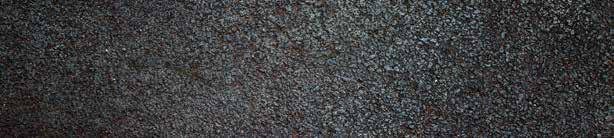
10 minute read
Source Quality Aggregates: an
Source Quality Aggregates: an Economic Discussion
FROM TRB
Editor’s Note: Asphalt professionals know getting hold of quality aggregate is becoming more difficult and costly in some areas. Recycling materials and blending virgin materials provide some solutions, but only if appropriate quality can be assured for the agencies letting the jobs/designs. Panelists for a Transportation Research Board (TRB) presentation on this topic, chaired by Andrew Dawson of the University of Nottingham and chair of TRB’s aggregates committee, drew on e NCHRP Synthesis 524 to provide guidance. Erol Tutumluer, of the University of Illinois at Urbana, Champaign, and Maziar Moaveni, of Savannah State University, Savannah, Georgia, are two of the authors of NCHRP Synthesis 524 report and discussed Aggregate Quality Requirements for Pavements during the presentation for the Transportation Research Board (TRB).
Sand, gravel and crushed rock are the second most consumed resource after water.
Each person in the United States uses about 8 tons of aggregate per year. That’s about 3 billion tons extracted per year, taking up about 44 billion cubic feet of space, which is equivalent to about 230,000 U.S. football fields, each 30 feet deep. That’s about the area of D.C. to a depth of 100 feet every four years. We, as an industry, don’t want to extract that much and leave that big hole.
Because transporting material from quarries and remote sources into the areas of demand is costly, we must make the best use of what we have wherever projects occur. To reduce waste at various sites, the presenters put forth the following: • Don’t over-specify, but instead, only specify the qualities that are needed for the desired application and performance; • Use available aggregates as best we can through selecting and blending; and • Reliably quantify what we have so we know the relevant characteristics available to us.
As a step in this direction, NCHRP Synthesis 524 was developed.
EROL TUTUMLUER, PH.D.: PROCEDURES FOR APPROVING SOURCES
Tutumluer acknowledged that methods of approving an aggregate source vary depending on the agency practices and most agencies provide lists of pre-approved sources on their websites. Approving an aggregate source may require that certain aggregate materials pass some quality requirements from that aggregate source. You’ll encounter different aggregate classes (and acceptance requirements) for different pavement applications.
Agencies also have established aggregate quality classes and associate the class with the use of aggregate material in a certain pavement layer application. For example, the Indiana Department of Transportation (DOT) has three general ratings for fine aggregates: • A5 is for natural sand approved in all pavement applications; • B5 is for applications that allow use of manufactured sands or fine aggregates; and • G5 is for fine aggregates that are not approved for use.
IDOT also has seven coarse aggregate classes starting with Class AP as the highest quality.
On the aggregate quality classes, Tutumluer showed typical quality requirements established by state agencies and Canadian provinces.
In the charts on page 46, you see virgin aggregates and recycled aggregates specifications quality requirements for Minnesota DOT. Within the charts, you see a detailed quality class specification going from 1 to 6, which is a common thread for states or agencies to adopt—going from 1 to 6 with numbers or A,B,C,D, type classes.
There’s a fairly detailed requirement listed, a lot of them related to the deleterious materials such as the shale content, maximum amount of fines, some L.A. abrasion requirements, crushing requirements, and so on.
You can clearly see that in the case of recycled aggregates such as RAP, maximum bitumen content and other deleterious materials are listed with maximum allotments.
Tutumluer explained, of the agencies that reported, 18 indicated they have established at least one quality class for one or more aggregate types, and this includes blast furnace slag, RAP, and so on.
Aggregate quality classes for use in pavement layers are established according to the pavement layer’s application. • Asphalt surface course • Asphalt base course • Asphalt surface treatment • Portland cement concrete • Aggregate base course • Aggregate subbase course • Permeable drainage layers • Filter materials for PCC pavements (One that Tutumluer didn’t mention is drainage surface aggregates (DSA), which are discussed in depth in the article “TRB Discusses Driving Surface Aggregate Specs” at https://theasphaltpro.com/articles/trb-dsa-specification/)
He pointed out that the responding states generally have less strict requirements for aggregates to be used in the asphalt binder course than in the asphalt surface course. For example, Iowa permits the use of classes A through D, steel slag in a proportion of 25 percent or less, RAP and RCA of greater than 50 percent in the binder course, whereas the state specifies five aggregate classes (Types 1 through 5) based on their frictional characteristics for use in surface courses. You can see how different state agencies establish different classes.
For surface treatments, look at micro surfacing in Minnesota. For micro surfacing treatment in Minnesota, a blend of Class A and Class B aggregates is allowed if material passing the 3/8-inch (9.5-mm) sieve and retained on the No.16 (1.18-mm) sieve is 90 percent or greater by weight from the Class A aggregates, the taconite tailings, or a mixture of both. Taconite tailings is a hard aggregate that can be used as a surface treatment aggregate. The micro surfacing aggregate durability requirements suggest the tests on aggregate include sand equivalent (AASHTO T 176), abrasion resistance (AASHTO T 96) and soundness (AASHTO T 104). For the abrasion resistance test, it is required to use Grade C for Type 3 material; use Grade D for Type 1 and Type 2 material. The soundness test should be performed on the Class B aggregate of the blend, if applicable.
Test
AASHTO T
AASHTO T
AASHTO T
Requirement
176 > 60%
96 < 30%
104 < 25%
In general, for concrete there is very low fines content allowed, very low deleterious materials allowed, and so on. You’ll see Class A quality class requirements for concrete courses.
Permeable drainage layers and filter layers require the highest quality of materials in terms of heavy open gradation specs so they can easily permeate and drain the water. Some agencies will allow recycled material in these drainage layers, but the open graded layer must be open to allow water to drain. Filter materials for PCC pavements need to satisfy certain aggregate quality and gradation requirements because the permeable subbases are constructed as the foundation of concrete pavements and cannot allow pavement faulting or pumping.
MAZIAR MOAVENI: SOURCES, RECYCLING AND BLENDING
An excellent response of 90 percent of the agencies have formed the foundation of the synthesis Moaveni discussed.
Basically, the aggregates used in pavement applications can be divided into two broad categories of stone deposits: • the sedimentary, igneous and metamorphic rocks; and • sand and gravel deposits, which are extracted from sand and gravel pits.
These sand and gravel deposits make up approximately 42 percent of the total aggregate production in the United States.
Here’s how the agencies characterize and categorize the products.
Thirty-eight percent of the agencies do NOT have approved lists of aggregates. (See an example of an approved list of aggregates at https://www.roads.maryland. gov/OMT/AggBit.pdf ) This is comprehensive and shows which aggregate can be used in which layer of the pavement. Having the approved list is efficient and valuable.
Agencies have developed tests to check for aggregate quality for requirements related to:
LIBRA REMOTE PRINTER TERMINALS
Are your ticket delivery methods stuck in the past?
Consider the efficiencies of keeping the driver in the truck and delivering tickets electronically!
Experience the Advantages: Printer
• Document presenter holds ticket for driver and retracts it into an internal box if not taken • Loop print presenter ensures jam-free operation by eliminating user access to the document while it is printing • Best reliability of print head, cutter and presenter (2x to 10x over other thermal printers) • Handles 3” or 4” wide paper and various paper thicknesses • Highest-speed printing • Exceptional print quality
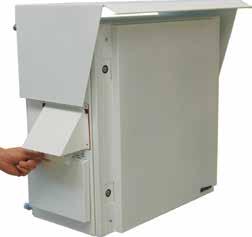
Enclosure
• Industrial enclosure designed to house printer and paper roll • Heat shield keeps printer cool in direct sun • Internal heater keeps printer warm in freezing climate • Motion-activated light illuminates when enclosure is opened
For more information, contact Libra Systems via email (sales@librasystems.com) or phone (215.256.1700)
• particle size distribution; • degree of crushing (percentage crushed, number of fractured faces); • liquid limit (LL) and plasticity index (PI); • durability; and • soundness.
The commonly used specs for procedures agencies use include those developed by: • AASHTO (modified); • ASTM (modified); • U.S. Army Corps of Engineers; and • individual state and provincial transportation agencies.
Remember that different tests can be required for different applications or pavement layers/performance requirements. For example, if an agency wants to test quality of virgin aggregate properties, respondents are running some combination of the following tests: • Expansion from hydration reaction; • Alkali Silica or Alkali Carbonate Reactivity (ASR and/or ACR); • Specific gravity and absorption (92 percent of respondents perform this test); • Freeze-thaw resistance test for durability; • Particle shape properties such as angularity, surface texture, flatness and elongation (79 percent of respondents perform these tests); • Harmful clay content, such at the Methylene Blue test; • Cleanliness, such as the sand equivalent test (66 percent of respondents do this); • Mineralogical composition; • Plasticity properties such as Atterberg
Limits; • Percent deleterious materials (75 percent of respondents test for these); • Resistance to polishing and degradation, such as the Micro-Deval test; • Resistance to degradation, such as the
Los Angeles Abrasion test (81 percent of respondents perform this test); and • Resistance to weathering by Na2SO4/
MgSO4 soundness (66 percent of respondents do this).
Similar testing is done for RAP aggregates, RCA and so on.
By blending, agencies can make more effective use of locally available materials and marginal aggregate materials and increase the effective use of RCA and RAP. But not all states allow blending. Those that do are blending to meet target gradation specification for mix design and to improve quality and so on. Recent studies of aggregate
blending have shown positive results. For example, Bennert et al. in 2000 showed blends of RCA, RAP and dense-graded aggregate base course obtained higher resilient modulus than virgin aggregates in use; blends with RCA accumulated the lowest permanent deformation. Arulrajah et al. in 2012 showed RCA and waste rock have geotechnical engineering properties equivalent to or superior to those of typical quarry granular subbase materials. This is an area that is under research right now.
PRACTICAL SOURCING
Overall, the synthesis showed source approval is a practical way of managing quality assurance of the aggregates industry uses, but the procedures and timing of the testing and analysis used needs careful consideration. Everyone wants the system to be straightforward and not too restrictive.
Specified characteristics of aggregate materials vary from state to state, so it’s appropriate that we match the assessments or the tests that we apply to the properties that those particular sources may or may not have. Then we can reject materials that don’t come up to standard and accept the materials that do. The best approach in one area of the country may not be easily transferred to “best approach” in another area.
It is possible to use nontraditional or marginal aggregates—ones that we wouldn’t usually have thought of using. Agencies have tests that we can apply to assess the applicability or “usability” of those materials. Then blending and selection are important tools in considering those sources.
Download the entire synthesis for your full review: www.trb.org/NCHRP/Blurbs/177913.aspx
Quality Requirements for Virgin Aggregates, MnDOT
Class
Requirement
1 and 2 3 and 4 5 and 5Q Max Shale, if No. 200 <7% by mass NA 10.00% 10.00% Max Shale, if No. 200 >7% by mass NA 7.00% 7.00% Minimum Crushing Requirements* NA NA 10%
Maximum Los Angeles Rattler (LAR) loss from carbonate quarry rock 40% 40% 40%
Maximum Insoluble residue from the portion of quarried carbonate 10% 10% aggreates passing the No.200 sieve *Material crushed from quarries is considered crushed material. Source: TRB webinar 10%
6 7.00% 7.00% 15%
35%
10%
Quality Requirements for Recycled Materials, MnDOT
Requirement Classes 1,2,3,4,5,5Q and 6 Maximum Bitumen Content of Composite 3.50% Maximum Masonry Block 10% Maximum Percentage of Glass* 10% Maximum Size of Glass* 3/4 in (19 mm) 10% for Class 5; 60% for Class 5Q; Crushing (Class 5, 5Q and 6) 15% for Class 6 Maximum Amount of Brick 1.0%/#
Maximum amount of other objectionable materials including but not limited to: wood, plant matter, plastic, plastic and fabric 0.3%/#
Source: TRB webinar