
4 minute read
PENTAURA PAVILION
The Pentaura Pavilion, located at the open area of Escola de Turo can Mates, a local primary school in Sant Cugat del Valles in Barcelona is a shelter designed to be used as a roof for an outdoor classroom as well as a play area for the primary school kids. Inspired from the thin timber shells and the concept of origami, the Pentaura, a five legged corrugated shell was designed using grasshopper for the geometric variations parametrically, which was later analyzed using Karamba and Kiwi3d plug-ins for the structural analysis.
Design // Methodoloogy
Form-finding
The corrugated shell was inspired by the Miura pattern in origami. Due to the constraints of the brief, the shell spans 9m with a maximum height of 3m. The base mesh was relaxed using Kangaroo to get the initial mesh from which corrugations were made and optimized. An optimum gap of 20mm was left between the 15mm thick panels for aesthetics and flexible connections. Metal plates varying from 60° to 179° were used as connecting members with M8 bolts and T-nut spiders to have seamless connections. Five bases of 18mm ply, in three layers and hardwood joists were used to anchor the whole structure to the ground. A 1:10 model was made to study the assembly.
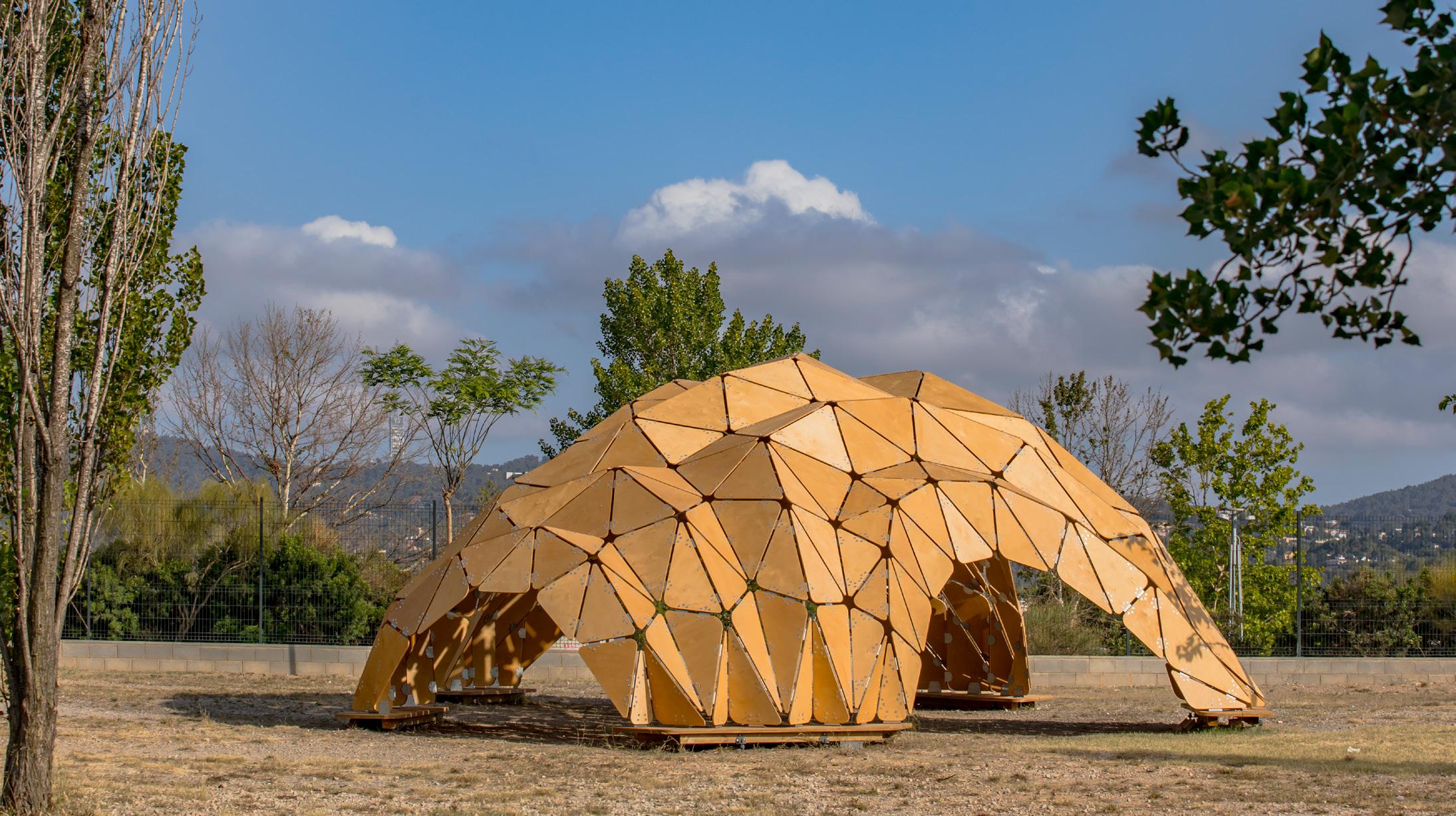
Methodology
As the project was being erected for a located school, there was a need to get the approval of the Town Hall of Sant Cugat, Barcleona. For this, the workflow included:
1. Graphic Documentation (planselevations-sections)
2. Bill of Quantity
3. Structural Documentation (as per Eurocode
Construction Stages
The construction process was split into three main stages, namely, Stage I // Prefabrication
Included processes such as fabrication of plywood panels, cutting-bending of the metal plates, ordering the bolts and spiders
Stage II // Off-site preparation
Done in the school workshop
Includes sanding, cleaning, painting varnish, drying and hammering spiders into the predrilled holes in the plywood panels
Stage III // On-site constuction
Site setting, anchoring bases to ground with spirafix, assembling clusters
Step I // building the 12 clusters 1
Step II // building the spine 2
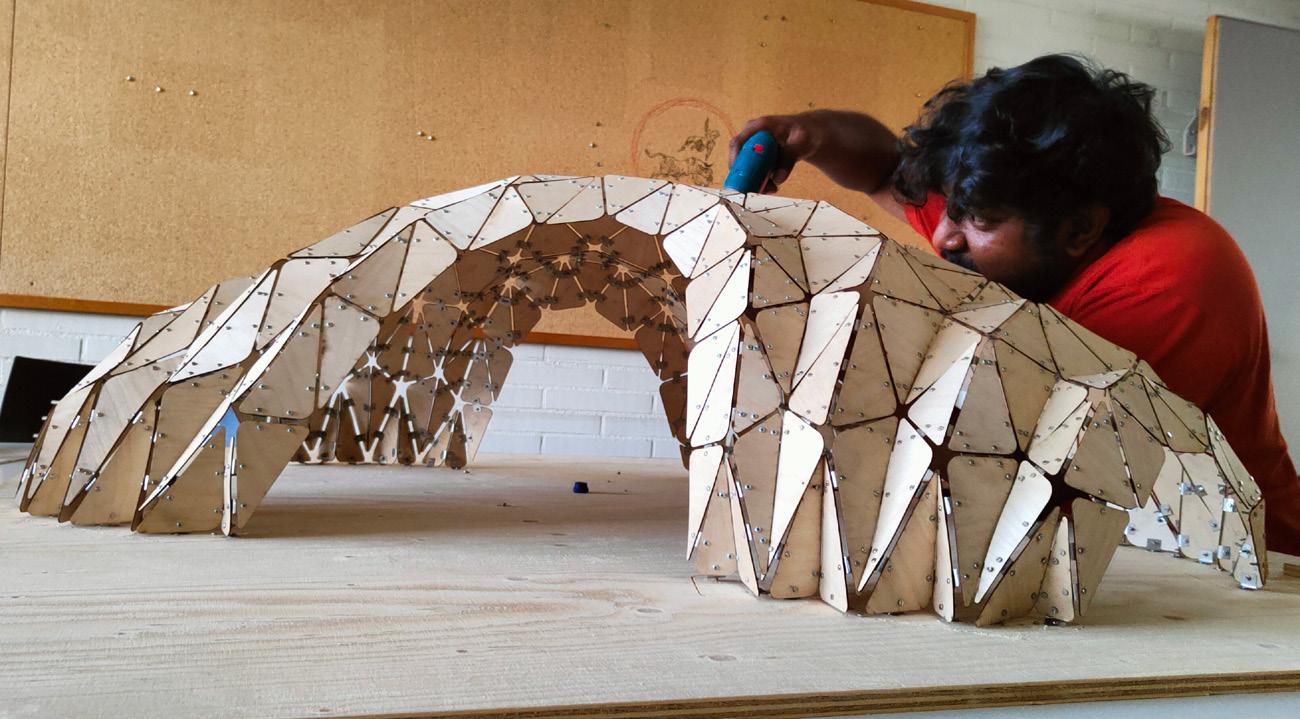

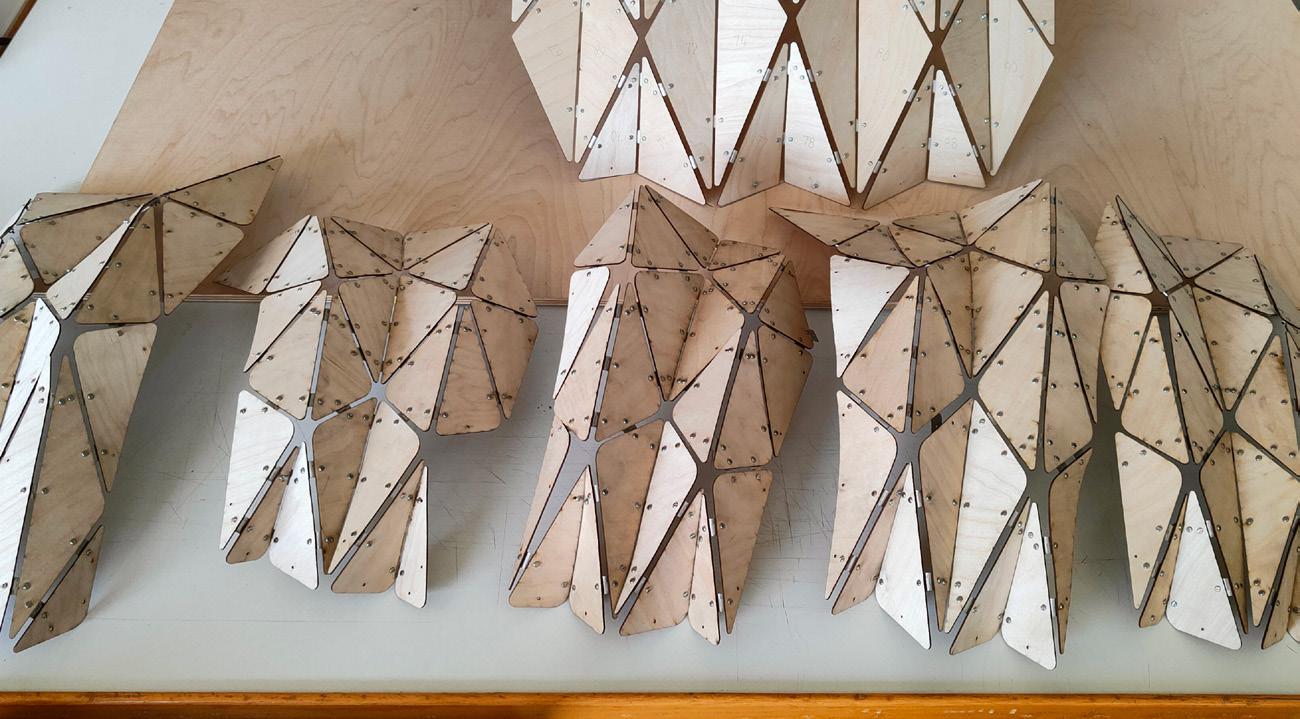
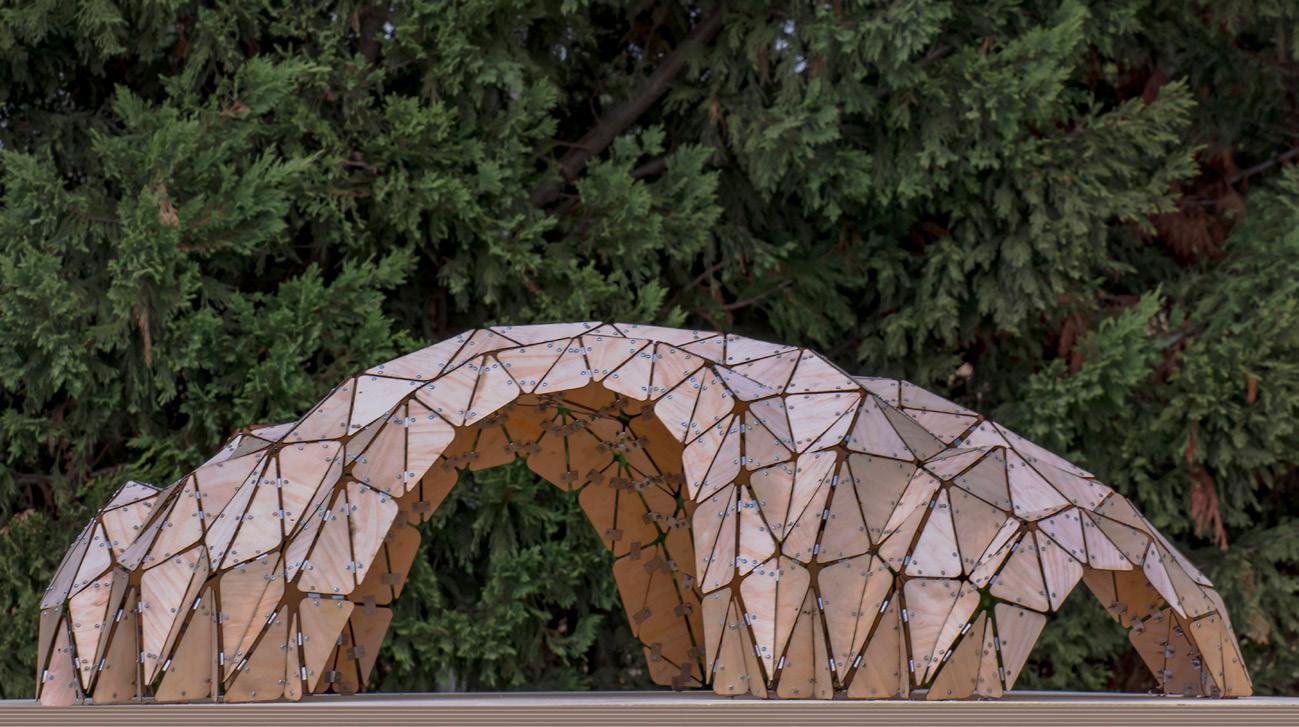
Step III // adding the remaining clusters 3
Model View // assembled model 4 structural analysis // various
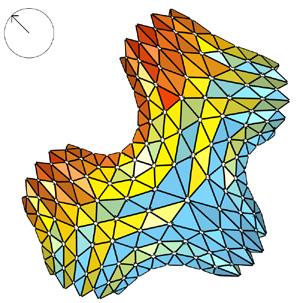
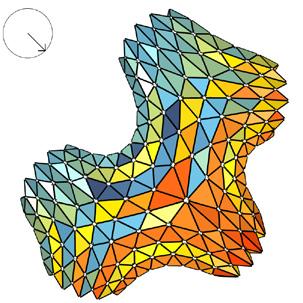
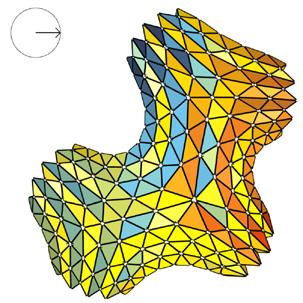
Structural Analysis

Brief
The structural analysis of the shelter was done in Karamba 3d. The different analysis done were:
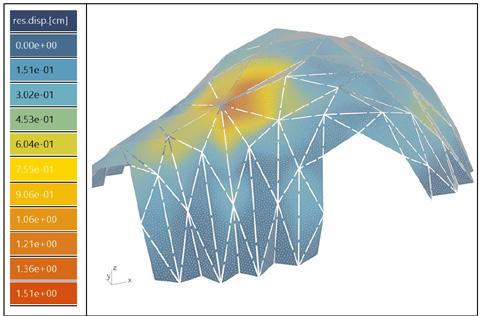
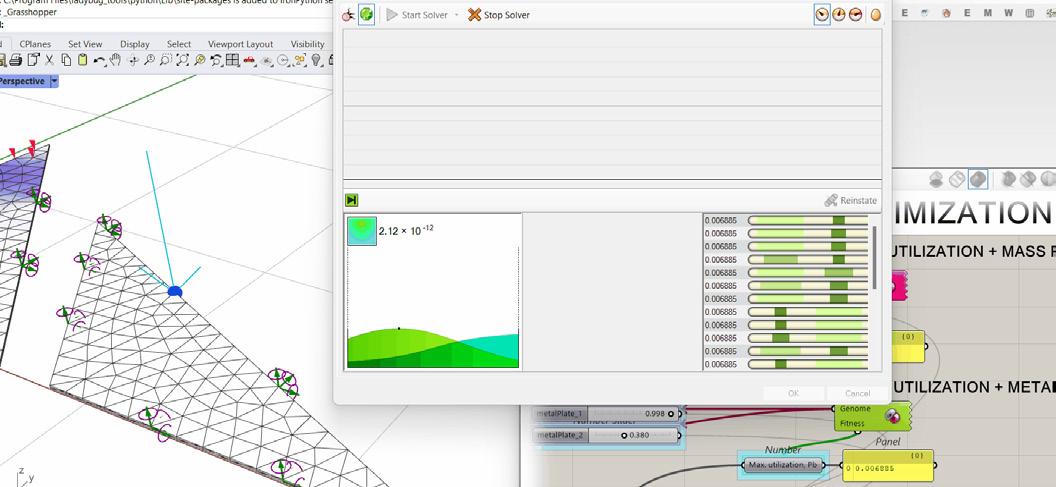
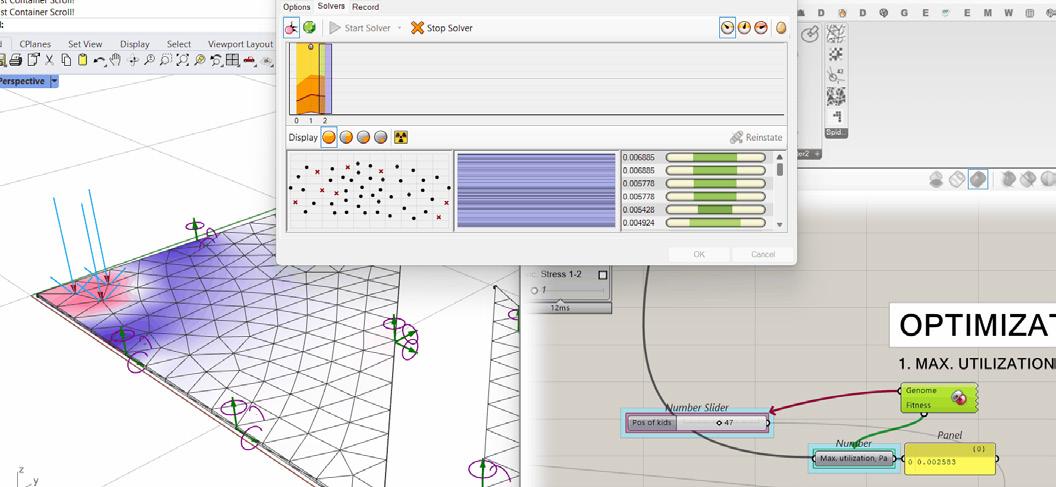
1. Displacement under different load types
2. Utilization

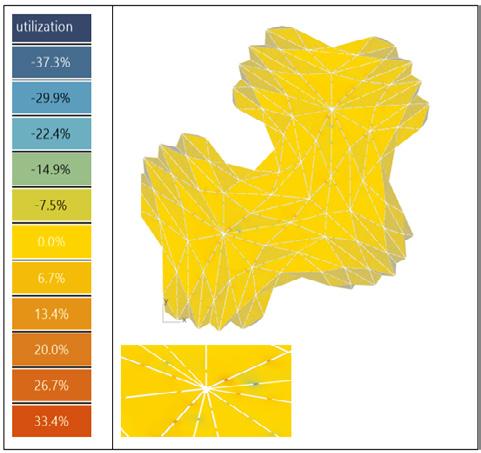
3. Stresses (tension and compression)
4. Cross-section optimization of the shell (with different thicknesses)
The factors and co-efficients were taken from the eurocodes, UNEEN 14080:2013 and CTE DBSE-M. Along with this material properties were considered to get accurate results.

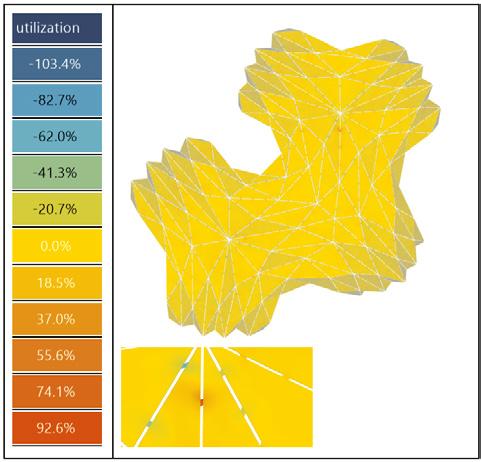
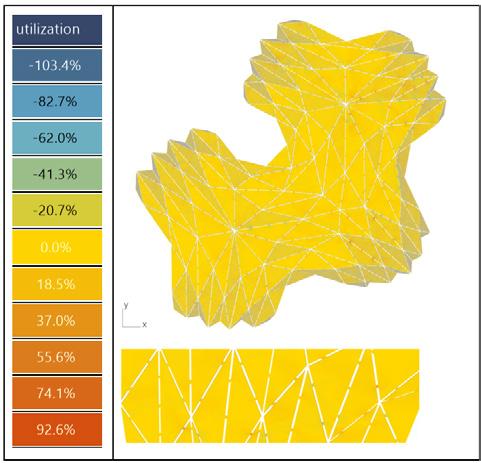
Material
Panels // 15mm thick birch plywood Base // 18mm thick birch plywood 50 x 50mm hardwood joists
Connections // Stainless Steel plates
Spirafix (anchors)
The plywood properties were taken from the Handbook of Finnish Plywood by UPM, namely, Elastic Limit = 225 MPa
Modulus of Elasticity, E = 210 GPa
Modulus of Rigidity, G = 81 GPa Poisson’s co-efficient, v = 0.3
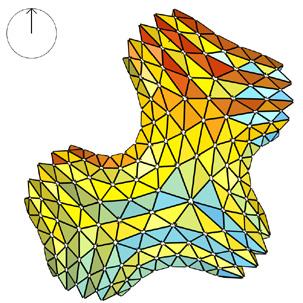

Thermal co-efficient, a = 2.10 Density, p = 680 kg/m³
Load and Combinations
The load types and their combinations were taken as per the Spanish guidelines, from the UNE-EN 14080:2013 and CTE DBSE-M.
The different load types are:
Dead load or gravity, G
Snow loads, Qs
Wind loads, Wx and Wy (Zone C with a base velocity of 29 m/s)
Asymmetrical loads, As Point loads, P (kids’ loads on climbing) galapagos optimization // position of metal plates
The load combinations included Ultimate Limit State (ULS) and Serviceability Limit State (SLS) combinations.
Day 01 // building base clusters 1
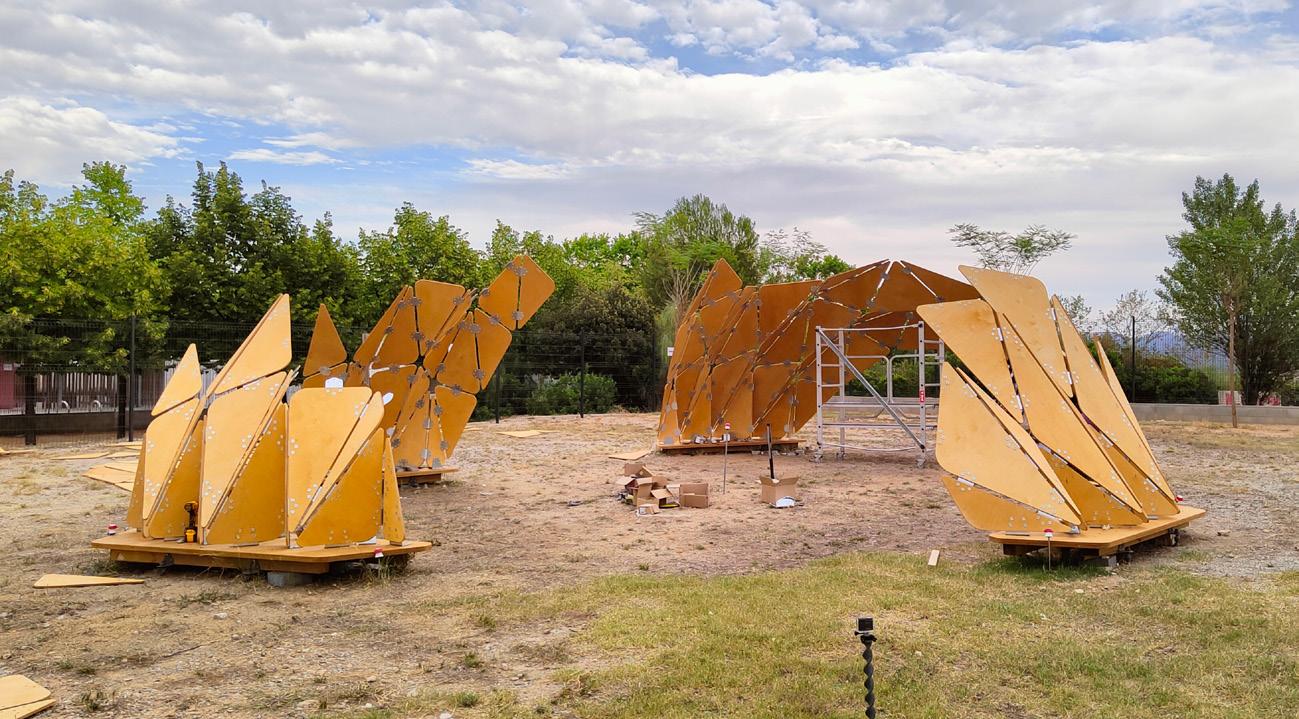
Day 02 // building arch clusters 2
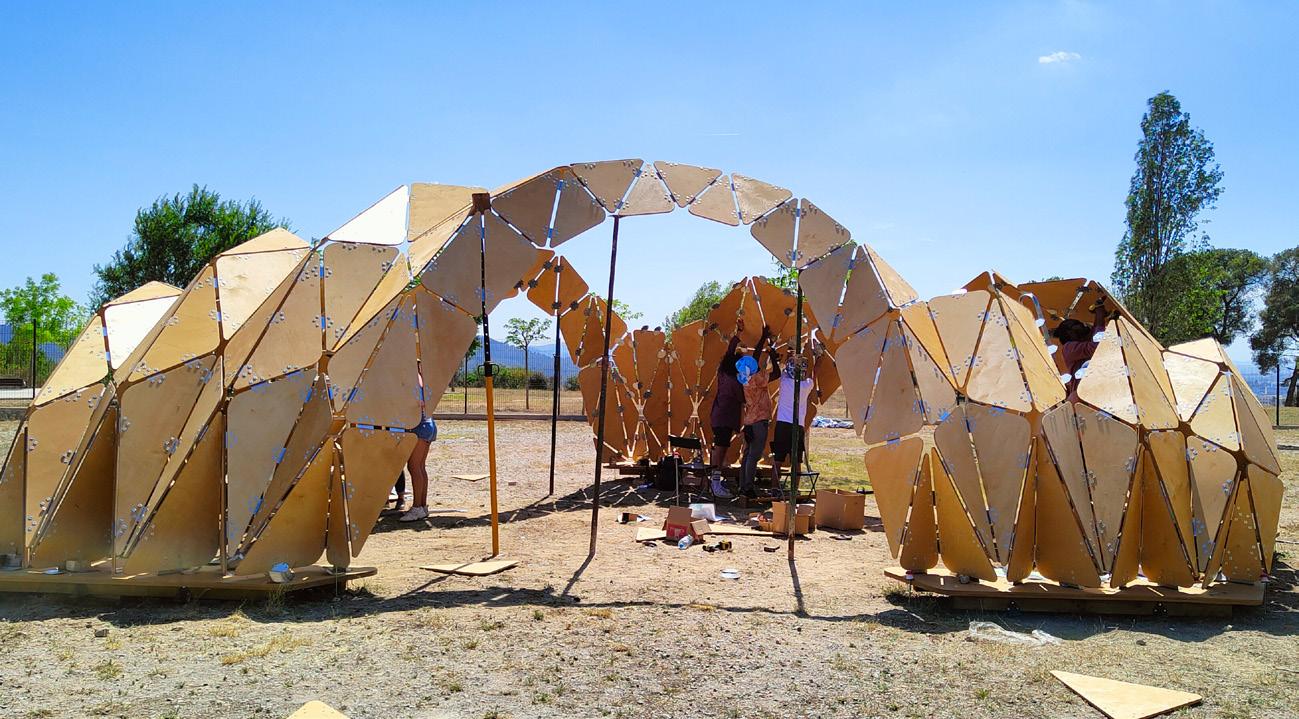
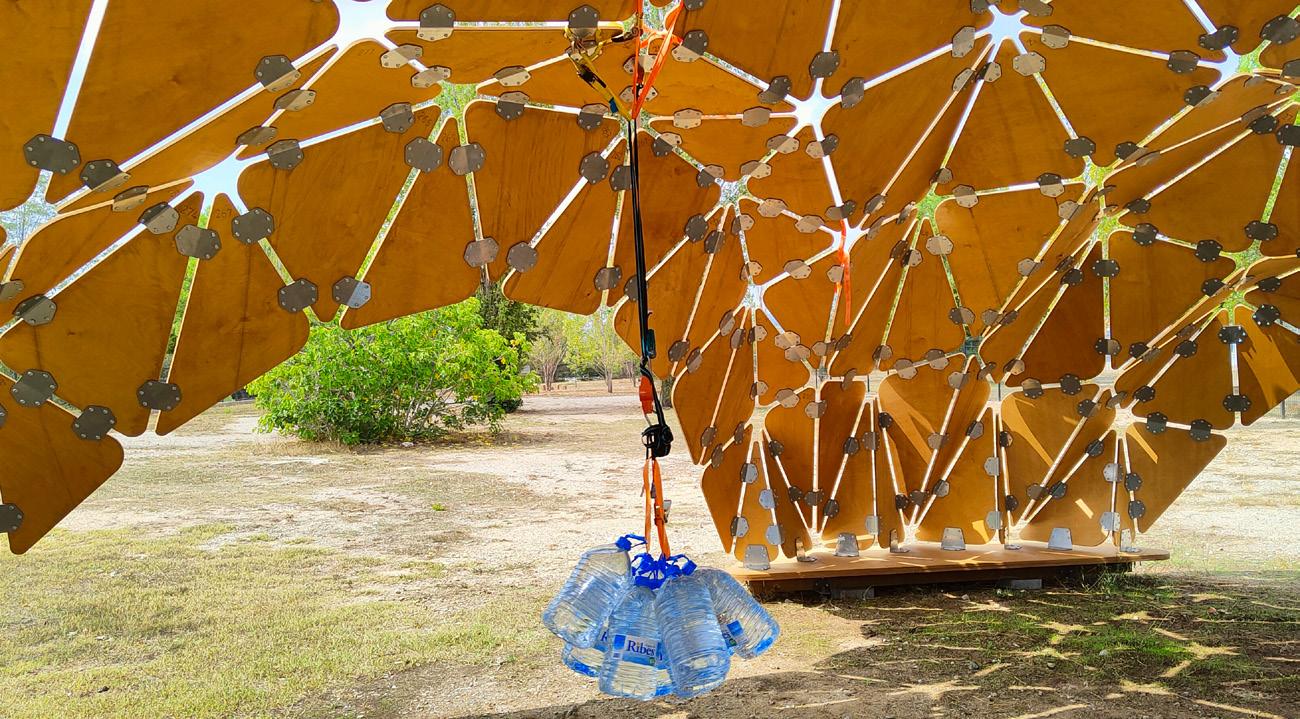
Day 03 // building remaining clusters 3
Load Testing // 9 water cans of 8L 4
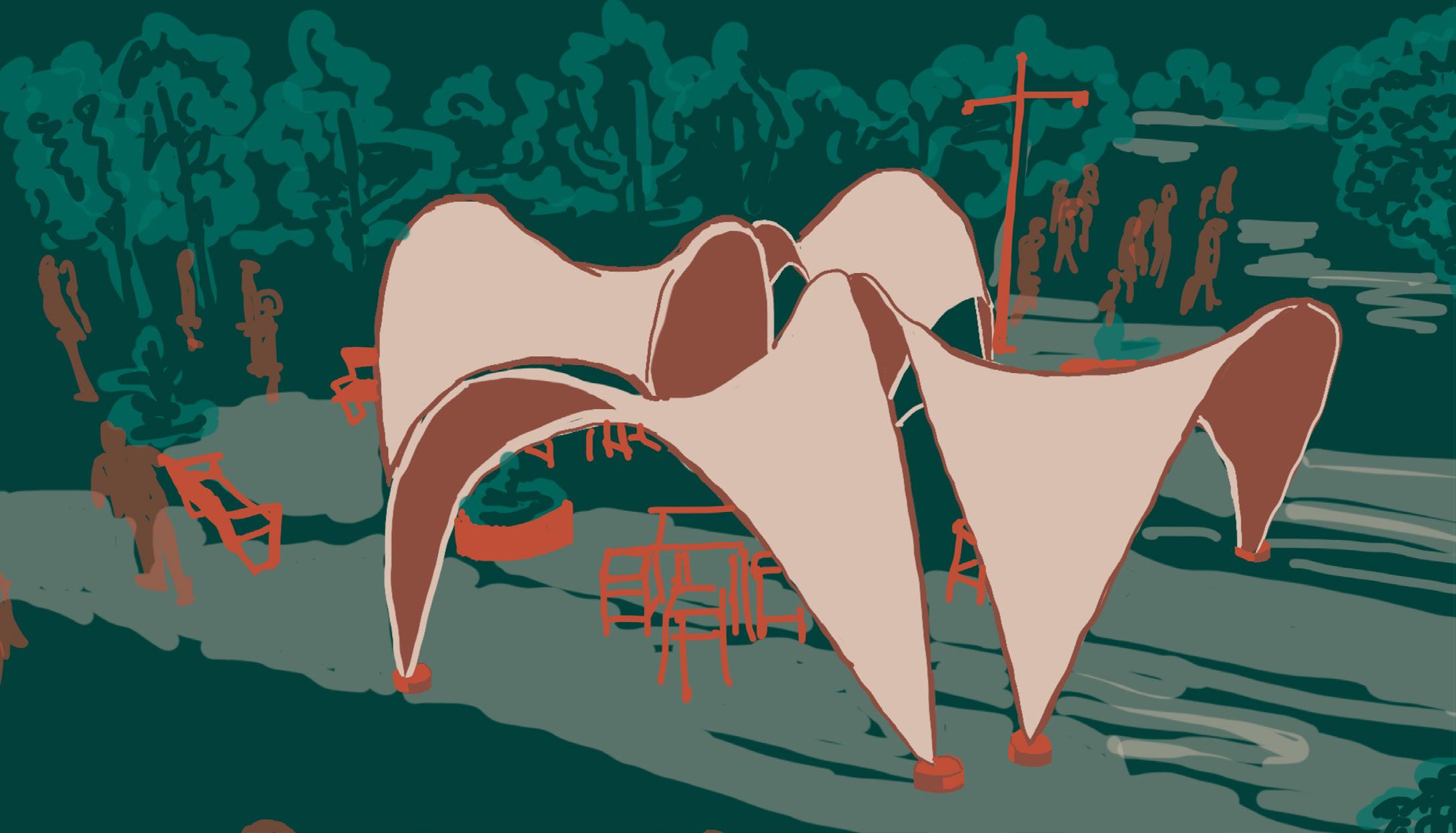