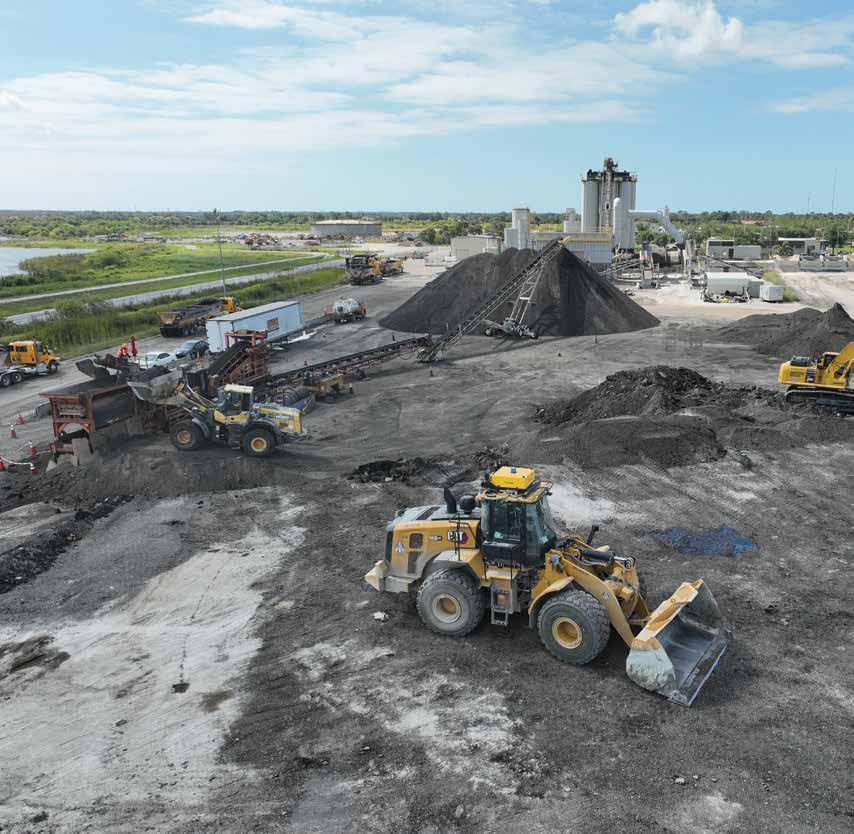
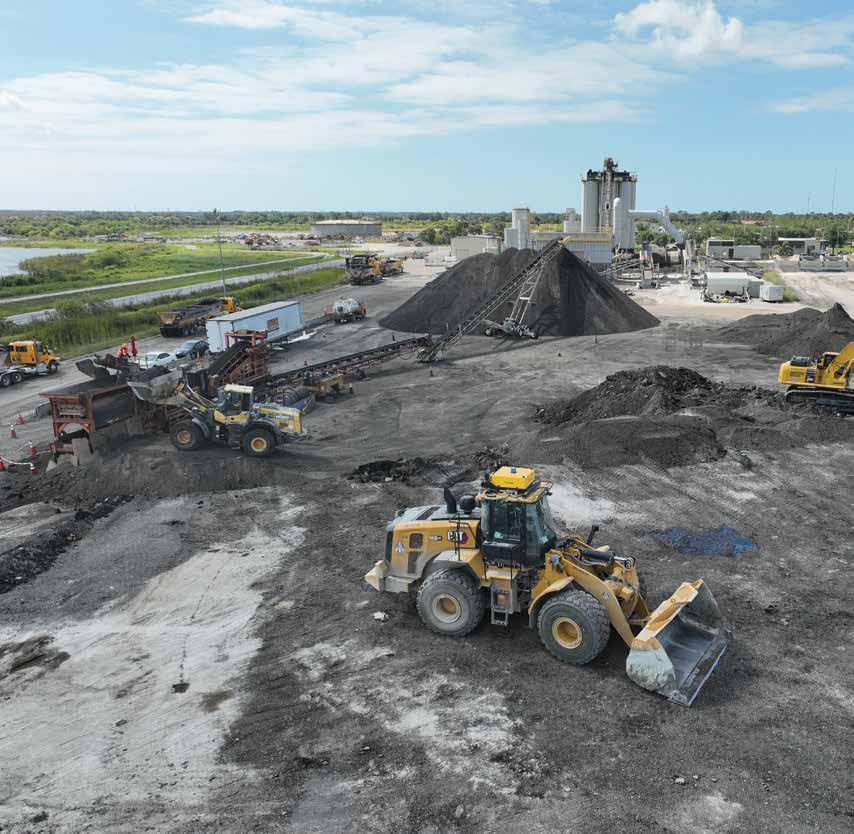
SUSTAINABLE INNOVATION
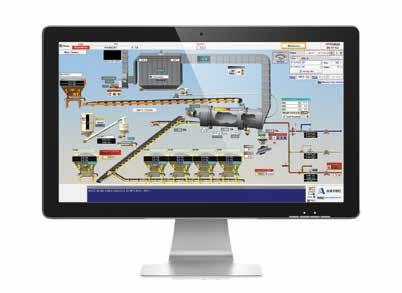
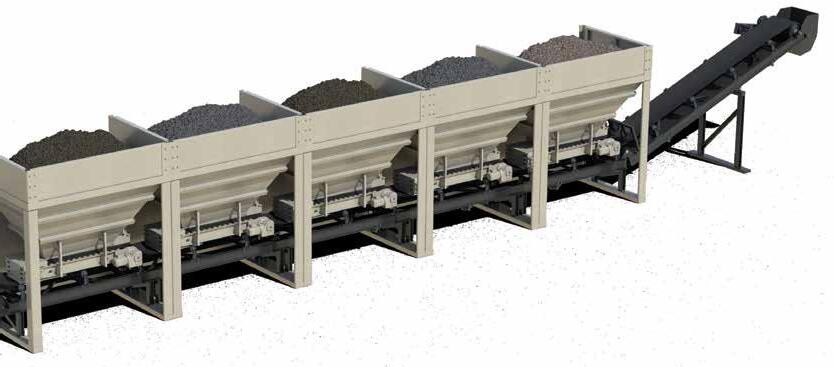
NEW IntelliPac ™ Moisture System
Astec paves the way for sustainable, innovative asphalt plants. The new IntelliPac Moisture System is a revolutionary solution that integrates seamlessly with Astec control systems. This provides unparalleled, real-time visibility into virgin aggregate moisture content. IntelliPac empowers operators to optimize mix design, minimize energy consumption, and reduce environmental impact. With Astec, you get superior asphalt production – better for the environment, better for your business.
BUILT TO CONNECT

TO SEE VIDEO
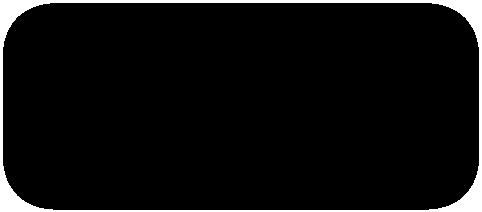
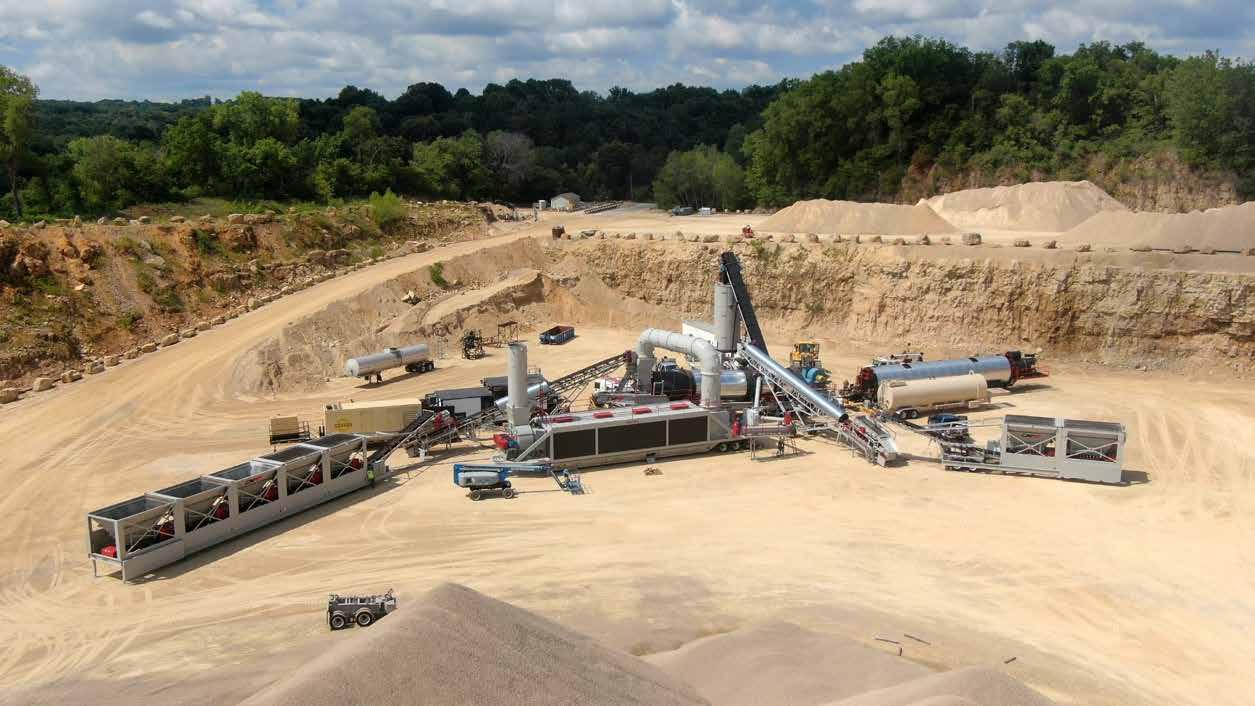
CWMF has been a trusted company in the stationary and portable asphalt industry for decades.
As a full-service manufacturing company, we engineer all of our products to order, allowing us to serve as a full-service, end-to-end provider of asphalt plant solutions. We have the machinery and equipment you need, and a confident team working together to make this happen. Whether it’s cold feed bins, drums, silos, or the entire plant, we get the job done in-house, from start to finish. This provides an exceptional experience for our customers, and for the dedicated team standing behind their products. We work hard not only to retain our reputation but to stay current on the latest industry trends and technologies.
Contact us for a site evaluation, expansion project idea, new equipment upgrades, or to discuss your custom needs.

A BRAND YOU CAN TRUST
At Gencor®, we’ve led the industry with the most fuel-efficient, environmentally clean and lowest-maintenance design available to the hot mix industry. Gencor Industries remains focused on proactively serving and satisfying its customers from all aspects.
Through improved cost-effectiveness, and quality of its products and services, Gencor’s personnel are dedicated to the principle of providing the highest quality to the industry to maintain a sustainable competitive advantage for Gencor®
The Leader in Performance and Reliability
or
www.gencor.com


CONTENTS asphaltPRO August 2024
DEPARTMENTS
EDITOR’S LETTER
8 – Let’s Pre-Solve an EV Pavement Problem
By Sandy Lender
SAFETY SPOTLIGHT
10 – 6 OSHA Training Tips
A former safety officer helps you navigate your 10-hour program to bring workers into safety compliance for asphalt construction workforce development efficiency. By AsphaltPro Staff
PRODUCER PROFILE
14 – Materials Supplier
Rooted in Quality
Russell Standard’s fourth-generation leader shares how he’s making his mark, taking a company back to material production with a state-of-the-art lab and recent Delaware terminal expansion. By Lindsay Matush, Vario
STREET SMARTS
20 – Attract Workers with Staying Power By Bill Stanley
PRODUCT GALLERY
36 – Who’s Your MVP? By AsphaltPro Staff
OFF THE MAT
45 – Terex Launches New Brand for Aggregate Businesses From Terex
NEW TECH
49 – Iron Sheepdog Solves the Trucking Problem at the Start By Sarah Redohl
50 – Trimble Flashtracts Payments
Trimble Acquires Flashtract, Streamlines Payment and Compliance Workflows for Pavement Contractors
By Meredith Bagnulo
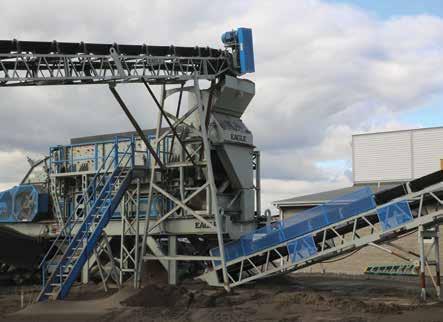

FEATURES
22 – Expand Into Production Crush Future Recycle Goals
Eagle Crusher offers realistic options for expanding your asphalt production with portable or stationary RAP crushing technologies. By Daniel C. Friedman
28 – Remote Technology Solves Plant Pain Points

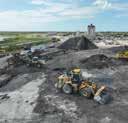
Teleo helps Ajax Paving broaden its hiring pool, cut costs, and improve operator physical and mental health with remote aggregate loading. From AsphaltPro Staff
32 – Best Practices for Mobile Asphalt Crushing By AsphaltPro Staff
ON THE COVER Teleo has assisted Ajax Paving of Florida in outfitting a Caterpillar wheel loader for remote control operation. See related story on page 28. Photo courtesy of Teleo
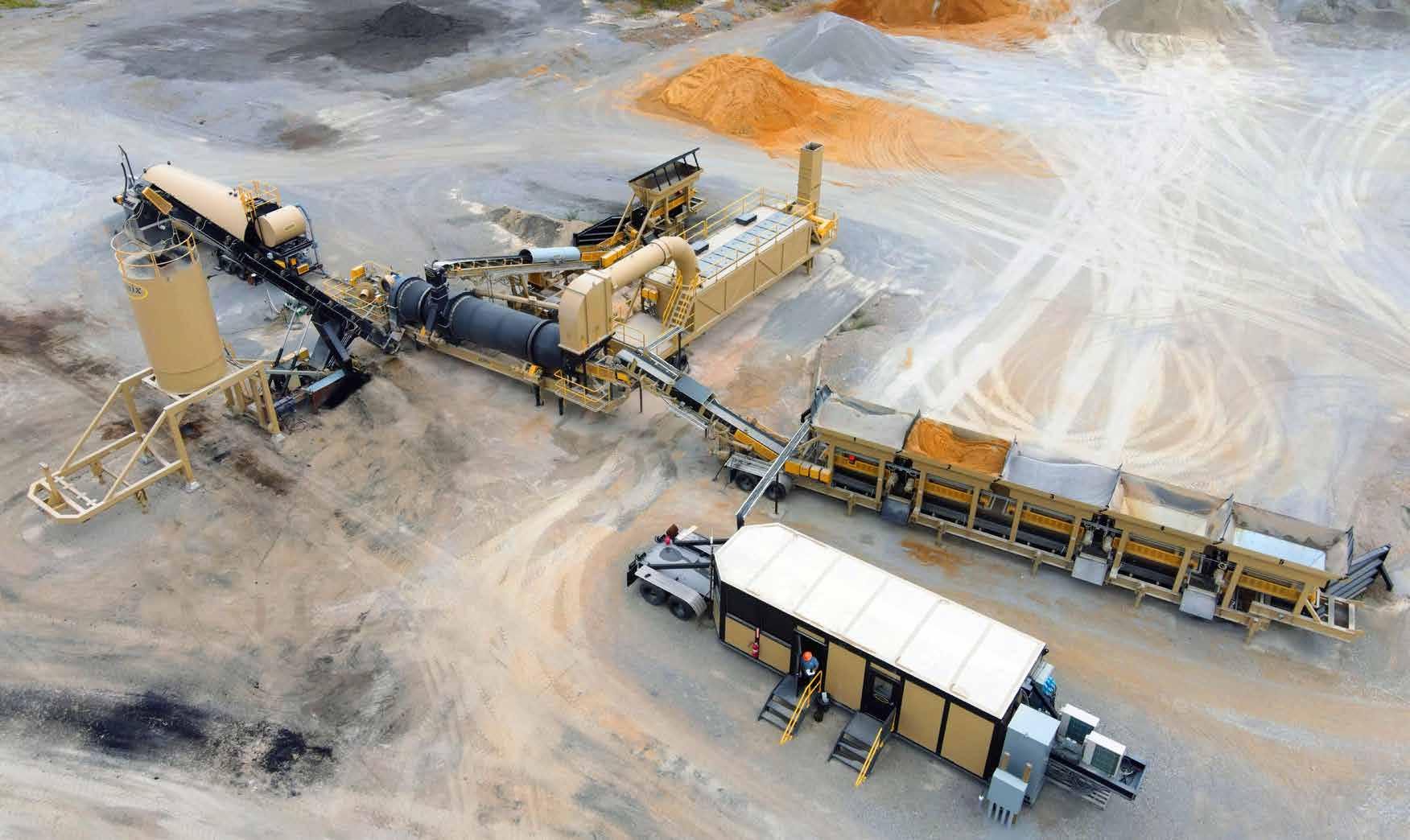

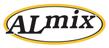
BUILT DIFFERENT BY DESIGN.
The future is connected. That’s why we’ve designed the ALmix Insignia Control System (ICS) around the power of high-speed Ethernet communication. An ethernet-connected facility means our team of programmers have complete visibility into your plant equipment and motor control center for diagnostics and remote troubleshooting. View and control data from your asphalt plants like never before. The Insignia Cloud Platform provides access while you are at the plant, in the office, or on the go. Critical, real-time, plant information is at your fingertips when you need it.
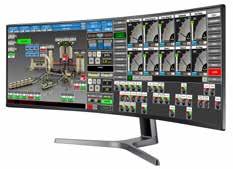
Whether you operate one plant or twenty, the Insignia Cloud Dashboard allows your plant data to be stored off-site and analyzed from any device, anywhere, at any time. Coupled with the ALmix Insignia Control System’s ethernet-connected PLC design and customized by our team of
program engineers, The Insignia Cloud is the most comprehensive plant overview tool on the market.

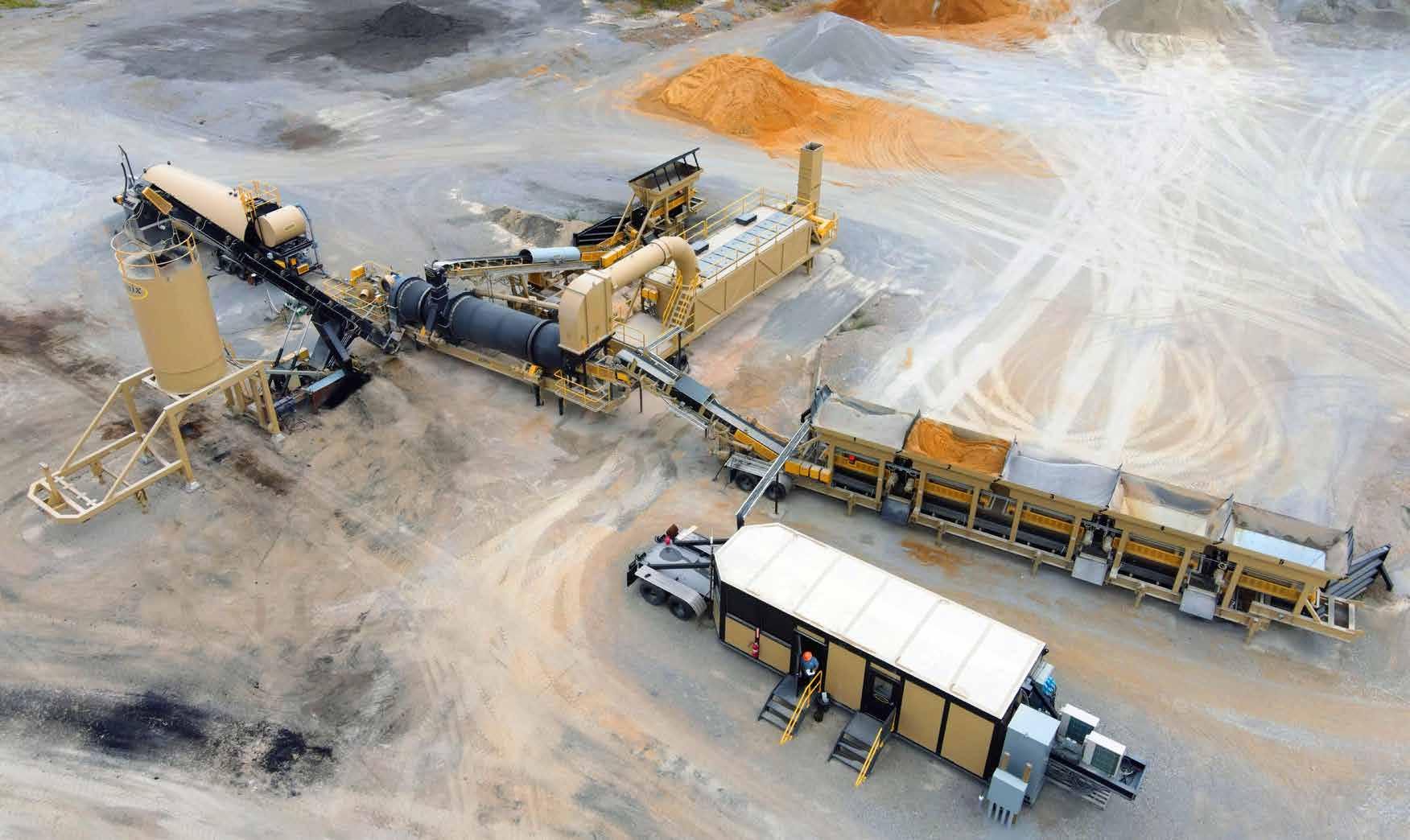

Let’s Pre-Solve an EV Pavement Problem
Call it lateral instability or wander effect, the fact of the matter is researchers have been studying the impact autonomous electric vehicles (EVs) are having on pavement systems. Let’s look at what might be happening and how the asphalt industry may assist.
The Federal Motor Carrier Safety Administration (FMCSA) announced earlier this year its second contract to continue its TechCelerate Now program. Among other things, the program furthers the implementation of advanced driver assistance systems (ADAS), which include steering-assist to prevent heavy trucks (whether autonomous or not) from deviating from a straight line. By employing autonomous driving and driver-assist systems in heavy commercial trucks, we’re stressing pavement systems that weren’t designed to handle that additional weight in that kind of pattern.
The weight of EVs isn’t a surprise to anyone. For instance, the researchers at insideevs.com discuss all facets of EV manufacture, infrastructure, ownership and so on. In an article from 2021, they were already looking at the topic of weight as it related to passenger vehicles.
They gathered data showing, of almost 70 vehicles tested, more than a third of them weighed more than 4,409 pounds (2,000 kilograms). They reported more than half of the models weighed between 3,307 and 4,409 pounds (1,500 and 2,000 kg). From the insideevs.com article “Electric Cars from Heaviest to Lightest,” we read:
“That’s a big issue for electric cars, because the heavier the car, the less efficient it is, which directly affects the range. Not only that, the car is more expensive as it must be equipped with more powerful brakes, suspension, wheels and tires that happen to last less. In general, a heavier car is also less environmentally friendly.”
The author, Mark Kane, was addressing the weight of an EV in terms of its efficiency or battery charge use. But let’s consider its impact on the horizontal infrastructure. Let’s look at the pavement system.
An article that gives a more recent look at battery weights and performance is https://www. etechnophiles.com/ev-batterysize-weight-power-capacity/.
The good news is the asphalt industry is superlative at preemptive problem solving. Remember the good old days of the 1990s when state departments of transportation and county agencies alike sought solutions for the rutting and cracking taking place at intersections? The asphalt industry stepped up and developed specific mix designs to handle the shear forces in those areas. We all remember presentations showing contractors running out the mix in the paver so they could set up at the beginning of an intersection to pull a lift with a new mix in a new truck from a designated silo at the plant.
I ask for your opinion. Is it time to balance some mixes for the forces coming from the EV sector?
It’s not only the rutting in heavy-congestion cities we must combat as commercial trucks bring goods to market along highways we build and maintain. Consider also the “smaller” projects where EV charging stations and stalls line strip malls and residential communities. Property managers turn to paving and pavement maintenance contractors to get the parking lot paved and treated correctly. They don’t want cracks spidering out from the charging station where an elite client parked a Tesla to charge every night for the past two months.
Kanishk Godiyal at eTechnophiles. com wrote in his article, “A Complete Guide to EV Battery (Size, Weight, Power & More),” that the battery weight matters in more ways than one. He stated, “The major part of an EV’s weight comes from its battery,” and explained the simple fact—the more powerful the battery, the greater its weight.
The asphalt industry offered solutions for pavement failures happening at intersections a few decades ago. I bet our industry can get ahead of the EV problem about to strike our infrastructure now.
asphaltPRO
602 W. Morrison, Box 6a Fayette, MO 65248 (573) 823-6297 • www.theasphaltpro.com
GROUP PUBLISHER
Chris Harrison chris@ theasphaltpro.com
PUBLISHER
Sally Shoemaker
sally@theasphaltpro.com (573) 823-6297
EDITOR
Sandy Lender
sandy@theasphaltpro.com (239) 272-8613
DIGITAL EDITOR
Sarah Redohl sarah@theasphaltpro.com (573) 355-9775
MEDIA SALES
Cara Owings cara@theasphaltpro.com (660) 537-0778
ART DIRECTOR Kristin Branscom
BUSINESS MANAGER
Susan Campbell (660) 728-5007
AsphaltPro is published 11 times per year.
Writers expressing views in AsphaltPro Magazine or on the AsphaltPro website are professionals with sound, professional advice. Views expressed herein are not necessarily the same as the views of AsphaltPro, thus producers/contractors are still encouraged to use best practices when implementing new advice.
SUBSCRIPTION POLICY: Individual subscriptions are available without charge in the United Sates, Canada and Mexico to qualified individuals.
One year subscription to non-qualifying Individuals: United States $90, Canada and Mexico $125.00. For the international digital edition, visit theasphaltpro.com/subscribe/
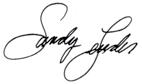
Stay Safe, Sandy Lender



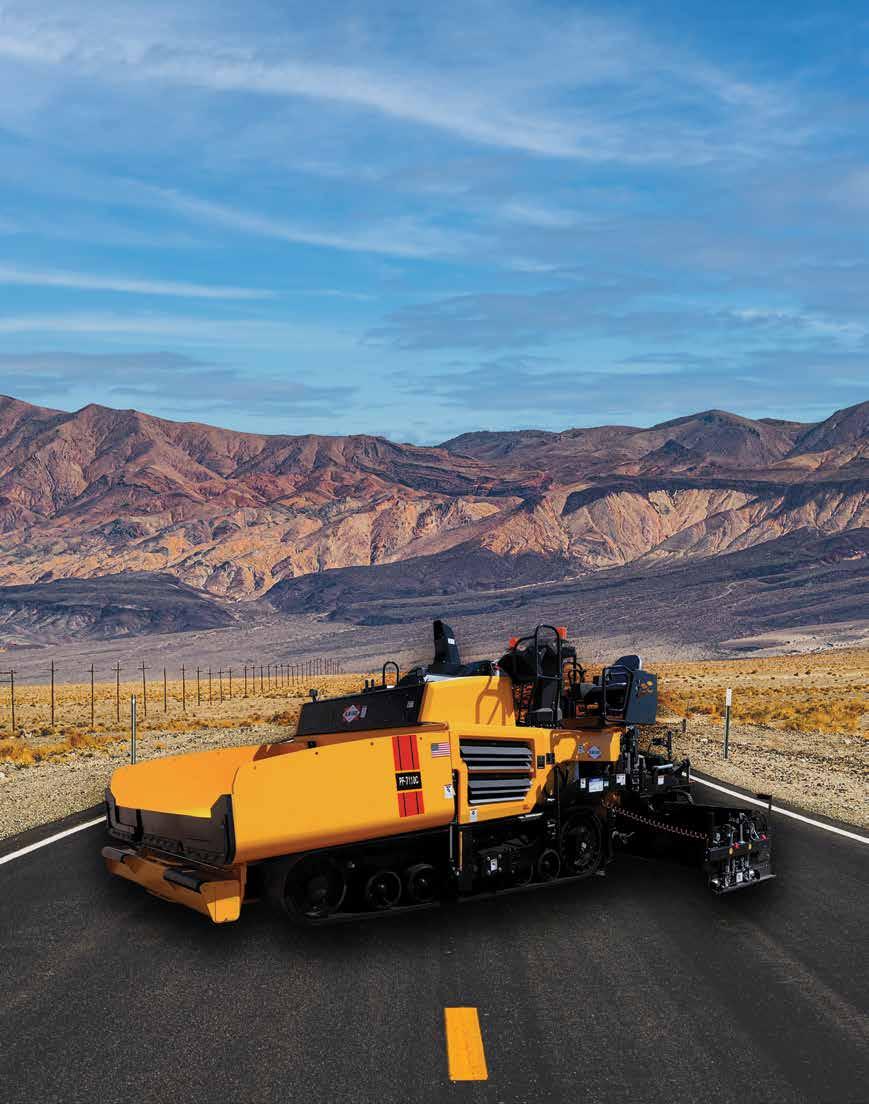
The all-new Blaw-Knox PF-7110C tracked paver combines all-around visibility, ease of operation and a new powerful Cummins 235hp engine for the ultimate in dependability and efficiency. The turbocharged diesel engine provides more torque and less weight in a more compact package, letting you power through steep grades with confidence. Coupled with the proven Blaw-Knox durable track and automatic tensioning system, the 7110C ensures smooth and consistent paving power on any terrain.
With over 90 years of proven Blaw-Knox paving technology, the PF-7110C delivers all the power you need and more.
BLAW-KNOX, THE LEGACY LIVES ON.
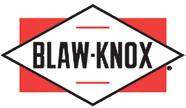

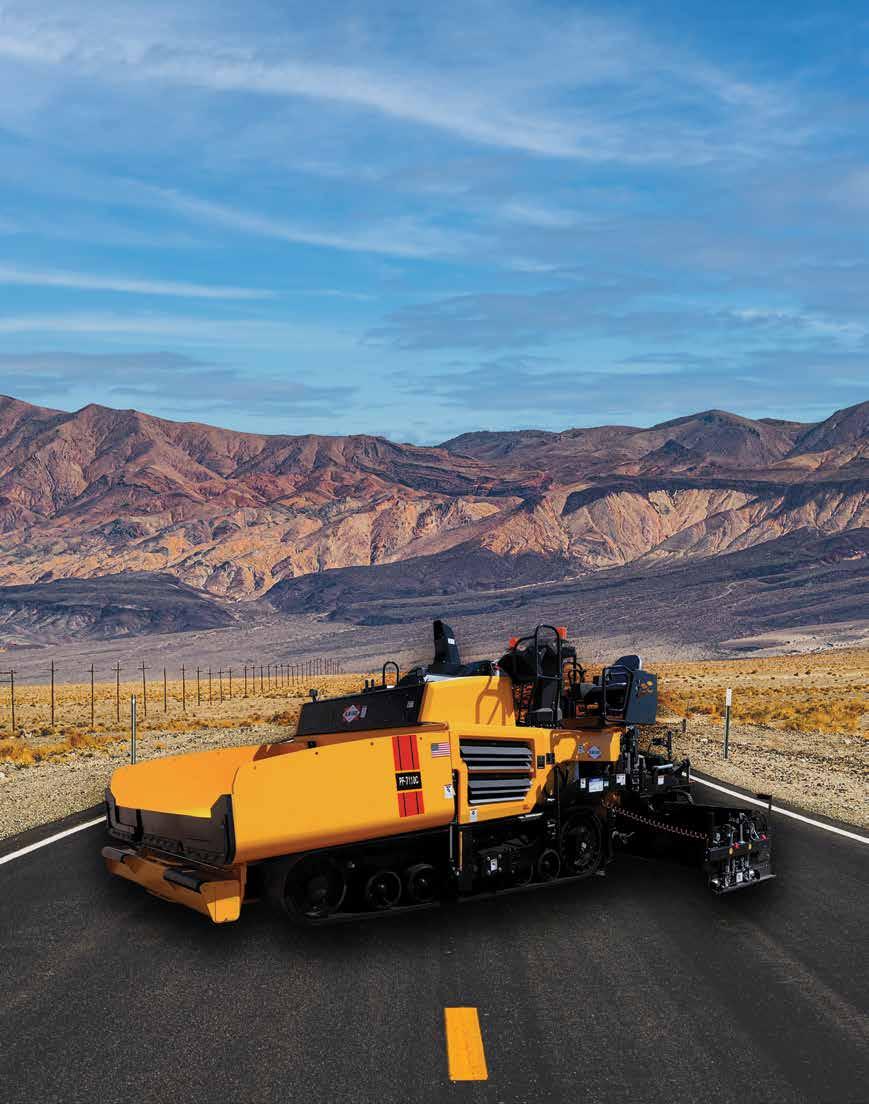
SAFETY
6 OSHA Training Tips
A former safety officer helps you navigate your 10-hour program to bring workers into safety compliance for asphalt construction workforce development efficiency.
BY ASPHALTPRO STAFF
We know Occupational Safety and Health Administration (OSHA) 10-hour and 30-hour training programs are set up as keystones for ensuring the safety and well-being of employees across various industries. The asphalt industry, like others, employs safety managers who ensure OSHA rules and regs are implemented correctly—among myriad other elements of an asphalt company’s safety culture. This month, we’re fortunate to hear from Elis Enano, a safety professional with six years of experience in both construction and manufacturing industries. She writes about OSHA compliance, safety standards, training procedures and other matters relevant to workplace safety and accident prevention. In the safety training realm, she has seen room for improvement.
“As a safety professional, I have observed many common mistakes that reduce the efficacy of workplace safety training programs,” she wrote.
She provided six areas to focus on when trying to educate your teams on safety and accident prevention:
• Customization;
• Comprehensiveness;
• Presentation;
• Interactive Learning;
• Resource Availability; and
• Reinforcement.
Let’s take a quick look at each of these areas to see how Enano recommends improvement for your OSHA safety training in your asphalt operation.
USE A CUSTOMIZED TRAINING APPROACH
Enano suggests performing a needs assessment to pinpoint any gaps between existing and desired levels of knowledge, skills and attitudes about safety. If you fail to perform a comprehensive needs assessment before developing your training program, you could be wasting time and resources on topics not relevant to your team or overlooking areas your team needs help with.
“During my time in the field, I’ve observed managers, under pressure to meet tight deadlines, rushing through the needs assessment phase,” she shared. “Since the assessment creates the foundation of the training, the hasty approach resulted in training programs that missed out on many nuanced safety issues that were crucial for effective safety training....it is essential to analyze workplace hazards, risks, regulations, and performance metrics while engaging employees and stakeholders to identify their learning requisites and preferences.”
COVER IT ALL
Comprehensive training coverage in OSHA training means you’re addressing all mandatory topics and relevant aspects of workplace safety. Enano reminds us this includes covering a wide range of subjects such as hazard identification, emergency procedures, equipment use and regulatory compliance specific to the asphalt industry.
IT’S HOW YOU SAY IT
Different people learn in different ways, which makes your presentation “technique” crucial for communicating safety information to employees. By using engaging methods such as visual aids, interactive activities, and real-life examples, trainers have a better chance of conveying information to workers and helping them understand and retain it.
“Unfortunately, many trainers miss out on case studies and interactive techniques and create presentations that cannot keep the students engaged,” Enano wrote. “In my experience, the best training sessions are those where the trainer converses with the students instead of simply bombarding them with information.”
She also stresses the importance of providing plenty of time for a Q&A session during OSHA training. “Overall, mastering effective presentation techniques is essential for delivering impactful OSHA training that promotes a culture of safety in the workplace.”
GET WORKERS ACTIVE IN LEARNING
As part of your presentation, consider how interactive you can make the training experience. This goes above and beyond an interactive Q&A session. The concept of interactive learning integration in OSHA training is designed to enhance learning for workers. You want to get everyone more engaged for a deeper understanding and to retain more information—have group discussions and exercises, include simulations, incorporate hands-on demonstrations.
GIVE THEM ACCESS TO RESOURCES
It may seem obvious, but you want to make sure you provide access to resources and tools for effective learning. This includes safety manuals and reference materials but also includes personal protective equipment (PPE) and emergency response resources.
“In one of the sessions that I observed, the trainer overlooked ensuring that each participant had access to the required safety gear, such as gloves, goggles and helmets,” Enano shared. “This resulted in a disjointed and incomplete training experience.”
You want to prioritize training in a space with adequate space, lighting and equipment to facilitate learning and skill development.
FOLLOW UP FOR SAFETY SUCCESS
Don’t forget to reinforce workplace safety training with follow-up measures—such as consistent feedback, practical application, acknowledging workers’ achievements— post-training. If you fail to reinforce training, workers can forget new safety skills or revert to old, unsafe habits.
Through the six tips sketched here, you can improve your OSHA and other safety training programs to foster a safer work environment. Your effective training methods can cultivate a safety culture where all workers are equipped with the knowledge, skills and attitudes they need.

THE POWER
Customize any ADM plant to your specific production needs with our standard components.
“Owning our ADM asphalt plant has been a real game changer. ADM focuses as much on service as on the sale of the plant, and the payoff has been well worth it.”
Trent Nielsen, President & Owner-Operator, Nielsen Blacktopping & Concrete
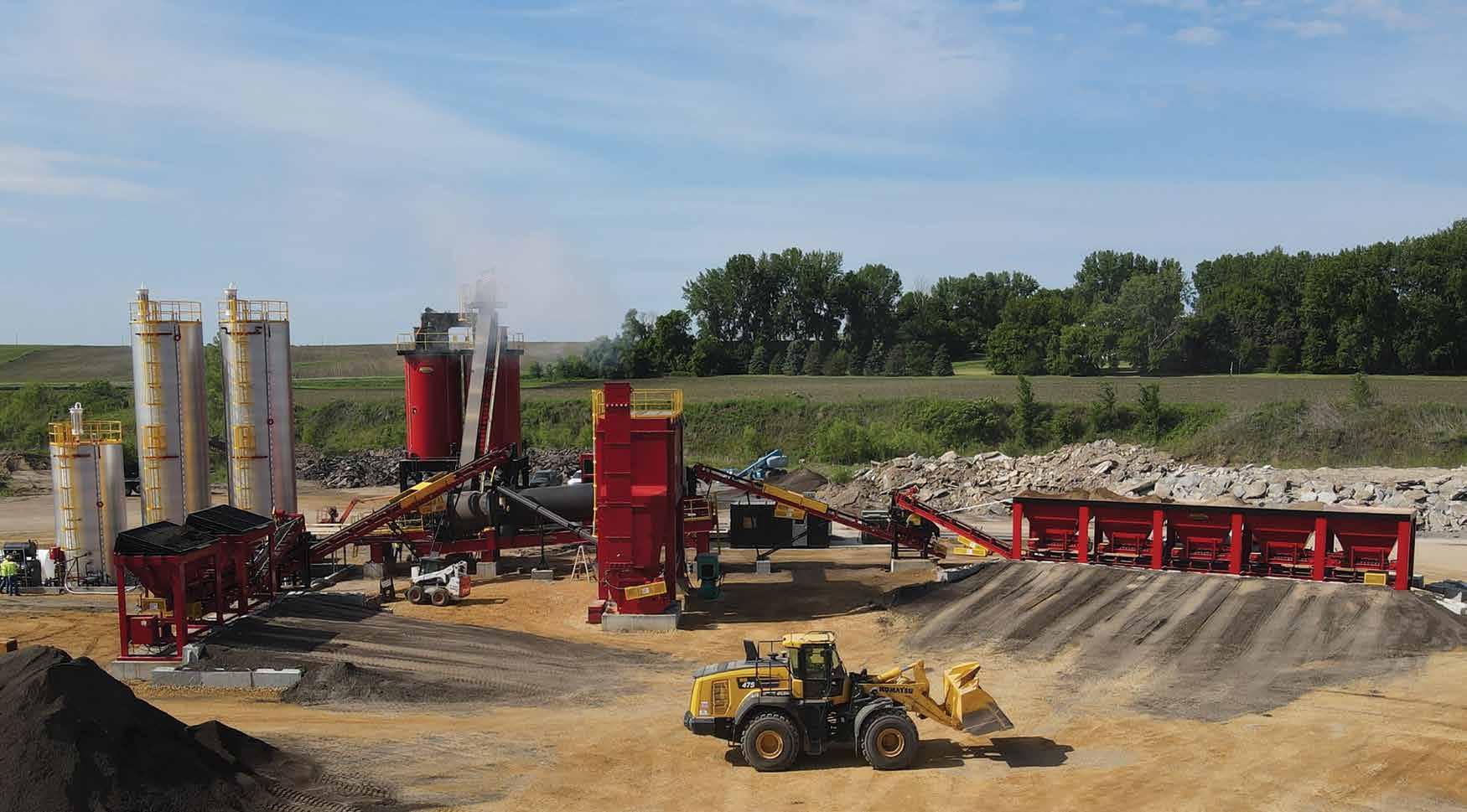
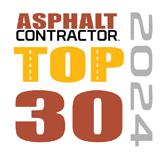
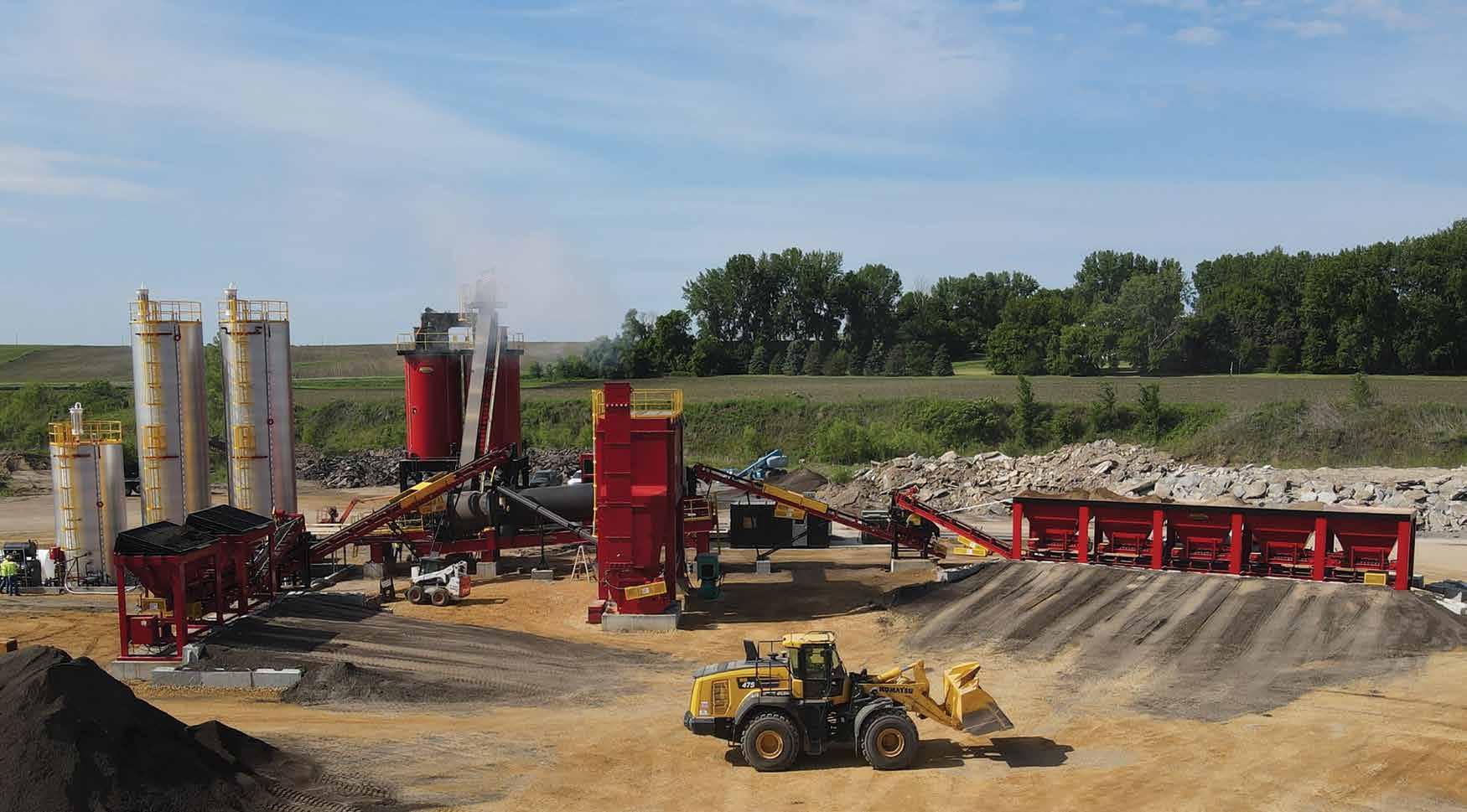
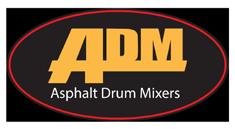
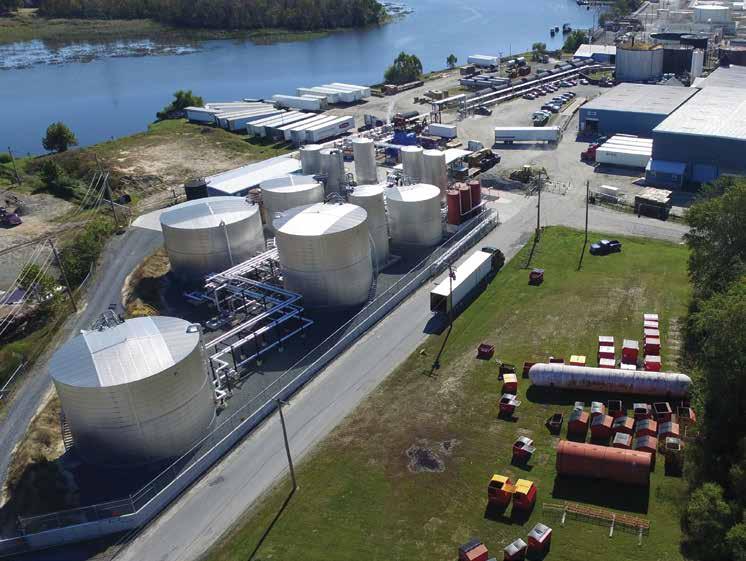
Materials Supplier Rooted in Quality
Russell Standard’s fourth-generation leader shares how he’s making his mark, taking a company back to material production with a state-of-the-art lab and recent Delaware terminal expansion.
BY LINDSAY MATUSH, VARIO
Matt Johnson is the president and CEO of Russell Standard, a company that provides asphalt materials, road preservation treatments and industrial asphalt solutions for the Mid-Atlantic region. Since taking the helm in 2004, he’s made it his mission to strengthen the company’s well-earned reputation for quality, partnership and innovation. His work these days focuses on getting the company back to its roots with innovation in the asphalt and paving materials departments, gearing these materials toward preventive maintenance.
See, Johnson is no outsider. He’s spent most of his life around or working in the business. Now, as CEO, he’s using his talents to refocus the company. This is a story about family, business, and the desire to establish one’s legacy after three generations of success in the paving industry.
LESSONS IN LIFE, AND BUSINESS
Founded in 1929, Russell Standard has remained a family-owned business dedicated to quality and advancing the asphalt materials space. Building on the company’s nearly 100-year legacy, Johnson represents the 4th generation of his family to lead the business.
ICP Group’s facility in Seaford was the only asphalt and emulsion terminal in Delaware. After hearing the facility was for sale, Russell Standard President and CEO Matt Johnson and his team jumped in to negotiate its purchase. Photos courtesy of Russell Standard
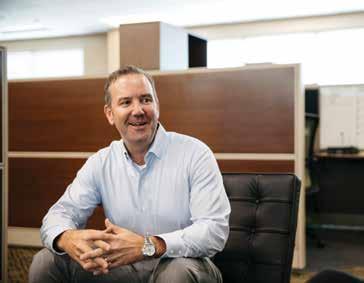
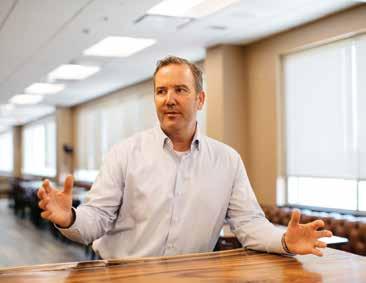
Matt Johnson is the fourth generation of the family to lead Russell Standard. Back when he was just five years old, he was riding along with his father, Jim, to attend to business. As a teen, he helped maintain the grounds around the plants and worked on the paving crews into college. “Growing up as a kid, it was always cool to be around the equipment and that continued until I was in college,” he said. “Once I was old enough to be in the field, I started working on the road crews. It was so cool to finally work with all the equipment, see the material go down, and know I was helping to build something lasting.”
His great-grandfather, Niles Russell, established the Tri-State Culvert Company in Pittsburgh just before the Great Depression. The company sold drainage products, trucks and construction equipment. Later, Russell would expand into coal trucking, a retail coal business and a successful topsoil supply operation.
During World War II years, Russell Standard became a major supplier of liquid asphalt for the road construction industry. Over the years, the company would expand its footprint with hot-mix asphalt (HMA) plants throughout Pennsylvania. Russell also directed the expansion into the company’s first emulsion plant in Mercer, Pennsylvania, in the early 1970s.
“MANY
CONTRACTORS IN [DELAWARE] WERE DRIVING TO MARYLAND, PENNSYLVANIA OR NEW JERSEY TO PICK UP MATERIAL. [RUSSELL STANDARD’S LEASE OF OPERATIONS] WILL DRAMATICALLY CUT DOWN ON TRANSPORTATION COSTS BY HAVING A LOCATION IN THE STATE THEY CAN GET THE SAME MATERIAL FROM. AND THE DOT WAS ALREADY HAVING MATERIALS DELIVERED FROM THERE. SO, IT’S REALLY THE LOCAL CONTRACTORS THAT WILL BENEFIT.”—MATT
JOHNSON
This is when Russell’s son, Ed Russell, continued a steady focus on paving and materials.
Next, Matt Johnson’s father, Jim Johnson, expanded the paving operations while adding a second emulsion plant in Chambersburg and a facility in Akron, Ohio. He also put his stamp on things by repositioning the firm as the go-to contractor for paving.
Matt Johnson has been in the business since he began riding along with his dad when he was five years old. As a teen, he helped maintain the grounds around the plants. Late in high school and into college, he worked on the paving crews. Russell Standard is in his blood.
“Growing up as a kid, it was always cool to be around the equipment and that continued until I was in college,” he said. “Once I was old enough to be in the field, I started working on the road crews. It was so cool to finally work with all the equipment, see the material go down, and know I was helping to build something lasting.”
His experience has helped him to never lose sight of where he’s come from. The hours in the truck and office working with his father have made a strong impact on who he is now.
“I learned a lot about family philosophies, the history of why things were done, and why we still do things,” he said. He spoke with pride of how the family business has built a reputation for treating its people well and being fair with customers. “We’ve always done both of those for generations. The people part of the business has always been important because, without those people, we really don’t have a business.”
In addition to the big-picture learning, there was plenty to learn about managing the day-to-day.
“It really gave me a good understanding of how we do things,” Johnson said. “What’s important on jobs, being well organized, and having everything you need on hand when you need it so crews aren’t waiting. The equipment is there when they need it. So we’re efficient moving from job to job. And what we do is so seasonal, you have to be ready to go to minimize any disruption.”
But one lesson stands out the most:
“It’s a difficult, demanding job,” he said. “That’s one thing I think about all the time. I think that was a huge benefit of growing up in the field was getting an appreciation for how hard the job is.”
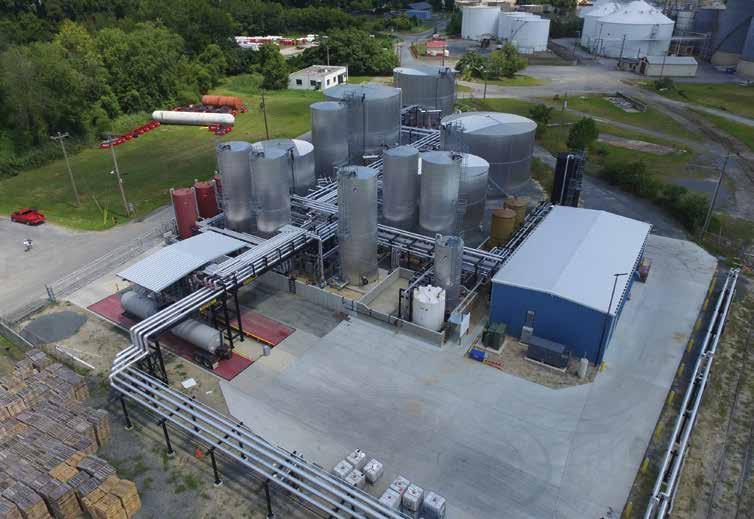
Matt Johnson said Russell Standard team members are always trying to innovate new or enhance existing products that focus on pavement preservation. “And we’re extremely excited about two we’re getting ready to roll out to the market.” The first is a high-performance solution focused on the top-down preservation of long joints; the second is a micro surfacing product focused on resisting cracking.
A RENEWED EMPHASIS ON MATERIALS
Since taking over the top post in 2004, Johnson added plants in Greensboro and Black Mountain, North Carolina; Baltimore, Maryland; and Reading, Pennsylvania. Today, his work is focused on getting the company back to its roots as a leading innovator of asphalt and paving materials geared toward preventive maintenance.
“I really like businesses where you bring in raw materials and turn them into something else,” Johnson said. “We’ve always had a manufacturing focus—we made materials and placed them. And that’s where I focus the business now—we’re mostly a materials business although we still do some contracting on projects that call for our own products.”
The company’s commitment to innovation is evident in its founding of The Lab in 2017 to support both the material science and contracting sides of the business. Then in early 2020, Russell Standard made a significant investment in a new, state-of-the-art facility. It’s a nationally certified, AASHTO-accredited laboratory and is equipped and accredited for testing involving performance graded (PG) asphalt binders, asphalt emulsions and asphalt cutbacks.
This is where the company focuses on research and development and custom blended solutions for customers.
“Our world-class lab is constantly working to ensure our material is meeting or beating specifications and operates with a near-obsessive drive to solve our customers’ biggest problems and innovate new solutions along the way.”
Johnson continued: “The Lab is a strength of ours. We’re always trying to innovate new or enhance existing products that focus on pavement preservation. And we’re extremely excited about two we’re getting ready to roll out to the market.”
• The first is a high-performance solution focused on the top-down preservation of longitudinal joints.
• Soon after, the company will be introducing an improved micro surfacing product to resist cracking.
Each is designed to give state and local agencies cost-effective and sustainably focused options for extending the life of their road networks. And will reinforce Russell Standard’s unique ability to manufacture material, lay material and test its performance to inform future innovations.

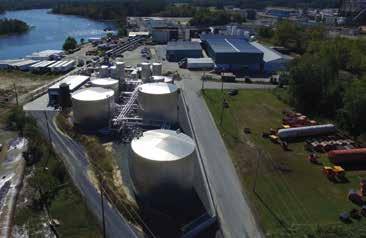
Local contractors, as well as the agencies they often work for, look for ways to enhance sustainability. By adding the plant in Seaford to its mix, Johnson said Russell Standard has offered local contractors a way to source materials in their vicinities. “This will cut down on the freight,” Johnson said. “And it will cut down on the number of trucks on the road. There’s a lot of benefit overall.”
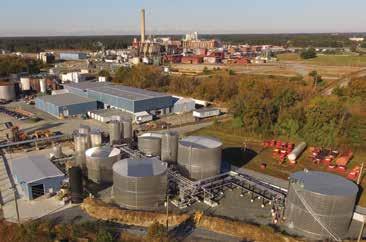
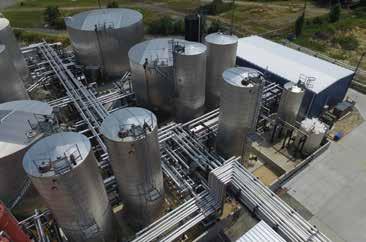
PRODUCER PROFILE
EXPANDING OPPORTUNITY
While managing production and innovation, Johnson also keeps an eye out for opportunities to expand. He recently found one in Delaware.
ICP Group’s facility in Seaford was the only asphalt and emulsion terminal in the state. After hearing the facility was for sale, Johnson and his team jumped in to negotiate its purchase. After lengthy discussions, ICP ultimately sold it back to its previous owner.
Recognizing its value to the region, Johnson’s team stayed on the offensive. In April, the company finalized a lease to take over operations at the facility from the previous owner. This move will bring Russell Standard’s proven dedication and laser-focused commitment to the Delaware Department of Transportation, counties and contractors throughout the state.
“It was a good growth opportunity to add an entire state that we had been servicing from our plant in Baltimore,” Johnson said. “This really allowed us to open up the entire state instead of just the fringes.”
Delaware now becomes the fifth state served by Russell Standard.
“We’re focused on growing the materials business where we can,” Johnson said. “So anything adjacent to us is attractive. Since Delaware is an adjacent state, it’s an easy place to tuck into what we’re already doing. Any time we can find something like that, we’d certainly be interested in it.
Until this point, most contractors in Delaware had been sourcing material out of state. This move establishes a local option for materials and emulsions that will greatly save on transportation costs for everyone involved.
“Many contractors in that state were driving to Maryland, Pennsylvania or New Jersey to pick up material,” Johnson said. “It will dramatically cut down on transportation costs by having a location in the state they can get the same material from. And the DOT was already having materials delivered from there. So, it’s really the local contractors that will benefit.”
SMART MOVES WITH LASTING BENEFITS
“Our crews know what it takes to perform successful, long-lasting treatments to strengthen communities and make them proud,” Johnson said. “From start to finish, our work and the way we do business all comes back to our mission—to be the most respected partner in the region by serving our team and customers like family.”
And with state and local governments focused on expenditures, Johnson knows they also keep a close eye on sustainability. By adding the plant in Seaford to the mix, “This will cut down on the freight,” Johnson said. “And it will cut down on the number of trucks on the road. There’s a lot of benefit overall.”
When you couple this locally sourced material with the material innovations from The Lab, Russell Standard is making it easier for agencies to cut expenses while making their roads last longer and meeting sustainability initiatives. And that’s good for everyone.
“Good roads are safe roads,” Johnson said. “And the better that a state or local government maintains its infrastructure, it’s better for everybody. It’s safer for the public. It helps facilitate commerce. Everything gets into a truck at some point. Whether it comes in by ship or by rail, it ends up in a truck to get delivered. So, the better the roads are, the better the economy is.”
And that’s a fitting way to leave your mark.
The aerial view of the Seaford facility in Delaware showcases best practices for piping jacketing (among other best practices) for environmental sustainability.

STREET SMARTS
Hard-won know-how for the next generation
Attract Workers with Staying Power
BY BILL STANLEY
HELP WANTED: Local paving company looking for laborers, drivers, machine operators.
BENEFITS: long hours, hard work, no set schedule, low starting pay, little to no time off, seasonal work.
When we outline the cold hard truth about starting a career on a paving crew, it’s no wonder why we struggle to attract the next generation.
Those of us who have been in the asphalt industry a while know the benefits of this profession. But for people just starting, that job description is pretty accurate. Not many will stick through the initially low pay (given the going rate for hourly labor these days), plus long hours and hard work to find out what you and I know: that the asphalt industry is a great place to build a career.
As a working owner, I get to experience what it’s like for the new members of our team every day on the job site. Here are a few things I’ve learned from my daily interactions with new employees.
NO ONE IS ABOVE HARD WORK
Here at American Pavement Specialists, all employees—including family—start at the bottom. Crew members who have been with us for 30 years all started this way. They tie their boots that first day, they get a crew nickname, and we hand them a broom. I make sure new employees know no one skips this step. It can’t be skipped if you want to become a seasoned pavement specialist.
It takes two to three years to train someone to understand all the moving parts of what we do. Training is daily and constant on our crews. Each new employee shadows me or one of my best employees. The goal here is not only to help the new person learn the skills they need, but it also shows we want them to succeed.
When I see a new employee with potential— which is easy to recognize quickly (do they buy into what we’re doing, are they eager to learn, etc.)—I go the extra mile to build their confidence, let them know I see their effort, and show I’m as committed to their success as they are.
But, how do we offer untrained, unqualified workers a high enough salary during the training period? The way I approach this with all new employees is more like dating than a job interview. We’re willing to date you for a while. If we like each other, we may get engaged. If we decide to get married, we promise you a very bright future and will do our absolute best not to let you down.
When I outline this approach with prospective employees, I make it clear that we need employees who want a career, not just a job. We aren’t on the dating app for a quick fling; we are looking for the real thing.
THE CREW IS A KIND OF FAMILY
No matter how many employees a company has, each paving crew consists of five to 10 people. They have to work together cohesively to get the job done, because paving isn’t a solo act. It’s an assembly line. Every employee needs to know their role on that assembly line, just as each family member has different roles and responsibilities.
And, if you plan on a career in this industry, you’ll spend more time with us than your actual family. During paving season, we’re going to be working long hours together with little time off. This is the nature of paving work.
That’s why team building and crew culture is so important. At APS, we don’t have time to take a day off to go to a forest and climb ropes together. We create our culture by how we treat each other on the job every single day. For example, building confidence is key to our culture. Every employee feels better when they experience success!
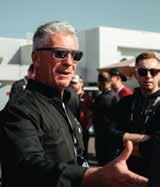
WHAT’S IN STORE (IF YOU STICK IT OUT)
Many years ago, my brother-in-law—an accountant at the time—joined me and my crew on a paving job. This single day led to a career change and a lifetime on a paving crew with no regrets. This story might not make sense to people who aren’t in our industry. But you and I? We get it. This industry affords a career with good pay and opportunities to progress, the feeling of having built something tangible at the end of each day, a work environment with a group of people who become like a second family. Not to mention, the money saved on the gym and a great tan!
This training period is the price of the experience required to truly know our trade. But if someone is willing to put in the work through this ‘basic training’ period, the company will prosper and so will the new employee!
NOT JUST A JOB, BUT A CAREER
There are quite a few six-figure guys on my crew. Every single one of them started off as $20/hour employees. After years of training, learning and building experience, they know their trade so well they are worth every penny.
I think we need to shoot straight about the pros and cons of starting a career in this industry. The new guy or girl should know what they’re getting themselves into. But, they should also know what’s in store for them if they stick it out.
What do you like about working in our industry? Share your thoughts when you see this post on AsphaltPro’s social media.
Bill Stanley owns American Pavement Specialists, Danbury, Connecticut, with his wife, Colleen. Stanley has more than 50 years of experience in the asphalt industry.
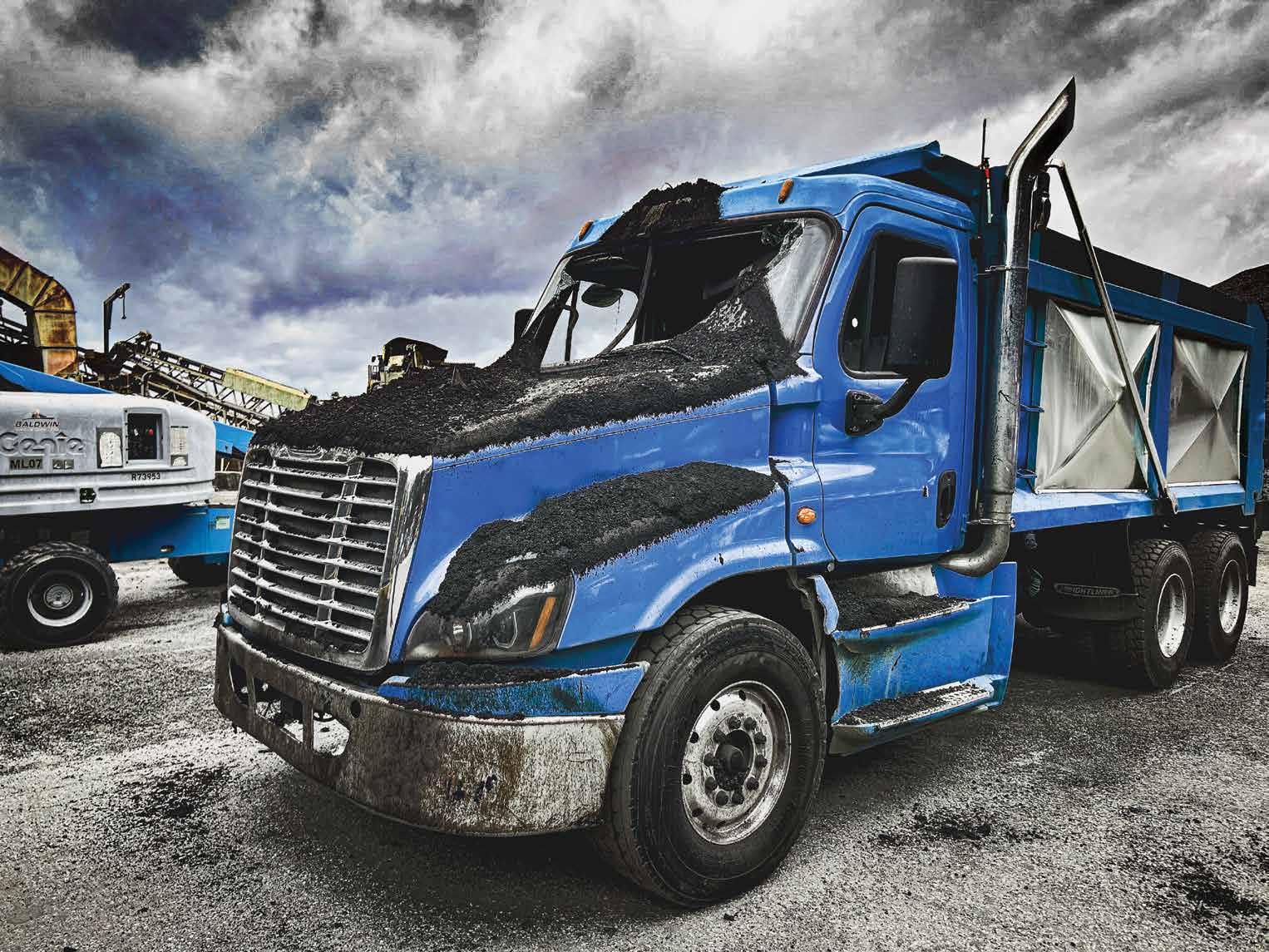

EXPAND INTO PRODUCTION
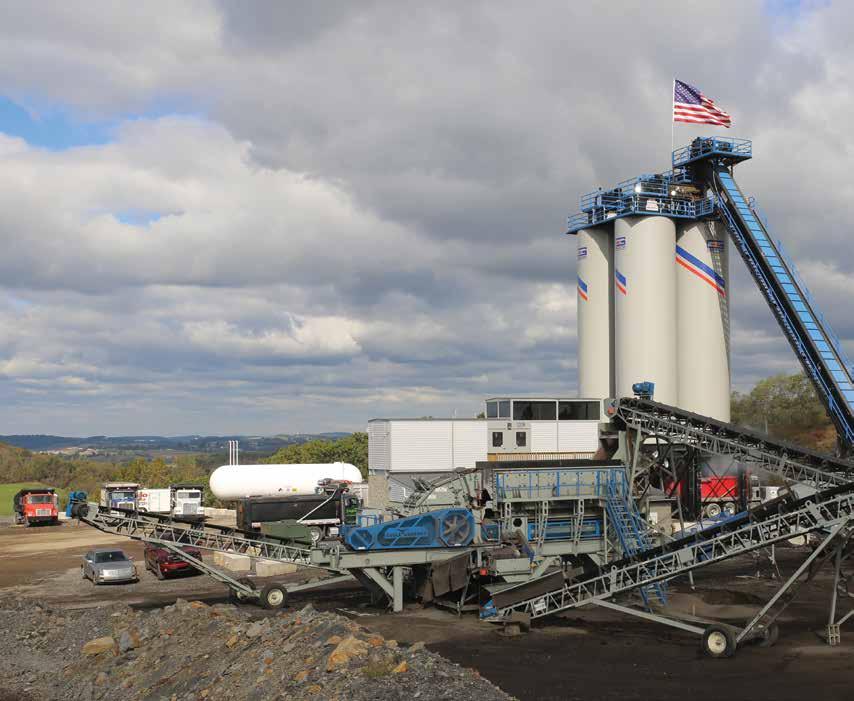
CRUSH FUTURE RECYCLE GOALS
Eagle Crusher offers realistic options for expanding your asphalt production with portable or stationary RAP crushing technologies.
BY DANIEL C. FRIEDMAN
Editor’s Note: For 2024, AsphaltPro Magazine allows experts in the industry to share how to expand your operations to the next phase of business. Are you ready to process your own recycled asphalt pavement (RAP) for your hot-mix asphalt (HMA) production? Let’s turn to some professionals who have equipment, services, software and tenure to help you expand to mix design, production, hauling and more. This month’s installment from Eagle Crusher takes an overarching look at the environmentally responsible task of adding recycling operations to your business.
IIf you don’t already have a recycled asphalt pavement (RAP) crushing plant to make your own crushed asphalt, you can take your production to the next level by adding a crusher to your operation. The benefits to your business can create a real boon for revenues and profits. Here, we outline the benefits and provide considerations to help determine if your own RAP crushing plant is right for you. There are many benefits to adding your own RAP crushing plant to aid in the production of your hot mix. Adding a RAP crushing plant to your asphalt production facility can help:
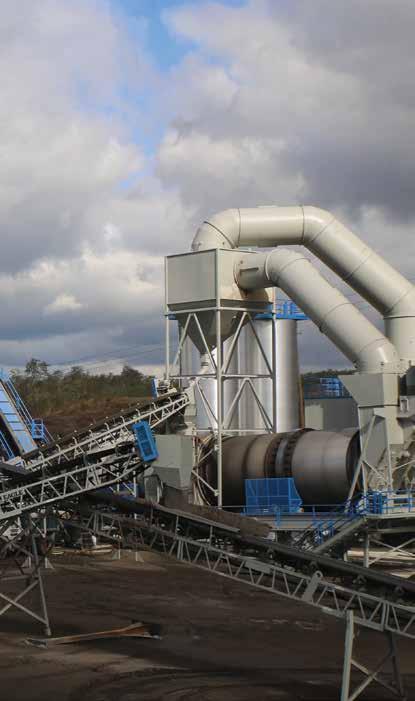
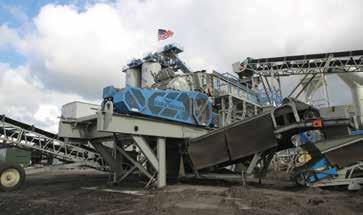
setting up the
pay
• save on material costs by producing RAP onsite compared to having a third-party deliver RAP to your facility, paying for an outside firm to crush RAP on your own site, or utilizing only virgin material;
• improve production control and efficiency by not relying on outside vendors’ schedules;
• increase revenues by accepting asphalt tear outs and millings from others; and
• maintain control over your mix quality and mix specs with production of your own high-quality RAP based on having the right equipment for the job.
Several factors play into the decision of whether adding your own RAP crushing plant makes sense for your business. These include:
• Market size
• Crusher location
• Crusher types and features
• Initial Investment and ROI
MARKET SIZE
Market size is important in considering whether you can realistically sell more asphalt. Are there enough commercial and residential paving companies in the area to buy the extra mix you may be able to produce? How many more contracts could you potentially be awarded by having better control and better quality of your hotmix production? Is your market large enough that you can obtain the RAP you need to produce crushed asphalt for your own mix use? Is there enough current and future residential and commercial market growth, and therefore paving demand in the market, to help you sell more?
CRUSHER LOCATION
You need to consider the location of your crushing plant should you decide to add a RAP crusher to your asphalt production operation. A primary consideration and a good starting point is the type of crusher that will be most beneficial to how your facility operates— such as whether your asphalt production uses stationary hot-mix plants to produce at one, on-site location or portable asphalt plants that move from site to site.
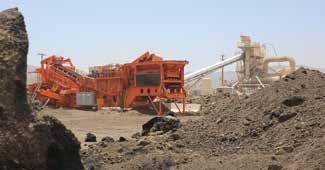
When deciding where to place the crusher in your yard, a good starting point is to consider the type of crusher that will be most beneficial to how your facility operates. Its size and configuration will help you decide where it should be located.
Other considerations are permitting and transport. Permitting rules and fees vary greatly from one locality to another and are different state-by-state, as well. Permit regulations may also differ based on whether you are opting for a stationary crusher permit or a portable crusher permit. Additionally, local environmental regulations may affect an operation’s ability to obtain a permit, depending on the
When
RAP crusher,
attention to the detail of skirting to mitigate dust. In these images you see the conveyor from under the UM-25 Impactor crusher. It feeds back onto the conveyor to be rescreened. All photos courtesy of Eagle Crusher
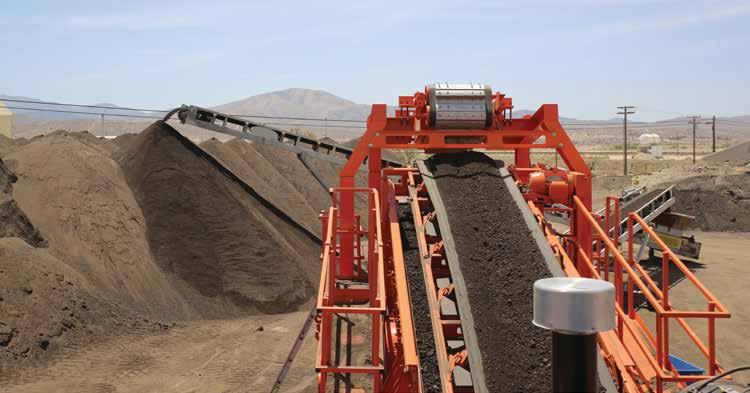
specific crusher specifications for which a business is applying. Acquiring a permit can take time, so it’s important to plan ahead and start the process early.
When it comes to portable crushers leaving their first jobsite to go to another locale, crushers may be permitted for one main location, and then, depending on the state or locale, subsequent temporary permits to move the crusher to different sites may be more easily obtained or may not even be required. You will want to research all of this based on your location.
CRUSHER TYPES AND FEATURES
If you are a start-up asphalt production facility and deciding on whether your operation will use portable or stationary asphalt crushing plants, consider that portable asphalt operations are best in areas where jobs are a considerable distance apart, a market has minimal growth and small population density, and where workloads shift from one area to another due to seasonal factors.
It follows that the type of crusher you choose will match what you choose for your hot-mix production, either portable or stationary. Beyond portable and stationary crushers, choosing the perfect crusher type for RAP crushing comes down to the specific features of the available types of crushers—jaws, cones and impact crushers. Impact crushers are typically the best choice for RAP crushing to achieve the highest quality end-product and the necessary production capacity to keep high-quality hot mix flowing.
Impact crushers use a simpler design comprised of a rotor and two bearings that spin to launch the RAP against a curtain or apron. The simplicity of an impactor like the Eagle Crusher threebar, solid-steel, sculptured rotor works to explode the RAP with the force of the blow bars and launching it into the primary cur-
tain at the proper angle, then smashing it again with the secondary curtain liners to prepare it for its final reduction, creating a very consistent mix to be sent on to the drum as a more structurally sound cubical product.
Jaw and cone crushers on the other hand utilize compression to crush, which can be advantageous when crushing hard rock from quarries. Asphalt crushing isn’t about crushing the rock, but instead about separating the asphalt bonds. When RAP is compressed, it can more easily fracture, exposing white rock and requiring more liquid asphalt to restore the full coating.
There are other issues with jaw and cone crushers, as well. Cone crushers have a significantly smaller feed material size range, meaning they can generally only be fed millings or material that has already been processed, like through a jaw crusher, requiring additional crushing equipment. Jaw crushers are limited on their final output size and cannot produce a cubical product, thus requiring further processing with another piece of equipment, like through a cone crusher.
Realizing that impact crushers are typically a producer’s best bet for crushing RAP, keep in mind that a properly sized and type of screen is critical to any RAP operation. Asphalt producers are typically making finer sizes than other types of aggregate and recycling production. For RAP, the screen is the determining factor for net production. If RAP can’t be screened, it probably can’t be used.
So, let’s explore the features of both stationary and portable RAP crushers. Consider looking for stationary crushers like the Eagle Crusher MaxRap® system, which is designed to crush and screen RAP for product consistency, productivity and profitability, using its UltraMax® impactor.
MaxRap can integrate with any asphalt plant automation. It allows operators to switch from top to base material production from
When setting up the RAP crusher, also pay attention to details like installing magnets to remove any last-minute deleterious material. In this image, you see a magnet affixed over the crusher discharge conveyor of the E-Plant. Material then falls onto the 5X16 triple-deck screen for precise sizing.


Boost Your Silo Performance
MEEKER SILOS & DRAG SLAT CONVEYORS

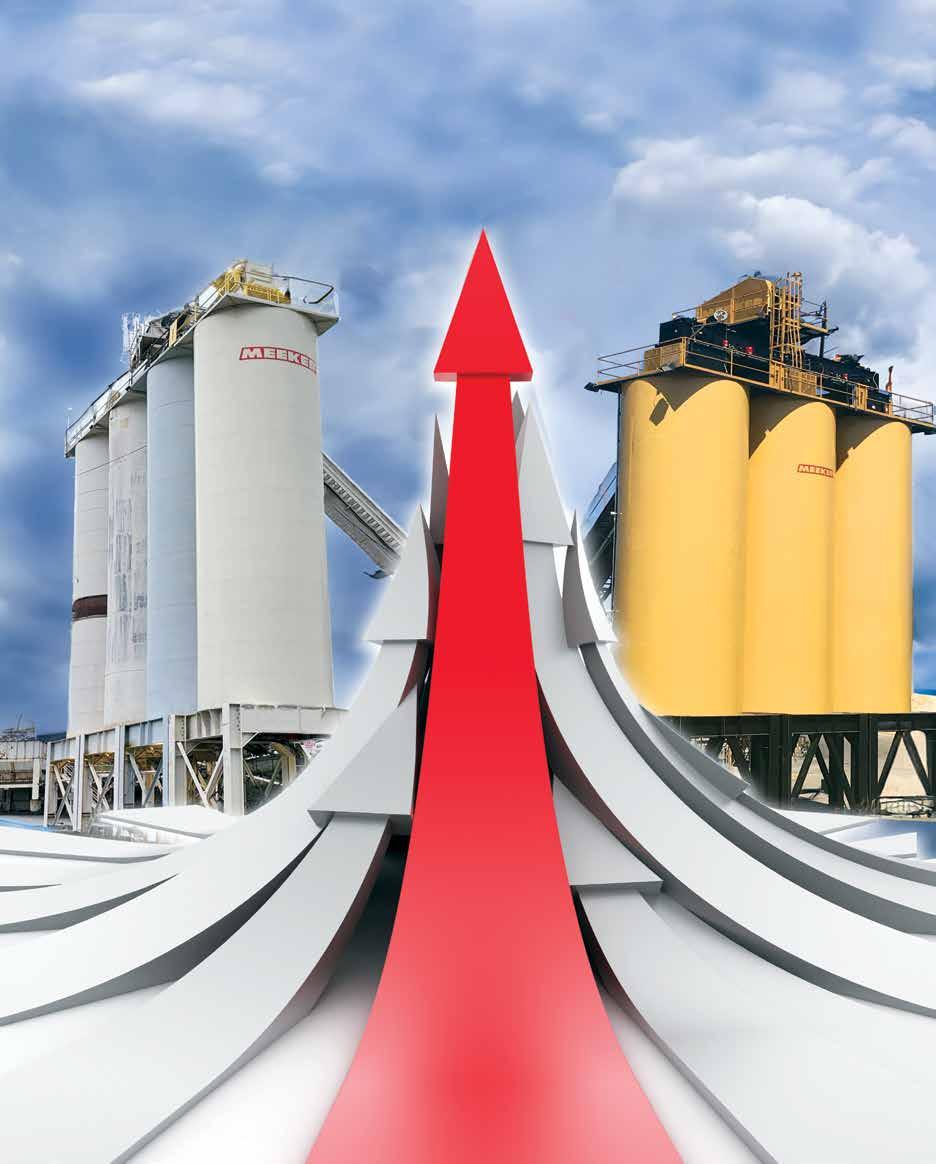

Silo cone opening is 36” wide for ef cient material ow.

Safety gates on all silos, including long-term and standard options.

Recessed tub liners prevent silo wall wear, avoiding bulging issues.

Silo bin top batchers feature secure long-term seals.

Recessed wireways on silo tops eliminate trip hazards.
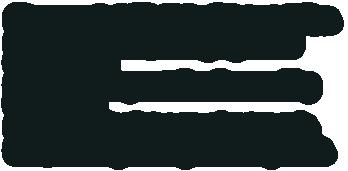
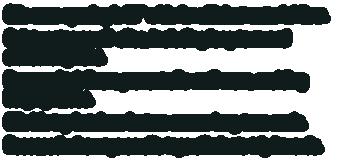

Meeker drag conveyors are larger, allowing slower chain speed and reduced wear.

Hydraulic chain adjustment on slats maintains asphalt entry point, minimizing wear.

Visual chain tension indicators on Meeker slat conveyors aid operators.

All silos prewired with top and bottom junction boxes.

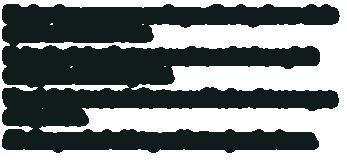
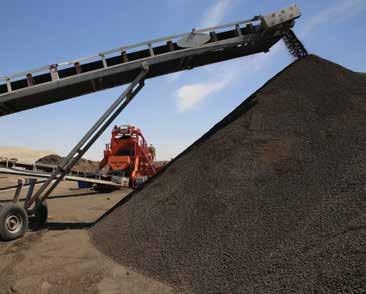
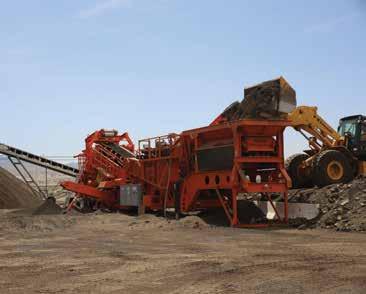
A PRIMARY CONSIDERATION AND A GOOD STARTING POINT IS THE TYPE OF CRUSHER THAT WILL BE MOST BENEFICIAL TO HOW YOUR FACILITY OPERATES.
A versatile and reliable portable RAP crusher should be able to provide the same precision crushing of a stationary crusher, while allowing operators to crush RAP at multiple locations. Such is the case with Eagle Crusher’s new MaxRap 25 Portable.
INITIAL INVESTMENT AND ROI
How do all of these considerations factor together to determine if adding a RAP crusher to your asphalt production facility makes sense financially?
First, with a crusher like Eagle Crusher’s MaxRap or MaxRap 25 Portable, one crusher replaces jaw, cone and screen multi-unit systems for a lower initial investment while maintaining high production of cubical spec product. Choosing a jaw crusher instead of an impact crusher requires additional equipment, like a cone crusher following the jaw, and in some instances, a vertical shaft impactor (VSI) to make a spec final product. This is because using a jaw crusher in a RAP circuit is for primary reduction only, then prepping RAP for a cone crusher, whereas using an impact crusher for most RAP applications requires only one crusher. Two may be necessary where very high capacity or special products are required.
Even if the cost of one impact crusher or crushing system is more than the cost of a jaw, cone and vertical shaft impactor combined, more and different pieces of equipment opens the door for more mechanical issues and more down time, versus keeping production high, and as previously discussed, the higher quality mix and the ability to have spec product high, as well. In most cases, however, the initial investment for an impact crusher versus two to three different crusher types pays for itself more quickly and improves ROI based on fuel savings and maintenance costs, among other factors.
The service friendly design of RAP crushers like the Eagle Crusher brand can help with time and labor costs and less down time while screening. The screening process can continue while the crusher is removed from the circuit. The screen chute system folds out of the way for ease of changing the screen cloth, and screen service platforms are positioned on both sides of the screen for ease of maintenance. All of this adds up to time and labor efficiencies and a better bottom line.
the control house, and most importantly, it produces highly uniform cubicle spec product with a minimum of white rock and a minimum of fines.
Actuated diverter chute work allows multi-feature deck selection, blending, and bypass while the calibration chute for sampling verifies that the mix-design spec requirement is correct. The side discharge conveyor from the crusher may be used for stockpiling or returned to another conveyor for re-circulating back to the plant screen for resizing, and with the system’s ability to screen only, all material can be conveyed to stockpile. The under-screen product conveyor to cross conveyor feeds to the drum mix feed conveyor of the asphalt plant for final processing and mixing.
Additionally, quality hot mix via crushing your own RAP with an impact crusher leads to new customer potential and repeat customers, adding to greater revenues and increased products. This is because RAP impact crushers lead to higher quality mix by separating the binding matrix, airing out the material releasing moisture, making for a drier material going into the hot mix. Drier material saves energy as it eliminates the need for more fuel in the burner.
All things considered, it is worth considering whether it’s time to add a RAP crusher to your asphalt production facility. We hope this helps get you started.
Daniel C. Friedman is the vice president of marketing at Eagle Crusher Co. Inc., Galion, Ohio.
The savvy asphalt mix supplier can be more precise in mix production when he directs crushed and screened product into specific stockpiles or when he conveys it directly to cold feed bins for production.
One of the benefits of having your own recycle processing operation is the ability to crush and screen material at your leisure and to your own specifications. Here a wheel loader feeds material for the E-Plant Triple Deck from Eagle Crusher.
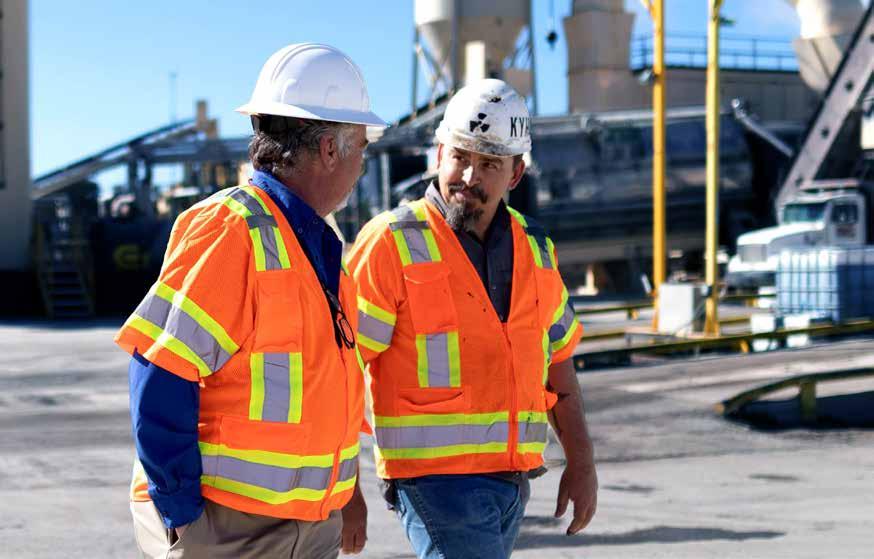
Unlock the Full Potential of Your Asphalt Plant
Sync your production, loadout, scale ticketing, and office processes to boost efficiency and maximize profitability.
Are you ready to experience the power of centralized data and processes?
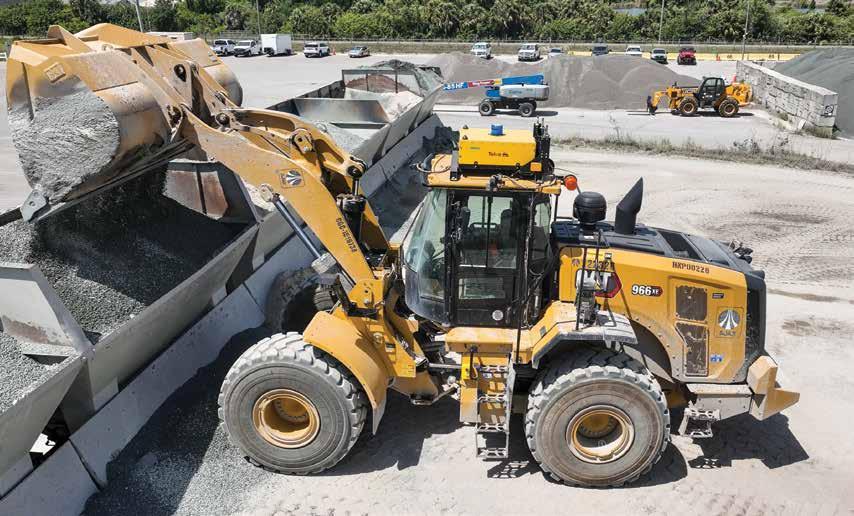
REMOTE TECHNOLOGY SOLVES PLANT PAIN POINTS
Teleo helps Ajax Paving broaden its hiring pool, cut costs, and improve operator physical and mental health with remote aggregate loading.
FROM ASPHALTPRO STAFF
TTeleo outfitted a new Caterpillar 966XE wheel loader with Teleo Supervised Autonomy, the technology that enables remote and autonomous operations of machines from a command center, for Ajax Paving of Florida. Now Ajax will have the option of running the machine, located at its Venice facility, even if the available worker for the day is clocked in at a command center 80 miles away. Here’s how Teleo is helping the asphalt industry attract workers who can keep production up and running.
Readers know asphalt production is a time-sensitive business. When customers need asphalt, it’s needed right away. Ajax Paving, which operates eight asphalt manufacturing plants across the state of Florida and has paved thousands of miles of roadways, needs to ensure they have enough operators to run the ma-
chines that feed their asphalt plants with reliability. The just-intime nature of the business is hampered, however, by an ongoing labor shortage that has made heavy equipment operator roles tough to fill. According to the Associated General Contractors of America, 91% of construction firms are having a hard time finding workers to hire.
Right now, Ajax’s plant in Venice, Florida has its first command center and the Teleo-equipped loader. The locations for the second wheel loader and the other two command centers will be determined by Ajax at press time.
This Caterpillar 966XE wheel loader, equipped with Teleo Supervised Autonomy, pulls aggregate from the stockpile and delivers it to the appropriate cold feed bin at an Ajax Paving asphalt plant.
Ajax Paving turned to Teleo for help. The Teleo-enabled heavy equipment will provide a practical solution to help alleviate Ajax Paving’s staffing challenges. The loaders are to be stationed at two of the company's asphalt manufacturing plants, which are roughly 80 miles apart. This means that once the second wheel loader is outfitted with Teleo’s technology, a single Ajax operator will be able to work across two job sites, simultaneously, from one of three of Ajax’s command centers.
Ajax Paving is also the industry’s first company to use remote operations to load an asphalt plant.
Vinay Shet, co-founder and CEO of Teleo, explained that the technology mixes remote and autonomous operations, and is designed to let a single operator control multiple machines. “When the machine is running in autonomous mode and it can’t handle a specific task, it stops and waits for the operator to take over to control the machine remotely,” Shet explained.
“For example, Tomahawk Construction integrated our technology into their operations and currently has a single operator in Ft. Myers, Florida, operating up to three articulated dump trucks 40 miles away in Naples, Florida.
“Ajax Paving has integrated Teleo Supervised Autonomy and will soon utilize the capabilities so that one operator can control Ajax’s two machines at once. The operator will have the ability to remotely operate one machine while the other is tramming, or autonomously hauling materials from one point to another, and the operator can switch back and forth between the machines and modes.
“Ajax will have three command centers in different locations from which the two machines can be operated. This provides for maximum operator flexibility: an operator in any of these command center locations can control any Teleo-equipped machine in their fleet.”
Andy DeCraene, the executive vice president of operations at Ajax Paving, shared their vision. “We'll be using Teleo at two of our asphalt facilities to remote-operate the loader which feeds the plant. This is going to allow us to not only staff the facility with just local folks, but we can do remote working from other places around the state.”
Having one operator able to control machines across multiple sites has many advantages for Ajax Paving. If an operator isn’t available on one site—due to a general staffing shortage or an operator calling out sick—another operator at a different site can step in and operate the machine.
SAFETY MATTERS
The safety aspects of operating multiple machines at once is handled through the machines’ pauses, as alluded to above. Shet explained, “Teleo’s central command center can control any type of machine and with Teleo Supervised Autonomy, one operator can safely control multiple machine types at once. It’s up to the customer and the operator's comfort level whether they want to or need to switch between the different types of machines. If an operator knows how to operate multiple types of machines, they should have no issue doing so using Teleo’s technology. Alternatively, an operator with no experience operating heavy machines, can learn to do so from the Teleo central command center.”
Shet continued, sharing the Ajax model specifically. “At Ajax Paving, an operator can remotely switch between Teleo-enabled
PUGM I L L SYST EM S
We’ve been designing and manufacturing custom mixing solutions in Tennessee for nearly 40
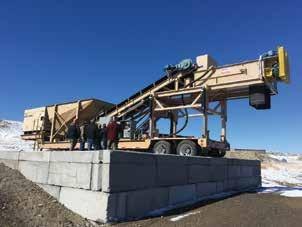

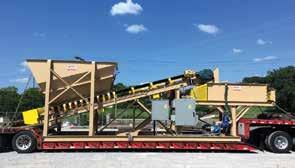
RCC • CTB • Pugmix • Stabilized Sand
Coldmix • Fly Ash • Salt Treatment
machines, but they are only remote operating one machine at a time. This means the operator’s full attention is on the machine and they have a complete view around the vehicle thanks to the many on-board cameras. Currently, they’re remotely operating a wheel loader and then parking the machine and switching to remotely operate another machine.”
Safety is enhanced by stacked technology that detects obstacles, as well as internal backups for shutting down if necessary.
“Our state-of-the-art tech stack is the same as what you’d find in self-driving cars,” Shet explained. “The perception stack detects obstacles such as people, vehicles, other construction machines, and when in autonomous mode, it will stop if something gets in its way. Further, there are multiple redundancies built into the system, so if there’s a network glitch or network loss, the vehicle comes to a safe, complete stop.
“Additionally, the onboard camera systems provide for a wide field of view when an operator is controlling a Teleo-equipped machine from the command center. They have better visibility from the command center than when they’re sitting in the machine because there are no blind spots.”
The perception system, which identifies objects around the machine using cameras, is always running and obstacles around the machine are detected when the Teleo system is on. In remote-operations mode, the operator is alerted by the visual—a big red box around the person or object—to draw the operator’s attention so they can react accordingly. If the machine is operating autonomously, the machine will stop if it detects any object without any need for oversight from the operator.
“Having the perception system running at all times provides the additional benefit of identifying potential hazards that can’t be easily seen by the naked eye, such as if a person or object is very far away or it is dark.”
LEARN MORE
Tomahawk Moves Dirt Remotely
At the end of 2023, Tomahawk Construction became the first of Teleo’s customers to deploy its autonomous capabilities on an active job site.
Tomahawk Construction’s articulated dump trucks used autonomous functions to move material to build a residential community in Naples, Florida, starting in December.
The initial autonomous capability being launched by Teleo was tramming, or autonomous hauling materials from one point to another. Tomahawk Construction used its Teleo-equipped articulated dump trucks for autonomous tramming across the Naples job site. The autonomous feature introduction began with three machines and rolled out to 12 machines over a few months.
By automating the tramming portion of a dump truck driver’s job, one operator can run multiple machines simultaneously, multiplying their productivity. The physical dumping of materials is handled remotely by one operator controlling multiple machines from a comfortable command center.
“Teleo’s technology has the potential to completely transform our operations,” said Scott Lyons, managing member, Tomahawk Construction. “With Teleo, two of our dump trucks that have been idle will be put back into service to haul dirt across the site autonomously, allowing our remote operators to do more. This will help us to run a more efficient operation.”
Shet outlined the safety multi-layer concept in the Teleo technology:
• Layer one: the system always self-diagnoses, and if any subsystem is not running perfectly the machine will safely stop.
• Layer two: full visibility. The operator is fully immersed in the world around the machine and the environment in which it’s being operated.
• Layer three: the full autonomy perception stack is running at all times.
“Further, all data is recorded and provided back to foremen and other worksite leaders so they can review and observe operations and use the information to help further train their operators.”
FOCUS ON HEALTH
While it may seem that younger, tech-native operators—those who are more familiar with gaming and technology—would be the only ones who adapt to this new technology, that hasn’t been the case. “Even some of the older generation operators have picked it up within 20-25 minutes,” DeCraene noted.
Shet explained that the ideal candidate for remote-operating equipment is anyone. “Remote operations make the operator role more attractive and accessible. Teleo eliminates physically demanding aspects of operating heavy machinery, like harsh vibrations or sitting inside the vehicle for long periods of time, making the machines easier to operate. We expect remote operations to help Ajax attract a more diverse applicant pool to include people who are typically under-represented in this industry including women, people living with disabilities, veterans and more.”
And workers don’t have to feel anxiety over learning the system.
“We provided three weeks of training for everyone in Ajax’s organization who needed to be trained to become proficient operators, including both the veteran and younger operators,” Shet said.
Stress is, in fact, one of the factors the remote operation is alleviating for workers. The technology addresses physical wellbeing and mental health by bringing workers to a central location.
The job of a heavy equipment operator can be extremely stressful, both physically and mentally, because of heavy machine vibrations, secluded job sites and more. Ajax Paving President Vince Hafeli is an advocate for mental health in the construction industry and he quickly recognized how Teleo could help both the business and its operators.
“One of the perks of integrating Teleo’s technology is that it takes operators out of the cab, making their lives easier,” Hafeli said. “By removing the physical aspects of doing this job, the mental demand automatically decreases. It’s a welcome benefit of the technology.”
Less Maintenance Through Precise Operation
One of the unintended positive gains Ajax realized after implementing Teleo’s technology was the savings that could be achieved with maintenance costs. “If we're running the machines only when we truly need to run them, we’ll get more production out of them while putting less hours on them. That efficiency is going to lower our maintenance costs,” added Ajax Paving Fleet Manager Dan Maitland.
Teleo provides a solution that will help Ajax Paving broaden its hiring pool, allows operators to control machines in more than one location simultaneously, reduces maintenance costs, and provides meaningful mental health benefits that are a priority for the company. According to Hafeli, “We say that the future is riding on Ajax. Well, the future is now at Ajax!”
RAISING THE STANDARD
Since its introduction, the Weiler P385 has set the standard for commercial pavers. The P385C raises that standard.
Increase to 120 hp with the Cat® C3.6 Tier 4F/Stage V engine.
Variable speed and reversible conveyors and augers and a 25% increase in tunnel height provide optimal material output.


Modular conveyor drive and sealed chain case increase feeder system reliability and life.
Enhanced heat system performance with direct-drive hydraulic generator and elimination of GFCI breakers.

BEST PRACTICES FOR MOBILE ASPHALT CRUSHING
BY ASPHALTPRO STAFF
MMobile asphalt crushing offers a range of benefits, from enhanced efficiency and flexibility to environmental benefits and lower costs. However, to harness these benefits, a crushing operation must operate efficiently or they risk wasting money on operating costs and limiting their production.
That’s why World of Asphalt 2024 brought together a panel of crushing contractors from around the country to discuss optimal crushing and screening setups, preventive maintenance processes, and common asphalt crushing problems.
HOW TO SET UP YOUR MOBILE CRUSHING SITE
When it comes to determining the setup of your mobile crushing operation, you must first know what you will be crushing, and what size you’ll be crushing it into. And, it largely comes down to reducing wear while maximizing production. “Your wear cost is very important,” said Ron Garofalo, president of DAG On-Site Crushing. “It’s not always about your production rate, it’s about your wear cost.”
For example, Allen Kurre of Kurre Contracting said, there’s no reason to run asphalt millings through the crusher. “It just causes unnecessary wear.” Eric Bruno, president at Midwest Crushing
& Recycling, estimates 70% of asphalt millings won’t need to be crushed, so when he’s handling millings, he adds a scalper to screen out that material ahead of the crusher. “Scalpers are easy to set up, easy to move, and that 70% of material pays for the scalper real quick if you’re looking at large quantities.”
Garofalo provided another example that increases production and reduces wear by removing the screen deck and crushing 2-inch minus material when applicable. “It’s a very usable material for fill, because when I say 2-inch minus off an impact, there will be a lot of 1 ½ inch in there, a lot of ¾ inch in there,” he said.
QUICK TIP: “With an impact crusher, you’re going to get very usable, symmetrical, compactable material,” Garofalo said. “With the jaw crusher, you might set it for 3 inches, but any material that can fit through the slot at the bottom is ‘done’ even if it’s 3x5 inches, so you’ll still need a secondary crusher when you’re running through a jaw.”
He uses a jaw crusher when crushing rock or as a primary crusher on large jobs. For example, they recently crushed 20,000 tons of con-
crete with rebar. “We ran it through the jaw, got the steel out with the magnet, and used our RM90 like a George Foreman grill,” Garofalo said. “We set it and forget it, because it’s getting fed 6-inch material all day from the jaw in front of it.”
Garofalo said using such a setup increased their production from 700 tons per day to 1,400 tons per day.
DJ Cavaliere of Cavaliere Industries has his own solution to maximize production. “We only make ¾-inch minus,” he said. “For years, we gave our customers whatever they wanted. Now, we’ve trained them that ¾-inch is all we do, so they bid their jobs knowing this. We aren’t going to change the screen deck or have a separate pile just because you want 200 tons of 1 ¼-inch.”
Cavaliere said this decision has been key to their business. “We do 25,000-30,000 tons on a yard the size of a postage stamp, where our waste bins hold 800 yards of material,” he said. “We probably have 500 yards of material on each end—finished and unfinished. What comes in goes right out.”
Bruno also makes only one product, ⅝-inch. They’ve configured a way to do so with a one-person operation. “I use my top screen as my finish deck and I don’t mess with my mids belt,” he said. “It looks funky, but it works.”
The operator feeds the scalper to size it, the finished product goes straight into the stacker and scale while the chunks go to the crusher. “I’ve got no material hitting the ground, it’s all hitting my stacker and my scale, so it’s making me money as fast as it can be processed,” Bruno said. “I’ve trained my customers that if that material hits the ground, it’s theirs to move. If I have to get a wheel loader out there, that’s going to increase their price.”
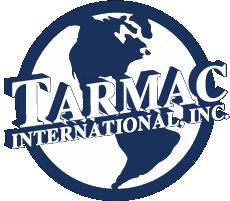
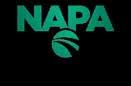
Garofalo has a different approach. “We’re a custom crushing company, so we crush what the people want,” he said. “We change our screens and we get paid to change our screens. It’s not for free. You have to get paid for what you do.”
QUICK TIP: Garofalo told the audience to keep fines from getting into the crusher. “There’s less wear on an impact crusher crushing concrete all day than crushing fines.” He recommends taking care to minimize dirt and other fines when loading the crusher. For example, when striping slabs of concrete, the operator should avoid taking any dirt with the slab.
START WITH GOOD MATERIAL
One lesson every crushing operation must learn is ‘Garbage in, garbage out,’ Garofalo said. “We’re running impact crushers, not incinerators,” Bruno added.
He stresses the importance of looking at the piles your customers are asking you to crush. “If it’s going to be dirty, I’m going to have to budget this much more per hour because I’m going to have to clean, we need separation time, etc.” Bruno said. “We aren’t choosing what people bring us, but we charge accordingly based on what they bring us,” Cavaliere added.
If you can’t view the piles, Bruno recommends contractually protecting yourself. “It’s important in your contract that you say, ‘You’re liable for that, because I can’t show up to a job five hours away from my house and be expected to know what’s in that pile.’”
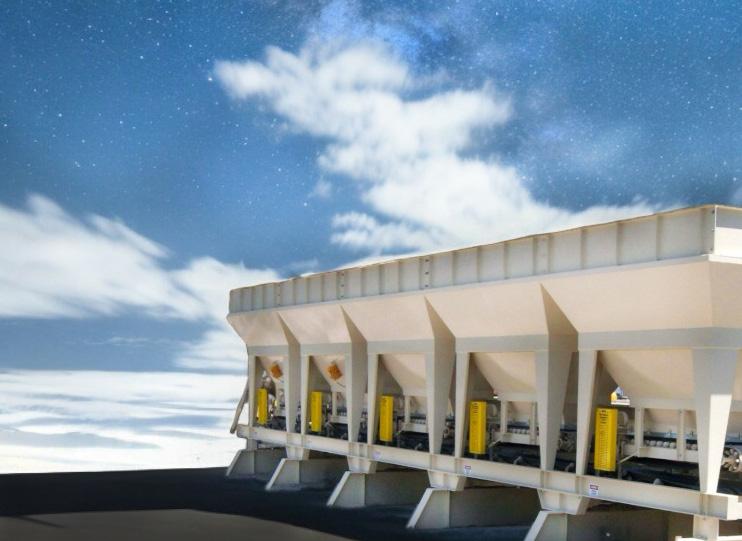


QUICK TIP: Although most panelists reject petromat outright, Bruno has found a way to process it efficiently. “My crusher has a cross belt on the bottom so you can run your trash in the opposite direction, so I can spit the petromat back on the ground without getting out of my excavator,” he said. “We have a lot of petromat in southern Illinois, and the ability to handle petromat sets me apart in my area.”
There are some materials Bruno simply won’t touch. For example, if they spilt liquid AC at the asphalt plant and shove it up into the millings or the plant waste. “If I roll up and find that, I’m not touching that pile because once it gets in my crusher, it’s going to build up, stop up, and I’m going to spend hours chiseling,” he said. “I’m not there to clean my crusher, I’m there to crush material.”
Part of this approach requires empowering operators to make decisions about what goes in the crusher. “I tell my guys if they see something that shouldn’t be put in the crusher, shove it to the side. That’s the customer’s to deal with.”
HOW TO CHOOSE THE BEST BLOW BARS
“Selecting the right blow bars will depend on what you’re crushing and how you’re crushing it,” Garofalo said. The goal, of course, is to get optimal wear out of each set of blow bars regardless of the material from which they’re made.
Kurre prefers high chrome hammers for crushing asphalt, estimating they get 15,000-18,000 tons out of each set. Cavaliere also prefers high chrome hammers for crushing asphalt, adding that they have high wear resistance but can be brittle. “If you get something like a sledgehammer head that ends up going through the crusher, it will crack that hammer,” he said.
Since his company has moved away from supplying multiple types of material, they primarily use hammers with a ceramic inlay. “We get the best wear and minimal breakage with those,” he said, adding that they get roughly 250 hours out of each set.
QUICK
TIP:
With a four blow bar system with two longs and two shorts, the operator is usually only changing two blow bars at a time. “Your longs become your shorts,” Garofalo said.
Bruno also prefers ceramic hammers. “They help take the heat off that steel and it increases our wear life,” he said, estimating they can get 20,000-25,000 tons per set in Illinois, where the rock is softer, but that the hard red rock they crush in Arkansas cuts that estimate in half.
Garofalo recommends high chrome hammers for crushing asphalt, but ceramic inlay hammers for concrete. Although his company crushes both materials, Garofalo said they don’t usually switch hammers if they are switching between asphalt and concrete regularly because of the time required—especially if they’ve been crushing asphalt due to potential AC buildup.
“If you have the choice and you’re doing both products, always run concrete through the machine a little bit before you’re going to change your blow bars because it loosens everything up,” Garofalo said. “That’s just one of those little things we just do because it saves half an hour or so.”
Ultimately, he said, it comes down to time and experience. “You have to watch, keep records, count hours, and you’ll learn for yourself what your optimum wear is out of what type of blow bar.”
QUICK TIP: Pretty much all the panelists prefer square mesh screens and have minimal trouble with sticking.
“Moisture kills everything in the material processing industry,” Bruno said, adding that if the material is wet, it’s going to stick. “If it sticks, we just go up there and tap the screen with a hammer and we’re good to go.”
HOW TO KEEP COMPONENTS CLEAN
One challenge when crushing asphalt in particular is that some of the fines will become airborne. When they hit the radiator or any other hot component, the AC will reliquify and stick to that component.
To prevent this from happening, Kurre recommends paying attention to the way the wind is blowing to minimize dust circulating to these critical components. Cavaliere recommends doing all you can to keep the dust down. “Our philosophy is to add more water to drop those dust particles to the ground,” he said. They also try to mix plant waste, which can be warm, with older millings to let it cool.
Daily maintenance is also key. Garofalo has a service truck out with every crew every day to meet the crew’s maintenance needs.
“We find keeping our [radiator] blown out every day and paying attention to the way the wind blows is usually enough,” Bruno said. “When we do have some build up, I found that spraying the radiator with a citrus spray and pressure washing it with hot water will break that stuff down and melt it right off.”
For Kurre, radiator buildup has been a significant problem. In the past, they’ve had an extra radiator on site so they can swap them out when the buildup gets too bad. “We’d have one in the machine and the other in a tub of citrus,” he said. Then, they began using miner’s moss around the outside of the machine to protect internal components. “That works really well for us. We can take it off, clean it, reuse it, throw it away when it gets too bad.”
QUICK TIP: Cavaliere recommends on cold nights putting antifreeze on the inside of your belts to prevent them from freezing overnight. Garofalo added that you should always run your belts to fully clear out your machine, especially in cold weather. “If you have debris left in there and there’s a rainstorm that night and it gets cold…you’re done,” he said.
“There’s nothing you can do until it gets a little warmer. Or else you’ll be tarping it and heating it with space heaters and you won’t start working until 9 a.m.”
HOW TO LOAD THE CRUSHER
“Crushing is the easy part, as long as the material has been prepared correctly,” Garofalo said. When it comes to crushing, slow and steady wins the race, he added. “We sometimes get calls from customers who think we aren’t loading the crusher fast enough, but I tell them as long as material is coming out of the final belt, there’s no sense putting anymore in the crusher because it’s not going to crush any faster.”
That’s because it is so important to check materials before loading them into the crusher. The way Garofalo handles this is by training operators to maximize the number of opportunities they have to check the material. “The first point is your ground man, and he’s looking all the time,” Garofalo said. “The second is the excavator operator is pushing that pile out [to see what’s in it] and scooping up that same pile each time.”
The third is by loading the back of the feeder for more time to see if anything undesirable is headed into the crusher so you can stop the feeder and remove it. “If you go to feed undesirable material into the crusher, you’re going to be inside the chamber getting it out,” Garofalo said.
Cavaliere’s approach is to use a 2-foot bucket all day long. “I don’t care if the operator has to make an extra cycle,” he said. “[If you’re loading too much at a time] you may not know you’ve put a rock in there that’s way too big and they’re not getting material through because they’re overfeeding it and jamming it.”
“I’d rather do 100 tons an hour all day long than 200 tons an hour for two hours,” Cavaliere said. “You’ve got to reduce that black belt time, and that starts with the prepping and feeding.”
Bruno uses a 3-foot bucket for a similar reason, adding that versatility and the ability to use a smaller bucket is why he opts for excavators instead of wheel loaders to feed the crusher. He’ll sometimes use a 60-inch bucket on his excavators if he’s crushing asphalt and using his screens, “but we’re still watching what we’re putting in.”
“You have to understand somebody’s going to throw teeth in a pile and you’re going to run it through your brand new machine and ruin $8,000 worth of hammers,” Bruno said. “You have to be cautious.”
Garofalo hit this point home with an example from a job where they were crushing 4,000 tons of asphalt millings and chunk asphalt. “You’d think there’d be no steel in it, but we came across a 988 loader tooth,” he said. Knowing if there was one there was likely to be more, that two-day job turned into a full week. “But we found every tooth! I don’t know why a mechanic would throw teeth in the asphalt pile, because he probably could have gotten a nice dollar in scrap for those, but you can’t take anything for granted when you’re loading the crusher.”
These best practices ultimately come down to the operators. “The operator is the most important part of the equation,” Garofalo said. “They have to be looking, they have to be able to hear. They can’t be operating with earbuds in so they can hear a rock caught on the belt and stop the machine.”
Kurre recommends having the same operator run the same machine every day, even in mobile operations. “You don’t want to bring your crusher to the job and have just any operator start loading it because he’s going to try to load it as fast as possible like it’s magic.”
About the Panelists
• Eric Bruno is president at Midwest Crushing & Recycling. The company started crushing in 2009 and last year crushed 100,000 tons of asphalt and 120,000 tons of concrete in southern Illinois, southeast Missouri and northeast Arkansas.
• DJ Cavaliere is with Cavaliere Industries, Stamford, Connecticut, which is a site contracting company started in the 1950s.
• Ron Garofalo is president of DAG On-Site Crushing in New Jersey. Originally a paving company, they purchased their first crusher in 2005 to recycle their own material, but the crushing business quickly grew to serve outside customers as well.
• Allen Kurre of Kurre Contracting has been crushing since 2004. They used to crush rock, but today the company focuses on concrete and asphalt, crushing around 150,000 tons per year.
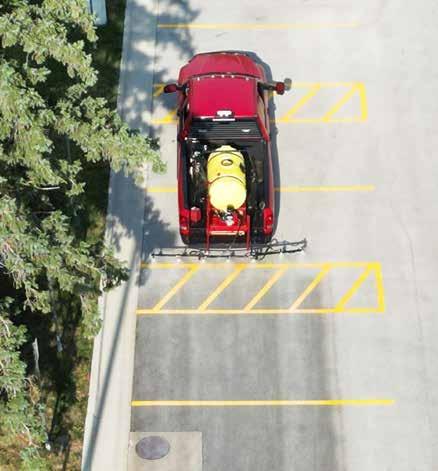
This isn’t your typical topical.
Invigorate Plus® sealcoat penetrates deep down to restore more of every road. Since this sealcoat is a polymer-modified solution, a single application both restores oxidized asphalt and seals the pore structure. It also goes on clear, so there’s no need to re-stripe the road.
Who’s Your MVP?
As we near paving season playoffs, you look for the most valuable workers, equipment and technology to get you through the season.
BY ASPHALTPRO STAFF
It’s the hottest part of summer and we’re ramping up for the home stretch. There’s only a few short weeks left in some parts of North America to get all those projects completed. We’re entering hurry-up-andget-it-done mode out there where every member of the crew is your most valuable player, and every project must be a winner.
There’s no time to get called back to fix something.
That means you want every piece of equipment to be “healthy” and ready to function at its best. From attachments to highway class pavers, original equipment manufacturers have been acquiring new partners and launching new iron and/or new updates to technology to make sure you have what you need to get through the end of construction season. Take a look at the offerings on the next few pages to see if there’s anything that can help you make a run for the playoffs.
AMMANN GROUP
Readers may be aware that Ammann Group, Langenthal, Switzerland, manufactures pavers and compaction equipment in addition to asphalt mix production facilities. This summer, the group announced it had finalized its acquisition of the ABG paving product line from Volvo Construction Equipment.
“ABG is a strong brand that we’re proud to welcome to Ammann,” said Hans-Christian Schneider, CEO of Ammann. “We will continue to build on ABG’s exceptional product line and reputation and provide complete roadbuilding solutions for the industry.”
This is an international move. The transaction includes the transfer of Volvo CE’s paving businesses in Linyi, China, and Bangalore, India, as well as Volvo CE’s ABG facility in Hameln, Germany. ABG pavers and screeds will continue to be produced at the facility in Hameln. The production facilities in Mehsana, India, and Suzhou, China, will also be a source soon. ABG in Hameln will become the center for paving
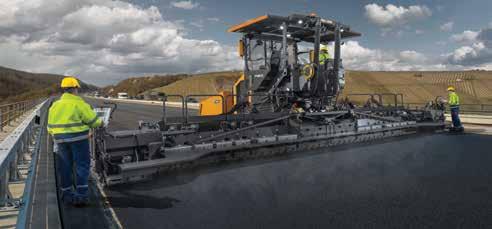
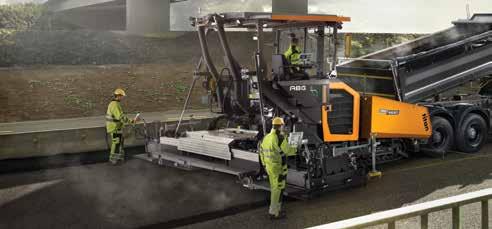
TOP: The Ammann ABG fixed screeds feature electric heating and offer paving widths ranging from 8 to 42.6 feet (2.5 to 13 m). BOTTOM: The Ammann ABG 6820 tracked paver offers a base paving width of 8 feet (2.5 m) and potential placement of 700 tonnes per hour. It features an advanced management system (EPM3, Electronic Paver Management) and user-friendly controls for performance, according to the manufacturer.
operations within the Group, according to a recent press release.
Initially established as a construction equipment repair shop in 1945, ABG in Hameln has evolved into one of the most recognized paving brands globally. Demonstrating its ongoing innovation, ABG recently introduced a new electric paver at INTERMAT 2024 in Paris.
Ammann will retain the respected ABG name. “The ABG brand is synonymous with quality in the industry and aligns perfectly with Ammann’s history in asphalt compaction,” said Bernd Holz, executive vice president at Ammann.
The range of paving products offered includes the compact Ammann ABG 2820 tracked paver, with a basic screed width of 4.9 feet (1.5 meters). On the other end of the spectrum, the Ammann ABG 8820 tracked paver boasts a 42.6-foot (13-m) paving width, large hopper and powerful engine for challenging production jobsites such as airports and highways.
“In addition to our smallest and largest pavers, we have several other models to meet the unique needs of every customer,” Holz said.
For more information, visit www. ammann.com
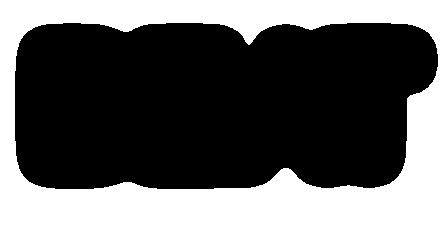
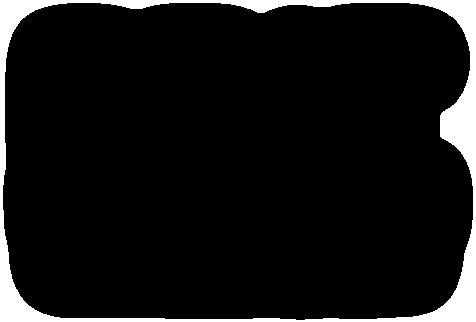
BEAT

WITH A DRUM RETROFIT
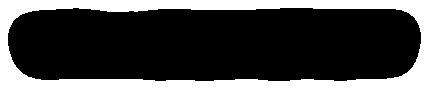


Increase production and efficiency without the investment of a new drum. A leader in the retrofit market, we’ll work with you to come up with the best solution at a competitive price.
· HIGHER RAP PERCENTAGES
· SINGLE POINT ADJUSTMENT
TRUNNION DESIGN WITH HEAVY
DUTY TIMKEN RAIL CAR BEARINGS
· WEDGE-LOK™ TIRE SUSPENSION
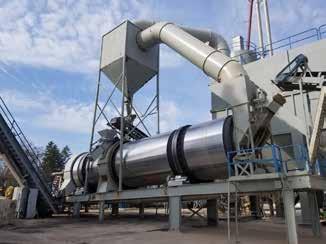
· IMPROVED FLIGHTING DESIGN
· PARALLEL TO COUNTER FLOW CONVERSIONS
· PORTABLE AND STATIONARY

PRODUCT GALLERY
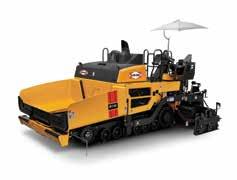
The PF2110C tracked paver from Blaw-Knox is a highway class paver featuring a Cummins Tier 4F/Stage 5-compliant engine and optional MOBA automatic grade and slope control.
BLAW-KNOX
The new Blaw-Knox 7000C series tracked paver was featured at the 2024 World of Asphalt show in Nashville. The all new PF7000C (and PF-5000C) series highway class paver features a new Cummins performance series engine, and all-new telematics. The all new “C” series pavers will boast a new Cummins Tier 4F / Stage 5-compliant engine as well as a MOBA automatic grade and slope control option, which is also available for the 5000 and 4410 series pavers.
For more information, visit www. blawknox.com.
CATERPILLAR
Caterpillar’s VisionLink cloud-based, customer-facing platform provides an integrated full-fleet management solution to track assets, maximize machine uptime and optimize utilization. The platform is scalable for customers of all sizes and offers streamlined subscription levels to suit varying customer needs.
The manufacturer integrated three previous offerings and added a refreshed, intuitive interface to deliver a solution to help customers manage an entire fleet, regardless of manufacturer. Migration from the three retired products to the new VisionLink is designed to be seamless for customers, automatically moving user accounts, asset information, current subscriptions and custom settings to the new platform.
The updated version continues to offer core telematics data standard with every machine to answer important questions about assets, including daily location, utilization, fuel usage, and maintenance re-
minders, and integrates with Caterpillar’s extensive digital ecosystem.
Top 4 Features of VisionLink:
• Full Fleet Visualization allows customers to access all their asset information for both Cat and non-Cat equipment—whether owned, leased or rented—in one centralized place. Dashboards allow customers to track by projects, groups and geofences.
• “Needs Review” is a feature that brings focus to instances that need action, creates workflows to schedule tasks, and provides links to buy parts or request services.
• Task Management creates and assigns tasks to ensure maintenance or service completion.
• Mobile App is optimized for smartphones to keep on-the-go customers updated with key metrics, asset locations, fuel levels, idle time, and more.
DYNAPAC
Dynapac celebrates its 90th anniversary by partnering with Dream On 3, a renowned charity dedicated to making sports dreams come true for children living with chronic illnesses, intellectual and developmental disabilities, and life-altering conditions.
Founded in 1934, Dynapac has a rich history of innovation and commitment to excellence in the construction industry. As the company reaches this significant milestone, it reflects on its journey and the communities it has impacted. To mark this special occasion, Dynapac is directing its efforts toward giving back to the community through a meaningful collaboration with Dream On 3.
As Dynapac celebrates its 90th anniversary, it acknowledges the importance of community support and its role in the company’s success. This partnership with Dream On 3 is a testament to Dynapac’s dedication to giving back and fostering a culture of compassion and generosity.
“We are honored to support Dream On 3 as part of our 90th-anniversary celebration,” said Dynapac President Jamie Roush. “This partnership allows us to give back to our community and make a meaningful impact for children and young adults with life-altering conditions. We are committed to helping make their dreams come true and believe in the positive difference it can make.”
For more information, visit: https://p2p. onecause.com/dynapacteeingupdreams/home.
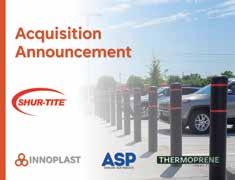
INNOPLAST
ScaleCo Capital (ScaleCo), Cleveland, Ohio, announced its investment in ShurTite Products LLC (Shur-Tite) in June. Shur-Tite is the second add-on acquisition for ScaleCo’s Innoplant Holdings (Innoplast), Garfield Heights, Ohio. Innoplast, a manufacturer and distributor of pedestrian and traffic safety solutions, was founded in 2005 and acquired by ScaleCo in April 2021. This acquisition will grow the Innoplast portfolio to 80 employees.
Founded in 2000, Shur-Tite, which specializes in designing, manufacturing, and distributing highway safety, pedestrian safety, and traffic safety products, has a rich history of partnering with all constituents involved in state and municipal roadway safety. Based in Gainesville, Texas, the company offers a broad portfolio of safety solutions to customers across the United States and five countries worldwide.
“Innoplast and ScaleCo couldn’t be happier with the addition of the Shur-Tite product line and team,” CEO of Innoplast Gary Bowling stated. “This partnership diversifies our product offerings from parking lot assets to the DOT space, increasingly growing our focus and expanding our reach in the conspicuity and traffic safety sectors.”
JETSTREAM
Jetstream of Houston LLP introduced its next generation of the MagJet® X40 waterblasting tool featuring high-speed rotation for cleaning industrial surfaces. The MagJet® X40 Gen 2 rotates in a 360-degree pattern at 1,500-3,000 rpm, doubling the typical operating speed of the previous model. Rated up to 43,500 psi (3,000 bar), the tool can be paired with Jetstream’s standard shotgun or QuadraBlast air gun for high-speed cleaning and surface preparation applications.
Do you have used equipment in your yard?
Le t the Stans te el team help you sell it .
Turn your surplus asphalt plant equipment into much needed plant upgrades.
Our trusted and reliable asphalt experts will come to your site and appraise your equipment or plant.
All you will have to do is sit back and let us bring approved buyers to you!
Inspection
Each piece will be inspected by one of our experienced team members.
This allows us to give you an accurate assessment of the equipment values, with the goal of getting you top dollar for your excess equipment.
Gathering all of the information up front allows us to respond quickly to inquiries, keeping the communications quick and efficient.
Marketing
Our website, stansteelused.com, has the latest analytics built in, so we can see who is looking for what, in what part of the country.
This info allows us to quickly qualify and narrow the search for buyers for your equipment. The Stansteel / Hotmix Parts Team has 100's of customer interactions each day, we get the word out quickly on used equipment.
With a database of 1,000's of Asphalt Producers in the US and Canada, we have the marketing power to get your equipment in front of more buyers than anyone.
Email - blast and print advertising are used to let buyers see your equipment.
Showing
Buyers will be accompanied by a Stansteel representative when they visit your site. All applicable Safety protocols will be followed. We do the work, so you don't have to.
Sales
We handle sales contracts.
Bill of Sale to transfer ownership. Funds paid in full before transportation. Loading / Freight Coordination Services are available as needed.
We are always here for the Buyer and the Seller, promoting a seamless transaction.
Support Team Available 24/7.
“The MagJet has been a reliable and popular tool for industrial cleaning applications,” said Jordan Koster, product and marketing manager for Jetstream. “However, customers were looking for higher rotational speeds without sacrificing quality. We took up the challenge and found the perfect solution when we decided to update the MagJet design. Not only does this generation of the tool allow for higher rpms, it also still provides efficient cleaning at the previous rotational speed, making it a great option for a variety of applications.”
Jetstream’s magnetic braking system controls the tool’s rotational speed. The MagJet’s updated design features magnets on the exterior of the tool and a copper ring on the interior, which dissipates the heat generated by the rotation and allows the tool to revolve at higher speeds without losing the magnetic hold.
The MagJet X40 Gen 2 uses up to four straight-pattern nozzles with a maximum flow rate of 7.0 gpm (26.5 lpm). The tool uses the company’s Sapphire UHPX/UHPXi Series or Synthetic Diamond UHPXD Series nozzles. The new design offers a lifespan between 50 and 75 hours, according to the manufacturer. Multiple head assemblies with optional kits are available to adjust the rotation speed across a wide range of flow rates for each project. The tool is compatible with waterblasting shotguns using a standard 9/16” HP female inlet connection.
PHCO
Process Heating Company (PHCo) Lo-Density® Rigid Tubular Drywell Tank Heaters provide an efficient and safe form of heat for asphalt and emulsion distributor truck tanks, according to the manufacturer. With the Lo-Density heating system, the operator simply plugs the heater in at the end of the day, and it maintains the emulsion at the correct temperature overnight or over a weekend. The result is that the truck is ready to begin work immediately in the morning, without waiting on burners to heat the asphalt at the beginning of the shift.
With no open flame, these heaters eliminate concerns associated with lighting and operating burners. PHCo’s unique drywell-style elements reside inside the heater’s sheath. The low-watt-density heaters dissipate controlled heat on the sheath, providing even heat distribution throughout the reservoir to prevent coking or damage of temperature-sensitive asphalt and emulsion material. The drywell-style

UL-listed controls located on the distributor truck fender offer easy-to-use complete automation of temperature regulation with the Lo-Density® Rigid Tubular Drywell Tank Heaters from Process Heating Company.
heating elements also are easily accessible from outside of the tank, eliminating the need to drain the tank to service them.
The tank heaters can be installed as new or retrofit equipment. In fact, in just the past few years, distributor truck manufacturers have increasingly promoted their ability to provide an electric heat option on their units. PHCo also offers a drop-in heater option for current truck owners who are interested in converting their trucks to either all-electric heat, or a combination of electric and fossil-fuel heat.
UL-listed controls located on the distributor truck fender offer easy-to-use complete automation of temperature regulation. The main indicating temperature control regulates the product temperature and includes a high-limit control for safety. The main disconnect and individually fused heat circuits provide overcurrent protection. All components are mounted and prewired in a UL-listed, weatherproof enclosure.
Each heating unit is designed for the individual application, and can be customized to meet the specific needs of the manufacturer or user for sheath diameter, number of elements and sheath length, or applications. Rigid Heaters can be made from mild steel or various grades of stainless steel, depending on the application. The sheath wall thickness ranges up to 0.3 inch for durability and corrosion resistance. The heating units are suitable for a kilowatt rating of up to 1,000 kW; voltages up to 600 VAC, in single- or 3-phase; and watt densities of 3 watts per square inch of heater surface being standard. Terminal enclosures come standard with moisture resistance. Process Heating Company stands behind its equip-
ment, offering an industry-exclusive five-year element replacement guarantee.
For more information, visit www.processheating.com.
POTHOLE HEROES
Pothole Heroes announced its expansion into the Atlanta metro area, in May. Pothole Heroes is a woman-owned business providing sustainable asphalt maintenance to commercial, residential and municipalities throughout the Southeast and Ohio Tri-state area. Pothole Heroes chose to expand its operations into Metro Atlanta due to the area’s rapid growth and need to maintain its infrastructure. Metro Atlanta has experienced an 18% gain in construction starts over 2023’s numbers, gaining about $5.4 billion in new projects breaking ground. Metro Atlanta’s new commercial and multifamily construction this year ranks third across the country so far, according to Urbanize Atlanta.
Leading the Atlanta-based team is Reggie Nevels, regional director of the Atlanta market. Nevels earned his undergraduate degree from the US Military Academy at West Point and his MBA from University of Notre Dame. His leadership experience includes working as an officer in the US Army, serving as a process engineer and enterprise innovation manager at USAA, and owning a storage and organization system solutions company in Central Florida.
“We are very excited to bring Reggie on board to lead our growth in the Atlanta Metro region,” said Rebecca Neidich, founder of Pothole Heroes. “His experience as a former business owner and US Army veteran brings efficiency, management and client relationship skills to the role.”
THUNDER CREEK
Coop’s Truck & Equipment of Bangor, Maine, has added the Thunder Creek lineup of field fueling and service solutions to its new equipment sales lineup. The company specializes in truck, trailer and equipment solutions for the construction and agricultural industries, including truck body fabrication, farm tractors and livestock trailers.
TOPCON
Topcon Positioning Systems announced an addition to its HiPer family of global navigation satellite system (GNSS) receivers. The HiPer CR is a compact and lightweight
INNOVATION ‘24 EAGLE
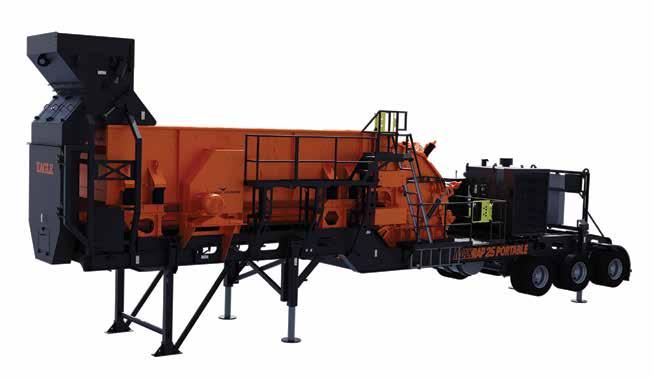
Discover the MaxRap® 25 Portable, Eagle Crusher’s latest new-product innovation for the asphalt industry. Featuring Eagle’s UltraMax® 25 impactor with its high reduction ratio and North America lifetime rotor warranty, the MaxRap 25 Portable provides the same precision crushing of the stationary MaxRap, allowing operators to crush RAP at multiple locations with ease.
Experience the benefits of multi-feature deck selection, blending, and bypass; sampling to verify the mix-design spec requirement is correct, and ability to use the system for screening, direct-to-stockpile only. Discover even more RAP benefits. Plus, this versatile plant may be used as a secondary unit for recycled concrete and aggregate by removing the diverter chutework to become two plants in one.

GNSS receiver designed for centimeter-level, real-time kinematic (RTK) accuracy for professionals engaged in a wide range of applications in the surveying, construction, engineering, forestry and mining industries. It joins a portfolio of fuller-featured high accuracy receivers, including the HiPer HR and VR.
TRANSTECH SYSTEMS
TransTech Systems Inc., Latham, New York, a provider of civil engineering solutions, announced the acquisition of Ames Engineering. “We are excited to welcome Ames Engineering to the TransTech family,” said David Apkarian, CEO of TransTech Systems, Inc. “This acquisition strengthens our
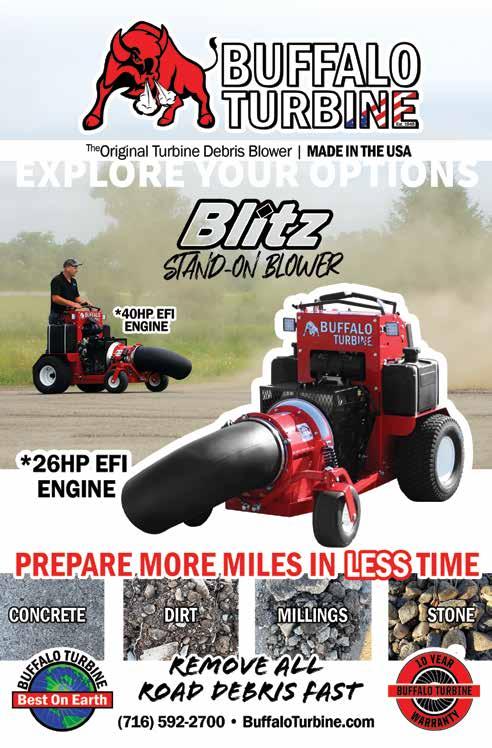
PRODUCT GALLERY
position as a leading provider of advanced technologies in civil engineering. By combining our expertise and resources, we will enhance our ability to meet the evolving needs of our customers and drive innovation in the industry.”
Ames Engineering has a long history of delivering high-quality testing equipment that ensures the integrity and safety of construction materials. Their products include high-speed inertial profilers, transverse imaging systems and laser texture scanners.
“Joining forces with TransTech Systems opens up new opportunities for us to expand our reach and deliver even greater value to our customers,” said John Maurer, founder of Ames Engineering. “Together, we will continue to push the boundaries of what’s possible in civil engineering, offering comprehensive solutions that empower our clients to achieve excellence in their projects.”
TransTech Systems Inc. and Ames Engineering will work closely to ensure a smooth transition for customers and partners. Existing customers can expect continued support and access to a broader range of products and services from this acquisition.
For more information, visit www. transtechsys.com.
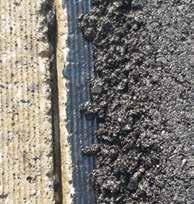
Correction: On page 20 of the May issue, the article, “NB West Wins with Smooth Asphalt Results, Again,” included an image with a caption that incorrectly stated the crew used J Band on the project. The team used the spray paver with Novabond. AsphaltPro regrets the error.
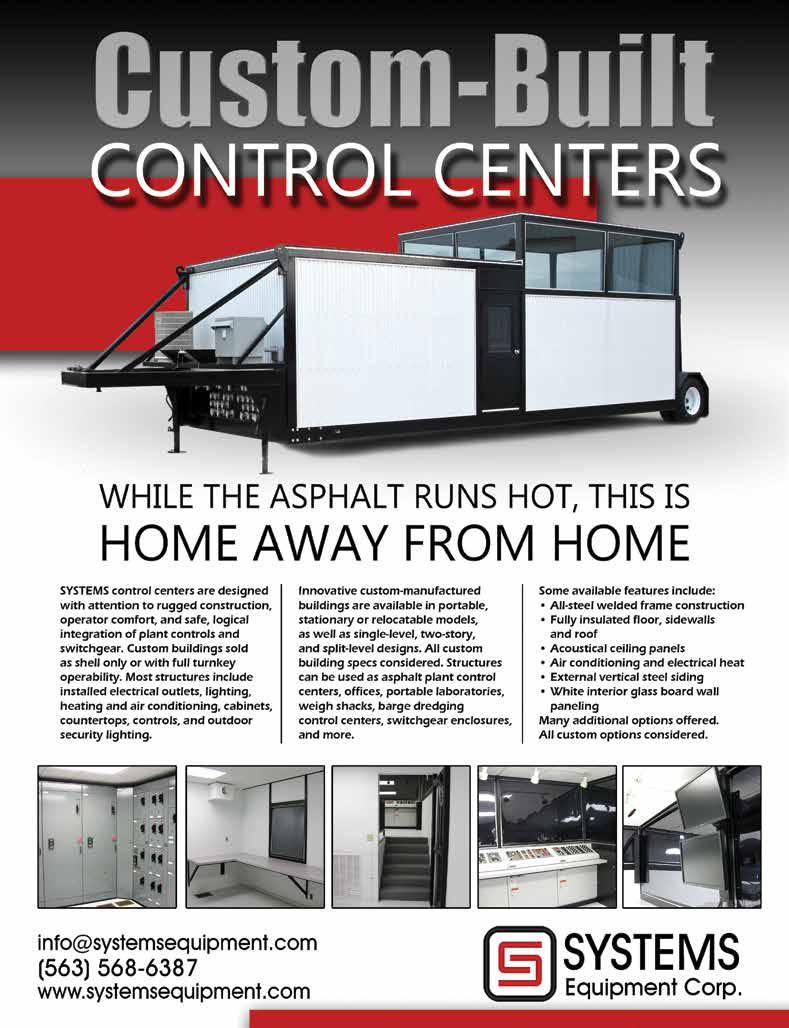



Visit our website at theasphaltpro.com for exclusive content, including videos demonstrating equipment or showcasing various projects and blog posts covering the latest industry news. theasphaltpro.com Join us on Facebook, Instagram, X and LinkedIn for daily tips to improve performance, asphalt industry history and trivia, construction humor, and news and happenings. facebook.com/AsphaltPro instagram.com/theasphaltpro @AsphaltPro linkedin.com/company/asphalt-pro-magazine Sign up for our weekly Toolbox Tip emails to inspire your daily toolbox talks. Toolbox Tips: bit.ly/toolbox-tips AsphaltPro magazine is the leading “how-to” magazine for asphalt producers, highway pavers and public works specifiers, but we’re more than just a magazine! Get your AsphaltPro fix between issues by connecting with us online.

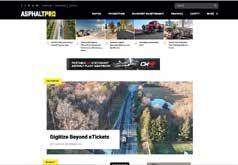
Terex Launches New Brand for Aggregate Businesses
FROM TEREX
Terex® is proud to announce the launch of MAGNA, a new brand to address the demands of large-scale operations in the quarrying, mining, construction and recycling industries.
Readers will recognize Terex has heretofore provided compact and mid-size crushing and screening equipment.
With decades of experience and a reputation for excellence across its Powerscreen, Finlay and EvoQuip brands, Terex has been at the forefront of providing innovative, high-quality equipment solutions, according to the manufacturer. Under the strapline ‘Made for More,’ MAGNA will build on this legacy, offering a new range of high-capacity machinery tailored to meet the needs of customers requiring larger output and volumes.
The launch of MAGNA supports the growth of Terex by expanding its offering with products that complement its existing portfolio. MAGNA will leverage the global presence of Terex that spans across all continents, providing solutions supported by a global network of skilled distributors.
Pat Brian, vice president of Terex Aggregates explained, “While we have a prominent position in the global market for compact and midsized materials processing equipment, MAGNA will position us to serve customers requiring higher output machines, via our renowned and extensive global distribution network. With an ambitious product roadmap and supported by Terex-wide engineering, manufacturing, marketing, parts and service capabilities, MAGNA will provide significant growth potential for Terex.”
Spearheading the launch of MAGNA is Neil McIlwaine, newly appointed business line director. Having previously worked for Finlay, McIlwaine completed several successful assignments in China and South Africa to establish and increase Finlay’s distribution footprint and continued growth strategy globally.
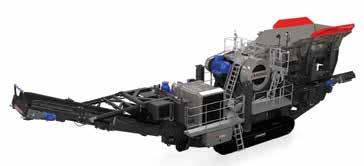
The MT130J features a Terex 51” by 39” single toggle jaw crusher. It’s one of many products in the MAGNA line, which includes crushing, screening, conveying and genset items.
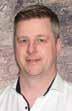
Neil McIlwaine brings 19 years’ experience in the global construction equipment industry with him to this role as business line director. Neil will be responsible for commercial, financial, sales, marketing and product development aspects of MAGNA, ensuring it achieves its growth and profitability targets.
“I am excited to leverage my experience to drive innovation, growth, and success for MAGNA,” McIlwaine said. “Large and robust crushing and screening equipment is essential for quarries and other operations that require high output and volumes. MAGNA truly is made for more; with equipment that is designed to have more power to handle more material throughput efficiently, ensuring more productivity and more cost-effectiveness for customers.”
For more information, visit www.terex.com/magna.
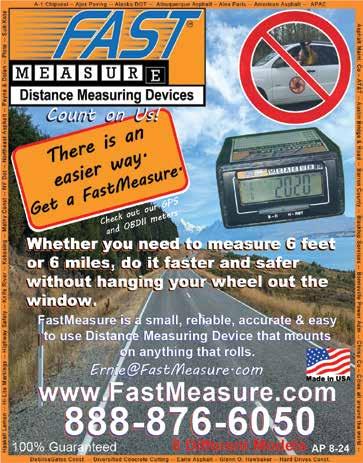
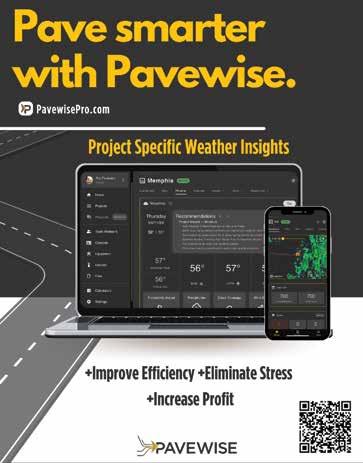
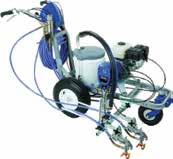
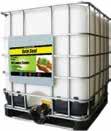
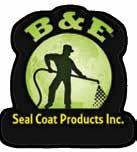
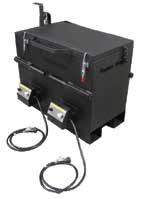


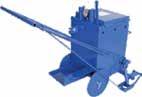
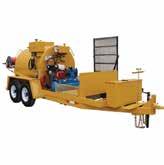

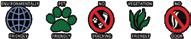

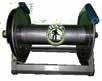



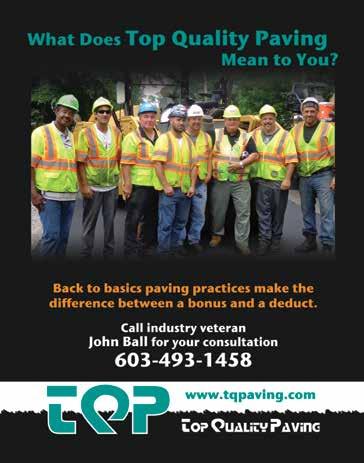
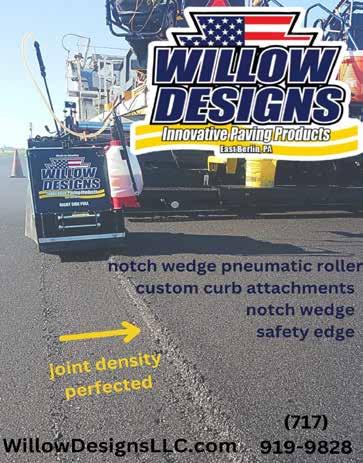
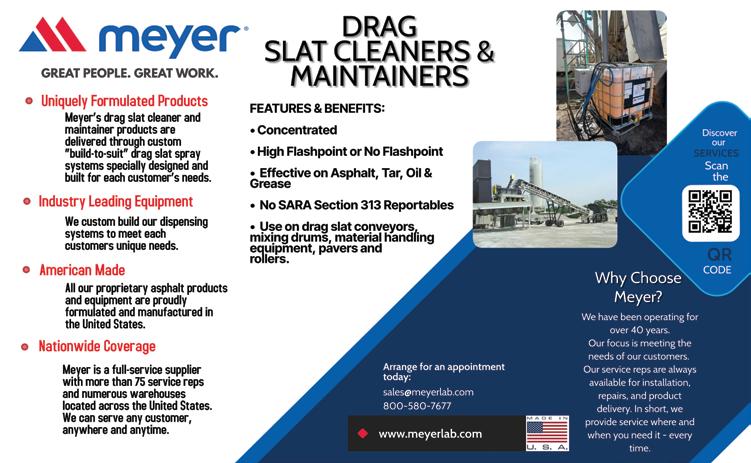


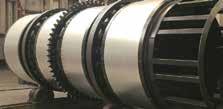



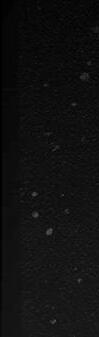

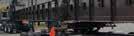


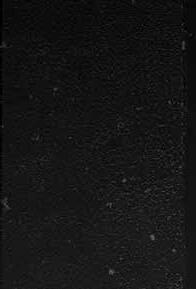


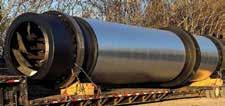
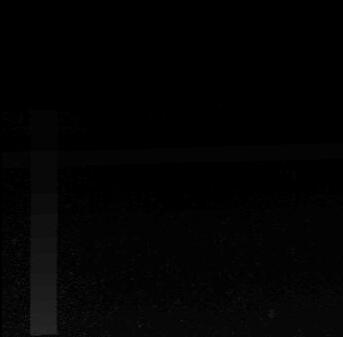
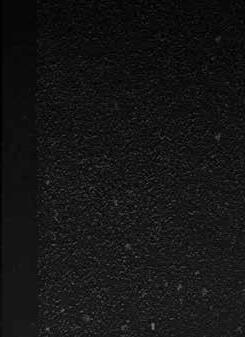
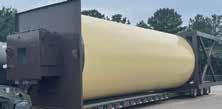
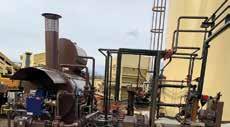

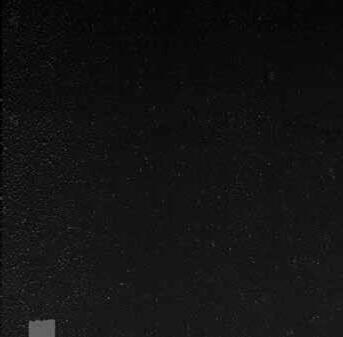
Iron Sheepdog Solves the Trucking Problem at the Start
BY SARAH REDOHL
In the 30 years Mike VanSickel has worked in civil construction, he was amazed by the evolution of trucking—or lack thereof. “It was paper tickets and invoicing when I started and when I left,” he said.
When VanSickel left his job as an executive in a large civil contracting company running 150 trucks a day between its asphalt plants and laydown crews, new solutions to the trucking problem were beginning to emerge. But, they were also beginning to create new problems.
To operate more efficiently, VanSickel’s employer knew they needed information from their brokers and owner-operators that they’d never be able to get without new technology. “We were signing these contracts with software providers promising to solve our trucking problems, but they weren’t focused on providing a solution for the broker and owner-operator network so there was no value to them,” he said. “Ultimately, we were adding overhead to our business to solve the problems of someone else’s business.”
VanSickel was determined to solve the trucking problem from the bottom up. “And the root of the problem isn’t that paving contractors want transparency and reliability from their trucking,” he said. “The problem is the adoption of technology by sub-haulers.” That’s why VanSickel created Iron Sheepdog.
BUILT FOR BROKERS
Iron Sheepdog is a trucking software built for brokers. “The brokers are our customers,” VanSickel said. “Their sub-haulers then use the platform, and the contractors are granted access to the data.”
Although each stakeholder benefits from the platform, the benefits begin with the brokers, like James Norris of Predestined Hauling LLC, Hampton, Virginia. Previously, the company ran its business “the old school way,” Norris said. “It was all paper tickets turned in to us by Saturday. My partner would sort the tickets on Sunday, and on Monday I would enter them into a spreadsheet and invoice.”
Norris knew he needed a better solution, but was hesitant to deploy Iron Sheepdog. He was nervous the platform would eventually try to cut out brokers like him. “It was hard to let [Iron Sheepdog] all the way into my multi-million dollar business,” he said. But, he’s glad he did. Not only did the platform eliminate his administrative burdens, but it also helped the business grow.
Since implementing Iron Sheepdog, Norris’s gross income has doubled while significantly reducing his overhead costs. The platform also enabled the company to expand operations across Virginia, North Carolina, South Carolina, Georgia, Florida, Tennessee and Maryland.
BUY-IN FROM DRIVERS
Although brokers are the first step in Iron Sheepdog’s solution to the trucking problem, the next step is getting drivers on board. “A lot of platforms sell to the contractor instead of the truck, but if the contractor can’t get the truck to sign on to the platform, the platform
means nothing,” Norris said. Now, the burden of getting the drivers to adopt the platform was on the broker.
“[Most drivers] have tried other platforms that require them to do all kinds of nonsense,” Norris said. “They were tired of change that only made their jobs harder. But, Iron Sheepdog is so easy to use that all my drivers were sold on it after one or two weeks. Now, they won’t run without it.”
Although ease of use is key, VanSickel also wanted drivers to have a reason to buy into the platform. “For truckers, Iron Sheepdog’s key benefit is that it gives them access to their money and control over the cash flow for the business they’re running,” VanSickel said. Haulers working through the app are able to accept jobs, check in and out of job sites, view their earnings and cash out from within the app.
Norris said the ability to get paid in as little as 24 hours was unheard of in trucking. “If a driver had a flat tire, they might not be able to run that truck for a week while they waited to get the money they were owed in order to fix that tire,” Norris said. “With the ability to pull their money in 24 hours, they can do what they need to do to keep their truck moving.”
BENEFITS TO CONTRACTORS
The contractors with whom Norris works have also benefited from Iron Sheepdog. “Coming up with the right amount of trucks for a job is one of the hardest things they have to do,” Norris said. “With Iron Sheepdog, they can see what they’re spending on trucking each day, so they know if they need to make any changes.”
This was a familiar problem for VanSickel. “Back when I was on the contractor side, I’d get mad at my haulers about cycle times when [delays] might have been because I didn’t order the right number of trucks,” he said. However, he didn’t have the data he needed to make a more informed trucking decision.
With Iron Sheepdog, the broker grants paving contractors or asphalt producers access to the platform at no cost to them. “They can see their digital tickets, view trucks in real time and perform load cycle analysis,” VanSickel said.
VanSickel said the first step for contractors interested in Iron Sheepdog is to ask their brokers if they currently use the platform.“The president of one of the largest paving contractors in the southeast recently called me up because they needed a new trucking solution,” he said. “He was surprised to learn two of our brokers already worked with him. All we had to do was have those brokers give him access to the data.”
This approach not only reduces costs to the contractor because they don’t have to implement a technology of their own or staff dispatch and ticketing employees, but it also means they don’t have to shut down operations to deploy new software of their own. Nor do they have to attempt to mandate the owner-operators and brokers they work with to implement new technology. “The sub-haulers have adopted it because the brokers adopted it,” VanSickel said. “If all your trucks run Iron Sheepdog, all the contractor has to do is ask their broker to set them up to see the data.”
Trimble Flashtracts Payments
Trimble Acquires Flashtract, Streamlines Payment and Compliance Workflows for Pavement Contractors
BY MEREDITH BAGNULO
In May 2024, Trimble acquired Flashtract, a company that delivers specialized technology to streamline the flow of payment and compliance information between construction general contractors and subcontractors.
This is good news for paving contractors that pay various subcontractors for services such as milling, striping, work zone safety management, etc. Current payment processes can be daunting and time consuming, from collecting payment applications through email, to tracking down lien waivers and replacing expired Certificates of Insurance (COIs).
Subcontractors can also benefit from a centralized, online portal that is designed to make uploading, updating and viewing documents easier and more accurate. Similarly, paving companies could benefit from these capabilities when they work in a subcontractor capacity, and the potential for faster payment is a strong advantage.
“Secure, reliable and fast electronic management of payments and lien waivers can be vital benefits to contractors, but many still manage these processes manually,” said Lawrence Smith, vice president of construction management solutions at Trimble.
Flashtract technology is used to manage payment applications, lien waivers and other compliance and billing documentation electronically, eliminating back-andforth communication and cumbersome document transfers. The technology, now called Trimble Pay, initially integrates with the capabilities of the Trimble Viewpoint® Vista™ ERP solution for construction.
With Trimble Pay, paving contractors can assign subcontracts to subsidiaries, self-performed groups, or separate divisions within their company so that billings are accurately submitted and flow seamlessly back into the contractor’s ERP system. This is designed to ensure each one is paid the correct amount along with all the external subcontractors being used on the job.
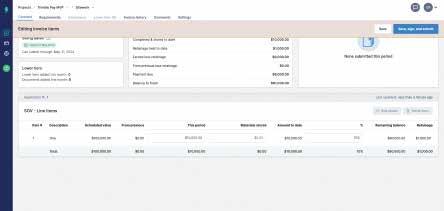

In this screenshot, we see an example of the invoice ready to be billed.
It also automatically tracks compliance information for first tier and lower-tier subcontractors. For example, instead of searching through binders or spreadsheets for COIs, Trimble Pay can send automated notifications to subcontractors upon insurance expiration, so they can be updated in a timelier manner.
“Adding the ability to manage these workflows with subs electronically through Trimble Pay helps contractors improve compliance and keep projects on schedule and budget by reducing the two to three days of man-
ual work per month by project managers or accountants,” Lawrence said.
Since its introduction in 2019, Flashtract has enabled contractors to minimize legal and financial risks while improving efficiency. Blair Chenault, co-founder and CEO of Flashtract, added, “Joining Trimble will allow our teams to advance these capabilities and help contractors make payments on time and keep management of financial and compliance documents from hampering project delivery.”
In this screenshot of the Trimble Pay software, one sees how the contractor is able to edit the information for a specific subcontractor. Images courtesy of Trimble
SHUTTLE BUGGY ® SB-3000
PAVING REVOLUTIONIZED
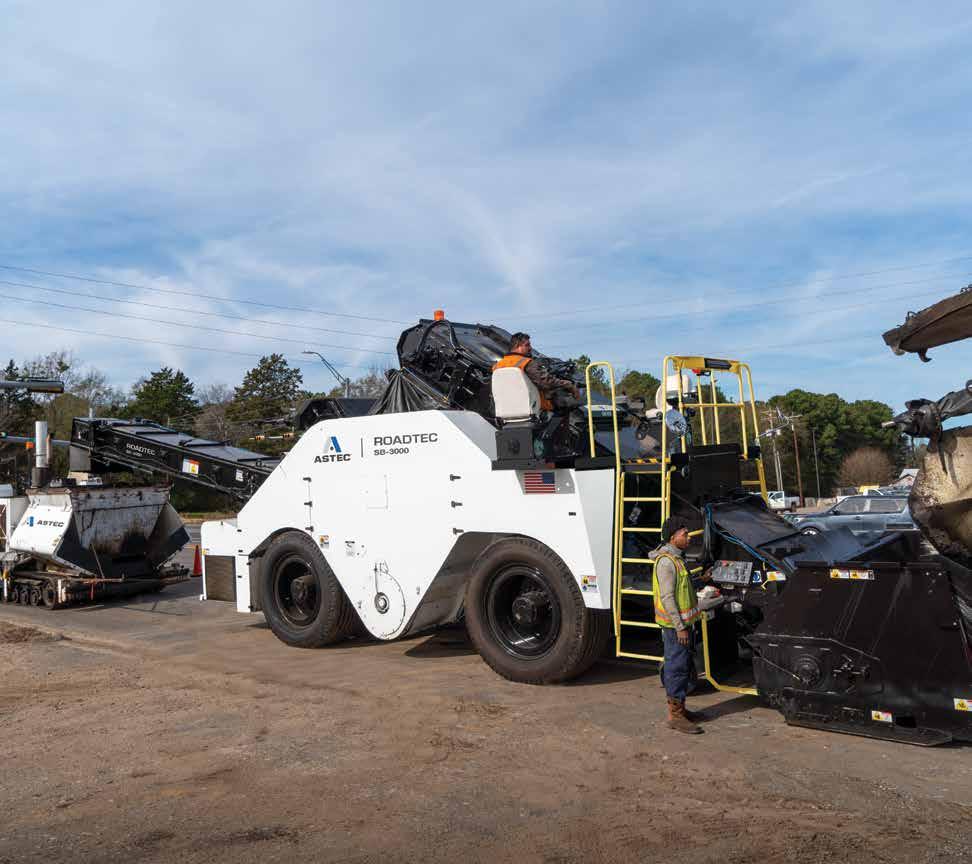
Roadtec Shuttle Buggy ® SB-3000
Astec revolutionized the paving industry with the introduction of the Shuttle Buggy, and now the SB-3000 sets a new standard in material transfer vehicles. Effortless maintenance, unmatched performance, and four steering modes for ultimate agility keep paving seamless. Experience groundbreaking innovation with the patented Ground Crew Control Station for the ultimate user experience and protection. The SB-3000 isn’t a machine, it’s a revolution in material transfer, built on Astec’s legacy of industry firsts.
BUILT TO CONNECT
