holes are of different sizes and therefore require different dispensing volumes. With the vipro-SPIN, the desired volume for each bore hole or joint can be precisely set and, if necessary, even changed during the process. This is easily set via the dispensing control. In this way, it is also possible to monitor whether and which quantity is being dispensed. In addition to single-component materials, the Rotorspray can even be used to spray two-component materials if required. The adhesive system or other two-component materials are fed mixed to the vipro-SPIN and applied by it to the component. Simple and fast disassembly of the spinner head or the dispenser itself allows uncomplicated cleaning of the components. Martin Höpfinger, Product Manager at ViscoTec, says: “The viproSPIN is an excellent addition to ViscoTec’s product portfolio. It offers an extra solution and enables dispensing and material coating for internal geometries. In combination with a ViscoTec dispenser, this results in another customer-friendly dispensing system from a single source.” www.viscotec-asia.com
● Beautiful Quality Spot Welds ● Eliminate Distortion & Misalignment ● Minimise Sanding & Grinding ● Reduce Setup & Process Time ● Achieve Weld Position Accuracy ● No Burn on Stainless Steel Welds ● “Easy Setting” Touch Screen Control ● Select Material Type ● Select Material Thickness ● Start Welding with Confidence
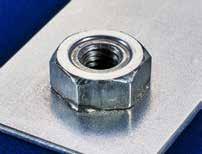
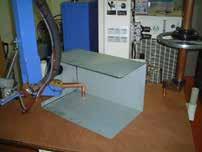
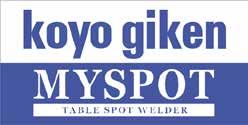

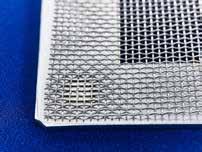

Models to Suit most Applications including Aluminium
Manufactured in Japan by Koyo Giken Co., Ltd MySpot® is produced in a variety of sizes and configurations, including pedestal style. Please visit www.koyogiken.co.jp/en/ for detailed information & latest technology Jim’s Machines and Accessories Authorised Sales & Service Agents Australia and New Zealand Call: +61(0) 414 646 212 Mail: info@jimsmachines.com.au
Hyster’s UT Series – Driver comfort and control lift productivity
Materials handling equipment specialist Hyster is expanding its UT Series with the introduction of its H5.0-7.0UT range of 5-7t forklifts, designed for optimum driver comfort and control.
The new forklifts follow on from the recent launch of the 4-5t range, with the additional lifting capacity for loading and unloading tasks involving heavier goods. “With the new forklifts, Hyster designers and engineers literally put themselves in the driver’s seat,” says Mark Chaffey, Hyster Area Business Director, Pacific. “For drivers to be productive and safe, they need to be confident in their equipment – and the equipment has to be designed to respond to diverse site conditions, with the features that global experience tells us are the driver’s choice. “The result was a robust and quality engineered forklift, designed to be the ideal solution to meet less frequent materials handling needs, while still offering the outstanding performance and service backup that Hyster is known for globally. Through our global network of authorised dealers, Hyster offers expert local service, spare parts availability and rapid response times, to keep industries moving with minimal downtime or delay.” Forklift drivers that are more relaxed, and experience less discomfort, tend to perform better and stay safer while on the job, so driver comfort was one of the top priorities in the design of the new Hyster UT Series 5-7t forklifts. Stand-out features include: • A full suspension seat, with an operator presence system fitted as standard, to provide comfort, right from the outset. • A low step height, with convenient step placing to suit a variety of heights, to provide easy access to the truck. • A high-strength overhead guard, made from profiled steel, to enhance operator protection. • A small 300mm steering wheel, with eight degrees of adjustment to suit different operators, and to allow for good maneuverability when working in confined spaces. • Wide mast view, which delivers excellent visibility of the load, as well as the operator’s forward view, thereby optimising safety and productivity. “Whether it’s loading or unloading a truck, or moving goods in a retail application, the new UT Series 5-7t forklifts provide the comfort to maximise productivity, efficiency and safety,” says Chaffey. “Another major focus for the new forklift range is low total cost of ownership, with a large range of spare parts that are interchangeable across the broader UT Series, and large access areas for easy servicing. The Hyster dealer and service network extends across Australia, New Zealand, Thailand, Malaysia, Vietnam, Indonesia, Singapore, Philippines, Korea and Taiwan. Chaffey adds: “Hyster authorised dealers are backed by the global Hyster-Yale group with a full product line of lift trucks in operation across hundreds of industries worldwide. Local dealers will carry strong supplies of spare parts and will be ready to provide expert service to local industries.”
www.hyster-yale.com
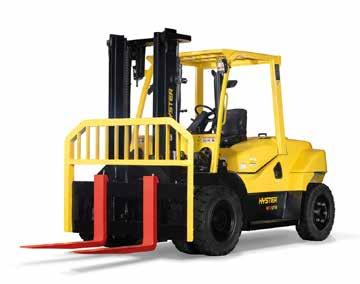
Mitsubishi Electric: SIMPLE graphic operation terminals facilitate remote access
Mitsubishi Electric has launched two additional Graphic Operation Terminals (GOTs) to its GOT SIMPLE Series lineup.
The 25cm and 18cm widescreen models, which support virtual network computing (VNC), can be used as VNC servers enabling remote access from offices or other remote locations where field engineers may find themselves. This feature will help meet customers’ needs for improved work efficiencies when performing monitoring and maintenance in factories, buildings, utilities and other automation applications. Another key feature of the new GOT models is a 1.5-times increase in onboard memory capacity to 15MB, making it easier to save more screen designs. Furthermore, by using an SDHC memory card, operation logs can be recorded in chronological order to achieve enhanced traceability. This can be useful for validating operations as well as troubleshooting when identifying misoperation or the potential root causes of problems. In addition, these latest models in the GOT SIMPLE Series now support outline fonts, offering clearer visibility of text on the screen by smoothing out edges of textual characters. This increased clarity can help prevent misreading but can also aid reading at a distance. Since communication interfaces are also another key factor for users selecting GOTs, Mitsubishi Electric has enhanced the builtin interfaces for these new models. In addition to the standard GOT SIMPLE Series interfaces of Ethernet, RS-232 and RS422 the new units also offer RS-485 support. This facilitates the connect of a wider variety of devices such as temperature controllers and MODBUS peripherals, making it easier for users to implement connected-digital manufacturing strategies in their operations. www.mitsubishielectric.com.au
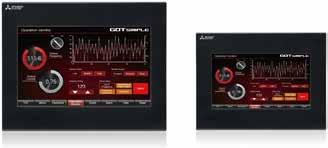
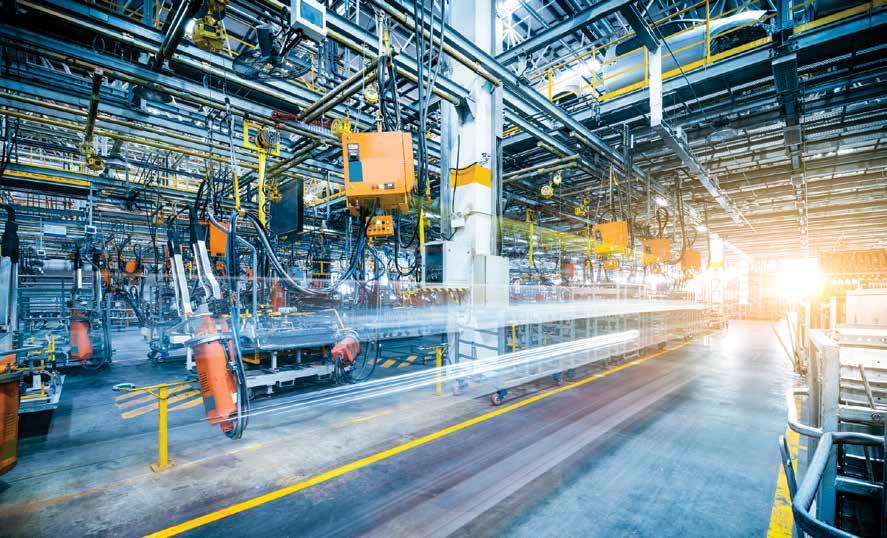
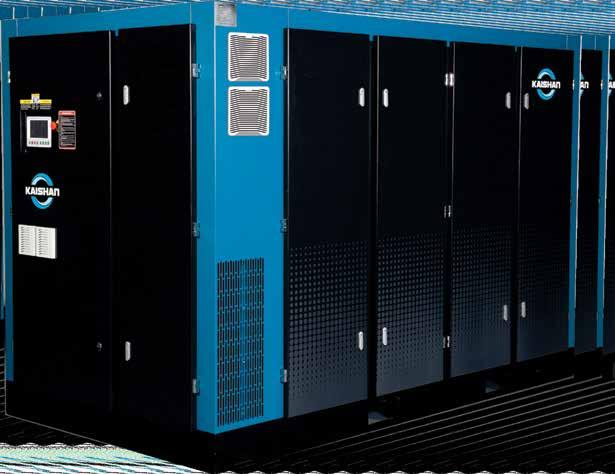