
16 minute read
Aggregates Help Pave the Road Forward
A look into scope 3 emissions reductions for aggregates sourcing
The Plattsburgh location for Colas Inc. boasts an efficient layout for optimum traffic patterns, most efficient fuel use, and least amount of dust production. Photo courtesy of Colas Inc.
ABY SANDY LENDER At the World of Asphalt/AGG1 combined conferences and tradeshows in Nashville this spring, multiple vendors showcased their offerings for introducing a new—or enhancing an existing—recycling component to your vertically integrated asphalt operation. Whether that takes the form of crushing recycled asphalt pavement (RAP), adding a cold central recycling plant to your equipment fleet, or one of the many other recycling related technologies and methodologies practiced within our industry, the options presented in both educational seminars and across the sold-out tradeshow floor gave attendees plenty of opportunity to consider how the new technologies and methodologies could assist on The Road Forward.
Vertically integrated contractors investigate more than their recycling operations. Quarry managers seek new and enhanced options for lowering a carbon footprint and raising an environmental credit score, within the framework of doing business before and after The Road Forward’s launch.
THE SCOPE OF AN INITIATIVE
The Road Forward is the initiative the National Asphalt Pavement Association (NAPA) set for the industry during its 67th annual meeting in Scottsdale. The plan outlines four industry goals to achieve net zero carbon emissions by 2050 that include: • achieving net zero carbon emissions during asphalt production and construction by 2050 (scope 1 emissions); • partnering with customers to reduce emissions through pavement quality, durability, longevity, and efficiency standards by 2050 (downstream scope 3 emissions); • developing a net zero materials supply chain by 2050 (upstream scope 3 emissions); and • transitioning to electricity from renewable energy providers in support of net zero carbon electricity generation by 2050 and reducing electrical intensities (scope 2 emissions).
For this article, we’ll focus on the third bullet point and its further explanation from NAPA’s printed materials, which state: “Supplier partnerships and net zero commitments are critical for the industry to achieve net zero carbon emissions. What the industry asks of and gets from its suppliers counts toward its own net zero goal.”
The tactics for accomplishing this third industry goal include, but are not limited to, engaging “with upstream suppliers to accelerate emission reductions in the material supply chain.”
While the National Stone, Sand, and Gravel Association (NSSGA) declined to comment on how its membership is assisting the asphalt industry in lowering its upstream scope 3 emissions to develop a net zero materials supply chain by 2050, there are copious examples available of aggregates producers already participating in environmental stewardship best practices and emissions reduction. As mentioned above, original equipment manufacturers (OEMs) are supplying the equipment to help. Materials suppliers are on point as well.
One example outlined in the August 2020 issue of AsphaltPro showed O&G Industries, Torrington, Connecticut, had not only in-
stalled the first of three solar panel arrays for its Southbury quarry, but the company was leading the way as the first asphalt company to sign up for the ENERGY STAR® industrial program with the U.S. Environmental Protection Agency and NAPA’s pilot project. And as you’ll see herein, aggregates managers and suppliers are doing their part to reduce emissions in an already low-emissions industry.
Joseph Shacat, director, sustainable pavements for NAPA, explained: “The good news is that the carbon footprint of aggregate production tends to be very low...”
Even with a low carbon footprint, the aggregates industry is an important one for partnership.
“Even though aggregates make up the bulk of an asphalt mix by weight, their impact on the overall carbon footprint of an asphalt mix is minimal in most cases,” Shacat continued. “With that said, we recognize the importance of engaging with upstream suppliers to the industry and we had a good initial conversation with NSSGA on this topic during World of Asphalt in March. “We’re also making efforts to align the environmental product declaration (EPD) programs between the two industries where feasible and appropriate. For example, during the recent revision of the Product Category Rules (PCR) for Asphalt Mixtures, we adopted the allocation approach for slag aggregates as defined in the PCR for aggregates. Two of the members from NAPA’s PCR Committee are currently serving on the PCR Committee for aggregates, with one of them actually serving as the chair.”
MITIGATE INDIRECT CONSEQUENCES
NAPA is also looking at the indirect effects of aggregates on emissions, such as absorption rates and residual moisture content requiring additional binder contents and additional drying times, respectively. Shacat explained this.
“Although the carbon footprint of aggregate production is fairly low, the indirect effects of aggregates tend to be more significant. For example, highly absorptive aggregates require a higher asphalt binder content, which can have a bigger impact on the carbon footprint of an asphalt mix than the aggregate itself. Another indirect impact is the residual moisture content of washed aggregates, which increases the amount of energy needed to dry the aggregates during asphalt mix production.”
One of these concerns is being addressed by Colas Inc. and is discussed below.
“Emissions associated with transporting aggregates can also be significant, depending on the distance between the quarry and the asphalt plant, as well as the transportation mode utilized,” Shacat continued. “In markets with limited availability of local aggregates, the most effective emission reduction strategies from an asphalt mix perspective center around reducing the impacts of aggregate transport. In these markets, emission reduction tactics include use of alternative transport modes (rail or barge), and use of locally derived RAP and other recycled aggregates.”
Seminars over the past few years have introduced the concept of modifying mix designs to incorporate local aggregates to not only reduce costs for agencies but also to reduce transportation-related emissions. If a local aggregate can be proven to perform, an agency may be convinced to make a spec change to a project.
Take the AASHTO PP83 for micro surfacing mix design as one example. Even before a pre-construction meeting, owner agencies will take into consideration changes to the mix design. Jim Moulthrop, a past executive director for the Foundation for Pavement Preservation (FP2) and an author of the Transportation Research Board’s (TRB) “Guide Specifications for the Construction of Chip Seals, Micro Surfacing and Fog Seals (NCHRP 14-27),” stated during a TRB webinar that field adjustments to the micro surface mix design are allowed if they are within the overall tolerances set forth in the job mix formula (JMF); changes can be submitted to an owner agency for consideration before work begins.
In other words, if a contractor or agency needs to submit a change order to incorporate a local aggregate for the purpose of reducing
WEB EXTRA
Learn how a Harsco Environmental company incorporates slag in the United Kingdom with “SteelPhalt Gives Slag a Second Life” from the February 2022 issue. https://theasphaltpro.com/articles/ steelphalt-gives-steel-slag-a-second-life/
LEARN MORE
Track the Scope of Legislation
Normative, a company that partners with climate change organizations, has launched an app to help businesses stay compliant with fast changing carbon legislation in the European Union, United Kingdom and United States. The free software is a carbon legislation tracker, which covers existing and upcoming legislation in some of the main markets for many businesses, including: • The EU’s CSRD, which will require all large EU businesses to report their full scope 1, 2 and 3 emissions; • The UK’s TCFD and SECR, requiring all large UK businesses to report emissions, including scope 1, 2, and (in the case of TCFD) very often also scope 3; and • The SEC’s recent proposal, that would require all publicly traded U.S. companies to disclose scope 1, 2, and typically also scope 3 emissions.
“Staying up to date with the changing legislative environment can be tricky. That is why we developed the tracker, to make carbon accounting accessible and easy for all businesses,” explained Kristian Rönn, CEO and co-founder of Normative, the world's first carbon accounting engine and the organization behind the tool.
The Carbon Legislation Tracker will be continuously updated to deliver a real-time snapshot of the legislative environment.
Normative provides science-based carbon accounting software and tailored advice from net zero experts, enabling companies to reduce their carbon footprints. “Many businesses want to do well but lack the resources or knowledge to do so, and this can result in involuntary greenwashing. At Normative we want to help enterprises and their value chains to do the right thing with accurate and truthful carbon emission accounting,” Rönn concluded.
For more information, visit https://normative.io/ carbon-legislation/.
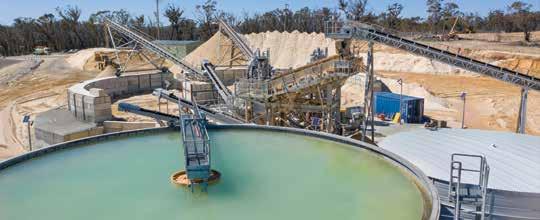
Dossing sludge with flocculant increases the speed at which clean water can be recycled back into the wash plant for Clarence Sands, Sydney, Australia. Photo courtesy of Terex Washing Systems
transportation-related emissions, this is not unheard of. The onus will be on the agency, of course, to ensure the local aggregate can perform as well as the original/specified aggregate to achieve the long-lasting pavement or treatment, which would lead us to the second bullet point in our list above—downstream scope 3 emissions. No one wants to trade one emissions source now for a worse emissions source later.
SUPPLIERS LESSEN DIRECT EMISSIONS
“As for direct emission reductions for aggregate production, the most effective strategies will likely focus on electrifying processes that rely on combustion of fuels, such as heavy equipment operation, and purchasing electricity from cleaner sources,” Shacat said.
As mentioned above, O&G Industries was leading the charge in clean electricity sourcing with its first of three solar arrays in 2020.
The team at Colas USA, with headquarters based in New Jersey, has committed to reducing its CO2 emissions by at least 30% by the year 2030, according to Brent Morrey, director of aggregate performance for Colas Inc. He shared specifically that this is a group initiative to reduce the company’s carbon footprint and an objective that has been launched in all countries and within all business activities in which they operate, including aggregates.
Morrey wrote: “Over the last few years, Colas has embarked on a journey to strengthen its overall aggregates position, which includes improving plant efficiencies and taking a more proactive role in reducing both energy and water consumption at our facilities. Although quarries have a much smaller carbon footprint to other construction materials activities, there are still many ways we can reduce our environmental impact, and actions are currently underway within all our subsidiaries in the United States to do just that.”
Shacat pointed to measuring or analyzing a company’s status as something NAPA has noticed. “One example of a trend that we are seeing with some of the publicly traded, vertically integrated companies in our industry is an effort to improve their approaches to quantifying GHG emissions. For example, Granite Construction’s 2021 Sustainability Report discusses their efforts to improve the data collection processes. They are also expanding the scope of their GHG emissions reporting to include scope 2 emissions, the upstream emissions associated with purchased electricity. Similarly, the Summit Materials 2021 Sustainability Report indicates that they’re measuring energy consumption to improve energy efficiency in aggregate production. This underscores the notion that you can’t manage what you don’t measure, so the first step in reducing emissions is to establish a baseline that can be used to measure progress.”
The Colas Inc. team started with an analysis approach to determine the optimum way forward.
Morrey wrote: “It is no surprise that the largest share of energy in our quarries comes from fuel, even when excluding outbound freight. Before jumping to new technologies and equipment, we first wanted to analyze the layout of our operations in general and to look for ways of reducing haul distances involved in moving materials. This simplistic approach has resulted in a significant reduction of fuel and overall energy consumption. Over the last two years, modifications were made to many of our sites including changing internal traffic patterns, rebuilding haul roads and ramps within the quarries, and moving processing equipment closer to our extraction zones. Some of our installations are quite old and although they are well maintained and run perfectly well, they may have been built without thinking of the things we are today in terms of carbon footprint. Stockpiling is a great example of this, where we are looking at conveying and stacking systems to increase our stockpile capacities and in turn, minimize or eliminate the use of loaders and trucks to stock finished materials.
“The most obvious thing that everyone thinks of when it comes to carbon reductions in our business is the replacement or conversion of trucks and loaders to ones that are more energy-efficient, such as hybrid and/or electric machines. We are looking at this and we have a couple such units within our fleet today that are working out great. We do realize however that we cannot change all our machines at once, and we are working together with our suppliers to help identify the most energy-efficient equipment for our applications. We also want to ensure that we are using the right-sized equipment that matches the production and shipping goals we intend to meet. Given some of the changes mentioned above, we have been able to reduce our total fleet needs and been able to downsize some of the machines that were historically in use. This has been a complete shift in mindset from the ‘bigger is better’ notion that may have existed in the past.
“When it comes to water usage, we are continuously looking at ways to reduce our consumption. We are looking at areas where traditional washing of aggregates can be replaced with a dry processing solution, and we have eliminated the need for water completely at a few of our locations. In some of our deposits, however, this has proved challenging, and so ways to consume less water in the process and reduce the water content in our finished products are then explored, which is also something that is welcomed by our customers. We continue to develop water recycling solutions at our facilities, especially at our sand operations, and in areas where water has become scarce. Simple things such as minimizing the number of transfer points by reducing the total number of conveyors at some of our larger facilities has also resulted in less dust creation, and the need for water for dust control is obviously reduced if there are fewer of them to begin with.
“Colas just hosted a global convention in Montreux, Switzerland, with the theme ‘Colas in Motion’ reinforcing our CSR corporate objectives launched in 2021 with A.C.T., which stands for Act and Commit Together. We got to see many ways in which our sister companies all over the world are tackling such important topics including energy consumption and energy production within our aggregates portfolio. Much is being done on a global scale within Colas when it comes to solar-power generation, and also in the use of gravity force to help power conveying systems. We have over 20 ongoing projects in France, Indian Ocean and the UAE that involve contributing power to a grid, and in some cases where the energy produced on site is being used to help power our processing facilities.
“We are not yet 100% carbon neutral, but there are many things our company and our subsidiaries are doing that are steps in the right direction, which not only provide environmental benefits, but economic ones as well. Working in a global company under a decentralized structure has allowed us to find creative solutions to a common issue. Our objective is the same, but how we get there may be different. There is a strong combination of eagerness and optimism on this topic within Colas, and I’m excited to see what the next few years will bring as our operations continue to be transformed.”
For the industry overall, the next few years promise to bring clean and pristine operations across the board for asphalt and aggregate operations. That translates to excitement for some, anxiety for some, but opportunity for all. That opportunity should see an industry marching toward climate stewardship optimization with suppliers like those in the aggregates industry easily assisting in net zero materials supply chain goals.
LEARN MORE
Recycle Water for Sand Processing
Clarence Sands, Sydney, Australia, installed a sand washing plant from Terex Washing Systems for its sandstone deposit located in the Blue Mountains. The bespoke design of the plant can produce up to 300 tonnes of sand per hour and recycles roughly 90% of the water used during the washing process.
A wash plant can’t do its job without water, which can be a difficult resource to manage in Australia. Terex Washing Systems advised the customer of the need for a water management system that would be both environmentally friendly and save on running costs.
To begin, the wash plant features a H30 feeder that receives the raw sandstone feed material and distributes it evenly on the main conveyor. At this point any stones or rock that are larger than 100 mm are removed from the feed material due to the grid covering the feeder.
The sand on the main conveyor makes its way up to the modular 20 x 8 two-deck rinser screen. A total of 19 spray bars gives the material an initial rinse as the vibrating screener shakes the sand and stone down through the polyurethane decks as it is classified by size. Any larger aggregates can pass through the screen onto oversize conveyors where they are stockpiled as products for sale.
Any sand, silt, clay or other fine impurities that were present within the feed material are washed to the split catchbox of the screener. The material is gravity fed into one of two FM 200C sand plants. Each sand plant receives a separate split—one coarse sand and one fine sand. For this application the standard units were upgraded to separators, rather than the standard hydrocyclones. This was done to cope with larger volumes of fines, as well as to deal with potential variation in feed stocks. Separators use centrifugal force to remove the sand from the silt and clay so that it can be transferred onto the high frequency dewatering screens. These dewatering screens remove the remaining water within the sand so that only 10-15% of water is left. The sand that is now up to spec is then transferred onto a 26-metre radial stacking conveyor that offers a large stockpile capacity.
The water that, up until this point, has been used to initially rinse the feed material, wash the sand within the FM 200C and has been recovered from the dewatering screen, is pumped into the 17-metre rake thickener tank. The rake thickener allows the silt and clay particles within the sludge to settle at the bottom of the tank, while the clean water weirs over the edge to be re-used. The integral scrapers aid transportation of material from the outskirts of the tank to the outlet, thus accelerating the removal of sludge from the thickener.
This process is sped up with the use of a flocculant dossing unit, which dosses the sludge on its way to the rake thickener. The flocculant that is added to the sludge causes the waste particles to bind together, creating a particle with a larger mass, which then sinks to the base of the tank faster. Dossing the sludge with flocculant increases the speed at which the clean water can be recycled back into the wash plant.
For more information visit www.terexwashing.com.
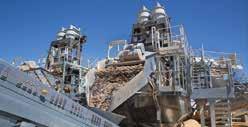
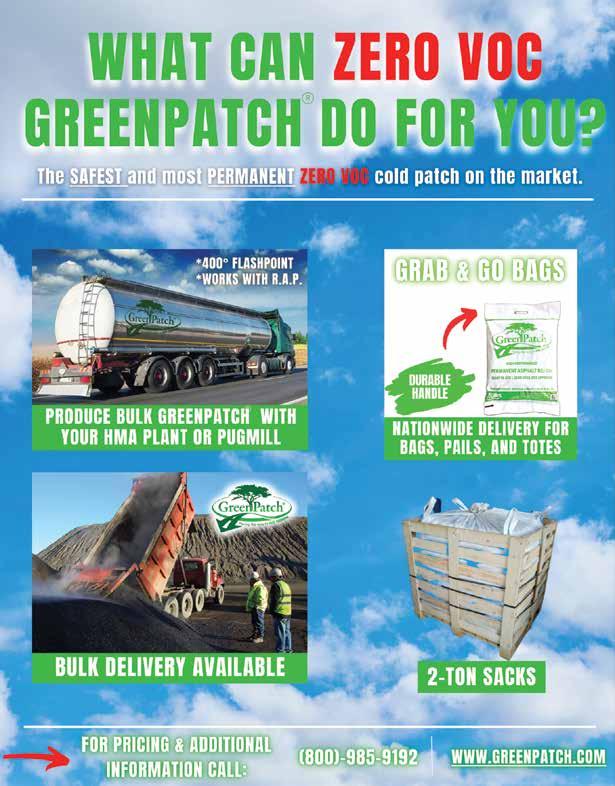