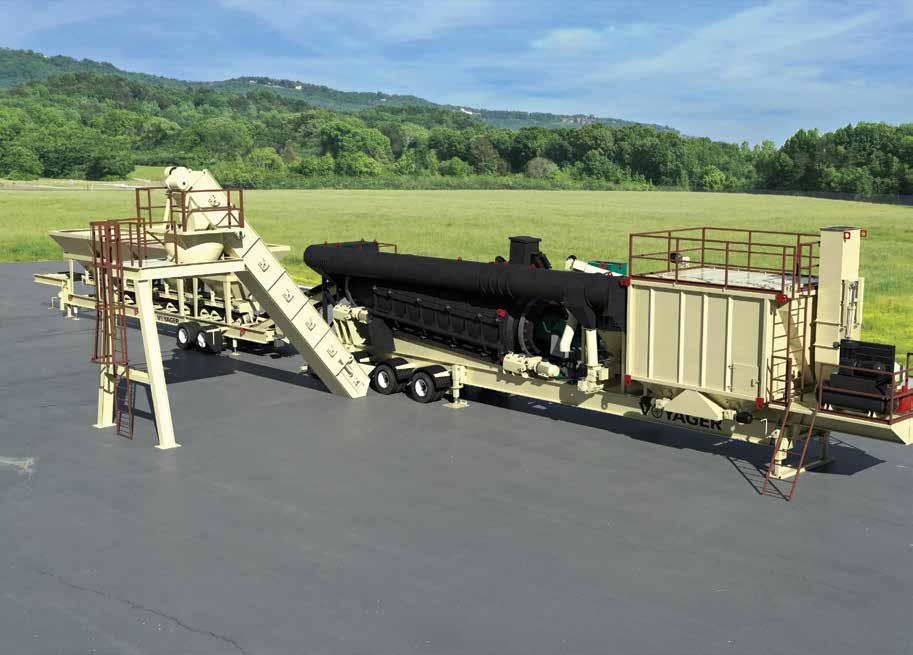
4 minute read
Standardize Your Cracking Language
WWithin the paving industry, different methodologies have different names in different areas of the country. Depending on which state you call home, you might refer to a fogseal as an emulsion spray. You might refer to a mill-and-fill as a mill-and-inlay or a mill-and-overlay. What I find interesting about the regional nomenclature differences is some professionals will argue their definitions as ardently as a Midwesterner testifying the proper word for soda is pop.
As of late, the terms and data collection practices used in describing pavement condition have become as plentiful as the test methods for determining a binder’s propensity to prevent the problem. We won’t get into the test methods here; you can read about those at theasphaltpro.com in the Mix It Up and Here’s How it Works departments. Instead, we’ll use this article to introduce a new document the Transportation Research Board (TRB) National Cooperative Highway Research Program (NCHRP) has released to make cracking data collection easier to navigate no matter where you’re located in North America.
In the NCHRP web-only document 288 titled “Standard Definitions for Common Types of Pavement Cracking,” the authors— Kelvin C. P. Wang; Joshua Qiang Li; Guangwei Yang, Oklahoma State University—offer standardization to make it easier for researchers, vendors, pavement cracking survey providers, pavement engineers at state highway administrations and others to conduct objective cracking measurements. TRB’s website states: “The standard definitions would be used to facilitate comparable measurement and interpretation of pavement cracking.”
The researchers came to their conclusions after the obligatory study of current/available literature and a survey of state highway administrations (SHAs). All data and explanations of it are included in the free downloadable document, but I want to call attention to chapter five, “Proposed Standard Definitions for Common Cracking Types” and the six principles that formed the foundation of the work researchers put into selecting and forming definitions. Specifically, Principle #3—Locating Cracks is More Feasible than Identifying the Causes of Cracks, from page 38 of the document, states:
Naming conventions that imply the cause of cracking should be avoided in automatic processing, simply because a computer driven cracking detection system does not have the intelligence or cognition to identify them with high accuracy. Crack location on the pavement surfaces, however, may indicate load or non-load associated cracks. Identifying crack location is relatively straightforward for automated algorithms; therefore, crack location is a recommended parameter in automated processing.
What the researchers have provided with this document goes beyond a set of “word” definitions. They’ve suggested to industry a common language for better communication. Using existing regulations from entities such as the American Association of State Highway and Transportation Officials (AASHTO), they’ve proposed levels of cracking data—for asphalt and concrete pavements—to assist technology vendors, pavement managers at a network level and pavement engineers at a project level. They’ve created a system in which all professionals can collect, analyze, process, report and apply data that will “make sense” to all professionals across platforms. From pages 62-63, the authors state:
Based on the survey of SHAs and research tasks completed for the project, three levels of cracking defini-
CONTROLStions were proposed to address the needs of both network and project level pavement management, MEP-
DG, and various reporting processes. Level 3 addresses cracking extent at the network level and is a macro-indicator of general cracking extent on a pavement section, or network. Level 3 data satisfies HPMS and MAP21 reporting needs and provides overall cracking infor-
CONTROLS mation, which can be used as the initial qualification and evaluation of potential technology suppliers. Level 2 contains cracking information with low, medium, and high severity levels for pavements. Cracking severity in each zone, including zones for each wheel paths (zone 2 and zone 4), is also computed. Information on
Level 2 can assist various network level PMS activities
CONTROLS and identify locations with specific distress problems.
Level 1 classifies linear cracking into longitudinal and transverse cracking in non-wheel paths, wheel path crack from the wheel paths, and sealed cracks for asphalt pavement. Level 1 also includes the proposed definition for concrete pavement. The general approach of applying the proposed cracking definitions are accumu-
CONTROLS lative. That is, cracking analysis always starts with Level 3, then to Level 2, and finally for the most detailed process to Level 1.
The authors state the next steps for implementation and validation of their new cracking definitions will include field implementation trials from SHAs, design experiments for “ground-truth” results, developing draft AASHTO standard for consideration, and additional steps. CONTROLS
– BY SANDY LENDER
Source: National Academies of Sciences, Engineering, and Medicine 2020. “Standard Definitions for Common Types of Pavement Cracking.” Washington, D.C.: The National Academies Press. doi.org/10.17226/25928
ULTRA-PORTABLE ASPHALT PLANTS PARTS
ULTRA-PORTABLE ASPHALT PLANTS PARTS
AND WE DO THIS...ULTRA-PORTABLE ASPHALT PLANTS PARTS
VOYAGER DOUBLE BARRELTM ASPHALT MIXING PLANT
Small plant footprint, big plant features. ULTRA-PORTABLE ASPHALT PLANTS PARTS
The Astec Voyager DB plants delivers full-size plant features in a compact, highly-portable configuration. Based upon
Astec’s proven Double Barrel® drum mixer, with production capacity up to 140 tonnes/hr and RAP mixing capability up to 50%, the Voyager DB plants sets the standard for portability, production, and sustainability. ULTRA-PORTABLE ASPHALT PLANTS PARTS
SALES: 423.867.4210
A unique approach to asphalt mixing technology.
MOBILITY
The modular design enhances portability and reduces setup time
EASY PLANT ERECTION
No cranes needed for set-up
RECYCLE
Can produce asphalt pavement mix with up to 50% recycle content
FLEXIBILITY
Easily adapts to the local site