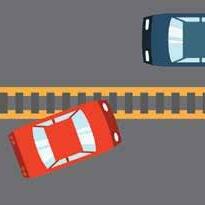
5 minute read
International 3D Parts
BY ASPHALTPRO STAFF
Additive manufacturing of parts could someday upend the supply of components globally. A small-scale trial of 3D manufactured parts is helping Sandvik Mining and Rock Solutions and Swedish mining and metals company Boliden explore the potential.
It’s no secret additive manufacturing—or 3D printing—is a maturing industry. The practice has progressed from printing plastic components for proof-of-concept parts and casts, as discussed in-depth in the article “Here’s How 3D Fabrication Enhances Asphalt Processes,” to now being able to print ceramics and metals. To discover the potential of the technology, Boliden and Sandvik announced prior to World of Asphalt/AGG1 2022 that they’ve teamed up to run a trial to discover the potential of the technology for machine parts printed digitally and installed on underground drill rigs.
OUR COMMON PAIN POINTS
Delivering drill rigs, slat conveyor sprockets, or other parts to remote areas where quarries or asphalt plants are often located isn’t always easy. Now add in a global shortage of key components such as semi-conductors, bottlenecks in transportation, COVID-19, soaring freight and material prices, and so on.
Robert Van der Waal is the vice president of logistics at the parts and services division within Sandvik Mining and Rock Solutions. His job is to make sense of the madness in the logistics sector and ensure customers get the parts they need.
“In 20 years, I’ve never seen anything like it, the whole world of logistics has been turned upside down,” Van der Waal said. “We just need to figure out how best to operate in this new dynamic.”
With the introduction of a new warehouse management system at its central distribution center in Eindhoven, Netherlands, Sandvik is on track to reshape its supply chain to suit the new dynamic, with the support of up-to-date systems, according to Van der Waal.
With the Eindhoven facility pushing out 40% more volume than before the system upgrade, as of April 12, even products stuck in ports such as California’s Long Beach and China’s Yantian were slowly moving through the supply chain. Geopolitics was still causing headaches, such as Mali closing its borders after a recent military takeover, meaning mines couldn’t be supplied via standard routes.
Van der Waal explained the company has changed its shipping methods to keep customers supplied. “In the past we sent 40% by air, 40% by sea and 20% by road—now as much as 70% of parts are being flown in. This is faster but the costs are enormous.”
It’s not just the cost of freight rising.
Everything from screws and bolts to the wood used for packaging is increasing in price. Ocean freight prices have skyrocketed from roughly $2,000 a container a few years ago to $18,000 today, and while Sandvik is absorbing much of these increases, the pressure is on. With even next-day couriers facing challenges, Van der Waal sees the need to adjust supply chains to still provide customers with the right product at the right time. “Where historically a supply chain was built around efficiency, the disruptions due to the pandemic and new market dynamics makes companies, including Sandvik, transform their supply structures to make them much more robust. Ones that are better able to handle disruptions and unexpected disturbances,” he shared.
That robust structure includes getting back to basics. New technology and processes undoubtedly have a role to play in ensuring Sandvik’s parts and equipment get to where they are needed. But rather than take big leaps of faith in new technologies (such as Artificial Intelligence), Van der Waal is counselling caution, and a more “back to basics” approach.
“New technology is going to play an important part in our future success, but we will only take steps we know we can manage—no more leaps of faith in IT. Getting parts to our customers on time is too important a priority to take risks with.”
MAKE THE PARTS
The trial with Sandvik and Boliden involves a set of specially redesigned components printed digitally at a Sandvik-managed facility in Italy, with their performance being monitored on machines in Boliden’s underground mine worksites. The first components had been put into operation in the Garpenberg mine prior to WOA/ AGG1 2022, with performance still to be evaluated.
“Additive manufacturing shows a lot of potential, both in reducing carbon footprint within the supply chain, through reduced or eliminated need for transport and storage of parts and also shorter delivery times,” said Ronne Hamerslag, head of supply management at Boliden.
Although in theory any part could in future be 3D printed, it is likely to be maintenance and repair operating items that are the first to get the additive manufacturing treatment.
“If you ask me, it’s the most exciting thing that’s happening in the supply chain,” Boliden’s Hamerslag said. “Its efficiency, speed and climate friendliness mean that we have to investigate additive manufacturing closely. We are only at the proof-of-concept stage with Sandvik right now, but it’s already clear that it could become a game-changer for the spare parts business in mining—for both miners and equipment manufacturers.”
Time to Protect the Middle of the Road
Rumblestrips + J-Band + AMIGUARD = Longer Lasting Safer Roads
AMIGUARD™ is a rapid penetrating emulsion (RPE) that is specially formulated to penetrate quickly and thoroughly. Its reduced surface tension allows it to seep into the pavement voids quickly, so drivers can get back on the road sooner.
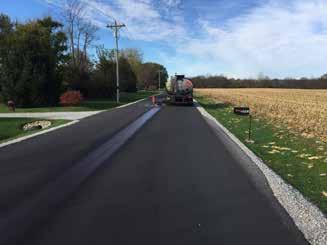
AMIGUARD Penetrate-CL and J-Band together can provide many years of protection for your pavements.
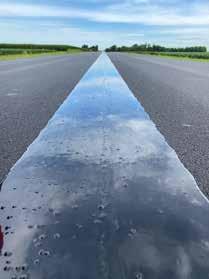
AMIGUARD should be applied soon after the rumble strips are ground. Centerline joints are particularly susceptible to air and water damage. For new pavements that will have rumble strips, it is critical to treat them proactively to avoid negative consequences in the future.
Applying J-Band®, an industry leading VRAM, at the time of construction, under the surface where centerline rumble strips will be installed, will reduce permeability in this most critical area.
This will extend the life of the joint and improve the performance of the entire pavement.
J-Band is a materials approach that is applied prior to paving under the eventual location of the longitudinal joint. As the hot mix is installed on top, J-Band migrates upward because of the heat and pressure.
Because of distracted driving, centerline rumble strips are becoming increasingly common. They can reduce head-on collisions by up to 50% and can be installed without compromising road life when J-Band and AMIGUARD are applied.
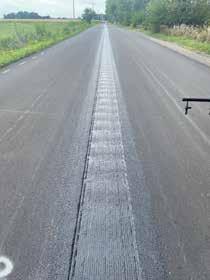