
13 minute read
Even More Production Equipment for More Tonnage
TTo get consistent production, your operation requires on-spec materials delivered in a metered, measured fashion. For the savvy plant operator, perusing lists of parts and services such as what you’ll find on the next few pages is part and parcel of doing business. The plant and production related original equipment manufacturers (OEMs) who provided information for this department signify by their participation that they’re engaged in educating the marketplace. They’re ready and willing to share not only their products, but also their expertise with you when you reach out for more information. Those who are also advertising partners who support this publication have live links to their favored landing page for your convenience when you view this department on our website at https://theasphaltpro.com/ departments/product-gallery/. Be sure to let these folks know you saw their information in The AsphaltPro magazine and make use of their knowledge and experience in the industry to enhance your bottom line.
ASTEC
While almost any Astec burner can be configured for a retrofit application, Astec recently launched a new burner designed to offer several advantages for retrofit customers. When creating the new Astec Versa Jet™ burner, Astec engineers reimagined the asphalt plant burner to create a new system that takes an evolutionary leap forward. According to the manufacturer, advantages the Versa Jet burner delivers for retrofit applications include: a versatile platform that has the capacity to fire at a range of rates and can be easily configured to meet production needs, the option to reuse an existing fuel train, compatibility with virtually all drum designs without complicated drum modifications, the ability to work with existing controls, and a unique platform that permits quick setup. The versatility of the Versa Jet burner means it can also be easily relocated to a different plant if the need arises. In addition, the Versa Jet burner uses less energy The Versa Jet burner from Astec is designed for use in retrofit applications.
than other comparable burners, according to the manufacturer.
For more information, visit: https://www.astecinc.com/products/dryingmixing/burners/versa-jet-burners.html
BROCK
BROCK, Chattanooga, Tennessee, announces Junior Lasley has joined the company as manufacturing manager. Lasley comes to BROCK after spending all 33 years of his working career at Astec Inc. At the time of his departure, he was responsible for most of the manufacturing facility that produced hotmix asphalt equipment.
Commenting on the addition of Lasley, Ben Brock, president and CEO of BROCK, said, “We are very excited and humbled to have someone of Junior’s knowledge, experience and character heading up the manufacturing arm of our company. He is an expert in his field and has been around the art of manufacturing hot-mix asphalt plant equipment for 33 years. He is a tremendous addition to our team and will be fantastic for our customers.
“With the addition of Junior to our team we are able to allow Anthony Caldwell to focus completely on our in-field Construction Services efforts,” Brock continued. “Anthony had been leading both manufacturing and construction. These moves, along with others that will be announced soon, are only possible with the incredible support of our customers. We thank our customers, and we remain focused on providing quality products, outstanding service and great relationships.””
For more information, contact Travis Sneed at (423) 476-9900 or visit www.brock.industries.
BROCK has brought a new manufacturing manager with 33 years of experience in HMA equipment on board.
CATERPILLAR
Caterpillar offers in the 9- to 11-tonne (10- to 12-ton) wheel loader class, the new Cat® 980 and 982 medium wheel loaders, stating they are up to 10% more productive and lower maintenance costs up to 20% when compared to the previous 980M and 982M powershift models. New to this class of medium wheel loaders, the Cat 980 XE and 982 XE models feature a Caterpillar designed and manufactured continuous variable transmission (CVT) that delivers increased fuel efficiencies up to 35% and lower maintenance costs up to 25% compared to the M series models. These new wheel loaders include an expanded technology platform to increase machine performance and improve operating efficiency, according to the manufacturer.
Standard Cat Payload with Assist on all 980 and 982 series loaders is designed to provide an accurate weighing of bucket payloads, so operators can load to target the first time every time. This new technology includes lowlift-weigh and manual tip-off functions.
For more information, visit your local CAT dealer.
COMMAND ALKON
Command Alkon, Birmingham, Alabama, and Libra Systems, a subsidiary of Command Alkon, are pleased to offer the Silo Safety System to ensure the safety of the driver and vehicle and eliminate loss of material in overhead silo
loadout situations. The standalone system is designed to support operations that have any type of overhead loadout scenario.
“Once the gates on the silo open, a literal ton of material, sometimes at 320 degrees Fahrenheit for asphalt loadout, is being dropped from the silo in the matter of one second,” said Greg Fleisch, Libra sales manager. “If the vehicle is not in the correct location, this puts the driver at risk for serious injury and can cause extremely expensive damage to the cab of the truck as well as lost time and materials in the production process. The Silo Safety System could more than pay for itself with the price of one accident.”
“Now that Libra Systems is under the umbrella of Command Alkon, we can offer this solution across our base of customers using Libra and Apex for asphalt and aggregate operations, as well as COMMANDbatch customers in ready mix operations to ensure safety and mitigate the risk of lost materials,” said Lori Allen, director of corporate marketing at Command Alkon.
The Silo Safety System features infrared sensors to enable each silo, if and only if, the truck is in the proper position. As the truck pulls through to the loadout station, it will break the infrared sensor beam to enable the silo to be opened. The Silo Safety System includes these important features and benefits: • Completely stand-alone system compatible for use with any overhead loadout scenario and automation system. • Two Infrared sensor sets indicate when vehicle is appropriately placed for loading and silo gate activation. • Three sensor set configuration allows for detection of space between cab and trailer. • Fully graphic touch screen display indicates sensor and silo gate activation to operator.
Available with pedestal stand for desktop placement or can be panel mounted. • Manual override mode with redundant loadout system interlock for scenarios not meeting standard vehicle and loadout situations. • Real-time alerts indicate potential defective sensor situations. • Stand-alone Junction Box and PLC controls ensure ease in wiring, installation, and sensor location tuning.
“This solution saved us the first day that we had it,” said Dewey East, owner and founder of Southeast Plant Services. “One of our operators tried to open the incorrect silo immediately after the installation, and the Silo Safety System prevented the gate from opening.”
For more information, visit www. commandalkon.com/getsilosafety.
CONVEYOR COMPONENTS
The Model CT, as manufactured by Conveyor Components Co., Croswell, Michigan, is comprised of a control unit and tilt probe, which is designed to sense the presence or absence of material. The cULus-listed control unit is enclosed in a cast aluminum housing with external red and green LED status indicator lights and surface mount printed circuit boards. Weatherproof, dust-ignition proof and explosion proof models are available. Optional black epoxy powder coating is available for corrosive environments. The tilt level controllers (CT-105, CT-106 or CT107) have an intrinsically safe output to the tilt probe and are cULus listed as intrinsically safe when used with the cULus-listed tilt probes, according to the manufacturer.
The Model CT is commonly used when other controls won’t work due to bin vibration, or actual bin walls aren’t available for mounting other controls. Typical applications include level detection in hoppers, silos, stackers, crushers and conveyor transfer points.
The CT tilt probes are available as a compact 6-inch tilt probe or the standard 9-inch tilt probe and have 25 feet of electrical cable. Stainless steel probe housings are available as an option. Float ball and paddle accessories are also available for fine-grain materials.
For more information, contact Conveyor Components Company at (800) 233-3233.
CORE
Core, headquartered in Palo Alto, California, announced the launch of Crews by Core Pro, a Labor Operating System (LaborOS). This new, single solution platform offers the capability to hire, and manage crews with a task and labor management tool that syncs with your existing systems, to get labor onsite, improve communication and reduce rework. Since its launch September 2020, the construction labor marketplace has matched hundreds of companies with thousands of workers, all with the help of technology and built-in algorithms that leverage keyword search for both jobs and workers.
“As a labor management platform, we’re connecting the whole team across the field and office, to optimize daily workflow and communication, especially for the foreman and project manager,” said Di-Ann Eisnor, CEO and co-founder of Core. “We spoke to over 5,000 trade professionals and 50 GCs to understand how we could best serve them—what we heard was an overwhelming need for better communication among crews and between the field and office. This feedback inspired us to develop a labor management and communications platform that supports productivity on the jobsite every day and reduces friction for everyone on the team.”
Across the world’s largest industry, construction, 52% of rework is caused by poor project data and miscommunication. This amounts to $31 billion in wasted investment in the United States alone. When combined with a 430,000-worker labor gap cited by the U.S. Bureau of Labor Statistics, the need for a worker-employer solution is imperative.
Crews by Core Pro LaborOS connects teams in a single system on desktop and/ or mobile. Project managers and general superintendents have access to managing thousands of tasks, keeping foreman and crews efficient and organized.
CWMF
The Wedge-Lok™ Tire Suspension System from CWMF Inc., Waite Park, Minnesota, has been in use for over 25 years. The design allows the end user to secure the tire to the drum and eliminate tire slippage by simply adjusting setscrews. The inclined plane mechanism provides superb holding strength and there is no need to apply shim stock, according to the
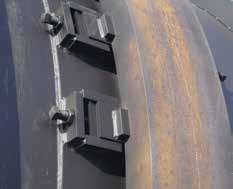
The Wedge-Lok™ from CWMF retrofits on this CMI drum.
manufacturer. A secured and balance tire extends the life expectancy and reduces costly downtime. CWMF will be introducing a new featured video onto their website (summer 2021), which will demonstrate how to properly install the Wedge-Lok™ Tire Suspension System.
For more information, contact sales@ cwmfcorp.com or visit www.cwmfcorp.com.
DUREX
Durex Products Inc., Luck, Wisconsin, a manufacturer of wire and polyurethane screen media technologies, announces its recent hire of Bob Doll, who joins as a regional sales manager covering the Eastern United States.
“As an effort to increase our Eastern U.S. market presence, we are excited to have Bob onboard,” said Chad Hackett, president of Durex Products. “Bob brings with him many years of industry knowledge and sales expertise that will be very beneficial to our customers.”
Doll comes to Durex as an industry veteran with 43 years of experience in crushing and screening, working for W.S Tyler, Metso, Buffalo Wire Works, and McCourt and Sons Equipment.
For more information, contact Durex Products at (715) 472-2111.
EVOQUIP
Powerscreen Crushing and Screening, the authorized distributor for EvoQuip’s compact mobile crushing and screening equipment for Kentucky, Tennessee, Alabama, Mississippi and Indiana has opened a new facility that encompasses a five-acre site with office, warehouse and workshop facilities in Indianapolis, Indiana. Heading up the new facility is Connor Cobane, originally from Carrickmore, Northern Ireland, a region well-known for being a center of crushing and screening manufacturing worldwide.
KUBOTA
Kubota Engine America, Lincolnshire, Illinois, offers the newly developed D902-K, announced by Kubota Corporation’s president and representative director, Yuichi Kitao, as “Kubota's first electronically controlled diesel engine below 19 kW.” The D902-K will bolster Kubota's diesel engine line as it responds to various regional emission standards, including EPA Tier 4, Stage V, China IV standards and China's Category III national smoke regulations, which will be implemented December 2022.
The new D902-K is a three-cylinder diesel engine with a displacement of 0.898 L and an output of 18.5 kW, and it consumes approximately 5% less fuel than its current conventional model. Tomokazu Matsushita, president of Kubota Engine America, said: “Kubota’s D902-K electronically controlled engine allows manufacturers to easily replace the existing engine without the need to redesign the current machine. It will match current dimensions, structures and power takeoff of existing engine.”
Mass production is scheduled to begin in 2022.
McCloskey
McCloskey International, Keene, Ontario, has unveiled the I4C, the latest entry into McCloskey's impact crusher line. According to the manufacturer, it brings the power and productivity of a 44.3-inch (1,125-mm) impactor to a compact footprint for maximum maneuverability.
The 44-inch impact crusher has been designed with a deeper chamber, creating greater tramp release space. With an aggressive blow bar and apron design, 4-bar variable speed rotor, and three crush zones with an optional fourth strike, the I4C can be set up as a primary or secondary crusher.
A new asymmetric feeder is designed to reduce bridging that can occur in some applications and, combined with the single-unit feeder-hopper construction, delivers better motion and vibration for the material as it moves into the impact chamber.
MAJOR
MAJOR, headquartered in Candiac, Quebec, has appointed Manganese Crushtech Systems its new aggregate and mining screen media authorized dealer in Africa. The company will serve customers in Zimbabwe. Manganese Crushtech Systems offers MAJOR’s screen media solutions, including FLEX-MAT high-vibration wire screens in tensioned and modular versions.
POWERSCREEN
Powerscreen, a Terex company, continues its decarbonisation story with its electrification strategy, including the brand-new Eco-Warrior battery powered screener.
Neil Robinson, Powerscreen product and applications manager said, “Some may view this topic as a recent trend, but for Powerscreen, decarbonisation is multi-faceted and has always been at our core. The Powerscreen mobile concept has always contributed toward decreasing the carbon footprint per tonne of material produced. This is done by reducing unnecessary material handling of hauling and loading material to static plants in aggregate production or in the ability to recycle and reuse material at point of use, for example in roadbuilding projects where sub-base material is produced in situ. Using stockpiling conveyors as part of a track mobile set-up is another perfect example of how to cut out unnecessary double handling, reducing fuel consumption and therefore carbon production.”
Powerscreen has evolved its product range to reduce environmental impact by making its crushing and screening equipment as fuel efficient as possible, using direct drive systems for its crushing range and improving engine capabilities and drive-line design for its screening range. Another important tool for its fuel efficiency is Powerscreen Pulse™, in-depth machine telematics that helps customers see how and where their machines are being operated, understand fuel consumption and carry out fault-finding activities to ensure optimised performance.
Electrification is currently a key focus of the Powerscreen decarbonisation strategy. The Powerscreen Hybrid range, designed to give customers alternative energy options to operate their range of crushing, screening and conveying equipment, has been enhanced to include more fully electric crushers and screeners as well as models powered by combinations of diesel and electricity. These options enable customers to choose which fuel to use, depending on cost, location and availability, and benefit customers who operate in an area where electricity is more cost effective than diesel fuel, where diesel engine noise is unwanted or on sites where electricity is the preferred energy source.
Neil continued, “Customers using Powerscreen Hybrid units powered off the grid have