• Select Your Thickness for Long-term Quality
• TransTech Shares Compaction QC/QA
• Set Your RAP Business in Motion
• PFAS Update from New York
• Fall PreservationPro
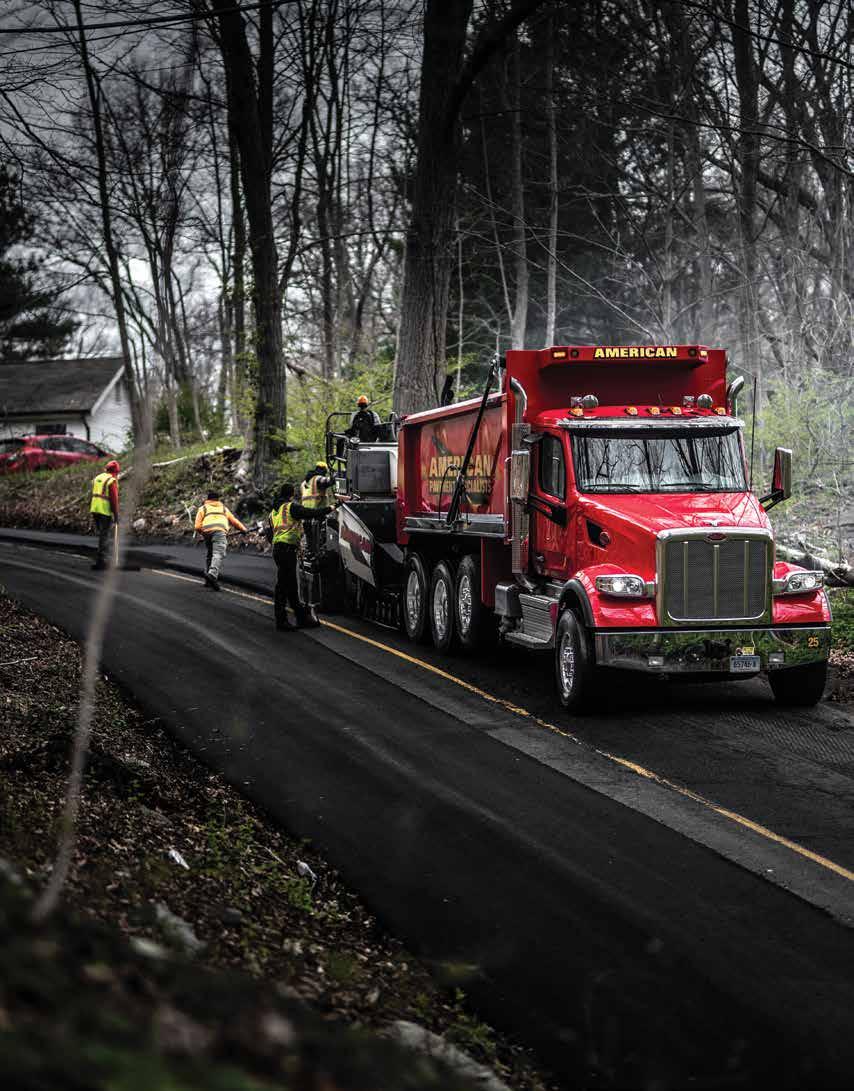
How Will You Finish the
• Select Your Thickness for Long-term Quality
• TransTech Shares Compaction QC/QA
• Set Your RAP Business in Motion
• PFAS Update from New York
• Fall PreservationPro
How Will You Finish the
Astec paves the way for sustainable, innovative asphalt plants. The new IntelliPac Moisture System is a revolutionary solution that integrates seamlessly with Astec control systems. This provides unparalleled, real-time visibility into virgin aggregate moisture content. IntelliPac empowers operators to optimize mix design, minimize energy consumption, and reduce environmental impact. With Astec, you get superior asphalt production – better for the environment, better for your business.
CWMF has been a trusted company in the stationary and portable asphalt industry for decades.
As a full-service manufacturing company, we engineer all of our products to order, allowing us to serve as a full-service, end-to-end provider of asphalt plant solutions. We have the machinery and equipment you need, and a confident team working together to make this happen. Whether it’s cold feed bins, drums, silos, or the entire plant, we get the job done in-house, from start to finish. This provides an exceptional experience for our customers, and for the dedicated team standing behind their products. We work hard not only to retain our reputation but to stay current on the latest industry trends and technologies.
Contact us for a site evaluation, expansion project idea, new equipment upgrades, or to discuss your custom needs.
At Gencor®, we’ve led the industry with the most fuel-efficient, environmentally clean and lowest-maintenance design available to the hot mix industry. Gencor Industries remains focused on proactively serving and satisfying its customers from all aspects.
Through improved cost-effectiveness, and quality of its products and services, Gencor’s personnel are dedicated to the principle of providing the highest quality to the industry to maintain a sustainable competitive advantage for Gencor®
The Leader in Performance and Reliability
or
www.gencor.com
14 – Prepare for Playoffs to Start Next Season Strong By Bill Stanley
16 – Stand Out with QC/QA How to enhance paving operations, customer satisfaction and pavement life with your best quality control practices. By John Lamond
20 – Meet a Woman of Asphalt: Iron Horse Asphalt’s Alisha Hatch By Sandy Lender
34 – International Outlook Interact Analysis Construction Barometer data visualization service suggests a tough year for the UK construction machinery market.
Alexander Jones
48 – Attain Quality Production From AsphaltPro Staff
57 – Middlesex Bolsters Customer Service with Tech By Jim Wahl
The future is connected. That’s why we’ve designed the ALmix Insignia Control System (ICS) around the power of high-speed Ethernet communication. An ethernet-connected facility means our team of programmers have complete visibility into your plant equipment and motor control center for diagnostics and remote troubleshooting. View and control data from your asphalt plants like never before. The Insignia Cloud Platform provides access while you are at the plant, in the office, or on the go. Critical, real-time, plant information is at your fingertips when you need it.
Whether you operate one plant or twenty, the Insignia Cloud Dashboard allows your plant data to be stored off-site and analyzed from any device, anywhere, at any time. Coupled with the ALmix Insignia Control System’s ethernet-connected PLC design and customized by our team of
program engineers, The Insignia Cloud is the most comprehensive plant overview tool on the market.
Iwant to ask if anyone else out there thinks the concept of worker total health was too big or too scary for our industry to accept. I’m concerned not only because I hear anecdotally of workers experiencing struggles that no one has time to address, but also because the number of people signing the Suicide in Construction Awareness Proclamation has dropped off considerably as we’ve moved into 2024. One of these barometers is, admittedly, based on stories that reach me, thus is non-quantifiable. The other is data I can track and see as woefully lacking.
It’s as if the couple hundred people who cared have signed the proclamation to indicate they intend to further the conversation about mental health wellness and suicide prevention in the asphalt and construction industry, and then did not share the concept outside their circle(s).
I’m sure there are plenty of safety managers and insurance professionals talking the talk, but how many asphalt contractors have instituted programs where workers can comfortably approach a co-worker, supervisor, HR director or member of the C-suite with concerns about their own— or a team member’s—mental health status? Let’s not overlook the fact that a worker exhibiting positive presenteeism is likely to complete a higher quality job and is also a safer worker on that job than the worker who is distracted by the stressors contributing to mental health lapses.
IT’S OKAY TO SAY, “I’M NOT OKAY.”
This is the Suicide in Construction Awareness Proclamation, which is housed at TheAsphaltPro.com/SuicidePrevention for your convenience. You have until Dec. 30, 2024, to access, read and sign the document. Learn more at the link.
What I want to drive home with this month’s editor’s letter is the idea that we have an opportunity to alert our safety directors and C-suites to the epidemic of suicide and mental health struggles in our industry before losing more of our valued and respected workers to these real-world issues. It can start with reading, comprehending and signing a proclamation; and it can grow with exploring the resources available to every member of the team for helping your employees recognize and address mental health matters.
602 W. Morrison, Box 6a Fayette, MO 65248 (573) 823-6297 • www.theasphaltpro.com
GROUP PUBLISHER
Chris Harrison chris@ theasphaltpro.com
PUBLISHER
Sally Shoemaker sally@theasphaltpro.com (573) 823-6297
EDITOR
Sandy Lender sandy@theasphaltpro.com (239) 272-8613
DIGITAL EDITOR
Sarah Redohl sarah@theasphaltpro.com (573) 355-9775
MEDIA SALES
Cara Owings cara@theasphaltpro.com (660) 537-0778
ART DIRECTOR Kristin Branscom
BUSINESS MANAGER
Susan Campbell (660) 728-5007
AsphaltPro is published 11 times per year.
A worker exhibiting signs of distraction due to overwhelming grief, undue financial stress, mismanaged medications, severe depression or any other mental health disruption is not exhibiting presenteeism. The distracted worker is more likely to make a mistake—supervisors should hope those are mere quality control mistakes that result in a few penalties and deducts rather than safety lapses that result in injuries or loss of life.
I want to encourage you to take two to three minutes out of your day to visit the Suicide Prevention page, to read Vince Hafeli’s mission, and to sign the proclamation that states you are now aware of the problem in our industry, you care about the problem, and you’re willing to talk about the problem with a heart toward helping solve it. Here is the link to visit right now: https:// theasphaltpro.com/suicideprevention/
Writers expressing views in AsphaltPro Magazine or on the AsphaltPro website are professionals with sound, professional advice. Views expressed herein are not necessarily the same as the views of AsphaltPro, thus producers/contractors are still encouraged to use best practices when implementing new advice.
SUBSCRIPTION POLICY: Individual subscriptions are available without charge in the United Sates, Canada and Mexico to qualified individuals.
One year subscription to non-qualifying Individuals: United States $90, Canada and Mexico $125.00. For the international digital edition, visit theasphaltpro.com/subscribe/
Stay Safe, Sandy Lender
The all-new Blaw-Knox PF-7110C tracked paver combines all-around visibility, ease of operation and a new powerful Cummins 235hp engine for the ultimate in dependability and efficiency. The turbocharged diesel engine provides more torque and less weight in a more compact package, letting you power through steep grades with confidence. Coupled with the proven Blaw-Knox durable track and automatic tensioning system, the 7110C ensures smooth and consistent paving power on any terrain.
With over 90 years of proven Blaw-Knox paving technology, the PF-7110C delivers all the power you need and more.
BLAW-KNOX, THE LEGACY LIVES ON.
BY RYAN LYNCH
As we look toward the future of surface transportation construction specifications, one thing is certain: change is coming. Specifically, environmental product declarations (EPDs) and product category rules (PCRs) are going to be critical components of change in the road-building process. When, where and exactly how are the big unknowns for many of us, whether we are owners, suppliers, producers or other industry-connected organizations and individuals. Specifically, the initial focus on cradle-to-gate metrics rather than a complete cradle-to-grave analysis has many of us pausing and wondering how this will translate into durability and quality of our roads.
However, one encouraging aspect of this otherwise uncertain future is the many existing products available to asphalt road builders and raw material suppliers that bridge the gap between these sustainability goals and legitimate long-term durability concerns. These products are often as cost neutral as they are carbon neutral, and in almost all circumstances, they provide net benefits to the performance and durability of our asphalt pavements.
Bio-based modifiers and recycling agents (often referred to as rejuvenators) are good examples of this, such as the Invigorate® and Invigorate Plus® lines of products offered by Colorbiotics, a Sika Company. These products—and products like them—have been part of our pavement ecosystem for the better part of a decade and have demonstrated the ability for pavement designers and builders to maximize recycled asphalt materials (RAM) without sacrificing per-
“CHANGE
formance. Many of these products, including Invigorate and Invigorate Plus, are USDA Certified Biobased.
What’s interesting about the development of these products is that they sprang up largely as rheology modifiers for asphalt refiners and suppliers, chosen solely for their efficiency and overall effectiveness in improving performance properties of asphalt binders.
Let me reiterate that point another way.
Refiners and asphalt suppliers, already entrenched in the supply chain for petrochemical products like aromatic and paraffinic oils— long used as asphalt binder extenders—looked outside that sector to explore new ways to improve their binders. At the time, due to the emergence of cokers, variability in crude supply and the resulting refinery economics, producing consistent, high-quality, performance-grade asphalt began to be more difficult.
Faced with these challenges, they turned to other petroleum-based modifiers to help them manage the quality of their asphalt. As I will detail shortly, those were not always ideal options, so they kept searching for alternatives, some of which were these bio-based modifiers.
Custom counterflow drum with Rotary Recycle Mixer ®. Multiple RAP and A.C. injection points.
Conversion from old parallel flow drum to 600 ton per hour counterflow running 50% recycle. technology.
Every Hotmix asphalt plant has different operating conditions, therefore, each replacement drum and dryer is custom designed and precision manufactured to meet your specific production demands.
Up to 17 ’ in diameter x 110 ’ long
Replaced failed triple drum with RAP EATER TM - Available in portable or stationary. Customized to retain existing frame, burner and trunnion spacing.
Upgrade every brand built in the last 100 years
Feed and flighting for every material
Asphalt knowledge and experience
Proven quality with over 6,000 rotary dryers built
Replacement and new dryers are Lowest Cost Per Revolution
Dependable per formance for decades
They discovered very quickly that these bio-based modifiers were the answer they had been searching for. In most cases, the bio-based alternatives were more cost-effective and also avoided several health, safety and environmental (HSE) concerns that came along with these petrochemical oils, most notably their effect on mass loss.
On top of this, binder performance most often decreased by using these traditional petroleum-based products. Sure, you could soften binders and provide a more diverse product slate, but a quick analysis of binders—whether it be by Delta Tc or Glover Rowe—often showed the resultant binders to be of lesser quality. Further aging studies even pointed to the susceptibility of worse long-term aging with binders containing these additives.
With bio-based modifiers, not only could you safely drop grades, but you could do it in a way that binder properties improved, even in long-term aging studies. Furthermore, these bio-based modifiers were found to be extremely compatible with the growing variety of asphalt streams around the country, as well as popular modification materials like SBS polymers. In fact, studies showed polymer solubility and crosslinking improved when these modifiers were present in the asphalt cement.
The more efficiently modified AC binder also delivered cost savings to suppliers, and by extension, producers and owners. A single supply point that could only provide one grade prior to modification was now providing several. That saved on freight and improved the quality of the asphalt stream since there was no longer a concern about the negative effect on quality of petrochemical modifiers.
All of this, of course, led to improved performance properties of the overall asphalt pavement. As you improve binder quality and overall softness, it helps counteract the embrittlement that occurs when you raise RAM content in a mix, effectively inundating it with age-hardened binder. This allowed users to start designing more sustainable and cost-effective roadways by boosting RAM content in their specification, while mitigating any performance issues they would see without the use of these bio-based additives.
This was all a result of basic business optimization by suppliers and refiners. The entire innovation occurred before anyone in the paving industry was using acronyms like EPDs or PCRs. However, since those two acronyms seem to come up in any conversation about asphalt pavements, it is comforting to know that in these additives there exists an opportunity for a massive win-win situation.
That win-win situation also fits nicely into the cradle-to-gate PCR the National Asphalt Pavement Association (NAPA) has put together. Let me briefly explain how:
• As noted, these additives are engineered from by-products of renewable energy technologies, lowering the carbon footprint of any asphalt mix where they are incorporated.
• With products like Invigorate and Invigorate Plus, producers can use them as warm mix additives as well, decreasing carbon emissions at plants by dropping production temperatures by as much as 50°F.
• Emissions are further reduced because the asphalt binder doesn’t have to be transported as far due to the supplier’s ability to use these bio-based modifiers to expand their product slate in closer terminal locations.
• These additives enable the use of more RAM, reducing the amount of virgin aggregate that has to be excavated, processed and transported to the plant site. This also contributes to a reduction in emissions.
• Additives like Invigorate and Invigorate Plus aid in compaction and obtaining density in pavements at lower ambient and mat temperatures, which increases the haul distance from fixed and mobile plants. That eliminates the carbon-laden mobilizations of these plants.
All these benefits can be realized in this first phase of NAPA’s PCR, a phase that has not yet weighed in on the environmental impact from the gate-to-grave, but their benefits extend far past that first milestone. Again, that stage is of particular concern to owners who are justifiably worried about the long-term durability of new pavements that were designed to meet these sustainability and reduced carbon emissions goals. As it turns out, they need not worry, as that is where these biobased modifiers like Invigorate and Invigorate Plus shine as well.
Largely due to balanced mix design (BMD) efforts, but also due to the past innovation plays by refiners and suppliers, we have a very good idea of how these pavements—with increasing amounts of RAM, bio-based modifiers and recycling agents—truly perform. Tens of millions of tons of hot-mix asphalt (HMA) pavements already contain these additives. And we have lab and field performance data from a variety of locations.
In all circumstances, testing with methods like Hamburg Wheel or IDEAL-CT on aged mixes shows increased performance versus control mixes not containing these bio-based modifiers. Extracted binder properties are improved as well, just as they are seen to improve virgin binder rheological testing. The National Center for Asphalt Technology has several sections containing these additives that show similar results.
So, as astonishing as it sounds, what we really have here is a “winwin-win” situation. Not only will these additives help us meet our sustainability goals, they will improve our pavements as well. Conveniently, the testing methodology innovations already being implemented into our industry are also extremely adept at evaluating the performance benefits these very additives provide.
It seems like we have a long way to go in bridging the expanse between a net zero carbon emissions future and the present need for upkeeping and even upgrading a surface transportation system. Our regulatory mechanisms and tools are still a long way from being finalized and implemented. Uncertainty, a bit of confusion and even an overall concern for the health of our roadways seems to be as prevalent today as it has been at any time in the past. Change always raises these types of concerns. It truly is the hardest and narrowest groove to enter. But enter we must.
Facing the understandable concern for the future, all of us in this industry—no matter our roles—can take comfort in the fact that we already possess the tools to bridge that gap between sustainability and performance. The difficult entry into this change has already been charted for us. We just need to decide as an industry to forge ahead, utilizing these innovative products confidently. The result is all but certain if we do: roads stretching through our environment, built with sustainability AND performance in mind.
Ryan Lynch is the national sales manager, Colorbiotics Asphalt Solutions. He grew up in a family construction business and has spent his professional career in positions at every level of the asphalt industry.
BY BILL STANLEY
It’s September and the plants are packed, the days are getting shorter, and we’re all up against the weather to end the season with a win. Welcome to the playoffs!
That’s what we at American Pavement Specialists call the busy months from September through December as we try to wrap up all our commitments for the year. By the time fall rolls around, clients of all kinds are ready to wrap up outstanding projects, from driveways to highways. The pressure is on. This is what we’ve been building toward all season long.
Just like any sport, playoffs can make or break you. If the team doesn’t win, fairweather fans could leave you with empty seats in the stadium come spring. If the paving crew doesn’t win, there are going to be empty slots in the schedule come spring.
Here are a few tips for ending the paving season with a win.
By the time a team reaches the playoffs, they’ve had all season to prepare. Paving playoffs is no different. The nature of our trade means our crews have had months to get warmed up by the time September rolls around. As the coach, I’ve got each player in the right position and they’ve had enough time in that role that they’re ready to take their game to the next level.
Because of this, I can do more in one day in September than in one week in April. Those first few weeks each spring, it’s like everyone forgot how to pave, forgot how to get to the shop, etc. No one knows where the jumper cables are. It takes an hour to leave the shop in the morning. By September, the team knows the drill. We meet at the shop at 6:15 a.m. and leave by 6:22. We’re paving at maximum efficiency. Every step in the process feels like muscle memory by now. Everyone is in the zone.
No equipment maintenance is done during playoffs. That roller leaking hydraulic fluid better be fixed. The supplies better be in. All equipment has to be ready for battle. Period. We’re also up against bad weather, shorter days, and impatient customers. Why would we ever want to start that game with a cracked bat?
Each night, we do as much as we can to prepare our equipment for the next day. As the weather gets colder, this includes preventing the water systems of our machines from freezing overnight. If the inside of that mill freezes, we might be looking at $5000 in damage and days of maintenance we just don’t have time for. Before it gets dark at the end of the day, we run antifreeze in the lines and drain them. All equipment gets loaded into our garage each night so we aren’t dealing with frozen lines, dead batteries or frost, snow and ice. Chipping ice off your car is bad enough, but if you have to chip ice off a roller even once, you won’t make that mistake twice.
Come September, Bill Stanley and the crew at American Pavement Specialists launch into ‘playoffs’ as they strive to complete every project before winter weather rolls in and plants shut down.
A manager doesn’t go into the first game of the World Series thinking about game seven. He focuses on one game at a time. By the time September rolls around, we’re often scheduling our crew one day at a time. We might be working in New York one day and Connecticut the next. It’s not unusual for us to complete 30 one-day projects in 30 days. Walmart on Monday, CVS on Tuesday, a private driveway on Wednesday, a road for this township on Thursday, another private driveway on Friday.
We might have Customer A booked, but Customer B calls with an urgent need. Often in this industry, other peoples’ emergencies fall into our laps. As much as I’d like to tell them their lack of planning doesn’t constitute an emergency for me…we want their business. We want their repeat business. I might call my guys on the way to the shop to tell them the day’s job has changed. Everyone has to be able to shift gears as needed. And sometimes we have to handle whoever is screaming the loudest.
Other times, we have to prioritize our long standing customers who pay on time over customers who are new or are slow to pay. It's a strategy, but it’s also a necessity. Every October, I find myself wondering how we’re going to finish every job by the end of the season. We always try to get to everyone before the end of the season—and thankfully we have a history of meeting all our commitments—but it’s not easy.
Of course, we have contracts that dictate that if the customer isn’t ready by a certain date that we may not be able to serve them. But that doesn’t sit well with me. If we don’t get to a customer by the end of the
season, he’ll find a paving company that can. And he’ll use that paving company next year and the year after that. When spring hits and we’re having a slower start, we don’t want to have lost customers because we couldn’t get to them—no matter whose fault it is.
The nature of our trade is that we’re the last ones in on any construction project. So, if construction is delayed on a building at the corner of Main and South streets as the end of paving season approaches, they still need to get their asphalt—rain or shine—because they’re not going to get their certificate of occupancy until that blacktop is down.
We always strive for quality. We try to avoid paving in poor weather conditions. We never want our pavements to fail. But sometimes, we have to do what the customer needs us to do. Sometimes we have to pave over mud just to get their asphalt down before winter, even if it means we’ll be back for repairs come spring. That said, I tell our customers what quality they can expect based on the conditions we’re facing. Whether or not they’re willing to sign off on those risks in exchange for having a paved lot all winter is their call.
During the fall, we use lighter rollers because the heavy rollers bring up more moisture. We also warn our customers to wait until the moisture is out before letting trucks on the asphalt, sometimes up to a week.
Even when we’re paving in adverse conditions, we apply best practices for that situation. If it’s a cold day and the wind is blowing, our rollers are right up behind the paver. If it’s raining and the slope of the parking lot goes left to right, we’re paving it left to right so we aren’t paving into puddles. If the ground is wet, we’re only paving the base course and will pave the top course come spring.
If we have a three-day job in the fall, we may need to pave it differently than we would in the summer. We might have to pave it backwards in case it snows tomorrow and the plant closes the next day. We might have to do the entrance and handicap stalls first so the owner at least has something to get him through the winter until we can pave the rest of the lot. Because it’s not up to us. It’s up to God and the asphalt plants. If they say they’re done making blacktop, that’s it. Season’s over, folks. Come again next year.
When these are the conditions we’re working in, how can we please our customers despite extreme weather, keep employees going despite the pressure, and round out the year with enough profit?
My final answer is preparation. Preparation, preparation, preparation. That’s what coaches do. Prepare. Playoffs are a hard time of year. Preparation and experience will get you through it. If your crew performs well during playoffs, this can be a profitable time of year that sets you up to enjoy the fruits of your labor during the slower winter months and prepares your company for bigger crowds come spring.
Let the games begin!
Bill Stanley owns American Pavement Specialists, Danbury, Connecticut, with his wife, Colleen. Stanley has more than 50 years of experience in the asphalt industry.
How to enhance paving operations, customer satisfaction and pavement life with your best quality control practices.
BY JOHN LAMOND
One of the most critical factors influencing the quality of an asphalt pavement is its density. To improve the quality, durability and life expectancy of asphalt pavement, you can reassess your current quality control (QC) procedures and introduce a plan that includes the monitoring and measurement of the in-place density of asphalt as it’s being laid. When you improve this basic best practice, potential bonus payments can be increased while claims and/or penalties that result from compaction issues can be reduced.
Let’s start with some facts our industry acknowledges:
• The normal minimum target in-place density on a “dense” hot-mix asphalt pavement is 92-93% of maximum theoretical specific gravity (Gmm) or 7- 8% air voids, but the preferred in-place compacted mat density value should be between 93 and 94% or 6-7% air voids.
• A potential 35% reduction in pavement service life can be seen from final in-place density values of between 90-92% compared to an in-place density of 93-95%.
• Monitoring the in-place density of the asphalt as it is being laid is one of the most direct and effective measures of compaction.
• A 1% reduction in air voids can potentially increase pavement life by up to 10%.
Let’s look at how that final point affects life cycle costs (LCCA) of your project. All things being equal, if you’ve increased the density of the pavement by 1%, you could conservatively see a 10% increase in service life. On a $1 million project, that equates to an 8.8% LCCA saving of $88,000. That’s significant for an agency or department of public works (DPW) wishing to extend its pavement maintenance schedule.
You might be among the paving contractors who operate in the commercial marketplace where there’s little opportunity to check the compaction and density of your work. You might rely on past projects and performance as a guide for your choice of mix and compaction process for
One way to improve density is to double-check your numbers. This crew sets the PQI 380 non-nuclear density gauge on the mat directly behind the screed to assess how much compaction they’re starting with before the breakdown roller even touches it. Photo courtesy of TransTech Systems
the upcoming job. In most cases, the responsibility falls to the paving contractor to provide a fit-for-purpose finished product that meets the client’s specification on performance and durability, and there are few specification documents in place to give guidance on best practices for commercial paving.
Consider the large number of commercial paving companies serving your local market. You could be in an area with a high level of competition where you need to differentiate your paving crews from your competitors’.
You compete based on your price, timeliness and quality. You can’t really control the weather, base conditions, which mix you get from the FOB plant, the public or the client, but you can control scheduling (such as when materials arrive), communication with the client and public, safety of the crew and public, your equipment, and most importantly your paving process. Your good reputation will lead to repeat business if you manage well the things you can control.
One of the critical elements you can control is achieving optimum density numbers through best rolling practices and
Since its introduction, the Weiler P385 has set the standard for commercial pavers. The P385C raises that standard.
Increase to 120 hp with the Cat® C3.6 Tier 4F/Stage V engine.
Variable speed and reversible conveyors and augers and a 25% increase in tunnel height provide optimal material output.
Modular conveyor drive and sealed chain case increase feeder system reliability and life.
Enhanced heat system performance with direct-drive hydraulic generator and elimination of GFCI breakers.
monitoring the quality. Even if you receive a bad mix to work with, you can overcome that problem because the compaction aspect is so fundamental to the success of the pavement. A bad mix with good density will outperform a good mix with poor density. So, let’s ensure you get good density. Set your rolling pattern but be flexible enough to change it if you need to. Then test the density behind the rollers.
If you’re working on a state department of transportation (DOT) project, you will likely be required to take cores for compliance testing, but this time-consuming and invasive method of checking density is rarely performed on any commercial projects. If you have rollers with intelligent compaction (IC) systems installed, your operator may be trained in the system’s use to monitor passes and assess pavement stiffness, but typical IC systems do not give a density value of the pavement. A ground penetrating radar (GPR) system also produces a high volume of data which may be better suited to a large project due to both the amount of data and the equipment’s complexity of operation. Another method of density testing is the use of a nuclear density gauge but this comes with a long list of costly licensing and restrictive procedures that any user must adhere to.
The method I propose is using a PQI 380 non-nuclear (electrical impedance) density gauge—as sold by TransTech Systems of Latham, New York—to measure the density of the pavement. The benefits to using this type of gauge include but are not limited to:
• You receive immediate information on the level of compaction as the material is being laid, letting you make adjustments to the rolling train, if necessary.
• Anyone can use the non-nuclear density gauge; it has no restrictions on storage, use or transportation.
• It offers no risk of radiation leak if the gauge is damaged on site and offers less risk of back injury than other, heavier types of non-invasive testing equipment.
• Having on-the-spot density readings will ensure that the specified percent relative compaction can be achieved, reducing the potential for claims or penalties.
The simplest and quickest method to achieve on-site assessment of the asphalt mat’s compaction is as follows:
Everyone should be keyed in to pavement quality. The entire rolling team from the roller operator to the laborer running the plate compactor to the density gauge technician to the foreman on the job—everyone is part of the team that ensures quality control/quality assurance for a longlasting asphalt pavement. And that means a happy customer turns to you for repeat business.
• Pick a location and measure the density with the non-nuclear density gauge.
• Start the rolling pattern over that location on the mat.
• Roll with one or two passes and take another reading with the device.
• Continue with another two or three passes and take another reading; note the increase in density.
• Continue the rolling and testing process until the density readings do not increase.
• If you see a slight decrease, you’re in danger of over compacting the mix. This is called the break point and is the maximum density you will achieve on this mix with this compaction equipment. To correlate a core to this location:
• Once the peaked location on the mat cools, mark a spot to cut the core.
• On the same spot, take a set of five readings with the gauge in a clover leaf pattern.
• Take the core from the mat and determine the density by an appropriate ASTM lab test method.
• Compare the core result to the gauge measurements at that location and calculate the difference.
• This difference is called the offset. (The offset may be negative or positive.)
• Input the offset value in the “Edit Mix” menu on the gauge. The device is now correlated to that specific mix and it should not need to be changed for any future projects involving that mix. By using a quality control/quality assurance device like the PQI 380 non-nuclear density gauge, you can monitor and measure the density of the asphalt pavement as you work. You can adjust your rolling pattern if necessary to achieve the optimum density for a long-lasting pavement that meets your customers’ expectations.
This supports your good reputation and puts you on the short list for future bidding opportunities. In other words, your good reputation keeping quality as a priority not only offers long-lasting pavements for our industry, but it also helps you stand out from your competition.
John Lamond is the Sales Manager at TransTech Systems, Latham, New York. He presented this topic at the National Pavement Expo (NPE) 2024 in Tampa. For more information, contact him at jlamond@ transtechsys.com.
Silo cone opening is 36” wide for ef cient material ow.
Safety gates on all silos, including long-term and standard options.
Recessed tub liners prevent silo wall wear, avoiding bulging issues.
Silo bin top batchers feature secure long-term seals.
Recessed wireways on silo tops eliminate trip hazards.
Meeker drag conveyors are larger, allowing slower chain speed and reduced wear.
Hydraulic chain adjustment on slats maintains asphalt entry point, minimizing wear.
Visual chain tension indicators on Meeker slat conveyors aid operators.
All silos prewired with top and bottom junction boxes.
BY SANDY LENDER
What do you do when you’re juggling a full-time job with raising a family and expanding an asphalt business? If you’re a woman of asphalt, you go all in! For Alisha Hatch, she’d been working at the Federal Bureau of Investigations (FBI) when she and her husband, Tyson Hatch, purchased Pocatello Sweeping in 2009. She left the office job to join the asphalt industry full-time in May 2017.
“We had three children at the time,” Hatch said. “The next year we had our twins, making five. Their ages now: Rex 11, Willow 9, Wynn 7, Otto 5, Wilder 5.”
When it became obvious the company was ready to expand into paving, she became majority owner of Iron Horse Asphalt. On the day we spoke, she shared that she’s technically the owner and office manager, but the day prior, she was a full-time estimator. We're fortunate she could take some time to share her story and show how a woman of asphalt gets the job done.
AsphaltPro: You shared that you worked full-time at the FBI prior to deciding to become a majority owner in the asphalt business. Could you share with the readers what the deciding factor was to jump in with both feet?
Alisha Hatch: We wanted to take our business to the next level, and we knew we couldn’t do that juggling children between us and me not able to help fill time. The year I joined Tyson we increased sales by 33% and the following year we increased by almost 60%.
AsphaltPro: What appealed most to you about the construction business and asphalt in particular?
Alisha Hatch: Our business was already going towards asphalt and working with Tyson was where I wanted to be. Asphalt and construction is not a woman’s world and
One of the many hats Alisha Hatch wears is that of an estimator. She’s the majority owner of Iron Horse Asphalt and its office manager, which means she handles whatever task the family-run operation requires. Photo courtesy of Iron Horse Asphalt
the challenge was appealing. Learning more about asphalt and being able to help our company move forward is exciting.
AsphaltPro: It’s no secret many women take on the caregiver role in families and our industry has been working to find ways to provide childcare options and family-leave options for family members who need flexible schedules or time off to care for aging parents, etc. What solution did Iron Horse Asphalt find for your schedule (or for the schedule of other women you have in your employ)?
Alisha Hatch: As business owners we work around the clock it seems. Our children are very involved and usually come with me to do estimates. We arranged the on-site estimating to once or twice a week so we’re not driving around all the time. I use lunch time and afternoon to write up the estimates and the kids help take care of each other. There are usually TV shows involved at that point, too!
AsphaltPro: You mentioned that the business is allowing you and your husband to work together toward a common goal. Could you share with the readers your philosophy on how the Iron Horse Asphalt business is allowing you to build this enterprise together?
Alisha Hatch: Tyson and I work very closely. I do the office work and estimating, and he does the groundwork. Working together has its ups and downs. We have to listen and respect each other’s needs and trust the work we are each contributing.
AsphaltPro: When do you find time for yourself and how have you found a work/life balance amid building a business you’re both a part of? (Are there any tips you’d offer to another woman of asphalt considering partnering in business with her spouse?)
Alisha Hatch: The balance is a work in progress. As our kids are getting older, we have been able to set aside time for date nights but that didn’t happen in the earlier years. Finding a babysitter was hard for five kids (two being infant twins). Vacations turn into taking work calls and kids’ school activities are sometimes missed by one of us. We know that what we have is made possible by God and our hard work and we’re grateful for it. We love having our kids involved and taking claim to building and working towards this with us. Our kids helped do some asphalt work at their school and thought it was pretty awesome. It gave them a sense of pride.
My tips for others working with their spouses is patience, look forward to set goals and look back at goals accomplished. We set a few five-year goals when we started and met all of them except one: me being able to quit my fulltime job. We added it again to our next fiveyear goals and we were able to make it happen. Sometimes when we’re down or frustrated with each other or the business it helps to reminisce how far we’ve come and what major milestones we have made together.
AsphaltPro: Iron Horse Asphalt isn’t a large corporate paving company. Could you describe the atmosphere you’ve built and what about the structure is most comfortable/ pleasing to you?
Alisha Hatch: We have a family-oriented approach to our company. All that are working with us, we feel are family and take that to heart when making any company decisions.
Through the busy season we’re usually 8-10 people. The atmosphere is casual and joking. Everyone gets along and no one is lost. Everyone is crucial to our success and our employees take pride in the work and care about the outcome and quality of the job.
AsphaltPro: Besides the sweeper, are there other pieces of equipment you’ve operated in the field? Which is your favorite?
Alisha Hatch: I operated the paver when someone needed the day off and I’ve operated the skid-steers. Up until two years ago we also offered snow removal; I drove plow trucks quite a bit. One particular storm was very intense and my job called off work for the day. I went straight to work in a plow still wearing my skirt, blouse and high heels!
Operating the paver is stressful and hard. I made a few mistakes, and I am very grateful we have qualified people to do that and not me. I enjoy the sweeper, probably because I did it the most in earlier years.
AsphaltPro: Which of your roles in the company is the most rewarding to you and what is it about the role that you find most appealing or satisfying?
Alisha Hatch: One of the most rewarding roles is following an estimate all the way through a job. I like meeting customers and when our crew provides a great end product, it’s very fulling.
AsphaltPro: As a contractor that performs commercial and residential installs, Iron Horse Asphalt must get to work with a variety of project owners/property managers. What is your favorite type of project to work on and what makes that intriguing to you?
Alisha Hatch: I like working with and developing relationships with long term customers the best. Homeowners are good to work with and the plus side to that is we get to meet a lot in our community.
AsphaltPro: Could you share with the readers what your role as the office manager
of an asphalt company, specifically, requires of you, in general and day-to-day? What are some “soft skills” you would recommend other women in the industry hone if they wished to step into an office manager role?
Alisha Hatch: Multi-tasking! I take calls from the customers, write up estimates and follow up on their needs. I manage the schedule and coordinate with Tyson and the crew
to make sure I’ve provided enough time for work. And when a job changes and all the work needs to be juggled around, I make a new schedule. Once the work is completed, I send out the invoices and also follow up on accounts receivable. Each day has a bit of everything mixed in.
But on a regular day, we get the younger kids to school. I home school our oldest son,
so I spend time between him and office work until we pick up our youngest twins. I finish up as much as I can before the rest of the kids get home.
I recommend honing in on customer service, project prioritization and allowing yourself grace when things get busy.
AsphaltPro: I don’t want us to ignore your early career in the FBI. Could you tell the readers what you found most valuable about that job and what skills you see yourself transferring from that career to your current career?
Alisha Hatch: I wouldn’t be able to do what I do without my experiences and growth at my previous job. I worked at the FBI for 10 years. I had many opportunities to work with a variety of people and learn quality control techniques and presentation skills. I managed several different teams and learned from others on how to and how not to manage people.
AsphaltPro: What do you think is the most important skill you’ve brought to your posi-
tion as first a sweeper operator and then as a company owner and project estimator in the asphalt industry? (And how would you encourage other women entering the industry to hone a similar skill to be any kind of construction professional they want to become?)
Alisha Hatch: Being part of all different aspects of the business has allowed Tyson and I to understand the demands of each position. This gives us the opportunity to know what each employee can and should be able to handle and also the limits of each position. Empathy is something women can bring to the construction industry. Construction can be rough around the edges and women can bring a lighter, more organized approach to employees and scheduling.
AsphaltPro: What would you say has been the most challenging “obstacle” you, as a female in the construction industry, had to overcome in the past 15 years, and how DID you overcome that obstacle?
Alisha Hatch: One of the biggest challenges is customers not accepting me as a knowl-
edgeable professional that can give educated answers to their questions and provide an accurate, quality estimate.
AsphaltPro: How do you think other women in the industry can incorporate that skill or habit into their workdays?
Alisha Hatch: I want to be a resource for our company and help where it’s needed. In order to do this, I ask a lot of questions, help fix the equipment on nights and weekends, and visit the job sites. I also travel to trade shows with Tyson to see what is going on in the industry and bring the knowledge back to our market.
AsphaltPro: Let’s talk about Teamwork. What is the most challenging project Iron Horse Asphalt has been a part of and how did you and your crew overcome the challenge?
Alisha Hatch: Our crew pulled off a big job without a full crew. We had a deadline for an install on campground. The job needed to get done so the area could be reopened for the weekend. On the morning of the project ev-
eryone was given their responsibilities knowing they’d have to pull extra weight and extra tasks to make it happen on time and be done well. Trucks started running behind and one truck blew a tire. Despite being shorthanded and having slow trucks, they were able to put down all the asphalt and have a high-quality product for the customer. While loading up the equipment, everyone was able to take a breath and really admire what they accomplished. Each member of the crew felt a sense of pride knowing what they had overcome.
AsphaltPro: Let’s talk about Perceptions. It’s a fact that asphalt paving can be hot and dusty. How do you respond to people who say it’s a “dirty job?” And how can we re-educate young people about to encourage more women to consider a career in the asphalt business?
Alisha Hatch: It is a dirty job! It’s real, honest work. Sometimes dirty jobs and asphalt work is looked down upon as a lower-class career.
There’s so much behind the scenes and on the job site that women can help with. We’ve had great women sweeper operators, because they have more of an eye for cleanliness. We’ve had women roller operators; they do great in that capacity because of attention to detail. Something I would tell a young lady to encourage her in this industry? There’s a lot of manly men in the world of construction! There are so many opportunities for growth and development that haven’t been tapped into yet for women. A new perspective on a mostly male run industry can use a feminine touch.
AsphaltPro: What is the most rewarding aspect for you of being in the asphalt business?
Alisha Hatch: The most rewarding has been bringing a fresh outlook to asphalt to our community. Sometimes dirty jobs and asphalt work is looked down upon as a lower class or low caliber career. We are trying to change that perception. We hire men and women who are respectable and hard working with a quality mind set. It is so rewarding to watch a customer be pleasantly surprised when we show up on a job site clean cut, respectful and with a desire to give the best product. When the job is complete, we have made one more person in our community think differently about the dirty work of asphalt.
AsphaltPro: Will you tell us about a person who served as a mentor for you and how this person encouraged you? Is there a piece of advice from this person that you would share with other women in the industry/other operators?
Alisha Hatch: My husband Tyson is my biggest mentor and cheerleader. When I get discouraged about people in the industry
thinking less of me as underrated woman of asphalt, he always jokes that if they only knew who ran this company! He teaches and pushes me to overcome these stigmatisms and show our community how a woman can do this too. You CAN be a big part of the industry, you can get your hands a little dirty and we can become more well-rounded women because of it.
BY KRISHNA SRINIVASAN
Editor’s Note: For 2024, AsphaltPro Magazine allows experts in the industry to share how to expand your operations to the next phase of business. Are you ready to take the plunge and increase your recycling efforts? Let’s turn to some professionals who have equipment, services, software and tenure to help you expand to mix design, production, hauling and more. This month’s installment from Sripath Technologies takes a look at methods of increased recycle content with mini case studies of the company’s additive products.
WWhen an asphalt pavement reaches the end of its life, it is milled off the roadway and crushed to create reclaimed asphalt pavement (RAP). Over time, mountains of RAP can accumulate—depending on the depth milled, just one lane-mile of pavement can generate several hundred tons.
For decades, RAP was considered a burden—waste material to be used on shoulders or stored in ever-growing piles. It was not un-
til the 1970s that our industry began to realize its incredible potential for reuse and recycling. The National Asphalt Pavement Association (NAPA) reported in 2021, over 95% of RAP generated in the United States is reincorporated into new pavement. And it’s not hard to see why. The use of RAP presents a trifecta victory for business through cost-savings, sustainability and road performance.
Contractors champion recycling as it helps them save on raw materials like virgin asphalt binder, typically the greatest expense in mix production. Reuse also benefits the environment, as it keeps old pavement out of landfills and reduces demand for carbon-intensive virgin materials, thereby cutting greenhouse emissions. And many transportation agencies now recognize that high-RAP roadways made with proper ingredients and mix design can yield equivalent performance to virgin-material pavement. Given its growing popularity, understanding the fundamental steps involved in RAP recycling is important for anyone in the asphalt industry.
The first step is to source and prepare your RAP, which can come from anywhere there was once asphalt pavement, including waste material from production facilities. Many transportation authorities are indifferent to RAP sourcing, as long as final aggregate and mix characteristics meet their specifications. However, some agencies are more restrictive, allowing only RAP that can be traced back to a specific project.
RAP particle size varies significantly, ranging from fine to coarse particles. Variability must be addressed, as an improper ratio of small to large particles can lead to poor gradation. Too many large pieces will not pack together properly, leaving excessive space between particles. Too many small particles will make the mix overly dense and therefore susceptible to cracking. Thus, it is important to classify RAP into different size fractions, allowing contractors to produce high-performance mixes that incorporate RAP from many sources.
The key stages of RAP preparation are:
• Screening: Mechanically screen RAP to separate large pieces and remove extraneous materials
• Crushing: Break apart large pieces with a crushing machine. Avoid pulverizing particles that are already small, as it will create dust.
• Fractionation: Separate and sort the crushed RAP into multiple size groups. Although this practice is not done in all asphalt recycling operations, it allows for a more flexible mix design and the use of higher RAP content.
• Homogenization: Once sorted into piles of different sizes, turn over each pile several times to make a more homogenous feed stock for plant operations.
To design a high-performance mix, it’s important to properly characterize the RAP aggregate and binder. Start by sampling the crushed and homogenized RAP stock, making sure to retrieve several representative samples. Extract aggregates from the RAP sample using an ignition oven or solvent. Determine the size analysis of these aggregates. It is important to have an optimal balance of fine and coarse particles. Next, extract and determine characteristics of the aged binder, as its properties will affect the final mix.
Crucial for the success of high-RAP mixes is a carefully engineered and balanced mix design. Fortunately, designing a high-RAP mix is similar in many ways to designing a traditional mix, aside from a few key steps. First, you must account for binder content in the RAP when determining how much virgin bitumen to add. Without factoring this into your calculations, the mix will likely be too rich in binder content. Second, most mixes with more than 25% RAP content, will require an asphalt rejuvenator or recycling agent. Many recycling agents are available, and choosing the right one will make a substantial impact on the pavement’s performance and lifespan. It will also affect your manufacturing and paving efficiency.
An ideal rejuvenator should:
• Soften the aged RAP binder,
• Restore the functional properties of the aged binder,
• Deliver excellent roadway performance and durability,
• Help improve compactability of stiff RAP mixes.
Designing a high-RAP mix requires a careful balance between cracking and rutting resistance. Several methods exist to evaluate cracking, including the Disc-shaped Compact Tension (DCT) test, Semi-Circular Bend Test (SCB), IDEAL-CT, Texas Overlay, and I-FIT test. Some commonly used methods to eval-
uate rutting performance include: Hamburg Wheel Tracking (HWT) and Asphalt Pavement Analyzer (APA) rutting test. Contractors nationwide have used Balanced Mix Design protocols to reap the benefits of recycling while maintaining excellent road performance.
One recent case study comes from the Virginia Transportation Research Council (VTRC), which organized a high-RAP demonstration trial in Ashburn, Virginia. Around 6,000 kg of PG64-22 binder dosed with ReLIXER®, an asphalt rejuvenator manufactured and marketed by Sripath®, was mixed with 40% RAP and fresh aggregates to produce about 2,000 metric tons of high-RAP mix. This mix was used to pave a 40 mm wearing course on an approximately 8 lane-km stretch of roadway in Ashburn, Virginia. As shown in Table 1, binder extracted from the high-RAP mix showed characteristics comparable to binder from the low-RAP control.
Another success story comes from the Illinois State Toll Highway Authority, which manages a 475 km network of highways across Illinois, subject to high traffic and extreme weather conditions. Close to 5,000 tons of a 40% ABR mix was produced to lay down 8 lane-km of wear, base, and shoulder courses on US Interstates I-88 and I-294. ReLIXER® additions at 2.0% and 3.6% of total bitumen content were evaluated. For comparison, a “softer” bitumen mix was also evaluated. As shown in Table 2, the properly designed and rejuvenated highRAP mixes surpassed all local specifications for low temperature cracking, rutting and air voids.
Recycled asphalt has made a long journey from being a waste material to becoming a cornerstone of our national sustainable infrastructure, demonstrating our industry’s dedication to environmental sustainability. The journey has only just begun. With an increase in recycling and reuse of reclaimed asphalt, the industry is poised to take advantage of the trifecta that RAP offers; a positive impact on sustainability, improved roadway performance and durability, and the benefits of cost-savings.
BY ASPHALTPRO STAFF
Asphalt professionals know the best practices to follow to avoid common asphalt distresses. We avoid stripping by washing our aggregate of dust and clay so the asphalt cement (AC) can bond to the aggregate. We apply a tack coat between pavement layers to avoid slippage cracking. We address drainage issues to mitigate future potholes. We achieve the correct density to avoid raveling and minimize cracking.
Asphalt professionals also know that asphalt is designed to be flexible. Normally, this flexibility is a benefit, allowing the asphalt to flex under heavy loads and repair itself in between these loads. But when a pavement isn’t properly designed to hold up to the traffic load upon it (or if that traffic load increases more quickly than the owner or agency can keep up), this flexing can result in the development of microscopic cracks.
California’s long-life asphalt pavement design is a perpetual pavement design that aims to produce a pavement that lasts 40 years or longer with minimal maintenance. The perpetual pavement approach was applied on a project on Interstate 5 near Sacramento, performed by Granite Construction and Teichert Construction.
“As the pavement ages and oxidizes, or if there’s not enough time between each load, those microcracks can’t heal themselves,” said Wayne Jones, senior regional engineer with the Asphalt Institute, during his presentation “Introduction to Thickness Design” at the 2024 National Pavement Expo in Tampa. “Eventually, they’ll accumulate and lead to fatigue cracking. And that fatigue cracking will work its way up through the pavement and you’ll see cracks in the wheel path.”
We can follow all the best practices of paving and maintain and rehabilitate the road perfectly, but time will pass and asphalt will age. The pavement will likely experience more traffic over time than it was initially designed for. These things are not in our control. So, how can we avoid fatigue cracking from the outset?
Jones suggested considering what kind of maintenance and rehabilitation the owner or agency has planned for the pavement during the design phase. “If you don’t do anything after the first day you open a new pavement to traffic, that’s the best condition it will ever be in,” Jones said. “If you can convince the owner to spend his maintenance dollars earlier on with seal coats and chip seals, then overlays, he’s going to get more bang for his buck. If he waits until the pavement is so distressed that it needs to be rehabilitated, it’s going to cost major dollars.”
Consider the Tack Coat
“Let’s talk for a moment about the importance of tack coat,” Jones said. “If you think of a pavement in terms of structure, those layers form a single beam. In a building, when a load is applied, the steel beams flex. The same thing happens with asphalt.”
In beam theory, Jones said, one factor that affects the strength of a beam is its height. “If we have five 1-inch beams, the height is cubed in that equation,” he said. “So, if I have five 1-inch layers of asphalt (1x1x1), that strength is one per layer times five layers, so five total. But if I glue those five 1-inch layers together (5x5x5), the strength is 125.”
That’s the role tack coats play in improving the strength of the overall pavement. “If those beams aren’t glued together with tack, they’re not nearly as strong,” Jones said. He shared an example of a colleague in Montana who tested the concept on multiple layers of 1-inch-thick plywood. “Unbonded, with three layers, there was ½-inch deflection with just a 60-pound load. But when they’re glued together, he put 160 pounds on there with only ¼-inch deflection. That’s why that tack coat is so important.”
“YOU CAN UPSELL YOUR SERVICES BY MAYBE AN INCH OR TWO [OF ASPHALT] AND GIVE YOUR CUSTOMERS A MUCH LONGER LASTING PAVEMENT THAN THE TYPICAL DESIGN THEIR ARCHITECT MIGHT USE. YOU CAN DELIVER THEM A PAVEMENT THAT ACTS LIKE A PERPETUAL PAVEMENT.”—WAYNE JONES
A pavement consists of several layers. The base, sub-base, intermediate layer and wearing course each play a role in structure and drainage—both key components to a pavement’s longevity. “All those layers together are there to ultimately hold up to the future traffic loading on that pavement,” Jones said.
The pavement surface serves four functions: It must have the structural strength to hold up to traffic. It must provide friction resistance for braking and steering for safe operation of vehicles. It must provide a smooth ride. And it must be a moisture barrier to prevent water from reaching the rest of the pavement layers.
When determining how thick each layer should be, the entire system must be taken into account. For example, will the pavement design be full-depth asphalt, or asphalt plus aggregate, Jones said. Thickness design must also factor in the subgrade, material selection, maintenance and rehabilitation, the environment/weather conditions, and traffic. “We need a thickness design program that addresses all these factors when we’re trying to design the thickness,” Jones said.
His preferred tool to account for these factors in pavement design is Asphalt Pavement Alliance’s tool called PAVEXpress. PAVEXpress is a free web-based pavement design tool to quickly determine the necessary pavement thickness for a given section of roadway or project. “You can create an account and store all your design data in there, and use past designs for future projects,” Jones said. After you input your data, it provides the recommended cross section.
Although the tool makes it easy to establish the correct minimum thickness of the cross section, PAVEXpress can also be used to determine how thick a pavement needs to be to be considered a perpetual pavement.
“About 20 years ago, we noticed that some interstates with really thick asphalt never experienced fatigue cracking,” Jones said. “What was happening there?”
Researchers discovered, as traffic increased, more and more layers of asphalt had been applied to the pavements until they were so thick that the tensile strength of the traffic never exceeded the internal strength of the asphalt.
“You don’t get that bottom up cracking,” Jones said. “If I never get those cracks from the bottom up, all I have to deal with is oxidation and maybe some block cracking—neither of which affect the en-
tire body of the pavement—so I can get by with much less maintenance and repair. That’s what we call a perpetual pavement.”
He estimates this can be accomplished by building an asphalt pavement that’s 20 to 25% thicker than what the typical design would be. PAVEXpress can give you this number.
“You can print out that recommendation, supported by all the research and science behind PAVEXpress, with your company name and logo on it and present that to your client,” Jones said. “You can upsell your services by maybe an inch or two [of asphalt] and give your customers a much longer lasting pavement than the typical design their architect might use. You can deliver them a pavement that acts like a perpetual pavement.”
“What soil are we paving on, what density does that soil need to be compacted to, is it properly graded?” Jones asked. The subgrade is an important factor to consider when determining pavement thickness. There are different ways to classify the soil you will be paving on, including the unified soil classification system and the AASHTO soil classification system.
The most common test to evaluate the subgrade strength of roads and pavements is the California Bearing Ratio (CBR), which determines how many pounds of pressure it would require for a 1-inch diameter cylinder to penetrate 2 inches into the material. “A good [material] would require 17 pounds of pressure; medium, 8 pounds; poor, 3 pounds,” Jones said.
Although subgrade can be tested with various nuclear and proctor tests, Jones recommends simply proofrolling it. “Proof rolling with a roller or heavily loaded truck will identify soft spots for corrective action,” he said. “If you see any flexing, it’s not stable enough. You need to strengthen that subgrade before you put the aggregate or asphalt down to make sure it’s strong enough to hold up the pavement and the loads that will be applied.”
Jones stressed the importance of achieving the correct moisture content of the sub-base before compaction, usually 3 to 6%. “Some contractors have a portable pugmill that they put their aggregate through to add the proper amount of water,” Jones said. “Then they run it up a conveyor or put it in a stockpile from which to load trucks, and then put that aggregate in an old asphalt paver to be laid. Then, it’s got perfect water content, it’s perfectly on line and grade, and it has some initial compaction to it.”
Sometimes, further stabilization may be required. A particularly challenging material in Jones’ experience is clay. He recommended the use of powdered lime. “Years ago, I was stabilizing the subgrade of a parking lot for a warehouse with a lot of trucking in and out of it, and I could not get the clay to dry out and stiffen up that late in the year,” Jones said. “I brought out a subcontractor who pulverized lime and water into the clay.” The result was a material that set up quickly and solidly.
“If you’re facing a similar situation, check out the Asphalt Recycling and Reclaiming Association to find contractors in your area who can help you with that, usually for just a couple dollars per square yard,” Jones suggested.
Interact Analysis Construction Barometer data visualization service suggests a tough year for the UK construction machinery market.
BY ALEXANDER JONES
Interact Analysis sees a positive outlook for road building—perhaps more than construction equipment—because, globally, there is still significant investment in roads in emerging economies and the US Infrastructure bill is supporting the repair of roads in the United States. The market research firm estimates the total number of road building vehicles to be sold globally will grow by 3.6% in 2024 versus the previous year, slightly less than the growth rate experienced in 2023, which was 4.3%.
The UK construction industry is facing a gloomy outlook for 2024, despite tentative signs that the economy is improving. Inflation is still above the Bank of England’s target and so, for the time being, we don’t expect the Monetary Policy Committee to vote for lower rates. This is making mortgages expensive and pushing up costs for new construction projects, serving to deter people from buying houses and to discourage companies from borrowing to build. This building slump is having a negative impact on sales of construction vehicles. (Activity could potentially increase by the end of this year.)
In five of the past six months, construction output has decreased compared with the previous month. For the month of March 2024, UK Construction Output was valued at £15.16 billion—this was a 0.4% decrease compared with February 2024 and a 2.2% decrease compared with March of the previous year (adjusting for seasonality and price changes).
Monthly deliveries of bricks data can be a useful leading indicator for the number of new houses planned to be built. Looking at the 12-month rolling average, month-on-month deliveries have decreased every month from October 2022 to March 2024—that’s a year and a half of consecutive decline. It’s a similar story for other building materials like sand and gravel. Assuming further reductions to inflation, and subsequent moves to decrease interest rates, there is a chance that house-building activity may start to pick up again by the end of the year.
High material prices are another dampener on the construction industry, as they impact margins and the general health of businesses’ cash flows. It is one of the main reasons behind the increased insolvency rates affecting the construction industry. In March 2024, 310 construction businesses became insolvent, while in the 12-month period leading up to March 2024, this figure was 4,274—the highest of any of the major industries in the UK.
Other reasons for these startling figures include persistent labor shortages and companies taking on more business than they are equipped to handle, leading to eventual loss of contracts. To survive in this market, operators must make choices about where to deploy capital. They may decide to hold off purchasing/renting new machinery or may decide to switch from their preferred brands, purchasing cheaper equipment and shifting the dynamic of the market.
Focusing on both off and on highway commercial vehicles, Data Analyst Alexander Jones suggests the current tentative signs of growth in the UK economy won’t bolster growth in the construction machinery sector until 2025. At this time, he sees a positive outlook for road building more so than general construction equipment in the United States. Photo courtesy of Sakai America
Finning, a major supplier of construction equipment to rental companies and big contractors, announced a Q1 year-on-year net revenue increase of 3% in the UK and Ireland. This was driven primarily by used equipment sales (which nearly doubled), while new equipment sales remained level. Finning’s product support revenue was down by 7% over the quarter, due to a combination of lower customer activity levels and reduced machine utilization hours.
Ashtead Group, a large equipment rental company, had a rental-only revenue increase of 9% in the UK, of which 7% was organic. This was driven by both increased rental prices and higher sales volume, allowing the company to gain market share.
A generally tough 2024 for the construction industry will negatively impact the number of construction vehicles sold. According to the latest edition of Interact Analysis’s Off-Highway Vehicles Market Study, the construction machinery market (in unit terms) is expected to fall by 6.6% in 2024 versus 2023, with just over 30,100 vehicles forecast to be sold. This includes vehicle categories such as bulldozers, excavators and loaders.
Beyond 2024, we anticipate a small improvement in sales, with 30,600 units projected to be sold in 2025—a year-on-year increase of 1.6%. However, we’re not expecting sales of construction machinery to match 2023 levels until at least 2027.
For more information, visit our webpage or contact Alexander Jones directly.
Albuquerque Asphalt’s I-40 paving project highlights the company’s streamlined preventive maintenance operations featuring two-man crews on service trailers requiring no CDL/HAZMAT.
By Eric Swan
Highway asphalt paving is a high-stakes performance of people, equipment, traffic, schedules and materials. It requires the best at it to be smart, organized and intentional. It also doesn’t hurt to have a little attitude, be a little lucky, and have a whole lot of commitment—to the work itself, and to the team around you.
Having spent time with the team from Albuquerque Asphalt Inc. as they completed a deep mill-and-fill project on I-40 in Albuquerque, it is evident the company has these traits in spades.
Founded in 1981, Albuquerque Asphalt Inc. specializes in arterial road rehabilitation, road reconstruction, commercial and industrial asphalt paving, and site development. Since the company’s founding, it has grown from a small asphalt repair company to a leading asphalt paving contractor, servicing much of central New Mexico and surrounding areas.
The project included a deep mill across two lanes of interstate and two lifts of fresh asphalt—all put down at night with the road being turned back over to the public at 5 a.m. every day.
For Albuquerque Asphalt, a team of more than 200 people spread across asphalt, dirtwork, concrete, crushing and production crews, it’s an extremely deliberate deployment of people and resources to ensure optimal asphalt quality while also working efficiently enough to make business profitable. That includes the timely and efficient performance of preventive maintenance fleet management activities.
Supported by Four Rivers Equipment, Albuquerque Asphalt restructured its preventive maintenance work to move away from larger service trucks that required drivers to have a commercial driver’s license (CDL) and hazardous materials (HAZMAT) endorsement because it became increasingly difficult to find those drivers. Oftentimes, those who do have the endorsements don’t always have the mechanic’s mindset to do preventive maintenance work. The solution: a two-person team matched with a truck hauling a Multi-Tank Oil [MTO] 690 trailer from Thunder Creek Equipment.
The Multi-Tank Oil (MTO) trailer is a hybrid preventive maintenance and fueling solution designed to handle up to 920 gallons and up to six different service fluids including oil, coolant and reclaim, as well as daily fluids like diesel, DEF and grease. It can also be equipped with various power systems.
In addition to the practical convenience of nighttime paving—especially in New Mexico where the combination of hot asphalt and high daytime temperatures can be brutal—Albuquerque presents a unique logistical challenge as it relates to traffic: there are only so many bridges that cross the Rio Grande River. Minimizing traffic disruption is critical.
Albuquerque Asphalt plans each shift of milling and paving intricately to ensure that it can get the day’s work milled and covered with at least one lift of asphalt on it so that it’s drivable by 5 a.m. With the deep mill on this project, each section works in a three-day cycle.
• Day 1: Mill a section and pave lift one.
• Day 2: Mill a section and pave lift one.
• Day 3: Pave the final lift across the previous two days’ work.
All equipment is lined up in the interstate median during the day and brought back to life again after dark to repeat the cycle.
The company has been at the forefront of many trends in the industry that have allowed larger paving companies to streamline operations. It owns its own asphalt plant, controlling the production, quality and access to asphalt. They also do their own quality testing at an in-house lab. And they have been long-time leaders in recycling crushed and milled materials, including using it as road base and by introducing a certain percentage of millings into the hot mix.
With their growth has come more equipment, greater scrutiny on uptime and a changing mindset on how to perform preventive maintenance work. The previous method involved larger lube trucks that required drivers with a CDL and HAZMAT endorsement. As the fleet grew, it became more difficult to find those drivers, and if they did find them, they were not always interested in doing preventive maintenance work.
“You can find CDL/HAZMAT drivers, but you’ve gotta find the CDL/ HAZMAT drivers willing to do this type of work,” said Jacky Spencer, vice president of operations, Albuquerque Asphalt. “We’ve taken younger people with more of a mechanic background and a good work ethic, and we train them to this specific task.”
Asphalt Materials has been a trusted partner in the construction industry for more than 60 years. We are dedicated to building longer-lasting, safer roads — providing customers with the finest asphalt materials available. Our proven suite of products means you’ll find the right solution for your project — and your budget — every time. Scan the QR code to learn more. asphalt-materials.com/products
The Thunder Creek MTO 690 is built to hold a total capacity of 690 gallons, but no one tank holds more than 115
to the manufacturer, which means the trailer doesn’t require a HAZMAT endorsement. When the contractor tows it with the right truck, it doesn’t require a CDL, either.
It was this challenge that led Four Rivers Equipment to introduce Albuquerque Asphalt to the MTO 690 trailers, which the company now owns three of.
“The last few years you can’t find anyone,” said Robert Wood, president and partner, Albuquerque Asphalt. “If you limit yourself to CDL-driven service trucks, that limits your pool of employees. My manager said ‘we can’t find CDL drivers,’ and these were available, and we thought it was a good idea.
“Now we have three of these units and we haven’t bought any more service trucks.”
Spencer and Joseph Otero, a superintendent with the company, have spearheaded much of this new approach to preventive maintenance. It revolves around the MTO 690 and a two-man crew. The men pull up to the median or right-of-way (or wherever the equipment might be staged), and they go methodically from machine to machine performing preventive maintenance work. One fuels while the other greases. One fills diesel exhaust fluid (DEF) while the other blows out air filters. One
The two-person crew gives the company flexibility in its staffing and helps ensure that preventive maintenance work is completed in a timely manner each day, versus being shorthanded if a driver is unavailable.
does a walkaround of the machine to identify any issues while the other tops off fluids. And then they move on to the next machine.
The Thunder Creek MTO 690, with its ability to hold critical service fluids in combination up to 690 gallons, is the centerpiece of this operation. Towed behind any of the company’s pickup or service trucks, the trailers navigate each job site and allow each team member to get close to the equipment they are working on.
“If you take a big lube truck, and you take this setup—this is still a lot easier to get inside of [safety] barrels and get next to stuff,” Spencer said. “I like that they’re not climbing up and down the side of the truck all the time. That’s a big deal for me. Everything is really accessible.”
Because each fluid compartment holds less than 119 gallons (115 gallons is the max), the trailer does not require a HAZMAT endorsement. When matched with the right truck, it does not require a CDL. Albuquerque Asphalt outfits each of its trailers with a combination of diesel, engine oil, hydraulic fluid, DEF, a greasing system and an oil reclaim system, allowing each team to perform all critical preventive maintenance work in the field. The on-board air compressor helps for numerous tasks, including blowing out filters.
“What’s nice about the Thunder Creeks is, when we go to do oil changes, you get the reservoir where you suck it up and put it in the tank as opposed to putting it in buckets—makes everything more efficient,” Otero said. “Greasing, fueling, oil changes. Then at the end of the day we regroup and dump everything out. It’s just rolling, rolling, rolling—it’s all productive.”
The two-person crew gives the company flexibility in its staffing and helps ensure that preventive maintenance work is completed in a timely manner each day, versus being short-handed if a driver is unavailable. If one of the crew calls out, they can be substituted by any team member. This has also helped prevent unnecessary downtime on the weekends.
“We cut down the cost, as far as hours,” Otero said. “Instead of working 60-70 hours, you include these bad boys and break up the work evenly…everything gets done across the board and it’s not slowing us down.”
Four Rivers has helped Albuquerque Asphalt every step of the way, serving as both fleet consultants for the equipment, and fleet management consultants as it relates to preventive maintenance.
“Four Rivers is always looking for a way to improve our business,” Spencer said. “When they have new products, they don’t push them on us, they bring them to our attention. A big part of our success right now is because of Four Rivers. They always answer the phone. They’re available 24 hours, seven days a week, because that’s what we run. Having somebody like Four Rivers is huge.”
For Spencer, the new approach to preventive maintenance and the flexibility of the Thunder Creek trailers are critical to the company’s highway paving success.
“They’ve been a gamechanger for us,” he said. “Servicing equipment is a fast-paced job. Everything’s got to be checked. Fueled up. Oil levels checked,” Otero said. “With the Thunder Creeks, everything’s done, everyone’s happy, and we don’t have to worry about anything.”
1-inch: Infill of Shallow Cracks
2-inch: Over-band of Joint / Filled Crack 4-inch: Over-band Joints / Utility Cuts
8-inch: Increase Vertical Joint Density
Innovation in snow removal equipment is enabling a leading New England company to clear more snow with less equipment, labor, maintenance and repair
By Carlo Chatman
any snow removal businesses base their decision on acquiring snow plow or pusher attachments on the initial cost, overlooking long-term expenses, improved efficiency, quality of clearing, and the potential to secure additional projects. When considering these factors for the upcoming winter down season, the optimal return on investment is achieved through adaptable and agile attachments, even if the upfront expenditure is a little higher.
According to Degen Kelly, director of operations at Outdoor Pride, Manchester, New Hampshire, a company that generates approximately $13 million in annual revenue from snow removal services, it is tempting to focus on the lower initial purchase cost or to simply order the same attachments other companies use. This leads many to just “rinse and repeat,” he says.
However, for the greatest overall returns, more attention should be given to the ROI that higher quality attachments provide. These attachments offer more flexible choices that allow a variety of movements in tight spaces, while adding to the value of skid steers, which are specifically designed to be nimble. Unfortunately, many standard snow plows and pushers have limited functionality, and if big and bulky, turn a nimble skid steer or wheel loader into a large, clumsy piece of equipment with limited maneuverability.
Of course, given the harsh environments where snow removal is required, these attachments must not only perform efficiently but also must last over time.
“Once you crunch the numbers, you see how much time [high quality attachments] can save, how much onsite equipment you can eliminate, how much quicker your operators can work, and how much longer the equipment lasts,” Kelly said. Earlier in his career, he was responsible for operating snow clearing machinery with a range of attachments from different manufacturers.
“Once you start to think about the ROI with the goal of doing more with less equipment, using a more flexible, quality attachment is a no-brainer,” Kelly said.
Removing New England’s Heaviest Snow Loads
Founded in 1988, Outdoor Pride has become one of the largest landscape and snow management providers in New England. Like many landscape contractors, the company offers year-round service that includes snow removal in the winter for large commercial and government-owned properties.
“All the facilities we maintain are zero tolerance, which means that if they ever had to shut down, they could lose a lot of revenue every hour,” Kelly said. “So, the ability to quickly and safely clear snow from a site is essential. We need our entire fleet of equipment effectively performing every day during snow events.”
According to Kelly, the average annual snowfall in New Hampshire amounts to approximately 60 inches. However, as recently as 2020, the state experienced winters with snowfall exceeding 100 inches. To keep up with the high demand for snow removal services, Outdoor Pride maintains a large fleet of more than 300 machines, ranging from trucks and full-size loaders to skid steers and walkway equipment.
For snow removal, the company has 85 Bobcat skid steers and mini loaders, each equipped with a unique AutoWing attachment from SnowWolf Plows, Rosemount, Minnesota.
Founded in Minnesota in the 1970s as a family run snow removal and landscaping contract business, SnowWolf transitioned into the role of equipment manufacturer in 1990. Today, the OEM offers a variety of models and sizes of snow plows, pushers, blowers and other snow removal accessories that are compatible with skid steers, wheel loaders, front-end loaders, tractors and other machinery.
Among the OEM’s offerings is its patented AutoWing QuattroPlows, available in four models and machine operating weights, which are specialized attachments that allow operators to switch between angle plowing, wide-angle plowing, pushing and back dragging on the fly.
According to Kelly, Outdoor Pride discovered the QuattroPlow seven years ago, at a time when they were looking for an alternative to the attachments they were using.
“Most of the other options were flimsy, fixed box [snow pushers]. You really didn’t have the flexibility to drag or angle. The attachments where
backdragging and angling was an option were bulky and limited the ability to easily maneuver the skid steer.”
In contrast, a key feature of the AutoWing design is the ability to extend and retract its side wings independently, depending on the width of the road or the amount of snow cleared. This allows operators to clear wider swaths of snow without manually adjusting the plow’s position, increasing productivity and reducing the need for additional passes.
The AutoWing is also unique because it only requires one hydraulic circuit for operation. No additional wiring is necessary and there are no specialized controls. The attachment can be angled left or right with a standard control feature on the joystick. The user-friendly design simplifies operator training.
“[The QuattroPlow] has all the great aspects of a fixed box, along with the ability to easily angle and back drag,” Kelly said. “It has a very simple setup with just two hydraulic lines.”
Outdoor Pride also elected to use SnowWolf’s ActivEdge, a unique design involving multiple cutting-edge sections with individual adjustability and adaptability. The floating cutting edges allow for more precise snow removal even on varied surfaces and minimizes the need for excessive salt or deicing agents.
“We have seen a benefit from utilizing the [ActivEdge]. Our plow edges are now following the contours of the pavement a lot easier.”
The increased efficiency of Outdoor Pride’s snow removal equipment has substantially improved its operations. Kelly estimates the amount of time to clear a complex area has been reduced by onethird, which often means an additional machine is not required. Due to its ability to conform to surface contours, the ActivEdge
more effectively clears the area, reducing the necessity for additional passes or excessive salt applied post scrape.
Although decreasing operator time is important to Outdoor Pride, Kelly says there are other ancillary factors that contribute to the ROI. One of those factors is the ability of the equipment to withstand the rigors of annual snow clearing.
According to Kelly, some of the accessories on the market, “seem to get banged up a lot easier and require some serious attention to maintenance. With some of the competitors [that we were utilizing at the time], the implement was unusable after just a few years and the repair cost would’ve been too much,” he said, adding that the QuattroPlows the company purchased seven years ago are still in service and other than new edges from time to time have required very little maintenance.
“The [attachment] is an investment, but from what we have found, it is an investment that gives us results and lasts,” Kelly said. “We are experiencing significant ROI in decreased operator time to get through an entire property. We also see it in the longevity of the product.”
While the initial cost of equipment like snow plows or pushers can be significant, it is essential to evaluate their long-term benefits, including increased efficiency, better quality of clearing and the ability to handle more jobs.
By opting for more flexible and nimble attachments, snow removal services can enhance their operational efficiency and effectiveness. When the ROI is carefully analyzed, it becomes evident that the initial higher investment in advanced attachments pays off, making them an indispensable component of modern snow removal strategies.
Increasing quality
for your
customers starts with wellmaintained equipment that can function the way it’s meant to
By Sandy Lender
s Eric Swan pointed out in his preventive maintenance article on page 38, performing in any sector of the asphalt industry requires all the moving parts be in sync—right down to a well-oiled engine. If the broom you intended to use behind your cold planer suddenly seizes, you can’t get the fine millings up, thus the tack isn’t going to stick properly, thus the asphalt isn’t going to adhere uniformly. If this takes place on a parking lot job, you might not see an immediate financial hit from an inspector docking dollars from the project, but you might have an angry customer calling you to come back and repair potholes in a couple months.
If the striping equipment arrives at 4 a.m. to prepare the lot for the day’s traffic, but someone didn’t tuck it away correctly last night and you must replace clogged nozzles before you get started, guess whose customer is about to get mad at a delay.
What Swan said holds true: paving is a high-stakes performance of people, equipment, traffic, schedules and materials. You need your equipment to be well-maintained. That takes training of invested workers who understand the importance of clean, working machines. John Ball, the proprietor of Top Quality Paving, Manchester, New Hampshire, has preached this gospel for years. When consulting from week to week, he sees asphalt professionals of all skill levels, and he commented on what he sees in the newcomers to the industry.
“These guys out there on the crew aren’t regimented,” Ball said. “There’s a certain procedure for cleaning and maintaining the equipment, but these guys aren’t following a procedure. They’ve got to learn to care. That attitude has to be homegrown. They’ve got to
Members of this paving crew get to work with putty knives, screwdrivers and release agent to remove built up material from different sensitive areas of the endgate to ensure it can function properly during the day’s shift. Without a smoothly moving endgate, you can’t expect to have a smooth mat.
If you allow material to build up on the paver’s tires, the tractor will have a bumpy ride. This means you’re not paving a smooth mat, and you could risk cooled, caked material falling from other areas onto your new mat, resulting in non-compactible areas that turn into potholes later. Photo courtesy of John Ball
be taught so they know why they’re taking time at the end of the shift to clean the paver.”
When the distributor truck driver sprays disappointing strings of tack on the surface to be paved, someone must care enough to speak up. As seen in the image at left, the operator didn’t have the right pressure dialed in and had clogged nozzles on the right side of the spray
bar. “You can’t have spaghetti strands,” Ball reminded readers. (See the article titled “Prevent Callbacks for Pavement Slippage” at https:// theasphaltpro.com/articles/prevent-callbacks-for-pavement-slippage/ for best practices in tack applications.) But someone has to train the operator on this, and the crew—or mechanic—must know how to solve the problem.
AsphaltPro magazine and paving consultant John Ball bring you the online training resource: Asphalt Paving 101. It’s available on any device, anytime, anywhere to train your entire crew.
Asphalt Paving 101 In this course, your crew will learn:
• How to stay safe on the job site
• How to build a takeoff ramp
• How to determine fluff factor
• How to determine yield
• How to prep for real paving in the real world
• and so much more…
The most important machine to check over is the paver.
No matter the size of machine you’re working with—whether that’s a sidewalk paver for a last-minute walking trail, a commercial paver handling a parking lot mill-and-fill or a highway class paver taking care of 1,200 tons on the mainline today—that machine is your lifeblood on the paving project. Its care and maintenance is the difference between achieving a quality job that gets full pay from the customer and a problematic job that gets a costly call-back to fix something later.
“The paver is your bread and butter,” Ball said. “If the endgates aren’t flush with the screed, you can’t pave a good joint. If you wrap your tires with asphalt, the tractor’s ride is going to be bumpy and the screed, which is your hot iron, won’t be able to smooth it out. Good cleaning and routine maintenance of the paver will make or break you.”
Due to the importance of this topic for a contractor’s pay, we’ll return to it soon. Use the tips offered with these pictures to guide your cleaning and maintenance routine and watch for upcoming articles on this topic from Ball.
he subject matter experts at Atlantic Testing Laboratories (ATL), headquartered in New York, have examined the issue of per- and polyfluoroalkyl substances (PFAS) occurring in the pavements milled during pavement maintenance activities at airfields. As discussed in the January 2024 issue, PFAS are a group of man-made chemicals, including perfluorooctanesulfonic acid (PFOS) and perfluorooctanoic acid (PFOA). The PFAS from firefighting foam is the specific concern for the asphalt maintenance and preservation industry that we’ll focus on here because the foam has been used in training operations at airfields and other locations where contractors now mill and overlay.
Cheyenne J. Dashnaw, P.E., is a senior engineer at ATL and wrote recently of the hazards contractors may encounter when milling at airports and other locations with a history of using firefighting foam. Contractors collecting contaminated recycled asphalt pavement (RAP) and/or recycled concrete aggregate (RCA) need to be aware of potential environmental and legal consequences.
“If contaminated RAP or RCA are relocated to a different site, the contractor could be considered a potential generator and transporter of hazardous materials,” Dashnaw wrote. He explained to AsphaltPro readers how the contractor could be seen as a “generator” in this circumstance.
“The definition for generator is ‘any person, by site, whose act or process produces hazardous waste…or whose act first causes a hazardous waste to become subject to regulation.’” In these cases, the United States
Environmental Protection Agency (USEPA) and the New York State Department of Environmental Conservation (NYSDEC) “would generally view the site owner as generators for most hazardous wastes, but could consider site owner and contractor as co-generators of certain hazardous wastes, especially for the scenario of a material being relocated to a different site without yet knowing it is a hazardous waste,” Dashnaw shared. “Additionally, if the materials are used as fill or an ingredient in new pavements, there is a risk of contaminating multiple other sites.”
The New York State Department of Transportation (NYSDOT) allows up to 30% RAP in its mix designs, according to Materials Method 5.16. Of course, the RAP material must meet spec. The NYSDOT Standard Specifications section 703-09 states:
“The aggregate component of the RAP shall meet the requirements of section 703, Aggregates. The bitumen component of the RAP shall be asphalt cement and shall be free of significant contents of solvents, tars, or other contaminating substances that will make the RAP unacceptable for recycling as determined by the Department.”
Dashnaw shared that in January 2021, NYSDEC Division of Environmental Remediation (DER) released a technical guidance document titled, “Sampling, Analysis, and Assessment of Per and Polyfluoroalkyl Substances (PFAS),” requiring sampling and analysis of environmental media for PFAS as part of remedial programs under 6 NYCRR Part 375. This guidance document has since been updated, with the current version dated April 2023.
W. R. MEADOWS has been providing proven pavement and highway products since 1926. Our dedicated investments in research and development mean you reap the benefits from our chemists’ premium product formulations. When it comes to ease of use, DOT-compliance, and economy, W. R. MEADOWS’ line of hot-applied joint sealants provides a great solution to joint and crack sealing needs. Learn more by calling (800) 342-5976 or visiting wrmeadows.com.
“Guidance values for limits in soil have been developed for sites in New York State, but soil cleanup objectives (SCO) are not planned to be established until at least a proposal and approval in a future revision to 6 NYCRR Part 375-6. The current guidance gives limit values for PFOA and PFOS based on the anticipated site use for soil and groundwater. While regulations are in progress, it is important to rely on knowledgeable environmental scientists and engineers to ensure that sampling and analysis are completed reliably and in accordance with the most recent and updated regulatory standards.”
Dashnaw clarified: “While the guidelines include soil cleanup objectives based on site use conditions, these are not yet established as regulatory standards and future regulatory standards may differ. If millings are known to be contaminated with PFAS, disposal at a permitted facility should be considered to err on the side of caution. At the very least, I would recommend deferring to the guidance value for Unrestricted Use, which is 0.66 ppb for PFOA and 0.88 ppb for PFOS. If you have samples exceeding these concentrations, disposal should be strongly considered.
“It is important to note that there is a risk that SCO could end up being lower than the current guidance values (and SCO could be developed for additional PFAS compounds other than PFOA and PFOS), but should at least work within the bounds of existing guidance.”
If a contractor suspects PFAS contamination, it’s wise to keep those incoming materials in their own stockpile. “Being able to separate materials is always beneficial, albeit not always obvious or practical,” Dashnaw said. “If a material does end up being discovered as contaminated, and it was managed separately, it is more efficient to track and less costly for subsequent removal and disposal.”
For more information, contact Cheyenne Dashnaw at (315) 386-4578 or info@atlantictesting.com.
BY ASPHALTPRO STAFF
With this month’s quality control/quality assurance (QC/QA) theme, let’s turn to the plant and quarry where quality begins. The original equipment manufacturers (OEMs) and service providers on the next few pages offer their solutions to help you achieve and maintain a quality mix design.
At the beginning of July, FAYAT Group, Bordeaux, France, announced it had acquired a controlling interest in Asphalt Drum Mixers LLC (ADM), based in Huntertown, Indiana. Through the acquisition of ADM, FAYAT further strengthens its strategic position in the road construction and maintenance equipment segment. ADM is joining the FAYAT Mixing Plants business unit, which includes the brands ERMONT, a worldwide leader in continuous mixing plants, and MARINI a worldwide leader in batch mixing plants.
The acquisition of ADM allows FAYAT to expand its strategic position in North America, by leveraging synergies with the following brands already present in the asphalt business: BOMAG, DYNAPAC and SECMAIR.
Being a family-owned business with decades of experience in the road construction and maintenance equipment business, the FAYAT Group will provide ADM with the backing to be a growing and longterm dependable partner for its customers. Moreover, to ensure continuity and an effective transition, FAYAT is pleased that the BoydDevine family will remain as a minority owner and that Mike Devine remains as president of ADM, a position he has held since 2004.
Under the FAYAT umbrella of companies, ADM will operate as an autonomous manufacturer continuing to market its products under the well-respected brand, ADM. ADM will also continue to provide its customers with long-lasting solutions to meet the custom requirements of every job, from planning to production to service after the sale. In the development of future technologies, ADM will collaborate with other companies within the FAYAT Group.
For more information, visit www.admasphaltplants.com.
Command Alkon is investing an additional $20 million to further accelerate its cloud native applications for aggregate and asphalt customers after the success of its initial 100 ready-mix cloud dispatch customers. This investment accelerates the rollout of advanced features for those customers, and the completion of the development of the company’s Aggregates and Asphalt Cloud software offerings, including Dispatch and Scale Ticketing.
Command Alkon’s Aggregates and Asphalt Cloud solutions will be available in early 2025 for implementation. These products will cover all essential functionality and seamlessly integrate with existing and future plant automation equipment, offering efficiency and integration advantages for vertically integrated businesses.
“Our aim is to simplify and unlock the advantages of a single platform for companies who produce and sell more than one material,” said Martin Willoughby, CEO at Command Alkon. “All Command Cloud
products are API-first, reflecting our commitment to interfacing with third party systems and ensuring customer flexibility. We are dedicated to supporting our customers’ transformation journey, whether they utilize our full suite, or integrate with other industry tools.”
This decision represents a major milestone in Command Alkon’s commitment to transforming the way that the aggregates and asphalt markets do business through streamlined workflows and seamless connectivity across their technologies and applications.
“Scalability, flexibility and real-time data insights have become essential in today’s fast-paced business landscape,” said Ranjeev Teelock, chief product officer at Command Alkon. He spoke of extending the benefits of dynamic dashboards, APIs, machine learning algorithms, AI capabilities, and more to customers in the aggregates and asphalt markets.
Command Alkon also announced the acquisition of Marcotte Systems. This strategic acquisition includes all Marcotte’s products, brings their employees onto the Command Alkon team, and reinforces Command Alkon’s dedication to leading the ready mix/concrete, aggregates and asphalt technology industry.
“Joining forces with Command Alkon marks a significant milestone, not only for our company, but for the heavy building materials industry as a whole as it will drive the next generation of fully automated plant solutions,” said Joel Bardier, CEO of Marcotte Systems.
Marcotte Systems, renowned for its substantial investments in plant automation through the Marcotte Batch system and the AI-driven Mintelligent product, is an invaluable addition to the Command Alkon family. This acquisition will bolster the development and global reach of these products.
The Marcotte team, including CEO Joel Bardier, will join Command Alkon, ensuring continuity for customers and projects and leveraging the deep expertise of Marcotte’s employees and new technologies to enhance plant automation solutions.
For more information, visit the website.
Increase production and efficiency without the investment of a new drum. A leader in the retrofit market, we’ll work with you to come up with the best solution at a competitive price.
· HIGHER RAP PERCENTAGES
· SINGLE POINT ADJUSTMENT
TRUNNION DESIGN WITH HEAVY
DUTY TIMKEN RAIL CAR BEARINGS
· WEDGE-LOK™ TIRE SUSPENSION
· IMPROVED FLIGHTING DESIGN
· PARALLEL TO COUNTER FLOW CONVERSIONS
· PORTABLE AND STATIONARY
We’ve been designing and manufacturing custom mixing solutions in Tennessee for nearly 40
Eriez® of Erie, Pennsylvania, launched its new SEV series of suspended electromagnets. These units feature stronger magnets housed in smaller enclosures, reducing overall weight and installation costs while optimizing performance efficiency, according to the manufacturer.
Integrated into the Eriez SE7000 line, the new SEV models leverage cutting-edge wire and conductor technology to energize the magnet circuit, also requiring less coolant for operation. The new wire configuration, boasting an ultra-thin anodized insulation layer, provides superior thermal conductivity, ensuring high heat dissipation within the circuit for improved magnet performance. Despite the compact size, these magnets deliver performance that surpasses larger counterparts, guaranteeing consistent and reliable operation.
Eriez also offers self-cleaning versions of all SEV models. Additionally, a variety of options are available, including dust hoods, coils derated for elevation, high fire point coolants, armor-clad belts and numerous other customizable features for every unique application.
John Deere, Moline, Illinois, launched the 744 X-Tier and 824 X-Tier wheel loaders in its production class. The new 744 and 824 X-Tier loaders feature the John Deere exclusive Electric Variable Transmission (EVT) E-Drive system. Both models will feature a JD9 diesel engine as the primary power source, however, the torque converter and traditional transmission have been replaced by the EVT system. Both models provide the Advanced Vision System and Advanced Object Detection as well as dynamic reversal projected path lines.
For more information, visit your local John Deere dealer.
Masaba Inc., based in Vermillion, South Dakota, builds pit-portable and road-portable plant chassis that are designed for high productivity and quick setup/teardown, while meeting states’ travel weight requirements. Wheeled plants allow use of large crushing and screening units, compared to track-mounted crushing and screening plants. For example, 36x50 jaw primaries, 500 HP cones, and 8x20 dual screens, with onboard and accessible conveyors, are designed to maximize throughput for aggregate processing operators.
Masaba plants are fabricated with quad-axle, stepped-frame chassis. Masaba Screen Plants, whether single- or dual-screen, are fabricated with tandem walking beam axles and heavy-duty leaf spring suspension. Masaba engineers help customers find the right crushing or screening plant to fit any pit or quarry need or design full plant setups for a complete aggregate solution.
Masaba partners with major crusher and screen brands. The manufacturer states it can standardize the portable crushing or screening plant with components of the same company, or can work with customers to build a fully customized plant, featuring elements from several different manufacturers. Masaba stands behind all of its equipment with a five-year structural and two-year component warranty.
Lo-Density® CLHR Inline Electric Fuel Oil Preheaters from Process Heating Company (PHCo) automatically provide precise temperature and viscosity control of heavy oils for efficient and steady delivery from the pump to the burner, according to the manufacturer. Viscosity is the primary concern for producers who burn heavy or used fuel oil in their plants, as these oils become virtually impossible to pump at low ambient temperatures. The lower the viscosity, the more easily a fluid will flow. Correct viscosity also provides proper atomization at the burner nozzle and clean burning of the oil. There are two methods available to adjust viscosity in heavy fuel oil. One is to cut or blend the oil with expensive #2 heating oil or diesel fuel—which raises operational costs because of the higher costs associated with these fuels. The preferred method to adjust viscosity is to preheat the fuel, allowing the heavier oils to move smoothly to the burner. The manufacturer states that PHCo inline heaters are fully automatic, easy to control, and—due to their removable drywell tubes—easy to clean, which is especially important when using recycled fuel oil.
PHCo’s 100% efficient electric heaters ultimately provide unique benefits for asphalt producers that include lower operating costs, improved product quality, reduced maintenance, significantly longer heater life, and enhanced sustainability. The PHCo preheater is plumbed between the pump discharge and the burner. The bypass line from the burner relief valve returns to the pump suction, and not the holding tank. This avoids adding heat to the storage tank, and also reduces electrical load by returning heated oil into the system. The unit includes sensors and thermocouples for main temperature control and high temperature limit. An oil flow switch located in the heater discharge piping keeps the heater from energizing unless there is sufficient oil flow. The patented Lo-Density Coil-Lock-design heating elements, which reside within a drywell, allow the units to dissipate controlled heat as low as 5 watts per square inch on the heater’s sheath, eliminating coking of the burner oil on the drywell tubes. All PHCo preheaters include a prewired UL-listed industrial control panel, housed in a weatherproof enclosure. The system can be powered by any industrial voltage to efficiently heat at a rate of 5-7 watts per square inch. For more information, call (866) 682-1582 or visit www. processheating.com.
The Precision Pin Pusher from Stansteel is designed to make pin removal faster and easier without the use of hammers or torches.
As asphalt producers plan ahead for seasonal downtime and maintenance, they can look to Stansteel of Louisville, Kentucky, for assistance. The company offers the Precision Pin Pusher, which is a hand-held, heavy-duty tool. The groundman uses it to push pins out on 4-inch and 6-inch pitch chains, which means one tool for multiple chain sizes. The manufacturer lists the following benefits:
• One tool fits most chain sizes.
March 25-27, 2025
The second annual “ WOMEN OF ASPHALT DAY ” will take place between March 25-27, 2025, in St. Louis, Missouri. In conjunction with the World of Asphalt, this conference is set to be a landmark event in the asphalt industry, bringing together women from all corners of the country to learn, network, and grow. Mark your calendars and plan to join us for this exciting event. Check out WofA’s website for updates on the event! Visit womenofasphalt.org or scan the QR code!
• It comes in a hard case for storage and security.
• It does not require hammers or torches.
• It offers the pushing power of 30 tons.
For more information, contact (800) 826-0223 or visit https:// stansteel.com
The L110H and L120H mid-size wheel loaders have become mainstays in the Volvo Construction Equipment lineup over the past decade thanks to their compatibility with a range of attachments and their productivity levels, ease of maintenance and superior operator comfort, according to the manufacturer. Now, these two machines have been given a comprehensive makeover that focuses on increased uptime and convenience for both operators and technicians, starting with a new Volvo D8M 8-liter engine that offers 256 hp on the L110H and 272 hp on the L120H. The D8M engine automatically regenerates while working—a technology that’s been proven on the company’s larger wheel loaders.
For more information, visit your local Volvo dealer.
Broad range of viscosities
Range of chemistry
Consistent quality
Low temperature enhancement
Polymer-modified performance
High temperature stability
Roofing flexibility and tack
Cold-in-place recycling
Improved hot-mix asphalt
AsphaltPro’s advertiser
BY JIM WAHL
The Middlesex Corporation, Orlando, has been safely building America’s infrastructure since 1972 when Robert Pereira founded the company. Middlesex has grown significantly over the years with divisions that specialize in heavy/civil infrastructure, transit, aggregates, energy and paving. They take pride in the core values of safety, quality, integrity, professionalism, strong work ethic and commitment. These core values develop amazing partnerships throughout the industry. The paving division goes over and above to complete projects and partner with any customer at any time.
There are many factors that have helped them to achieve this level of success, including the adoption of technology to better serve their customers. Middlesex is committed to using technology and real-time information to keep internal teams and customers moving forward. Real-time data and communication allow all parties to learn, grow and develop lifelong partnerships in the industry.
One of the technologies that Middlesex uses daily is FleetWatcher, which provides transparency to their paving operations. Knowing where each truck is, where it is headed, laydown speed, cycle times or bottlenecks, and wait time at the plant and paver, allows Middlesex personnel to make changes that provide immediate results.
Vice President Michael Iapaluccio recalls what it was like beforehand.
“It was very reactive. We were getting paper timesheets, and it was after the fact. While approving timesheets we might see that a truck took three hours to get to the jobsite and question why, but we already lost the money.
“Middlesex has been using FleetWatcher for over five years now and it is a different story,” he continued. “Middlesex created a live dispatch team to process the live data. It allows you to be the quarterback and the support for the paving crews, customers, and drivers.”
All 70+ of the Middlesex trucks and equipment have FleetWatcher hard-wired into them, to capture data. Third-party trucks use the FleetWatcher app. All they need to do is sign in, and sign out, daily, and are then pinged every 30 seconds to know their time at each location. Electronically capturing data has not only improved its accuracy but has also enhanced production efficiency. Before the daily start, load times, paver speed and arrival times are entered into FleetWatcher, the data is live and ready for the shift to begin tracking.
“Every job is different, bid differently, and every job has a different budget, depending on mileage, locations, accessibility in and out of the jobs,” Iapaluccio said. “If they see that wait times are extending at the paver, they will pull trucks from that job and put them on another project. Or if there is a traffic tie-up along the route, they can reroute trucks around it. If the plant is backed up, we can silo manage.”
“Every paving project is set up in FleetWatcher. On a day-to-day basis, trucks are set up according to the job and the tons to be placed. As the job is loading or as the job is running, FleetWatcher updates the
When the target tonnage has been delivered the status on the order will be marked “completed.” With the FleetWatcher technology, a list of all loads, trucks and job history is available 24/7. The accuracy of past load counts, performance and cost efficiencies in those reports gives Middlesex ammunition at the bid table.
live LCA (load cycle analysis) Graphs, which are analyzed by the dispatch team.”
Although Middlesex has the largest asphalt plant in Florida, they do not lay all that product themselves. With the use of FleetWatcher, Iapaluccio and his team allow their customers that same visibility into the trucks hauling their materials.
Once given access, the purchaser can monitor delivery status and timing, ensuring that someone will be there to accept delivery and order additional materials on the fly. All parties can see exactly where the trucks are, when they are expected and how much of the order has been delivered versus how much is still to come. The LCAs are a major tool in this daily process. Best of all, from Iapaluccio’s standpoint, they were able to provide this service to their customers without changing their business model or procedures.
FleetWatcher also allows state DOT inspectors access to electronic tickets on DOT projects to help streamline the inspection process.
Middlesex uses FleetWatcher to enhance its internal processes and provide a quicker, more effective customer service experience. That is the value add for Middlesex and their adoption of technology.
Free software Veta can be used to fuse data from e-ticketing, paver-mounted thermal profile and intelligent compaction technology.
BY SARAH REDOHL
What happens when some of the cores taken from a paving job don’t hit density specs? You might go home and spend the evening wondering why. Was it the roller operator’s performance? Were some of the trucks not tarped, creating issues with temperature segregation? Was there an issue at the plant? Were the paver settings off?
“How do we know which, if any, of those factors came into play?” asked George Chang, director of research at The Transtec Group, Inc., Austin, Texas, during his presentation at World of Asphalt 2024. “If we don’t measure [things], we won’t know.”
The goal of his presentation was to illustrate how a free intelligent construction data management (ICDM) tool called Veta can be used to combine and compare data collected by a variety of construction technologies, including e-ticketing, paver-mounted thermal profiling (PMTP) and intelligent compaction (IC). Veta, which was initially developed in 2013 with funding from the Federal Highway Administration (FHWA), is now on version 8.0 and is required in IC specifications for FHWA, the American Association of State Highway and Transportation Officials (AASHTO), and more than 20 state departments of transportation.
With Veta, information from these technologies is available within one platform, making it possible to “track down what is the culprit for failing the density” in the above example, Chang said, “so we can fix it tomorrow.”
The ultimate goal is to make asphalt paving more consistent, Chang said. Not only would improvements in consistency lead to better performance, he added, but it would also result in improved construction efficiency, cost savings and create a record of relevant project data.
“The bottom line is if you measure [this data], you can trace [low density] back to
what might have happened,” Chang said. “If you do not [measure it], then it’s just a guessing game.”
Imagine an intelligent paving project where the haul truck arrives with an e-ticket containing source information, truck ID, amount of asphalt, route information, how long it was waiting at the job site, and when/where it was dumped into the paver (and, therefore, where each load is in the final road).
The asphalt passes through the paver and is scanned for temperature with the PMTP system behind the screed. “That will give you an idea of whether or not you have a uniform thermal profile behind the screed,” Chang said.
Then, there’s the IC-enabled roller train communicating via WiFi to coordinate and track roller passes, compaction temperatures, and level of compaction. “Then, we have dielectric profiling systems (DPS),” Chang said. This three-sensor system measures the dielectric profile on the surface behind the finish roller and correlates those measurements to cores or pucks in the lab to establish project-wide mat density. “Then, you have a very full coverage of the density on the finished mat.”
Such a project results in a massive amount of data, Chang said. “Each technology is great, but when you fuse all these technologies together, there’s a wow factor,” he added. That’s where Veta comes in. “All this data can be accessed within one interface [with Veta].”
Once all the data is in Veta, users can compare and contrast data in easy-to-read formats, including graphs and maps. For example, one could look at a map of the thermal profile compared to paver speed, or the average number of roller passes compared to roller speed.
Veta can also see whether the roller speed has been consistent throughout the project, and impacts per foot. “This will show you whether the combination of speed and vibration frequency are in concert [with that goal],” Chang said.
Veta also has a feature called ‘threshold value,’ where the user can set upper and lower limits, for example, on the rolling operation’s compaction temperatures. On one project, Chang said, “we set the lower limit [for compaction] to 180 degrees Fahrenheit and the upper limit of 225.” If any rolling occurs when the mat is outside this temperature range, the paving crew will be notified.
During his presentation, Chang shared several real-world examples where Veta was used to assess and correct compaction issues. For one project, Veta was used to compare thermal profile data against paver speed to illustrate that a failed core came from a location where the paver stopped. On another project, Veta was used to look at DPS data compared to IC data, which showed that density issues along the edge of the pavement were a result of those areas only seeing one pass by the rollers instead of the two or three passes the rest of the mat experienced.
On a 2017 project, Veta was used to compare thermal profile data against paver speed/ stopping. “You could see every paver stop, the duration of the stop, and the lower temperatures in those areas,” Chang said. The project also had a smoothness spec, and it was found that IRI issues on the project mirrored locations where the paver had stopped.
“By comparing one factor against another, these combinations can be used to determine why you may have passed or failed on your density,” Chang said. “If a core fails, [with Veta], you can trace where that failure comes from. Was it a result of roller passes, was it a delivery issue? All that data is at your fingertips.”
Astec revolutionized the paving industry with the introduction of the Shuttle Buggy, and now the SB-3000 sets a new standard in material transfer vehicles. Effortless maintenance, unmatched performance, and four steering modes for ultimate agility keep paving seamless. Experience groundbreaking innovation with the patented Ground Crew Control Station for the ultimate user experience and protection. The SB-3000 isn’t a machine, it’s a revolution in material transfer, built on Astec’s legacy of industry firsts.