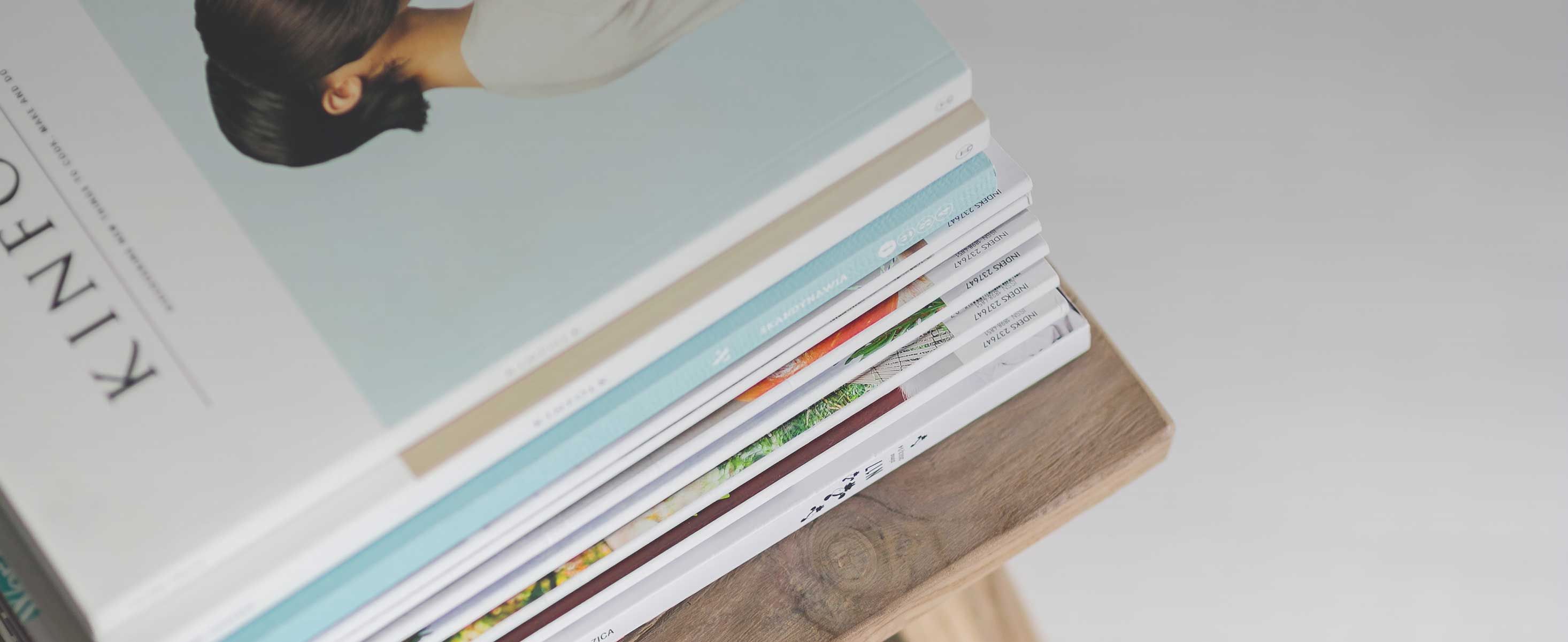
4 minute read
Zonar SightIQ Provides Aggregate Operations Analytics
Zonar’s SightIQ consolidates asset diagnostic and work site metrics to reveal areas to reduce cost-per-ton, drive uptime and unearth profits.
BY SARAH REDOHL
Zonar SightIQ is an analytics solution for construction aggregate operations launched March 2022 by fleet management solutions provider Zonar, based in Seattle.
The asset productivity and health solution aims to increase efficiency and cycle times in pits and quarries by delivering real-time insight into an operation’s equipment, machines and vehicles regardless of make, model, year, manufacturer or asset location.
“The future of construction-aggregate site operations is in leveraging not only more but better data and technology for improving the speed of business and growth of production while ensuring best practice safety and environmental conditions are met,” said Nick Grandy, general manager of vocational and industrial services at Zonar.
Grandy said these abilities have only become more important following the passage of the Bipartisan Infrastructure Law (BIL). “With the federal funding that’s coming, the aggregates industry will need to produce more material, which requires greater efficiency and more assets to monitor and maintain to meet those demands,” he said.
PREDICT & MAINTAIN
SightIQ includes both SightIQ Predict and SightIQ Optimize.
SightIQ Predict collects diagnostic information and OEM data from all assets within a fleet at multiple work sites in one continuous data stream, providing predictive and preventive maintenance guidance with asset health scoring.
SightIQ meets the Association of Equipment Manufacturers Professionals (AEMP) 2.0 telematics standard, pulling asset data from all major yellow-iron OEMs (including data for assets that do not have a factory ECM) into a singular unified view accessible through Zonar Ground Traffic Control.
“Typically, the customer would have to go to several websites to pull all the information they need,” Grandy said. “With SightIQ, all that information is available in one place.”
Grandy gave the example of a customer using SightIQ to monitor its loader. “The loader is the quarterback for the whole site,” he said. “If it goes down, it’ll stop production until a spare loader arrives or the existing loader can be repaired. This can result in thousands of dollars lost. With SightIQ, the shop could essentially predict what would happen next based on the codes they received. They knew that if a certain maintenance activity was delayed by a week, there was likely to be a breakdown in the pit and they'd lose money and time.”
Another customer was able to use SightIQ to identify why they were tearing up tires on one side of all their equipment. “The haulers were going too fast with a heavy load at too tight an angle,” Grandy said. With that insight, the company was able to mandate speeds and enforce a specific route through the area using traffic cones.
OPTIMIZE WITH EVIDENCE
The SightIQ Optimize feature set connects previously manually captured production study data with telematics and OEM data streams from all fleet assets to help increase productivity by reducing the cost-per-ton of aggregate while saving time and money with reporting on operator management, idle times and fuel efficiency.
To determine cycle time without SightIQ, Grandy said the foreman would have to sit in a truck at the bottom of the pit with a clipboard and stopwatch to check cycle times throughout the day. “There is a cost to having someone do that,” he said, “but there’s also the matter of it not being a true representation of cycle time if everyone is doing a particularly great job while the boss is watching.”
With SightIQ, cycle time is monitored constantly and automatically. Grandy said this can help a company more easily identify issues that might be causing delays. “Maybe you’re seeing bunching because the road down to the pit isn’t wide enough or the dump area for the plant isn’t big enough,” he said, adding that a company isn’t likely to spend money to correct such issues without proof they are causing a delay. “Bunching is a significant root cause of unnecessary idle time and fuel use.”
One customer invested in SightIQ for this very reason, to gather evidence that the site needed a new pit road to improve cycle time. “No one was listening to him, so he used SightIQ to prove it,” Grandy said.
Zonar has estimated, based on its customers’ experience, that even a 58-second longer cycle time can cost quarry fleets more than $180,000 in lost productivity per day. One customer was able to save 4 cents per ton for a total savings of $236,000 on 5.9 million tons since they began using SightIQ.
SIMPLIFY & STREAMLINE
Another benefit of SightIQ, Grandy said, is the simplicity and customizability of the platform’s user interface. “Our customers are very busy,” he said. “They aren’t usually sitting at a desk looking at a computer screen, so we want to make sure when they pull up SightIQ on their device that the dashboard they see reflects what’s most important to them so they don’t have to dig through different reports to find what they need.”
In the future, SightIQ hopes to bring its abilities to plant equipment. “We want to pull in data not just from yellow iron, but from the plants,” Grandy said, adding that OEMS are now putting telematics control units (TCUs) onto those assets so owners can pull API data from belts, crushers, etc. “The plant is like any other piece of yellow iron. As long as we’re aggregating data in the correct way, there is a high value to having all that data.”