Milestone Celebrates
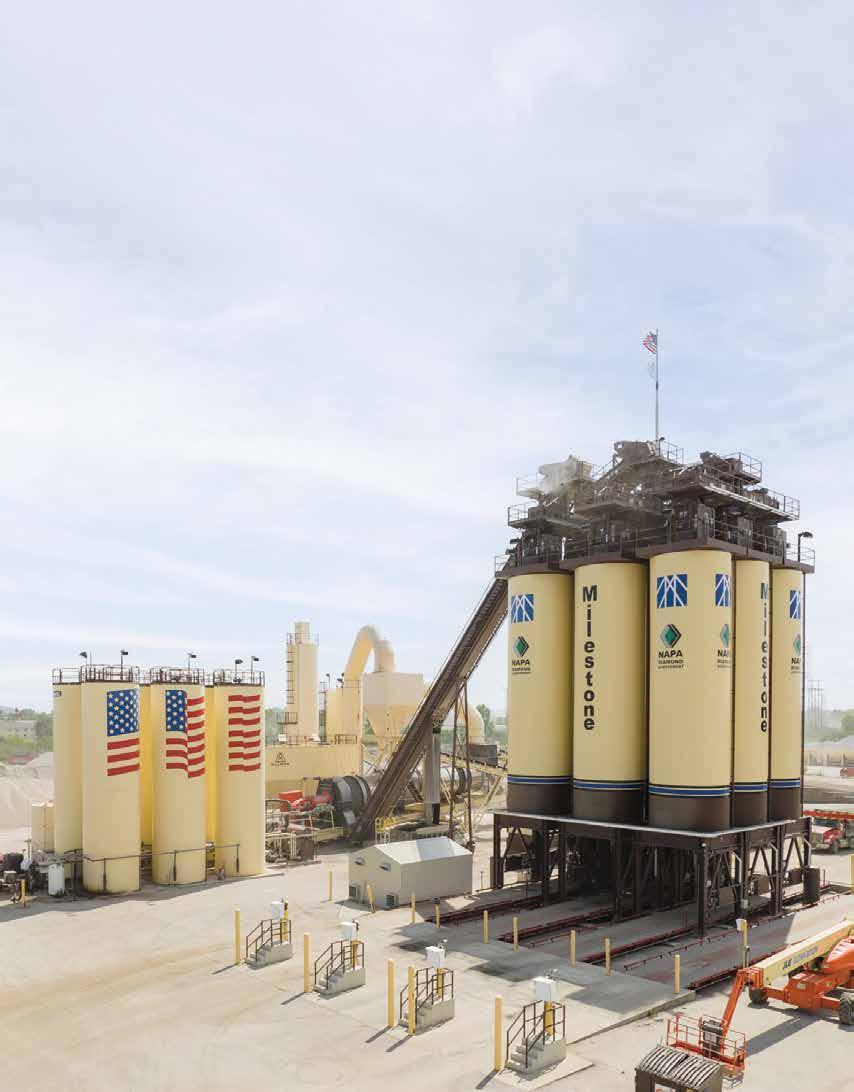
• Bituminous Paves FedEx with Precision
• CSI Takes SDX Control of Innovation
• 5 Ways to Pay for Plant Controls
• Step Up to Burner Efficiency
• 2024-2025 Training Guide
• Bituminous Paves FedEx with Precision
• CSI Takes SDX Control of Innovation
• 5 Ways to Pay for Plant Controls
• Step Up to Burner Efficiency
• 2024-2025 Training Guide
Astec paves the way for sustainable, innovative asphalt plants. The new IntelliPac Moisture System is a revolutionary solution that integrates seamlessly with Astec control systems. This provides unparalleled, real-time visibility into virgin aggregate moisture content. IntelliPac empowers operators to optimize mix design, minimize energy consumption, and reduce environmental impact. With Astec, you get superior asphalt production – better for the environment, better for your business.
CWMF has been a trusted company in the stationary and portable asphalt industry for decades.
As a full-service manufacturing company, we engineer all of our products to order, allowing us to serve as a full-service, end-to-end provider of asphalt plant solutions. We have the machinery and equipment you need, and a confident team working together to make this happen. Whether it’s cold feed bins, drums, silos, or the entire plant, we get the job done in-house, from start to finish. This provides an exceptional experience for our customers, and for the dedicated team standing behind their products. We work hard not only to retain our reputation but to stay current on the latest industry trends and technologies.
Contact us for a site evaluation, expansion project idea, new equipment upgrades, or to discuss your custom needs.
6 – Control Your Most Successful Operation
SAFETY SPOTLIGHT
8 – Safe Footwork
J. J. Keller and Juno Jones collaborate to provide safety footwear for Women in Construction
From J. J. Keller
STREET SMARTS
10 – Stop Struck-Bys By Bill
Stanley
14 – SDX Trial Success
Testing screed types side-by-side in the badlands of North Dakota proves industry can increase density, improve ride with patterned screed, innovation, best practices.
By Sandy Lender
PRODUCER PROFILE
22 – Paving Anniversary Milestone From building roads to preserving icons: 30 years of Milestone Contractors By Zoe Buhl
58 – AEM Continues Cross-Country Tour From AsphaltPro Staff
66 – International Installation From Terex Corporation
It’s hardly controversial to suggest every asphalt plant keep its controls system(s) up to date. With the growing number of sensitive parameters asphalt producers track and report to make environmental product declarations (EPDs) possible, it makes sense that fine-tuned controls are on board. Every part per million matters and you’re likely being asked to account for them. All of them.
Beyond the mind-numbing over-greening we’ve been subjected to as of late, there are basic safety and operational controls to investigate at the plant and in the field. In this month’s issue, we see how implementing innovations as well as intelligent controls assisted Central Specialties Inc. for a national parks project (see page 14). Detroit Stoker Burner gives us some backto-basics for burner sizing and controls at the plant (see page 38). And the team at Stansteel offered five tips to see a quick ROI when installing or updating controls at the plant (see page 36).
Let’s focus on the plant for a minute. Consider the wisdom of monitoring tank levels and temperatures. The last thing you want to have happen to your liquid asphalt cement (AC) heating element is coking. With a robust controls system, you set an alarm on your tank that lets you know when you’re approaching a low-level situation before it becomes a problem. The alarm sounds and shows you where the problem is occurring.
Some systems tell you how to solve it.
With the plant-of-the-future we’re being promised, some system someday will go ahead and resolve the issue without a human in the control house. While that concept raises all the red flags for safety in my mind, there are people excited about it as an answer to workforce shortages.
Hopefully no truck drivers will be relying on the machines at that point. But let’s talk about the drivers and loadout systems for a minute.
Your controls have probably focused on improving loadout and ticketing for years now. Additional safety features have recently offered more ways to ensure drivers position different types and sizes of haul trucks perfectly beneath the appropriate silo for loadout in the most advantageous method to prevent material segregation and windshield shots.
Once again, it’s not earth-shattering for me to suggest these systems as upgrades to your operation. Implementing and integrating updated controls at the asphalt plant gives you your best opportunity for an efficient, safe and successful operation. With winter down season right around the corner, now may be the right time to investigate upgrades and options.
602 W. Morrison, Box 6a Fayette, MO 65248 (573) 823-6297 • www.theasphaltpro.com
GROUP PUBLISHER
Chris Harrison chris@ theasphaltpro.com
PUBLISHER
Sally Shoemaker sally@theasphaltpro.com (573) 823-6297
EDITOR
Sandy Lender sandy@theasphaltpro.com (239) 272-8613
DIGITAL EDITOR
Sarah Redohl sarah@theasphaltpro.com (573) 355-9775
MEDIA SALES
Cara Owings cara@theasphaltpro.com (660) 537-0778
ART DIRECTOR Kristin Branscom
BUSINESS MANAGER
Stay Safe, Sandy Lender
Susan Campbell (660) 728-5007
AsphaltPro is published 11 times per year. Writers expressing views in AsphaltPro Magazine or on the AsphaltPro website are professionals with sound, professional advice. Views expressed herein are not necessarily the same as the views of AsphaltPro, thus producers/contractors are still encouraged to use best practices when implementing new advice.
SUBSCRIPTION POLICY: Individual subscriptions are available without charge in the United Sates, Canada and Mexico to qualified individuals.
One year subscription to non-qualifying Individuals: United States $90, Canada and Mexico $125.00. For the international digital edition, visit theasphaltpro.com/subscribe/
The future is connected. That’s why we’ve designed the ALmix Insignia Control System (ICS) around the power of high-speed Ethernet communication. An ethernetconnected facility means our team of programmers have complete visibility into your plant equipment and motor control center for diagnostics and remote troubleshooting. View and control data from your asphalt plants like never before. The Insignia Cloud Platform provides access while you are at the plant, in the office, or on the go. Critical, real-time, plant information is at your fingertips when you need it.
DON’T LET YOUR EXISTING ASPHALT PLANT CONTROLS KEEP YOU GUESSING:
The Insignia Control System is available on all new ALmix Asphalt Plants and is also available for existing plant control upgrades.
SCAN HERE TO LEARN MORE OR TO SCHEDULE A DEMO
FROM J. J. KELLER
J.
J. Keller & Associates, Inc., Neenah, Wisconsin, announced in August a strategic collaboration with Juno Jones Safety Boots, Philadelphia. This alliance aims to elevate workplace safety and comfort for workers across various industries.
Juno Jones makes award-winning safety footwear by working people, for working people. Founders Emily and Ryan Soloby, with roots in the trucking and footwear industries, created Juno Jones after they noticed a gap in the safety footwear market around issues of inclusivity. The brand launched with women’s footwear made especially for female foot measurements and style, and its viral popularity quickly grew the brand to include men’s durable safety footwear built for all day comfort.
Juno Jones Safety Boots has won the National Safety Council Award as a safety shoe company.
“The combination of Juno Jones, with roots in trucking and adjacent industries, and J. J. Keller & Associates, Inc., serving the safety needs of these industries, was a natural fit,” said Juno Jones CFO Ryan
Soloby. “We look forward to helping J. J. Keller’s customers stay safe and comfortable, even when they're on their feet all day.”
J. J. Keller, a family-owned company, has served the safety market since 1953, with a purpose of protecting people and the businesses they run. Today, the company serves more than 500,000 companies across North America, who rely on J. J. Keller’s expertise to safeguard workers, reduce risk and build operational confidence.
“At J. J. Keller, we’ve conducted studies on the challenges of finding safe, well-fitting PPE in women’s sizing, and it is clearly a challenge for those working every day on job sites and those who purchase PPE for their companies,” said Lisa Karpinski, executive vice president of marketing at J. J. Keller. “We were inspired by Juno Jones’ focus on inclusivity in safety footwear. And we’re excited to offer both the Juno Jones women’s and men’s lines.”
In addition to the new Juno Jones boots, J. J. Keller offers a wide selection of quality, comfortable personal protective equipment under its proprietary SAFEGEAR®️ line of PPE. SAFEGEAR offerings include high-visibility apparel and accessories; safety gloves; hard hats and helmets; safety glasses and goggles; and hearing protection, in both traditional and women’s sizing.
You can shop J. J. Keller and Associates’ products, including the new Juno Jones line, at www.jjkeller.com. To learn more about Juno Jones and its mission of diversity in safety, go to www.junojones.com.
The all-new Blaw-Knox PF-7110C tracked paver combines all-around visibility, ease of operation and a new powerful Cummins 235hp engine for the ultimate in dependability and efficiency. The turbocharged diesel engine provides more torque and less weight in a more compact package, letting you power through steep grades with confidence. Coupled with the proven Blaw-Knox durable track and automatic tensioning system, the 7110C ensures smooth and consistent paving power on any terrain.
With over 90 years of proven Blaw-Knox paving technology, the PF-7110C delivers all the power you need and more.
BLAW-KNOX, THE LEGACY LIVES ON.
Hard-won know-how for the next generation
Bill Stanley can be found in a variety of roles on his paving crew, but when traffic control on a project is particularly complicated, Stanley often opts to take on that role.
BY BILL STANLEY
Igot hit by a car the other day.
We were paving a country road just off a busy highway that’s a popular shortcut for area commuters—despite being barely wide enough for two cars at 18 feet wide. Not only is the road narrow and busy, but there’s also an S curve right at the top of a hill
As I often do on jobs with complicated traffic control, I was directing traffic when a driver going 40 in the 25 mph zone struck me. Whether or not the driver noticed (though I’m sure he heard the thump), he certainly didn’t stop! Thankfully, my years of experience have taught me which drivers require extra attention and I’d backed up further than I otherwise might have, so he only grazed my wrist.
Anyone working in our industry for a while probably has at least one close call story like this. Struck-bys are a leading cause of injury and death in our industry, and it feels like it’s only getting worse. It used to be that people wouldn’t pay attention to anything beyond their bumper; now, they barely pay attention to anything beyond their phone.
That’s why teaching your crew how to function safely on the job site is one of the most important lessons that can be taught—because it’s literally a matter of life and death.
Struck-by incidents are the second leading cause of death among construction workers, accounting for 150 deaths and 14,000 nonfatal construction sector injuries in 2020, according to the Center for Construction Research and Training (CPWR).
If I had to reduce all our safety training down to a single sentence, it would be, “Everyone has to watch everyone else’s back.” This is especially true for the new member of the crew. It isn’t that the new person on the crew lacks situational awareness, but they’re in a new situation where they don’t yet know all the threats to be aware of. And, believe me, there are a lot of threats to be aware of on our job site because there are so many moving parts!
That’s why we try to pair new crew members with experienced crew members who have strong situational awareness. We have a few people on our crew who always seem to be in the right spot at the right time. No matter what the circumstances of the job, they just know where to be and what’s around them. That’s the person I try to plant the new person next to.
NO ONE SHOULD EVER WALK BETWEEN THE PAVER AND A BACKING TRUCK!
We treat our jobs like an assembly line, the same way we unloaded groceries in our house when our kids were little. Everyone has their place in the line to get the job done. If I can put the new crew member between two workers with strong situational awareness, all the better!
We don’t have a formal toolbox talk every morning, but identifying hazards and communicating them to the whole crew is always the first thing we do at any job site. Maybe we’re paving around a corner and the cars are traveling fast. Maybe there are overhead wires or tree branches. We point out all the warning spots. Not only does this make everyone aware of the job’s threats, but it also sharpens that sense of situational awareness.
Although the traveling public is certainly a threat, so is the heavy equipment operating within the job site. A common trait among nearly all new crew members is the tendency to take the fastest route from A to B, even if it’s through a no-go zone.
In our industry, being between the paver and a backing truck is one of those no-go zones. New crew members want to be helpful, so they’ll go clean out the back of a truck or the front of the paver, and this has to be trained out of them. No one should ever walk between the paver and a backing truck!
New crew members also love to walk between machines and buildings. We train that out of them, too. I was once on a skid steer in front of a garage ripping out a tree stump when I hit a hornets’ nest. I got stung and my foot slipped off the brake. It took all of two seconds to find myself busting into the garage!
Such an event could happen to anyone on any job. What if the operator in that machine sneezes or coughs, what if they have a heart attack or have to itch their foot? You have to be prepared for the unexpected.
If you do find yourself working near heavy machinery, we train our workers to work in front of the machine (at a safe enough distance) so the operator has a good view of them. I don’t care what fancy technology might be on that machine—cameras, sensors, whatever—no one works behind or to the side of our equipment.
On our crew, training never stops. I imagine this is true on every crew, because the job site is always changing. For example, 10 years ago we had one small mill and we used it once a week. Now, we’re milling every day. Material formulas change, and new formulas re-
Hard-won know-how for the next generation
quire different laydown procedures. Each of these changes to the job present new safety considerations. There’s no “graduation day” for training.
We train on the job, all day, every day. However, we also try to train wisely based on the conditions of the job. I would never train anyone on something new on a job like the one where I recently got hit. On a job like that, I would (and did) tell any new member of the crew to stay on the shoulder, well away from the cone line. They’re just not ready for that.
Instead, I’ll wait until we’re paving a parking lot that isn’t very busy to train new skills. Somewhere the conditions are easy to control, somewhere there’s plenty of space between them and the rest of the crew. I want to teach a new operator on a football field, not in a shoebox!
Despite all the years I’ve spent on job sites, despite the sixth sense I’ve honed, I still got hit the other day. It isn’t the first time I’ve been hit, and it isn’t even the scariest struck-by near miss I’ve witnessed.
That title belongs to a job on Route 9 in New York when a car ripped down four barrels to breach our construction zone going 60 mph, punched the gas and exited our construction zone doing 80 mph on the grass. He missed my flagger by two inches and crashed a few miles down the road. We are very lucky nobody was killed.
It’s important to remember that no matter how many years of experience you may have on the job site, an event like this can happen at any moment. Even with a well trained crew and exceptional traffic control, we cannot always control the traveling public. A key part of any training program is teaching your crew to expect the unexpected, remain aware of their surroundings, and watch each other’s backs.
Bill Stanley owns American Pavement Specialists, Danbury, Connecticut, with his wife, Colleen. Stanley has more than 50 years of experience in the asphalt industry.
• Automatic bintop and batch control with full manual backup
• Drag slat and bintop zero speed alarm
• High silo alarm & shutdown
• Silo inventory output pulse provides silo level monitoring
• Baghouse pulse or rotor control
• Baghouse auger zero speed alarms
• High hopper alarm
• Important pressure monitoring and control
• Internal scale calibration to meet or exceed state specifications, fast and simple
• Dual scale capabilities - alarms when scales are out of calibration
• Scale bypass feature
• Optimal - quick calibration check capabilities
• Superior filler weigh pod control
• RAS belt scale or weigh feeder control volumetric
• Liquid additives of all types: Anti - strip, rejuvenators, warm mix, etc.
• Calibration accuracy to 2/ 10 of 1%
• Back up A C meter using the pump
• Automatic A.C. line prefills
• Individual A C on/off times for each mix design, reducing waste
• Mass flow meter and even multiple meters
• Material no-flow alarm
• Automatic bin vibrator control
• Individual feed stop/start times to reduce waste
• Calibrate feeder in minutes
• Feeder zero speed indication
• Standard 16 feeder bin control
• Multi-point feeder calibration to improve gradation accuracy
• Pre - calibrate multiple materials per feeder
The Accu-Track AdvantageTM, using patented technology and techniques, was developed over the past 45 years from an accumulation of installations on all brands, types and manufac tures of asphalt plants.
The new user-friendly interface is made for the modern era of fast communication, remote accessibility and SAFETY.
Testing screed types side-by-side in the badlands of North Dakota proves industry can increase density, improve ride with patterned screed, innovation, best practices.
BY SANDY LENDER
By paving in echelon up and down the hills of Highway 85 in the North Unit of Theodore Roosevelt National Park (TRNP), the award-winning team of Central Specialties Inc., headquartered in Alexandria, Minnesota, tested densities and smoothness achieved behind the SDX screed plate design from Caterpillar alongside the traditional SE60 screed plate design. The crew performed this 10.214-lane-mile build in spring of 2024, achieving an average density improvement on the SDX lanes of 1.7% directly behind the screed and 1.2% after the finish rollers. The overall smoothness results paint a sustainable picture for the asphalt industry.
“We increased the density by 1 to 1.5% and ride by 10% behind the paver equipped with the SDX screed compared to the traditional one,” Bryce Wuori said. He’s the pro-
prietor of Pavewise, headquartered in Bismarck, North Dakota, and was hired by Caterpillar to serve as a consultant on the project. “We saw a 25% decrease in standard deviation. The 10,000-foot view on this project was innovation and technologies that are pushing the industry forward can be proved with this data.”
The Theodore Roosevelt National Park is divided into three parts in western North Dakota, which include a South Unit and Elkhorn Ranch Unit. CSI paved in the North Unit in the spring of 2024.
Not only was the team using the innovative SDX screed plates on one of the pav-
ers, but they also employed thermal mapping, intelligent compaction (IC) and multiple data-collection technologies to assess quality control/quality assurance (QC/QA) along the way.
One of the newer tools on hand was the GroundTruth system from Pavewise, which helped monitor environmental conditions in real time. This solar-powered, mini weather station was situated at the project site to communicate with the Pavewise software when inclement weather was rolling in. It also documented conditions for the team. For example, during southbound paving on May 29, the average ambient temperature was 64°F with an average wind speed of 9 miles per hour (MPH). That night, the area experienced 1.2 inches of rain. During northbound paving on May 30, the average ambient temperature was 57°F with an average wind speed of 11 MPH.
The CSI team executed paving both lifts of more than 12,000 total tons along the 10+ lane miles in two days.
The TRNP project in McKenzie County required paving 10+ total miles from the park entrance to County Road 30 (23rd Street NW). The crew was responsible for grading, aggregate base, hot-mix asphalt (HMA), culverts, box culvert, a pedestrian walking trail, the retaining wall, signage, pavement markings and incidentals. The mix design used on the project was North Dakota’s FAA45, which uses a PG64-34H binder. The CSI team produced the mix at its parallel-flow drum plant from CWMF, Waite Park, Minnesota, which was located outside Watford City. Typical production was 610 tons per hour with a propane-fueled Hauck Eco Star 200 burner. The average mix temperature out of the trucks was 306°F.
Belly-dump, live-bottom and tandem trailers delivered material ahead of two Weiler windrow elevator pickup machines, which in turn fed the two Cat AP1055F pavers with SE60 V-XW screeds vibrating at 1,200-1,400 VPM, and working in echelon.
“The paving widths were 18 feet behind the traditional screed AP1055 and 20 feet with 4-foot slough behind the 1055 with the SDX screed,” Wuori shared. See Figure 1 for more detail.
The base course was 2 inches compacted; the wearing course 1.5 inches compacted. Longitudinal joints were created with the notch wedge joint system from Willow Designs LLC, East Berlin, Pennsylvania. Jerod Willow, proprietor of Willow Designs, spoke to the efficacy of using a joint-making system with a vibrating screed.
“Screed vibration has no effect on the notch wedge device or produces no damage to the joint itself,” he said. “Willow Designs actually has options for electric vibrators on the notch wedge devices themselves because I believe using screed vibration is a good thing to a certain extent.”
Willow expanded on his theory and offered a tip for vibe settings. “Having screed vibration set at a moderate and manageable speed is key to help manipulate, turn and lock the aggregate in the asphalt mix together as it is protruded under the screed. A way to find manageable screed vibration per minute (VPM): stand a shovel on the catwalk of the
Readers may remember the introduction of the patterned screed and its “conductor plate” installation system from the January 2021 issue of AsphaltPro Magazine. You can review that introductory walk down Memory Lane at this link, https://theasphaltpro.com/ articles/axenoxs-oxclaw-screed-systemcreates-buzz-in-asphalt-industry/ and see how early adopters Valley Paving and Shilling Construction used the system on projects at these links: https:// theasphaltpro.com/articles/patternedscreed-plate-smooth-mat/ and https:// theasphaltpro.com/articles/shillingconstructions-proven-screed/.
paver screed. If it vibrates off and falls down, the VPM is too high.
“I believe too high screed VPM just causes excessive wear and tear on equipment with minimal results in increased mat density,” Willow continued. “Think about it like this: we are trying to keep the screed of the paver planted to the ground to assure a good ride quality of the pavement we are placing, but now using vibration at a high VPM is like having the screed of the paver do all these ‘micro jumps.’ Think about how vibration impacts work on roller drums. High VPM on the screed seems counterintuitive. From a highly technical standpoint, paver screeds should oscillate to be effective and produce minimal deviations of mat quality as far as smoothness and rideability.”
To assess mat temperature behind the screeds, the crew employed paver-mounted thermal profiling (PMTP). The SDX-equipped paver employed the Caterpillar thermal camera system, and it collected data showing the average lot temperature behind that screed was 267°F. It also showed a low to moderate incidence of thermal segregation. The traditional paver employed the MOBA thermal camera
“FROM A HIGHLY TECHNICAL STANDPOINT, PAVER SCREEDS SHOULD OSCILLATE TO BE EFFECTIVE AND PRODUCE MINIMAL DEVIATIONS OF MAT QUALITY AS FAR AS SMOOTHNESS AND RIDEABILITY.”—JEROD
WILLOW
system, and it collected data showing the average lot temperature behind the traditional screed was 259°F. It also showed a moderate to high incidence of thermal segregation. Wuori indicated: “Thermal consistency behind the SDX produced a lower thermal segregation index than the traditional screed.”
He explained: “The 3D textured surface of the SDX screed kneads the aggregate together, forcing it to move into position. This action develops more density and thermal consistency behind the screed with this manipulation.”
Multiple steel drum Cat rollers equipped with intelligent compaction (IC) and Versa-Vibe worked in breakdown, intermediate and finish positions to achieve compaction. The IC used included a CB-460 display with Trimble Systems, VRS positioning data and WorksOS. Each of these provided the operator with a means to track passes, temperatures and impacts-per-foot to ensure the highest quality of rolling was being achieved on the project.
For the SDX-equipped paver, the rollers were a Cat CB15 in breakdown position and another Cat CB15 in the intermediate position. For the traditional-screed paver, the rollers were a Cat CB66 in breakdown position and another Cat CB66 in the intermediate position. Both paving lanes shared a Cat CB15 in static mode in the finish position.
Paving team Bradley and Jill O’Brien are a married couple who handled compaction behind the SDX screed plate. Jill operates the breakdown roller while Brad operates the intermediate and finish.
They shared that the mat behind the SDX, “takes fewer passes to get density compared to the conventional screed; less water consumption. When following a rubber-tire roller, the turn around spots are smoother and
all-around marks less visible. The SDX screed also prevents less mat tear marks from the steel rollers.”
Using IC was a benefit for the O’Briens as well. They explained the system allowed them to see how many passes they’d completed and where they’d already rolled. “Just like flying an airplane at night—you know where the runway is.”
With compactors working on the rolling pattern, the team could start gathering density data. They used a NoNuke density gauge from Instrotek Inc., Research Triangle Park, North Carolina, to collect 360 points—97 of those behind the screed—before rolling. They used the PaveScan 2.0 RDM from Geophysical Survey Systems Inc., Nashua, New Hampshire, to
LEFT: The CSI crew used paver-mounted thermal profiling (PMTP) to assess mat temperatures immediately behind the screeds. The SDX-equipped paver employed the Caterpillar thermal camera system, and it collected data showing the average lot temperature behind that screed was 267°F. It also showed a low to moderate incidence of thermal segregation. Consultant Bryce Wuori shared: “Thermal consistency behind the SDX produced a lower thermal segregation index than the traditional screed.” RIGHT: The team gathered thousands of data points during and after paving to prove the award-winning team of Central Specialties Inc. executed a stellar roadway project for the Theodore Roosevelt National Park with both traditional and patterned screed plates. The data also showed overall smoothness results that paint a sustainable picture for the asphalt industry, proving the innovative use of the SDX patterned screed offers a quality option for contractors.
LEFT: The crew set up Pavewise’s GroundTruth system, which helped monitor environmental conditions in real time. Here you see the solar-powered mini weather station, which communicated with the Pavewise software to alert the crew when inclement weather was rolling in and documented weather conditions. RIGHT: Thanks to the GroundTruth system from Pavewise, the team collected environmental conditions data during the project. On May 29, while paving southbound, the average ambient temperature was 64°F with an average wind speed of 9 miles per hour (MPH). That night, the area experienced 1.2 inches of rain. The seasoned professionals at CSI have excellent stockpile management practices and know how to handle a heavy rain event. Paving northbound on May 30 saw an average ambient temperature of 57°F with an average wind speed of 11 MPH and consistently good data points in the northbound lanes.
gather 19,609 DPS data points—9,932 of those behind the SDX screed. An operator from Robison Grinding & Profiling LLC, Gillette, Wyoming, drove the SSI Zero-Speed Inertial Profiler along the project’s base and surface/wear courses.
The results showed a high-quality job. Starting with the non-nuclear density gauge results, Wuori reported the average density directly behind the SDX screed was 91.5%; the average behind the traditional screed was 89.8%. Notice that’s not a bad number. The CSI paving crew was handling mix delivery and paving with best practices. But they were seeing a 1.7% density increase immediately behind the screed with the patterned plate.
Check out this article on the use of zero-speed inertial profiling: https://theasphaltpro. com/articles/mississippinchrp-10-106-testing-showsrepeatability-of-zero-speedinertial-profiling/
John Fales, CSI paving superintendent on the project, said, “This paving crew is like a well-oiled machine. They take pride in the work they do every day and pave some of the best asphalt roads in the Midwest.”
The non-nuclear density gauge numbers behind the finish roller told a similar story. The CSI paving and rolling train was knocking it out of the park, achieving 93.6% average density in the traditional-screed-plate lane. They hit an average density of 94.8% in the SDX lane, which is a density increase of 1.2%.
Moving to the DPS data on the SDX section, both northbound and southbound driving lanes offered a dielectric value of 4.50 with a standard deviation of only 0.11. This converts to a density of 94-94.5%.
“To CSI’s credit, this was the lowest STD ever collected with the PaveScan DPS unit on an asphalt surface,” Wuori shared. “A decrease in standard deviation equals more consistent average densities. A lower standard deviation is better for percent-within-limit (PWL) projects and decreases the chances of lower/higher cores or dropping the average of a lot down to less of a pay factor.”
The DPS data on the traditional section, both northbound and southbound passing lanes, offered a dielectric value of 4.40 with a
“TO CSI’S CREDIT, THIS WAS THE LOWEST STD EVER COLLECTED WITH THE PAVESCAN DPS UNIT ON AN ASPHALT SURFACE.” —BRYCE WUORI
behind the SDX screed failed and only one of the cores behind the traditional screed failed to get above the required 92%. This testing showed a 0.44% density increase behind the SDX screed.
What the pilot project on Hwy. 85 showed is the use of innovation and best practices brought a slew of data to the industry. This data proves the innovative use of the pat-
terned screed plate, PMTP and IC can offer improved densities and a smoother ride for the taxpayer. When asphalt pavements have a solid and sound foundation, they last longer and offer not only a quality driving experience for the end user, but also a more sustainable option for agencies/owners. The use of such innovative technologies is a win all the way around.
standard deviation of 0.15. This converts to a density of 93.5-94%.
The zero-speed inertial profile data is in Table 1 below. Wuori summarized the results, showing the driving lane average difference—with the SDX—was 25.77 with a decrease in roughness of 2.61. The passing lane average difference—with the traditional screed—was 23.26. “This shows us a 10% improvement with the SDX,” he shared.
Despite its destructive nature, the team had to take some cores—11 random cores behind the SDX screed, 11 random cores behind the traditional screed and 10 randomly along the joint. The engineers Kadramas Lee & Jackson shared that none of the cores
with SDX screed plate NB driving 38.89 with SDX screed plate SB driving 39.25 with traditional plate NB passing 38.88 with traditional plate SB passing 38.5 DIFFERENCE IN IRI Change with SDX screed plate NB driving 26.06 with SDX screed plate SB driving 25.48 with traditional plate NB passing 20.16 with traditional plate SB passing 26.16
BY ZOE BUHL
TThis year, Milestone Contractors proudly celebrates its 30th anniversary, marking three decades of growth, innovation and commitment to quality in the construction industry. A significant facet of Milestone’s legacy is its long-standing relationship with the iconic Indianapolis Motor Speedway (IMS). This partnership has led to innovative pavement preservation strategies, ensuring the track remains in top condition
for events like the Indianapolis 500. Today, Milestone Contractors stands as a testament to continuous growth and excellence.
Milestone Contractors has a rich history marked by strategic acquisitions and growth. The company traces its roots back to 1954 with the founding of Columbus Paving Company, which merged with Mesh-
berger Stone Company to form Meshberger Contracting, Inc. Over the years, the company expanded through strategic acquisitions, starting with Lucas Paving Company in 1971. In 1970, the Fehsenfeld family purchased the company, renaming it Contractors United Incorporated (CUI) and incorporating it into The Heritage Group (THG) family of companies. Founded in 1930, THG is a fourth-generation family-owned
Milestone and its partners have played a large role in preserving the iconic Indianapolis Motor Speedway (IMS) track, home of the Indianapolis 500. In 2004, THG’s research and development lab Heritage Research Group (HRG) developed a pavement rehabilitation strategy for the pavement to last 15 years in conjunction with Milestone and Grady Brothers Asphalt. This year celebrates the 20th anniversary of the most recent IMS paving.
When the track was paved 20 years ago, US Aggregates® provided all the aggregate for mixes, while Asphalt Materials, Inc. (AMI) produced all the liquid asphalt.
Through the present day, all involved in the preservation of the IMS track have worked closely with the IMS to determine the best strategy to extend the pavement life while maintaining a safe racing surface.
The pavement of a racetrack is vastly different than a typical HMA project. Smoothness and friction is important to both INDYCAR and NASCAR, but NASCAR consistently challenges the pavement surface at the IMS due to their higher weight and higher tire pressures.
business that manages a diverse portfolio of companies specializing in construction and materials, environmental services and specialty chemicals.
Following additional acquisitions through the 1990s, CUI, Fauber Construction Company and Astro Paving united under the name Milestone Contractors, LP in 1994. The company continued to expand in the 2000s and 2010s, acquiring Indiana Asphalt, Inc., Walsh & Kelly, Berns Construction and Lica Construction. Recent years have seen Milestone further solidify its presence with acquisitions like Yates Construction in 2018 and the assets of RA Myers, Inc. in 2021, in addition to the Speedway and Primco acquisitions of 2022. This year marks the 30th anniversary of Milestone Contractors’
name, and Milestone continues its steadfast dedication to quality within the construction industry.
Milestone has nine principal offices, 19 hot-mix asphalt plants and 15 concrete batch plants strategically located throughout Indiana, and it employs about 2,500 people during construction season. The company offers a comprehensive range of construction services, focusing on asphalt and concrete paving. It also specializes in bridge construction and site development, handling projects of all sizes with a commitment to safety and sustainability. Milestone Contractors is dedicated to delivering high-quality, innovative solutions The Milestone Way, with a focus on trust, quality, commitment and passion in every project. Today, Milestone continues
to grow within the Heritage Construction + Materials (HC+M) division of THG.
“Milestone Contractors is proud to serve communities across Indiana, delivering high-quality solutions to enhance local infrastructure,” said Milestone Chief Operation Officer CJ Potts. “Our team’s commitment to innovation has made a significant impact, fostering community development throughout the state.”
Milestone is also an active member of the National Asphalt Pavement Association (NAPA) and the American Concrete Pavement Association (ACPA) and received many awards through both organizations in 2023. Six Milestone projects received the ACPA’s Excellence in Concrete Award in 2023, including three projects at the Indianapolis International Airport, and six additional projects also received NAPA’s Quality in Construction Awards. In 2022 Milestone was also awarded the Indiana Constructors, Inc. (ICI) Gold Safety Program Award.
Notedly, Milestone and its partners have played a large role in preserving the iconic Indianapolis Motor Speedway (IMS) track, home of the Indianapolis 500. In 2004, THG’s research and development lab Heritage Research Group (HRG) developed a pavement rehabilitation strategy for the pavement to last 15 years in conjunction with Milestone and Grady Brothers Asphalt. This year celebrates the 20th anniversary of the most recent IMS paving, marking a significant achievement in pavement rehabilitation, preservation techniques and innovation.
The paving history at the IMS dates to the 1930s, and Grady Brothers took care of the asphalt paving from then until 2004. HRG was involved in the 1988 overlay, and by 1995, the organization was not only designing the mix but also developing the pavement rehabilitation strategy.
By 2004, Milestone sister companies were heavily involved in the materials production in addition to HRG. When the track was paved 20 years ago, US Aggregates®️ provided all the aggregate for mixes, while Asphalt Materials, Inc. (AMI) produced all the liquid asphalt. Milestone was responsible for making and controlling the production of the mix, and HRG developed the pavement rehabilitation strategy.
“When I was there in 2004, they were long, hard, hot days of work, but I still found myself realizing the opportunity
Milestone was given to be part of history,” said Milestone Vice President and Area Manager Scott Cornelius.
THG companies developed several innovative products near the 2004 paving that have since become widely used in the industry. One such product was J-Band®️, AMI’s void reducing asphalt membrane (VRAM) product. J-Band was applied at the eventual location of the three paving joints between lanes on the track. VRAM works to fill air joints in the longitudinal joint, the most vulnerable part of a pavement, and today, J-Band is used on highways across more than 27 states.
A rapid penetrating emulsion (RPE) was also placed in the fall of 2004 after paving. RPE is designed to reduce the permeability of the asphalt mix from the top of the pavement down by penetrating and filling air voids. Additionally, a joint adhesive produced by AMI was applied on the face of joints to provide additional joint compliance. These advancements have significantly improved the IMS’s pavement performance and durability.
Noticeable cracks did not begin to appear on the pavement until 2016, when HRG partnered with the IMS to determine the best process to fill the cracks. All hands were on deck to use squeeze bottles to fill the cracks by hand with emulsion specially made by HRG. Through the present day, all involved in the preservation of the IMS track have worked closely with the IMS to determine the best strategy to extend the pavement life while maintaining a safe racing surface.
“In everything from how the mix was produced and handled at the plant, how it was unloaded from the trucks, paved, compacted and more, we tried to be very consistent,” said HRG Quality Control Director Bill Pine. “We learned how that plays a huge role in performance over a period of time.”
The pavement of a racetrack is vastly different than a typical HMA project. Smoothness and friction is important to both INDYCAR and NASCAR, but NASCAR consistently challenges the pavement surface at the IMS due to their higher weight and higher tire pressures. Racetracks require densely compacted surfaces, and the turns require special attention to detail in paving. Not only has paving and preservation evolved to rise to the challenge in the last 20 years, but the IMS has evolved with it. The number of events and races held at the IMS has increased significantly since 2004, which causes more stress to the pavement, and scheduling can impact maintenance efforts.
Experience the industry‘s most comprehensive curriculum, all in one world-class facility.
AT THE WIRTGEN AMERICA CENTER FOR TRAINING AND TECHNOLOGY, we provide an extensive curriculum tailored to the learning needs of technicians, operators, work crews, site managers, service engineers, and service department personnel. From guardrail to guardrail and 20 inches down, our courses cover everything from aggregate production, to paving, compaction, and recycling of road materials Experience high-quality teaching from industry experts that keeps attendees in step with Wirtgen Group’s cutting edge technology.
CLOSE TO OUR CUSTOMERS
The Milestone team is always on call to ensure the track maintains its high level of quality and to react to pavement preservation strategies in real time. Milestone’s relationship with the IMS goes beyond the project itself. Milestone and HRG lead routine smoothness and friction testing and reporting and do isolated bump grinding to smooth specific high spots. The IMS has also trusted Milestone with additional paving around the track including a full reconstruction of its 2.4-mile road course in
2013. Milestone has also paved the IMS’s internal lots, roads and cart paths.
“From my perspective, there’s a long history of our relationship with the IMS, and it’s imperative to make sure it is preserved and passed on to those that follow us to maintain that relationship,” said Scott Cornelius.
Milestone’s commitment to safety and innovation has been a constant as it’s grown throughout the decades. Operating acquired companies in unison is challenging, but with the implementation of its Best Practices in 1997, Milestone grew stronger and more efficient. The Best Practices allowed the company to take strengths from each of its areas of business and implement them company-wide, resulting in consistent business practices. This led to a 75% decrease in recordable incidents from 1996 to 2004.
Milestone was also one of the first companies in the surrounding area to have Stop Work Authority (SWA). SWA is a safety program that empowers employees and contractors to halt work if they perceive unsafe conditions or behaviors. The goal is to prevent accidents and ensure a safe working
environment. Milestone also requires new hires to wear different colored hard hats than the rest of its employees to ensure crews can easily identify those who may need an extra hand. This was a groundbreaking practice when it was implemented in 2005.
Outside of its continued use of innovative materials and processes, many technological advancements globally have impacted the way Milestone does work. Computer advancements allow companies to bid more work than ever before, upgraded GPS and UTS equipment allows more efficiency in the field and hiring is done primarily online today.
Through decades of innovations, Milestone has not only expanded its footprint in Indiana but also set new standards in safety and sustainability. The company’s pivotal role in preserving the iconic Indianapolis Motor Speedway underscores its expertise and dedication to excellence. As Milestone celebrates its 30th anniversary, it continues to build on its rich legacy, driven by a passion for delivering high-quality, innovative solutions. Looking ahead, Milestone remains poised to lead the industry with its steadfast focus on trust, quality, commitment and passion in every project.
Nate Larson, construction technologist with Bituminous Roadways, said, “Our dispatchers, foremen and superintendents rely on the realtime updates and digital visualization of the scheduling software to coordinate crews, equipment, materials and up to 200 trucks daily during peak season.” For the FedEx parking lot project, the team resolved low drainage areas as soon as they were detected. When it came time to pave, the crew had confidence in a surface area that measured 282,000 square yards.
BY VICKI SPEED
The newly constructed, 217,000-square-foot FedEx Ground Distribution Center in Rosemount, Minnesota, may look like just a new place to sort and distribute packages. A little deeper dive reveals a powerful demonstration of how construction technology and data, especially when they are interconnected, can drive better project— and ultimately, product—delivery.
Asphalt paving firm Bituminous Roadways, Twin Cities, was tasked by R.J. Ryan Construction with paving 282,000 square yards of surface around the new facility—the largest asphalt parking lot project in the company’s history. The job required 204,000 tons of rock and 63,500 tons of asphalt.
From initial bid to delivery, the entire project was facilitated via a cohesive technology workflow that helped Bituminous Roadways deliver this award-winning project with efficiency, ease and accuracy.
Bituminous Roadways has long taken a strategic and transformative approach to projects. It’s a foundational principle that has kept the company at the top of the industry for more than 75 years. In today’s environment, increasingly connected technology is both integral and essential to the firm.
For the FedEx paving project, estimating software—in this case B2W Estimate—helped Bituminous Roadways do more than win the bid. Bid data went directly to the B2W performance tracking and scheduling applications to help managers establish daily field logs and assign resources according to how the job was envisioned in the bid.
“Because these systems are connected, data moves seamlessly,” explained Kim Scales, IS technology manager. “This allows us to collaborate more effectively across departments and to eliminate redundant data entry and all the wasted time and opportunity for error that go along with that.”
Data transfer efficiency continues from the field to the Viewpoint Spectrum ERP system. Labor hours, production quantities and material and equipment utilization, for example, are imported directly to the accounting system after they are recorded on daily electronic field logs.
Nate Larson, construction technologist with Bituminous Roadways, said, “Our dispatchers, foremen and superintendents rely on the real-time updates and digital visualization of the scheduling software to coordinate crews, equipment, materials and up to 200 trucks daily during peak season. The daily visibility into project progress via the performance tracking software is especially important on long-term projects where scope creep can be a concern.”
In parallel, a Bituminous Roadways survey team took a Trimble®️ SPS986 GNSS Smart Antenna rover with a Trimble TSC7 Controller running Trimble Siteworks Software for field measurements, as well as a Trimble SPS930 Universal Total Station. A Trimble R750 GNSS Modular Receiver base station was already set up on site. And, for one of the first times, a drone was added to the field survey workflow to verify subgrade and calibrate the surface conditions.
At the beginning of the FedEx project in 2022, Bituminous Roadways had invested in a drone and Trimble Stratus Software for as-builts and progress scans. Because of its scope and scale, the project became somewhat of a proving ground for the technology and its integration into the operational workflow.
Larson explained, “Initially we flew the entire site to verify subgrade was to spec (plus or minus 1/10-foot). Since we were new to the aerial data, we verified that data with the rover. The imagery aligned well with the ground survey data—and helped us find several issues, such as low drainage areas that would have caused warranty issues in the future. If we didn't have these tools to find issues early on, we would likely have delays and change orders down the road.”
He pointed to one particular condition. “Because we had the rover walking the site, we found a 2-foot grade bust on one side that ended up delaying the project about a month as we waited for a redesign. If we hadn’t caught these types of issues early on, we probably would have overrun this project by 10%. Today, drone surveys are a standard tool for most jobs,” he added.
Once the team was ready to begin paving, Bituminous Roadways shifted gears to jobsite production, also a technology enabled workflow that works in parallel with the bidding, estimating and jobsite planning.
The project team received a digital model from the customer that was then built out in AutoCAD. That model was shared with Trimble Business Center to develop the machine guidance files.
“We’ve used machine guidance solutions on our equipment for so long that I think we often underestimate the value, particularly on a large paving job,” Larson said. “It wasn’t that long ago, we'd send out two operators with a dozer and a motor grader to install the aggregate. On a project this big, we would have needed four people. Overall, I think our efficiency improvement is around 30%.”
For the FedEx job, Bituminous Roadways used a Cat 140M motor grader equipped with the Trimble Earthworks Grade Control Platform and a Cat D6T dozer equipped with the Trimble GCS900
Nate Larson explained the team verified data with a rover. When aerial imagery aligned with ground survey data and showed low drainage areas, the team was able to correct those areas immediately and avoid warranty issues later. “If we didn't have these tools to find issues early on, we would likely have delays and change orders down the road,” Larson said.
Grade Control System. The models were sent to the machines seamlessly via Trimble WorksManager Software.
Of particular benefit because of the job size was the Trimble Earthworks “autos” or automatics mode. In this case, the operator controls the machine’s speed and steering, while the Trimble Earthworks system controls the blade so that it stays on grade, allowing operators to achieve high accuracy grade at a consistent rate.
“We use WorksManager on a daily basis to transport files and just navigate to different job sites,” Larson said. “As work is completed, whether it’s laying aggregate or paving, that data is uploaded back to Trimble Business Center.” At the time, the group was also evaluating the benefits of Trimble WorksOS Software for jobsite management.
“We tested it [WorksOS] out on the FedEx project to track job progress from the blades and dozers and to see how fast we’re putting in the rock, etc.,” Larson confirmed. “We see that technology as a way to get better insight into our productivity, a real-time estimate of our capabilities, whether it's installing rock tolerancing or checking operator efficiency. It could even help with the takeoffs to supplement the drone data—and there’s no data disconnect. Everything just moves seamlessly from one system to another.”
Bituminous Roadways met and even exceeded tolerance specifications on the FedEx paving project.
“Typically, it’s a lot harder to hit estimated productions on the paving side. With this workflow, we are pretty dialed in—and that showed on the FedEx job,” Larson said. “We hit our production per crew hour thresholds, even with some additional training for our new operators.”
The advantages of technology such as grade control has them considering investment in 3D milling machines, skid blades and paving systems, while also looking to expand the use of drones in more creative ways and further build connections between various solutions.
Scales added, “We do over 1,000 jobs in a nine-month period in any given year. We have to be efficient and cost-effective to get all of that work done.”
Larson concluded, “Right now, from a data perspective, the schedule is our link—and that drives our digital workflow from the start, both on the operational side and in the field with survey and paving. It gives everyone, from the survey and civil team to the superintendent, a starting point. While our digital workflow is working well—it’s a source of continuous improvement and it helps to have integrated solutions and a more cohesive technology ecosystem to build on.”
Vicki Speed is a freelance writer covering the construction industry.
FedEx Paving Specs
• 282,000 square yards of surface area
• 204,000 tons of rock
• 63,500 tons of asphalt
• 1 motor grader
• 1 dozer
• Trimble Earthworks Grade Control Platform
• Timeline: 2 years
• Accuracy: 1/10 foot w/rover; 1/10 inch w/total station
BY ASPHALTPRO STAFF
By this point, all hot-mix asphalt (HMA) producers understand the value of using a robust controls system at the plant for mix design, production, ticketing and so much more. In simple terms, controls packages give everyone from plant operators, managers and ground crew to owners, bean counters and FOB customers, valuable insight and information in real time and—after a project—on demand for quality product, improved uptime, streamlined operations, trackable data and so much more.
If a plant didn’t come with a full controls system plugged into every aspect of production and loadout, or if you’ve pieced together a plant from components salvaged from multiple sites, you may be looking at the return on investment for installing controls after the fact. Here are five tips Stansteel/Hotmix Parts & Service of Louisville, Kentucky, shared for offsetting the cost in short order.
1. Calibrate belt scales in the controls
Many producers calibrate belt scales during the down season and call it good. Let’s make this a higher priority item. You could have a builtin calibration deviation alert for your belt scales and your liquid asphalt cement (AC) metering within your controls.
2. Regulate AC extractions in the controls
Many producers send start-up and shutdown mix to the waste pile as a quality control/quality assurance (QC/QA) measure. This is a good best practice to adhere to, but you don’t have to lose 100 tons (or more) each week to these “pulldown piles” of wasted material. You can use your controls to regulate AC extractions and meter material back into the system as recycle, thus saving big costs.
3. Tweak AC percentages with your controls
Speaking of extractions, do you ever have to wait for extraction and gradation test results to “tweak” AC percentages in your mix designs and production? If your mix designs are tested, tried and approved, then saved in your control system database, you have a leg up on Day 1 of a project.
Stansteel pointed out: “If your operations are like many plants, it really can’t get started, particularly on critical government jobs, until the first run of mix is checked for AC content and gradations. Sometimes, people are adjusting it every day or certainly every week. If you can avoid this, you may start up immediately. Instead of having delays and penalties on a job, get paid bonuses for being on-spec with your AC, always hitting the target.”
4. Troubleshoot with confidence for get-back-uptime
Your control system should allow you to “alarm” components in a way that lets you find and resolve issues efficiently. Stansteel pointed out that a feeder no-flow situation, a fines/dust plugged situation, an empty AC tank or a high-level alert in the silos could take some time to
find if you don’t have a control system with an alarm showing you where the problem is occurring.
“With a general industry condition of fewer plant operators and grounds people who have many tasks to take care of in a day, it’s almost impossible to watch and monitor everything on a plant, with truck traffic, loader feed and aggregate control.” By installing a controls system, like the Accu-Track Advantage the company offers, the system monitors hundreds of points on the plant multiple times per second.
“Any upset will either give an alarm or sequentially shut the plant down, depending on how critical it is to the operation and integrity of the mix.” Having a system that pinpoints the problem for efficient troubleshooting helps you get back in business more quickly, and that’s a cost saver.
As you see in the New Tech department every month, technologies and services in the asphalt industry are changing all the time. As controls systems advance for asphalt plants, you may find new ways to save on time and costs.
Stansteel acknowledges this: “As technology and materials advance, there will likely be more and more demand for adding more ingredients, whether it be hydrated lime, liquid anti-strip, chemical foamers, rejuvenators, RAS and more. If the control system you have is a relic of the past, it might prevent you from doing this correctly. It could result in the manufacturer having a huge cost to make the modification or doing it in a cobbled-up manner.”
By investing in updated controls, you can invest in a system that gives you more flexibility, better efficiency and a faster return on investment.
For more information from Stansteel, visit stansteel.com
Since its introduction, the Weiler P385 has set the standard for commercial pavers. The P385C raises that standard.
Increase to 120 hp with the Cat® C3.6 Tier 4F/Stage V engine.
Variable speed and reversible conveyors and augers and a 25% increase in tunnel height provide optimal material output.
Modular conveyor drive and sealed chain case increase feeder system reliability and life.
Enhanced heat system performance with direct-drive hydraulic generator and elimination of GFCI breakers.
BY JIM FEESE
Editor’s Note: For 2024, AsphaltPro Magazine allows experts in the industry to share how to expand your operations to the next phase of business. Are you ready to start making your own hot-mix asphalt? Let’s turn to some professionals who have equipment, services, software and tenure to help you expand efficiently to mix design, production, hauling and more. This month’s installment from Detroit Stoker Company delves into the mechanics of sizing the aggregate dryer properly for your intended HMA production plant.
PProperly sizing your aggregate dryer burner for optimum plant production should be a straightforward exercise; however, in many cases the burner is sized for significantly more than typical plant operating practices or even production capability. This can lead to multiple performance-related issues, reduce both burner and overall dryer efficiency, and reduce equipment lifespan.
Let us first explore why or how a burner gets over-sized. This typically happens one of two ways. One, an existing burner gets moved from one plant to another by the owner or via a used equipment sale. Although the plant may only require a 100 MBtu/hr burner, the next larger size (or two) may be the only unit available on the used equipment market and/or from a different plant in the owner’s fleet and that burner gets applied to the system. Second, when purchasing a new burner, the customer tends to “over-spec” the burner such that it is sized for
the maximum tonnage rate the plant could ever produce in addition to very high maximum material moisture percentages.
the
Let’s look at a simple example. A customer is purchasing a new 400 TPH counterflow drum mix dryer with the following specifications:
Discover the strength of the most versatile, durable, and reliable crushing equipment on the market today. Take on even the toughest applications with confidence. Experience unparalleled parts and service support, 24/7. Let Eagle Crusher keep you up and crushing, year in and year out.
The above example yields a required heat input of 91.1 MBtu/hr with a specific fuel consumption of 227,810 Btu/ton of material. Because the nearest available burner is rated at 100 MBtu/hr, the customer wishes to go up a size for “safety” reasons and selects a 125 MBtu/hr rated burner.
Now let’s look at typical plant operation. The plant runs on average at 250 TPH production with 3% moisture in the virgin material. The heat balance now looks like this:
air, we now must tune the burner for say 50, 60% excess air or more at this lower load (and larger size burner) to get sufficient air/gas mixing to ensure complete combustion—minimum Carbon Monoxide (CO) emissions.
Assuming 60% excess air, the overall loss in combustion efficiency due to heating up this additional airflow results in fuel consumption increase of 2.3%. Further, even with the additional excess air to drive mixing, it still often leads to additional CO emissions as the added excess air quenches the flame. Excessive CO emissions often coincide with unburnt fuel, which means HydroCarbons (HC) out the stack, which are typically not measured by most portable combustion analyzers. An increase in CO emissions alone of 200 ppm (CO has a higher heating value of 321 Btu/scf) will result in 52,240 Btu/hr of lost fuel (not accounting for additional HC losses).
The above simplified example demonstrates how over-sizing the burner can easily cost a plant 3% or more in additional fuel costs per ton of asphalt. Additional potential problems include:
• Tuning the burner to meet more stringent NOx and CO emissions requirements or permit limits can be substantially more difficult if not impossible to achieve. Decreasing CO emissions through tuning will typically increase NOx and vice-versa.
In this example, we now have a burner that typically fires at 38% (47.5/125 x 100) of its rated capacity. We’ll see why this is a big deal as we look at burner design.
A burner is a fixed orifice (both air passages and gas passages are of set design or dimensions), which is sized for at least the maximum rated capacity of the unit (plus some safety factor to ensure the burner does not blow-out or the flame lift off at or near the maximum capacity). This means with the above 38% output a few things are happening. The airflow and fuel flow are now exiting the burner at approximately a third of the maximum design velocity.
The burner’s function is to stabilize the flame and to properly and thoroughly mix the air and fuel to ensure complete combustion. In a rotary dryer, that combustion must be completed as quickly as possible in the limited combustion zone length. You may recall from high school physics:
KE = ½ M x V2
(Kinetic Energy = ½ Mass x Velocity2)
Assuming a Detroit®️ HADES burner (each burner make and model will result in different values, but the overall reduction in KE will be the same), the HADES-100 burner is designed for a peak KE at maximum firing rate of:
KEdesign = 5,586 ft-lbs/s
Note: this is technically “rate of change of Kinetic Energy” or “power.”
The HADES-125 example burner selected (for “safety” sizing purposes) is being fired at 47.5 MBtu/hr at 250 TPH production rate or:
KEactual = 315 ft-lbs/sec (assuming we could fire at the same 25% excess air level)
The over-sized 125 MBtu/hr rated burner is now firing at approximately 6% of the optimum discharge energy design point. This has a significant impact on air/fuel mixing, emissions and ultimately dryer performance.
The burner almost certainly must now operate at significantly higher excess air levels to get some of that lost air/gas mixing (kinetic energy) back. So instead of firing at optimum design point of say 25% excess
• Material temperature can fluctuate widely as small percentage changes in burner output cause relatively large changes in fuel flow as only a small band of the actual burner output range is being utilized.
• If a burner fires at very low output (and correspondingly excess air is not high enough to drive the air/fuel mixing process) it is common to find burner front end over-heating damage. Warped and/or overheated burner parts can be costly and time consuming to replace and will decrease burner combustion efficiency and performance as the deterioration worsens.
• Combustion flight damage could also occur resulting in costly and more frequent flight replacements.
• Additional performance related issues with balance of plant equipment operation can occur depending on drum, baghouse and exhaust fan sizing to name a few.
A corollary to burner sizing is air/fuel ratio control. The burner control system must be able to keep the air/fuel ratio optimized at all firing rates or burner efficiency will suffer for the same reasons cited above. Linkage-less control with direct coupled fuel flow valve/actuators and direct coupled air dampers/actuators or better yet, air flow control via variable frequency drive (VFD) is the best solution when properly integrated with a PLC based combustion control. The PLC control is designed to provide a tuning curve to enable optimal adjustment of the air/fuel ratio at all firing rates.
Note there are a lot of assumptions involved in this simplified example not the least of which is material moisture, percentage of RAP in the mixture as well as overall RAP moisture, etc. These are especially important considerations when sizing the proper burner. The burner manufacturer should be consulted early in the burner specification stage to ensure the plant needs are being properly met with a correctly sized burner for peak operating efficiency.
While over-sizing the burner may seem to be the right decision for future big jobs or anticipated growth, it can be a costly one, perhaps avoided by better plant operations including silo storage and truck load out to the job site, etc. Properly sizing the burner from the start can pay for itself in fuel efficiency gains in relatively short order.
Jim Feese, P.E., is the director of the burner group for Detroit Stoker Company, Monroe, Michigan.
AsphaltPro magazine joined forces with hall-of-fame paving consultant John S. Ball III of Top Quality Paving & Training to bring you the newest online training resource for your crew: Asphalt Paving 101.
The course is available on any device, anytime, anywhere to train your entire crew. Your single subscription to the best curriculum of all time gives you access to train all of your employees, each time you bring in a new hire.
In this course, your crew will learn:
• How to stay safe on the job site
• How to build a takeoff ramp
• How to determine fluff factor
• How to determine yield
• How to prep for real paving in the real world
• How to maintain equipment the right way
• Job responsibilities for each paving crew member
• and so much more…
Purchase your access to the course at: http://training.theasphaltpro.com/p/asphalt-paving-101
Find the educational guidance you need to produce, pave and maintain the nation’s infrastructure from parking lots to interstates. In this year’s guide, read up on the allimportant haul truck driver training that’s lacking in our industry today.
BY SANDY LENDER
EEach autumn, we present the annual AsphaltPro Training Directory to help the industry identify events or entities that offer education for new and veteran employees. And each summer, as I prepare the content, I find myself repeating how important training is. This year is no different, but I’ve found myself aware of a renewed need to discuss the safety element behind training.
I don’t limit that concept to safety training. I mean teaching and reminding everyone of best practices for the purpose of executing a quality project safely. I also mean enticing an ample stable of workers into the fold with encouragement and education so they can be shown best practices for safe and quality work.
As I was finishing this article for you, the American Council of Engineering Companies (ACEC) dropped a press release announcing the results of its Q3 2024 Engineering Business Sentiment Study. The report showed that optimism in our industry is high.
“For the first time since the Institute began its quarterly surveys, industry executives are optimistic across all market sectors for future growth,” they wrote. But there’s a problem with that growth.
An area of concern is the lack of well-qualified candidates for employment across the industry. ACEC said 71% of the respondents predicted an increase in hiring over the next 12 months, but 78% of them believe the lack of qualified, trained, educated workers is a barrier to the growth they’re excited about. Basically, 9 out of 10 (89%) of firm leaders told ACEC that it’s difficult to find qualified engineers and 62% told ACEC that it’s challenging to find non-engineering staff.
“We’re simply not graduating enough engineers, and many of those who do graduate are international students who have difficulty
The mechanics for these crews have added reflective tape to the screed decks, which offer extra safety for the paving crews on night projects. Adding this reflectivity along with strobe lights not only makes the paver stand out for the traveling public, but also makes it stand out for approaching haul truck drivers who are looking for their entry to the work zone and their target for delivering material. That extra reflectivity helps roller operators who might be getting hypnotized by their repetitive passes at night. Every bit of this is a help to everyone who sees it out there on the project but only if it’s clean and visible. Photos courtesy of John Ball, proprietor of Top Quality Paving & Training, Manchester, New Hampshire
• Week 1: January 20 - 23
• Week 2: January 27 - 30
• Week 3: February 3 - 6
• Week 4: February 10 - 13
CLASS SIZE IS LIMITED !
To secure your seat, please register before December 15, 2024
Details can be found at www.gencor.com/training or call us at 407-290-6000 ext. 342.
Improving overall plant production and efficiency are all common concerns for plant owners and operators. Having a well-trained technical crew is vital to maintaining plant performance and efficiency.
Gencor and its training staff represent the biggest concentration of knowledge and expertise in all the sciences and technologies involved in the production of asphalt plants. Customers who attend these seminars benefit by having the support and focused attention of the best specialists in the asphalt industry.
Using Gencor’s state-of-the-art control simulators and actual equipment, our experts take you stepby-step through a comprehensive & intensive concentrated hands-on training program providing the latest techniques on optimizing production efficiency.
staying in the country to apply the skills learned in American universities,” said Daphne Bryant, executive director of the ACEC Research Institute. “The workforce challenge remains one of the most pressing barriers to growth in our industry, which has significant implications for America’s economic growth and the future of our critical infrastructure.”
The good news is ACEC and the ACEC Research Institute aren’t letting this slide. They are among the entities we’ll talk about in this year’s training directory that offer opportunities to fix the problem.
In April, ACEC held its first Engineering and Public Works Workforce Summit with its partners, the American Public Works Association (APWA) and the American Society of Civil Engineers (ASCE). This launched an Engineering Workforce Consortium to come up with potential policy solutions to our workforce problem. The Institute is engaged in a research project looking at the engineering “Firm of the Future” to explore what talent and skills will be needed to staff the firm of 2035. You can get more information about the program and training opportunities for engineers at https://www.acec.org/research-institute/.
Now let’s look at other entities and reasons behind training in the niche industry of asphalt paving and production.
Most of the equipment-operation seminars you attend at a state asphalt pavement association (SAPA) lunch-and-learn or annual meeting or at a national convention like the National Pavement Expo (NPE) or CONEXPO-CON/AGG begin with an instructor reminding students to clean and maintain the machine. Almost every article I prepare with paving consultant John Ball includes a mention of cleaning the machine and I find myself curbing Ball’s enthusiasm for that topic.
The reason for the cleanliness topic’s popularity is its importance to the rest of equipment operation and safety. A dirty, gunked-up paver track isn’t going to roll smoothly along, thus isn’t going to allow smooth mat placement.
This offers a quality control issue. If you have a worker reaching in to get a chunk of material out of the bogies during the forward motion of the paver, you have a setup for an accident.
Something more obvious for a team to recognize as dangerous is a broken strobe light atop the operator platform or forward conveyor of the milling machine. If the haul truck driver can’t see the mill at night, he’s more likely to back into the conveyor arm. If the traveling public can’t see the mill, something more catastrophic could happen.
Look to the condition of the reflective tape on every piece of equipment on your paving train. From the skid steers to the haul trucks to the distributor truck to the finish roller in the lonely dark so far behind the main action, these machines need clean and visible reflective tape that catches the light from oncoming traffic and makes it abundantly clear that your workspace is right in front of them. A warning sign that’s been smeared out by grease and asphalt on a haul truck is no longer of any use to you.
Clean and maintain your equipment for safety’s sake. Teach the newcomers to your team why it’s important to stop and clean a machine at the end of the shift. Train them on taking safety seriously.
You also want to train workers on the “why” behind newfangled technology on their equipment. We’ve all heard the stories of operators switching off automation and new controls systems at the paver or screed. This negative practice can be attributed to fear of the unknown, fear of technology in general, fear of the machine taking over the operator’s role or job, fear of looking foolish if the operator pushes the “wrong” button, fear of making a costly mistake if pushing the “wrong” button, and so on. What do you see as a common thread there?
As company owners, managers and trainers, it is up to the operators’ supervisors and upper management to alleviate fear through proper training. When someone is made to feel comfortable with new technology, that
fear factor recedes, and confidence takes its place. Confidence in the equipment and technology means best and safest practices can be followed. Sometimes that means you need a team manager or leader who’s supporting the new tech—cheerleading the implementation—and helping the others learn.
There’s wisdom in appointing a person whom you train to be the trainer. There are entire programs set up to “train the trainer” who then goes back to the crew and makes sure each member of the crew is performing at peak efficiency.
One example of this is the Smith Systems driving instruction program that Woman of Asphalt Tracy Richard participates in for Aggregate Industries Northeast Region Inc., a division of Holcim. While she is the quality control technician for the company, she has been trained in the driving school and uses the down season each winter to train members of the Aggregate Industries team in the Smith Systems program.
Check out the WofA article featuring Tracy Richard in the May 2022 issue.
Another great example of building up trainers in your company is the First Aid program that Vince Hafeli, president of Ajax Paving Industries of Florida, has championed. While this human resources and safety related program isn’t training crew members on equipment operation, it is teaching personnel the importance of whole-body wellness and how to help one another on the job. It’s giving workers permission to say “I’m not okay” on those days or in those situations that could compromise personal and crew safety. It’s giving workers permission to help
You can get free tailgate talks from AsphaltPro Magazine to use in teaching new and veteran crewmembers. Safety, equipment operation, back-to-basics, plant concept, lab & QC/QA tips and more quick ideas arrive in your inbox Sunday night in time for the Monday morning tailgate talk. Sign up for these free nuggets of howto info under the “Subscription” tab at TheAsphaltPro.com.
Sync your production, loadout, scale ticketing, and office processes to boost efficiency and maximize profitability.
Are you ready to experience the power of centralized data and processes?
themselves and one another through the difficult conversations that surround mental health wellness in our industry. At this time, Ajax Paving has an in-house certified mental health first aid trainer who has trained approximately 50 employees.
When you look around your paving and production operation, what technologies and systems do you see where a trainer would be beneficial? Original equipment manufacturers (OEMs) and software developers like Astec Industries, Blaw-Knox, Command Alkon, Gencor, Stansteel and Wirtgen not only partner with AsphaltPro Magazine to keep technical, how-to information coming to you every month, but they also provide training opportunities for your personnel.
Look at the Astec schools for starters. The OEM has multiple divisions under one roof and boasts on the training website: “Astec experts have hundreds of years of combined technical and application experience. We invest in your people who operate, maintain and service your Astec equipment for maximum production and decreased downtime. Our training solutions are offered throughout the year via factory training, on-site training, virtual online training, on-demand training and custom programs.”
Even though the company offers year ’round training opportunities, it also offers hands-on training during the scheduled Asphalt Customer Schools, Asphalt Burner School, a plant controls school, a paving professionals school and others too numerous to list. See their ad on page 49 for more information.
The Blaw-Knox University, now in its 58th season, is dedicated to training paver operators and foremen on proper paver operation and maintenance, paver hydraulic and electrical systems, and applied best paving practices through several classroom-style and hands-on application courses. See their ad on page 53 and check out the four-day university where paving professionals learn such topics as:
• paving safety on the job site;
• material quality;
• paving principles;
• hands-on paver preparation;
• paver and screed operation;
• joint construction;
• troubleshooting mat defects;
• automatic grade & slope operation with Blaw-Kontrol, Topcon or Moba; and
• daily maintenance.
Command Alkon offers a learning opportunity each autumn called the Elevate Conference and attaches training days to it to make travel and education one easy package for attendees. See their ad on page 47 for more information.
Gencor Industries offers its four-day training courses in plant operation and maintenance to teach self-sufficiency. Years ago, Gencor adopted the philosophy of “self-help” when it came to plant-downs because the OEM felt no one but the plant personnel could respond fast enough to minimize the costly experience and be able to get up and running quickly, even if the OEM had a serviceman nearby. At Gencor University, expert instructors provide step-by-step comprehensive and concentrated training on a state-of-the-art control simulation and plant equipment to share the science and technology of hot-mix asphalt production. Gencor also offers custom training; contact them for more information. See their ad on page 45 for more information.
Also check out Stansteel’s Hotmix University, which offers annually a four-day course for plant managers called the Managers Exchange and two four-day sessions for operators called Operators Course. See their ad on page 55 for more information.
Wirtgen Group also offers training in their state-side training center, a robust facility with classroom and outdoor demonstration areas for attendees. The company’s Center for Training and Technology (CTT) is located outside Nashville and hosts multiple courses. Because the courses include crushing, screening, cold planing, paving, compaction and more, customers have options for training. See their ad on page 57 for more information.
Of course, there are many OEMs and service providers beyond these six who offer inhouse training, dealer-sponsored training, customized training at your facility and other forms of education to help you build the confidence and skills of your workforce. It is as easy as picking up the phone to call your dealer to ask about what training help is available. If you’ve purchased equipment second-hand or at an auction, you might not have a relationship with the local dealer, but you shouldn’t let that stop you from inquiring. Most dealers will be happy to begin and build a relationship with you if you have a piece of equipment they know and understand—and know you’ll want to replace someday.
Also look to our industry for consultants who can assist you in training the basics that
go beyond the piece of equipment in front of your worker. If you’re a regular reader of AsphaltPro, you know we often feature backto-basic, how-to articles from paving consultant John Ball, who has been in the industry for decades. You can reach out to him by phone or email and see where in his crowded schedule you might fit for some one-onone, in-person help for your crew.
Also look to those entities offering online training that you can accomplish during rainy days and the down season. AsphaltPro Magazine has an online training course with eight modules, each containing separate lessons, to help your new workers get their feet on the ground. We also recommend the course for veteran employees who’ve been away all winter and are looking for a refresher on the basics that will keep them performing efficiently and safely. See our ad on page 42 for more information.
Beyond the OEMs and service providers, there are associations—like the aforementioned SAPAs—that offer education for free, as part of your annual dues or for a nominal fee if you aren’t a member. Definitely look into the opportunities the industry associations offer. And don’t forget that entities like the National Center for Asphalt Technology (NCAT) at Auburn University, Transportation Research Board (TRB) and The Center for Construction Research and Training (CPWR) offer in-person and online seminars and webinars for a variety of educational opportunities.
Training is all around you all the time. Take advantage of continuing education and focused training to bring your workers up to speed on not only equipment operation, but also best practices for top quality project execution and their safest work environments.
You can train your paving crew online as many times as you want, for one set price. AsphaltPro Magazine offers Asphalt Paving 101. This back-to-basics course is available to everyone on your crew with the purchase of only one subscription. Take the online course as many times as you need to with as many crewmembers as you need to for life with that one purchase. Visit the “Training” tab at TheAsphaltPro.com.
Astec is more than just equipment. We’re your partner in success. Our expert instructors, with decades of combined experience, are dedicated to helping your team achieve peak performance.
Benefit from:
• Tailored Training Solutions: From factory-based courses to on-site workshops and virtual options, we offer a variety of training formats to meet your specific needs.
• Experienced Instructors: Our trainers bring decades of real-world experience to the classroom, ensuring you receive practical, actionable insights.
• Hands-On Learning: Our in-person training combines classroom instruction with practical, hands-on exercises. Led by seasoned professionals, you’ll gain the skills and confidence to optimize your equipment’s performance.
Ready to invest in your team’s success?
Scan QR Code for complete list of trainings.
When the haul truck arrives at the work zone, the driver should know how he or she is expected to enter the work zone. They should know who the dump person is for the day or for the job so they know exactly who they’re looking for as their point person on the job when they arrive. This should be covered in the pre-job tailgate meeting.
BY JOHN BALL
TThe haul truck is not just the vessel that brings vital, perishable material to our job sites throughout each shift. It’s a large and lumbering piece of equipment. The unladen truck can be 50,000 pounds by itself. Add 18 to 23 tons of hot-mix asphalt (HMA), and you have a heavy vehicle for the driver to control. The heaviest one I’ve seen arrive on a job was about 50 tons. That was on a project in Montreal where it’s not uncommon for larger live-bottom trailers to bring heavy loads to the paving project.
No matter what size of truck they’re driving, if the driver hasn’t been properly trained and shown best practices for every aspect of loading and delivery, they can be a liability for their company, the general contractor and the
traveling public. Let’s look at the main areas where they need training:
• Cleaning out the truck bed and getting out of the work zone
• At the plant and during loadout
• On the road, routes to and from the job
• Getting into the work zone and to the paver
• Charging the hopper
Before we look at some tips for training in each of these areas, let me share an example of why they’re all vital. During the 2024 construction season, I was helping a crew on a night project that involved paving one 12-foot lane of a five-lane highway. We followed the MUTCD and had barrels delineating the work zone; four state troopers were assisting with traffic control.
A subcontracted haul truck driver completed charging the hopper of the Shuttle Buggy around 3:15 a.m. and pulled away from the paving train. We didn’t know it, but the driv-
er pulled over about a half of a mile ahead to clean out the bed of his triaxle while still within the safe confines of the work zone. He raised the body to clean it out and returned to traffic with the body still up.
About a quarter of a mile from his self-appointed cleanout area—still in the work zone—the elevated body struck and knocked down an overhead highway sign, resulting in debris in the road. The driver didn’t tell anyone what had happened, but continued to the plant, where he parked his damaged truck, signed out and went home.
Back at the debris field, tragedy was about to unfold. A motorcyclist entered the closed work zone at highway speeds and encountered the mangled signage. The tack truck driver saw this accident happen and was able to call for help, but the motorcyclist didn’t survive his injuries.
Notice a host of best practices in play here. First, the crew members are using headsets for clear communication. The guidebar on the paver is clean and follows a marked line for the paver operator to guide off of. The haul truck’s mud flap is up out of the way of the push rollers, which the back tires are snuggled against so the live-bottom can feed the hopper without dribbling mix in front of the paver.
This loss of life could have been prevented if the driver had been trained on proper cleanout practices, if he had an alarm that alerted him when his truck body was elevated when moving at travel speeds, if he had stopped and asked for help after striking the highway sign, if the motorcyclist had heeded the signs telling him the highway was closed, and so on. A series of mistakes and lapses in judgment led to a terrible accident that we can only learn from now. Let’s look at a few lessons we can take away from this awful scene.
The main training category for this article is that of assigning a dedicated cleanout area for trucks and making sure all drivers understand where it is and how to use it safely. Each driver who will be bringing material to the site should know a designated cleanout area exists and should know where that area is.
If the work zone is exceptionally long and the cleanout area will “move” before the job is complete, then each area designated on a map should be pointed out to each truck driver. Each area should be highlighted with the date
and/or time it will be available for drivers to use. This type of update is easy to indicate in today’s work zone apps. Check with your app provider to ensure all members of the team— including subcontracted drivers—have access to the information in real time.
When the cleanout area is available for drivers, it should have clear, legible signage in the languages your team members read. Lights and arrows should designate how to
access the area and where cleaning can happen. Tools and safety equipment should be easy to use. Then additional lights and arrows should designate how to leave the area safely.
For nighttime work zones, the cleanout area needs additional lighting to not only give the truck drivers a well-lit work area, but also to make it painfully obvious to motorists that this is a dangerous construction area off to the side of the road and not a rest
During the pre-job tailgate talk or safety meeting, all members of the crew, including subcontractors, should be present to learn what safety protocols are in place. This pre-job meeting gives the superintendent the chance to make sure everyone is on the same page not just for quality and best practices that will ensure a top quality performance, but also for safety of the crew members and the public.
This is when you make sure everyone is assigned a safety buddy, has a safety whistle and knows what to do if safe-
ty alarms go off on the crash attenuator. This is when you go over the plan for trucks to get into and out of the work zone. This is when you remind everyone that they cannot walk between a backing truck and the paver. This is when you remind everyone of the mile marker or street name for the project in case they have to call for emergency help during the shift. This is when you show the truck drivers where they can clean out the bed of the truck and remind them there’s no other place in the work zone where they should be outside of the cab.
The mud flaps lay on the back tires, out of the way
The mud flaps are returned to hanging position for safe travel.
When the haul truck backs to the paver, either the dump man or the truck driver will want to position the mud flaps over the back tires. There are systems available for trucks today that allow the driver to press a button and have the mud flaps retract or lift without anyone having to physically touch them. This means there’s nothing between the truck tires and the paver’s push rollers. When the truck is ready to leave the paver, the mud flaps need to be returned to their proper position not only for traffic safety but also to be “street legal.” If the driver has a button he can press in the cab to lower the flaps back in place, that’s great. Otherwise, he can ensure they’re hanging properly when he stops at the designated cleanout area.
stop or place where the traveling public is welcome. Signage and arrows should make it clear this is a lighted area for large trucks/ heavy equipment only. The last thing you want is for confused motorists to think they’ve come to the end of the work zone “early” and enter this well-lit area where a haul truck driver might be outside of his or her cab.
The driver uses a 3-inch putty knife or scraper to maneuver around the tailgate and hinges/ dog ears to clean. This is also the time to reposition the mud flaps. They were lifted out of the way of the paver’s push rollers—now lower them back where they need to be for legal travel.
As cumbersome as it may seem, setting up a mechanical flagging system that clears the haul truck for return to traffic at the end of the cleanout area could prevent the type of accidents that happen from raised truck bodies. A system that prevents the truck from leaving the area if it can’t fit under a mechanical flagger’s arm will keep drivers from hitting bridges, overpasses, highway signs and other overhead obstructions. (Check out the Federal Highway Administration’s technical report “Review of Low-Clearance Early Device Warning Options for Illinois” for ideas on how LCDW systems are being used on bridges and other structures to reduce collisions.)
One of the basics for asphalt paving is getting the mix from the haul truck to the paver’s hopper, which is referred to as “charging the hopper.” It takes a gentle touch and careful release of tension when it comes to the truck’s brake. Follow these steps for your best chances at a smooth process.
1. Have the haul truck driver locate the dump person upon arrival at the work zone.
2. Back the truck to the paver and stop when the dump person signals that the truck’s back tires are within an inch or two of the paver’s push rollers. Then firmly push your foot down on the brake pedal.
3. Have the paver operator gingerly drive forward so the push rollers are kissing the truck’s back tires. This should be a gentle touch.
4. With your foot still on the brake pedal, release the tension just a bit as you feel the paver engaging you forward. Let the paver drive and push the truck forward.
5. The dump person will signal for the haul truck to begin raising the truck body to discharge material in a consistent, even flow into the hopper. It is important for the truck driver to maintain “even” pressure on the brake pedal! That surge of material will try to push the truck out of the hopper and away from the paver, resulting in a mess for the crew to clean. (Even if you had the emergency
One of the ways to prevent a mess like this is with best delivery practices.
brake on, that sudden surge if the bed was raised too high too quickly would push the truck out, so make sure you don’t raise the bed too high too soon.)
In the event of a spill, it is vital for the crew to hop into motion and get the mess cleaned up. The crew can’t be lazy and leave a pile of material for the paver to try to drive over, as you can see was attempted in this photo.
Jump into action and clean up the material using a skid steer so you don’t have temperature segregation and mounds of mess getting caught up in the paver’s track or wheels.
2025 DATES
• January 20 - January 23
• January 27 - January 30
• February 3 - February 6
• February 10 - February 13
REGISTRATION
CLASS SIZE IS LIMITED, register today!
All details can be found at www.blawknox. com/training or contact at (407) 290-6000 ext. 342 or training@blawknox.com
The Blaw-Knox University, is dedicated to training paver operators ad foreman on proper Paver Operation and Maintenance and applied Best Paving Practices through classroom-style and hands-on application courses.
For over a half a decade Blaw-Knox has earned its reputation as the go to source of training and instruction on hot mix paving.
Blaw-Knox provides improved technical and problem-solving skills on a variety of paver operations and maintenance topics. Course instructors share decades of field and teaching experience with attendees, including training on the latest DOT requirements.
The other training points mentioned at the beginning of this article can be covered when a company implements procedures and makes it clear those procedures are to be followed.
There absolutely should be a procedure in place for drivers to sign in, do a walkaround of the truck in a safe and well-lit location at the plant site, ensure previous maintenance items have been addressed, and check out the vehicle for the shift. When a shift is complete, there should be a procedure for the driver to do a walkaround of the truck in that same safe and well-lit location as before, perform cleaning of the equipment, ensure an easy and well-documented way to inform mechanics of any maintenance issues or worries, and to check in the vehicle at the end of the shift.
Have you cleaned the reflective tape, taillights, safety placards and other lighting lately? Make sure reflective tape, safety signs and lights on your haul truck aren’t obscured by grease or asphalt build-up. You want headlights hitting the tape to reflect light to the motoring public. You want them to see you. Your lights cannot do their job of protecting you, the crew and the public if they’re filthy and covered with grime. Get these and other training tips in the free document titled “12 Safe Steps for Haul Truck Drivers” at TheAsphaltPro.com’s Digital Downloads page.
To make truck traffic safer at the plant, to make loadout safer under the silos, to make travel safer along designated routes to and from the job site, to make backing to the paver a safer operation and to make charging the hopper safer, drivers should be aware of the proper procedures at each step. And they need to be told why.
The reason for using the three-drop method of loadout at the silo makes perfect sense to the seasoned plant operator and the paving superintendent out on the job site. But the subcontracted driver who’s been hauling asphalt for two hours has no idea why he must stop the truck, receive a drop, back it up, receive another drop, and so on. This may feel like wasted time to him when he
Shouldn’t it be obvious that a driver must keep his or her eyes on the road when driving a 50,000-pound haul truck? Sadly, attention can get divided on the job site and this is where we need clearly defined rules and roles for drivers, ground personnel and safety buddies as well as the use of proximity alarms, whistles, headsets and other safety equipment that can prevent accidents and/or sound the alarm when something is about to go terribly wrong.
In the example I’ll outline here, a subcontracted driver in control of a 10-wheeler backed to the mill on a parking lot project. He watched that piece of equipment out the right-hand side mirror. Moving forward slowly, he continued to keep his eye on the mill, continuing to monitor the right-hand side mirror.
The groundman was also on the right-hand side of the mill, directing the operation.
From half the parking lot away, I realized, too late, that the driver wasn’t going to notice his truck getting dangerously close to parked vehicles. I couldn’t shout loud enough to get his attention before he hit the parked work truck’s pendle hook (trailer hitch) and dragged the work truck about 2 feet into the neighboring parking stall before noticing me yelling and waving and the crunching sound beside him.
Thank God no one was unloading the back of the work truck. Thank goodness this truck belonged to the boss and not a litigious member of the traveling public.
It takes training and all hands on deck to avoid pricy mistakes like this. If I’d had a safety whistle around my neck that morning, I could’ve blasted the shrill sound to get the driver’s attention—of course, the driver would have to know that the sound of the whistle means to stop in your tracks and look for the safety problem. If the team had assigned safety buddies at the start of the job, someone would’ve been looking out for the driver. Someone would’ve been keeping an eye on the mill operator. Someone would’ve been keeping an eye on the groundman beside the mill. Someone would’ve noticed the truck veering too close to parked vehicles.
Luckily, this is the kind of accident that only damages equipment and results in a few minutes of delay. It’s something the
The subcontracted driver was watching the right-hand mirror to monitor the cold planer behind him, and didn’t notice how close he was veering to the parked vehicles on his left.
To make the situation worse, after hitting the tow hitch and dragging the work truck a few feet into its neighboring parking stall, the haul truck driver backed up and continued working as if nothing had happened. If not for me waving at him and calling for someone to assess any damage, he wouldn’t have alerted anyone to the problem. We must work together in the field for accountability and safety.
crew can learn from and then move on with the day, working smarter and with heightened senses. But it’s the kind of accident we can avoid if we train truck drivers to pay close attention to their driving skills when on the job. If your foot isn’t on the brake, your truck is moving. Watch where it’s going.
Join us for Hotmix University in Louisville, Kentucky. During the focused exchange sessions, participants enjoy a combination of lectures and interactive lab sessions in our shops.
PLANT MANAGERS are interested in making their plants run better while maintaining maximum profitability. Other topics include:
Industry changes and trends which require Plant Response/Modifications.
Tuning Plant Asphalt Automation to achieve 100% End Results and Project Bonus Pay.
Importance of Combustion and Air Systems to Achieve Production Rates.
Benchmarking and Measuring Plant Performance. Safety Controls to help Prevent Hood Shots.
PLANT OPERATORS will invest half of their course time with interactive demonstrations of asphalt equipment. The other half of the course time will be invested in learning via classroom-style presentations. Topics include:
Specifies where the Hotmix Asphalt Plant fits into the entire business operation including the management of aggregates, liquid A.C., paving, and quality control.
Dr ying Systems: Alignments, flighting, and troubleshooting.
Slat s & Silo System monitoring and wear-reduction. Plant Automation and Multiple Liquid Blending.
could center the bed under the silo gate and receive one lump stockpile of 20 tons, then get on with delivering the load. He doesn’t understand—yet—that taking one lumped load leads to material segregation and contributes to problems when charging the hopper. This isn’t something he’s born knowing—he has to learn it, like each one of us had to learn it. (Watch the November issue for an article on how to load out different types of trucks most efficiently.)
When the driver gets to the paving site, depending on the type of project, he’ll have a variety of options for backing to the paver. The first and most important procedure is to locate the dump man when he gets to the job. In the pre-job meeting or tailgate talk, he’ll be told who the dump man is for the job—and that might be the paver operator or the foreman. (See the sidebar titled “You Can’t Skip the Tailgate Talk” for information.)
No matter what kind of project the driver is delivering to, the dump man will be
the person who guides him and helps him get lined up to the paver’s push rollers. That person, normally, will be wearing a different colored shirt, vest and/or hat. He should have a safety baton or a safety whistle, as well, to acknowledge the driver and direct him. (See the article “Save on Costs with Your Professional Guide to Asphalt Mix Delivery, Part 3—An Independent Look at Best Haul Truck Practices” on TheAsphaltPro.com for a detailed discussion of how to get to the job and deliver material to the hopper efficiently.)
For drivers who will be receiving millings in an empty bed, locating the ground man is just as important. This person is the driver’s second set of eyes; both driver and ground man must trust one another but this doesn’t leave room to forget good training. On a recent parking lot project, a haul truck driver watching the milling machine via his side mirror neglected to watch where he was going and ran into a
parked work truck (See the sidebar titled “Train Drivers to Watch Where They’re Going” for details). This accident proves we need to keep all our senses on alert when in the field.
The haul truck driver can’t be expected to handle everything that’s happening around his truck when he gets to the job site, but we can give him a fighting chance at safe success when we train him on the proper, safe procedures expected of him. We must train the drivers who are controlling these large and lumbering vehicles that come so close to our co-workers, pricy equipment and motoring public if we want to have quality jobs with safe records.
John Ball is the proprietor of Top Quality Paving & Training, Manchester, New Hampshire. For more information, contact him at (603) 493-1458.
Experience the industry‘s most comprehensive curriculum, all in one world-class facility.
AT THE WIRTGEN AMERICA CENTER FOR TRAINING AND TECHNOLOGY, we provide an extensive curriculum tailored to the learning needs of technicians, operators, work crews, site managers, service engineers, and service department personnel. From guardrail to guardrail and 20 inches down, our courses cover everything from aggregate production, to paving, compaction, and recycling of road materials Experience high-quality teaching from industry experts that keeps attendees in step with Wirtgen Group’s cutting edge technology.
CLOSE TO OUR CUSTOMERS
BY ASPHALTPRO STAFF
As part of its Manufacturing Express national tour, the Association of Equipment Manufacturers (AEM) stopped at the compact track loader production facility for Takeuchi-US in Moore, South Carolina, Aug. 27, 2024.
AEM advocates on behalf of more than 1,000 members, representing over 200 product lines, to urge elected officials to champion policies that create a globally competitive business environment, rebuild our nation’s infrastructure, open up foreign markets for equipment manufacturers in the United States, better prepare the next generation of America’s workforce, and keep the U.S. economy strong. The “AEM Manufacturing Express” is developed and executed by AEM to proudly display the equipment manufacturing industry’s commitment to building communities through family-sustaining jobs, education, environmental stewardship, and strong economies. To that end, Takeuchi and AEM had some special guests at the August event.
Congressman William Timmons, 4th District, South Carolina spoke at the event, noting the importance of manufacturing in Spartanburg County and thanking Takeuchi-US for putting its faith in the Moore community by locating its compact track loader production facility there two years ago. Several other dignitaries were also on hand for the festivities, including:
• David Britt, Spartanburg (SC) County Council Vice-Chairman
• Allen Smith, President & CEO, OneSpartanburg, Inc.
• Kyle Sox, VP of Industrial Development, OneSpartanburg, Inc.
• Katherine O'Neill, Chief Economic Development Officer, OneSpartanburg, Inc.
• Dwayne Hatchett, Director of Existing Industries, OneSpartanburg, Inc.
• Cole Alverson, Administrator, Spartanburg County
• Carter Smith, Advisor, OneSpartanburg Inc.
AEM recognized Takeuchi-US and its employees as industry leaders for their contributions to the local community and manufacturing industry. At the event, Takeuchi-US also celebrated the production of its 10,000th compact track loader, a TL12 model, at the Moore facility, which opened in September 2022. Takeuchi’s employees signed the interior of the TL12’s rear cover, and soon, this unique, one-of-a-kind 10,000th machine will be delivered to a Takeuchi customer.
Takeuchi-US was the 43rd stop on the AEM Manufacturing Express tour, which will visit 80 manufacturers across 20 states. The tour showcases the cutting-edge technology and innovations that power modern equipment, as well as the innovative technologies, processes, people and products revolutionizing this industry across America.
For this month’s paving-related product gallery, let’s take a look at not only the compact loaders that help out around a job site, but also the paving equipment and services that keep you building our nation’s infrastructure throughout the busy end-of-season.
ASV, Grand Rapids, Minnesota, introduced its new generation RT-65 Posi-Track®️ loader, now powered by Yanmar, in August. The compact track loader is redesigned and now includes a 67.1-horsepower Tier 4 Final Yanmar diesel engine and optional 26.7 gpm high flow. ASV’s RT65 is a brand-new radial-lift machine with new hydraulics, engine, controls, wiring, pumps, hoses, frame and more, offering a 2,000-pound rated operating capacity and 5,714-pound tipping load. A cooling system and optimized hydraulics are designed to allow operation at 100% load, 100% of the time up to 118°F.
The machine is 7,385 pounds and includes ASV’s Posi-Track rubber track undercarriage. It includes a suspension system made up of two independent torsion axles per undercarriage, allowing for a smooth ride and speeds up to 9.1 mph.
ASV includes a 2-year, 2,000-hour warranty.
For more information, visit your local ASV dealer.
Blue Diamond™ Attachments, Knoxville, Tennessee, announced in August the launch of a new line of rubber tracks. Available for compact track loaders, mini-excavators, mini-loaders and multi-terrain loaders, and with the four most common track patterns (Block, C-Lug, MultiBar and Zig-Zag), the new line is designed to perform under a wide range of working conditions.
Blue Diamond’s rubber tracks are custom manufactured with a blend of tough rubber compounds, combining unique resistance features with outstanding durability, according to the manufacturer. The abrasion-and-wear-resistant materials are designed to provide a comfortable and safe ride for operators, which reduces fatigue and vibration-related equipment issues.
A continuous steel cord structure with solid steel forged links and a reinforced roller path minimize the risk of track breakage by distributing the tension forces along the entire track. Application-specific lug patterns offer enhanced traction, as well as chunk and tear resistance.
“Our new line of rubber tracks are built to withstand heavy jobsite use while still giving a comfortable ride for operators,” said Drew Truan, chief operating officer at Blue Diamond Attachments. “Our products are compatible with most OEMs and have a similar wear lifespan at a fraction of the price, making them the perfect choice when tracks need to be replaced—and all are supported by Blue Diamond and our dealer network.”
The new line of rubber tracks come with the Blue Diamond Satisfaction Guarantee and are backed by a 2-year warranty.
Dynapac North America LLC, Fort Mill, South Carolina, announced in July the addition of Century Equipment to its growing network of authorized dealers. This strategic partnership enhances the availability of Dynapac’s construction solutions across Utah, New Mexico and Wyoming.
Century Equipment will now offer the full range of Dynapac products, including the latest models of soil compactors, asphalt rollers and pavers. “Partnering with Dynapac allows us to offer our customers some of the best road construction equipment available in the market today,” said Tyler Hill, vice president at Century Equipment. For more information, visit https://dynapac.com/us-en/
Grote Industries, Madison, Indiana, launched its new WorkShield™ product line, powered by HINVII®️ technology, in August. These products are a new line of warning lights powered by the company’s HINVII technology. The WorkShield lamps use minimally visible, low-wavelength light to illuminate high visibility material, which raises its conspicuousness without distracting personnel or disturbing traffic.
Designed to deliver the visibility critical to worker safety, Grote’s WorkShield lights are designed for any application—they can be strategically mounted on a wide variety of equipment like utility trucks, tow trucks and emergency response vehicles, to name a few. This allows them to illuminate the high-visibility clothing and material on a work site without directing visible light into traffic or other surroundings.
“Our team is excited to bring this innovative product to market,” said Matt Forner, Grote’s director of aftermarket sales. “The HINVII technology built into our quality lamps brings a new layer of safety to work sites, further building on our commitment to make the world a safer place.”
The WorkShield product line currently features two flat-mount options: the first uses six LED diodes producing low-wavelength HINVII light, while the second supplements the base model with four amber light diodes. Both versions mount to nearly any solid, flat surface and are available through Grote distributors now.
The Reynolds Warren Equipment (RW) team announced in August that it is the new municipal dealer for Kärcher Municipal North America (KMNA) for the state of Georgia. KMNA is the official, exclusive, North American importer and distributor of Holder brand tractors and Kärcher brand sweepers produced by the German-based Kärcher Municipal GmbH.
The RW team stated in a press release: “As with all equipment RW provides, quality and customer experience are of utmost importance. KMNA demonstrates similar values by producing municipal equipment through innovative technology and advanced solutions. This shared passion will have a significant impact on Georgia municipalities.”
“We at Kärcher Municipal are thrilled to announce our new partnership with Reynolds Warren, a leader in the asphalt paving and concrete contractor industry in Georgia,” said KMNA vice president of sales, USA, Noah Knoble. “This collaboration is a natural fit, as Reynolds Warren’s strong focus on infrastructure aligns perfectly with our advanced sweeper and implement carrier solutions. By joining forces, we’re enhancing the range of services Reynolds Warren can offer to their already impressive customer base, providing even more comprehensive solutions for municipal projects. We’re excited to work closely with Reynolds Warren and look forward to supporting this partnership as we grow our mutual business in the municipal market.”
Road Widener LLC, Floyds Knobs, Indiana, offers the patented FH-R material placement attachment, which the manufacturer states provides contractors with 50% reduced labor at a fifth of the cost of traditional self-propelled equipment. The remote-controlled design of the attachment is designed to allow the operator of the host machine to control the attachment via remote control, thus enhancing safety.
The FH-R is a solution for material placement, dispensing topsoil, gravel, asphalt, limestone and more with an attachment compatible with common machines that contractors already own.
“With the current Bipartisan Infrastructure Deal there is a renewed focus on repairing and reconstructing our nation’s roadways,” said Jack Guebard, Road Widener regional sales manager for the central
Increase production and efficiency without the investment of a new drum. A leader in the retrofit market, we’ll work with you to come up with the best solution at a competitive price.
· HIGHER RAP PERCENTAGES
· SINGLE POINT ADJUSTMENT
TRUNNION DESIGN WITH HEAVY
DUTY TIMKEN RAIL CAR BEARINGS
· WEDGE-LOK™ TIRE SUSPENSION
· IMPROVED FLIGHTING DESIGN
· PARALLEL TO COUNTER FLOW CONVERSIONS
· PORTABLE AND STATIONARY
• See the latest equipment
• Learn best practices and techniques
• Improve your jobsite and business March 25-27, 2025 | St. Louis, MO
United States. “Now is the time to modernize our infrastructure, making it safer and more resilient. The FH-R allows contractors to get the job done more quickly and efficiently. Our two-step process eliminates the need for grading and sweeping by placing the material right where it needs to go the first time.”
The remote-controlled attachment connects to most skid steers, compact track loaders, road graders and wheel loaders, operating off the host machine’s engine and hydraulics. It is available in left, right or dual dispensing configurations. The attachment is designed to streamline a variety of tasks including backfilling, road widening, road shoulder repairs, remediation and aggregate placement. The material is poured into the hopper at the top of the FH-R and then dispensed via remote control in adjustable lay down widths from 1 to 6 feet (0.3 to 1.8 meters). The attachment dispenses up to 20 tons of material in under 10 minutes.
“Our customers often tell us the swift capabilities of the FH-R have a tremendous effect on their business,” Guebard said. “With labor shortages spiking, contractors are often running with a lean crew. However, the demand for infrastructure remediation is only rising. The FH-R helps to solve this challenge by efficiently and precisely laying material with only one operator. Some of our customers can lay up to 5 linear miles a day with our machine, making it truly a gamechanger for any business, no matter the size.”
For more information, reach out to your local equipment dealer.
AsphaltPro’s advertiser index is designed for you to have quick access to the manufacturers that can get you the information you need to run your business efficiently. Please support the advertisers that support this magazine and tell them you saw them in AsphaltPro magazine.
Delivering mobile crushing, screening and conveying equipment to remote locations isn’t always easy, but the result pays dividends for socioeconomic growth. The service team for Powerscreen®️, a division of Terex Corporation, proudly announced in August the successful installation and operation of equipment in Ladakh, Northern India—one of the world’s most challenging environments.
A Powerscreen PT400X Jaw Crusher, 1000 Maxtrak Cone Crusher and Chieftain 1700 Screen were commissioned to work on a Border Roads Organisation (BRO) project near Demchok, close to the China border, at Umling La, Leh Ladakh (UT). At an altitude of 19,024 feet, this project is at the world’s highest motorable pass and is set to produce road construction materials such as granular sub base (GSB), wet mix Macadam (WMM), and aggregates sized 5 mm, 10 mm and 20 mm.
The site’s high altitude presented significant challenges due to low oxygen levels and temperatures, which dropped to -23°C during the project. Additionally, the terrain was hilly with sharp bends and no feasible roads, complicating the transportation and installation of the equipment on site. Powerscreen equipment has been designed and tested to withstand harsh environments— including high-altitude conditions.
The successful deployment of Powerscreen equipment at Umling La has enabled the BRO to produce the necessary materials for their road project, ensuring the continuation of vital infrastructure development in the region. The infrastructure will improve access to remote villages, making it easier for residents to travel for medical care, education and other essential services. The road will also facilitate the delivery of goods and services, contributing to the region’s overall socioeconomic development. The enhanced connectivity also boosts local businesses and tourism, with many tourists attracted by the world’s highest motorable road providing new income opportunities for locals through homestays, guided tours and local crafts.
For more information, visit: www.powerscreen.com
To navigate the rough terrain, the service team expertly dismantled the Powerscreen equipment for transport and reassembled it on site. Despite the extreme conditions, the service team completed the installation and commissioning in 15 days.
Astec revolutionized the paving industry with the introduction of the Shuttle Buggy, and now the SB-3000 sets a new standard in material transfer vehicles. Effortless maintenance, unmatched performance, and four steering modes for ultimate agility keep paving seamless. Experience groundbreaking innovation with the patented Ground Crew Control Station for the ultimate user experience and protection. The SB-3000 isn’t a machine, it’s a revolution in material transfer, built on Astec’s legacy of industry firsts.