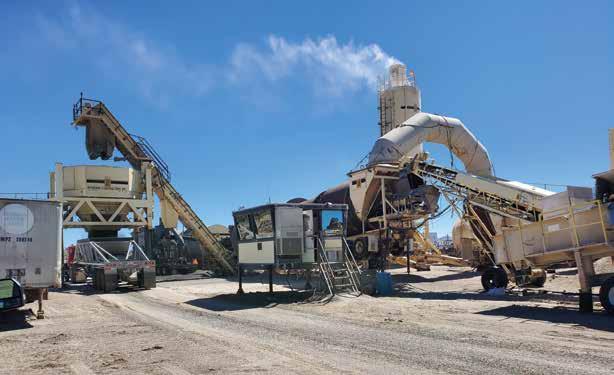
4 minute read
Riverside Contracting Wins Wyoming
Riverside Contracting Wins Wyoming Smooth Roads Award
BY SARAH REDOHL
Riverside produced the mix for its award-winning job on US-14 with its CMI 500-tph portable plant set up at the company’s gravel pit in Aberdeen,
Wyoming, 15 miles from the project.
BBighorn National Forest is a U.S. National Forest spanning more than 1.1 million acres in north-central Wyoming. First established US-14 has an average annual daily traffic count of 4,427. as a forest reserve in 1897, it is one of the oldest governmentprotected forest lands in the United States. US-14 is a common route for visitors to access the forests and According to Riverside Project Manager Kurt Kaufman, the alpine meadows of Bighorn National Forest. After an awardexisting pavement was in fair condition but cracks were beginning winning recent asphalt overlay, Bighorn’s tens of thousands of to appear across the road. Riverside completed the bulk of the $1.8 visitors will have a smoother ride, thanks to Riverside Contracting million project in the fall of 2019, returning to US-14 in the spring to Inc., Missoula, Montana. complete seeding, signage and mile markers.
In April, Riverside was honored with the Wyoming Department “That section of road now has the necessary improvements to of Transportation’s Smoothest Pavement award for a project make it better for the traveling public,” said Jerry Buckley, retired without a wearing course, for its performance paving US-14. The WYDOT resident engineer who oversaw the project. “I’m pleased 5.1-mile project between Dayton and Ranchester required milling with the work Riverside did for WYDOT and the people of Wyoming.” up 2 inches of asphalt and paving the two-lane highway and 6-foot WYDOT began recognizing high-quality asphalt pavement based shoulders with a new asphalt overlay. Riverside also added a turning on smoothness in 2001 in an effort to recognize exceptional work lane in front of a school in Ranchester to improve traffic flow. on road surfaces that will benefit the traveling public. WYDOT
officials evaluate smoothness based on calculations that use an International Roughness Index (IRI). The IRI value of the 5-mile section of US-14 was 38.76, at the completion of the project.
“The key factors that contributed to the success of this project are the crews and leaders our company has,” Kaufman said. “Riverside has extensive knowledge and many years of experience on what needs to be done in regards to smoothness when it comes to paving.”
Since Riverside was founded in 1981, the highway construction company has worked on more than 4,100 national highway system miles in Montana and more than 3,000 national highway system miles in Wyoming.
“We pride ourselves on knowing that we will produce a finished product safely, with high quality, and completion of the project on time,” Kaufman said. The project on US-14 was no exception. “We were able to complete the project within the contract timeframe and provide WYDOT and the public a safe traveling condition headed into the winter.”
Collaboration and a good working relationship with WYDOT was also key to the project’s success, Kaufman said. “We try to plan our paving projects with our crews and WYDOT so the correct lengths and widths are paved daily, which minimizes the amount of cold joints and maximizes smoothness.”
Riverside’s relationship with WYDOT was also useful when they unexpectedly found a number of soft spots in the driving lanes. After receiving a change order, the soft spots were excavated and replaced with suitable material from WYDOT’s maintenance areas and Riverside’s gravel pit in Aberdeen, Montana, to bring it back up to grade. “Other than those soft spots, it was a pretty straightforward job,” Kaufman said.
Riverside subcontracted the milling to Industrial Builders, West Fargo, North Dakota. “The key to milling for a smooth final surface is to keep the road’s profile,” Kaufman said. “The sub took it slow, did it right, and did a great job for us to pave on.”
Riverside also used a Roadtec SB2500 Shuttle Buggy as a material transfer device, which set them up for a smoother pavement. “We like to keep moving so we don’t have to stop,” Kaufman said. “Stopping the paver tends to create bumps.”
The overlay was paved in one 2-inch lift with Class III Marshall mix design, with PG64-28 AC, which was produced by a CMI 500- tph portable plant set up at Riverside’s gravel pit in Aberdeen, 15 miles from the project.
Another contributing factor to the smoothness of the final pavement was the use of sensors on its AP 1055F from Caterpillar Inc., Peoria, Illinois. “If there are any dips or bumps in the road or any ruts created by milling, the use of sensors will keep the paver smooth,” Kaufman said.
Riverside’s crew finished the project with two Dynapac rollers and one Caterpillar roller. In the end, the project’s average density was 95 percent.
Based on the final project’s results, Riverside not only won an award for smoothness, but also qualified for a number of quality bonuses for smoothness, gradation and density.
“Our company is very quality-oriented,” Kaufman said. “We do a lot of work in Wyoming, and we strive to get those quality incentives so we give Wyoming a superior product.”
Help educate future generations about the value of asphalt roads while providing a positive community message about your asphalt facility!!!!!
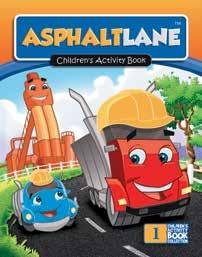
USE ASPHALT LANE FOR:
• Curriculum ideas • Tradeshow giveaways for your local school • Giveaways to local district or your child’s favorite restaurant, elementary class church, synagogue. • Company Events: picnics, open houses, plant tours • A career day activity at your facility