
9 minute read
How to Exceed the Long Joint Density Spec
The construction of notched wedge joints to achieve a quality end result is catching on. Jerod Willow shared: “I have heard Wyoming and South Dakota are in the process of implementing a joint density spec. It also sounds like Illinois is starting to dabble with notch wedge joints on their J-band projects. Arkansas has fully specified a joint density spec now after working with it the past 18 months. I have also heard some limited talk in West Virginia and Ohio.” Photos courtesy of Bryce Wuori, Wuori Consulting
NNorthern Improvement Company, Dickinson, North Dakota, completed a cold in-place recycle (CIR) and paving project on Highway 8 in Dickinson County Sept. 17, 2021, with impressive density numbers. Their secret to success is wrapped up in proper equipment and best practices with the state’s new joint density spec. Let’s take a look at how Northern Improvement built a 26-mile notched wedge joint and achieved an average of 94.8% density on the longitudinal joint with 93.9% average density on the mainline.
To begin work on the Hwy. 8, JCT ND 12 to W JCT ND 21 project in early August 2021, Northern Improvement performed CIR to a depth of 3 inches.
The paving consultant on the project, Bryce Wuori of Wuori Consulting LLC, Bismarck, North Dakota, observed, “The existing road surface prior to the CIR was so rutted and had such deep transverse cracks it was almost unsafe to travel down the road at the designated speed limit. There was no ride incentive included on the project for Northern due to how rough the existing road surface was prior to construction. After the CIR and before the asphalt paving, the road surface rode very nicely, almost comparable to that of a common low-volume asphalt highway.”
Paving began Aug. 9 and involved two lifts of 1.5 inches of Superpave FAA 43 with a CHS 58S-28 AC for a total design lift thickness of 3 inches. As required by the Jan. 5, 2021, NDDOT longitudinal joint for hot mix asphalt pavements special provision, the team built a notched wedge longitudinal joint, which had a required average density of 90.5 on the joint. The project called for at least a 92.5 required density on the mat. They used the Notch Wedge System from Willow Designs LLC, East Berlin, Pennsylvania, attached to a CAT SE60 screed. The system consists of the Willow Designs notch wedge joint maker and notch wedge pneumatic roller.
“Something unique about Bryce is that he uses ground penetrating radar (GPR) as quality control to improve density consistency in the mat and, more specifically, the longitudinal joint,” Jerod Willow said. “We share a lot of the same clients in that region and we often converse on how to improve a contractor’s ability to get density in the mat and joint. He has some pretty impactful data from this season.”
Wuori explained how Northern Improvement built the joint with quality control as part of the process. “We used the Notch Wedge System from Willow Designs to construct a ½-inch notch. The key part of
compacted lift thickness
1/2 " 1/8± " 1/2 " 1/8± "
12 Inches
The North Dakota Department of Transportation released a special provision Jan. 5, 2021, detailing the manner in which contractors would be paid for density of longitudinal joints for hot-mix asphalt pavements. If a notched wedge joint is used, it is to be constructed according to the diagram in Appendix A of the special provision. Illustration by Maranda Wilbanks for AsphaltPro
this system is rolling the wedge properly to set the joint in for optimum density. The density on the joint is measured with a combination of a Troxler nuclear gauge and the PaveScan 2.0 GPR.”
The technology he references is from Geophysical Survey Systems Inc. (GSSI), Nashua, New Hampshire, which makes the PaveScan RDM 2.0 continuous, non-destructive, asphalt density assessment tool described in the May 2017 Here’s How It Works department. Wuori explained that he can walk the entire length of the project with the PaveScan device, taking readings along every inch of the joint. If he were to receive a reading indicating a weak area, he could inform the paving crew immediately, rather than waiting until after construction is complete to return to the field to address possible failures.
“In the event of reading below the 90.5 requirement, I would advise Northern to look at rolling patterns and what rollers are being used for compaction, then inspect and evaluate the setup of the notch wedge system as well,” Wuori said. “Typically, if the notch wedge is being constructed properly and rolled correctly the contractor will pass joint density requirements on every paving day. I have been on over six projects this year where the addition of the Willow notch wedge and correct rolling procedures brought the paving contractor from failing required density specifications and getting deducts on the joint density to passing with incentives with the addition of the notch wedge and correct rolling procedures.”
The PaveScan, coupled with density gauges, played a hand in setting up the rolling procedures. Wuori explained: “Average mat density is recorded with the combination of destructive coring, nuclear testing and the PaveScan GPR. We use the PaveScan GPR and nuclear gauge to set up rolling patterns and develop a paving process for success and compare this data to the results performed in the destructive coring process. Northern Improvement also used intelligent compaction on this project to give roller operators temperature zones for optimum compaction and roller pass counts for efficiency and accuracy in the rolling process.”
The rollers they used were a CAT CB 16 with an oscillating front drum in the breakdown position, a CAT CB 66 with dual vibratory drums in the intermediate position, and a CAT CB 68 set in static only in the finish position. The operators stayed aware of temperatures and rolling zones, which fluctuated for this mix.
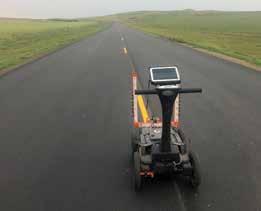
The quality control team was able to run the PaveScan 2.0 ground penetrating radar device along the joint to take continuous density measurements. The device is available through InstroTek Inc. as of Q1 2021.
On the left side of the screed, you see the system from Willow Designs building the first pass of the notched wedge joint. On the right side of the screed, you see the contractor-built sluff box and roller creating the safety edge. Superintendent Joshuah Davis shared: “We use a company designed system that we call a sluff box that’s adjustable in width and slope to achieve a 4-1 slope that is rolled with what we call a sluff roller. This is a safety edge required on all North Dakota roads.”
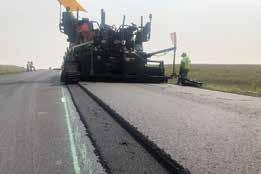
“The average temperature the mix was delivered to the paver ranged from 250 to 280 degrees depending on the weather that day and the distance we were paving from the asphalt plant,” Wuori explained.
“Notch wedge joints work because they confine the asphalt mix in the joint better than a butt or vertical joint, meaning that there is 85% less loose mix in the joint,” Willow explained. “Loose mix in the joint means a failure. Notch wedge joints are also stronger joints due to the increased surface area of the joint; this style of joint and similar forms of this joint have also been used in other construction materials from wood, metal and stone dating back hundreds of years.”
“This mix had a very good design and was an average mix to achieve density with when compared to the FAA 43 mix designs,” Wuori said. “Due to the high amounts of aggregate absorption in the aggregate used in the design, the AC content was higher than what is normally seen on this type of mix design (6.8 percent). The one drawback of this mix in the field was its ability to turn tender on the hotter days of paving.
“On these days, we would have to get most of our compaction up front on the hot mat with steel drum rollers before the mix cooled to 200 degrees. At 200 degrees the mix would develop a tender zone that would hold until about 160 degrees. This was only on days that the ambient temperature was above 85 degrees with very little wind on the project.”
On the hotter days, when the tender zone appeared, the rolling train switched out the CB66 steel drum with a Sakai GW750-2 vibratory pneumatic roller. “We would also introduce a pneumatic roller into the train to get through the tender zones because a steel drum would tear and fold the mat if used when the mat was tender.”
Despite the tender zone challenges, the roller operators achieved higher-than-required results. “The overall average joint density for the project was 94.8%,” Wuori shared. “One day’s average joint density was a 95.7 on 13 core locations. The roller operators do an exceptional job of holding patterns and understanding when the mix would become tender or what would need to be done to battle this issue. Having good, trained roller operators that understand their equipment and how important their skill is to the finished asphalt product is key in producing successful projects. These roller operators have been trained very well and have been put through some of the most difficult projects out there and have shown how a skilled roller operator can make or break a project.”
The roller operators included Raquel Davis on breakdown, Kim Bumgardner on intermediate, and Luellen Johnson on finish. The Hwy. 8 CIR and pave project was a team effort that included the skills of roller operators and the entire quality-minded crew. Superintendent Joshuah Davis shared: “The crew from front to back were Brad Barnick dump man; Alyssa Polanski paver operator; Mac Cook screed operator; Amber Hoots and Ron Comon QC; fill in roller operators were Deryk Drew, Cody Bellon; plant operator and foreman Tom Stickel; supervisors were Jason McIntosh foreman and myself. Also a huge part of all this is Bryce Wuori. Because of his training and vast knowledge, he has helped me make this crew into what they are today. Without them we would never be able to achieve this. They do such a good job with the flow and consistency to achieve the compaction and ride.” Wuori also commented on some of the best practices he saw in the field.
“Their best practices for quality included paver setup/ and consistency. By eliminating paver stops and keeping the paver at a consistent speed throughout the day. Then roller consistency using Intelligent Compaction as a tool to keep operators in designated temperature and pass count efficiency. And proactive quality control to ensure paving and rolling techniques being performed during paving operations produced the desired results.”
By the time Northern Improvement was ready to turn the pavement over to the stripers Sept. 17, they had a new roadway made safe for motorists in Dickinson County.
– BY SANDY LENDER

