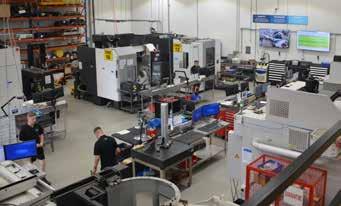
4 minute read
Real-time productivity for APT with Okuma Connect
from AMT APR/MAY 2022
by AMTIL
Real-time machine productivity for APT with Okuma Connect Plan
In Melbourne’s south-eastern suburbs, advanced precision engineering company Australian Precision Technologies (APT) is achieving amazing real-time machine productivity thanks to Okuma’s latest Connect Plan Machine Monitoring.
As part of its continuous improvement strategy, this qualityaccredited, AS9100 rev D (Aviation, Space & Defence) and ISO 9001 company has introduced the Okuma Connect Plan, connected to 18 CNC machines to monitor the production process, efficiency and performance of all the machines in real time with immediate visual information on centralised screens. The Okuma Connect Plan is a system to increase process efficiency, collecting machine tool data and presenting it in a veryeasy-to-understand format to optimise machine operations. This A1 algorithm tool is not just for Okuma machines but any brand of machine tool or equipment. The Okuma Connect Plan data collection system features a simple visual aid, consisting of: Red – machine is down; Yellow – machine is idle; and Green – machine is running. It learns how you use your machine tool information to predict the ever-elusive yellow machine status. It utilises the system variables, parameters, machine specs and other tool information to automatically determine why a machine is sitting idle. Once corrected, it will spot that and similar scenarios during operations in the future. “This modern-day tool, Okuma Connect Plan, provides a hightech solution for customers with technological advantages with the ability to connect to different machines, showing which machine is running, review schedules and fully optimise production,” said Mark Richards, Okuma Australia Branch Manager for Victoria and Tasmania. “It provides the operational history of every machine, their exact productivity, and optimises maintenance schedules. Okuma’s Connect Plan is a system that provides analytics for improved utilisation by connecting machine tools and visual control of factory operation results and machining records with up to 30 machines per licence.” Okuma Connect Plan is promoted with three key advantages such as Connect, Visualise and Improve; planned machine historical data; preventative maintenance scheduling and analyse, all providing exact productivity of the factory. APT Managing Director Richard Weinzierl commented: “Okuma’s Connect Plan is APT’s way of measuring the efficiency of our production processes and provides my company with actionable data to measure machine performance. Okuma Connect Plan is recording in real time machine productivity. From the easy-to-read data, Connect visually records spindle uptime/downtime in an easyto-read format. Machine utilisation can quickly be increased when we know what to look for and a system such as this for measuring data so we can adjust processes. “With this information also available on my smart iPhone and other devices, I have become almost addicted as I can view what is happening in real time – anytime and anywhere in the world. Importantly our machine operators are watching and monitoring the colour-coded centralised screen all the time, reviewing their output in parts per month to maximise efficiency.” APT is currently celebrating its 30th anniversary and this private family business, which started from small beginnings, is today employing 30 highly skilled operators and four apprentices with some of the most advanced precision plant and machinery in operation. “State and Federal Government support for manufacturing has helped the company enormously, enabling us to invest in the latest precision machines to produce internationally competitive components and assemblies, an important factor as we see more
Australian Precision Technologies (APT) has introduced the Okuma Connect Plan connected to 18 CNC machines at its factory in Berwick.
Australian Precision Technologies (APT) Managing Director Richard Weinzierl (second from right) with members of the APT team.
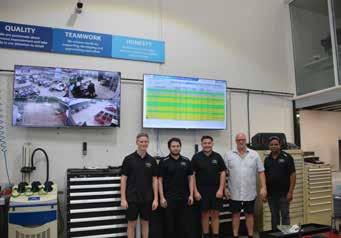
onshoring of products occurring for Australian manufacturers,” commented Weinzierl. “This has been a critical factor in the development of the company, which five years ago participated in a key Centre for Defence seminar providing guidelines and strategies on what we needed to do for the future, resulting today in more than 80% of our company’s production in defence contracts.” As an expert in its field, APT was inducted into the Victorian Manufacturing Hall of Fame in 2014, the company was a finalist in the Defence Industry Awards in 2019 and was awarded Casey Business of the Year in 2021. Central to APT’s continuous improvement development is its care for its people and the strong culture of involvement, resulting in staff engagement in excess of 85%, with values set and acted on by the company including Vision, Mission, Quality, Teamwork and Honesty. “Okuma is leading the way in the Smart Factory development in manufacturing with up-to-the-minute modern day tools such as Okuma Connect Plan,” said Okuma Australia’s Managing Director Dean McCarroll. “We are currently in the process of installing Okuma Connect Plan in a number of other companies and we look forward to watching APT and others continue to grow and expand production with the introduction of further efficiencies with the benefit of the Okuma Connect Plan.”