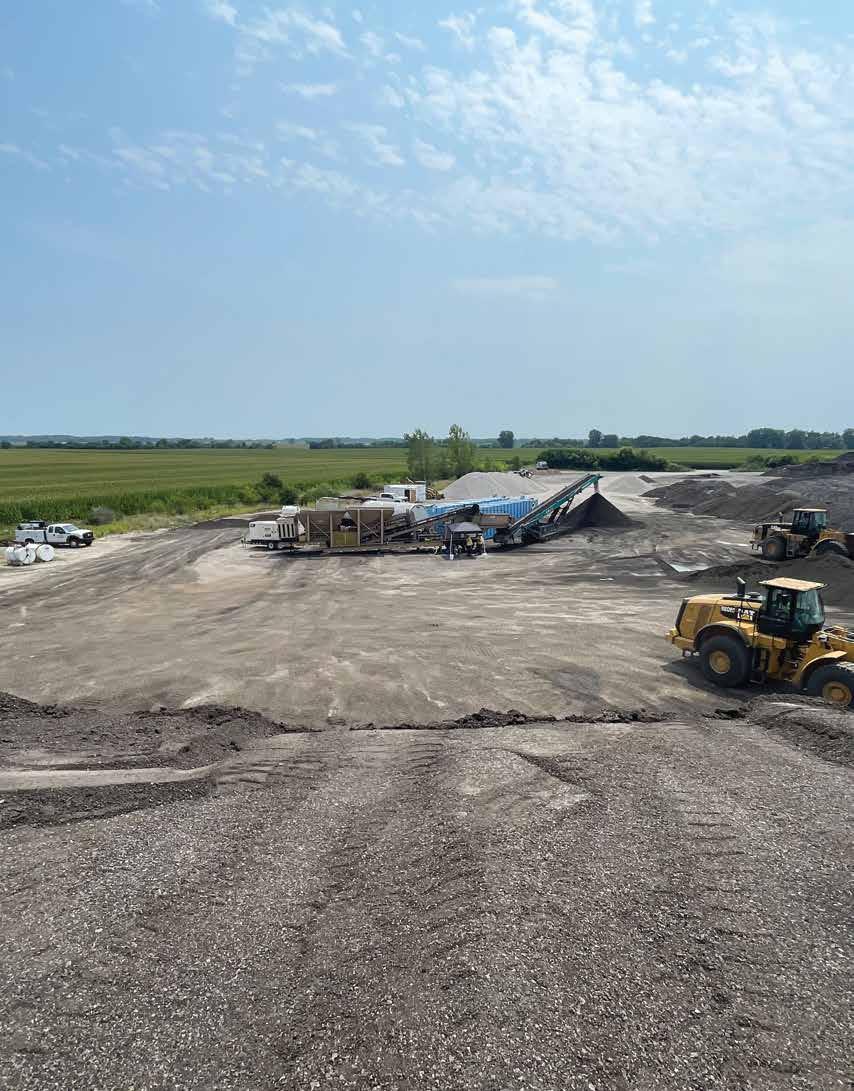
• 7 Habits of Highly Effective Safety Leadership • Your Mechanic Determines Spring Startup Success
• 7 Habits of Highly Effective Safety Leadership • Your Mechanic Determines Spring Startup Success
Astec paves the way for sustainable, innovative asphalt plants. The new IntelliPac Moisture System is a revolutionary solution that integrates seamlessly with Astec control systems. This provides unparalleled, real-time visibility into virgin aggregate moisture content. IntelliPac empowers operators to optimize mix design, minimize energy consumption, and reduce environmental impact. With Astec, you get superior asphalt production – better for the environment, better for your business.
The reverse air baghouse engineered to lead your plant to peak performance.
The Dust Pilot reverse air baghouse is built for high-capacity operations with precision airflow control and fewer moving parts, minimizing maintenance. Its robust, customizable design ensures cleaner air, enhanced plant performance, and compliance with environmental standards. Available in multiple sizes, the Dust Pilot delivers reliable and effective dust control tailored to your plant's needs.
EDITOR’S LETTER
6 – Help Industry Track Recycling By Sandy Lender
MIX IT UP
8 – Front Range AC Supply Gets a Boost By Alix Kendall
SAFETY SPOTLIGHT
12 – 7 Habits of Highly Effective Safety Leadership By Sarah Redohl
STREET SMARTS
18 – Best Paving Practices (When Conditions Aren’t the Best) Part 4: Issues with Equipment By
Bill Stanley
22 – Talk to Your Mechanic
No one will know what the equipment needs to prep it for spring startup if we don’t communicate this winter By John
Ball
PROJECT MANAGEMENT
24 – CCPR in Indiana
Embracing greener roadway strategy: cold recycling mix design at work By Olivia Kortepeter
PAVEMENT MAINTENANCE
30 – High-RAP Recycling By Jill N. McConaghie
WOMEN OF ASPHALT
34 – Meet Two Women of Asphalt: CAT Scholarship Recipients for 2024 By AsphaltPro Staff
INTERNATIONAL SNAPSHOT
37 – International Crushing
The first MT120J from MAGNA heads to Australia for large-scale operations From Terex
PRODUCT GALLERY
48 - Production From the Start From AsphaltPro Staff
THE MAT
58 – Asphalt Pavement Market Expands with Colorado Wins By Thomas Peterson, P.E.
38 – Focus on Performance A Review of Burner Emissions Control Means for Asphalt Plants By Malcolm Swanson, P.E. 44 – Assess Your Pugmill Health Here’s how to inspect the
It doesn’t seem as though an entire year has passed since I last wrote on the theme of responsible reuse of materials for our annual recycling issue. As luck would have it, the asphalt industry is still on an upward trajectory of using reclaimed asphalt pavement (RAP) in fresh mix designs to build and maintain the infrastructure of the United States. Let me give you a source and some numbers for that statement and let me direct you to the highRAP article prepared by the team at Sripath Technologies on page 30 of this issue.
First, I draw your attention to the annual Asphalt Pavement Industry Survey on Recycled Materials and Warm-Mix Asphalt Usage 2022, published by the National Asphalt Pavement Association (NAPA) in May 2024. This Information Series 138 report shares a ton of data, including the very basic idea that, yes, our industry continues to lead the way in environmental excellence through our reuse of materials. According to NAPA, “2022 data collected by NAPA showed 93 percent of asphalt mixture was used to construct new pavements, with the remainder going toward other civil construction applications...In total, asphalt mixture production increased by 2 percent from 2021 to 441.9 million tons.”
Here’s where I want to go off script for a minute.
The survey published in May 2024 includes data collected from 235 companies. Those companies pulled production data from a total of 1,305 asphalt plants, according to NAPA.
The U.S. Environmental Protection Agency (EPA) reports there are 3,600 asphalt plants in the United States. According to Jim Musselman of the Florida Department of Transportation, speaking at the December Asphalt Contractors of Florida (ACAF) winter conference, 100 of those plants pro-
duced mix for his state over the past year. That’s just Florida. Were all 100 of them included in the 1,305 of the 2022 survey?
My point is two-thirds of the industry’s data is missing, but those entities have an opportunity to contribute to something that benefits the industry.
One of the ways Behavior Expert Chase Hughes teaches to form good habits is through asking the question, “Is this going to benefit me later?”, before taking on a new task. Of course, I’ve never heard him suggest we forego helping one another if there’s no “benefit” to ourselves, but I have heard him remind his audiences of the satisfaction that comes from giving of oneself and helping our fellow man. The twist I’d like to give to Hughes’ teaching today is this: “Is this going to benefit the asphalt industry later?”
The report for RAP and WMA data collected in 2023 is coming up next from NAPA. But I want to encourage members of the industry to watch for the annual survey links that are posted around the Internet, including on AsphaltPro social media platforms, inviting you to participate in the survey. It’s anonymous. It doesn’t ask you to provide proprietary information that your competitors can use against you in bidding. Instead, it asks you to take a little time to share information that benefits an industry that is bigger than the individual. When you see the links for the 2024 RAP and WMA survey invitation, ask yourself, “Is this going to benefit the asphalt industry later?”
Stay Safe,
Sandy Lender
602 W. Morrison, Box 6a Fayette, MO 65248 (573) 823-6297 • www.theasphaltpro.com
GROUP PUBLISHER
Chris Harrison chris@ theasphaltpro.com
EDITOR
Sandy Lender sandy@theasphaltpro.com (239) 272-8613
DIGITAL EDITOR
Sarah Redohl sarah@theasphaltpro.com (573) 355-9775
MEDIA SALES
Cara Owings cara@theasphaltpro.com (660) 537-0778
ART DIRECTOR
Kristin Branscom
BUSINESS MANAGER
Susan Campbell (660) 728-5007
AsphaltPro is published 11 times per year. Writers expressing views in AsphaltPro Magazine or on the AsphaltPro website are professionals with sound, professional advice. Views expressed herein are not necessarily the same as the views of AsphaltPro, thus producers/contractors are still encouraged to use best practices when implementing new advice.
SUBSCRIPTION POLICY: Individual subscriptions are available without charge in the United Sates, Canada and Mexico to qualified individuals.
One year subscription to non-qualifying Individuals: United States $90, Canada and Mexico $125.00. For the international digital edition, visit theasphaltpro.com/subscribe/
BY ALIX KENDALL
The Hudson Asphalt Terminal (HAT), a new ground-up asphalt storage and distribution facility, is positioned to become a key supplier to the Colorado construction industry. Located at the BNSF Railway Logistics Center in Hudson, Colorado, the cutting-edge terminal will serve as a vital source of asphalt binder to area pavers in the Front Range, addressing local supply challenges and offering significant economic benefits. Cenovus Energy, a large North American oil and gas producer and refiner, is an important partner in the project as it provides a reliable supply of asphalt at the facility to help meet the growing demand for high-quality asphalt products in the region.
“Hudson Asphalt Terminal has been welcomed by the road construction industry as well as the community,” said Cenovus Director Asphalt & Industrial Products Martin Ray. “Cenovus is excited to expand to new markets, become a trusted supplier with area producers, and help support the region’s ongoing growth and construction needs with quality asphalt products.”
The HAT project is a strategic collaboration between multiple industry leaders, including Cenovus, BNSF Railway, ECF Inc., and Hudson Asphalt Terminal LLC. The initiative was driven in part by demand and
changes in the Colorado market. These changes left the region’s construction and paving industries with limited access to asphalt binder, a critical material for infrastructure development.
As an established North American producer of refined products, Cenovus entered the project as a key partner, recognizing the asphalt supply gap and demand for reliable product in the region. Cenovus saw an opportunity to provide asphalt products that are stored at and distributed through the Hudson Asphalt Terminal as well as use its expertise in refining and asphalt production to ensure a steady flow of asphalt binder for construction companies in the Front Range region. This, along with the company’s established infrastructure, played a key role in ensuring the terminal can meet the market demand.
The HAT officially broke ground on Sept. 25, 2023. HAT is a joint effort with ECF Inc., Columbia, Illinois, which specializes in asphalt terminal design and construction. ECF was tasked with building the facility, and Hudson Asphalt Terminal LLC, the operation of the facility. The project moved quickly from planning to execution, with the terminal receiving its first railcars of asphalt binder on July 10, 2024.
The terminal’s strategic location at the BNSF Railway Logistics Center offers graded, shovel-ready sites and advanced infrastructure,
With over a century of innovation to its credit, Blaw-Knox® pavers have earned a reputation for quality, durability, and performance unmatched in the industry. Our continued focus on innovation is what drives our product engineering with designs that improve performance while maintaining user-friendly, ergonomic comfort and reliability for the operator. BLAW-KNOX, THE LEGACY LIVES ON. For more information contact your Blaw-Knox dealer or visit www.blawknox.com
allowing for expedited development and helping the project meet its aggressive timeline.
With its completion, the HAT provides approximately 275,000 barrels of storage capacity, fed through two rail spurs with 20 railcar unloading spots, supporting two truck loading racks for outbound product.
Several companies played a significant role in the development and operational planning of the HAT:
1. Cenovus Energy: An integrated energy company with operations across the full value chain to develop, transport, produce and market crude oil and natural gas in North America and internationally. The company’s physically integrated upstream and downstream operations help mitigate the impact of volatility in the market by capturing value from production through to the sale of finished products, such as asphalt. Cenovus produces asphalt binder at its refining facilities and transports the product to the HAT for storage and distribution to Colorado’s construction industry.
2. BNSF Railway: The Hudson Logistics Center is owned and operated by BNSF, which plays a pivotal role in providing the rail infrastructure necessary for the transportation of asphalt. BNSF’s established network and favorable freight contracts allow the terminal to receive asphalt by rail, reducing transportation costs and improving the efficiency of the supply chain.
3. ECF Inc.: Responsible for the design and construction of the terminal, ECF Inc. leveraged its experience in building specialized asphalt facilities to ensure the terminal would meet the region’s storage and distribution needs. Their expertise was crucial to the fast-paced development of the facility.
4. Hudson Asphalt Terminal LLC: Responsible for operating the facility and providing terminal services to area customers in a safe, responsible manner.
The HAT is expected to provide significant and far-reaching economic benefits for both the local and wider Colorado economies.
• Job Creation: The construction and recent start of operations at the terminal has already created many new jobs in Hudson and surrounding areas and will continue to generate employment opportunities through direct roles at the terminal, as well as indirect jobs in logistics, transportation and supply chain management.
• Enhanced Supply Chain Efficiency: The terminal’s storage, railcar unloading and truck loading capacity will help address the supply challenges caused by the regional refiners transitioning to biofuel production. The terminal is designed to quickly distribute asphalt products to contractors and developers, reducing delays and inefficiencies in the region’s construction sector.
• Cost Impact: By sourcing asphalt through Cenovus Energy’s asphalt supply at the HAT, contractors will reduce their dependence on a limited number of refineries and avoid price volatility caused by supply shortages.
• Economic Development: It is anticipated that the terminal will attract further business development to the BNSF Logistics Center, creating additional opportunities for local businesses and boosting the economic profile of the Hudson area.
Hudson Asphalt Terminal LLC is responsible for operating the HAT and providing terminal services to area customers in a safe, responsible manner. At this time, the HAT supports two truck loading racks for outbound product.
The terminal’s storage, railcar unloading and truck loading capacity will help address the supply challenges caused by the regional refiners transitioning to biofuel production. The terminal is designed to quickly distribute asphalt products to contractors and developers, reducing delays in the region’s construction sector.
The HAT represents a vital investment in Colorado’s infrastructure, addressing critical supply chain gaps while supporting the region’s ongoing economic growth. The partnership between Cenovus, BNSF Railway, ECF Inc., and Hudson Asphalt Terminal LLC is an example of industry collaboration helping meet market demands to provide long-term benefits for local economies. By storing and distributing high-quality asphalt binder and streamlining regional supply chains, the HAT will be essential in the development of Colorado’s infrastructure for years to come.
BY SARAH REDOHL
What does it take to be recognized as a leader in safety?
For Granite Construction, Watsonville, California, the answer lies in a commitment to continuous improvement and a culture that prioritizes safety across all levels of the organization. In 2024, Granite Construction was honored by the American Road & Transportation Builders Association (ARTBA) as the Grand Champion in the over 1 million personnel hours category of its Contractor Safety Awards.
“The judges were impressed with Granite’s empowerment of their workers to enhance safety on every work site, as well as its communicating safety concerns and solutions to its employees,” ARTBA wrote.
Let’s take a look at Granite’s award-winning approach to safety through these seven habits of highly effective safety leaders.
Granite’s safety culture thrives on full organizational buy-in, from leadership to workers in the field. “From the C-suite to our craft professionals, everyone in our organization prioritizes the importance of both employee safety and motorist safety,” said Granite Senior Safety Manager Wendy Warner.
This is evidenced by Granite’s Craft Safety Connection concept, where employees from a variety of trades within the organization gather regionally each month to discuss events in the organization and provide feedback from the field.
“Craft Safety Connection is the platform through which our employees have a voice about the changes we’re making and can suggest changes themselves,” said Granite Corporate Compliance Safety Director Jesse Torres. “They usually know how to fix the issues they’re facing better than anyone.”
Another recent safety success story is the Granite Guard initiative, which introduced a minimum safety standard for small tools across the company. This includes a company webshop where Granite employees can select replacement equipment for their crews that has been thoroughly vetted to ensure it meets Granite’s safety standards for hand tools. Like the Craft Safety Connection, this initiative heavily relied on input from craft employees.
“In 2022, the equipment and safety departments came together to discuss the ongoing safety issue of lacerations on the construction site,” Torres said. Granite crews spent one year testing different tools and reporting their thoughts on various safety features. “Based on their experiences, we identified a group of tools—many from Milwaukee Tool—
that have safety features our employees prefer, including dual handed triggers, rapid-stop features, anti-bind and auto-stop features, etc.”
In the future, Granite plans to expand Granite Guard to include a broader variety of hand tools, including plate compactors.
Granite was also recently recognized by the Associated General Contractors (AGC) of California with a Construction Safety Excellence Award (CSEA) with an award for general safety in the over 1 million personnel hours category, as well as an award for safety on a high-hazard project for its work on the BNSF Railway, San Bernardino Mt. Vernon Bridge Replacement Project.
Safety is also a priority for all departments within Granite. “Safety isn’t just for the safety team,” Warner said. “It’s marketing, accounting, payroll. It’s everybody.”
For example, the marketing department is heavily involved in safety, producing safety-related content for daily toolbox talks as well as special initiatives such as Construction Safety Week.
“We put together videos with safety leaders across the company and got employees to write articles about specific safety efforts,” said Granite Marketing & Communications Manager Mark Philllips. “We’re constantly sharing safety messages through our social media posts, flyers that go out to our job sites, our quarterly employee magazine and more.”
The benefits team is also involved in safety. In light of data showing high rates of suicide in the construction industry, Granite’s benefits team has expanded the company’s benefits package to include up to
eight free and optional counseling and coaching sessions per year for each employee and covered family member through Spring Health. Safety messages even come from the accounting team in the form of paycheck stuffers on safety subjects.
Granite plays an active role in promoting safety across the construction industry. The company was a founding member of Construction Safety Week in 2014 and continues to play a significant role in CSW each year. Granite employees also participate in the Construction Industry Safety Initiative, where they regularly meet up with other construction companies to discuss safety topics. “It’s an opportunity for us to share what we’ve learned and push other companies to be better, and for them to share what they’ve learned and push us to be better,” Warner said.
“One of the most impactful initiatives was sitting down in 2018 to put together a safety strategic plan for the entire company,” Warner said. “That plan has allowed us to stay focused on our goals.”
The strategic planning process began by looking at the company’s safety data to identify areas of concern and opportunities for improvement. “We want to focus on leading indicators versus lagging indicators so we could be more proactive in our approach,” Warner said. To do so, the company utilized HCSS safety management software to record daily toolbox talks, employee observations, inspections, near misses, etc.
“All that data is captured, analyzed and organized into a scorecard of leading indicators and performance indicators,” Warner said. “Each
region’s management team reviews their data with their frontline supervisors on a monthly basis to analyze and address those trends.”
Granite set a target to reduce its OSHA recordable incident rate from 1.07 in 2020 to 0.70 by 2023. Ultimately, Granite exceeded its target, achieving an OSHA recordable incident rate of 0.67 in 2023.
After reviewing historical safety data and discussing with employees, Granite was able to compile a list of activities with a high potential to cause employees harm. Rather than write and distribute this list, they decided to create a system that would stick with employees.
“We call it STCKY: Stuff that can kill you, other companies call it ‘High Energy Hazards,’” Torres said. “It’s not a new program, it’s just an enhancement of our existing program to keep it simpler than the usual 600-page Standard Operating Procedure rulebook.”
At the beginning of each shift, the crew meets for a toolbox talk and together identifies all the STCKY hazards on that day’s job site. “It’s a daily assessment of dangers,” Torres said. “The goal is to point out all the sticky hazards and discuss how they plan to handle them.”
Every employee on Granite’s crew has stop-work authority. Ensuring employees have the authority to speak up is one thing; Granite’s approach also prioritizes listening through its Speak Up, Listen Up initiative.
“That was a training module with Caterpillar Safety Services that we incorporated into our organization 10 years ago that continues to live on,” Torres said. “We want our employees to know they can speak up when they see something unsafe,” Torres said, “but also to listen when they’re getting feedback.”
Supervisors undergo training on the Speak Up, Listen Up initiative as part of Granite’s “robust supervisor training program,” Warner said, which includes training on Granite’s behavior-based safety approach. Behavior-based safety is an approach to workplace safety that focuses on observing, analyzing and modifying employee behavior for improved safety.
“Our supervisors are phenomenal at what they do, but they’re not trained public speakers,” Warner said. However, they are expected to lead toolbox talks at the start of each shift. That’s why Granite implemented Take 5 scorecards, where its safety professionals will go out in the field to provide feedback to supervisors on how to make their toolbox talks more effective and engaging.
“IT’S NOT A RACE TO BE NUMBER ONE IN SAFETY. IT’S ABOUT HELPING THE INDUSTRY AS A WHOLE TO BE SAFER.”—JESSE TORRES
A few years ago, Granite changed the way it approached incidents. “We changed our process from one that was focused on fault-finding, where people felt as though the goal of the process was to get them in trouble, to a collaboration to figure out and fix the root cause,” Warner said. Instead of performing incident reviews, Granite now has a Collaborative Learning Event (CLE) after significant incidents. “That approach encourages people to come up with solutions rather than excuses.”
The difference between an incident review and a CLE, Torres said, is asking better questions. “All our safety leaders read the book ‘Better Questions’ by Todd Conklin to try to get a picture of the full story, not just the event itself,” he added. “We’ve also done some micro learning training on the CLE process and how it’s more about helping each other versus blaming each other.”
Granite Guard, the webshop of safer hand tools, was an idea that began during a CLE.
“If I had to summarize Granite’s safety culture in one word, I’d choose ‘evolving’,” Warner said. “We are focused on continual improvement.”
Granite’s Construction Technology Team is heavily invested in trialing technology that can improve safety at the company. “Right now, they’re testing out various AI platforms that could assist with safety assessments and analyzing data,” Phillips said. “They’re looking at proximity sensors for work zone intrusions and about a dozen other cutting edge safety solutions.”
Investing in new technology is one part of it, but the other part of it is never remaining stagnant when improved safety is on the line. This approach is evident in Granite’s recent transition from hard hats to safety helmets for all its road construction crews.
“Hard hats haven’t been revamped in 50 years,” Warner said. “But, in that same period, football helmets have constantly changed and implemented new technology to reduce head injuries.” Unlike hard hats, helmets offer protection from side impacts and are more likely to remain on one’s head in the event of an accident.
Granite looked to its vertical construction crews, who had already been using helmets, for advice and best practices. They purchased some leading helmet options and let their heavy civil employees test them out. “We wanted to know how they fit, how they felt, does it stay on, is it too hot, too bulky,” Warner said.
“The idea to implement helmets was top-down, but we wanted the employees to have a say, too,” Torres added.
“We really tried to get the message across that this is an investment we’re making in our employees’ safety,” Torres said, adding that it wasn’t cheap at $100 per helmet times 10,000 employees. “But the brain is the most important part of our employees’ bodies, and it’s worth investing to protect them.”
Over the past 18 months, Granite has made an effort to identify women-specific PPE for its employees, “so women in the field can request PPE that actually fits them,” Warner said. This includes partnering with Zena Workwear so Granite’s employees can get a discount on the best steel-toed boots to fit their feet.
Ultimately, Granite hopes that its safety evolution will inspire other companies to take the next step in their safety journey. “I like to think that we’ve been able to positively influence work zone safety at a local and national level,” Warner said. “And I’m honored to have the opportunity to share some of the things that have worked for us at Granite.”
WITH OVER 30 YEARS’ EXPERIENCE IN THE ASPHALT INDUSTRY, we have the knowledge and expertise to help you reach your goals without breaking the bank. Specializing in locating and retrofitting any equipment you need, we are all about upgrading your asphalt plant to maximize output and efficiency — with less lead time than others! Talk to us about your next project.
• PLANT RELOCATION / CONSTRUCTION
• PLANT MAINTENANCE
• CONSULTING
• NEW/USED PARTS
• NEW/USED EQUIPMENT
• INDUSTRIAL INSULATION SERVICES
• HOT OIL PIPING & AC PIPING
• SILO & TANK CLEANING
BY BILL STANLEY
We had our paver break down on one of our jobs last summer. The paver itself was fine, but one of the sensors started acting up. No one on our crew knew where this sensor was, or that it even existed, until it shut down our project as five loads of asphalt sat in the middle of the parking lot, waiting to be paved.
Eventually, we found the problem—a loose wire. We jiggled it and everything started working again just fine. But it took us an hour to locate. Since it was summer, the asphalt was still hot and we had plenty of daylight left. We were able to stay late and get everything paved before heading home around 7:30 p.m.
That $12 sensor cost me some overtime, but if it had gone out on a colder, shorter day, we’d have had a real problem on our hands. There’s no way we’d be able to pave all that asphalt in the dark and cold and still leave our customer with a quality product. That sensor might have cost me a loyal customer or else $10,000 in wasted asphalt.
Your typical paving company might be able to take a loss like that every once in a while and stay afloat. But taking that kind of loss once a week? Or taking an even bigger loss once a year? That could be enough to sink even a successful company like ours.
When you’re handling a perishable product like asphalt, an equipment breakdown can end up costing a whole lot more than the cost of the replacement parts. Here are my best practices for maintaining equipment—and what we at American Pavement Specialists do in the event of a breakdown.
We prefer to stick to certain brands we’re familiar with, but at the end of the day I don’t care much about the name on the machine. All machines are going to break. What I care about is the service I’ll get when that happens. We look for brands who partner with dealers we know we can rely on. We want a dealer that answers the phone when we call, stocks every part we need, has skilled mechanics
When you’re handling a perishable product like asphalt, an equipment breakdown can end up costing a whole lot more than the cost of the replacement parts.
and technicians, and has auxiliary equipment available to us if we need it.
There are two reasons we buy new equipment. One, when there’s new technology we think is important to our jobs or the industry is requesting. Two, when that machine starts seeing heavy wear. If it’s a staple piece of equipment, like a paver or a roller, we’ll swap them out pretty early regularly.
When it comes to preventative maintenance, it’s obviously important to pay close attention to all your service intervals. It’s also important to perform daily, weekly, monthly preventative maintenance on your machines. A clean piece of equipment will typically run better. That buildup on your machines makes them run hot, so if you aren’t keeping your equipment clean that decision will come back to bite you. Do you want your machine to overheat and shut down when you’re in the middle of a big job on a hot day—because you haven’t taken the time to clean your machine properly?
Another aspect of preventative maintenance is to train your operators to get to know the quirks of their machines. A skilled operator who uses the same machine regularly may be able to hear or feel a problem before the sensors or error codes even go off!
This is another reason why we tend to be brand-loyal, even though I don’t care much about the name on the grill. Once you run a machine for a couple of years, you begin to understand its quirks and can better prepare to get ahead of them.
When we come across an issue on the job, our crew is pretty mechanical and can often fix issues themselves—unless it’s something a technician needs to fix. A lot of modern machines will throw codes that shut down the machine, and you need a technician trained by the manufacturer to resolve those. Last summer, we had a machine go down and the technician was able to diagnose and resolve the problem from his phone! For problems in between what our crew can do themselves and what requires a technician, we have a local mechanic on speed dial.
When we’re on a job that’s far from our yard, we make sure to bring common replacement parts to the job. This gets easier when you get to know the quirks of your equipment. For example, we have a beautiful paver that we love running, but the O-ring on its hydraulic pump breaks pretty often. The first time it broke, it took us a while to locate the issue. It’s an $0.80 rubber seal, but it’s an important part of the machine. One month later, the O-ring broke again. Another month later, it broke again. We started bringing spare O-rings with us on every job.
Stocking up on spares doesn’t stop with parts. On particularly important jobs, jobs far from our shop, or when paving in cold weather, we might even bring a spare paver or roller to the jobsite. Just the other day, we were on a project and the paver broke down. Because we had our spare paver on that project, it wasn’t a problem to heat it up and swap it out until our primary paver was repaired.
If you don’t have auxiliary equipment, you still need to have a backup plan. My rule of thumb is the more trucks you have on a job, the more important it is to identify auxiliary equipment ahead of time. Other factors I consider are the importance and timeline of the job and its proximity to our shop and our dealers’ auxiliary equipment.
Know your local dealers and who has what equipment for you to rent on a moment’s notice. Consider friends in the industry you could call on to borrow something in a pinch. Over the years, I’ve built good rapport with other contractors in our areas. It’s not unusual for me to get a call about borrowing spare equipment.
Not too long ago, I got a call at 6 p.m. on a Friday from a contractor from Pennsylvania who was paving in our area. His brand new paver had broken down, he didn’t know how to fix it, and there was $20,000 of asphalt waiting to be paved on a big parking lot job. Sure, I could have been mad about the extra competition coming from out of state, but I wouldn’t wish that situation on my worst enemy. We brought over a spare paver, it saved his project and I made a friend.
Last year, a friend of mine who runs a large asphalt paving company called me with a
“We prefer to stick to certain brands we’re familiar with, but at the end of the day I don’t care much about the name on the machine,” Stanley said. “All machines are going to break. What I care about is the service I’ll get when that happens.”
huge job to pave a stretch of a highway. It was a simple job that paid very well, but I turned it down. The job was scheduled for the very end of the paving season, placing 8,000 tons from Friday night to Sunday night.
To feel comfortable in those conditions, I knew we’d need backups of every piece of equipment that we just don’t have. We’ve paved highways before, but it’s not something we do every day, so we only have one highway paver. That wouldn’t have been a problem if the job were happening in the summer, when I’d have enough time to find a solution to any problem that might come up. But the truth was I didn’t have the equipment I needed to do that job that time of year.
Maybe nothing would have gone wrong on that project and we’d make a bunch of money in one weekend. But maybe every-
thing would have gone wrong and the project wouldn’t be up to the standards we set for ourselves. No one who’d ride that highway would know the terrible conditions we were paving in. Bad weather, a tight timeline, long lines at the plant, or a broken paver. All they’d see is the end result and judge us for it.
If I’d had that offer when I was younger, I would have jumped at the chance no matter the time of year. Now that I’m older and wiser, I knew it was a risk I shouldn’t take. I’d rather protect my reputation than have that money (or risk losing money, if something went wrong).
I’ve seen a lot of paving done wrong in my career. I’ve paved in all kinds of conditions. I’ve made mistakes and learned from every single one. Experience is the only real way to learn the best paving practices for when conditions aren’t the best—but I hope this four-part series has given you a bit of a shortcut to that experience.
BY JOHN BALL
No one will know what the
equipment
needs to prep it for spring startup if we don’t communicate this winter
hen we’re talking about maintenance—with the paver or the roller especially—we’re also talking about mat quality. When I look at a paver, I focus on two categories—the screed and the tractor. These two main components affect the quality of the mat you’re placing; both have to be in optimal working order if you want a top quality mat. Both are on the mechanic’s mind when he gets started on winter maintenance.
When the mechanic enters the garage in January or February, he’s not going to know what might have been going wrong with the paver last season. Why? Because no one communicated it to him.
Even with telematics and fancy apps that automatically ping him about how many hours the paver has worked and when it’s time to grease a joint, no one stopped to tell him about a driver smashing the screed on the lowbed or the depth crank getting loose in its sleeve or the time the extension folded in and pinched the feed sensor’s wire. Those important things get lost in the day to day and add up to poor production for the paving crew, and they surprise the mechanic during the winter maintenance season if we don’t tell him about them.
The lowbed drivers have beat up the screed platforms of this paver. The crew has learned they can’t have the left platform in place when the screed is lowered for paving or this element will drag and leave a gouge in the mat. The middle piece that you see in this picture is a tripping hazard. The mechanic has to order new parts to repair this problem for the crew.
The wire for the feed sensor will extend and flex but you still want to pay attention to it. Keep asphalt from building up and burying it. Make sure the extensions don’t pinch or damage it. Watch out for both the wires and the sensor itself when shoveling or manipulating mix near the endgates so you don’t damage these expensive components. But if something happens to damage them, let the mechanic know right away. These elements are in place to help you get a quality mat; don’t wait until winter downtime to surprise your mechanic with their need for repair.
We need a system in place to forewarn the mechanic, telling him to order a new screed platform to replace a bent one so the broken one isn’t digging into and marring a mat we’re trying to build. And we need to use that system, communicating with the right people to get action when action is needed.
For example, when I noticed the lower scraper bar was missing on the back drum of one contractor’s breakdown roller, I asked the operator about it. His response was that he had informed a foreman about the missing scraper bar a few times already. But the foreman didn’t recognize the importance of the problem. He wasn’t the right person in the chain of command to do anything about the problem, the roller consistently used more water from the back tank than the front, and the machine went without a repair for months.
This is unacceptable, but the operator couldn’t get help with the problem until we went to a supervisor who had direct communication with a mechanic who could order the replacement part.
Inside the red circle, you can see the bracket for the scraper is still in place, but the scraper bar itself has been knocked off by incorrectly loading onto the lowbed. While the roller can still operate and still get compaction, it’s not efficient like this. There are two scraper bars on the drum for a reason: each bar collects and spreads the water across the width of the drum to lubricate the drum and assist in keeping it from picking up material as you compact the mat. When you remove one of these, you remove that device from either the forward or back motion of the rolling pattern.
Here’s a Quick Tip:
Spray Pledge furniture polish in the paver’s extender cylinders so they slide out smoothly and properly.
You have to deliver a note—and usually it’s done at the end of the year—from the equipment operator to the mechanic, sharing what they think is broken or needs repair. Besides the mechanic using the manufacturer’s list of what needs to be done at 500 or 1,500 hours, for regular wear-n-tear, to check pump pressure, to replace seals, to check conveyor chains, and so on, he’ll also use a list from the operator of the piece of equipment. I have a maintenance sheet that I had at Pike Industries that I used for years and years and AsphaltPro has a paver maintenance checklist, a roller maintenance checklist, a crusher maintenance checklist and even a plant maintenance checklist at the magazine’s Digital Downloads page.
https://theasphaltpro.com/ digital-downloads/
When we hand these lists of what we see going wrong to the mechanic, they include more than what you see flagged in an app or a telematics report. If I have a frayed wire, that may not come up. The telematics might pick up there’s a hydraulic leak, but not that there’s a failing O-ring. You must have the operator’s input to understand what’s going wrong and where with the piece of equipment he’s operating day in and day out. He’s using a special set of tools to notice when something needs to be scheduled for the mechanic’s attention.
The operator’s tools:
• His eyes to look over the machine
• His nose to smell oil, fuel, exhaust
• His ears to hear when something has changed, for example if the bearings in the tamper start to squeal
• His hands to write down a note to assist the mechanic
• His common sense and a few years of training
In the end, the mechanic starting his winter season maintenance on the paver,
roller, sweeper, material transfer vehicle or other equipment will have his best chance at setting the crew up for springtime success if the crew has made notes for him. If the paving crew and maintenance crew work hand in hand and with the operators’ notes—with telematics, apps, tablets, paper-and-pencil and phone calls to discuss the fine details—then the whole team can
return in the spring with optimized, safe, efficient equipment to get a top quality mat right off the bat.
John Ball is the proprietor of Top Quality Paving & Training, Manchester, New Hampshire. For more information, contact him at (603) 493-1458 or tqpaving@yahoo.com.
Here the team paves the first of two 3-inch lifts of cold central plant recycling (CCPR) mix made with AMICYCLE, a specially formulated emulsion. All images courtesy of AMI
BY OLIVIA KORTEPETER
Across the United States, road management agencies are moving beyond conventional repaving methods, embracing cold pavement recycling treatments to reduce environmental impact and stretch their budgets further on critical infrastructure.
Since 2018, the Indiana Department of Transportation (INDOT) has specified Cold Central Plant Recycling (CCPR) treatments on six state route rehabilitation contracts. Their treatment selection has been crucial to project success, through thoughtful consideration of options paired with an understanding of the in-situ pavement structure and the long-term needs of the network. In adopting CCPR as a rehabilitation technique, INDOT has gained a cost-effective, reliable and sustainable solution.
CCPR begins by milling reclaimed asphalt pavement (RAP) from a roadway and storing it at a nearby stockpile site. Often, with the majority of asphalt pavement removed, more invasive work can be done below the pavement whether utility excavation, subgrade treatment, or testing and inspection of underlying materials. Upon completion, a mobile mixing unit (pugmill) at the stockpile site blends the sized RAP with an asphalt emulsion, creating the CCPR mixture. The resulting mixture is then re-
turned to the roadway as an intermediate pavement lift, reducing the demand for new materials.
One of INDOT’s earliest and largest CCPR projects took place on State Route 236. During the 2021 and 2022 construction seasons, contractors collaborated to transform 13.36 miles of a narrow road with yielding subgrade into a wider, stabilized pavement structure topped with a hotmix asphalt (HMA) surface course.
To minimize disruption, the project was executed in phases to accommodate local traffic. Each segment followed a multi-step rehabilitation process lasting approximately two months:
1. Sampling and Mix Design: Pavement engineers took samples of the roadway material. In a lab, they designed and tested the correct composition of materials to create the new paving mixtures.
2. Milling Existing Asphalt: The asphalt was milled to a depth of 8 inches, and the RAP was transported to a central processing yard no more than 10 miles from the site, minimizing haul times and emissions.
3. Full Depth Reclamation (FDR): A nominal 3 inches of corrective aggregate was added to the exposed road base, then pulverized to a depth of 10 inches and stabilized with Portland cement.
4. Creating the CCPR Mixture: The RAP was crushed, screened and sized to the required specifications before being mixed with
a specially formulated engineered asphalt emulsion in a specially designed mobile mixing plant.
5. Paving and Layering: Trucks delivered the CCPR mixture back to the job site, where it was laid in two 3-inch lifts using standard paving equipment. A 2-inch HMA lift was applied as the surface course, followed by permanent pavement markings. This process not only optimized material reuse but also demonstrated the adaptability of CCPR in combination with other treatment types to tackle a variety of roadway conditions in a manner reflective of reconstruction.
Asphalt Materials Inc. (AMI) developed this specially formulated emulsion, branded as AMICYCLE. The CCPR mixture was sampled in the field and then laboratory-designed by Heritage Research Group (HRG). Their mix design was specific to the materials present and the construction details specified in the project plans. Quality Control (QC) for the CCPR was also overseen by HRG, ensuring the mixture met the standards outlined by the specification.
In the lab, the RAP was crushed down and mixed with the engineered emulsion, which can be adjusted based on the expected temperatures and haul times, to produce 4-inch-diameter (100 mm) specimens for
testing. The team created these specimens from both a medium and fine gradation, each mixed with three different levels of emulsion content. These six combinations underwent compression by a hydraulic press to test for stability and rutting resistance. Testing ensured the mix met durability standards before full-scale production.
With the optimal mixture selected, the HRG team worked closely with the pugmill operator to ensure the CCPR mix was precise, following the specifications outlined by INDOT for mix design and testing. HRG performed QC checks on the RAP gradation and mixture ratios throughout the process to ensure accuracy.
The mobile mixing plant (pugmill) used for the CCPR was custom-built by Pugmill Systems in Columbia, Tennessee. “AMI commissioned this unit to fit a specific combination of criteria not met by other machines on the market: tons per hour, ease of transportation and variable temperature handling,” said AMI’s Bruce Wehr. “[This] pugmill was designed to process a higher volume, up to 300 tons, of material per hour. Even with increased machine capacity and size, the unit was built with less weight so it could be hauled without permits, unlike many other pugmills. Finally, this machine had a wide operation range for liquid temperatures, handling materials ranging from CCPR at 100 degrees to Cold Patch at about 300 degrees. The Allen Bradley operating controls and mass flow meter allowed for this diversity of temperatures. With these capabilities, AMI’s custom mobile mixing plant was optimized for CCPR production.”
Once the CCPR mixture was placed, nuclear density gauge testing was performed to optimize the mixture’s compaction to ensure
consistency and long-term performance. HRG monitored the curing of the CCPR lift, which can range in duration from 2 to 10 days, depending on environmental factors. INDOT specification requires the CCPR mat to reach a moisture content below 3.0% prior to HMA paving. The roadway was opened to local traffic immediately following the finish rolling operations.
Besides this meticulous testing and QC, continuity was another key to success. The same team that sampled the roadway’s millings also designed the mix and performed quality control throughout the entire process.
The success of this ambitious project was made possible through collaboration. After the prime contractor, Milestone, crushed and sized the RAP stockpile, AMI, HRG and Pavement Maintenance Systems (PMS) managed the creation of the CCPR mixture at the central processing yard. PMS’s John Seabrooks operated the mobile mixing plant, while Wehr and Tim Zahrn of AMI supported the process, with HRG engineer Zach Robinson, who designed and tested the product mix.
CCPR offers an alternative to conventional construction methods. For State Route 236, CCPR worked in place of an additional stone base and intermediate HMA layers. By using 100% of existing materials and reducing transportation costs, CCPR was 30% more cost-effective for the
state than its HMA counterpart. The combination of FDR and CCPR also allowed for treatments at greater depth but at a lower cost per square yard, resulting in cost-effective, long-term pavement performance.
"If designed appropriately and used in the correct application, CCPR has comparable durability to traditional treatments,” explains Zach Robinson, Senior Engineer of Pavement Research at HRG.
On top of cost-efficiency, CCPR reduces greenhouse gas emissions by up to 50% compared to conventional construction methods, positioning the technology at the intersection of smart economic decisions and greener solutions. In recent years, the federal government has begun incentivizing carbon-conscious materials and offering grants to support the reduction of greenhouse gases.
INDOT has secured several grants that underscore the state's commitment to environmentally conscious practices. The Federal Highway Administration's "Climate Challenge" grant will help benchmark the environmental impact of pavement materials. Meanwhile, the funding awarded to INDOT from the Low-Carbon Transportation Materials (LCTM) grants program will support the adoption of materials and products with lower embodied carbon. By expanding its cold recycling initiatives and actively capturing federal funding, INDOT is steadily advancing its sustainability goals.
Indiana is one of many states committed to adopting more sustainable practices, including improving energy efficiency and reducing reliance on traditional material resources. Cold recycling treatments like CCPR support the components of a strategic and sustainable infrastructure plan, helping states improve their pavements while reducing lifecycle emissions.
CCPR is gaining traction across the Midwest. Beyond INDOT's six projects, PMS and AMI have completed more than 10 CCPR projects in Ohio, Michigan and Illinois. In addition to states in the Midwest gaining traction with these processes, the Virginia Department of Transportation (VDOT) continues to lead with their adoption of cold recycling into highway reconstruction projects like I-81 and I-64. Their work further demonstrates the successful use of cold recycling technology on higher-volume interstates.
The SR 236 project showcases how innovative techniques like CCPR can redefine modern road construction. By combining cost efficiency, sustainability and adaptability, CCPR not only strengthens infrastructure but also reduces environmental impact.
As more agencies recognize the long-term benefits of cold recycling, its adoption is likely to grow — paving the way for greener, more resilient roadways across the nation. With key players like INDOT, AMI and HRG leading the charge, the future of sustainable infrastructure is promising.
BY JILL N. MCCONAGHIE
Using asphalt to pave U.S. roadways is nothing new. But what has fast become a fresh focus for the paving industry are new ways to sustainably develop and maintain those roadways.
From transport agencies to contractors, minimizing carbon footprint without sacrificing performance has become an industry imperative. The National Asphalt Pavement Association (NAPA) included sustainability in its 2023-2025 Strategic Plan, and National Highways, the primary transportation agency in the United Kingdom, has established a goal of net zero emissions from construction and maintenance of roadways by 2040.
Asphalt is not only prominent in global usage—ResearchAndMarkets.com estimates it will reach 225.9 million tons by 2030—but it also remains one of the world’s most recycled materials. NAPA’s “Asphalt Pavement Industry Survey on Recycled Materials and Warm-Mix Asphalt Usage 2022” extrapolated, in the Unites States alone, 98.1 million tons of reclaimed asphalt pavement (RAP) were used in mixes in 2022, a 75.2% increase in usage since 2009.
Critically, positive environmental outcomes are a direct byproduct of increased RAP use. Per NAPA, incorporating RAP in asphalt mixes also reduced greenhouse gas (GHG) emissions by 2.7 million metric tons of CO2e in 2022, equivalent to the annual emissions of 600,000 passenger vehicles. The solution to more sustainable roadways is more than a one-to-one swap of virgin materials for RAP.
RAP is produced by removing existing damaged roadway surface material that has aged due to exposure to high traffic and environmental conditions. With milling anywhere from the top 2 inches of surface all the way to full-depth reclamation of up to 10 inches of material, RAP can take on many shapes and compositions. When processed properly, RAP is screened, crushed and fractionated to create a homogenized pile that can be used in an asphalt mix.
Typically, the binder within the RAP particles has aged over time and has lost its key functional characteristics. It no longer be-
According to FHWA’s “User Guidelines for Waste and Byproduct Materials in Paving Construction,” from FHWA, roadway milling produces over 45 million tons of RAP in the U.S. annually. Photo courtesy of Sripath Technologies
haves like virgin binder. In such a case, the RAP particles behave like black rock and are effective only as a replacement for aggregate. In the past, this has resulted in limited use of RAP in an asphalt mix.
In its document “Asphalt Pavement Recycling with Reclaimed Asphalt Pavement (RAP),” FHWA defines a high-RAP mix as any containing over 25% RAP, and NAPA’s research showed a national average of 22.2% RAP usage through 2022 in the Unites States. Of RAP produced in Europe, a document at the National Library of Medicine titled “The Challenges of Using Reclaimed Asphalt Pavement for New Asphalt Mixtures: A Review,” shows 51.4% was used in hot-mix or warm-mix applications with 9.63% finding its way to landfills.
Over recent years, the availability of asphalt rejuvenators or recycling agents has
helped contractors incorporate higher levels of RAP into asphalt mixes. An effective rejuvenator rapidly penetrates the RAP particles and restores the functional properties of the aged binder. This allows the bitumen in RAP to behave as an effective binder, allowing higher levels of RAP to be incorporated into the mix. This also results in the need for reduced levels of virgin bitumen.
The interest in high-RAP mixes that meet desired performance requirements through balanced mix design (BMD) approaches has grown considerably. BMD is a method engineers use to formulate asphalt mixes that addresses multiple modes of distress taking into account mix aging, traffic conditions, location and climate. It typically involves balancing the fracture toughness and rutting resistance properties.
Silo cone opening is 36” wide for ef cient material ow.
Safety gates on all silos, including long-term and standard options.
Recessed tub liners prevent silo wall wear, avoiding bulging issues.
Silo bin top batchers feature secure long-term seals.
Recessed wireways on silo tops eliminate trip hazards.
Meeker drag conveyors are larger, allowing slower chain speed and reduced wear.
Hydraulic chain adjustment on slats maintains asphalt entry point, minimizing wear.
Visual chain tension indicators on Meeker slat conveyors aid operators.
All silos prewired with top and bottom junction boxes.
This approach also affords mix designers with the opportunity to incorporate higher amounts of RAP into their mixes through the use of an effective rejuvenator or recycling agent. The result can be mixes that incorporate high amounts of RAP, up to 100% in some instances, when dosed with an effective rejuvenator.
A good recycling agent not only supports high-RAP content in mixes, but it also preserves roadway performance and durability, lowers the amount of virgin bitumen required, and helps reduce the overall cost. The result is often a more sustainable approach to paving alongside a more economical and high-performing material.
Roadways incorporating high amounts of RAP are becoming more commonplace across the paving industry as departments of transportation and contractors focus on achieving their sustainability goals. To achieve these objectives, it is essential to utilize an effective rejuvenator that helps restore the functional properties of the aged RAP binder and helps reduce the overall carbon footprint.
Not all recycling agents are created equal when it comes to performance. Some are less effective in restoring the functional properties of the aged RAP binder than others. In addition, some can pose challenges that run counter to sustainability goals.
Biobased oils, such as Sripath’s ReLIXER, have a strong track record as an effective asphalt rejuvenator or recycling agent. Such rejuvenators can effectively restore the functional properties of the aged RAP binder. Made from bio-based oils produced
Additional References
from cultivated crops that do not impact food sources, such rejuvenators are uniquely designed with sustainability in mind. Leading rejuvenators, like ReLIXER, have comprehensive certified Environmental Product Declarations (EPDs) easily accessible online. Such rejuvenators have a negative value for Global Warming Potential (GWP). As an example, the GWP for ReLIXER is -1.45, demonstrating the product’s ability to help reduce the environmental impact and overall carbon footprint.
A variety of real-world applications have demonstrated ReLIXER’s ability to increase RAP mix content without compromising roadway surface performance. One demonstration trial conducted in New York City showed a 100% RAP mix dosed with ReLIXER exhibited outstanding mix properties without the need for any virgin binder. The 100% RAP mix dosed with just 0.55% ReLIXER met or exceeded spec-
ifications when evaluated for compaction (Marshall Test), rutting (Hamburg Wheel Tracking Test), and cracking resistance (Semi-Circular Bending Test).
High-performing sustainable products are a growing priority for contractors looking to keep up with demand for environmentally friendly paving solutions. These measures encompass the entire lifecycle including energy and water consumption, waste management, and recycling capabilities from cradle to gate and, ultimately, the roadway application itself.
By considering asphalt mix based on a balanced mix design concept, the resulting sustainability impact can be felt across the lifecycle of the roadway: incorporation of high amounts of recycled pavement material, use of an environmentally friendly recycling agent, and reduction of carbon emissions resulting from repair and maintenance
Check out the National Asphalt Pavement Association’s 2023-2025 “Strategic Plan” here: https://www.asphaltpavement.org/about/strategicplan and the National Highways’ “Net zero highways: Our zero carbon roadmap for concrete, steel and asphalt” here: https://nationalhighways. co.uk/media/2prpkf4e/net-zero-roadmap-for-concrete-steel-and-asphalt.pdf
Get your copy of “Asphalt Pavement Industry Survey on Recycled Materials and Warm-Mix Asphalt Usage 2022” from the NAPA store here: https://go.asphaltpavement.org/hubfs/NAPA%20Store/IS138-2022_RAP-RAS-WMA_Survey_%20WITH%20APPENDICES_508.pdf
Find FHWA’s “Asphalt Pavement Recycling with Reclaimed Asphalt Pavement (RAP)” here: https://www.fhwa.dot.gov/pavement/recycling/rap/ Review “The Challenges of Using Reclaimed Asphalt Pavement for New Asphalt Mixtures: A Review” here: https://pmc.ncbi.nlm.nih.gov/articles/ PMC7560297/
Read more about ReLIXER in “Our Focus on Sustainability” at https://sripath.com/sustainability/ and “ReLIXER Technical Overview” at https:// sripath.com/resources/documents/.
Since its introduction, the Weiler P385 has set the standard for commercial pavers. The P385C raises that standard.
Increase to 120 hp with the Cat® C3.6 Tier 4F/Stage V engine.
Variable speed and reversible conveyors and augers and a 25% increase in tunnel height provide optimal material output.
Modular conveyor drive and sealed chain case increase feeder system reliability and life.
Enhanced heat system performance with direct-drive hydraulic generator and elimination of GFCI breakers.
BY ASPHALTPRO STAFF
From a competitive pool of more than 120 applicants, Meghan Roy and Lilia Yakimyuk received the 2024 Women of Asphalt Scholarship in conjunction with Caterpillar Inc in fourth quarter 2024. Caterpillar provided the women free registration to the Caterpillar Paving Operations Training, which took place the week of Nov. 18. In the October 2024 WofA newsletter, the organization stated:
“Women of Asphalt has proudly supported Meghan and Lilia’s professional development by covering all travel-related expenses, ensuring they can fully focus on enhancing their skills and advancing in the industry without the burden of travel costs. This includes airfare, accommodation, transportation, and meals, enabling a seamless and enriching experience.”
Caterpillar Paving Operations Training is a four-day program designed to enhance paving technique, improve mat quality and boost profitability. The course offers two hours in the classroom each day, followed by six hours at a demonstration site where students receive hands-on training with Cat® paving equipment.
Roy is a paving laborer at Tilcon Connecticut, where she has worked for the past three years. From the personal essay she submitted with her scholarship application, we learn that she’s not only passionate about asphalt, but she’s also sharing her strong work ethic and desire to continue learning with her 11-year-old son.
“When I first started at Tilcon, I was a shoveler and have now progressed to be a Shuttle Buggy grounds-person on our Ultra-Thin crew. My typical work schedule is Sunday - Thursday, from 6:00 p.m. - 6:00 a.m. My job varies monthly based on project schedules ranging from interstate highways to local town roads.
“As I progress in my career journey, I want to continue to learn more about the business and the asphalt industry. I am curious to know how each machine works and the different parts... Each night, I prioritize asking our operators questions to expand my knowledge on how to run the different machines. My goal is to eventually have experience running machines and teach others on how to become an operator. I am fascinated by the whole production of paving, working with regular Asphalt and Ultra-Thin Asphalt. Starting my career
as a Laborer has given me a solid foundation in the asphalt industry. Now, I want to build on that knowledge and advance my career by becoming an operator.”
Roy’s desire to advance her career includes advancing those around her. She shared in her essay: “For me, working in the asphalt industry is more than just a job—it’s a way of life. It's how I provide for my son, it's a career that has given me a sense of purpose, and most importantly, it's what inspires me to strive for career advancement. If I can use my experience to increase awareness, share knowledge, and create a supportive community for other aspiring women, that would mean everything to me.
“I owe a lot of my asphalt knowledge to the men who taught me. Now, I want to learn and grow my skills so that I can be the woman who teaches the future generation.”
Yakimyuk is a roller operator for Lakeside Industries and has been an apprentice equipment operator in Local 302 for the past four years. From the astounding personal essay she submitted with her scholarship application, we learn that she’s the daughter of Ukrainian immigrants, born in the United States and honed by hard work and a drive to succeed. Her desire to help others in the workplace is a built-in character trait that shows an empathetic and team spirit valuable to an asphalt paving crew.
She wrote that during a job at a laundry facility when she was 18 years old, she assisted co-workers whom the supervisor didn’t have time to assist because, “it was painful to watch the struggle of others. Manual labor was no stranger to me.”
Her extra efforts there didn’t go unnoticed, and she was promoted to production supervisor shortly after two months of employment. Although there were promotions and advancements at that job, it wasn’t the fulfilling post she knew she could achieve, and she knew to go for more, she needed to study at night to attain her G.E.D.
So, she did.
That level of effort, reaching for more, and attaining education has served Yakimyuk well over the years as she achieved her G.E.D., served in the U.S. Army until age 26, and dove into the Helmets to Hardhats program. It’s not been an easy journey, but it’s one she’s proud of.
She wrote, “I love my job. I feel like I found my place in the world. I love the bumpy road I took to get to where I am today. I love the rush of conquering challenges. Doing things you've never thought you'd be in a position to do. I love all the people I've met, who mentored, guided, encouraged, and motivated me. I am, without a doubt, a very blessed woman. To have a job I look forward to every morning, co-workers who are arguably the best in the field, and an employer who in my opinion is the best paving company in the Northwest area.”
Rachel Quam, director of sales for North America, paving products at Caterpillar’s Global Construction & Infrastructure, shared, “I would say both these ladies saw it as a growth opportunity for themselves within their respective careers.”
The WofA organization wrote, “These incredible women have demonstrated exceptional dedication to their craft and are making waves in the asphalt industry. We are proud to support them on their journey toward further growth and success.”
Watch for announcements regarding the 2025 Women of Asphalt Scholarship opportunity, which the organization will be sharing via social media in late first quarter 2025. And start preparing your personal essay now.
• See the Latest Equipment
• Learn Best Practices and Techniques
• Improve your Jobsite and Business March 25-27, 2025 | St. Louis, MO Use SAVE20 to Receive 20% Off your Admission to World of Asphalt
The first MT120J from MAGNA heads to Australia for large-scale
The first MT120J, ready to ship to Mineral Processing Solutions in Australia at the end of 2024, featured a diesel/direct drive configuration. The MT120J model can also be built as a fully hybrid unit to utilize the onboard genset drive system or accept external electricity supply (MT120Je).
MAGNA™, a Terex brand, announced in December 2024 the completion of the first MT120J large jaw crusher, on its way to Mineral Processing Solutions in Australia. The heavy-duty jaw crusher plant is designed for large and medium-scale operators across quarrying, mining, demolition and recycling applications.
It is manufactured at the Terex Crushing Technology Centre of Excellence in Coalville, England, and features a chamber of 47.25 x 32.25 inches (1200 x 820 mm). The MT120J has an output potential of up to 661 U.S. tons per hour (600 tph), depending on material type and crusher settings.
The machine includes a ground-level hydraulic folding feed hopper with a hydraulic locking system. Additionally, the MT120J is equipped with a wide bypass chute to optimize material flow, while the crushing action of the high swing jaw encourages efficient material entry into the chamber.
The MT120J is fitted with a PLC control system that includes an auto start facility. It also comes with radio remote control and MAGNA telemetry as standard. The product conveyor is angle adjustable, which lowers for easy access and transport. The MT120J is also equipped with a dust suppression system to provide cleaner operations as well as straightforward access to the power unit canopy for maintenance and service.
“The MT120J is a solution built for high performance and maximum productivity,” said Neil McIlwaine, business line director for MAGNA. “It has advanced features and durability that make it the ideal crusher for Mineral Processing Solutions in Australia, who needs equipment that can keep pace with the demands of large-scale projects. We look forward to seeing it deliver exceptional performance and support their continued success in Australia.
For more information, visit terex.com/ magna
Thermal NOX is formed at flame temperatures of 2200°F and above.
BY MALCOLM SWANSON, P.E.
Editor’s Note: The new Focus on Performance series from AsphaltPro Magazine allows OEMs and service providers in the industry to highlight asphalt professionals who have improved efficiencies and the bottom line through best practices and performance. This month’s installment from Malcolm Swanson, P.E., dives specifically into efficiencies gained through controlling the combustion process. As always, we’re honored to share Swanson’s knowledge with the industry.
TThe challenge of controlling emissions from fossil fuel burning industrial processes has been a major focus of industry since the passage of the Clean Air Acts of 1970 and 1990. So, the subject of this article is nothing new; but what makes the best emissions control methods work is not widely understood, even today. It’s good to know what works and why.
Controlling burner emissions is really all about controlling formation and/or emission of certain chemicals. If you look at it from this point of view, our physical world is composed of chemicals. The cleanest things in nature, like pure water and fresh air, consist of chemical elements and various compounds of those elements. Air is mostly nitrogen—about 78%. Oxygen is the next most abundant element in air at about 21%. That leaves 1% for things like carbon dioxide, argon, hydrogen, helium, etc.
We can’t live without chemicals. In fact, we too are composed of chemicals. (I am not talking about our soul and spirit of course, just our bodies.)
There are chemicals that are harmful to the environment and to our health. However, even where “harmful” chemicals are concerned, the issue of danger is really about concentration.
For example, we all breathe carbon dioxide every minute of every day, but it doesn’t hurt us because normal air doesn’t contain a high enough concentration to damage our health. We can’t live without carbon dioxide because the plants that make oxygen and provide us with food need carbon dioxide to live and grow.
So, the real reason we try to control combustion process emissions is to keep the ambient concentrations of certain chemicals that have harmful potential at levels low enough to avoid harm. With that in mind, let’s consider what goes into controlling the
oxides of nitrogen (NO and NO2, together referred to as NOX), carbon monoxide (CO), carbon dioxide (CO2), and total hydrocarbons (THCs).
To narrow the focus of control efforts a bit, until climate change became the main issue, NOX had been considered the major offender, because it is a contributor to smog and can cause irritation of our respiratory systems. It has, therefore, received much attention. Controlling NOX emissions has been and remains difficult partly because some NOX control technologies tend to cause increased CO and CO2 emissions.
There are several different groups of technologies that have been developed to control NOX emissions. The major ones are combustion modification, exhaust gas treatment, staged combustion, fuel selection and combustion quality management. The last of these is probably not as familiar to many readers as the others. I will briefly discuss all five and then focus on the last.
To understand NOX emissions and how to control them, we must understand how they are created in the combustion process. NOX is formed through two different mechanisms and is referenced by those mechanisms—thermal and fuel.
• Thermal NOX is formed in burner flames at very high temperature by burning the nitrogen in the air. This happens when fuel is burned, with air as the source of oxygen, at temperatures of about 2200°F and higher. With thermal NOX, the higher the temperature and the longer the time at high temperature, the more NOX is produced.
• Fuel NOX is made when the “bound nitrogen” in the fuel compounds unites with oxygen in the flame. The amount of fuel NOX made is not so much related to time and temperature as it is to the amount of nitrogen in the fuel. Some fuels contain much more bound nitrogen than others. Basically, the heavier the fuel, the more bound nitrogen it contains. Coal, heavy oil, number 2 oil, propane and natural gas contain bound nitrogen, in this order from most to least. There isn’t much way to control how much fuel NOX is made in the burner flame except to use fuels that are low in bound nitrogen, like natural gas and propane, and burn as little fuel as possible by maximizing combustion and process efficiencies.
HARMFUL POTENTIAL AT LEVELS LOW ENOUGH TO AVOID HARM.
Because thermal NOX formation is strongly affected by temperature, much of the control efforts have been toward reducing flame temperature. Here are some ways that have been implemented. Flue Gas Recirculation (FGR), which is one of the means of reducing flame temperature, was the first effective means of NOX control implemented in asphalt plants.
FGR, which is also referred to as exhaust gas recirculation (EGR), is effective at reducing NOX, because it does two things that are unfavorable to NOX formation. First, it reduces temperature. It also reduces oxygen concentration in the flame making oxygen a little less available for bonding with nitrogen. However, FGR can only be pushed so far, because a deficiency of oxygen and low flame temperatures cause increased CO, CO2 production and exhaust gas volume.
Water injection directly into the flame was another early means of NOX control by suppression of flame temperature. Results were similar to FGR, but it was not quite as effective.
Staged combustion is another method of NOX control by reducing flame temperature and by creating zones where the fuel air mixture is not favorable for NOX production. The “stages” are points or areas within the combustion zone where portions of the total fuel and/or air are injected. Usually, a fuel rich zone is followed by a fuel lean zone so that the overall fuel air mixture is right but the mixture at each stage, rich or lean, is different from the final overall mixture. These methods are combustion modification techniques.
Treatments of the exhaust gases downstream of the process have also been used to reduce NOX, CO and TOCs but not so much in asphalt plants. In fact, my first patent in the asphalt industry was for catalytic reduction of NOX in the exhaust stream.
The patent was issued but the equipment was never built due to there being less expensive alternatives. Urea injection into the exhaust gas stream is another effective means of NOX reduction but it has seen little, if any, use in our industry.
Fuel selection has become the most common means of combustion emissions reduction, even though, by itself, it often does not provide enough emission reduction to comply with applicable regulations. Natural gas is currently the fuel of choice. It is usually available and affordable and contains the least amount of carbon and bound nitrogen of any fossil fuel. If natural gas is unavailable, propane is the next best thing.
The discussion on Combustion Quality Management (my term) is the most interesting, in my opinion.
Burners, not just in this industry, but burners in general and especially large ones such as those we need for drying, have not been very good burners. For the most part, they have been perfectly adequate to provide the necessary heat and decent fuel efficiency for the drying process but have not been adequate to meet increasingly stringent emissions limits.
Most of the burners that have been used in this industry did not maintain consistent fuel air ratio throughout the normal firing range, but they were close enough for drying. It should be obvious that consistently maintaining the right fuel air ratio is critically important to controlling emissions. If you use too little air, the fuel burn will be incomplete and a lot of CO will be produced. Flame temperature will also rise causing excessive NOX production. If you go the other way with too much air the NOX may practically disappear because the flame is cooled by the excessive air but, again, CO emissions will increase because the “chilling” of the flame slows the chemical reaction of combustion and prevents complete burning. Too much air will also impact production rate by increasing exhaust gas volume.
However, let’s assume we have that part whipped. We can maintain the right ratio. There are some total air burners in the industry of which that assumption is nearly true. Our (this industry) burners still have not done a good job of emissions control for one reason: They do not mix the fuel and air very well.
When the fuel and air are not well mixed, what do you get for a flame? What you don’t get is a homogeneous mixture and, therefore, you don’t get a homogeneous flame. Rather you get a heterogeneous mixture and flame.
Think of the flame volume, with poor mixing, this way. It is as if the flame is composed of “pockets” of fuel-air mixture. Some pockets are fuel-rich while other pockets are fuel-lean. The rich pockets tend to burn hotter than the overall average flame temperature while the lean pockets burn cooler. We have both ratio problems—too rich and too lean—in one flame that is of the correct overall fuel air ratio. So, the flame makes too much NOX and too much CO even though the fuel air ratio is right.
These pockets of fuel air mixture of different ratios burn at different rates. This tends to make the flame large. For the typical 100 million BTU/hr gas burner the flame will be 12 to 14 feet long and 6 or 7 feet in diameter. That not only takes up a lot of the space in the dryer drum, but it extends time in the flame for every molecule. More time at temperature means more NOX.
This is what we have had. Now what do we do?
Dig deeper…down to the molecular level. Oxygen molecules prefer fuel molecules and do not like nitrogen molecules. Nevertheless, they will “marry” something if what they prefer is not readily available. Similarly, a carbon molecule will settle for one oxygen molecule if it can’t get two. So, the key to good clean burner emissions is mixing.
Mixing must be so good that nearly every fuel molecule ends up right next to an oxygen molecule. When that happens, the oxygen molecule will take the fuel and reject the nitrogen.
Of course, there isn’t enough fuel to suck up all the oxygen, so some NOX will be formed but it will be greatly reduced. Also, CO production will be minimal. Finally, combustion efficiency will be high, which reduces the fuel burn and, therefore, CO2 formation.
If it sounds crazy to say molecules have preferences, it won’t once you understand how it works. It’s called activation energy. To get the combustion reaction going, you must put some heat energy in and then you get much more back out. A match provides the activation energy to start the wax in a candle wick burning. The fuel/oxygen reaction requires less activation energy than the nitrogen/oxygen reaction. So, given equal availability of nitrogen and fuel to an oxygen molecule, the fuel/oxygen reaction is the one that will happen.
Something else that is really cool is that you get a flame with uniform temperature. There will be no hot or cold pockets. So, there are no “super emission producing” pockets in the flame. Also, because the fuel doesn’t have to waste time searching around to find an oxygen molecule to marry, marriage happens quickly, resulting in a very short flame.
The 100 million BTU/hr flame described above shrinks dramatically. It can be as small as 2 or 3 feet long and 2 or 3 feet in diameter. Flame volume shrinks to about 3% or 4% of that of the typical burner. That means very little time at flame temperature as well as no hot or cold pockets. Time in the flame drops to a few milliseconds.
The question becomes, “How do you get that kind of extraordinary fuel air mixing?” You may be thinking “premix,” and you could be right, but most premix burners don’t get there. Premix is not necessarily better than nozzle mix. That is why there is such a thing as “lean-burn premix” firing. If the mixture is really good, the extra excess air of lean-burn premix isn’t needed. (The extra excess air is not a good thing because it reduces the plant production capacity by adding load to the exhaust system.)
The thoroughness of the mixture isn’t achieved just because it is premix or nozzle mix. It doesn’t really matter whether you get there by premixing the fuel and air upstream of the burner nozzle or do it at the nozzle. However, no one has been able yet to get that level of mixing in a nozzle-mix burner, as far as I know. I’m not saying that nozzle-mix burners are not good burners. There are some excellent nozzle-mix burners, but they aren’t ultra-low NOX burners.
As I share all these things, just so you know, I am not revealing any secrets. The basic science is the basic science. No one owns it. How to employ it to achieve these
Increase production and efficiency without the investment of a new drum. A leader in the retrofit market, we’ll work with you to come up with the best solution at a competitive price.
· HIGHER RAP PERCENTAGES
· SINGLE POINT ADJUSTMENT
TRUNNION DESIGN WITH HEAVY
DUTY TIMKEN RAIL CAR BEARINGS
· WEDGE-LOK™ TIRE SUSPENSION
· IMPROVED FLIGHTING DESIGN
· PARALLEL TO COUNTER FLOW CONVERSIONS
· PORTABLE AND STATIONARY
We have the information your peers use for quickn-effective Monday morning tailgate talks. You can receive that information for free, too! While you’re in St. Louis, stop by booth 3036 to visit with AsphaltPro staff and to sign up for our weekly Toolbox Tips.
Bring your project story ideas so we can talk about how to brag on your good work in the magazine!
advantages has already been revealed in the patents. I am explaining in “English” what the patents and the science say in more complicated language.
The formation of carbon dioxide comes from burning fuels containing carbon. All fossil fuels contain carbon and hydrogen; hence, they are called hydrocarbon fuels. Those that contain the most carbon will produce the most carbon dioxide when burned. The ranking from most to least is the same as the ranking above for fuels containing the most bound nitrogen. With any particular fuel, the amount of carbon dioxide released is determined by efficiency. Obviously, burning more fuel makes more CO2 while burning less makes less. If you are going to burn a fossil fuel, the only means of CO2 control at the burner are fuel selection and efficiency.
Fuel selection is obvious: Use natural gas if possible.
Efficiency has two parts. First, there is combustion efficiency. The best possible combustion efficiency is basically burning all the fuel with the least possible amount of air. The least possible air is called “theoretical air” or “stoichiometric air.” In reality, burners never completely burn all the fuel and always use more air than the theoretical air. Combustion air, in excess of theoretical, is called “Excess Air.” Even the best commercial / industrial burners must have some excess air (usually about 25%) to get a good fuel burn. It might surprise some of us to know that minimizing burner emissions is not just about the burner.
The second part of efficiency is process efficiency. It is possible to have near perfect combustion and still have high fuel consumption and emissions because of waste in the downstream process. If you burn, for instance, 20% more fuel than is necessary, you make 20% more emissions. The telltale of poor process efficiency is high exhaust temperature and high equipment surface temperatures.
Good equipment insulation and good process heat transfer are the means of control for post combustion process efficiency. Asphalt plant dryer heat transfer efficiency is determined by controlling the exhaust gas temperature using the dryer flight system and drum rotational speed. Exhaust gas temperature should be maintained just above dewpoint temperature, with some allowance for cool and windy weather conditions. Dewpoint temperature in the plant exhaust stream actually changes very little. It is almost always in the range of 160 to 175°F. On a warm sunny day, it is safe to operate with 185°F stack temperature with no worry about mud in the baghouse. On a cold windy day, with uninsulated ductwork and baghouse, going up to 240°F stack temperature would be safer. With a good insulation system, cold and windy doesn’t matter. Operating with stack temperature near dewpoint provides much better process efficiency than is typically found among asphalt plants.
So, what is out there and available to manage your combustion quality? Astec has a low excess air premix burner that does the extraordinarily good mixing that I have described and achieves ultra-low NOX levels. There is also a good Hauck premix burner. Genco has a good, staged combustion burner. I am not trying to promote any particular burner. I just want to help increase understanding of the challenges and solutions of asphalt plant burner emissions control.
I hope, as you read everything above, that you didn’t brush over the importance of process efficiency as opposed to combustion efficiency. High fuel consumption caused by high stack temperature will increase emissions and decrease profits, even with the best burner in the world.
Malcolm Swanson, P.E., is the proprietor of e5 Engineers. For more information, he welcomes you to contact him at malcolme5engineers@gmail.com or (423) 667-6781.
Here’s how to inspect the pugmill for best cold central plant recycling service
BY RICK REES
After the pugmill is installed and working, don’t take production for granted. Keep your best production numbers going by performing routine, scheduled maintenance. All photos courtesy of Stansteel Hotmix Parts & Service, Louisville, Kentucky
AAssessing components at the hot-mix asphalt (HMA) plant is only one step in the overall picture of plant health. The cold central plant recycling (CCPR) site or batch plant has its best chance at optimum, clean, most efficient production when all components and electronics are functioning properly without signs of wear or damage. If an injection line, motor, end liner or other component develops a small leak, electrical issue, shiny surface or other problem, more than production suffers. Because this is the annual recycling issue of AsphaltPro Magazine, let’s begin this new series of assessing the
asphalt plant for maintenance purposes with the pugmill that’s integral to the CCPR process.
The first step with any plant maintenance is to make sure all inspections, markings or repairs happen while using proper OSHA Lockout/Tagout procedures. Ensure you have complete power disengagement before performing any inspections or repairs. For observations that require motors or other components to be operating, listen or watch for vibration and noises from a safe distance or rely on controls systems to provide feedback on specific parameters.
For this series on assessing your asphalt plant for upcoming repairs and to avoid unplanned downtime, plant owners are reminded that only fully trained personnel should be allowed to conduct work on or around the equipment. For safety’s sake, the worker(s) should be fully trained on and act in accordance with all federal, state, county and local laws and regulations, and that includes OSHA and MSHA laws. You want your workers to be familiar with and act in accordance with the equipment specifications and manuals as well as your site-specific safety rules and regulations.
Workers have to take responsibility for their own actions, inactions, consequences and results, but you can ensure the best possible outcome for their safety and your operation’s success when you take the time to train and educate each worker who has access to the equipment and material at your facility.
Always use OSHA Confined Space procedures.
Starting with the exterior of the unit, make a note of any wear areas. Write down what you’ve noticed or type that into your inspection document and make a note to double-check when the repair is completed.
Discover the next generation UltraMax® 1200-CC, Eagle Crusher’s most popular plant enhanced with new features to make setup, operation, and transport a breeze. The plant features a redesigned return conveyor, allowing quicker setup without having to attach parts after extension. The plant also features a new fully hydraulic side discharge conveyor, making setup and teardown easier as well as a self-lowering control panel, no longer requiring additional equipment to remove from the plant. The new 1200-CC is also available with an onboard cross-belt permanent magnet that stays on for transport.
See how this next generation of Eagle Crusher’s 1200-CC plant can work for you.
Let’s begin this “asphalt plant maintenance 101” new series of assessing the asphalt plant for maintenance purposes with the pugmill that’s integral to the CCPR process.
ENSURE
Next, remove the inspection doors to access the drive components. You’ll be looking specifically at the motors, reducers, sprockets and guards.
❒ Check that motors have been operating at normal temperatures.
❒ Has there been excessive noise or vibration during motor operation?
❒ Are there any unusual odors from motors during operation?
❒ Make sure all wiring connections are tight. (you don’t want loose wires)
❒ Make sure all motors are properly ventilated.
❒ Make sure all motors are connected to drive coupling.
❒ Check and, if necessary, achieve proper oil levels in motors/reducers.
❒ Make sure oil samples have been taken and make a note to have the results checked.
❒ Inspect the pugmill shaft bearings.
❒ Inspect the timing gears.
Moving away from the motors, let’s look at the heart of mixing.
❒ Inspect the pugmill shaft and mixer shanks. Check for excessive wear and/or broken tips. Note this for immediate replacement.
❒ Inspect the pugmill end liners. Check for excessive wear and note it for repair or immediate replacement.
❒ Inspect the pugmill bottom liners. Check for excessive wear and note it for repair or immediate replacement.
❒ Inspect the pugmill gate.
❒ Inspect the air cylinder.
Stansteel Hotmix Parts & Service engineers provided a closer look at the elements that make up the pugmill.
❒ Inspect the air lines.
❒ Inspect the solenoid valves.
❒ Inspect the filter, regulator, lubricator (FRL) system.
❒ Inspect the limit switches.
❒ Inspect the gate slide rails.
❒ Inspect the gate liners. Check for excessive wear and note it for repair or immediate replacement.
❒ Inspect the liquid AC injection line. Check for leaks and note this for immediate repair.
❒ Inspect all spray nozzles to make sure none are in danger of clogging. If you have comments on any of the elements you’ve inspected, make those notes for your grounds crew or mechanic and set a date by which you’ll check back on the progress of repairs. A well-maintained and properly functioning pugmill is integral to the success of your batch plant or CCPR facility. Keeping it in good working order keeps your operation safe as well as efficient.
Get a clear picture of your spending, efficiency, asset utilization, and profit opportunities.
With Zonar on board, easily create custom data visualization in Microsoft® Power BI to t your operation’s unique technology, challenges and goals.
With just a click, focus on the metrics that matter most to you, from fuel ef ciency to driver performance to asset utilization.
Make more informed decisions, quote jobs more accurately, identify areas to improve, and maximize overall performance. All without wasting time and resources sifting through loads of raw data and building reports on your own. Zonar gives you an unprecedented window into your vehicles, assets, and personnel for custom insights and a competitive advantage. That’s data done right.
To begin the production-related products and services gallery for 2025, the team at Persistence Market Research has reported on an element of gathering the aggregate that comprises the bulk of asphalt pavement. Their research shows innovation is not only revolutionizing, but is also driving, the future of mining operations. Here’s what they provided:
The global mining truck market is projected to attain a value of USD 22.2 billion by 2024, growing at a compound annual growth rate (CAGR) of 5.5% from 2024 to 2031, reaching an estimated market size of USD 32.3 billion by 2031. From 2019 to 2023, the market experienced a CAGR of 4.7%.
The mining truck industry is witnessing a range of innovations aimed at improving productivity, safety and sustainability. These technological advancements are transforming how mining operations are conducted and enhancing the overall value of mining trucks.
Electric vehicles are gradually taking over various industries due to their environmental benefits. Leading mining truck manufacturers have begun integrating electric powertrains into their vehicles to reduce emissions and fuel consumption. For example, companies like Komatsu and Caterpillar have introduced fully electric mining trucks. These electric trucks [are intended to] reduce the cost of maintenance and fuel, providing long-term savings to mining companies. The transition to electric-powered mining trucks is expected to accelerate as global regulations on carbon emissions become stricter.
Another groundbreaking innovation in the mining truck market is the introduction of autonomous or self-driving mining trucks. These trucks operate without human intervention, allowing for continuous 24/7 operation. Autonomous mining trucks are equipped with advanced sensors, GPS systems, and artificial intelligence to navigate mine sites efficiently. Companies like Rio Tinto and BHP have already deployed autonomous fleets in their mines, improving safety by reducing the risk of accidents
caused by human error. The adoption of autonomous trucks also optimizes operations by reducing downtime and enhancing fleet management.
3. Electric-Hybrid and Hydrogen-Powered Trucks
To address the challenges of long operational hours and heavy loads, mining truck manufacturers are increasingly focusing on electric-hybrid and hydrogen-powered trucks. These alternative fuel solutions combine the benefits of electricity and traditional internal combustion engines, providing greater fuel efficiency and longer operational range. Hydrogen-powered trucks, in particular, are being explored for their potential to offer zero-emission solutions while maintaining the high power and performance needed for demanding mining environments.
4. Telematics and Data Analytics
Telematics, which refers to the use of technology to collect and transmit real-time data, is becoming a key tool in managing mining truck fleets. Mining companies are leveraging telematics systems to monitor truck performance, track fuel consumption, assess vehicle health, and predict maintenance needs. This data-driven approach helps mining operators maximize vehicle uptime and reduce operational costs. With the integration of data analytics and machine learning, mining companies can now make better-informed decisions regarding fleet management, repair schedules and route optimization.
The mining truck market’s growth is influenced by several factors that are driving increased demand and adoption of advanced mining trucks.
1. Increasing Demand for Minerals
As the global economy continues to grow, the demand for minerals, such as copper, gold, coal and rare earth elements, has surged. These minerals are crucial for industries ranging from electronics and automotive to energy and infrastructure. The rise in demand for these resources has led to an increase in mining activities worldwide, directly impacting the need for efficient and robust mining trucks.
2. Focus on Operational Efficiency and Cost Reduction
Mining companies are continuously looking for ways to improve operational efficiency and reduce costs. Mining trucks with higher payload capacity, lower fuel consumption and advanced maintenance features help operators cut operational costs and increase productivity.
3. Government Regulations on Environmental Sustainability
Governments worldwide are increasingly implementing strict environmental regulations to curb pollution and reduce carbon emissions. This regulatory pressure is encouraging mining companies to adopt cleaner, more sustainable technologies, like electric, hybrid and hydrogen-powered mining trucks.
4. Technological Advancements in Mining Equipment
The mining industry is gradually moving toward more advanced and integrated technologies, including those related to mining trucks. As mining trucks become more technologically advanced with features such as autonomous driving, electric powertrains and real-time performance monitoring, they are becoming indispensable tools for mining operations. These advancements are
driving the adoption of mining trucks, particularly in large-scale mining operations that require maximum efficiency and output.
Despite the growth outlook, the mining truck market faces a few challenges. The high initial cost of advanced mining trucks, such as electric and autonomous models, remains a major barrier for small and medium-sized mining companies. Furthermore, the need for skilled operators and maintenance personnel to manage and repair these advanced trucks poses another hurdle. Overcoming these challenges requires investment in workforce training, financial incentives and cost-efficient technological solutions.
The mining truck market is expected to continue expanding at a strong pace. Innovations in electric and autonomous trucks are expected to play a pivotal role in this growth, driven by the increasing focus on environmental sustainability, cost reduction and operational efficiency. Companies like Caterpillar, Volvo and Komatsu are poised to lead the charge in developing next-generation mining trucks that combine cutting-edge technology with rugged performance.
The future of the mining truck market is undoubtedly intertwined with advancements in technology and growing demand from the global mining sector. With significant investments being made in electric, autonomous, and hybrid technologies, the market is expected to experience a transformative period over the next decade.
The mining truck market is on the brink of transformation, with ground-breaking innovations in electric vehicles, autonomous operations and hybrid technologies driving the industry’s future. With an increasing focus on sustainability, efficiency and safety, mining trucks are becoming more advanced, offering benefits to mining operations worldwide. As mining companies continue to embrace these innovations, the demand for next-generation mining trucks will continue to rise, leading to a more efficient, sustainable and profitable mining industry.
The Asphalt Airport Pavement Technology Program (AAPTP) released in July 2024 its “Guidance for Selection of Proper Asphalt Binder Grade” (AIR-002, July 1, 2024).
The AAPTP is a cooperative agreement effort between the National Asphalt Pavement Association (NAPA) and the Federal Aviation Administration (FAA). Together, the associations work to advance the positive use of asphalt with “21st-century solutions for asphalt pavement design, construction, and materials deemed important to airfield reliability, efficiency, and safety with the overarching goal to keep America moving forward,” according to NAPA’s website. The “new” report is available for download at https://www. asphaltpavement.org/expertise/engineering/airports/resources-reports. It is designed to assist owners/agencies in simplifying the asphalt binder selection process for airfield flexible pavement designs. A web-based tool is in development.
ALmix, Ft. Wayne, Indiana, offers the Reign of Fire hot oil heater controls for hot oil heater management and controls. New ALmix hot oil heaters are supplied with the ALmix Reign of Fire (ROF), PLC-based, total heater control and alert system. The ROF system utilizes a 15.6-inch touchscreen HMI setup for local and remote control. ROF can use either an ethernet connection or a cellular-based setup allowing for remote access, monitoring and custom alerts from any internet-connected device. With ROF, whether you are at the plant or on the road, you can control your heater schedule, monitor key temperatures, view the heater operation log or even reset your burner. Existing heater control retrofits are available.
The ALmix ROF control system has a built-in alert system. Each alarm can be configured to be sent out to a single contact in the contact list or a whole group. The alert can be configured to be sent as an email or a text message. Once a contact has received a message, he or she can connect to the system remotely to see what corrective action is needed.
The alarm display screen shows the first out alarms, current alarms and alarm history. There are buttons to clear the first out alarms as well as the PLC safety and burner enable resets.
For more information, call (260) 672-3004 or visit ALmix.com.
CWMF Corp., Waite Park, Minnesota, offers the Honey Badger RAP Crusher, which you can see on display at World of Asphalt in booth 6525 in St. Louis this March. Check out these features of the Honey Badger Hammer Mill:
Bi-directional operation (forward or reverse)
· Dual, hardened Anvil bars
· Metal trap area (mill teeth)
· Hydraulic 2-way power pack load chute operation (up and down)
· Design is conducive to perform maintenance
· AR450 internal wear components
· Half section AR450 side plates (replace the half that wears out more)
· 60HP drive TEFC drive motor
· Hood latches on drive inspection access
· 14 Hammer rotor design
· Premium Carbide impregnated casted hammers
· Equipped with 1” grate
· Other grate sizes available upon request
· Relieved grate design for anti-plugging
· Spherical roller bearings
For more information, call (877) 457-3938 or visit cwmfcorp.com.
With winter upon us, aggregate producers face the critical task of preparing their equipment for seasonal challenges. The downtime during this period presents an ideal opportunity for thorough maintenance and inspection of vibrating screens and classifiers. Many operators utilize Compass Wire Cloth’s hardware and parts to ensure their equipment remains in optimal condition, thereby extending its lifespan and improving operational efficiency.
Preventive maintenance is essential to avoid costly breakdowns and repairs. Regular inspections can reveal issues such as broken wires that may necessitate more durable media, loose panels that require tightening, and worn components that need replacement. Compass Wire Cloth emphasizes the importance of a structured maintenance schedule: daily checks for cleanliness and loose parts, weekly inspections of structural components, monthly evaluations of motor mounts and belt tension, and annual assessments of rubber mounts and springs.
Compass Wire Cloth’s aggregate hardware & parts are engineered to withstand harsh operating conditions while enhancing the performance of aggregate processing equipment. By addressing common issues such as loose panels and damaged parts during winter maintenance, operators can significantly reduce the risk of unscheduled downtime and improve operational performance throughout the year.
•
•
• Environmentally
•
The company’s range of parts and accessories for all aggregate OEM screener equipment includes screen bolts, tensioners and fasteners available in a wide range of sizes and styles, made from various steel grades. Side clamp rails are manufactured in standard A-36 steel for all makes and models, with thicknesses from ¼- to 5/16-inch. Channel rubber is stocked in various sizes with a flat top/open channel design to prevent premature screen wear. The lineup also features T-Scale rubber, spray bar deflectors, skirtboard rubber and classifier shoes.
EvoQuip®, a provider of compact crushing and screening equipment, announce in Q4 2024 the appointment of RTL Equipment as an authorized distributor. The collaboration will expand EvoQuip’s footprint in the Midwest, offering customers in Minnesota, North and South Dakota access to its innovative equipment solutions.
The Raptor® Recycle System from MAXAM™ Equipment Inc., Kansas City, Missouri, holds patent number 7,357,562 and is designed to eliminate issues with steam, blue smoke and higher fuel costs associated with superheating virgin aggregate for use with recycled asphalt pavement (RAP). The system introduces RAP directly into the combustion zone of the drum to take advantage of radiant heat there. The patented method is designed to allow the RAP to absorb enough heat to drive off moisture without allowing material to burn. According to the manufacturer, advantages of the Raptor include:
• Lower fuel consumption
• Fewer emissions
• Higher RAP percentages
• Lower stack temperatures
Reliable Asphalt Products, Shelbyville, Kentucky, has launched the Blend Pro 2.0 plant controls system from AARC Systems this winter. The company will have information at booth 4702 at World of Asphalt. For more information, visit https://reliableasphalt.com/
In October 2024, Rotochopper celebrated Manufacturing Month by showcasing the innovations and craftsmanship that drive our industry. Through events with local schools and community outreach, the company highlighted exciting career opportunities in manufacturing and emphasized the potential of this evolving industry.
Superior Industries Inc., Morris, Minnesota, announced in November 2024 the opening of its new crushing manufacturing facility in its hometown during a ribbon-cutting ceremony. The new facility, dedicated to producing jaws and cones, will increase Minnesota’s crusher production capacity by 50%. This expansion enhances support for dealers and producers across North America’s aggregates and mining industries. Superior’s impact crushers, including vertical shaft impactors and horizontal shaft impactors, will continue to be produced at the company’s other crusher facility in Belen, New Mexico. Additionally, Superior’s global network includes crusher manufacturing sites in South America and Asia, broadening its reach to serve international markets.
“This new facility means more opportunities for everyone connected to Superior—from our dealers and producers to our team members and local communities,” said Jason Adams, president of Superior Industries. “With more capacity and smoother operations, we’re able to stay true to our purpose of serving others by providing products that help our partners succeed!”
The facility features an integrated hydraulics assembly area, an inline test zone and expanded parts warehousing to support the growing need for critical components.
Tesab Engineering, Etna, Ohio, offers the 623CT tracked impact crusher for up to 150 tons-per-hour (TPH) production of cubical shaped product in recycled asphalt processing. The crushing unit is available with tipping grid option and is currently distributed by McCourt Equipment in Texas, Oklahoma, Louisiana, Arkansas, Mississippi and Florida. The 623CT has a maximum feed size of 8 inches (200 millimeters) and a hopper size of 7.9 cubic yards (6 cubic meters) and a weight of 58,091 pounds (26,350 kilograms). Watch this space for an update to the 623CT in April and visit the Tesab booth 2122 at World of Asphalt.
Zonar Systems Inc., Seattle, joined forces in December 2024 with GPS Trackit. Zonar is a provider of commercial vehicle fleet health and safety technology. GPS Trackit is an award-winning, cloud-based, IoT fleet solutions and GPS fleet tracking provider and a portfolio company of Inverness Graham. Zonar will operate as part of the GPS Trackit portfolio while continuing to provide fleet health and safety solutions, particularly in the government and education sectors. Together, the two companies will form a comprehensive platform that serves fleets of all sizes.
“We are thrilled to welcome Zonar into the GPS Trackit family,” said GPS Trackit CEO, Charles Kriete. “This alignment represents a significant step forward in our shared mission to deliver innovative, customer-focused fleet management solutions. By combining our strengths, such as our best-in-class video platform, with Zonar’s advanced technologies and industry expertise, we are poised to create unparalleled value for our customers and further disrupt the market as two industry leaders in overall customer satisfaction. We look forward to building on Zonar’s legacy of excellence and driving transformative growth together.”
“Zonar is excited to join forces with GPS Trackit. For more than two decades, GPS Trackit has been a pioneering force in cloud-based, IoT fleet solutions and GPS fleet tracking—with an impassioned focus on world-class customer service. The breadth of our technology solutions is highly complementary, and combining resources to rapidly accelerate innovation and growth makes perfect sense,” stated Zonar CEO, Michael Gould.
For more information, visit https://www.zonarsystems.com/
RRust is a familiar sight for most of us. Rust and other forms of corrosion are part of everyday life, causing assets to lose their value and functionality. But while the problem is obvious, the cause and the solution are less apparent to most. However, understanding the cause of corrosion provides an important key to unlocking powerful solutions such as Cortec’s Vapor phase Corrosion Inhibitors (VpCI®) for metals preservation in industrial settings and beyond.
Corrosion is an electrochemical process that seeks to return refined metals to their natural state. For example, steel is made from iron ore containing iron oxides (aka, a natural form of rust). To turn iron ore into steel, energy (e.g., intense heat) must be added to convert it into a useful state. Unfortunately, as time goes on, there is a strong pull on that refined steel to turn it back into its natural form of iron oxide, or rust.
The key to stopping rust is understanding the corrosion triangle and knowing how to break it.
For corrosion to occur, three components typically must be present:
• Metal
• Oxygen
• An electrolyte
Oxygen combines with metal molecules to create an oxide or corrosion product at what becomes the “anode” site of a corrosion cell. Water provides a perfect environment in which charged particles (electrolytes) can dissolve and electrons can flow from the “anode” to the “cathode” site to complete the electrochemical process. Breaking the connection between any of these elements interrupts the corrosion mechanism and keeps the metal from degrading. If there is no oxygen, the metal cannot oxidize. If there is no electrolyte, it is difficult for electron transfer to take place. If there is no metal, there are no iron molecules to combine with oxygen and create rust.
Cortec’s Vapor phase Corrosion Inhibitors can break two sides of the corrosion triangle by creating a molecular barrier that interrupts the interaction of metal with electrolytes and oxygen. Vapor phase Corrosion Inhibitors such as amine carboxylates have an affinity to metal and can “stick” to them thanks to this attraction. Similar to the effective but temporary bond of a magnet on metal, these Vapor phase Corrosion Inhibitors “adsorb” onto a metal surface, making it more difficult for oxygen and moisture to interact with metal ions.
This is like attending a social gathering and finding a table to sit at. If all the seats at a table are already full, it will be much more difficult to engage with the people at that table than if there were an open seat to take. The same is true for metal. If Vapor phase Corrosion Inhibitors are taking all the available “seats” on the surface of the metal, there is no room for oxygen and moisture to sit down at the “table” to have a “conversation” that results in corrosion.
While it is important to know how Vapor phase Corrosion Inhibitors interrupt the corrosion process, it is also important to understand how they are applied, since this has direct implications for their benefits and ease of use. An advantage of Vapor phase Corrosion Inhibitors is that they vaporize or sublimate from a liquid or solid into a vapor, subsequently diffusing into areas of lower concentration until they reach their specific level of saturation. Because these vapors will continue to diffuse through the air unless they are trapped, they must be applied in an enclosed space to keep the protective layer intact. However, this vapor-phase action makes them much easier to apply to surfaces that are intricate or difficult to reach and eliminates the need to apply greasy rust preventatives that eventually must be cleaned off.
Sometimes, applying Vapor phase Corrosion Inhibitors is as simple as wrapping an part inside a piece of paper coated with Vapor phase Corrosion Inhibitors or putting a component into a VpCI®-126 Blue bag. Other times, it means placing a VpCI®-111 Emitter into an electrical cabinet so Vapor phase Corrosion Inhibitors can diffuse through the breathable membrane, condition the enclosure, and adsorb on intricate metal wires and contacts without disturbing service. Still on other occasions, it may involve fogging waterborne Vapor phase Corrosion Inhibitors into a power plant HRSG (heat recovery steam generator) for preservation during layup with an eye to speedy recommissioning.
While there are many possible ways to interrupt the corrosion cycle, Vapor phase Corrosion Inhibitors provide an efficient method of protection for metals within enclosed spaces.
For more information, contact Cortec.
In
•
•
•
•
•
•
BY THOMAS PETERSON, P.E.
For many years, the focus of the Colorado Asphalt Pavement Association (CAPA) was to support asphalt users in the proper design, construction and maintenance of asphalt pavements. One crucial reality was the fact nearly every governmental agency lacked adequate funding to properly maintain the condition of their road network. To address this challenge and recognizing that nearly 40% of the 9-million-ton asphalt market in Colorado is city and county pavements, we expanded our advocacy to include guidance on pavement management and asset management.
A key focus of Mike Skinner, P.E. CAE, director of engineering at CAPA, is to support cities and counties throughout the state in making the case to increase funding to maintain and improve the condition of streets and roads. Mike stated, “Increased funding for streets and roads is a win-win-win for all involved. The citizens win with smoother, safer roads that are often tied to the mantra ‘No More Potholes.’ The local governments win by improving the street network and being able to stretch the taxpayer dollars by improving streets in fair condition for much less than rebuilding them [later]. The industry wins by having more tons to pave and [work for] their crews.”
As an association, we have helped a number of agencies over the years. This includes tax measures in the City of Greeley, Grand Junction, Denver, Littleton, Canon City and Colorado Springs, to name a few. We have provided funding resources to implement voter outreach campaigns and have provided stakeholder input into best practices for success.
One shining example is the City of Fort Morgan, which is a city of approximately 15,000 located along I-76, 80 miles northeast of Denver. It is known for having an agricultural economy and for the Cargill meat packing plant. In 2017, the city budget for street maintenance and capital improvement was around $1 million. City leaders were considering a sales tax ballot measure.
CAPA hosted a luncheon of stakeholders to consider a campaign and providing funding for voter outreach. A 1% sales tax measure was proposed and a “Strictly Streets” campaign developed. The City Council approved the initiative on the condition that the funds could only be used for streets. The ballot language stated, “street, alley and related infrastructure improvements and maintenance.”
Arguments in favor of the sales tax were that the city streets were in poor condition, in decline and that current funding levels were not adequate to maintain, let alone improve, the condition of the street system. The sales taxes are paid by everyone who shops, eats or stays in Fort Morgan, not just city residents. The city attracts spending from a regional market of about 38,000 people—more than 3 times its population—and all of that spending could help fix the streets. Also, there had not been a tax increase of any kind since at least 1992—25 years.
The Fort Morgan Chamber of Commerce stepped up and led an effort that focused on a Sales Tax Issue Messaging Plan. The plan included a community wide survey, website, Facebook, Twitter, public meetings, town hall meetings with civic groups, guest columns in the newspaper and paid advertisements highlighted by utility bill inserts. The result was a voter-approved measure (61% in favor) and an increase in street funding from $1 million per year to $3 million per year. The city develops an annual Street Improvement Plan
and has made great progress in improving street condition since the start of the program in 2018. To learn more about the Fort Morgan Strictly Streets Program, visit https:// www.cityoffortmorgan.com/822/strictly-forstreets-progress-and-update.
The November 2024 election saw four local agencies in Colorado receive voter approval for street/road funding measures. This includes the City of Colorado Springs, the City of Greeley, Arapahoe County and Jefferson County. Each agency had voter outreach and education campaigns. Two agencies that failed in voter approval for street/road funding were the City of Ft. Collins and Mesa County; they did not have voter outreach campaigns.
The asphalt industry of Colorado through CAPA understands the benefit of educating agencies and consultants on the principles of pavement management (keeping the good roads good) and the value of asset management (spend a dollar today to prevent spending $10 dollars tomorrow). We will continue to support asphalt users throughout the state to create wins through increased funding for streets and roads.
Tom Peterson is the executive director of CAPA. For more information, contact him at tompeterson@co-asphalt. com or Mike Skinner at mikeskinner@co-asphalt.com or visit the CAPA website at www.co-asphalt.com.
Astec revolutionized the paving industry with the introduction of the Shuttle Buggy, and now the SB-3000 sets a new standard in material transfer vehicles. Effortless maintenance, unmatched performance, and four steering modes for ultimate agility keep paving seamless. Experience groundbreaking innovation with the patented Ground Crew Control Station for the ultimate user experience and protection. The SB-3000 isn’t a machine, it’s a revolution in material transfer, built on Astec’s legacy of industry firsts.
Calibrate your LIQUID ASPHALT in a quick, safe, cost effective manner with our new calibration tank. This innovative system eliminates the costly, time consuming, and unsafe procedures normally associated with LIQUID asphalt calibration. Our 1,000 gallon tanks are offered in both stationary and portable arrangements. A C C a l i b r a t i o n T a n k s F o r S a l e
3” flanged fill / return connection
Hot Oil supplied heat ring at inlet / discharge
Three 5,000 lb load cells with summing board
Rice Lake Digital Readout S t a r t i n g A t $ 1 5 , 9 0 0