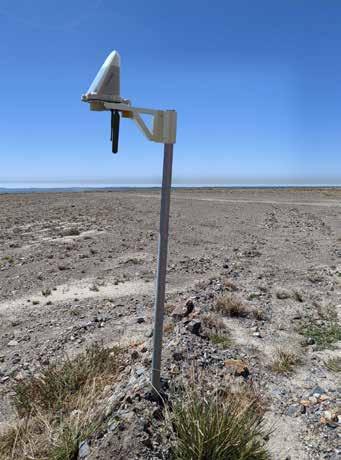
3 minute read
How Monitum future-proofed its business with Ind.4.0
from AMT APR/MAY 2022
by AMTIL
Geospatial data is a critical component of every construction project, reducing risk and improving efficiencies. But gathering this data is often costly and labour-intensive, something that Lee Hellen, MD of leading Australian automated monitoring business, Monitum, knows firsthand.
When working on a complex, high-risk surveying project in 2012, Hellen imagined the difference an affordable solution that automatically monitored displacement could make to industry. “As our sector advanced, we recognised the need to harness the Internet of Things (IoT), cloud computing and artificial intelligence to provide precise and accurate insights to manage risks around buildings and structures,” he said. And in 2019, Monitum, in partnership with Queensland University of Technology (QUT), embarked on a $4.5m collaborative research project to bring such a product to market. The three-year project, supported by $875,000 in funding from the Innovative Manufacturing Cooperative Research Centre (IMCRC), has developed a cost-effective IoT solution using low-medium-end Global Navigation Satellite System (GNSS) sensors and low-power wide-area networks (LPWAN). According to Hellen, Monitum’s Australian-made product will make precise GNSS positioning accessible and affordable, with many applications across industries such as infrastructure, transport and mining. “We’ve created a fully-integrated smart device that is supported by a cloud processing and data analytics service. Together, they enable millimetre-precise deformation data to be obtained automatically, remotely and in near real-time,” he said. Central to delivering such an innovative outcome was the expertled research provided by QUT’s project team, headed up by Professor Yanming Feng. Hellen said that working closely with QUT researchers in GNSS, networks, data science and geotechnical engineering provided Monitum with greater capacity, depth of thought and understanding and the ability to conduct cutting-edge geospatial research. The collaborative wins are demonstrated in the optimal manufacturing and data infrastructure design of the sensor and the adoption of state-of-the-art analytical techniques, including machine learning, to develop the monitoring service. Professor Feng said collaborating with Monitum had been a unique experience in applying QUT’s expertise, bolstered by mutual trust and the ability to communicate openly. “Because of our respectful working relationship, QUT and Monitum were able to effectively manage the inherent risks and multifaceted challenges posed by undertaking research,” he said. “Collaborating with smaller businesses like Monitum can increase efficiency within research and development (R&D) projects because you’re able to work directly with key stakeholders. In this instance, we were able to work together as one team, and the project outcome is a testament to the importance of this effective integration.” Raymond Johnson, Manager, Industry Engagement (Science and Engineering) at QUT, added that having strong ties to businesses like Monitum supported the development of new technologies and improved university-industry collaboration. “Throughout the collaboration, Monitum gave the QUT team the freedom to apply their knowledge and expertise as they saw fit to deliver mutually beneficial outcomes,” he said. “One of the major project outcomes for QUT is that the successful research findings have strengthened the university’s credibility within the geospatial sector. QUT now has a persuasive case study in geospatial science to demonstrate its capability, allowing the university to undertake more diversified research in IoT and positioning technologies.” As part of the project, Monitum engaged Brisbane-based electronics designer and manufacturer, Intellidesign, to apply the research findings to the design and production of the monitoring device. Commenting on the project, Matt Bromwich, Intellidesign’s CEO, said that collaborating with Monitum had been a rewarding process. “Monitum approached us with a well-proofed concept. By applying our mutual understanding of the market and technical requirements, we’ve collectively transformed Monitum’s concept into an innovative product ready for mass production,” he said. Hellen also identified IMCRC’s business model as key to supporting the fruitful research project, as it incentivised university-industry collaboration and drove co-investment. “By championing the project and being a hands-on advisor, IMCRC helped to formalise our idea, keep us committed to the innovation, and ensure we were able to reach mutually beneficial outcomes,” he said. “This enabled us to guarantee our supply chain and offer consumers an Australian-made product in a market that’s currently dominated by overseas competitors. “The project is an exemplar of how a small business with fantastic ideas, passion and drive can partner with university to transform its offering and create significant opportunities for Australia’s manufacturing sector. “And by embracing Industry 4.0 technologies, we’ve been able to future-proof our business,” Hellen concluded. Monitum will launch its new technology under the name of ‘Kurloo’ in 2022. www.monitum.com.au