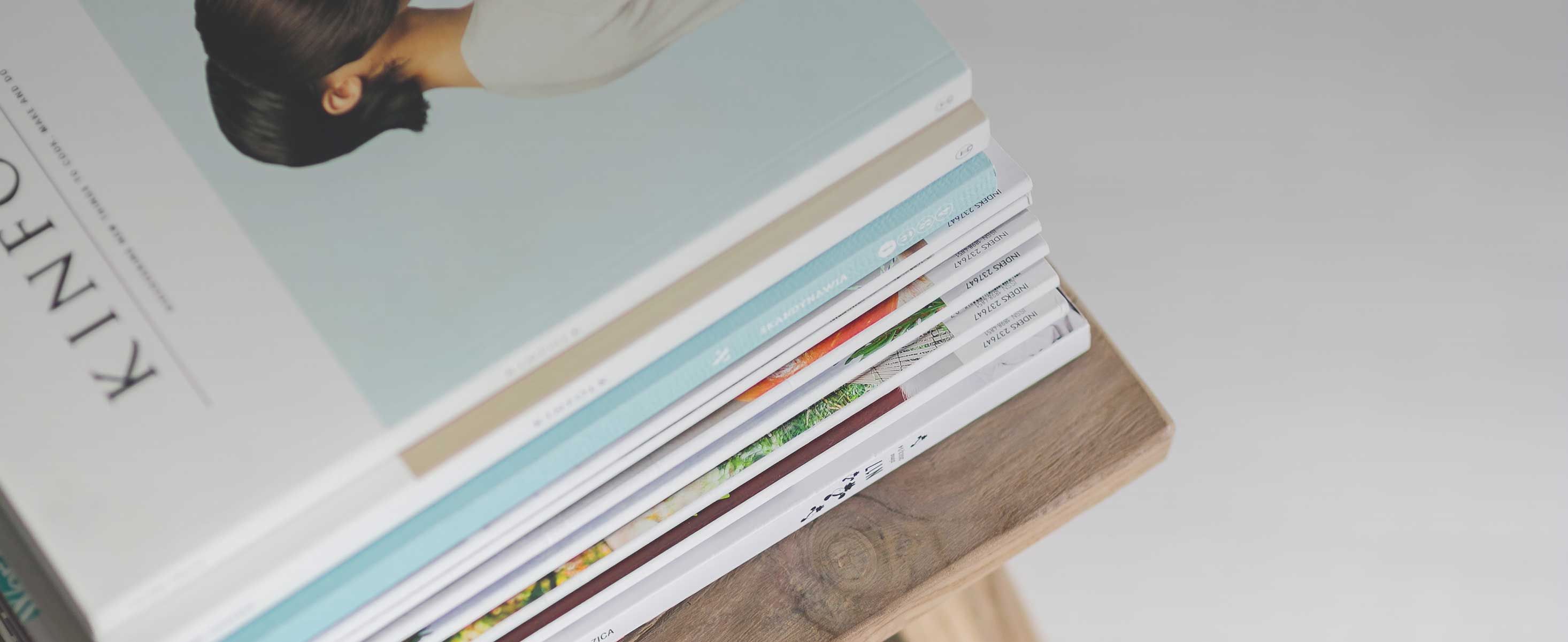
4 minute read
Mitigate Pyrophoric Material in AC Tanks
PPyrophoric material is any material that spontaneously ignites or burns in air when rubbed, scratched or struck. While not a common problem at asphalt plants, it’s important to understand pyrophoric material and limit related risks.
According to the Asphalt Institute’s recent white paper, “Pyrophoric Material Formation in Heated Asphalt Storage Tanks,” in the asphalt industry, pyrophoric material includes compounds that form on the inner surfaces of the tank, including iron and sulfur compounds or pyrophoric carbonaceous deposits usually found in coke formed on asphalt storage tanks.
“The reaction of iron oxide (rust) and hydrogen sulfide, a common volatile component of asphalt, can create iron sulfides, which are pyrophoric,” said Bill Lee, PhD, terminal manager at Century Asphalt, Baytown, Texas.
These materials can serve as a fire’s ignition source in asphalt storage tanks, which regularly meet other criteria of the fire tetrahedron, including heat, fuel, and oxygen (which can make its way into asphalt storage tanks during product transfers or maintenance).
For example, when a radar level probe was removed from the top of a heated asphalt storage tank for maintenance, air containing oxygen was able to enter the tank and reacted with pyrophoric materials in the tank—in this case, coke along the tank walls—to ignite combustible vapors in the tank’s headspace. This caused an explosion, blowing the roof off of the tank and causing a fire.
LOWER TEMPS, LOWER RISK
Lee explained the minute amounts of phosphorus in asphalt is not elemental phosphorus and thus isn’t pyrophoric. The potentially pyrophoric iron sulfide or coke that builds up in tanks is not in the original asphalt, he continued, but is created when the asphalt is exposed to high temperatures.
“When we’re talking about pyrophoric materials, we’re talking about materials that can spontaneously ignite regardless of heat,” Lee said. “In this case, heat doesn’t start the (pyrophoric) fire, but can produce the pyrophoric products that ultimately can combust.”
“Pyrophoric materials are more of a concern for different types of material other than asphalt, but could be present in asphalt due to additives that contain pyrophoric materials,” said Greg Jones, manager of heat and storage systems at BROCK, Chattanooga, Tennessee. “Where you are likely to run into issues are with cases where you’re keeping asphalt at very high temperatures, above 400 to 450 degrees Fahrenheit. The critical temperature depends on the grade of asphalt.”
These temperatures are well above the average temperatures at which HMA plants typically store asphalt, so they are usually only reached in a select few processes. “That isn’t something you’d typically see at a hot mix plant, but rather asphalt terminals and blending facilities,” Jones said.
“The most likely place for substantial iron sulfide formation would be within the polymer-modified asphalt (PMA) mixing and storage tanks,” Lee said. “The most widely used crosslinker chemical is sulfur. This means at PMA production and storage locations, the addition of crosslinking sulfur to the naturally occurring sulfur in asphalt would result in the highest concentration of hydrogen sulfide in the asphalt production or storage process.”
MINIMIZE COKE FORMATION
In its white paper, the Institute recommends a number of ways to control the conditions of coke formation. For example, air sweeping to remove fumes/vapors and maintain oxygen levels above those that encourage the formation of coke.
Another option is to blanket the liquid in the tank with oxygen-deficient atmospheres, like nitrogen or flue gas. This may encourage buildup of pyrophoric materials in the tank, but it also reduces the probability of a fire.
“Using a nitrogen blanket means replacing oxygen with nitrogen, which is non-reactive so it won’t catch fire,” Lee said, adding that such a system could be helpful during the heating process before adding ground tire rubber.
The Institute also recommends maintaining heated asphalt storage tanks’ operating temperature as low as possible to limit asphalt fumes/vapors and pyrophoric materials, and adding instrumentation to automatically monitor and adjust tank temperatures.
Coke formation can also be limited by maintaining asphalt at least one foot above the tank’s heating elements and using level control technology to fill the tank while the fill pipe is still covered by material (to prevent asphalt splashing onto tank walls).
The tank should also be stainless steel or covered with a barrier coating like phenolic epoxy to hinder rust formation. Vertical tanks can also minimize coke buildup.
KEEP YOUR TANK CLEAN
Lee’s top tip to prevent pyrophoric events is routine observation and cleaning of any coke buildup.
“The bigger the buildup, the better chance you have of having a problem,” he said. In addition, routine observation and cleaning will minimize rust formation. “You just have to keep an eye on the buildup and clean the tank when it needs to be cleaned. That alone would reduce the chances of a pyrophoric event happening.”
However, Lee cautioned, it’s important to use the proper tools. “Some tools could create a spark and ignite the pyrophoric material,” he said. That includes metal hand tools, but also jackhammers. One option Jones and Lee recommend is high pressure water jetting. “Just be sure to let the tank fully drain and dry before reintroducing asphalt,” Lee added.
One final suggestion from Lee is to use hydrogen sulfide scavengers in processing and storage. “If you reduce the hydrogen sulfide evolution, you reduce the chances of significant iron sulfide formation,” he said.