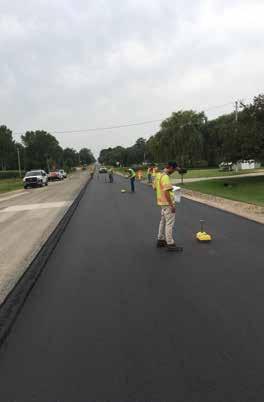
8 minute read
Wisconsin Job Exceeds Longitudinal
sState Trunk Highway 23 is a rural highway connecting Fond du Lac and Rosendale, Wisconsin. Surrounded by farmland, the highway hosts plenty of agricultural traffic. Aggregate pits to the north and west of STH-23 and heavy trucking coming out of the Fox Valley manufacturing area also contribute to the roadway’s high level of truck traffic. Trucking accounts for nearly 14 percent of STH-23’s 7,900 average annual daily traffic. STH-23 is also well-traveled on weekends to access Green Lake, a popular vacation spot.
When the road was in need of rehabilitation, the Wisconsin Department of Transportation decided the project would be an ideal opportunity to test its longitudinal joint density specification and percent within limits (PWL) sampling specification.
PWL is a statistical based method to measure quality. Wisconsin’s PWL specification provides an incentive/disincentive structure to reward construction of a high-quality pavement.
“Across the state, there has been a significant effort to focus on the centerline joint to ensure improved durability,” said Dan Grasser, Wisconsin division manager at Alfred Benesch & Company, Chicago, Illinois.
“We’ve tried a number of ways to improve that joint in the past, and this is a new way of measuring the quality of that joint and how it will hold up over time,” said Bryan Schaller, Benesch’s project construction leader on the job. “STH-23 was a good road for these tests because it’s a long roadway without any major intersections.”
STH-23 became one of the first projects in the state to combine WisDOT’s longitudinal joint density specification and PWL sampling specification. For the project, WisDOT selected Benesch to be its on-site engineering personnel working alongside the contractor, Northeast Asphalt, Greenville, Wisconsin.
“For this longitudinal joint density pilot project, we made sure everyone understood what the new spec requires,” Schaller said. “We also helped develop the methodology and ultimately updated the spec for future projects.”
According to Schaller, STH-23’s use of both a longitudinal joint density spec and the PWL spec is significant, “because with PWL, it isn't about hitting the minimum. It’s about consistency.”
PERCENT WITHIN LIMITS IN WISCONSIN
WisDOT’s Northeast Region office, which oversaw the STH-23 project, is a leader in PWL development in Wisconsin, said Steve Hefel. He’s the Central office HMA supervisor for WisDOT. The Northeast Region office began using the PWL spec on all qualifying projects starting in 2017. Hefel also singled out Northeast Asphalt, for its part in producing consistent mix and achieving good density “highlighting the benefits of the specification.”
Based on data collected on WisDOT projects, Hefel said PWL projects show an increase in density of 0.7 percent compared to its standard quality system.
“A national rule of thumb states that a 1 percent density improvement results in 10 percent better life, so we should expect our PWL projects will last 7 percent longer,” Hefel said. “That alone more than offsets the maximum of 4 percent incentive a project can have.” Additionally, Hefel said, the PWL spec results in improved mixture air void average and consistency, which also prevents pavement distress.
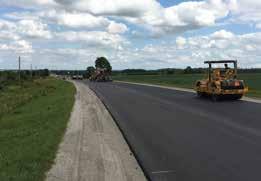
According to Wisconsin Asphalt Pavement Association Engineering Director Deb Schwerman, Wisconsin’s PWL specification is recognized as one of the best in the country. “The focus on longitudinal joint density was a logical progression to enhance the PWL requirements,” she said.
Schaller said the staff at WisDOT’s Northeast Region were instrumental in the success of the project on STH-23. Szalewski also credited Project Manager Zach Jolma for his instrumental role of communicating with all parties on a day-to-day basis.
HIT JOINT DENSITY SPECS
Northeast Asphalt began its work on the STH-23 project in the summer of 2018. The crew first had to remove and replace the damaged sections of concrete beneath the existing asphalt roadway before it could begin paving the 7.5-mile stretch in August.
“Setting the table for a successful pave started with our milling crew,” said Northeast Asphalt’s Lead Project Manager Ric Szalewski. Their Wirtgen W-250i milling machine was equipped with Level Pro mill grade and slope control.
The crew used a Roadtec SB 2500-C material transfer vehicle to allow for continuous paving and limit thermal segregation. The crew paved two lifts of asphalt with its Volvo 7170 paver, equipped with a Carlson Easy Screed IV screed. Its paver was also equipped with a contact reference ski and Blaw Control 7.0.
The first lift was 2 ¼ inches and required 22,230 tons of fine graded 19mm 3MT 58-28S. The second lift of 1 ¾ inches required 18,289 tons of fine graded 12.5mm 4MT 58-28S. Benesch sampled mix for quality verification while Northeast sampled for quality control at the 400-tph Dillman counter-flow portable asphalt plant Northeast brought in for the project. Testing was done at a WisDOT lab about 1.5 hours from the project.
Since the project kept one lane in each direction open to traffic at all times, Northeast paved the job with a notch wedge joint, paving one lane on day one and the second lane against the cold joint on another day.
“Like the rest of the industry, we realize that joint construction is very important,” Szalewski said. Although Northeast has always aimed to build quality joints, Szalewski said the project on STH23 would put their practices to the test. Because there had been no specifications for joint density on Northeast’s other projects, they didn’t know if their normal paving practices would achieve the joint density specified on the STH-23 job.
To collect data ahead of the STH-23 project, Northeast tested its rolling pattern on a different job they were paving and took some informational tests on joint density.
“We wanted to make sure the emphasis we normally put on joint quality would get us the numbers we needed in regards to STH-23’s specs,” Szalewski said. “We found that what we were doing on our existing job actually met what we needed to do on this job.”
The crew made seven passes with its Sakai 850 78-inch high frequency breakdown roller, then put its BOMAG BW27 rubber-tire roller on the mat for intermediate compaction, and performed five passes with a DD-110 cold roller. Schaller said making an extra pass along the joint with a rubber tire roller helped to achieve density on the joint.
One minor tweak Northeast did to ensure joint density was utilizing the data it collected about joint density to communicate with the crew and inform any adjustments as the crew paved. This
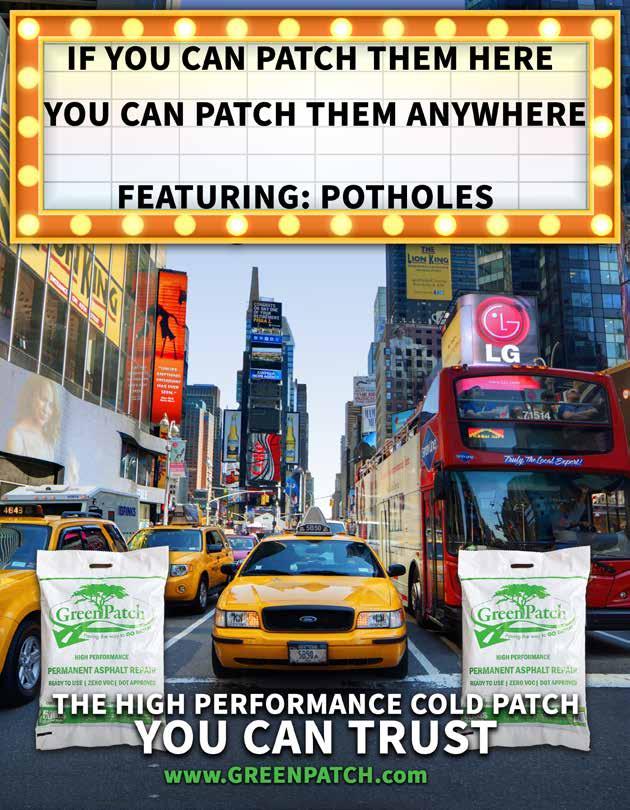
Northeast Asphalt set its paving speed for the job at 22 feet per minute.
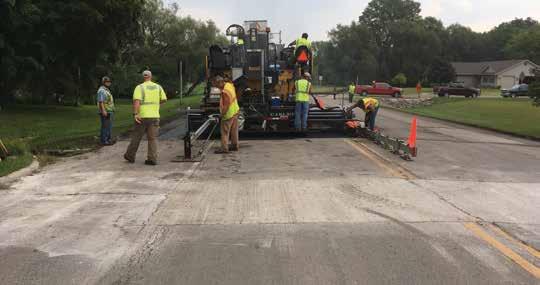
constant communication also allowed the crew to adjust its feetper-minute for “a bit more production,” Szalewski said, adding that they were able to bump it up by 2 or 3 feet per minute while still reaching the density spec on the joint. Based on Northeast’s test strip paved on the job, its paving speed was set at 22 feet per minute.
The mat temperature was about 290 degrees Fahrenheit at the breakdown roller during joint construction.
Benesch used a nuclear density gauge to measure percent compaction within 6 inches of the edge of the joint along the length of the project. They performed one test within every 1,500 lane feet, equivalent to one test for every three quality control tests by the contractor.
Completing all the necessary testing required collaboration among all project stakeholders from the very beginning. “With the significant increase in the amount of testing being done on this project, we knew we had to be well-prepared in advance to make sure we got all the tests we needed while staying on schedule,” Schaller said.
WORK HARD, GET RESULTS
In the end, Northeast Asphalt overcame the challenges of the STH23 job. In fact, the job received a Quality in Construction award from the National Asphalt Pavement Association.
Northeast Asphalt also achieved the highest available incentive for more than 95 percent of the project for the longitudinal joint. “The contractor did a really nice job out there getting density along the joint—way better than they thought was possible,” Schaller said.
The target minimum density for the traffic lanes on STH-23 was 93 percent. The target density was reduced by 1.5 percent at the longitudinal joint where the crew would be paving up against an existing lane or by 3 percent when paving the first pass, without lateral confinement. Hefel reported that STH-23 project earned a longitudinal joint density incentive of $0.34 per lineal foot on the lower layer and $0.36 per lineal foot on the upper layer. Wisconsin’s maximum longitudinal joint density incentive is $0.40 per lineal foot.
“We also looked at how much confined or unconfined joints affected the density achieved,” Schaller said. They discovered an average of 93.31 percent density (3.31 percent above minimum) across the 206 testing locations along unconfined joints, and 94.88 percent (3.33 percent above minimum) across the 224 testing locations along confined joints. “Overall, the density achieved on the joints was consistent at 3.3 percent above the specified minimum for both confined and unconfined.”
The crew also succeeded on pavement smoothness, achieving an International Roughness Index (IRI) score of 31 on westbound STH-23 and 28 on eastbound STH-23.
Northeast Asphalt isn’t the only stakeholder for whom the STH23 project was a resounding success. WisDOT is walking away from the project with plenty of insight to apply to future projects, and a longitudinal joint density spec will become the new standard in Wisconsin.
The taxpayers of Wisconsin also win. As a result of the project’s success, it is anticipated that the life of the pavement on STH-23 will be extended.
“One challenge with research projects in general is making sure that we construct the project in the best interest of the research, but not to the point that it is a detriment to the project quality,” Schaller said. Although it’s a balancing act, the project on STH-23 achieved both of those goals.
“Independent of the valuable research done, this was a quality project,” Grasser said.
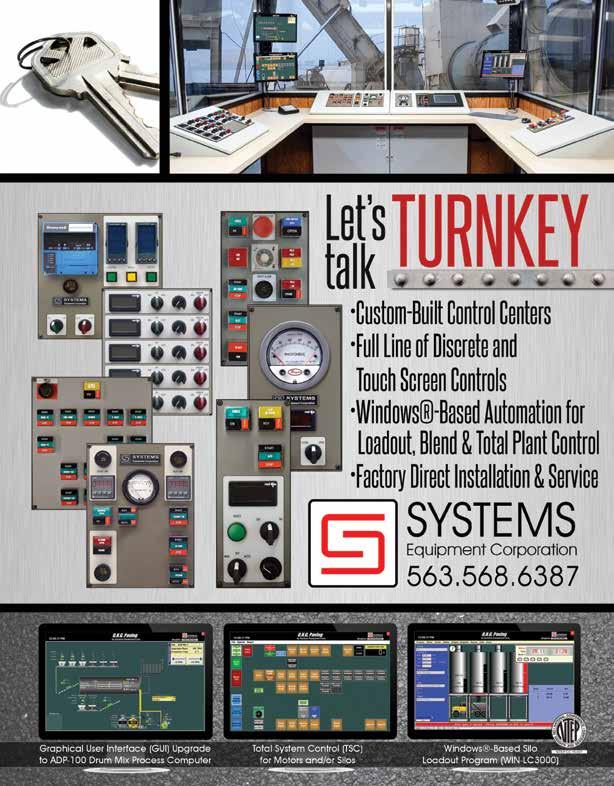