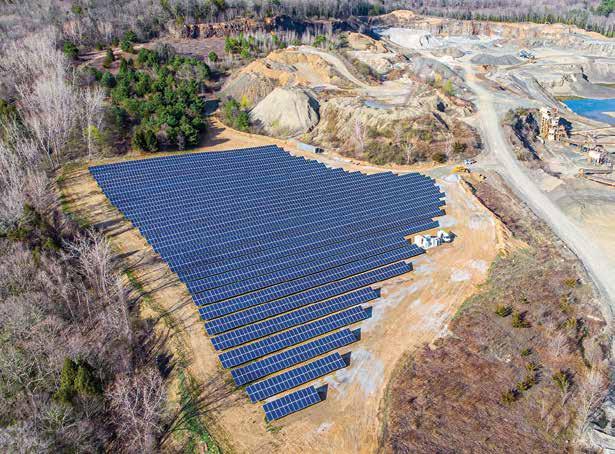
12 minute read
O&G Installs Solar Array for Quarry
O&G Installs Solar Array for Quarry, O&G Installs Solar Array for Quarry, Plant Operations Plant Operations
OBY SANDY LENDER On five acres of its existing Southbury O&G’s now-retired director of planning “Th e idea of a minor modification quarry footprint, O&G Industries of and permits. Ken worked at O&G for over was rejected and a hearing required,” Torrington, Connecticut, had room to 30 years in the role and had established very Balavender explained. “We had space install a sustainable energy platform good relationships with the town boards available within the existing footprint of to power its quarry and asphalt plant and local officials that he engaged with on the quarry for the improvement.” operations. The company went live with a regular basis.” As outlined in a blog post With the permit secured, O&G began a 1.3-megawatt (MW) solar array at the for The Town of Woodbury, Connecticut, construction with site clearing June 2019. quarry on Roxbury Road in spring 2020. April 28, 2019, the zoning commission They installed panels October 2019. They
Planning and permitting for the project commended O&G’s concept to “go green” flipped the switch March 27, 2020. What began in autumn 2018. The company’s with the solar panel project, but its town they’ve accomplished is an environmentally chief counsel, Paul Balavender, explained, attorney deemed a hearing necessary laudable concept for other quarries and
“Local permits were secured by Ken Faroni, before the project could be permitted. plants to consider. O&G Engineerin g
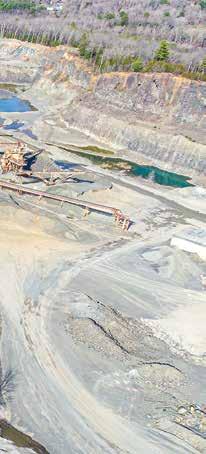
Manager Matthew Tobin explained that by middle of May: “The solar array has produced approximately 184,000 kW-hours of electrical power to date, so that is power that we did not have to purchase from the utility.”
PARTNERS TO POWER UP
The solar contractor, Solect Energy of Hopkinton, Massachusetts, partnered with O&G to bring the project to fruition. Solect’s vice president of business development, Andreas Schmid, shared how this project’s power collection is an example for other members of industry to consider.
“Pairing solar generation with battery storage is probably the biggest thing happening in the solar industry right now,” Schmid said. “Solect began working with O&G team members on preliminary designs, engineering, state incentives and utility applications in September 2018. I reviewed LEFT: The 5-acre area where the 3,762 six-foot panels are installed was made up of quarry spoils and acreage to be cleared. The soil included boulders and dense aggregate that was difficult to grade, thus crews used special ground screws to anchor the panels to withstand high winds. Engineering Manager Matt Tobin described how the team constructed a specialty junction box for the medium voltage connections: “We ran approximately 1,100 feet of conduit and wire to the existing transformer at the concrete plant. When we reached the transformer, there was no easy way to get the wire into the vault under the transformer as its foundation was comprised of mafia blocks with a concrete topping. We brought the conduit to the side of the mafia block foundation and had an “L” shaped junction box fabricated to connect to some spare conduits running to the vault. Luckily, there were some spare conduits we could connect to; otherwise we would have been tunneling!” ABOVE: Matt Tobin, who has been with O&G Industries for two decades, is the engineering manager for the company and served as project manager for the solar array installation.
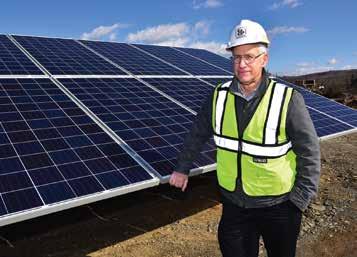
The solar array project was completed in collaboration with Eversource, Solect Energy and EnelX.
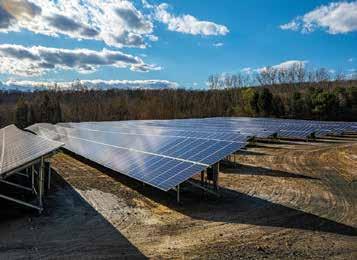
The panel array is coupled with a 280-kW energy storage system that will help to augment supply during peak demand cycles, such as early morning hours. The project is one of three solar projects that O&G has developed with the quarry installation being the first of its kind in the state. Solar arrays have also been installed on the rooftops of the company’s fleet maintenance facility in Torrington and mason supply showroom in Bridgeport.
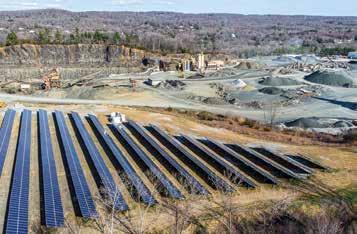
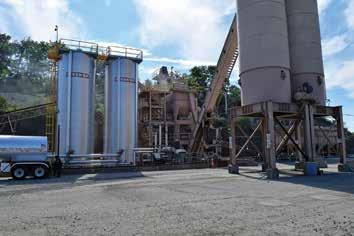
the project and determined that it was a good fit and a viable project from the beginning, especially given O&G’s commitment to see it through and Solect’s track record with similar projects. O&G is a great customer due to their responsiveness, and detailed step-bystep approach. Early in the process, we were all clear on the requirements to complete a project like this and the 18-month timeline.
“The investment required for a solarplus storage project produces attractive investment returns while also helping to make our world more sustainable,” Schmid continued. “Firms like Solect possess the expertise and knowledge to fully understand the cost of development and the savings unique to specific localities and utilities. The ability to produce the power a facility requires is now within reach of a significant portion of energy consumers and firms like O&G are helping lead the way.”
O&G leads the way with its participation in a number of environmentally sustainable measures. Melissa Hulting of the U.S. Environmental Protection Agency (EPA) shared that O&G was the first asphalt company to sign up for the ENERGY STAR® industrial program with the National Asphalt Pavement Association (NAPA) pilot program. She shared: “We are trying to expand participation in our national industrial partner network, which includes companies in many different sectors, including getting more small- and medium-sized manufacturers involved.
“Our industrial partner meeting at the end of September will be held virtually, so we’d love to see more companies become partners and participate in the meeting. I’ve witnessed firsthand how energy managers from different industries can learn from each other, especially as it relates to managing the overall corporate energy program and engaging employees from across the organization—from senior managers to equipment operators. (See the sidebar on page 36.)
“NAPA and the pilot companies have been excellent partners in this effort, and we’ve already had companies enroll plants in the Challenge for Industry—O&G was the first to register plants for the Challenge. They are being smart by taking advantage of the utility assistance available to them to improve the efficiency of their plants.”
PRACTICAL SUSTAINABILITY
Brad Oneglia, vice president of O&G Industries, shared some of the steps they’ve taken so far to improve efficiency. “Most of these improvements have been behind the scenes,” Oneglia said.
In New Milford and Stamford, among other locations, the company has upgraded burner controls, added variable frequency fan drives, eliminated air leaks, and installed insulation on tanks and piping. Enrolling the plants in the ENERGY STAR program is just one piece of O&G’s commitment to sustainability, as evidenced by the additional partnership with Solect to install the solar panel array for power. Oneglia was involved in those initial conversations.
“I don’t think there was an overarching goal for power generation or cost reductions,” Oneglia said. “We’re part of the younger generation and we all feel there is a need to keep in mind environmental sustainability and to preserve our natural resources. Fairfield County is an air quality non-attainment area (meaning air quality is worse than the National Ambient Air Quality Standards as defined in the Clean Air Act Amendments of 1970) so we want to demonstrate our commitment to the
community. By getting the ENERGY STAR certificate, we can show we’re as good as we can be.”
He pointed to a number of positive steps the company has taken over the years as good stewards of the land, including the New Milford Quarry receiving the 2017 Sustainability Award from the Connecticut Chapter of the American Planning Association for constructing a brown bat hibernaculum.
“The solar array is just one more step in doing the right thing. It was a best case scenario where we could do the right thing and it was a good business decision. Funding was available to offset the cost. It’s the right thing to do, but, at the end of the day, you have to be able to make a business case for it as well.”
“O&G, with Solect’s assistance, bid into a State of Connecticut program, called the Zero Renewable Energy Credit (ZREC) program,” Tobin explained. “This program pays O&G for the solar power that it produces.”
“Solar and storage facilities like this one must apply for and receive approval to tie in with the grid as well as comply with all engineering standards,” Schmid said. “The local utility provider plays a key role in understanding the impact on the broader grid and ensuring that individual solar arrays and storage facilities are designed and engineered to align with current infrastructure as well as future plans for the local utility. The approval of the local utility is an essential requirement for developments of this type to achieve the business and engineering objectives.”
“The electrical distribution system at the quarry is the same voltage as the Eversource distribution grid—13,800 volts, or 13.8kV,” Tobin explained. “In order to connect to the plant distribution grid, we had to install a 480-V to 13.8-kV transformer at the solar array, install approximately 1,100 feet of underground conduit and medium voltage (MV) wire, and install a custom junction box to connect to the existing transformer at the concrete plant, so it was a fairly involved effort worth approximately 3.5 percent of the project
How to be an ENERGY STAR®
The National Asphalt Pavement Association (NAPA) is working with the U.S. Environmental Protection Agency’s (EPA) ENERGY STAR® industrial program to develop a sector-specific program to help asphalt mix producers manage and reduce energy consumption at asphalt plants. Joseph Shacat, the director of sustainable pavements at NAPA, shared: “Through the program, which is currently in the pilot phase, a small group of companies has been participating in peer group meetings to exchange information on best practices for energy management. NAPA has hosted several ENERGY STAR educational webinars, recordings of which are available to download for free through NAPA’s online store. An energy guide for asphalt plants is under development.”
Melissa Hulting, of U.S. EPA Region 5, explained: “We are drafting an asphalt mix plant energy guide using existing NAPA guidance materials as a starting point, which will include an Energy Treasure Map that will list different actions that plants can take. The pilot group will provide input on the guide.”
The treasure map is linked to a concept EPA calls “A Treasure Hunt.” Hulting described it for readers.
“A Treasure Hunt is a one- to three-day event where teams walk around a facility looking for ways to save energy, with a focus on no- or low-cost actions (though Treasure Hunts can also reveal opportunities for equipment replacements, etc.). These quick fixes can add up. Some organizations have used Treasure Hunts to reduce their facilities’ energy use by up to 15 percent.
“For asphalt mix plants, such fixes could include checking for and repairing compressed air leaks, insulating hot oil lines, and managing aggregate pile moisture.”
“ENERGY STAR provides a great framework for industrial facilities like asphalt plants to manage and reduce their energy consumption,” Shacat said. “They also bring highly competent professionals to the table who can help companies develop and improve their energy management programs.”
“The goal is to work with the asphalt pavement producers to improve energy efficiency in the sector and complement NAPA’s existing sustainability efforts,” Hulting said. “We want to leverage ENERGY STAR’s existing tools and the expertise of NAPA and the participants to help the sector as a whole.”
One of the many ways HMA producers can save energy is by installing insulation on tanks and piping, as O&G Industries has done at its Southbury plant. Photo courtesy of O&G Industries
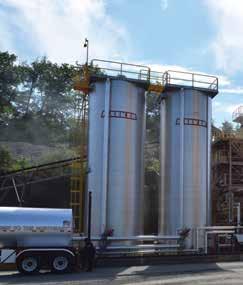
For information on becoming an ENERGY STAR industry partner,visit: https://www.energystar.gov/buildings/about-us/ become-energy-star-partner
For information on the treasure hunt, visit: https://www. energystar.gov/buildings/about-us/campaigns/treasure_hunt
A generic treasure map for manufacturing facilities currently exists here: https://www.energystar.gov/buildings/tools-andresources/energy_treasure_map_manufacturing_plants
cost. Solect’s original contract ended at the low side of the 480 V to 13.8 kV transformer at the solar panel array. I did issue Solect a change order to install the MV conduit, so they had some involvement.”
The environmental positives from the project are already apparent.
“Obviously, the electrical production from the solar field will displace electrical power that would otherwise have been generated at a combined cycle natural gas plant or at a peaker plant, so that serves to cut fossil fuel emissions,” Tobin said. “Also, being located in a quarry on reclaimed land, the solar field did not disturb any pristine habitat and it is not really visible to the public.”
The Town of Woodbury blog stated this will assist in lessening the 50,000 gallons of diesel burned on average at the operation each year, which will further reduce emissions.
A 280-kilowatt (kW) energy storage system functions like a battery backup to augment supply during peak demand cycles. This includes early morning hours when the sun isn’t strong enough to generate at full capacity, but demand at the facility peaks with quarry and asphalt plant operation startup.
“We fire up the plant to service the business,” Oneglia said. “The new storage system limits that drain on the power grid. We’re able to draw from a reserve power base.”
Oneglia also spoke of the positive experience the work toward higher efficiency has been. “All of the partners involved, from consultants to engineers, were very good to deal with.”
Tobin also gleaned valuable experience from the project. “As I had not been involved in a ground-mount solar installation before, this was a valuable learning experience for me and it was a pleasure working with the plant superintendent, Tom Alexson Jr., who was extremely helpful, with the O&G operators and carpenters who helped build the project, and with our counsel, Paul Balavender, who helped with the contractual end of things.”
“O&G has been outstanding to work with,” Schmid said. “Their team asked all the right questions from the beginning and wanted to ‘go deep’ in understanding the technical requirements and financial aspects of the solar PV and battery energy storage systems. I personally appreciated the commitment from O&G, as did the rest of the team at Solect.
“We were really able to dive into this project and execute it at the highest possible level,” Schmid continued. “This was accomplished in the most honest, forthright and friendly way. Our main contacts at O&G (Paul Balavender, legal counsel; Matt Tobin, engineering manager; and early on before he retired, Rick Audette, director of power & energy for O&G) were all smart, responsive, welcoming and always on the ball. They truly were a great team to work with.
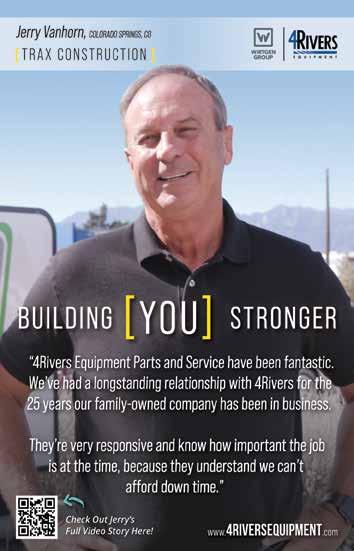
“I think we all particularly enjoyed discussions around batteries and battery management processes, technology and innovation, and how employing the cutting edge for O&G could make the project work better for them in terms of achieving even better sustainability and financial results. All of this timely collaboration resulted in a better project and better relationship.”