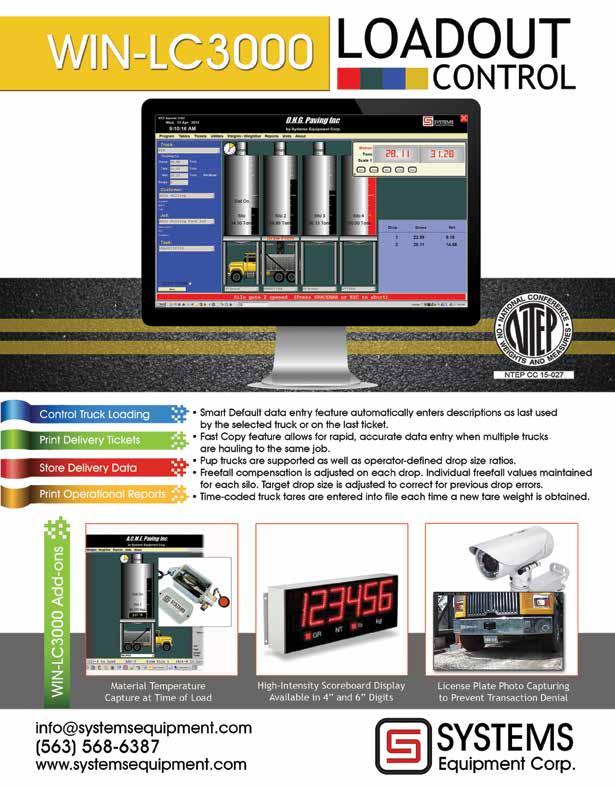
4 minute read
The Broad Strokes of Better Micro Surfacing
MMicro surfacing is used by many local governments on pavements with a variety of average annual daily traffic counts up to 250,000 vehicles per day, said FP2 Past Executive Director Jim Moulthrop. He’s one of the authors behind the Transportation Research Board’s “Guide Specifications for the Construction of Chip Seals, Micro Surfacing and Fog Seals” (NCHRP 14-37).
Moulthrop highlighted the broad strokes of several best practices from the construction guide in a recent TRB webinar.
Weather
The guide specification calls for ambient temperatures of 45 degrees Fahrenheit and rising, with no anticipated rain before the mix cures and no anticipated freezing temperatures within 24 hours of construction.
Mix Design
AASHTO’s micro surfacing mix design is PP83. “That’s usually required on all work being done for an agency,” Moulthrop said, adding that it is prepared by an AASHTO-accredited lab, and submitted to the owner agency before work begins. “Field adjustments to the design are allowed if they’re within the overall tolerances set forth in the job mix formula.”
There are a number of tests that are performed in the lab to measure the design components, including mix time, cohesion, stripping, wet tack (one-hour and six-day), lateral displacement and sand adhesion tests. “These tests typically run during the design phase.”
Pre-Construction
“Before the project starts, it’s always a good idea to have a pre-construction meeting between the agency and contractor,” Moulthrop said. He recommends discussing the construction process, quality control plan, the mix design, ingredients and materials control and measurement, as well as traffic control plans, inspection, construction of a test strip, any unique project conditions, project documentation, agency expectations and the construction schedule.
Surface Prep
To prepare the surface for micro surfacing, it’s important to properly prepare the surface. This may include crack sealing, covering utilities, patching and leveling, and removal of plastic pavement markings. You’ll also sweep, blow, or otherwise clean the pavement.
If you perform any crack sealing, Moulthrop recommends doing so at least 30 days before micro surfacing.
Application Equipment
There are generally two types of application equipment for micro surfacing, truck-mounted units and continuous run machines. Continuous run machines are fed by trucks as it goes to prevent stopping and limit transverse joints as much as possible. These are usually used on major highways and arterials, Moulthrop said.
Truck-mounted units return to the stockpile location when empty before returning to the job site to continue application. They are more commonly used in local government work and residential areas, but can also be used on highways, Moulthrop said.
Within the application equipment, there will be a spreader box with augers to continuously agitate the micro surfacing material. Then, there’s the initial strike off and secondary strike off to provide the finished surface to the material.
Calibration
“Calibration is a very important part of the operation,” Moulthrop said. “The idea behind calibration is that no machine can be used on the project until calibration has been completed and accepted.”
Each machine should be calibrated with the aggregate and emulsion to be used prior to the project, usually in the presence of a representative of the specifying agency. The name of the person who carried out the calibration and documentation should be provided.
“Generally each unit should be calibrated prior to the beginning of each project, or as required by the agency,” Moulthrop said. If you’re using the same mix throughout the season, he adds, some agencies will require calibration only once at the start of each construction season.
Test Strip
Performing a test strip offers a chance to optimize materials proportions; verify application rates, uniformity of the surface and proper alignment of the material; ensure equipment is in good condition; and the contractor has adequate workforce and workmanship to perform the job. Test strips also give us a chance to confirm cure time before you can let traffic on it.
Traffic Control
Contractors should conform to the latest version of the Manual on Uniform Traffic Control Devices (MUTCD) and state and local requirements. One concern specific to micro surfacing is ensuring the surface has had time to cure before traffic returns to the pavement.
Project Documentation
Project documentation should include the amount of aggregate, emulsified asphalt, mineral filler, additives, and water used. You should also document the percentage of emulsified asphalt, surface area application rate, and surface area application rate.
Quality Control
“Quality control is very important,” Moulthrop said. The contractor’s QC manager may or may not be on the project the whole time, but the QC technicians will be there to sample and execute the quality control plan. There have also been some efforts to certify crew members, and this may even be required in some specifications.
Testing may be done on-site with a field testing lab containing the necessary equipment, or might require technicians to return to the stockpile location where a lab can be set up.
“If we want our micro surfacing to perform, it’s important that materials, design, and construction activity meet our requirements,” Moulthrop said. – BY SARAH REDOHL.