
10 minute read
American Pavement Paves the Way for Amazon
DDuring World War II, the building at 75 Aircraft Road, Southington, Connecticut, was home to the aerospace manufacturer Pratt and Whitney. After its construction in 1942, the facility spent the war manufacturing and repairing Double Wasp engines and producing components used in the Republic P-47 Thunderbolt fighter and Consolidated B-24 Liberator bomber.
According to Preservation Connecticut, a nonprofit organization established by the Connecticut State Legislature to preserve the state’s historic buildings, operations at the facility peaked for the company in 1968 and steadily declined until Pratt and Whitney’s parent company, United Technologies Corporation, announced the plant would close in 1995.
For more than 20 years, the building and its 300,000-square-foot parking lot sat empty, until it was leased as a fulfillment center in 2017. Now, Amazon uses the facility to park more than 700 vans each night. It is one of a handful of facilities the company has invested in throughout Connecticut over the past few years.
According to the Hartford Business Journal, realty experts say Connecticut is an “ideal choice for fulfillment- and distribution-related enterprises” due to the many major interstates running through the state and the availability of large land parcels. For this particular distribution center, Amazon didn’t have to start from the ground up, utilizing the old Pratt and Whitney factory.
However, the parking lot was a different story. According to Josh Stanley of American Pavement Specialists, Danbury, Connecticut, the lot was between 30 and 40 years old and full of potholes and spider cracks. There were issues with standing water and it seemed as though multiple patch and shim jobs had been laid throughout the lot to maintain it over the years.
When American Pavement was hired to repair the parking lot, the company decided full depth reclamation (FDR) was the best course of action so Amazon would have a new pavement from the subgrade up.
The crew placed 1.5 inches of Class I asphalt, followed by a 1.5-inch top course of Class II asphalt. In total, the job required 6,000 tons of asphalt. The job was awarded very late in the 2020 season, with American Pavement beginning their work early November.
FROM INSTAGRAM TO AMAZON
The prime contractor, Lascon Inc., Eastchester, New York, asked for quotes from three paving companies: two large paving corporations and American Pavement, “the lean, mean paving specialists,” Stanley said. Although American Pavement had bid on other Amazon projects, this was the first one they were awarded.
Ultimately, Stanley said, they were awarded the job after Lascon spent some time on their Instagram page. “They said once they saw the pride we took in our work and the way we operate, they felt we were the right company for the job,” Stanley said.
The job was awarded very late in the 2020 season, with American Pavement beginning their work early November. The Tilcon asphalt plant located five miles from the project would be closed over the winter, so the job needed to be completed before the plant’s season shut-down Dec. 14.
Once the reclaimer was in the ground and there was enough room for the grader, the crew began grading. As soon as the grader finished a section large enough and compacted enough for paving to begin, the paving crew set to work. “Our projects are one continuous ballet of equipment and manpower,” Stanley said.
The job called for FDR, using the underlying materials for a stabilized base course. They reclaimed the existing asphalt and gravel subgrade to a depth between 8 and 12 inches. The crew performed this with its Wirtgen WR 200i reclaimer. Due to the large size of the lot, American Pavement hired out a CMI reclaimer from Garrity Asphalt Reclaiming Inc., Bloomfield, Connecticut.
“Hiring a second reclaimer to help with the cutting was one of the best decisions we made,” Stanley said. “That one decision probably cut two days off the entire project.”
BUILT TO CONNECT
Efficiency and Productivity
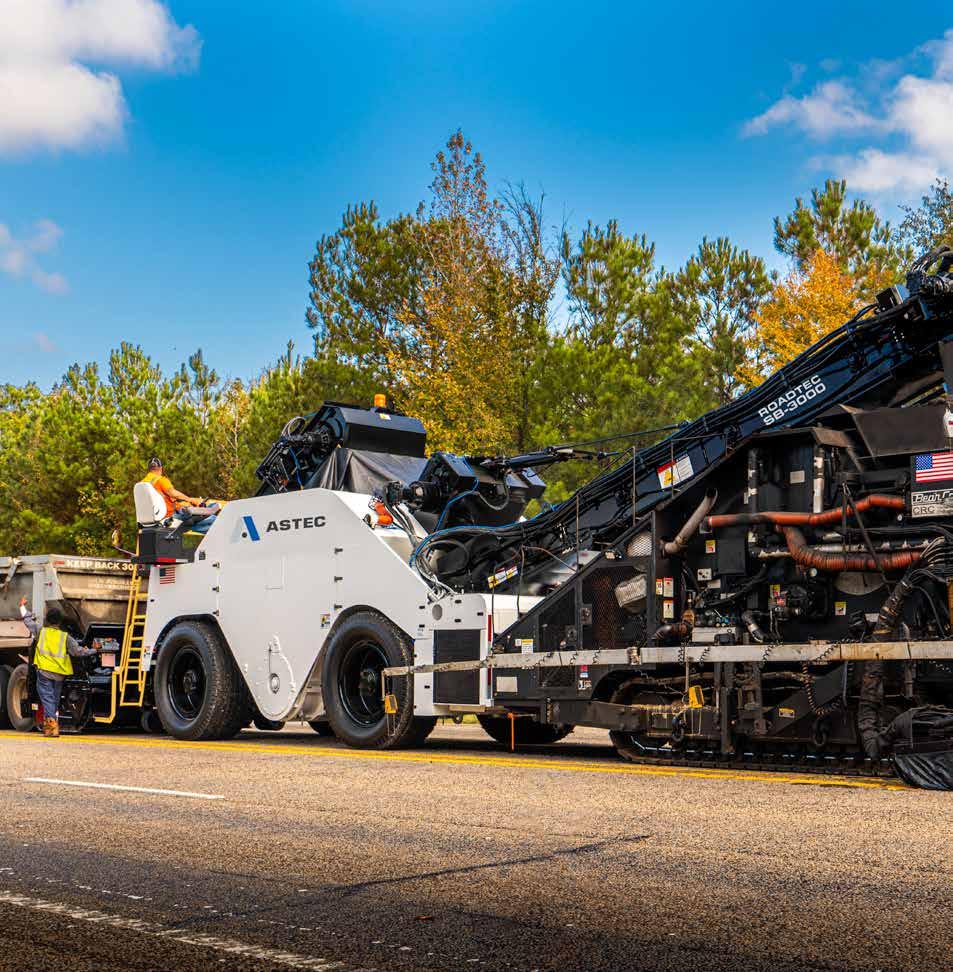
Designed with safety and operator comfort in mind, the Shuttle Buggy® SB-3000 material transfer vehicle features adaptive cruise control, bright LED lighting, four-wheel steering for easy transport and ground-level maintenance access for added convenience. Operators can rely on clear sightlines and the ground operator is safely protected inside the structure of the machine. The Roadtec SB3000 is the perfect blend of traditional craftsmanship and modern technology.
The age of the lot presented challenges to the process. The asphalt varied between 3 and 8 inches thick, with structures and wires buried and abandoned throughout the project. The entire lot was surveyed by Call Before You Dig (CBYD), which marked out all utilities. “When working on a parking lot this old, the prep process is very difficult because you never know what you are going to run into when you put your teeth in the ground,” Stanley said. “When ripping up a lot this old, you can bet there’s always surprises.”
A reclaimer could not be used for the entire parking lot, due to the buried utilities and proximity to curbing, fences and catch basins. Roughly 10,000 to 15,000 square feet of the asphalt had to be removed with an excavator or skid steer, loaded up, and hauled off site. Then, the rough grading, compaction and fine grading could begin.
“The original asphalt grade wasn’t great, so during this fine grade process there was quite a bit of cutting and filling being done,” Stanley said. Thankfully, the company’s Leeboy 685 and John Deere excavators and its Mauldin 413 MXT Maintainer and John Deere 333G skid steers got the job done.
Next, the crew placed 1.5 inches of Class I asphalt, followed by a 1.5-inch top course of Class II asphalt. American Pavement’s Vogele 5100-02 Vision 8-foot track paver put down the majority of the first course of asphalt. By the end of the season, the screed plates were pretty worn out. When Caterpillar offered the company a demo of a Cat AP555F 8-foot track paver, the crew ended up using the machine to pave the majority of the top lift in the larger areas.
The final sections of the top lift, about 600 tons total, were in smaller sections of the lot. The crew paved this portion of the project with its Leeboy 6150 paver. “Operating a Leeboy in a parking lot, versus a larger road paver, makes a huge difference in the amount of hand work for the paving crew,” Stanley said. “Being able to get closer to structures and closing gates at the end of passes reduces handwork a ton.” In total, the job required 6,000 tons of asphalt.
The crew took their time with the layout to maximize its efficiency, marking out each pass beforehand. “On jobs this size, we like to lay out the parking lot the night before,” Stanley said. “All our crews need to do the next day is fuel up the equipment and start paving.”
The mat was compacted with American Pavement’s Hamm HD70, HD80, HD14 and HD12 vibratory rollers, all equipped with oscillation. In the final phase, the crew finished up sidewalks, curbing, aprons and performed site clean-up.
Paving up the curbing/sidewalk turned out to be one of the more challenging aspects of the job. “The sidewalk in front of the building—1,000 feet of sidewalk—was completely flat with zero pitch,” Stanley said. “We had to get creative and create a high point on the curb line.”
This meant they lost their 6-inch reveal, but the engineers on the site acknowledged the problem they were facing and approved the fix. “It took some time, but we eventually were able to pave along this sidewalk and not leave any puddling. The paving gods were with us on this day!”
The size of the lot was also unwieldy. “It literally took five minutes to walk from one
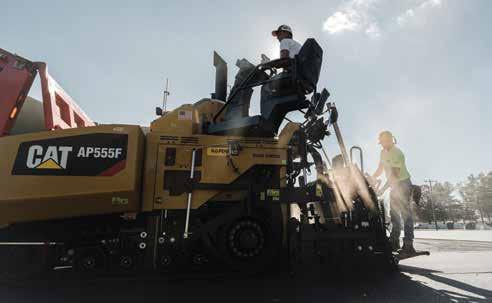
The lot was between 30 and 40 years old and varied between 3 and 8 inches thick, with structures and wires buried and abandoned throughout the project. The entire lot was surveyed by Call Before You Dig (CBYD), which marked out all utilities.
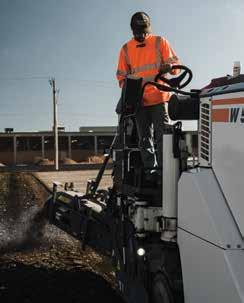
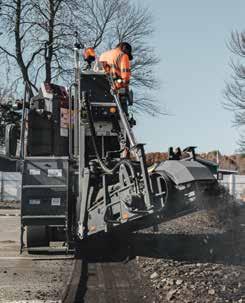
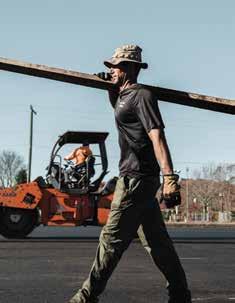
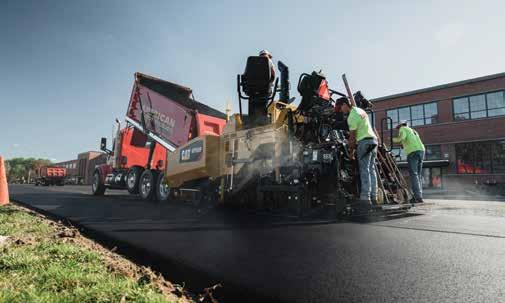
LEFT: The mat was compacted with American Pavement’s Hamm HD70, HD80, HD14 and HD12 vibratory rollers, all equipped with oscillation. RIGHT: The Tilcon asphalt plant located five miles from the project would be closed over the winter, so the job needed to be completed before the plant’s season shut-down Dec. 14.
The 300,000-square-foot parking lot is used to park more than 700 vans each night.
side of the job to the other,” Stanley said. “If your crews get spread out and tools get dropped all over the place on such a large property, production decreases quickly.”
Throughout the job, the crew also had to contend with more than 700 Amazon delivery vans using the lot on a daily basis. The size of the lot made this less of a problem, except for one day when there was a miscommunication about where the crew would be working. However, the crew was quickly able to adjust its operations for the day to accommodate the customer.
“Field decisions like this are great examples of the benefits of working with a lean, mean, versatile company like ours,” Stanley said. “Having the boss and multiple foremen on site at all times is why we’re able to quickly adapt and overcome any obstacles thrown our way.”
DELIVER ON DEADLINES
Typically, a project like this would have taken the company 14 days to complete, but weather conditions and the customer’s tight schedule required them to work as quickly as possible. They finished the project in just eight days. In fact, the speed at which the crew was able to pave the lot was one of the coolest aspects of the job, according to Stanley.
“It’s very rare that we get to pave large open parking lots with 1,000-foot-long passes,” Stanley said. The crew was able to pave at a very fast pace for parking lot paving, up to 80 feet per minute. Some days, the crew was able to pave 700 tons before noon. “It’s a rewarding feeling to be able to complete such large areas in one day.”
One of Stanley’s tips for performing the job under such a tight deadline is teamwork. “We strive to keep our laborers and machines working in unison,” Stanley said. They’ve found that their laborers don’t work as quickly when working apart from one another. “We always stress to work together. Don’t spread the crew too thin.”
He also recommended starting the day in areas where the crew can maximize its output early on and meet the least resistance, opting to begin in wide open areas versus difficult ones. “Just like in your daily routine, a productive morning brings a productive day,” Stanley said. “It’s no different in paving.”
And on this job more than most, productivity was imperative. American Pavement’s end-of-season schedule was tight, there were only four or five weeks left in the paving season, and American Pavement never wants to be the type of company that is too busy for its customers at the end of the season, requiring them to find another contractor.
“We tell our employees that the last two months of work are not for us as a company, but for our customers,” Stanley said. “Our loyal customers put food on our table all year long. We have to come through for them at the end of the season when they need us the most.”
“This project was like the battle that ended the war,” Stanley said, and a great bookend to a busy season. “The guys absolutely killed it! When you get a chance to pave a project this large, it’s something special. We know it, the crew knows it, and the customer knows it.”
