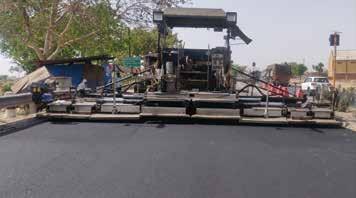
19 minute read
Sripath PGXpand® Used to Reduce Rutting in India
Bitpath Pvt. Ltd., located in Mumbai, India, is an affiliate of Sripath Technologies LLC, New Jersey, USA. Recently, Bitpath and PATH India Ltd. successfully completed a roadway trial, incorporating PGXpand modified bitumen into the wear layer, on a four-lane kilometer stretch of the Agra-Gwalior Highway in India. Lion Engineering Consultants were retained by National Highway Authority of India (NHAI) to assist with the project.
Sripath® develops, manufactures and markets a range of innovative additives used to enhance performance of bitumen. Sripath is a global company, with offices, affiliates and agents in USA, India, Australia, UK, Brazil, and South Africa. PGXpand®, a specially engineered polymer, is designed to interact with bitumen in a very unique and innovative manner. PGXpand enhances high temperature properties of bitumen without impacting low temperature properties. “PGXpand delivers outstanding rutting resistance, fatigue properties, long-term durability, and overall roadway performance,” said Krishna Srinivasan, president of Sripath Technologies. Prior to the field trial, PGXpand was evaluated by PATH India and an independent renowned research facility. Based on this evaluation, a mix design for the field trial was finalized and approved. According to Sachin Raje, general manager of Bitpath, “PGXpand is highly dosage efficient, about 1.5 weight percent of PGXpand was added to a VG30 grade bitumen for this trial to create a PMB. The mix based on this PMB was used to pave a 30-mm wear layer on a 4-lane-km stretch of the Agra-Gwalior highway near Morena, Madhya Pradesh, about 40 km from Gwalior.” The Agra-Gwalior Highway is part of major arterial expressway connecting the northernmost tip of India to its southernmost tip. Gwalior is a major city in the State of Madhya Pradesh, about 120 km south of Agra and 340 km south of New Delhi. The highway is subject to heavy truck and vehicular traffic all year round and is exposed to high air temperatures, in excess of 45 degrees C, for extended periods of time. “Rutting has been our main concern on this highway,” said Mr. Dharmendra Mishra, quality control manager, PATH India. He further stated: “With PGXpand, we hope that our problem is resolved successfully.” PGXpand was easy to incorporate into the bitumen, mixed within one hour at a temperature of 160 degrees C. The polymer lowered the viscosity of the bitumen and allowed for reduction of the paving temperature from 160 to 130 degrees C. Overall, it was helpful in reducing both energy consumption and overall costs. “The PGXpand Modified Bitumen trial was very successful. It was hassle-free to manufacture the PMB and the Mix, it was simple to transport the Mix to the site, and the roadway was easy to pave. We are waiting for the post-trial evaluation results and, if everything looks good, we will surely use PGXpand on our other projects”, remarked Mr. Nakul Agarwal, Project Head, PATH (India) Ltd.
Samples of the loose mix, PMB, and post-compaction field cores were collected and submitted to the independent research facility for evaluation and testing. The Agra-Gwalior Highway section from the marker at 71 Kms to the marker at 69 Kms, when travelling from Gwalior to Agra, will be monitored over the next few months to gauge the effectiveness of the trial. Deepak Madan, Chief Marketing & Business Development Officer at Sripath Technologies elaborated on other applications of PGXpand, he said: “PGXpand is also used to manufacture hybrid PMB systems, allowing engineers to design mixes with lower levels of elastomeric polymers while delivering better or equivalent roadway properties. PGXpand Modified Bitumen can also be used in hot spray seal applications on roadways, allowing for improved workability and better performance. PGXpand Modified Emulsions are used for repair and maintenance applications in the paving industry to deliver long-term durability and reduce frequency of road repairs.” “PGXpand has been tested, evaluated, and vetted by leading experts in academia, industry and transportation agencies from around the world. It has been trusted and effectively used on roadways across the globe since 2015.”, remarked Sachin Raje, General Manager of Bitpath.
For more information, visit https:// sripath.com
Sripath PGXpand® modified bitumen is placed on a field trial to improve rutting performance of a major highway in India.
B2W
B2W Software, Portsmouth, New Hampshire, has added application programming interface (API) features to its B2W Estimate platform to automate data transfer for customers. The API feature automates connectivity between B2W Software’s flagship estimating application and data sources used to generate estimates. The API also enables a new Production Rate Actuals feature within B2W Estimate, giving estimators streamlined access to current and historical performance data from the field. The information from B2W Track, an application for field tracking and analysis, can be used to improve accuracy of rates applied within current bids.
“The B2W Estimate API allows our users to create automated connections between the B2W Estimate database and other systems like accounting, bid collection and contact management applications,” explained Pat Reitz, product manager for B2W Estimate. “This eliminates the need to enter the same data in multiple places and ensures that all systems are always up to date with each other.”
Reitz cited automated updating and retrieval of labor rates, equipment rates and burdens as examples of how the API can eliminate the need to search for and enter data. The API can also automatically update pricing and other information from organizations such as vendors and subcontractors and keep job-cost identification codes up to date and in sync between estimating and accounting systems.
For more information, visit the B2W website.
BOMAG
Bomag, Ridgeway, South Carolina, has released the BOMAG BM 2200/65 large planer, weighing in at 60,296 pounds for halflane milling. It has a 58-inch milling radius. Its conveyor offers a 16-foot discharge height plus larger, 130˚ conveyor slewing angle—65˚ to the left/right of center—allowing material to be discharged into trucks on both sides of the mill. To facilitate transport, the conveyor retracts to a length 23.6 inches shorter than previous designs. The mill’s 630-horsepower engine meets Tier 4 Final/Stage V emissions standards, according to the manufacturer.
The slim profile of the BOMAG BMS15L quick-change cutting tooth holder system is designed to reduce resistance and deliver up to 20% fuel savings. The BM 2200/65 planer offers a range of milling drum designs and the choice of three different rotor speeds to tailor rotor speed to a range of asphalt and concrete milling jobs. The manufacturer states: “To simplify milling control, BOMAG Easy Cut technology automatically regulates the height of the rear drive, so the rear of the machine follows the front to its set depth, making the operator’s work simpler. BOMAG Easy Level clearly displays grade and slope settings on the large 7-inch display, and settings are quickly changed with minimal screen navigation.”
The standard water spray and dust extraction systems, complete with conveyor shrouding, remove fine particulate matter from the machine. Removing up to 80% more fine dust particles smaller than 10 microns in size, the optional Bomag Ion Dust Shield—described in the July 2021 issue—is a pioneering technology designed to meet stringent fine dust regulations.
For more information, contact your local Bomag dealer or visit www.bomag.com.
CASE
CASE Construction Equipment, Racine, Wisconsin, expands its dealer network with the opening of a new 48,800-square-foot facility in Little Elm, Texas, and with two new facilities in Asheville and Leland, North Carolina. with focus on new equipment sales, rental and service.
ASCO Equipment Company (ASCO) has opened the facility in Little Elm to provide the growing Dallas-Fort Worth metroplex and Denton County with additional service, support, and equipment sales and rental. The new facility will be the largest of ASCO’s 24 locations with an expansive showroom dedicating 15,000 square feet to sales and rental, 25,000 square feet to a service shop with 14 super bays and so on.
The Hills Machinery dealer has opened two new facilities in Mills River and Leland, North Carolina, to focus on new and used equipment sales, rental, support, service and parts access. Both new locations are now open, provide opportunity for expansion and strengthen the CASE dealer network in the Southeast.
CM LABS
CM Labs Simulations, Montreal, Quebec, has announced the release of its Compact Track Loader (CTL) Simulator Training Pack. It is simulation-based training that replicates machine instability and lift clearance. The vertical lift CTL training pack comes with fork and bucket attachments with progressive learning exercises designed to gradually build the trainee’s skill and confidence. Trainees work on skills such as controls familiarization, addressing the risk of tipping, handling view-blocking material, live attachment changing, loading and unloading, dealing with difficult terrain, and working with small margins for lift clearance while dumping dirt into a truck.
The training pack runs on all of CM Labs’ simulator platforms, including the motion-enabled Vortex Edge Max, the fully immersive Vortex Advantage, and the desktop Vortex Edge Plus. Performance metrics are tracked during training exercises including safety violations, load control, and operational efficiency. The simulator training pack rounds out the range of CM Labs’ earthworks machines, making it ideal for training schools or companies with a wide range of equipment in their fleet.
“With no training certification required to run a CTL, operators are often at risk,” explained Alan Limoges, product manager at CM Labs. “With this in mind, we designed our learning program based on the most stringent labor competency recommendations to deliver the industry’s best training.”
For more information, contact info@cm-labs.com.
CRAFCO
Crafco Inc., an Ergon company, Chandler, Arizona, introduces two new equipment innovations for its melter/applicators. Crafco’s new Work Area Camera is designed to improve crew safety and efficiency by providing drivers towing any Super Shot™ Series, Patcher II
The BM 2200/65 cold planer from Bomag
CRUSH RAP COSTS
with the HONEY BADGER
From replaceable abrasion-resistant steel wear liners to a 1/2" steel pulverizing hopper, this machine is ready for wear and tear. And by reducing material handling and minimizing moisture, the Honey Badger increases production and saves on fuel costs. Average return on investment is 1/8 the cost of other crushing operations. Fully-equipped with max power, reliable operation, and easy maintenance, the Honey Badger is ready to crush your costs!
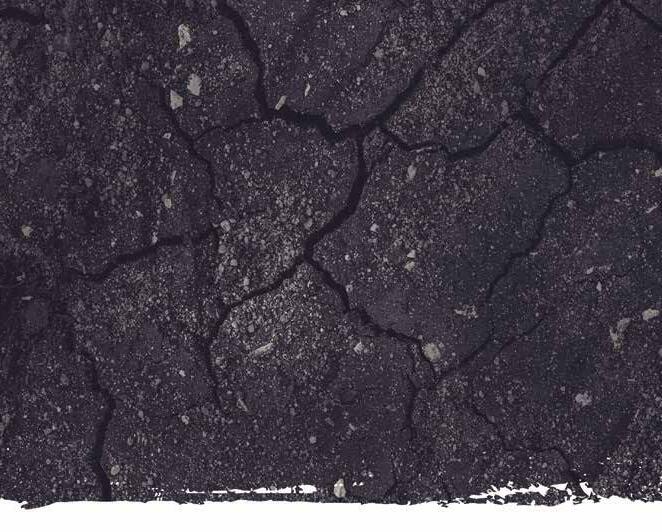
Reduced RAP moisture = lower fuel consumptions
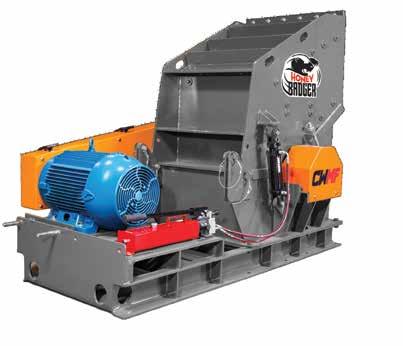
Reduce or eliminate crushing costs
Typical 6 month ROI
(300,000 ton/season plant)
Minimize material handling
STATIONARY PORTABLE

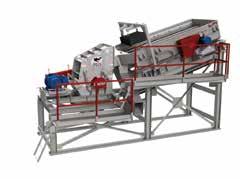
or EZ Series II melter with instant feedback on crew location.
The waterproof backup camera with infra-red night vision attaches to the rear of the melter, while the 5-inch LED digital monitor’s suction cup mount adheres to the towing truck’s windshield. The Work Area Camera provides live, wireless transmission so the driver can see what’s happening in and around the melter in real-time. The new Driver Alert System allows a crew member operating an applicator wand a more effective and efficient way to communicate with the team and driver towing any SuperShot or EZ Series II melter with an electric heated hose. A signaling device similar to a vehicle backup alarm, Crafco’s Driver Alert System releases a short, high-pitched tone that signals the crew and driver to move forward, stop, accelerate or slow down. The new Driver Alert System is powered by a conveniently located wireless switch easily adjustable to the operator’s dominant hand.
“Crafco melter/applicators consistently answer pavement preservation challenges through innovation,” said Crafco’s vice president of national sales and marketing, Tom Kelly. “Our Work Area Camera and Driver Alert System are two new equipment innovations that work to support safe and efficient crack sealing operations for contractors and agencies alike.”
For more information, visit www.crafco.com and https://ergon.com/sustainability.
DYNAPAC
The Swedish National Road & Transport Institute (VTI) confirmed the fuel-saving performance of the new CA3500D SEISMIC soil roller from Dynapac, xxxx.
In any compaction job, finding the right balance of factors for the best results has always been a science. The CA3500D SEISMIC soil roller, designed to achieve fast, cost-effective compaction while reducing both fuel and emissions automatically enables the roller to determine the optimum frequency for material to be compacted. At the heart of the system is an onboard machine control unit, as well as a next-generation compaction meter. This feature lets SEISMIC sense the dynamic characteristics of the material and then calculate the optimum frequency required for the best compaction results. The entire process is achieved using an advanced data flow from the SEISMIC Compaction Meter to the onboard machine control unit, which regulates the machine’s hydraulics. By working together with the soil, the SEISMIC feature applies the correct amount of energy where and when it’s required and hydraulically changes the vibration frequency, every 0.2 seconds for maximum performance.
The fuel efficiency performance has now been verified by the Swedish VTI, which supervised a series of fuel consumption tests on the CA3500D SEISMIC soil roller. It was tested in three different settings over a period of two weeks.
There are three different settings on the CA3500D SEISMIC: • Standard mode where the engine runs on high RPM and the vibration frequency is 29Hz in high amplitude and 33 Hz in low amplitude; • Eco mode where the engine runs on lower
RPS that is automatically adjusted to the engine needs; and • Eco + SEISMIC mode, which has a lower
RPM controlled by the Eco setting and automatically adjusts the vibration frequency to maximize the compaction effort.
The two test weeks were identical regarding procedures and were performed twice to validate that similar test results were reached. The results VTI measured showed a fuel reduction consumption of 28-35% compared to conventional compaction (fixed frequency). Moreover, they registered a good alignment with the onboard telematics, which reported savings of 36-38%. This means that under real job site conditions, there is an overall savings of around 55% to complete the job.
For more information, visit the Dynapac website.
ELGIN
Elgin Sweeper, Elgin, Illinois, has officially announced the new RegenX1®. The RegenX1 is a customer-driven design, mid-dump regenerative air street sweeper. The RegenX1® is a single-engine, truck mounted regenerative air sweeper designed to eliminate the work of maintaining two engines and the cost exposure resulting from “missed” auxiliary engine regenerations. The new sweeper also uses a dust separator and large screen surface area to reduce carryover and sand blasting.
A 56-inch roll-off container dump height with 50-degree dump angle and 8-cubic-yard hopper helps avoid double handling and reduces the need to drive back to the facility to dump. They also help avoid environmental ground-dumping restrictions. Additional features are designed to make it easy to clean, including a simple hopper with rounded corners and an external self-dumping dust separator.
For more information, visit the Elgin website.
FAE
The team at FAE USA Inc., Flowery Branch, Georgia, displayed four attachments for the paving and quarrying market during World of Asphalt/AGG1 2022 in Nashville. One of those attachments that the company suggested for use in the growing cold in-place recycling (CIR) market is the FAE MTL 225, a “light” version of the multi-task line, which includes the MTM and MTH machines.
These machines are a multi-function attachment that combine the mechanisms of a soil stabilizer, rock grinder, rock crusher and asphalt shredder in one compact machine. The MTL is designed to be compatible with a wide range of tractors on the market. It is designed for rock crushing and full depth reclamation (FDR) up to 11 inches deep.
The main features of the unit include: • A variable displacement chamber with technology that allows the ground to be penetrated with the hydraulically adjusted rotor while the skids maintain ground level for better depth control. This results in minimal traction stress, optimized fuel consumption, increased operational speed and homogeneously stabilized soil at all working depths, according to the manufacturer. • Adjustable Hardox® counter-blade. • Hardox steel wear plates. • Rear grids to optimally control the size of the output material. • Dozing blades with spring system to further level and compact the crushed material into a uniform base. • Two options for water spray system with dual function of cooling and mixing. • Multiple tooth options. • Optional hydraulic top link.
For more information, call (770) 407-2014.
FLEETWATCHER
Earthwave Technologies, Indianapolis, offers the FleetWatcher telematics platform to monitor four key safe driver metrics, allowing companies to track and amend driver behavior. This GPS-based platform captures vehicle
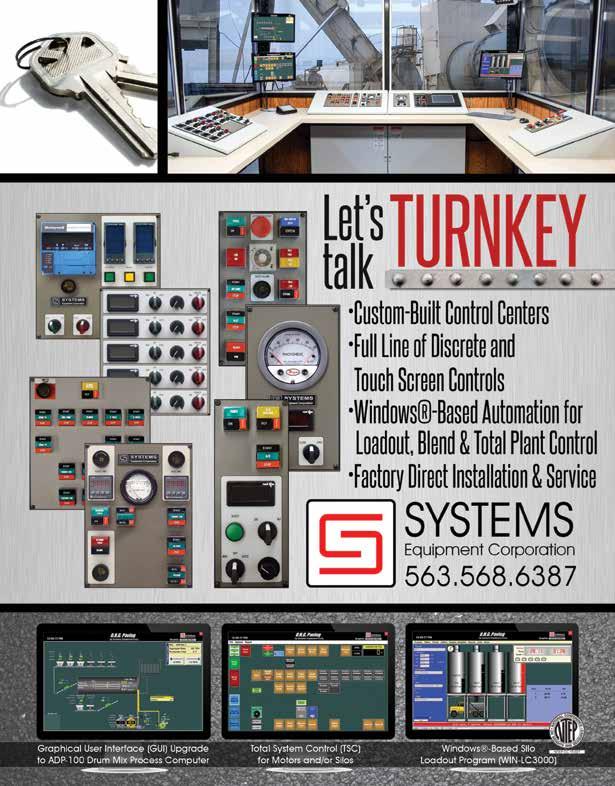
data from either the FleetWatcher App or from an in-vehicle device. It simplifies safe driver programs by focusing on four key metrics: • vehicle speed relative to posted speed limits; • fast starts; • hard braking; and • hard turns.
This data is reported continuously and can be used to assign a numeric or letter grade to drivers, who can then be commended or counseled for their performance. Whether required by insurance carriers or as company policy, FleetWatcher customers using this feature have reported significantly improved driver grades when this is added to their safe driver programming.
Speed, which is continuously monitored, can be categorized by vehicle type. For example, a pickup truck driving up to 10 MPH over the posted speed limit may be deemed OK (shown in green), while 11-15 mph over is unsatisfactory (shown in yellow), with anything over 15 mph over the speed limit flagged as excessive (shown in red). A tri-axle dump trailer, on the other hand, may be deemed safe while travelling up to 5 mph over the speed limit, with anything over that flagged as excessive (shown in red). Speed ranges and grades are assigned by user administrators and can be varied by vehicle type.
To assess hard-braking, fast stops are also monitored, as are fast starts and hard turns. Each are similarly assigned numeric or letter grades. Administrators can select how important the various safe driver aspects are, and how to aggregate them into an overall score, which can then be used in driver counseling.
For more information, visit the FleetWatcher website.
HAULHUB
HaulHub Technologies, Boston, announced the United States Patent and Trademark Office has issued a notice of allowance for its patent application, serial number 17/513,745. This patent application is directed to the use of a digital chain-of-custody system for construction materials that is resilient to wireless connectivity disruption. HaulHub reported on its website: “State transportation agencies nationwide are leading the charge to implement e-Ticketing as a standard operating procedure on construction job sites across the United States. However, the United States Department of Transportation (USDOT) estimates that 68% of the nation’s lane miles are in rural areas, often the same areas which lack reliable cell phone coverage, ensuring operational connectivity is still a massive challenge and prevents technology adoption.”
“DOT field staff need a reliable solution they can use under any circumstance. Even job sites with 5G phone service still lose internet access from time to time,” said Joe Spinelli, HaulHub’s CEO and founder. HaulHub’s DOTslip application, relies on the newly allowed patent application to ensure that the inspector can accept, reject, and record quality information or other load details without reliance on internet connectivity, allowing the project to continue seamlessly.
HaulHub’s technology is designed to ensure that industry participants have an easily accessible, reliable and cost-effective solution that works on all job sites. The newly allowed patent application more specifically covers the ability for any information about the load to be used to reconcile the work performed by the inspector into the chain of custody for construction materials. This innovation goes beyond connectivity issues, as it also directly aligns industry participants with Federal Highway Administration’s (FHWA) objectives and guidelines for using e-Tickets as source records for payment on Federally funded projects.
The underlying technology covered by the newly allowed patent application is designed to work in tandem with the technology behind US Patent No. 11,210,635 to provide simple, inexpensive, and intuitive options for supply chain stakeholders to participate.
For more information, visit the HaulHub website.
JOHN DEERE
John Deere and Wacker Neuson will collaborate on the development of excavators less than 5-metric-tons, including battery electric excavators, that will be manufactured by Wacker Neuson. Additionally, John Deere will have control of the design, manufacturing and technology innovation, for the 5-9-metric-ton models.
Distribution, parts, service and support will continue through the John Deere dealer network.
“We’re excited about the expanded agreement as it supports our goal of bringing productivity-driven features and industry leading technology to customers with greater agility,” said Jerred Pauwels, vice president, excavators, strategy and business development, John Deere. “Through this relationship, we’ll innovate faster, and offer additional features and performance differentiation for our customers.”
The Wacker Neuson Group is an international group of companies headquartered in Munich, Germany, employing around 6,000 people worldwide. As a leading manufacturer of light and compact equipment, the Group offers its customers a broad portfolio of products and a wide range of services.
For more information, visit your local John Deere dealer.
SEALMASTER
SealMaster Pavement Products & Equipment and Pioneer Industrial Systems (PIS) have introduced the CrackPro Robotic Maintenance Vehicle (RMV). Minimizing labor and keeping crew members off the road, it requires a driver and a person who stays on the back of the unit to monitor application and replenish the crack sealant.
The CrackPro RMV’s AI vision system measures and scans cracks, controls material flow, communicates with a robotic arm, and guides the wand and shoe of the heated hose to dispense crack sealant, after the automated blower system cleans cracks for sealing.
The RMV features a full truck chassis, equipped with a FANUC R2000 robot, generator, integrated blow-off system, custom Crack Pro 260, LED safety lights and rear safety cage to alert drivers.
Todd Hendricks of PIS came up with the concept when he saw a crack sealing crew on his way to work in late 2019. Then, he proposed a challenge: “How could we apply our robotics expertise to increase safety and efficiency in routine road maintenance?” The company soon established its RMV division, and ultimately partnered with SealMaster on the venture.
For more information, visit the SealMaster or PSI websites.
THE TANK
100 YEARS OF DOING IT BETTER
WE ARE A UL-142, ASME SECTION
VIII AND API APPROVED TANK
MANUFACTURER. Our facility is quality control inspected by
Underwriter’s Laboratories four times per year.
WE ARE A LICENSED MANUFACTURER
FOR THE STEEL TANK INSTITUTE (STI). We are the recipient of STI’s
Quality Award 16 consecutive years and inspected two times annually.
ALL ASPHALT TANKS ARE BUILT
TO THE UL-142 CONSTRUCTION
CODE. We keep records of the steel purchases, welding practices, pressure tests and other quality control measures.
WE USE 6” INSULATION ON TOP
AND SIDEWALLS OF OUR TANKS.
The bottom of our tanks are insulated with foam glass block.
ALL OF OUR SHELL JOINTS ARE
DOUBLE BUTT WELDED AND NOZZLE
JOINTS SEAL WELDED INSIDE AND
OUT. 100% Welded - The strongest union of two pieces of steel possible.
WE ARE CONSTANTLY IMPROVING
OUR TANK DESIGNS. The only way to keep our tanks better than any other tank on the market!
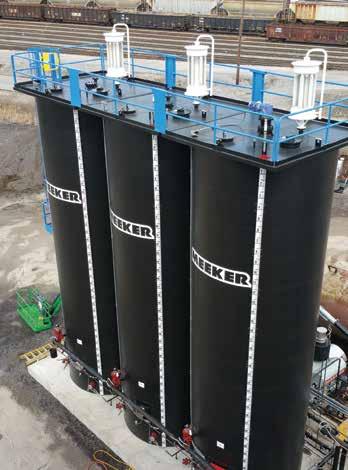
Call us toll free! (888) 333-0323
www.meekerequipment.com
Your Preferred Asphalt Equipment Resource Contact Information
Meeker Equipment Headquarters 4381 Front Mountain Road Belleville, PA 17004 Phone: (717) 667-6000 Fax: (717) 935-2389 E-mail: info@meekerequipment.com