
6 minute read
Applied’s expanded Yawei range and new Fanuci welder
from AMT APR/MAY 2022
by AMTIL
Applied rolls out expanded Yawei range and innovative new Fanuci welder
For over 15 years, Applied Machinery has been supplying Yawei precision sheetmetal machinery to local manufacturers and job shops, maximising their productivity, boosting quality and broadening their capabilities.
“Increased sales growth and demand across Australia has resulted in us steadily expanding the Yawei range, which today includes CNC fibre lasers, tube lasers, pressbrakes, turret punch presses, guillotines and smart-factory automation solutions,” said Applied’s Sales and Marketing Manager, Daniel Fisher. “The value for money and performance aspect is why so many companies have opted for Yawei. The competitive price of Yawei machines has enabled many local manufacturers to bring their fabrication work back in-house. It has also allowed job shops to expand their range of services and capabilities enabling them to secure new business opportunities.” Two new models recently introduced further add to the impressive line-up: a laser punch combination and a panel folder.
The new HPML Laser Punch Combination combines the forming capabilities of a turret punch press with the flexibility of a fibre laser cutter - all in the one machine. The machine features class-leading components which are a hallmark of all Yawei machines; these include a Siemens 840D controller, IPG laser source and Precitec auto-focus cutting head.
“Forget tedious slow punching,” said Fisher. “Companies can now boost their productivity with this versatile two-in-one machine. For fabricators that want to take their manufacturing to the next level, the new laser punch combination will allow them to do just that.” The other new Yawei model is the innovative new FB Series CNC Panel Folder, which offers fast speed, high efficiency panel folding with automation options available to maximise productivity. “These two new models will further cement Yawei’s reputation for providing Australian manufacturers with high quality precision sheetmetal machinery designed to maximise their productivity, boost quality and broaden their capabilities,” Fisher added. In addition to the two new Yaweis, the recently launched Fanuci handheld fibre laser welder allows for easier, smoother and quicker welding. Handheld laser-welding machines are increasing in popularity for the many benefits they offer compared to conventional welding. The Fanuci fibre laser welder provides high-speed welding coupled with a far superior, smoother weld line. It features low heat input, small deformation, large penetration depth and good repeatability. The unit offers low energy consumption and is virtually maintenance free.
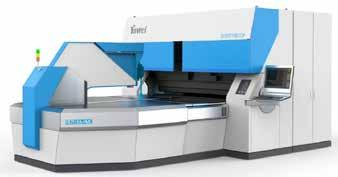
Fanuci’s wobble welding technology ensures that operators can achieve a consistent and aesthetically pleasing weld. The quality of the weld presentation can eliminate the need to clean-up the weld with a secondary process, which in turns saves time and money. Fanuci fibre laser welders are all manufactured to CE/TUV standards. The range includes 1,000W, 1,500W and 2,000W models. “Given its capabilities, build quality and unique features, we expect to find a ready-made market for the Fanuci fibre laser welder in Australia,” said Fisher. “Companies can now take their welding to the next level with a far superior weld, coupled with increased productivity and reduced operating costs.” While the new products add to the impressive rage of machines that Applied Machinery distributes, it is the expert advice, service backup and support provided by Fisher and his team that has won them many new customers over the last few years. “Our number one priority is ensuring that our customers across the country get the machinery they need, with the support they expect,” Fisher said. “We view ongoing service, training and support as critical to ensuring our customers can extract maximum return from their machinery investment. “Unlike some suppliers who are here one day and gone the next, we’re here for the long term. With nearly 30 years’ experience and thousands of satisfied customers across the country we’re a true machinery partner.” The growing list of satisfied customers is evidenced by the portfolio of well-known engineering companies across Australia that have chosen to partner with Applied. These include JC Butko Engineering, Eilbeck Cranes, Wildcat Industries and Alliance Metal Solutions. “One of the outcomes of the COVID pandemic is recognition of the importance of nurturing and assisting local manufacturing,” Fisher concluded. “We’re proud to be able to play our role in supporting Australian manufacturers with high quality, value for money products that will boost their productivity and provide them with a competitive advantage in the marketplace.”
www.appliedmachinery.com.au
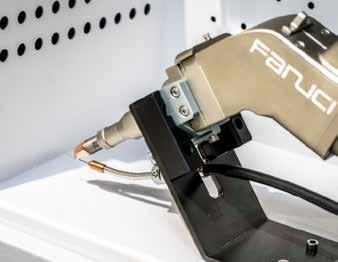
Speedpanel embraces Industry 4.0 to streamline steel panel manufacturing
The Innovative Manufacturing Cooperative Research Centre (IMCRC) grants cutting-edge fire-rated and acoustic panel system manufacturer Speedpanel and Deakin University $100K in funding to refine steel panel manufacturing process.
During the 10-month research collaboration, the project team will use new steel forming and joining solutions to further enhance Speedpanel’s production technology, with a focus on reducing waste and optimising and strengthening panel design. This research will also support Speedpanel’s high-volume production output and enable the business to have a more refined platform for continued expansion locally and abroad. Commenting on the project, Lindsay Evans, Speedpanel’s Sales and Operations Manager, said the IMCRC activate funding would assist Speedpanel to further revolutionise the way it manufactures its fire-rated and acoustic systems. “By streamlining manufacturing processes with innovative joining solutions and advanced techniques for material monitoring and process control, we’ll be able to evolve our product offering and bring a more environmentally friendly and sustainable panel system to market,” said Evans. “Tapping into Deakin’s expertise in material analysis and forming process control will enable us to assess and monitor material properties and key production parameters throughout the process to enhance process efficiency, enabling better quality control and reducing waste.” Matthias Weiss, Senior Research Fellow at Deakin University, highlighted the importance of connecting with the manufacturing industry on research and development (R&D) projects. “Manufacturing large hollow sections of steel represents a major challenge for industry. With Speedpanel and IMCRC, Deakin University is helping to solve this problem by providing extensive support in material parameter monitoring and process control solution development,” said Weiss. “We’re also taking the findings from a previous Deakin University industry collaboration which has established a new and structurally optimised wall panel design and applying them to adapt Speedpanel’s cutting-edge system.” Dr Matthew Young, IMCRC’s Manufacturing Innovation Manager, said IMCRC was delighted to be co-funding the R&D required to advance Speedpanel’s manufacturing process to improve design, manufacturability, and performance characteristics of the wall system to help expand markets and profitability. “Speedpanel has been a market leader in conventional panel manufacturing methods for the past 20 years,” said Young. “In only 10 months, this research collaboration has the potential to deliver transformational change to the business and pave the way for future product developments. Supporting small to medium manufacturing enterprises (SMEs) like Speedpanel to embrace new technologies and the application of Industry 4.0 remains central to creating an Australian manufacturing sector that is thriving and globally relevant.”
www.imcrc.org www.deakin.edu.au www.speedpanel.com.au
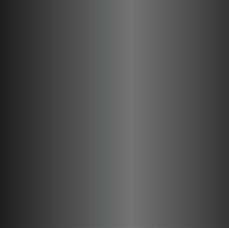
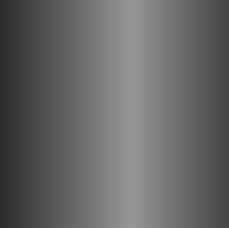
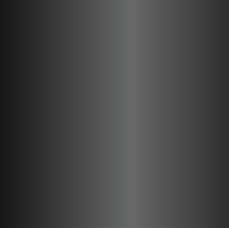
Your Specialist in New CNC Machines, Service & Support
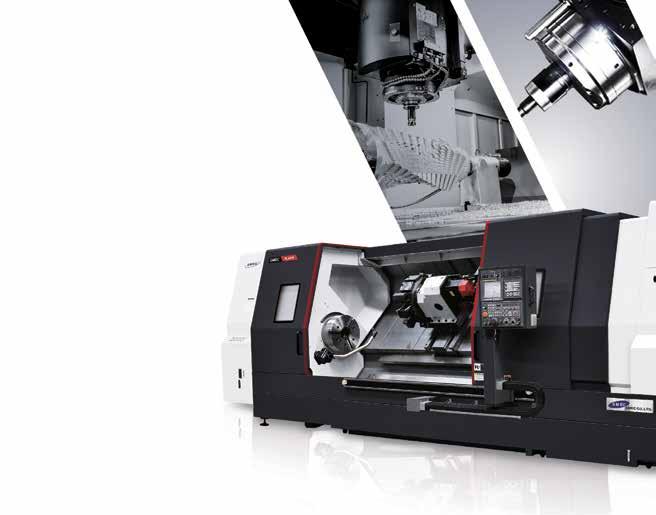
Call us today for a quote 1300 252 262
Proud Partners
I
bjcmachinetools.com.au I BJCMachinetools I BJCMachinetools