The Big Paving Issue
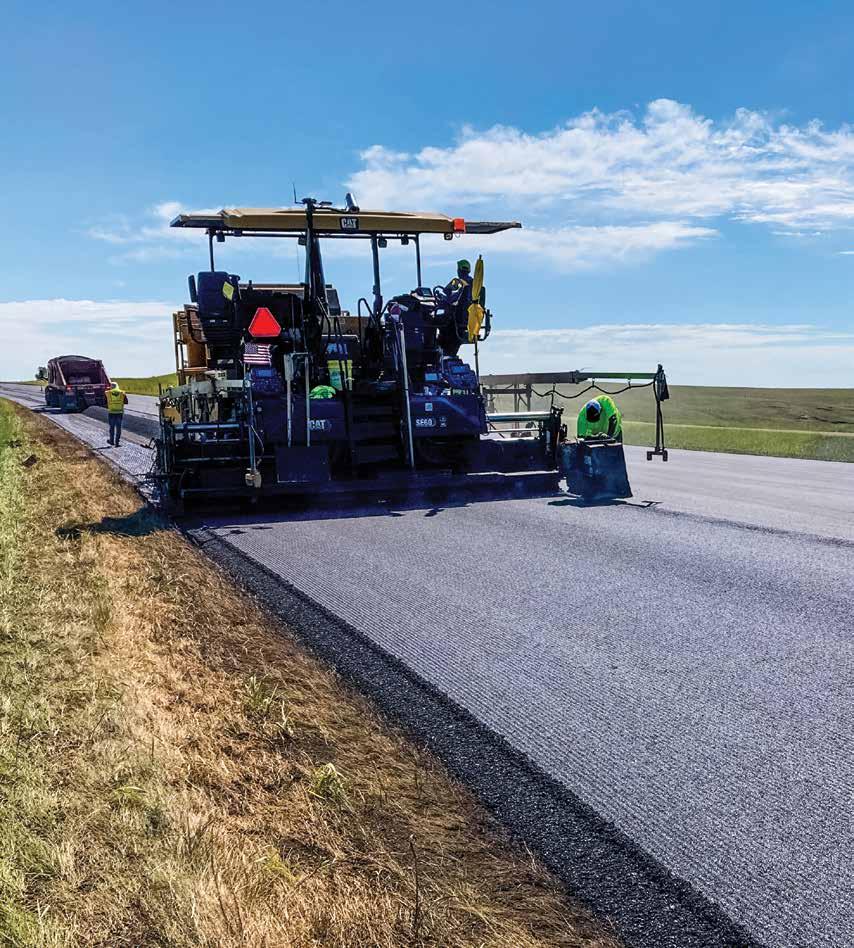
• How to load different truck body types at your plant
• How to perform an ultrathin bonded wear course
• How to move material safely over live traffic
• How to build a maintenance company
• How to pave on a sand subbase
• How to load different truck body types at your plant
• How to perform an ultrathin bonded wear course
• How to move material safely over live traffic
• How to build a maintenance company
• How to pave on a sand subbase
Astec paves the way for sustainable, innovative asphalt plants. The new IntelliPac Moisture System is a revolutionary solution that integrates seamlessly with Astec control systems. This provides unparalleled, real-time visibility into virgin aggregate moisture content. IntelliPac empowers operators to optimize mix design, minimize energy consumption, and reduce environmental impact. With Astec, you get superior asphalt production – better for the environment, better for your business.
CWMF has been a trusted company in the stationary and portable asphalt industry for decades.
As a full-service manufacturing company, we engineer all of our products to order, allowing us to serve as a full-service, end-to-end provider of asphalt plant solutions. We have the machinery and equipment you need, and a confident team working together to make this happen. Whether it’s cold feed bins, drums, silos, or the entire plant, we get the job done in-house, from start to finish. This provides an exceptional experience for our customers, and for the dedicated team standing behind their products. We work hard not only to retain our reputation but to stay current on the latest industry trends and technologies.
Contact us for a site evaluation, expansion project idea, new equipment upgrades, or to discuss your custom needs.
• Week 1: January 20 - 23
• Week 2: January 27 - 30
• Week 3: February 3 - 6
• Week 4: February 10 - 13
CLASS SIZE IS LIMITED !
To secure your seat, please register before December 15, 2024
Details can be found at www.gencor.com/training or call us at 407-290-6000 ext. 342.
Improving overall plant production and efficiency are all common concerns for plant owners and operators. Having a well-trained technical crew is vital to maintaining plant performance and efficiency.
Gencor and its training staff represent the biggest concentration of knowledge and expertise in all the sciences and technologies involved in the production of asphalt plants. Customers who attend these seminars benefit by having the support and focused attention of the best specialists in the asphalt industry.
Using Gencor’s state-of-the-art control simulators and actual equipment, our experts take you stepby-step through a comprehensive & intensive concentrated hands-on training program providing the latest techniques on optimizing production efficiency.
EDITOR’S LETTER
6 – I’m Thankful for Paving Restoration By
Sandy Lender
SAFETY SPOTLIGHT
8 – Safety Wins
J. J. Keller shares winners’ safety stories and metrics amid 22nd year of the SPOTY awards From AsphaltPro Staff
STREET SMARTS
10 – Best Paving Practices (When Conditions Aren’t the Best) Part 1: Customer Budgets & Expectations By
Bill Stanley
PROJECT MANAGEMENT
12 – Crossing the Finish on S.T. Wooten’s I-40 Overhaul in Raleigh By Matt Davis
PRODUCER PROFILE
18 – Bowes Buys Uptime, Security, Production By Sarah Redohl
WOMAN OF ASPHALT
24 – Meet a Woman of Asphalt: Pothole Heroes’ Rebecca Neidich By Beth Brody
PRODUCT GALLERY
50 – Get Clean Production Next Season From AsphaltPro Staff
58 – International Stability From AsphaltPro Staff
30 – Central Specialties Wins and Expands
Quality asphalt paving leads to additional opportunities for the general road contractor across North Dakota By Sandy Lender
36 – Ultrathin Bonded Wearing Courses, Explained By Sarah Redohl
42 – Expand Into Production Loadout Tips By John Ball 46 – Maximizing Off-Highway Haul Truck Productivity By AsphaltPro Staff
IRI of 25 on I-94 and took home an award from the DOT for it. See related story on page 30. Photo courtesy of
As this issue was preparing for production, Hurricane Helene was ravaging its way up the Southeast section of the United States. After the storm lost its hurricane status, high winds and torrential rains turned areas of Georgia, Tennessee and the Carolinas into flood zones reminiscent of the Midwest in 1993. Creeks and rivers broke through dams to disastrous effect and as I type this, the horrifying news of a rising death toll breaks our hearts in this nation.
By the time this issue reaches readers’ mailboxes, search and rescue efforts will have revealed final numbers of lives lost. Dollar figures will be assigned to the natural disaster and contractors will be working to restore roadways, bridges, interstates, water systems and other infrastructure.
You might be wondering what that has to do with the November “Big Paving Issue” of the magazine. First, we have an article (on page 12) detailing the completion of the I-40 widening near Raleigh, North Carolina, which can now facilitate movement of emergency needs to the western part of the state. We also have positivity to be thankful for amid the tragedy.
Here in the state of Florida, while certainly not unaffected by the storm, we had enough warning to prepare facilities to come back online quickly while distributing aid with Operation Blue Ridge. The Florida Department of Transportation (FDOT) provided 7,500 feet of temporary bridges and a convoy of staff and equipment, and the Florida National Guard was deployed to help the North Carolina National Guard with search and rescue, along with many other resources, detailed in this article: https://www.fox35orlando. com/news/multiple-florida-agencies-providing-hurricane-helene-recovery-assistance-impacted-northern-states
We are fortunate to have one another in times such as these.
Also, by the time this issue reaches readers’ mailboxes, we’ll be well into autumn and preparing for a tumultuous election cycle’s result. This November, when we typically ask one another what we’re thankful for, you might be feeling overwhelmed by current events.
As cliché as this sounds, I invite you to count this industry of resilient and caring workers among your blessings. More than emergency workers appeared when Americans needed rescue from roofs while flood waters from a failed dam rushed by. Neighbors and private pilots manned their fishing boats, private helicopters and drones to assist. And transportation officials alongside contractors arrived with equipment to clear roadways for responders to access dangerous areas.
The task of rebuilding will now fall to the contractors who helped build this nation in the first place. We are fortunate to have resilient and competent contractors around us in times such as these. And that’s something I’m thankful for.
My prayers are focused on the recovery and safety of everyone affected by the recent storm and my gratitude is extended to all the individuals who have boots on the ground—and in the air—to assist. I’m thankful for the asphalt industry and its members who build and maintain the services we use daily. And I’m thankful for the agencies and engineers who design the structures that will, one of these days, restore some semblance of normalcy for the souls impacted that deadly weekend in September.
602 W. Morrison, Box 6a Fayette, MO 65248 (573) 823-6297 • www.theasphaltpro.com
GROUP PUBLISHER
Chris Harrison chris@ theasphaltpro.com
PUBLISHER
Sally Shoemaker sally@theasphaltpro.com (573) 823-6297
EDITOR
Sandy Lender sandy@theasphaltpro.com (239) 272-8613
DIGITAL EDITOR
Sarah Redohl sarah@theasphaltpro.com (573) 355-9775
MEDIA SALES
Cara Owings cara@theasphaltpro.com (660) 537-0778
ART DIRECTOR Kristin Branscom
BUSINESS MANAGER
Susan Campbell (660) 728-5007
AsphaltPro is published 11 times per year. Writers expressing views in AsphaltPro Magazine or on the AsphaltPro website are professionals with sound, professional advice. Views expressed herein are not necessarily the same as the views of AsphaltPro, thus producers/contractors are still encouraged to use best practices when implementing new advice.
Stay Safe, Sandy Lender
SUBSCRIPTION POLICY: Individual subscriptions are available without charge in the United Sates, Canada and Mexico to qualified individuals.
One year subscription to non-qualifying Individuals: United States $90, Canada and Mexico $125.00. For the international digital edition, visit theasphaltpro.com/subscribe/
The future is connected. That’s why we’ve designed the ALmix Insignia Control System (ICS) around the power of high-speed Ethernet communication. An ethernetconnected facility means our team of programmers have complete visibility into your plant equipment and motor control center for diagnostics and remote troubleshooting. View and control data from your asphalt plants like never before. The Insignia Cloud Platform provides access while you are at the plant, in the office, or on the go. Critical, real-time, plant information is at your fingertips when you need it.
DON’T LET YOUR EXISTING ASPHALT PLANT CONTROLS KEEP YOU GUESSING:
The Insignia Control System is available on all new ALmix Asphalt Plants and is also available for existing plant control upgrades.
SCAN HERE TO LEARN MORE OR TO SCHEDULE A DEMO
The team at J. J. Keller & Associates Inc., Neenah, Wisconsin, announced in September the recipients of the top three 2024 Safety Professional of the Year (SPOTY) award. The SPOTY Awards, now in their 22nd year, highlight individuals who achieve excellence by building a culture and vision for safety and ensuring employees return home each day to their families. The winning safety professionals were selected by a panel from J. J. Keller’s staff of 70+ safety consultants and editors.
First Place: Matthew Rehlander
National OnDemand, Inc., provides fiber construction and last mile services for the fiber, wireless, energy and technology sectors in the United States. The company has more than 1,600 employees. Rehlander leads a team of eight in EHS, fleet and risk management today. When he began with the company about in early 2023, he immediately began to build out the department and formalize EHS and risk management functions while instilling a safety culture that teaches people to be their own safety professional in keeping themselves and others safe.
“For the safety profession, it needs to be about meeting the workforce where they are,” Rehlander said. “Participate with them as the expert in solving their safety and risk con-
cerns. Take their ideas and suggestions and formulate the resources to make those real. Change the culture from ‘I have to do safety’ to ‘I want to do safety.’”
“We are incredibly proud of Matthew Rehlander and the profound impact he has had on our organization in such a short time,” said Douglas Boteler, National OnDemand CEO. “His dedication to building a robust safety culture from the ground up, combined with his forward-thinking approach to risk management, has been transformative for National OnDemand. Matthew’s leadership ensures that our employees not only feel safe but are empowered to take ownership of safety in their daily work. His recognition as J. J. Keller’s Safety Professional of the Year is a testament to his commitment to excellence, and we are thrilled to see him honored with this prestigious award.”
Paladin Capital Inc. provides dedicated truckload direct store delivery of groceries and dry goods in the Eastern United States, with 1,000 shareholders. Crabtree has been with Paladin for 17 years and has a total of 45 years in the transportation industry. Today he leads nine full-time shareholders in risk management roles. Most recently, he has led the company in deploying event recorders, or dash cams, on all tractors within all eight department of transportation operating affiliates and in deploying a progressive disciplinary process around hand-held mobile devices. He has initiated
many risk management best practices over the years, which are used in the industry today.
“Our organization is extremely pleased to see the many years that Harry has built a world-class safety culture around all the affiliate companies of Paladin Capital,” said Brian Hall, Paladin Capital CEO. “We live and breathe safety every day, and for him to be recognized by outside affiliates is very rewarding.”
Mt. Diablo Resource Recovery serves over 250,000 residents and thousands of businesses throughout Contra Costa, Napa and Solano counties in California. Mt. Diablo Resource Recovery combines excellence in safety and customer service with competitive rates, operating recycling and recovery programs designed to increase sustainability and reduce greenhouse gas emissions. Miller and his team have excelled in analyzing the risks associated with complex employee-machine interfaces and developing protections against those risks, and reinforcing defensive driving skills for the company’s drivers, who are always working amid the motoring public.
“We are currently coaching to driver behaviors and workspace ergonomics for multiple job tasks using video technology,” Miller said. When asked what his next focus in safety will be, he answered that it “will be working toward a robust, leading metrics-driven supervisor-employee connection program.”
For more information, visit www.jjkeller.com.
2025 DATES
• January 20 - January 23
• January 27 - January 30
• February 3 - February 6
• February 10 - February 13
REGISTRATION
CLASS SIZE IS LIMITED, register today!
All details can be found at www.blawknox. com/training or contact at (407) 290-6000 ext. 342 or training@blawknox.com
The Blaw-Knox University, is dedicated to training paver operators ad foreman on proper Paver Operation and Maintenance and applied Best Paving Practices through classroom-style and hands-on application courses.
For over a half a decade Blaw-Knox has earned its reputation as the go to source of training and instruction on hot mix paving.
Blaw-Knox provides improved technical and problem-solving skills on a variety of paver operations and maintenance topics. Course instructors share decades of field and teaching experience with attendees, including training on the latest DOT requirements.
BY BILL STANLEY
Picture this: You’re paving the entrance to a large condominium complex. Everything is going smoothly until 3:30 p.m. hits and 30 cars swarm your job site as parents living in the condominium complex wait to pick up their children from the school bus. Your job site comes to a complete stop at the worst possible location. The area is so clogged with cars and the crew that traffic on the road is backed up. A state trooper pulls up and starts yelling at you about the traffic. Then, the asphalt plant calls and says they’re closing early for the weekend and they need you to come get whatever mix you need to finish the job. You can’t shut down for the day because the customer needs this job done by 4:15 p.m. today. You can’t come back Monday because you’ve got another job that can’t be rescheduled. What would you do?
This is exactly what happened on a job the American Pavement Specialists crew was on this spring. Our only option was to stop the job to wait for the kids to get off the school bus and the cars to clear, send all the trucks back to the plant for the last load of mix, and hustle to finish the job by the end of the day.
When it comes to best paving practices, there are tons of resources available. Those may be applicable on the jobs you’re on Monday through Thursday, but what about Friday when you’re on a job like the one described above? Or the following week, when the plant breaks down and it’s 60 degrees Fahrenheit and windy as hell?
Believe me, I wish it were possible to train my crew on a set of best practices and be done with it. But in our industry, every day is different. We’re using a different material in a different area under different weather conditions. To be an asphalt pro, you have to be ready to switch up your best practices to meet the conditions of that particular job site. The training never really stops.
That’s why over my next few articles, I’m going to talk about best paving practices for when conditions aren’t the best. In part one, we’ll cover customer expectations and
In Part One of Stanley’s series about paving in adverse conditions, we look at customer expectations and budgets. “One thing that drives me crazy is when folks who aren’t in our industry tell me, ‘Did you see the job X contractor did on Y road? Terrible!’” Stanley writes. “Maybe they did a terrible job. Or maybe they were forced to pave under adverse conditions. You and I have no idea what the customer asked them for, what the customer’s budget was, or all the contractors’ recommendations the customer might have rejected.”
budgets. In part two (December 2024), we’ll cover weather conditions. In part three (January 2025), we’ll cover issues at the asphalt plant, and in part four (February 2025), we’ll cover equipment issues.
Let’s start at the beginning, with your customers.
One thing that drives me crazy is when folks who aren’t in our industry tell me, “Did you see the job X contractor did on Y road? Terrible!” Maybe they did a terrible job. Or maybe they were forced to pave under adverse conditions. You and I have no idea what the customer asked them for, what the customer’s budget was, or all the contractors’ recommendations the customer might have rejected.
Let’s face it, some customers want their product to be perfect and are willing to pay
for it. Other customers might just want the parking lot to look black. Asphalt pavement is basically one big math problem. The customer could spend $1 million, or $500,000, or even $100,000, and you can’t expect the contractor to give a $1 million result for $100,000. If the capital’s not there, it doesn’t mean we can’t make the pavement better than it was within the customer’s budget. But, to assume the results of the project are the contractor’s fault is unfair unless you know the customer’s demands.
If a customer comes to you with a budget smaller than what their pavement actually needs, you can either turn down the project or deliver the best you can for that amount of money. If you take on the project, be sure to manage their expectations for their pavement now and in the future.
On a job with a tight profit margin, choosing which crew members to send may be counterintuitive. It may be the case that I send my best guys when you might think I’d send my second stringers. This is because if the profit margin is so thin, I cannot afford mistakes like putting 2 ¼ inches of asphalt on there instead of the 2 inches they’re paying me for.
This is true for their budget, but also for adverse project conditions. Imagine the weather turns bad, but the customer still needs their lot done. Imagine the plant breaks down in the middle of their project. It’s not your fault, it’s not the customer’s fault. No customer wants their lot to suffer for that. Somebody has to answer for that and it’s probably going to be you. Manage expectations from the get-go.
If I can’t deliver quality results on a project, I typically won’t accept the job. We can only do so many projects per season, and I’d like to fill that book of work with customers who are interested in quality, customers who are reasonable, customers who are appreciative.
This fall, a new customer called me needing to pave a 3-acre parking lot and said he had $20 million on the line. Knowing what it could cost him if the project didn’t get done, I moved heaven and earth to finish a five-day job in three days. When we wrapped up at 6 p.m. on Friday, he stopped by and demanded—not asked—that we repair a couple of catch basins. If he’d been appreciative, we probably would have done the work for him. Now, I know not to work with him in the future.
Also this paving season, I was called to give an estimate for a driveway project in Long Island Sound for a mansion on 20 acres with ocean on three sides and a 50-car garage beneath the house. I knew from the project timeline that we probably wouldn’t be called to pave until after Thanksgiving. Even though we would have protected ourselves by having that customer sign off on work so late in the season if we’d estimated the project, we didn’t want to risk it. Let’s face it, even with the customer signing off on that late season work, they have more money than we do so they’d likely win in court. Even if we won, we’d have a black eye from it. We’ve been in business 32 years, and
I’ve never stepped foot in a courtroom, and I’d like to keep it that way.
I’m not afraid to turn down a job that isn’t right for us. I’m not afraid to pass on a project where I know I can’t deliver the type of quality I want my company to be associated with. I’m not afraid to say no to a customer that doesn’t seem like a good fit when I could have filled that time doing something else.
Those are my own best practices for choosing my customers and my projects, but like anything else on the paving train, this may be subject to the specific conditions your company faces. It’s a math problem every contractor’s going to have to solve for themselves.
BY MATT DAVIS
While S.T. Wooten crews knew the I-40 road widening project was going to be expansive, nobody could have guessed just how far it would take them. The project already marked a milestone as the biggest in company history when construction kicked off in 2018, but new initiatives combined with Raleigh’s fast growth brought adjustments that added extra years of work to the scope.
S.T. Wooten’s I-40 project was initially scoped as a four-year, $360 million job, but expansions added an extra $60 million to the budget along with two additional years of construction. The project will be reaching completion this fall as crews put the finishing touches on years of hard work and dedication.
The purpose of the I-40 project was to improve traffic conditions through a busy 13-mile stretch—extending from the I-440 divide in Raleigh to 2 miles east of the N.C. 42 interchange in Johnston County—with two new lanes added in each direction. Construction also involved a total of 15 bridges being built or revamped, along with the installation of two diverging diamond interchanges (DDIs).
After the project was underway, the North Carolina Department of Transportation (NCDOT) was challenged to address additional traffic concerns along Jones Sausage Road from a new Amazon distribution center, which S.T. Wooten also worked on. The NCDOT took swift action and with recommendations from their engineers, decided to retrofit a DDI across the existing bridge that crosses I-40 to help with congestion. That’s just one example of how the NCDOT was flexible in making accommodations for the developing area to better help the traveling public.
The first DDI crews tackled for the I-40 project was positioned at the 40/42 area, which is where Highway 42 crosses over I-40. To accommodate the DDI, two new bridges were constructed with the roads widened on either side of the bridge. The new pattern was put in place during the spring of 2024.
For construction on the DDI at Jones Sausage Road, the process was unique since it was built utilizing the existing bridge. Work included:
• Tearing down existing barrier rail and adding sidewalk and 3-bar metal rail
• Installing new latex deck overlay
• Installing a median barrier to separate traffic
In the fall of 2023, the intersection was put into a temporary single-lane DDI pattern. Crews had to pave the first lift of surface then adjust and activate new signals for the pattern over a single weekend. Once in this pattern, there was a 28-day timeline to complete the median barrier and islands before opening to a full pattern. Crews successfully opened into the full pattern on the weekend before Thanksgiving in 2023.
There’s a great deal of wisdom in enclosing the conveyor that carried HMA over the highway, including protecting the temperature of the mix. Safety is the most obvious reason for the conveyor being enclosed. The team was conveying hot asphalt across live interstate traffic. Being enclosed took away the risk of any material getting into traffic. All photos courtesy of S.T. Wooten
Faced with constant traffic surrounding the I-40 work zone near Clayton, S.T. Wooten engineered a unique asphalt conveyor to help streamline hauling processes for crews. The solution helped move asphalt safely from the Astec double barrel plant, over the highway, and into an 85-ton Gencor silo in the median-area work zone. From there, dump trucks were able to transport the asphalt to onsite paving equipment without having to haul through traffic and impact the traveling public.
The plant had two 300-ton silos and was rated for 350 tons per hour. The team produced multiple mixes for the project—the average load out temperature was 300 degrees for standard B and C mixes utilizing 64-22, and 325 degrees for the D mixes utilizing 76-22 asphalt cement.
We used Astec’s Weighmate system for controls and ticketing; communication among our team members was excellent. Between the plant control house, median control house, as well as the person controlling the trucks dumping for transfer across the conveyor, we used handheld radios. We also used red and green lights operated by the median control house to make sure the hopper and belt weren’t overloaded when the trucks were dumping.
The approximately 280-foot-long conveyer offered benefits to both crews and drivers. The system:
• Handled about 169,000 tons of asphalt, transporting it through an enclosed conveyor belt over the highway.
• Prevented dump trucks from needing to merge in and out of traffic while working. This ended up saving crews about 8,500 truckloads entering and exiting traffic.
• Reduced the total number of trucks and fuel needed to run the project. A single truck only has to drive around 100 yards to move the asphalt from the plant to the conveyer. Compare this to a 20-mile round trip that might be required without the conveyer.
While it was a unique structure, S.T. Wooten has used the asphalt conveyor approach before—about a dozen years ago on a separate stretch of I-40.
Like most large highways, I-40 has a split between the eastbound and westbound lanes. To accommodate construction, a tall barrier wall was installed the full length of the median and in some areas with the roadway positioned at different elevations. This was done to ensure crews could adjust the profile of the roadway to accommodate the additional lanes.
That difference in elevation, also called a “bifurcated” slope, was successful in allowing each direction of I-40 to have necessary variation and reduce the amount of cut or fill dirt needed. Using this bifurcated setup also made it easier to split off the ‘collector’ and ‘distributor’ lanes that people use for entering and exiting the highway, which was important in helping ease the flow of traffic in the NC-42 and newly added Cleveland Rd. interchange.
With the additions considered, the number of lanes throughout the length of the entire project varies from 12 lanes (six in each direction)
After the project was underway, the North Carolina Department of Transportation (NCDOT) was challenged to address additional traffic concerns along Jones Sausage Road from a new Amazon distribution center, which S.T. Wooten also worked on.
to six lanes (three in each direction) and due to the very wide pavement section and the curvature of the road the bifurcation was required.
While traffic was the most consistent challenge for crews on I-40, other obstacles came up as they do with any project. The pandemic, employee turnover and bad weather all threw a wrench into plans at times. Traffic shifts were also a unique element to manage and execute – since crews were on a tight turnaround to complete the paving and grading before traffic had to be re-opened with each transition.
Strategic planning and close communication between crews and subcontractors was instrumental in staying on schedule with so many moving parts across the I-40 job. Experience was also an asset for the team, as S.T. Wooten has now worked with the NCDOT on numerous large road construction projects – including a similarly expansive overhaul taking shape on I-95 near Fayetteville.
The I-40 project wouldn’t be reaching its completion date without the significant progress made by crews this past year. Crews have been working diligently to finish the surface and complete the punch list
for the final stretch running from 70 bypass to Cornwallis Road. Extending 4 miles, that covers roughly a third of the total project. Final touches will also include wrapping up construction at NC42, Cleveland Road and Rocky Quarry Road.
While the team is excited to finally cross the finish line, lessons learned from the project will be invaluable for future jobs. One such thing is the ability to adapt to changing conditions and situations. We go into these projects with a very detailed plan and schedule, but being flexible to make adjustments as you move forward—even if it’s not what you initially had in mind—is key to success.
Hundreds of crew members had a hand in construction on the I-40 project over the past six years. They should be proud of their work and a successful product that commuters will be grateful for in Wake and Johnston County’s growing communities.
Matt Davis is a division manager for S.T. Wooten Corporation. He shared, “Our hearts are with all the individuals and communities affected by Hurricane Helene, which unfolded as this article was going to press. We stand in solidarity with everyone impacted, and we are committed to supporting recovery efforts during this challenging time.”
Bowes Construction’s first season with its new asphalt plant, 2023, was the company’s second highest production year on record, producing 145,000 tons.
BY SARAH REDOHL
Over the years, Bowes Construction, Brookings, South Dakota, made significant updates to the stationary 250-TPH Barber Green plant it purchased in 1991. They replaced the wet dust collector with a baghouse for improved air quality, purchased a new control house, and modified and replaced their drum several times to increase production.
“It got to the point where the drum had been modified so much that we felt we needed to do a full upgrade to increase our daily and hourly production,” said Joe Mendel, asphalt production manager for Bowes. Although they enjoyed their Digi control system, it became increasingly more difficult to find parts. “Our big fear was at some point, something would happen, and we wouldn’t be able to source parts for the control system and we’d be shut down for two, three, four weeks.”
Simultaneously, local market conditions indicated it was time to increase production. “We’ve seen people flocking to South Dakota, I think as a result of our lower cost of living, increased safety, and lack of an income tax,” Mendel said. According to the U.S. Census Bureau, South Dakota is the 10th fastest growing state in the country, with a population change of 3.7% from 2020 to 2023. “With that growth, we’re seeing a need for new housing development and infrastructure.”
Bowes Construction’s asphalt plant is located in the state’s fourth most populous city (Brookings, population 24,000), which is halfway between the state’s most populous city (Sioux Falls, population 206,000) and its fifth most populous city (Watertown, population 23,000). It was in a prime location for growth.
“Sioux Falls has three asphalt plants and Watertown has one, but being 50 miles from both cities puts us in a great niche to serve our area while remaining competitive for projects both to the north and south,” Mendel said. “We’ve seen a lot of growth [in the state] for the past five or so years, and there’s definitely been a lot more infrastructure work going on in the past three years—including in smaller municipalities where we don’t typically see much work—and we don’t think that’s likely to stop.”
Given the state of the plant, the controls, and the market conditions, it was an ideal time to invest in a new asphalt plant.
The general population growth in South Dakota has also helped Bowes in terms of attracting talent.
“We’ve brought staff in from Florida, Indiana, Canada,” Mendel said.
Once the company decided to invest in a new plant, the real work began. “We needed to identify the type of plant we were looking for, the manufacturer we wanted to purchase it from, and how we were going to make the transition without losing any production time,” Mendel said.
Ultimately, Bowes chose to invest in a stationary 400 TPH plant with a parallel flow drum from CWMF, Waite Park, Minnesota. “They’re only three hours away from us, so we consider CWMF local,” Mendel said. Furthermore, Travis Mick at CWMF had been helping Bowes with issues arising at its existing plant over the years. “He’d been giving us a lot of attention, so of course CWMF was top of mind when we started looking at new plants.”
Given the company’s customer service and that the price was right for Bowes, it turned out to be a perfect match. “From the moment we chose CWMF, we felt very comfortable about everything,” Mendel said.
They chose a Hauck MegaStar burner, running on natural gas “because it’s readily available, cheaper, and we feel it runs better,” Mendel said. Bowes’ existing plant used a Hauck JetStar burner, which gave them confidence to stick with Hauck for the new burner. “We had good luck with our JetStar, so we wanted to stick with a Hauck burner while upgrading to more of a Cadillac burner model.”
Bowes also chose to invest in CWMF’s 80,000 cubic foot DustEater baghouse. “We only needed 70,000 cubic feet of space, but by stepping up the size a bit we know our production will never be limited by the size of our baghouse,” Mendel said.
According to Mick, vice president of CWMF, the company’s equipment production rates are based on composite moisture of 5%. “A general rule of thumb is that you need 200 cubic feet per minute (CFM) per ton of produced material at 5% composite moisture,” he said. In Bowes’ climate/conditions, Mick said their moisture levels are unlikely to reach 5%. However, he added, the baghouse size is good insurance. “Extra air can make up for nuisance leaks that may not yet be corrected. It also allows you to still get your desired production levels when moisture levels spike due to rain, given that a 1% increase or decrease in composite moisture will have an impact on production by about 13%.”
Mick cautioned against oversizing too much, though. “Oversizing a baghouse will make it difficult to reach appropriate temperatures at the stack, as it may be too large of a space to heat with the given BTU from the burner on the drum,” he said, “and temperatures below 212 degrees Fahrenheit can start to result in moisture
Bowes also opted for an 86-foot drag slat conveyor, the first drag slat system for the company. “Our old plant had a vertical bucket elevator,” Mendel said. Bowes also replaced the two 100-ton silos at its existing plant with one 200-ton CWMF silo.
“At the old plant, we almost never used our second silo because the plant could only produce 250 tons per hour,” Mendel said. “Once we loaded our first round of trucks, our plant couldn’t keep up with our production in the field.”
Although outside sales only comprise 10 to 15% of Bowes’ asphalt production, if they received an order of even a few hundred tons on a day where their own crews were busy, the plant would struggle. “Under perfect conditions, our old plant could only push out 2,500 tons per day, which limited our production in the field while facilitating outside sales,” Mendel said. “Upgrading to a bigger plant eliminated that issue.”
Given the role plant controls played in Bowes’ decision to invest in a new plant, investing in the right controls for their new plant was very important. After much research and discussion, Bowes chose Minds for its plant controls. “Minds controls allowed us to have a more programmable and updatable control system as the plant grew,” Mendel said.
“We actually installed them at the old plant a year prior to the installation of the new plant to protect against our old controls going down again,” Mendel said, “and so we could get familiar with them before the new plant came to avoid having to learn everything at once.” This approach enabled them to be 100% focused on each new component during the installation process.
Bowes shut down its old plant for the last time on Nov. 10, 2022. By Nov. 15, they began tearing it down—a process they would complete before Christmas so they could start the install in January 2023.
“We started with a clean slate, except for our control shack,” Mendel said. They installed the platform scale, silo footings, drum platforms, concrete platform, etc. in January, working through the cold, snow and wind to stay on schedule. “Thank God for Carhartt gear!”
Throughout the spring, Bowes organized the transport of each new piece of equipment. The two cranes from Northwest Construction, Sioux Falls, that had been on site for the teardown of the old plant were mobilized to set up the new equipment as each piece arrived. “By April 29, we were commissioning the new plant, integrating the Minds controls, performing our calibrations, and finalizing our setup for production,” Mendel said. “Our normal startup date is the last week of April, so we were right on target for the tear down and install.”
Ultimately, other than challenges with weather, the entire process went smoothly, “better than anyone had even hoped for,” Mendel said, attributing the success of the transition to the planning that went into every step of the process.
“We looked very hard at what we wanted, how we would implement it, the location, etc.,” he said. At one point in the process, Mendel said they considered moving the plant to another location, but decided against it due to infrastructure challenges. “If we had relocated the plant, we wouldn’t have been under such a tight schedule.” Keeping the plant in the current location also simplified the permitting process.
• ASPHALT MANAGER 2 cuts down on passes and avoids over compaction.
• Delivers professional level compaction results even when a novice is operating the roller.
• No manual drum adjustments required.
TanGO Takes the Risk out of Compacting near
• Tangential Oscillation (TanGO) is simple to operate and safe to run on bridges and near buildings.
• The TanGO technology creates a smooth mat finish even at higher working speeds.
Reduce Passes by up to 40% without losing
• Pair BOMAG BOMAP technology with ASPHALT MANAGER 2 and reduce your number of passes by up to 40% without compromising mat quality.
• Track and document compaction results in real time with the BOMAP App.
For Truly Intelligent Compaction look to BOMAG Heavy Tandem Rollers and BOMAG advanced compaction technologies like ASPHALT MANAGER 2, TanGO and BOMAP. BOMAG technologies not only improve finish quality but also reduce the number of passes needed and increase your compaction efficiency across the board. Even a novice operator can get professional level results with BOMAG! Contact your local BOMAG Dealer today to learn more. www.bomag.com
“We crossed our fingers, kept the plant where it was, and thankfully everything went right,” Mendel said. “But it only went right because we had our i’s dotted and our t’s crossed. The planning was a big part of the success of the transition, paired with a little good luck.”
Mick seconded the importance of planning. “Without planning, success is just good fortune,” he said. At CWMF, he added, planning is a team effort. This starts with highly detailed layout drawings in 2D and 3D to ensure everyone is on the same page. “Taking it a step further, before projects are released from engineering, we have a meeting with our clients to give them a 3D virtual tour of their equipment. This helps to ensure that we address any issues or concerns right then and there versus in the field, where delays can be detrimental to the outcome.”
This meant everyone was on the same page by the time the equipment arrived at Bowes’ plant site. “Bowes supplied a great team to install the equipment and CWMF was onsite to assist as needed,” Mick said. “It was a great effort by all parties involved.”
After the new plant began producing mix in the spring of 2023, there were of course minor bugs to find and correct. “Those little tweaks are to be expected with any plant,” Mendel said. “You’re never not tweaking something at the plant.”
For example, minor electrical issues or learning how the new plant affected the mixes Bowes uses most often. “It’s like cooking the same thing you’ve made for years in a new oven with a different sized pan,” Mendel said. “It’s going to come out a little bit differently.”
“Once we got the plant dialed in and calibrated and learned how the new plant affected the mix designs we regularly use, she’s been running very well,” Mendel said. “As with anything, we had some fine tuning to do on those little things that are bound to pop up, but our first season with the plant went really well.”
In fact, 2023 was Bowes’ second highest production year on record, producing 145,000 tons. “Our volume really depends on the DOT and county work available, and in 2023 we had two big DOT projects and one big county job that really brought our production up,” Mendel said. “It was a perfect year to have our new plant, because it would have been difficult to get the production we needed with our old plant.”
Although increasing production was of course one of Bowes’ goals for its new plant, a pleasant surprise they learned throughout the first year with the plant was that its production capacity was in fact more than the company had anticipated. “Even with how big 2023 was for us, we haven’t had to push the plant too hard yet, but we know that we could if we needed to,” Mendel said.
The troubleshooting didn’t stop with the plant installation. By nearly doubling Bowes’ mix production capacity, the paving crew also had to make adjustments. “They’d been used to laying down at a certain rate, and now they aren’t hampered by the plant,” Mendel said. “They can pave twice as fast as they could with the old plant.”
Although Bowes’ paver was big enough to handle the increased production rate, that wasn’t the only piece of the equipment equation that needed to be adjusted. “When the plant and the paver are achieving a higher production rate, you have to have enough rolling power and trucking capacity.”
Bowes invested in a new control system from Minds a year prior to the installation of the new plant to protect against its old controls going down and also provide enough time to learn the new system without having to also learn a new plant at the same time.
By April 29, Bowes was commissioning its new plant, integrating the Minds controls, performing our calibrations, and finalizing its setup for production. “Our normal startup date is the last week of April, so we were right on target for the tear down and install,” Mendel said.
Bowes staffed its jobs with additional rollers and trucks. “Trucking capacity wasn’t an issue with our old plant because once you initially got that first hundred tons loaded, you could only load so many trucks an hour,” Mendel said. “We’ve pretty much doubled that, so there was a bit of a growing pain there.”
To date, Bowes hasn’t been on a project its new plant couldn’t handle. “I don’t think this plant would have any problems producing 4,000 to 4,500 tons per day if we had the right road to pave,” Mendel said. “And that’s not even pushing it very hard, just letting the plant hum along. It’s a big step up from 2,700 tons per day at our old plant’s very best.”
The new plant should certainly enable the growth Bowes is anticipating in the coming years, but the company isn’t stopping there. “We built the plant with a second set of silo footings in order to add another 200-ton silo in the future,” Mendel said. “That’s not in the works right now, but we expect it to come eventually and want to be ready when the opportunity arises.”
BY BETH BRODY
Rebecca Neidich, co-founder of Pothole Heroes is the heart and soul of the company. She brings a background in human resources, construction, marketing and entrepreneurship to her eco-friendly asphalt maintenance company, which has rapidly expanded to serve the Southeast United States and the Ohio tri-state area since its founding in 2021. Prior to becoming an entrepreneur, Neidich was the human resources & recruiting manager at a major nationwide furniture chain’s corporate office. This background in organizational development and employee relations would serve her well as she went on the road to entrepreneurship.
Neidich’s first foray as a business owner was in 2003, as the co-founder of walk-in tub manufacturer, Safety Tubs, LLC, with her husband, Andre Neidich. After Safety Tubs and its patents were acquired, she took some time off to be a stay-at-home mom and ponder her next opportunity. When she and her husband realized that asphalt maintenance was an underserved area, it led to the establishment of the company, Pothole Heroes, which was named by her nineyear-old daughter.
Pothole Heroes started in Orlando in 2021 and was an immediate success. Neidich hasn’t looked back. Over the past three years, Pothole Heroes has grown to serve Tampa, Daytona, Gainesville, Jacksonville, Melbourne, Miami, Naples, Marco Island, Pensacola, Tallahassee and West Palm Beach, Florida, as well as the Cincinnati, Ohio tri-state areas. In the first four months of 2024 alone, Pothole Heroes expanded to two new locations—Charlotte, North Carolina, and Atlanta, Georgia. Expansion plans include additional locations in the Southeast.
Pothole Heroes is a woman-owned business providing sustainable asphalt maintenance to commercial, multi-family, HOAs and municipalities. One day, Neidich’s team might be repairing the asphalt in the parking lot of Mt. Hermon Lutheran Church in Statesville, North Carolina, or resealing the asphalt at Bunker Hill Condominium Association in Mount Dora, Florida. In addition to pothole repair and pavement patching, her company also specializes in sealcoating and striping, concrete services, utility cut repairs, trip hazard repairs, ADA compliance, and emergency repairs.
Neidich knew that practicing preventive maintenance throughout the lifespan of an asphalt surface can extend its usable life and dramatically reduce long-term costs. And preventive maintenance is one key to Pothole Heroes’ success. Another element that contributes to the company’s high standing in the industry is their sustainability practices.
As the co-founder and owner of Pothole Heroes, Rebecca Neidich encourages more women to join the growing asphalt industry. She’s a member of several industry groups, including the Women of Asphalt. “There is much room for growth for women in the industry...It is good, steady work that pays well and there are always roads, highways, paths and parking lots that need maintenance.”
One of the company initiatives Neidich is most proud of is the focus on environmentally friendly processes. Pothole Heroes uses infrared technology, which helps asphalt repair be more efficient and reduces the carbon footprint. Called “hot in-place,” this type of repair recycles the asphalt that is already in place. This is an environmentally friendly, cost-effective method of rejuvenating asphalt surfaces to good-as-new condition. Like all recycled asphalt treatments, hot inplace has a small carbon footprint and reduced binder consumption, which leads to reduced emissions.
“We are dedicated to reducing the company’s carbon footprint and hot in-place infrared recycling goes a long way to helping our clients achieve that goal,” Neidich explained. “In addition to the dramatic cost-benefit of recycling 100% of existing pavement, hot in-place has the bonus of reducing business disruption and user delays.”
Pothole Heroes’ infrared recycling system combined with their fleet of state-of-the-art eco-friendly trucks gives the company an edge when it comes to reducing the carbon footprint. Pothole Heroes has a goal of achieving 100% sustainability and net zero CO2 emissions within 10 years.
“We are typically in and out in far less time than conventional repairs,” Neidich explained. “Less time on the job and running back and forth to asphalt plants means less CO2 spewing into the air. In addition, all our Pothole Heroes custom clean-fuel trucks are equipped with solar panels for recharging our battery-powered peripheral equipment like saws and blowers. These measures offer the opportunity to save money, save time, and help us all breathe a little easier.
“Our company mission is to make a difference in the asphalt industry, with a commitment to promoting women in leadership roles, educating outsiders about sustainability and better environmental practices, and creating solid community leaders,” she continued. “Pot-
hole Heroes and the executive team are determined to help make the world a little nicer than we found it.”
Neidich is a member of several industry groups, including Women of Asphalt, which supports women in all aspects of the asphalt industry through mentoring, education and advocacy, and encourages women to seek careers in the asphalt industry. She’s also in the Society for Human Resource Management, the leading professional human resources membership association.
“There is much room for growth for women in the asphalt industry,” Neidich said. “I encourage more women to enter this growing field. It is good, steady work that pays well and there are always roads, highways, paths and parking lots that need maintenance.”
Silo cone opening is 36” wide for ef cient material ow.
Safety gates on all silos, including long-term and standard options.
Recessed tub liners prevent silo wall wear, avoiding bulging issues.
Silo bin top batchers feature secure long-term seals.
Recessed wireways on silo tops eliminate trip hazards.
Meeker drag conveyors are larger, allowing slower chain speed and reduced wear.
Hydraulic chain adjustment on slats maintains asphalt entry point, minimizing wear.
Visual chain tension indicators on Meeker slat conveyors aid operators.
All silos prewired with top and bottom junction boxes.
BY SANDY LENDER
TThe team at Central Specialties Inc., headquartered in Alexandria, Minnesota, isn’t new to achieving quality with its work. With the motto of “It’s on Us,” the full-service general road contractor has received accolades from various departments of transportation and recently expanded operations to handle the additional work that comes with success. As demonstrated in the Highway 85 project we discussed in the October issue, they’re open to trying out new technology and they put innovation into their day-to-day business for continuing success. Let’s look specifically at an award-winning project CSI performed
on Interstate 94 (I-94) in Stark County in 2023 for another example of their innovation and quality workmanship, and how it all contributes to the expansion.
The mill-and-overlay project called for two 1.5-inch lifts along 9.6 miles of two-lane interstate. Operations Manager Joey Johnson shared that it involved concrete removal and repair, as well as hot-mix asphalt (HMA) repairs before the team mobilized their HMA plant for mainline paving to the tune of 38,000 total tons—about 18,500 per lift.
The plant they used for the project is a parallel flow drum plant from CWMF, Waite Park, Minnesota, which can produce up to 700 tons per hour (TPH). CSI positioned their plant about 14 miles from the project and produced the RAP Superpave FAA 45 with a PG58H-34 asphalt cement at 295°F.
CWMF Vice President Travis Mick spoke in glowing terms of the team. “Partnering with Central Specialties has been a rewarding experience due to their dedication to excellence and integrity, which perfectly complements our own values at CWMF. Their ‘get it done attitude’ and commitment
Here we can see the SDX screed pattern on the mat and the roller operators performing their passes. All photos provided by CSI
to building the best road infrastructure ensure our equipment is utilized to its fullest potential, resulting in outstanding outcomes for their projects.”
While the crew used state of the art equipment and new technology like infrared thermal mapping and the patterned SDX screed, Johnson also credits the people who take the time for best practices for a stunning finish. You see, the I-94 project won a North Dakota Pavement Quality Award for ride and density. Johnson reported the bonus-worthy overall total international ride index (IRI) was 25.8 and the average density was 98.7%.
At the North Dakota Department of Transportation (NDDOT) meeting in April 2024, the company received the 2023 Hot Mix Asphalt Quality Award for its excellent work on the I-94 project. From left, Speaker Matt Linneman, P.E., NDDOT, presented the award to Project Manager Dave Winkler and Supervisor John Fales. Linneman shared with the audience, “It was exceptional quality, density and ride.”
Those are numbers worth emulating. Here’s how they did it.
On I-94, the team was getting good density right off the bat. Immediately behind the breakdown roller, which was a CAT CB 15 with VersaVibe, purchased in 2020, they were getting a density of 92.5. In the intermediate position, on the bottom lift, they ran a CAT CW34 pneumatic purchased in 2017. In the intermediate position, on the top lift, they ran a CAT CB 15 purchased in 2018. The finish roller was a CAT CB 34.
Laying the first lift was straightforward. It was a standard mill-and-fill. On the second lift, they used the notched wedge joint system from Willow Designs LLC on the center seam to increase longitudinal joint density.
First of all, they were getting good density numbers behind the screed. Johnson shared: “The Trimble infrared thermal imaging camera was used for tracking mat temperature. Combined with VETA data and analysis software it gave us good confidence with our rolling pattern coverage which resulted in good densities.” As mentioned above, they were seeing densities of 92.5 behind the breakdown roller.
“To be honest, this [thermal mapping] is a very helpful tool to be able to better help get density and ride, seeing issues and ways to improve rolling patterns,” Johnson shared.
The crew wasn’t using a material transfer vehicle on this project—just best practices and a cohesive team. The paver operator, Tomas Chavez, has been with the company for two years and was at the helm of a CAT AP 1055F paver equipped with the new SDX screed CSI is testing for Caterpillar.
Johnson shared that the paving widths varied along the project from 10 to 12 to 16 feet, yet the crew handled the changes smoothly. The dump man on the project was Jose Becerra, and the screed operator, Carlos Pasillas, has nine years of experience.
“Carlos is a very strong leader for our main line crew and a positive person,” Johnson shared. “I believe the reason we won the award was that the crew works together to make the best road possible. There is really a team atmosphere when it comes to Plant 4 crew for CSI. It really starts with John Fales leading the crew and developing them and then the crew taking ownership of the paving. At the end of every job the crew is always asking how they did on ride and density, which shows they have pride in their work.”
Discover the strength of the most versatile, durable, and reliable crushing equipment on the market today. Take on even the toughest applications with confidence. Experience unparalleled parts and service support, 24/7. Let Eagle Crusher keep you up and crushing, year in and year out.
CSI began the I-94 project April 4, 2023, and finished it Aug. 14. During those four months, the crew had challenges to overcome to hit an award-winning completion.
“There was a lot of concrete removal, and the state would only close down a certain amount of interstate at a time,” Johnson explained. “Then we would have to go out and patch back in to let traffic back on it. It was difficult scheduling to keep subs on track working and getting a crew deployed on a short window to get the patching done.”
He gave credit to Dave Winkler, the project manager, and John Fales, the paving superintendent for their leadership and expertise on the job. “The project manager really kept a close eye on the subs on when they would be completed with their phases and lining up our paving crew to come in and patch in mix, then move the subs to the next phase to complete to stay on track for the job.”
One aspect of the project that the crew gave extra attention to was the centerline joint. “Making sure centerline is clean after the milling machine,” he shared. “On the bottom lift we had some longitudinal joint failures
that we had to mill out and repair because we did not get centerline completely clean but after finding the issue the crew took ownership and got the project back on track.”
At the end of the day, the crew handled best practices and challenges with professionalism that Johnson’s proud of. “I like the fact that when there were issues the crew stuck together to get the job done. They never pointed the finger; they owned the issue and moved on. That is what makes a great crew.”
If you think the logistics of the I-94 project look complex on paper, consider what it was like in the field. With the amount of work available across North Dakota, CSI management decided it was time to expand operations. They purchased a building to start a shop and office in Watford City, North Dakota.
“We expanded with offices and a shop in Watford City, North Dakota, in January of 2024,” Johnson said. The team then used the office space to hold interviews every two to three weeks and set up the offices and a conference room for the project managers to use during the 2024 construction season
for both a home base and for meetings with local agencies when needed.
“The shop is running well,” Johnson shared. “We have three current mechanics working out there and are looking to staff up to four to six full-time mechanics in the future. That will really save us time and money in the future not hauling our equipment in the area all the way back to our main shop in Alexandria, Minnesota.”
Fleet maintenance, whether in Watford City or Alexandria, is another key to CSI’s success. “We really feel that we keep our equipment up to date and have some of the best technology. We swap out our mainline pavers every three years and we send our crews to paving classes every year to keep them up to date on new methods and ideas. We are constantly trying innovation to see what works, such as the new SDX screed CAT has us trying out.”
With updated technology and innovation for a fully trained workforce, CSI takes ownership of its success on every project. The award-winning I-94 project exemplifies this attitude and aptitude and offers a great example of the company’s motto “It’s On Us.”
Increase production and efficiency without the investment of a new drum. A leader in the retrofit market, we’ll work with you to come up with the best solution at a competitive price.
· HIGHER RAP PERCENTAGES
· SINGLE POINT ADJUSTMENT
TRUNNION DESIGN WITH HEAVY
DUTY TIMKEN RAIL CAR BEARINGS
· WEDGE-LOK™ TIRE SUSPENSION
· IMPROVED FLIGHTING DESIGN
· PARALLEL TO COUNTER FLOW CONVERSIONS
· PORTABLE AND STATIONARY
BY SARAH REDOHL
strategically placed
Aapply
An ultrathin bonded wearing course is a single-process application of an ultra-thin overlay, typically ¾ inches thick or less, designed to improve pavement performance on high-speed, high-traffic roadways.
Initially introduced to the U.S. market from Europe in the early 1990s as NovaChip, the use of bonded wearing courses has evolved alongside advancements in materials, equipment and construction practices, allowing it to be applied effectively across diverse traffic conditions and climates.
“The use of [bonded wearing courses] has really boomed in the past five or 10 years, particularly in the northeast,” said Robert Betsold, director of marketing at All States Materials Group (ASMG), Sunderland, Massachusetts, during a presentation about the process at World of Asphalt/AGG1 2024. “It’s really become a workhorse application for a lot of the interstates throughout the northeast.”
During his presentation, Betsold discussed how the process compares to traditional thin-lift paving; the materials, equipment and construction methods used; and the best practices of selecting projects for this application. Let’s take a closer look.
The key differences between this treatment and a conventional thin lift overlay are the reduced thickness and the higher tack coat application rate. “When we talk about hot mix overlays, we’re usually talking 1.5 inches or less,” he said. “With [bonded wearing courses], we’re talking about ¾ inches or less.”
The application is designed for high-speed, high-volume roadways, Betsold said, attributing bonded wearing courses’ performance in those conditions to the increased tack application. Betsold estimates a typical tack application for an overlay in the northeast to be 0.05 gallons per square yard, while a bonded wearing course sees an average of 0.2 gallons of tack per square yard.
“The tack is the basis for the performance of this treatment and the ability to pave thin without the typical challenge of delamination,” Betsold said. “If the materials are made right and the application is done right, you don’t have that concern. The material is locked in place.”
Although the process looks similar to conventional paving, there are also differences in application. “If you tried to spray out 0.2 gallons of tack per square yard and tried to drive trucks over it and pave over it, you’d have a mess,” Betsold said. That’s why this process relies on the use of a spray paver with an onboard emulsion tank for the tack and strategically placed spray nozzles that apply the tack immediately before the mix is applied atop it. “The tack is never touched by anything other than the mix going on top of it.”
“This is a great process for agencies looking to get into preservation, because it looks like conventional paving to the driving public,” Betsold said. “They see dump trucks, they see a paver, they see rollers and they see a smooth paved surface. The performance of the application is different, but the outward appearance is the same.”
According to Betsold, the tack most commonly used in the northeast is a polymer modified tack (usually CRS1P). “We get the performance of that polymer modified liquid,” he said, “but it’s really the thickness of the application that gets us the adhesion we need without delamination.”
However, such a thick tack application brings concerns about flushing. That’s why Betsold said the process usually uses a gap graded mix. “This falls in between dense graded and open graded mixes, which allows for the wicking of that 0.2 gallons of tack up into the mix to get that really strong bond,” Betsold said.
“If you have a thickness of ¾ of an inch, you’re typically going to get about ⅜ of an inch (about half the cross section) that will be flooded with the tack coat,” he said. “When you take cores and look at a cross section of it, you’ll see that there are pretty much no air voids. By filling those in, you’re sealing it/waterproofing it.”
Betsold said polymer-modified mix is also often used on these projects, particularly higher volume state roads in the northeast, but that he’s also seen asphalt rubber used successfully. “In the local agencies, the traffic doesn’t warrant [polymer-modified mix] in terms of the upcharge, so the majority of the municipalities are still using conventional hot mix with this application.”
The American Association of State Highway and Transportation Officials (AASHTO) is in the process of finalizing specifications for ultrathin bonded wearing courses, Betsold said. In addition to his role at ASMG, Betsold is a member of AASHTO Emulsion Task Force, serves on the board of FP2, and is an industry representative on the board of the Northeast Pavement Preservation Partnership. “Soon, we’ll have a national specification from AASHTO to be a guideline for local agencies,” he said.
The ultrathin bonded wearing course put down in 2015 on Massachusetts’ Route 3 has become a poster child of success for this application, Betsold said. Route 3 is the main north-south route
from Boston to New Hampshire, seeing more than 100,000 vehicles each day, he added.
The project consisted of nearly 1,000,000 square yards of mainline bonded wearing course application with fog seals on the shoulder as a trial project through the SHARP program for high volume preservation. The project was divided into three test sections, one using conventional hot mix, one polymer-modified mix, and one mix with asphalt rubber.
It was estimated that a typical mill-and-fill application would take two to three years, whereas the application of a bonded wearing course could be completed in one construction season. Ultimately, the project was paved in 51 night shifts, starting the first lane at 10 p.m., the second at midnight, and opening the road to traffic by 5 or 6 a.m.
MassDOT was hoping to get seven to 10 years, and eight years later Betsold said the treatment is performing “far beyond their expectations. This was really the project that springboarded [the use of this application] in the northeast.”
Betsold said that although the performance of the bonded wearing course on Route 3 has been very good across the board, the polymer-modified and asphalt rubber sections of the project have outperformed the conventional hot mix section, “which is what we would expect if we were putting a traditional hot mix overlay out there compared to polymer-modified and rubber.”
The Route 3 project illustrates the types of applications for which ultrathin bonded wearing courses shine: high speed, high volume, demanding applications. “It’s really going to perform when you get into those applications where you’ve got truck traffic or more than 100,000 vehicles per day,” Betsold said.
One difference a conventional thin lift overlay and a ultrathin bonded wearing course is the higher tack coat application rate, applied immediately before the asphalt using a spray paver like Vogele’s S18003i SprayJet.
However, the treatment can be used on a variety of applications, from high volume roads down to low volume municipal roads. “New York is doing a lot of neighborhoods and subdivisions with it,” Betsold said.
In municipal settings, Betsold said, the treatment is most often used in urban environments with higher traffic counts. He provided the city of Newton, Massachusetts, population 100,000 just outside Boston, as an example. “They’ve been using this in a variety of applications with a lot of success,” Betsold said. “It’s really become a workhorse for them in their preservation program.”
Newton’s first use of bonded wearing courses was a standard preservation overlay in 2018. “Based on the performance of that project, they started looking at how they could use it in other applications and it’s really expanded into some unique applications,” Betsold said. For example, to treat approximately 10 miles of exposed concrete roads “they were paying a tremendous amount to maintain and remove.”
Working with the city, a consultant engineer and various contractors, Newton established a process for applying ultrathin bonded wearing courses to those concrete roads. “They’re typically doing a ¾-inch mill of that existing concrete, doing mastic on any joints or larger cracks, patching if necessary, putting down an asphalt rubber chip seal as an interlayer to get that sealing and crack resistance, then surfacing it with that bonded wearing course as the final surface,” Betsold said. “The first was done in 2020 and to date is performing very well with some minor cracking.”
Ultrathin bonded wearing courses can be placed over asphalt or concrete, atop existing surface or a milled surface, with tweaks to tack application based on the existing surface and traffic type. “If you’ve got a drier surface, you may bump that tack application rate up a bit,” Betsold said. “If you have a richer surface, you might back that application down a little.”
Despite the success of ultrathin bonded wearing courses in a variety of applications, Betsold stresses the importance of understanding its benefits and potential drawbacks. “By no means is this the best application for everywhere,” he said. “I’m a big proponent of using the right treatment, in the right place, at the right time.”
For example, as with any polymer-modified mix, it’s important to minimize handwork. “I was on a project in metro Boston a few years back that had 300 utility structures and trying to rake out the polymer-modified mix was not fun for the crew,” Betsold said. The polymer-modified mix also results in a shorter potential construction season.
The gap graded mix design is also less ideal for projects with significant handwork, for example, cul-de-sacs, sharp turns or variable width roads. “There aren’t a lot of fines with that gap graded mix, so raking it too much can result in shadowing,” Betsold said. “Your better bet may be to mill those out and pave them with a traditional hot mix and then do your main line with the bonded wearing course.”
Betsold said candidates for ultrathin bonded wearing courses must still be in good structural condition. “If it’s new to the agency and you use it [on that kind of a pavement] and it fails, it’s going to be a whole lot more difficult to get them to let you do it again. We need to make sure we’re setting our projects up for success.”
Betsold also cautions against what he calls “scope creep” on bonded wearing courses. “This process was developed to be a quick in-and-out application, not a full-blown construction project,” he said. However, he’s seen some projects in the northeast “where there’s been some scope creep and they’ve turned a process that’s meant to save time and money (while extending the roadway) into a full-blown construction project, which drives up the cost tremendously.”
Although the ultrathin bonded wearing course paving process may look similar to conventional paving to the untrained eye, Betsold outlined some differences it’s important to understand. This begins with prep work.
“Ultrathin bonded wearing courses will fix some minor defects in your profile, but this is not a thick overlay,” Betsold said. He recommends filling any cracks ¼ inch or wider. “Crack sealing creates a tremendous increase in the performance of all types of pavement preservation treatments including overlays, because we’re preventing water intrusion for pennies on the dollar.”
In Betsold’s experience, many state projects using bonded wearing courses are micro milling ahead of treatment. Although milling often isn’t necessary because the lift is so thin, he said it isn’t uncommon for bonded wearing course projects to be milled full-width or gutter milled to maintain curb reveal.
The use of a gap graded mix also has benefits in terms of tire spray, Betsold said. “We all know when we drive on a dense graded mix, we get that tire spray. With gap graded mix, you are going to see reduced tire spray due to that water shedding, although not to the extent of what you’d see with open graded mix.”
“A lot of state projects in the Northeast (and even some municipal settings) have utilized a milled fog line,” Betsold said. This is when they apply a fog seal on the shoulder. “That allows them to handle the shoulders with a less expensive treatment…while tying the surfaces right in together so you don’t have any drop off.”
Then comes the spray paver, which applies both the tack and the hot mix in a single pass. “The only thing that goes on top of that [tack] is the mix,” Betsold said. Calibration here is exceedingly important. “Everything is metered and controlled. You need to make sure your equipment is calibrated correctly so you’re actually getting what the system is telling you you’re getting.”
Areas that require extra attention include takeoffs and joints. “I’ve seen the tack be a bit skinny on the takeoff, which is a potential point of failure,” Besold said. “Using the hand hose allows you to get that consistent heavy application of tack.”
“If you don’t have that tack out there or your application is off, and you’re trying to get ¾ of an inch to adhere without that wicking action, you’re setting yourself up for potential issues,” he said.
Betsold said overlapping at the centerline joint can be a material solution to a persistent industry problem. “A slight overspray as you pave that joint allows for that adhesion and waterproofs that joint to address some of those issues,” Betsold said. However, he added, “we need to be careful we aren’t overspraying too much and causing flushing.” The exact right amount of overspray depends on the balance between the mix design, the gradation of the mix, the existing surface of the roadway and the tack application rate, he said.
The rollers play a significant role in the wicking action Betsold describes. “We aren’t rolling for density, but to bond that material to the tack and to provide a smooth final surface.”
Usually, these projects require just one roller, though Betsold said two may be used on some state projects. Regardless of the number of rollers, Betsold recommends the roller(s) be immediately behind the paver.
“You can cover a lot of ground really fast at ¾ inches thick,” he said, which also increases the speed of the rollers. “Because we don’t need to hit that traditional density, the speed you can get traffic back on the road is certainly a benefit to the application.”
This benefit was put to the test on one of the first bonded wearing course projects Betsold was ever on. It was a municipal paving project in a Vermont subdivision with just three houses. “Not a single car had come out all day,” Betsold said. The paver was ¾ of the way done when an impatient driver in a Porsche rolled up. “The roller took two passes, and the Porsche drove over it, no problem.”
Ultrathin bonded wearing courses can be used successively, Betsold said, but the existing surface must be considered as always. “If we have a bonded thin lift out there and put a second one on seven to 10 years later, there are a couple things that come into play,” he said. “You have extra air voids [with the gap graded mix], so when you put the tack on there, you’re going to lose some of it down into the previous lift, so you aren’t getting as much wicking action up into the successive lift.” This, like many other factors, must be considered when determining the tack application rate.
On another municipal project near a fire station, the paver was ¾ of the way done when the fire alarm went off. “The roller went over it, then the fire trucks immediately after, and that pavement is still there five years later,” Betsold said.
The key to such a successful project, as with any treatment, is quality control. “Quality control is at the forefront of everything that we do,” Betsold said. He stressed the importance of a quality control plan, “especially if an agency is new to the process.”
“There are agencies out there who think they’re inspecting this the same way they’d inspect traditional hot mix,” he said. “Yes, it’s paving, but it isn’t the same as paving. There are nuances you need to understand in terms of materials, gradation, application rates. Those little nuances can have a big impact on the performance of that application. When we’re talking about such a thin pavement layer, if we’re off by a little bit, that can have a significant impact on the long-term performance of that treatment.”
Loading mix correctly at the plant is only one step in preventing material segregation. Maximize loadout efficiency by considering truck body style. All photos courtesy of John Ball, Top Quality Paving & Training
BY JOHN BALL
Editor’s Note: For 2024, AsphaltPro Magazine allows experts in the industry to share how to expand your operations to the next phase of business. Are you ready to start making your own hot-mix asphalt? Let’s turn to some professionals who have equipment, services, software and tenure to help you expand efficiently to mix design, production, hauling and more. This month’s installment from Top Quality Paving & Training, Manchester, New Hampshire, delves into the mechanics of safe loadout for the new plant operator and new haul truck driver, no matter the type of truck.
NNot all haul trucks are built the same. They shouldn’t all be loaded the same to deliver our perishable hot-mix asphalt (HMA) to the job site. Something I noticed while helping a crew in 2023 made me reconsider offering the same old advice of the three-drop method for loading all trucks at the silo.
We had a live-bottom trailer on its second round-robin to the job site and as the material slid into the hopper, chunks of cooled hot-mix asphalt (HMA) plopped in, too. When I investigated, I discovered the railings across the top of the truck’s bed were acting as a shelf for mix that had dropped from the silo.
In the first picture, we can clearly see the support frame of the live body trailer with material loaded properly beneath and between the supports. In the next picture, we can see where the material was loaded too high and dropped over the supports. Mix has piled on top of the frame where it has cooled. The next load of mix will knock these cooled chunks into the bed where they will contribute to segregation.
Mix sitting on the support structures cooled as the perishable material was delivered to the job. The material cooled more as the truck returned to the plant. Then new mix knocked the cold chunks into the bed. Let’s talk about how to avoid this problem and how to best use different truck bodies for asphalt delivery.
Think about your tandem haul trucks. They’re typically square-bodied. They haul about 20 to 24 tons on average. It’s smart to put a plastic liner in them to create curves in the corners so mix isn’t lodging and building up in the corners. Make sure to stop and spray a release agent in the bed before approaching the scale.
We’ve been designing and manufacturing custom mixing solutions in Tennessee for nearly 40
These workers are cleaning the live-body trailer at the designated cleanout area. In this image, you can see the conveyor system at the bottom of the “V” of the bed.
When you get to the scale, follow the marks or lights that the plant has in place to help you line up under the gate correctly. Many plant loadout controls these days won’t let the silo gate open until the operator sees that you’re in the correct position and presses a button “unlocking” the system. This is for your safety. (See the sidebar about AI Loadout Technology for more information.)
BY SANDY LENDER
“I NOTICED SOMETHING THAT MADE ME RECONSIDER THE SAME OLD THREEDROP METHOD FOR LOADING ALL TRUCKS.”
The plant operator will want to use the three-drop method to load in three “hills” in the truck to minimize material segregation. You start with the first drop at the very front of the bed; pull forward so the second drop lands in the back of the bed; then back up so the third drop lands in the center. Pull forward, raise the tarp, and proceed directly to the job site. When charging the paver’s hopper, you can raise the bed in a manner that helps the material move as a mass, but the mix tends to
Many of our advertising partners have asphalt plant control systems that allow the plant operator to prevent the silo gate from opening until the haul truck driver has positioned the body correctly on the scale. Back in 2007, when AsphaltPro Magazine was preparing to make its debut, a conversation with Richard Young of B&S Light Industries, Claremore, Oklahoma, revealed the need for a publication that would discuss the importance of this safety technology.
Seventeen years later, software providers as well as asphalt plant original equipment manufacturers (OEMs) make loadout controls a focal point of plant control for good reason. Not only is this an area where safety is of utmost concern, but it is also an area where quality control and bean counting can derail if all parties aren’t paying attention to details—or letting new technology assist.
Let’s focus specifically on the Look, Lock ’N Load system by Stansteel/Hotmix Parts & Service, Louisville, Kentucky. The system uses artificial intelligence (AI) to “learn” about incoming trucks and to load them accordingly.
As a truck approaches the loadout area, the Look, Lock ’N Load system digitally scans it and is designed to differentiate the cab area from the loadout bed. The control display shows the operator a red zone for the cab and a green zone for the loading bed. It recognizes the truck’s position and links that to the silo loadout system to confirm when a specific truck is in the loading zone, approving the silo gates to open. The console allows manual override and an optional keylock to prevent bypass loadouts, if the plant manager wants that.
In the end, the system is mathematically using images to teach its neural network about the trucks that frequent your plant and
The Look Lock’N Load system from Stansteel/HotmixParts & Service uses AI technology to train its neural network about the trucks frequenting your asphalt plant.
learning how to load them safely. The Stansteel AI-based scanning and visual identification technology is similar to that used by Amazon and United Parcel Service for rapid, high-volume package sorting, according to the manufacturer.
It would take multiple pages to share all the robust and innovative programs OEMs and software providers have implemented to enhance the safety and efficiency of HMA loadout. Instead, asphalt producers are encouraged to peruse the ad index on page 56 for plant components and controls providers as well as plant manufacturers. These companies, as well as consultants in our industry, are available to discuss upgrades and enhancements to make loadout safe and efficient at your operation.
When drivers fail to clean the truck beds, material can build up on the sloped walls of the live-body trailers as easily as it can build up in the corners of tandem bodies. Spraying beds with a release agent at the plant prior to loadout will only go so far to help with charging the hopper smoothly and with cleanout. Make sure you get to a designated cleanout area and take care of issues like this before they can cool and become a material segregation problem in the next load of material.
roll. (See the article “Save on Costs with Your Professional Guide to Asphalt Mix Delivery, Part 3—An Independent Look at Best Haul Truck Practices” on TheAsphaltPro site for best practices when approaching the job site and backing to the paver.)
U-shaped bodies have no corners or crevices for material to build up in. They haul about 20 to 24 tons on average. You’ll want to use the same three-drop method for these trucks. When you charge the hopper at the job site, the mix won't roll as much as it slides. Be aware, it’ll slide out quickly.
The live-body trucks are typically v-shaped with a chain, like a lattice, or a conveyor belt at the bottom of the V. This conveyor moves the whole load in a mass to help eliminate material segregation; the mix doesn’t roll at all, but moves as a mass. These trucks haul anywhere from 20 to 28 tons, although I’ve seen ones in Canada capable of hauling 35 tons.
For this type of truck body, you want to load in four 5-ton dumps instead of three larger dumps. It’s smart to line the truck up under the silo so you center the gate between the support bars of the truck body. You want to keep each of the “hills” lower than the rafters so the material can’t collect up there and begin to cool.
Getting the mix loaded correctly at the plant is only one step in preventing material segregation. You can maximize the efficiency of that loadout if you take your truck body style into consideration.
John Ball is the proprietor of Top Quality Paving & Training, Manchester, New Hampshire. For more information, contact him at (603) 493-1458 or tqpaving@yahoo.com.
Most haul trucks do not come standard with a tailgate, but adding one can improve the truck’s load distribution to combat uneven wear on the tires and chassis. Photos courtesy of Philippi-Hagenbuch
BY ASPHALTPRO STAFF
In asphalt and aggregate production, improving efficiency is essential for meeting demand and staying competitive. Off-highway haul trucks are often hindered by issues like underutilized capacity, spillage and downtime, which limit productivity.
At World of Asphalt/AGG1 2024, Josh Swank, chief growth officer at Philippi-Hagenbuch, Peoria, Illinois, and Philippi-Hagenbuch customer Clay Albright, vice president/owner at Caldwell Stone Co., Inc., Danville, Kentucky, discussed how haul trucks in quarry environments can be tweaked with tailgates and sideboards to increase load capacity, reduce material loss and speed up loading times.
Before Albright invested in tailgates on all of Caldwell Stone’s trucks, he ran the numbers using his scale ticketing software. “For the year before we put the tailgates on, one of our trucks averaged 31.4 tons [per load] for the year, with more than 1,000 loads across the scale that year,” Albright said. The 40-ton truck provided a good comparison, since it only hauls two types of material (½-inch chip or 3/16-inch sand). “After we put a tailgate on it, that truck was hauling an average of 36.7 tons per load—a 17% increase.”
According to Swank, tailgates increase volume capacity anywhere from 10 to 20%, depending on the material size and density. “The average most of my clients see is around 12%,” he said. For example, he added, “If you have a 70-ton haul truck and you’re leaving 8.4 tons
behind per pass, that’s more than 20 tons per day and 1,000 tons per week you’re leaving behind.”
Regardless of which OEM you go with for your aftermarket solutions like tailgates and sideboards, make sure they’re mining-duty versus agriculture- or construction-duty, Swank said.
Swank said adding tailgates to your haul trucks also improves loading efficiency. “It creates a larger loading target for your loader operator,” he said. “Without a tailgate, they’re trying to load closer to the front of the truck to keep material from falling off the back.” This results in slower loading times as operators take care to load material so it won’t fall out the open back.
3. Minimize Maintenance
This method of loading can also increase the maintenance your trucks require. “[Loading the front] puts more load on your front axle versus your rear axle,” Swank said, “and trucks are designed to have equal weight on all tires.”
Whenever Swank visits his clients, he always checks if any tires are more squished than the others (assuming equal air pressure). “If so, that means the weight distribution is off and creating unnecessary tire wear.”
Since its introduction, the Weiler P385 has set the standard for commercial pavers. The P385C raises that standard.
Increase to 120 hp with the Cat® C3.6 Tier 4F/Stage V engine.
Variable speed and reversible conveyors and augers and a 25% increase in tunnel height provide optimal material output.
Modular conveyor drive and sealed chain case increase feeder system reliability and life.
Enhanced heat system performance with direct-drive hydraulic generator and elimination of GFCI breakers.
4. Reduce Spillage
Tailgates reduce spillage off the rear of the truck, while the addition of vertical side extensions/sideboards reduce spillage off the sides of the truck. “When you’re loading, it’s not uncommon for the loader operator to be so concerned with material falling off the back that they load it so material falls off the sides,” Swank said. “Sideboards are a very simple, easy way to keep the rocks in the box, while also increasing volume.”
Sideboards can be used with or without a tailgate, Swank said, adding, “As you go over the 6 to 9 inch number, it’s important that if you’re going to build up the sides you have a unified height all the way around.”
5. Reduce Emissions
“The more trips you take, the more fuel you burn, the more emissions you have,” Swank said. “If you can minimize your fuel burn, that’s great for your bottom line and for the environment.”
According to Albright, the 17% increase per load for their 40-ton trucks resulted in a negligible amount of extra fuel use compared to multiple additional haul loads per day to make up that 17% difference. “We’re getting closer to capacity on every load,” Albright said. “We’re making less trips and filling up quicker.”
6. Improve the Bottom Line
According to Swank, the average return on investment for adding tailgates to your trucks is 30 days. “I did a case study with a client a couple
Adding a tailgate and sideboards increases a haul truck’s volumetric capacity, helping operations maximize their efficiency by hauling the truck’s full rated weight.
years ago, and those tailgates paid for themselves in five days because of the efficiencies they added,” Swank said. “Now, they have them on every truck in their company.”
“What else can you do to achieve that much growth in efficiency with an average return on investment of less than 30 days? The numbers don’t lie.”
Ultimately, Swank said, the addition of both tailgates and sideboards are a small tweak companies can make to their existing fleet to make it as efficient as possible. “It’s not about the number of trucks but about maximizing utilizing what you already have,” he said. “It’s ultimately going to be better for you to expand your trucks, not your fleet.”
BY ASPHALTPRO STAFF
To gear up for season shutdown, you're probably making your maintenance plans. Over the next few pages, original equipment manufacturers (OEMs) and others show off the components and services they can offer to help you through the winter. An OEM tangentially related to our industry offered some ideas for cleaning your heating elements. Let’s look at getting scale off the boiler tubes before it becomes a hazard.
For boilers that produce hot water and steam for industrial activities, scale buildup can creep into operations without you realizing it. The team at Cortec® Corporation explained scale forms when minerals such as calcium carbonate in the water combine and create scale deposits on boiler internals. The thicker the buildup, the harder it is for water or steam to flow through the pipes. This means heat transfer efficiency drops, demanding more energy to heat the boiler water and create steam.
Scott Bryan, CWT and technical sales manager of Water Treatment at Cortec® Corporation, summarized, whenever scale is forming in any system, “If you are starving that system of its needed heat transfer efficiency, you are hurting the performance of that whole process.”
As discussed in the October issue of AsphaltPro, it takes a good overall controls system to monitor all the parts and pieces of a plant. Not every asphalt plant will employ steam heat these days, but if you’ve got it and your system doesn’t alert when there’s a change in flow or heat transfer efficiency, your facility could experience scale buildup problems long before realizing their effects. Bryan explained, if this proceeds too far, it could result in a boiler pipe that ruptures without warning, leading to major problems.
“A boiler will blow a tube and cause the whole system to come down, and that could create a catastrophic event at worst and an unplanned maintenance shutdown at best,” Bryan said. In either case, at least some plant operations will grind to a halt.
To avoid such serious problems, it’s important that boiler owners and managers take preemptive steps. The best plan is to minimize the formation of scale deposits by adding an anti-scalant to the normal water treatment program. These chemistries keep dissolved minerals such as calcium carbonate from combining and depositing on the metal. Cortec advises its own product, the S-14 Series, be added to standard water treatment formulations.
The second step is to periodically remove scale that has formed. This should be done whenever pressure increases and heating demands rise. However, since these indicators can be difficult to detect in a boiler, it is a good plan to conduct scale removal every few years during routine maintenance. Cortec advises using a product like EcoClean® Biodegradable Scale and Rust Remover, which is designed to dissolve scale.
Scale is a normal nuisance in boilers. However, by catching the problem early, boiler owners can avoid the most serious issues that come from scale-induced surprises such as melting or bursting boiler tubes.
For more information, contact the Cortec team at https://www. cortecvci.com/contact-us/
It’s a good idea to conduct scale removal every few years during routine maintenance. Photos courtesy of Cortec Advertising
have chemistries to keep dissolved minerals such as calcium carbonate from combining and depositing on the metal. This buildup prevents efficient heat transfer.
Not all heating systems look alike but the concept remains the same. Preventing liquid asphalt cement coking or scale buildup on different heating elements protects those elements from inefficiencies and potential ruptures or breakdowns.
ALmix, Ft. Wayne, Indiana, offers the two-story control house. All ALmix 2-Story Control Houses are designed to provide a safe, refined and controlled environment for your asphalt plant operators, automation systems, and sensitive electrical equipment. The lower story of the control house features a UL-Approved Motor Control Center (MCC) as well as a personnel bathroom and garage area. The upper level serves as the control room and contains the blending and loadout computers and boasts a full 360-degree view of your plant.
For more information, call (260) 672-3004 or visit ALmix.com.
Ammann America, Orlando, announced earlier in 2024, its newest counterflow drum mix plant specifically designed for high production and high-capacity recycling technology. Available in stationary, relocatable and portable configurations ranging from 300-600 tons per hour.
The Alpine series is designed to enable HMA producers to maximize high total production and amount of recycled asphalt pavement (RAP) content without sacrificing mix quality using Ammann’s controls and technologies. The Alpine series control system is intuitive and allows tracking and analyzing plant operating data in real time to provide real opportunities to gain further efficiencies.
The OEM lists the following benefits of the new plant:
• Single drum, multi-zone drying and mixing system with VFD
• Modular and scalable designed components
• High RAP capabilities up to 60%
• Warm asphalt capability with the proven Amman foam system
• Easy customization of plant arrangements
• Easy retrofit to existing facilities
• Extreme wear packages for extended operating life
• 24/7 local support with a hands-on project management team
Ammann’s HMA storage silos have capacities ranging up to 300 tons with extended mix storage options available. Silos are engineered
with expansion in mind. The modular silo batcher arrangement is expandable for retrofitting and matching silo deck heights.
Ammann’s aggregate feed systems include troughing feed belts to eliminate spills and large bin openings for greater capacity. The reverse-air baghouse system is the newest version of a broad range of existing Ammann dust control products.
For more information, visit www.ammann.com
Astec Industries, Chattanooga, announced in August the integration of charcoal filters into its renowned, patent-pending Fiberbed Mist Collector. This enhancement improves the system’s ability to capture and eliminate odor-causing compounds, delivering air quality and community satisfaction for asphalt facilities.
Astec’s Fiberbed Mist Collector captures and cleans blue smoke generated during silo or loadout operations. With the addition of charcoal filters, the system now offers a more comprehensive approach to odor control. By trapping and neutralizing odor-causing compounds, the charcoal filters reduce detectable odors emanating from the facility, fostering a more pleasant work environment and strengthening community relations.
“We are committed to providing our customers with industry-leading solutions that address their environmental challenges,” said Catherine Sutton-Choate, director of environmental compliance at Astec Industries. “The integration of charcoal filters into our Fiberbed Mist Collector is a testament to our dedication to innovation and our customers’ success.”
Blue smoke, caused by the condensation of asphalt fumes, has long been a source of frustration for asphalt facilities. Astec’s Blue Smoke System, which includes the Fiberbed Mist Collector, effectively controls emission opacity by limiting the escape of vaporized asphalt fumes into the atmosphere.
For more information, visit www.astecindustries.com.
BROCK LLC, Chattanooga, builds asphalt cement (AC) tanks with a variety of capabilities, with standard sizes ranging from 10,000 to 35,000 gallons in 5,000-gallon increments. BROCK AC tanks come standard with 6 inches of insulation covered with aluminum skin. BROCK designs these tanks with three different floor options. The standard floor is a flat design; the other two designs are sloped with low point drains
to help prevent build-up in the tank bottoms and around the coil area. The BROCK standard fill lines (Bull-Horn Design) promotes agitation below the heating coil each time the tank is filled. “The BROCK AC storage tank is quickly becoming one of the most desired products offered by BROCK LLC and a favorite of many customers, resulting in numerous repeat business opportunities,” the OEM stated. “Everyone at BROCK is thankful to the customers who are experiencing the high quality and dependability of the BROCK AC storage tanks.”
For more information, contact Travis Sneed at tsneed@brock.llc or visit www.brock.llc
Eagle Crusher Co., Galion, Ohio, hosted the Association of Equipment Manufacturers (AEM) Manufacturing Express on Sept. 13, 2024, at its Bucyrus manufacturing facility as the tour’s 55th stop, celebrating company employees and highlighting the critical role that Eagle Crusher plays in advancing American manufacturing and its contribution to the local economy. Eagle Crusher employees and their families, AEM, and members of the local Bucyrus and Galion communities, including
During the Eagle Crusher stop on the AEM Manufacturing Express, attendees were able play the industry-themed online game, "The Manufacturing Challenge," for a chance to win the grand prize, a Ford F-150. They also had an opportunity to take a guided factory tour.
local officials and policymakers, gathered to recognize Eagle Crusher as an industry pioneer for its contributions to U.S. manufacturing and witness firsthand the high-quality crushing and screening equipment for which Eagle Crusher is known.
Through Eagle Crusher Co.’s investment in the local workforce, the company plays a key role in maintaining the economic vitality of the area. Mike Tinkey, president, Eagle Crusher, thanked all who attended and contributed to making the event a success.
Kip Eideberg, senior vice president, Association of Equipment Manufacturers, stated, “The AEM Manufacturing Express traveled to Ohio to celebrate the grit, determination, and can-do spirit of the people who build things in America and to remind everyone that when the equipment manufacturing industry is strong, communities like Bucyrus are also strong.”
For more information, visit https://eaglecrusher.com
MAJOR, Candiac, Quebec, has updated The MAJOR App as of September 2024. The new application update combines The MAJOR App with the FLEX-MAT Sensor App to create one resource for mining and aggregate producers and MAJOR dealers. Depending on the type of user, the app includes marketing materials, expert documents and a newsroom with articles and announcements as well as the RFID reader technology and the FLEX-MAT Sensor.
“Simplifying The MAJOR App allows customers to access all their screen media data in one place—saving time and virtually eliminating room for measurement errors,” said Kevin Laporte, MAJOR R&D manager.
The MAJOR App streamlines customer and dealer processes by digitalizing relevant product information. Customers and dealers can track and store screen media data such as screen dimensions and customer-defined details to simplify the ordering process through FLEX-MAT ID Enabled. The RFID technology allows customers and dealers to access product information through The MAJOR App without needing an additional reading device. Operators scan the FLEX-MAT screen with The MAJOR App to access product information. This makes the reordering process easier by minimizing the need to climb onto the screen deck to measure screen. For screen media without ID Enabled features, the app includes an augmented measurement tool where customers and dealers can use their phone camera for approximate measurements.
The app also features the FLEX-MAT Sensor, a vibration data measurement tool operators can utilize to fine-tune their screen machine without shutting down the equipment. Merging The MAJOR App with the FLEX-MAT Sensor App makes updating the app easier, especially when it comes to measurement and ordering. Combining these applications creates one location for all functionalities, creating a more secure login system and making updates easier in the future.
The application also includes an efficiency calculator, open area calculator and a warehouse function that compiles a list of screen media in storage along with their specifications. These features help operations closely monitor production and inventory for improved efficiency.
The free app is available for Apple and Android phones. For more information, contact MAJOR.
MASABA Inc., Vermillion, South Dakota, announced earlier this year it has begun work on a new state-of-the-art steel fabrication facility located adjacent to its existing 211,000-square-foot manufacturing facility. The new building will create an additional 125,000 square feet of fabrication space and over 20,000 square feet of office space. The facility will house more than $15 million in new steel fabrication equipment and will be fully operational by May 2025.
According to Jerad Higman, MASABA founder & CEO, “MASABA continues to invest in our team, the industries we serve, our local economy and America. MASABA will be on the leading edge in steel processing and will continue to increase the bar on quality. This expansion will allow MASABA to centralize all processing equipment in one building and utilize automation to process all our plate and structural steel.
“Our investment in the new facility will streamline our operations, expand manufacturing space, and give us the ability to become more vertically integrated,” Higman continued. “We will be able to repurpose our current steel fabrication area into additional weld and assembly bays, which will allow us to meet the increased customer demand we have seen since 2020. The expansion positions us well for future growth. The City of Vermillion and the State of South Dakota have been great partners and supporters of this project.”
Meeker Equipment’s line of baghouses includes the Freedom Series reverse air baghouse and jet pulse baghouses. Our reverse air baghouse
is designed to pulse an entire turret one revolution or half a revolution; and pulse in selectable sequence instead of one after the other.
The manufacturer states: “We use cuff bottomed bags so cages don’t ‘squeeze’ up over time. Our reverse air and jet pulse baghouses are insulated, which saves start up time and heating costs. Tube sheets are epoxy coated or available in stainless steel for difficult applications.”
The OEM offers baghouses up to 120,000 CFM, knockout boxes, ductwork and screw conveyor systems for a complete dust handling solution.
For more information, call (888) 333-0323 or visit https://www. meekerequipment.com/productDetails-57.
Process Heating Company LLC, Seattle, has been supplying customers with a clean, reliable heat source since 1947. In recent years, PHCo researched the cost calculations for maintaining 30,000 gallons of asphalt cement (AC) at 300˚F over a 24-hour period (1 MMBTUs)* with the fuels of natural gas, LP propane, No. 2 oil and No. 6 oil, and electric heat. Producers can review the results of the research at https://www.processheating.com/wp-content/uploads/2022/06/PHCo-Asphalt-Heating-Cost-Comparison.pdf. At that same link, the interactive heating cost calculator allows producers to insert their own local energy numbers and stack permit costs to calculate your daily and annual heating costs.
For more information, visit www.processheating.com/.
AsphaltPro magazine and paving consultant John Ball bring you the online training resource: Asphalt Paving 101. It’s available on any device, anytime, anywhere to train your entire crew.
Asphalt Paving 101
In this course, your crew will learn:
• How to stay safe on the job site
• How to build a takeoff ramp
• How to determine fluff factor
• How to determine yield
• How to prep for real paving in the real world
• and so much more…
Rotochopper, St. Martin, Minnesota, held its ribbon-cutting ceremony in August in celebration of its newly expanded research and development innovation center. This 12,000-square-foot expansion includes a state-of-the-art production space, significantly increasing the company’s manufacturing capabilities, along with an office area to enhance collaboration and efficiency. Additionally, the new facility features a dedicated space for research and development. This space will allow Rotochopper’s engineering and R&D teams to continue driving innovation.
Staar Lubricants LLC, Reynoldsville, Pennsylvania, has launched its asphalt release agent and solvent titled Trick Shot® for the industry. Available in sizes conducive to pre-treating hand tools and components, the liquid also comes in totes for use at the asphalt plant or wherever you pre-treat the asphalt haul truck bed.
The company states the bio-based Trick Shot “sustainable products asphalt solvent and cleaner has been specifically developed as an EPA allowed alternative for the asphalt production, paving and maintenance industries.” Also labeled Trick Shot Asphalt Solvent & Cleaner (TSAS&C®), the product is formulated to dissolve bitumen, tar, oil and tack from paving equipment without harsh chemicals. The manufacturer states, “It does not release harmful fumes, is non-flammable, safe for contact with skin, and is even registered NSF-H1 food safe.”
Purchase your access to the course at: training.theasphaltpro.com
LEFT: “A prominent trend in the asphalt market is the increasing demand for products that are environmentally sustainable and eco-friendly. Another significant observation in this market is the rising incorporation of technology to elevate both the quality and efficiency of products.”—Qazi Taimoor Ali
RIGHT: The Green Products team used a prime coat on this cycle track prior to paving the asphalt lift.
Qazi Taimoor, HSE engineer at GSPD, shared the Green Products team typically uses a geogrid material like Triaxial or Biaxial, as specified by the consultant, to stabilize the base when paving on a sand subbase.
FROM ASPHALTPRO STAFF
Green Solutions Projects Development (GSPD), founded in the United Arab Emirates in 2011 and a known member of the Paradise Group, performs major and minor asphalt projects, highway construction, bridges, flyovers, earthwork, and more, with about 70% of their work being asphalt paving. Some of the higher profile projects the company has been involved with include the Abu Dhabi Island at Grade Cycle Track Network Package 1 and 2, and the Saadiyat Infrastructure Public Realm & Landscape Construction Works Package 2 for the Beach & Marina Districts. The health, safety and environment engineer at Paradise Group, Qazi Taimoor Ali, shared Green Solutions has seen rapid growth due to efficient management and strong HSA and technical teams.
“In the city of Abu Dhabi, over 80% of asphalt paving are newly constructed in the last 15 years,” Taimoor said. “The most common types of used flexible pavement include hot mix asphalt (HMA) with pavement categorized into light traffic, medium and heavy traffic pavement based on the intended traffic use.
“Abu Dhabi is known for several things, including its impressive road network. This road network is extended to every corner of the Emirate, connecting different geographical areas. It is designed considering the increasing traffic congestion in the Emirates. Abu Dhabi’s construction sector experienced notable growth, with a 13.1% increase in 2023 compared to the previous year, reaching over AED 97 billion, marking its highest performance in a decade.”
Astec revolutionized the paving industry with the introduction of the Shuttle Buggy, and now the SB-3000 sets a new standard in material transfer vehicles. Effortless maintenance, unmatched performance, and four steering modes for ultimate agility keep paving seamless. Experience groundbreaking innovation with the patented Ground Crew Control Station for the ultimate user experience and protection. The SB-3000 isn’t a machine, it’s a revolution in material transfer, built on Astec’s legacy of industry firsts.
T A N K
C O N T R O L
S C R E E N
B O O S T E R
P U M P
C O N T R O L
S C R E E N
H
E A T E R S P E C I F I C A T I O N S : P A N E L S P E C I F I C A T I O N S :
S i z e s r a n g i n g f r o m 1 0 m i l l i o n B T U o n u p
S k i d - m o u n t e d a n d f u l l y p l u m b e d .
S i t e g l a s s i n d i c a t o r .
A u t o m a t i c c o n t r o l s .
W e b s t e r / P o w e r F l a m e c o m b i n a t i o n b u r n e r .
F u l l y m o d u l a t i n g b u r n e r .
L a r g e c o i l d i a m e t e r .
A S M E s t a n d a r d s .
D o u b l e - p a s s d e s i g n .
O p t i o n a l s t a c k - m o u n t e d e c o n o m i z e r .
P r e - w i r e d a n d f a c t o r y c o n t r o l p a n e l .
H e a v y d u t y 1 / 4 ” s h e l l w i t h c e r a m i c f i b e r
b l a n k e t .
M o n i t o r c a p a b i l i t y w i t h r e m o t e s t a r t / s t o p
a c c e s s .
C o l o r f u l u s e r - f r i e n d l y t o u c h s c r e e n
c o n t r o l .
R e m o t e c o n t r o l f r o m y o u r p h o n e o r
t a b l e t . T e x t / E - m a i l a l e r t s f o r f a u l t s o r
i n f o r m a t i o n .
O n - S c r e e n a n d r e m o t e r e s e t o f f a u l t s .
G r a p h i c a l f l a m e s i g n a l i n d i c a t i o n .
U p t o 6 l i q u i d a s p h a l t t a n k s .
( T e m p e r a t u r e a n d L e v e l )
D i s p l a y o n M a i n S c r e e n . ( o p t i o n a l )
U s e r - c o n f i g u r a b l e f e a t u r e s .
U p t o 4 b o o s t e r p u m p s . ( o p t i o n a l )
U p t o 1 0 a d d r e s s e s t o r e c e i v e a l e r t s .
N u m e r o u s A l e r t O p t i o n s A v a i l a b l e .
5 2 1 O l d S e v e n M i l e P i k e
S h e l b y v i l l e , K Y 4 0 0 6 5
s a l e s @ R e l i a b l e A s p h a l t c o m
8 6 6 - 6 4 7 - 1 7 8 2