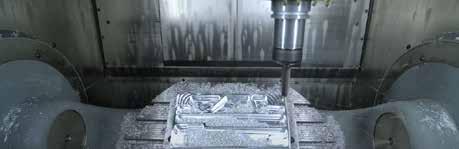
4 minute read
Multi-axis roughing extends tool life
from AMT APR/MAY 2022
by AMTIL
Multi-axis roughing extends tool life and speeds production success
For decades, Seco has encouraged customers to optimise chip thickness, feeds and speeds, and heat dissipation during the machining process. The increasing sophistication of the technologies that support machining applications has helped make it easier for shops to pursue these approaches consistently.
When CAD/CAM programming still involved manual creation of every line of code, the complex process limited machining strategies considerably. CAD/CAM systems couldn’t produce corners or automate complex moves, and no programmer had time to write thousands of lines of code to produce the small stepovers involved in dynamic milling. Now, the CAD/CAM universe has caught up with the message that Seco has been communicating for many years: programming must consider all aspects of the tool and the workpiece to formulate an approach that optimises both. Today’s CAD/CAM systems can implement the full range of these strategies, achieving the capabilities that Seco always builds into its tools and making it easy to automate an optimised approach to every workpiece. One of the most important of those CAD/ CAM developments gives shops the ability to control table movement so they can produce precise rounded surfaces. This multi-axis version of dynamic milling – also known as optimised roughing or adaptive milling – helps shops use Seco tools more efficiently. With this approach, not only can shops extend tool life, but they can do a better job of predicting it in advance. The strategy provides better control of cutting speeds, feeds and depth, as well as chip thickness. It also enables shops to reduce machining and programming time while they run tools evenly throughout a machining process. Multi-axis milling strategies
Five-axis adaptive milling helps reduce the heat build-up that results when a tool engages fully with workpiece material but the CAD/CAM program does not use the right types of tool paths to match the milling strategy. With new adaptive milling strategies, shops can take advantage of the connection between cutter engagement and diameter on the one hand and cutting speeds and feeds on the other. For example, when 2% of the cutter engages with the workpiece, cutting speed can increase by up to 80%, and when Ae rates reach 2% of cutter diameter, feed rates can climb by 50%. With new developments in CAD/CAM software, shops can leverage these relationships in ways that Seco always has understood but the technology could not accomplish. To showcase simultaneous five-axis roughing in NX CAM with tools optimised for use in aluminum, Seco recently assisted its partner IDEAL GRP to produce a thinwalled demonstration part. Similar to components often produced for use in aerospace or general engineering, this type of part typically becomes a short-run job that shops cannot create cost effectively through casting or forging. The menudriven, point-and-click automated solution from IDEAL GRP can reduce machining time by up to 60%, using large depths of cut and small radial stepovers to maintain constant chip thickness and material removal rate with minimised vibration and heat. The operation automatically finds the largest open region within the cut area and uses one of several cut patterns to produce short tool paths. Arc-shaped cutting movements extend the full width of the cut region with a small lift between cuts. The process also works smoothly over a free-form surface. Constant tool engagement maintains optimal cutting conditions and increases material removal rate. Although this is a roughing strategy, it yields better tool life – and produces results that come closer to finished shapes, with fewer operations and setups. Aluminum provides an extremely high level of heat conductivity, so much of the heat generated from machining processes – up to 95% – dissipates through chips. This limits the need for coolant in this type of roughing application and offers environmental benefits as a result. Shops gravitate toward coolant use because it does a great job of maintaining consistent workpiece temperature, clearing away chips and keeping the machine itself clean. However, coolant also causes hundreds of little temperature fluctuations during every minute of machining, and this triggers the development of small cracks that shorten tool life. The application in the IDEAL GRP demonstration used a harder aluminium that did not need coolant to avoid the tool-clogging chips that can form with very soft aluminium alloys. Solid and indexable SECO tools excel in aluminium
In this collaboration with IDEAL GRP, Seco used four tools, three of which were run without coolant. The machining process was begun with a Seco 97-series end mill, designed for face, side and copy milling. This initial roughing pass used very steep ramping angles that ran as high as 15°, combined with a 10%-20% radial stepover. Next, Seco ran an 8mm JH40 highperformance end mill to create pocketed areas. With two flutes, this end mill produces thicker chips. In this application, Seco used a 10%-20% radial stepover to avoid metal pickup on the tool. The same tool also performed spiral cutting to rough out large pocket areas and finish the profiles of pocket walls. The last two processes began with a 16mm JS534 ball nose end mill that finished the top surfaces of the part. Finally, a JS509 chamfer mill with 0.8mm tip engraved the IDEAL GRP and Seco logos into the part, using coolant to avoid clogging the tool. Throughout the demonstration, Seco showcased a match between tooling and material, with solid and indexable tools specifically made for use with aluminium. Shops can adapt Seco technologies to match not only the parts they create but the machine tools they use. Seco gives customers the flexibility to use a high-feed milling cutter in a fast machine or other options in a bigger, slower machine. Thus, shops can find multiple ways to accomplish the same task. With a broad cutting tool portfolio, Seco offers proven, successful selections for every need.