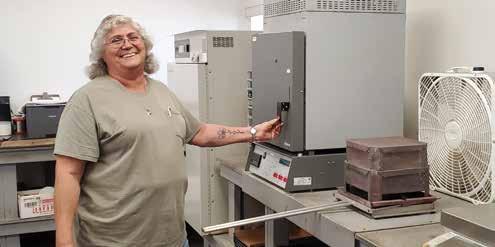
20 minute read
Two Women of Asphalt Meet Ajax’s Jewel Eggleston and Renee Aguis
TThey started in different roles but now work on quality control/quality assurance (QC/QA) from two angles to place award-winning pavements for the Southeast. QC Lab Technician Jewel Eggleston and Roller Operator Renee Aguis are just two of the team players for Ajax Paving Industries of Florida LLC, headquartered in North Venice. Here they share what brought them to the asphalt industry and what makes them proud to be women of asphalt.
Ajax Paving Industries of Florida is an equal opportunity employer and boasts a number of women of asphalt, including Project Manager Jessica Kiesel, who will be featured in an upcoming edition of AsphaltPro. This month, let’s take a look at the way Eggleston and Aguis handle QC for a company that has served more than 2,000 clients and garnered more than 500 awards.
AsphaltPro: Could you share with the readers your career trajectory since joining the asphalt industry and what challenges you’ve overcome along the way? Jewel Eggleston: I was all around the asphalt industry for years. I drove truck as a transport driver and delivered asphalt from local plants for three years. Then in the late ’90s, I became a QC plant inspector.
I started with Ajax Paving Industries of Florida in 2007 as a quality control lab technician. The most rewarding aspect is the relationships I have formed with our outside sales customers and our plant employees. We have become family-like over the years. Jewel Eggleston is the quality control lab technician for Ajax Paving Industries of Florida. She stated the plant and loader operators are her key team members at the asphalt plant.

Renee Aguis is a lead roller operator for Ajax Paving Industries of Florida. She stated one of the biggest obstacles she’s had to overcome as a woman in the paving industry is that some of her male colleagues didn’t look past her gender to recognize her knowledge and skill. “I did not fit the typical stereotype of a woman in construction: I like to have my nails done and like to have my hair done. All I can say is always be you, do not try to be who you think other people want you to be. Stay true to yourself and you will perform your job better.”
I used to watch the TV show “That Girl” with Marlow Thomas. I always wanted to be “that girl.” She had her own apartment, had a job and was self-sufficient—didn’t need help from anyone else. That show was my motivation. Renee Aguis: “My career in asphalt began at age 41, in 2014, accidentally. My first career was as a stay-at-home mom of my first three boys. I was the wife of an asphalt man, so I did have some knowledge at the beginning. At the dinner table, he would explain to the boys and me the different details of his day, what the machines did, etc. I recall at the time I did not understand the terminology he would use. Therefore, I would look up some of those complex words so I would have a better understanding of what he was saying the next night.”
In 2013, after welcoming their fourth son, Aguis suffered from postpartum depression. “With four kids, one income, and very little to no self-esteem, my husband encouraged me to go back to work.”
Finding a job after being out of the workforce for 17 years wasn’t easy. Aguis’s husband asked his foreman to help out. At the time, Ajax used a labor service so they brought Aguis on as a flagger for the crew. She says the crew thought her shy and insecure nature, combined with the humidity of Florida and high asphalt temperatures, would keep her asphalt career short.
“Of course, I had to prove them wrong. As a result, I was asked if I would like a permanent position. During my hiring process, the crew had a few people not show up for work. My foreman asked me if I would like to learn to back roll. Honestly, I was petrified of getting on that roller but I wanted to be helpful. As apprehensive as I was I climbed up on that roller and had my first on-the-job training of how to operate a roller.”
It took the foreman about 30 minutes to teach her the basics. “I was attentive and guarded and rolled at a snail's pace. I remember being told, ‘all you have to do is go back and forth and make sure you cover the whole mat.’ That is when I did what I am known for; I asked my first question why? In my months of flagging, I had watched all three rollers and what they could do. It took a short time to learn how to maneuver all three but I wanted to know why? What is the purpose? Once I was taught what the purpose of the machine was, I started to become more comfortable. However, I also did enough research to know to not get too comfortable and to stay alert at all times. One wrong move and you could either hurt yourself or, worse yet, someone else.”
AsphaltPro: Could you share with the readers what your job as a QC lab tech for Ajax requires? Jewel Eggleston: Taking asphalt samples from the trucks, running the necessary tests to make sure our mix meets the necessary mix design standards, test liquid asphalt contents, compaction of mix, etc.
AsphaltPro: Why did you become a QC tech in the lab and what about that position is most rewarding to you? Jewel Eggleston: I was encouraged by other people in the industry to get my level 1 and level 2 asphalt certifications, which opened the door for me to get into the lab. I find it rewarding to put out a good mix and quality material. It makes me proud to see locations around town where we laid our mix. I am excited when it rides nice and looks great.
AsphaltPro: Could you share with the readers what your job as a roller operator for Ajax requires? Renee Aguis: My current position at Ajax is lead roller operator, also known as the breakdown roller. My job as lead roller assists in achieving density and sealing the mat behind the screed. A lead operator must remember several factors: • They should keep up with the speed of the paver. • The current weather conditions factor into how long the asphalt will take to cool off. • Every operator is taught differently, but I make sure to pinch and seal up any joints and handwork first.
Part of my daily routine is to do what we call a 360 walk around. At first glance, I check the obvious things that are essential to a productive day such as the condition of my cocoa mats. Is the roller clean? I also check my fluids such as oil, hydraulic fluid and diesel fuel, and water. I also check my lights, brakes and scrapers. I also check for the operator standards, which are located in a black box on my roller. Every piece of equipment should have one. The operator standards are reminders and sheets with information on how to properly care for your piece of equipment.
I operate multiple rollers. • Sakai vibratory and oscillating roller • Bomag 5 to 8 roller or known as a steel wheel • Nine wheel or traffic roller
My favorite is the cat nine wheel and the steel wheel is also used as a finish or back roller.
AsphaltPro: Why did you become a roller operator? What about that position is “most cool” to you? Renee Aguis: As I stated earlier I was striking out everywhere trying to find a job so it kind of was an opportunity I ran with. I enjoy the daily challenges of improving my skills. Becoming an operator has given me the confidence that I have lacked in myself for most of my life. The coolest part of my job is the different locations. I am not in the same place every day. I have joked in the past that there are times I have the most beautiful view from my office. It could be along a beach one day and the next by the railroad tracks. Strange opportunities arise unexpectedly like the time we got to meet Steven King.
AsphaltPro: What do you think is the most important skill you’ve brought to your position in the asphalt industry? Jewel Eggleston: You have to be able to work well under pressure, have people skills to handle face-to-face interactions, and the ability to multi-task. Renee Aguis: My special skill is my ability to ask a lot of questions so that I can fully understand the purpose of my job. By knowing what my machine's purpose is and what’s expected of me I can perform my job from the training I acquired by watching other operators and listening to their advice. There is not a lot of time for one-onone training. You more or less learn as you go. So my advice to any woman out there is you can learn any job on an asphalt crew if you ask questions and remain focused.
WE HAVE YOUR HAULING NEEDS COVERED
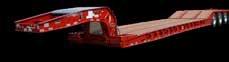
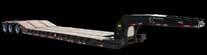

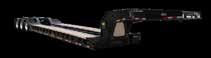
IN STOCK FOR IMMEDIATE DELIVERY!
INTERNATIONAL
Oregon, IL
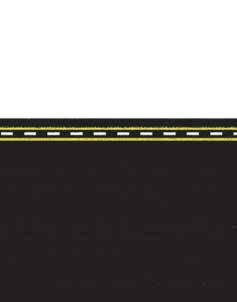
etnyre.com
800.995.2116 815.440.2959
AsphaltPro: Jewel Eggleston commented that the field QC technicians work with the roller operators to set the patterns from the QC tests. Could you elaborate? Renee Aguis: At the beginning of each shift, we have a safety huddle or a beginning of the day/night meeting where we discuss the plan. When it comes to density I mostly confer with my QC and the rest of my rolling team. I usually have a partner who will run tandem with me on the Sakai and then we use sometimes the nine wheel and then my back roll operator. Usually, my QC gives us a pattern and we try it on the first pass; he will check to see if it’s correct. If not, we will tweak it a little bit and sometimes he will ask for my partner or my advice on what we think we should do.
AsphaltPro: What do you think is an incorrect perception that we, as an industry, can re-educate young people about to encourage more women to consider a career in the asphalt business? Jewel Eggleston: It is not just a man’s world; women have proven they can work in the industry, too. There is so much room for advancement in the construction industry. I encourage all women to be a lady when you need to be and be a badass when necessary. Renee Aguis: The stereotype that women do not belong on a construction site but rather in the kitchen or home tending to the children has been around for ages. Not all women are meant to live that life. Just like not all men are meant to do vigorous labor.
Women have a lot to offer in the construction field. They have long attention spans, good focus and are extremely good problem solvers. Rolling requires focus and paying attention as well as knowing how to operate and maneuver the machine. Safety is a big factor.
Women also think differently than men and can probably give another perspective on a job. For any woman, I would encourage them to try something that is out of their comfort zone. It gives you a feeling of accomplishment whether you are perfect at it or not. Working on an asphalt crew has given me confidence that I never thought I could feel. I am close to 50 now and I know that there’s nothing that I won't try at least once.
There are many rewarding aspects of being in the asphalt business. One of those aspects is the proud feeling I get when I drive down the road that I participated in making with my team. Another rewarding aspect is being part of a team. Everyone’s position on our crew is equally important. Without one person doing their job the correct way the road would not come together properly; we all have to work together for the final product.
Finally, probably the most rewarding aspect of being in the asphalt business is hearing and seeing how proud my son is of me, to hear him tell his friends, “my mommy built that road, she runs a roller.” I hope that I am teaching my son that no matter who you are whether you’re male or female, black or white, you can do and accomplish anything you put your mind to.
MENTORS
Jewel Eggleston listed Plant Manager Rickey Stevens as a mentor from her asphalt career. “I liked the fact that he wanted to see the daily reports and had an interest in the quality of the mix that was going out. The quality of our mix represented all of us at Ajax Paving Industries of Florida and we want to provide our best mix possible to our customers and our paving crews.” Renee Aguis listed Luke Van Tassel, a tack truck driver from the first crew she worked with, as a mentor from her asphalt career. While Van Tassel didn’t immediately warm up to the idea of having a woman on a construction site, sharing with Aguis that he wouldn’t want his wife or daughters working in field conditions, he came to recognize she was good at her job. “He was one of the men that took the time out to explain to me in detail in words that I could understand exactly what it was that my nine wheel did. He has since moved away and has a new job but we do keep in touch; he was one of the first people that I called when I was promoted to lead operator.”
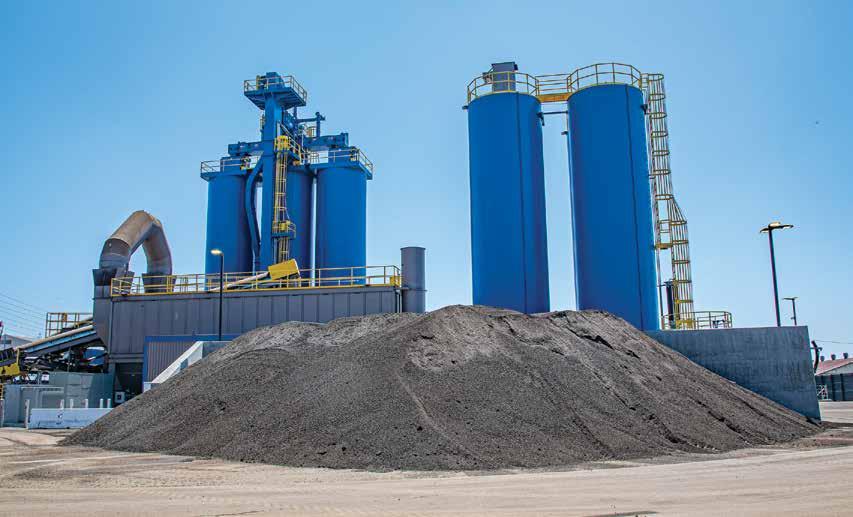
While the site doesn’t have room for multiple large virgin aggregate piles, it has to accommodate a RAP pile. In the background, you can see the 76,000-CFM pulse-jet baghouse, three 300-ton storage silos from Astec and at least two of the three 35,000-gallon AC tanks from CEI Enterprises, an Astec company. All photos courtesy of City of L.A. BSS
Asphalt Equals Climate Stewardship
Here’s how the City of Los Angeles inserted dust and mist collection to garner an Envision® award for 2021
BBack in March, the Institute for Sustainable Infrastructure (ISI) announced that the L.A. Asphalt Plant No. 1 (AP1) replacement and modernization in an industrial district of Los
Angeles, California, had received its Envision®
Bronze award for sustainable infrastructure.
While this is a laudable project on its own merits, AsphaltPro would like to share with the industry a few tips from the project to assist in other producers’ journeys toward net zero emissions and positive climate stewardship.
ISI stated in its March 10 press release: “To earn Envision Bronze, a project must demonstrate that it delivers a range of environmental, social, and economic benefits to the host and affected communities.”
Let’s look at how a plant from 1947, operated by the city of Los Angeles Bureau of Street Services (BSS), could produce between 100,000 and 200,000 tons of hot-mix asphalt (HMA) per year in an environmentally friendly manner. Specifically, how could a plant of that age introduce between 7.5 and 20% recycled asphalt pavement (RAP) without causing emissions troubles? The answer involves new technology, careful planning, and dust and emissions collection for re-use.
BY SANDY LENDER
MAP THE PLAN
For starters, the city worked closely with Partner Engineering & Science and brought in a full-service general contractor—Papich Construction Inc.—to demolish the old plant, remove old soil and detritus, bring in clean fill dirt, and build a new plant, alongside vendors such as Astec Industries of Chattanooga and Butler Justice Inc., of Long Beach, California. To get the new plant to fit on a roughly 2-acre site in an industrial area, the team had to create a detailed layout.
Eddie Van Zyl, sales director west integrated process solutions for Astec, told us the layout went through upwards of 20-plus revisions to ensure smooth traffic flow on the site for worker safety. “The biggest challenge on this project was to get all the equipment to function on a small site without being disrupted by truck traffic,” he explained. “We had to get all the pieces to work harmoniously with aggregate, RAP, and liquid asphalt deliveries taking place and not interfering with the hot-mix asphalt and Tac Oil pickup. Besides the asphalt plant, the site also houses Street Services personnel in the new administration building.”
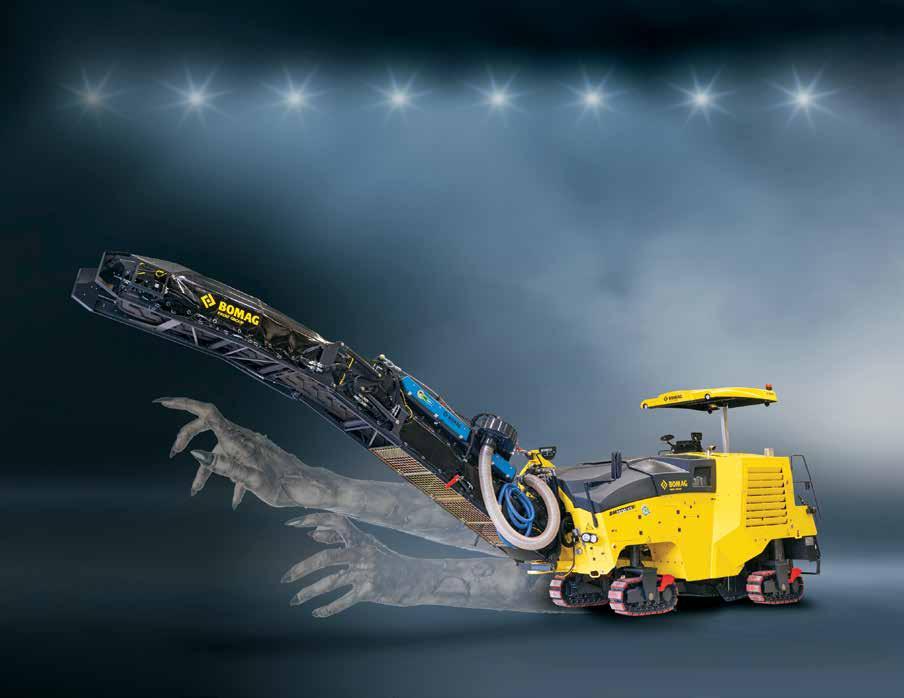
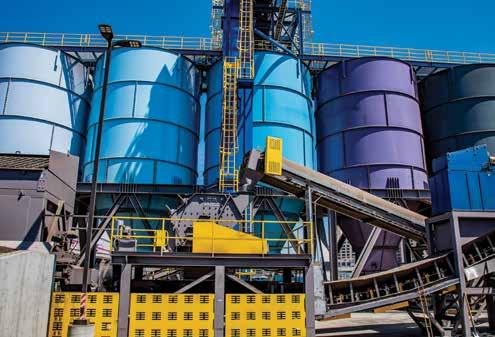

TOP: On the far right of this picture, the blue box is one of the two insertable baghouses described in this article. Mike Butler explained these small dust collectors are gaining popularity with established plants where owners want additional dust control and want RAP dust to remain in the circuit. The RAP screen is completely covered so that any dust created is mitigated. BOTTOM: The truck loading zone is completely enclosed and outfitted with u-shaped collectors at each silo gate to capture emissions as mix is discharged. You can also see here the auxiliary intake at this end, designed to prevent emissions from escaping when trucks exit the scale. To the side, notice the conveyors and transfer points are all covered carrying material to the 40-foot Double Barrel drum with V-Stack temperature control.
The truck traffic continues night and day, he said. “And that’s the challenge. They’ve got to be very well coordinated.”
The ISI release stated the “new AP1 will continuously produce asphalt at a rate of up to 400 tons per hour, up to 600k tons per year, and utilize up to 50% recycled asphalt product.”
“The plant can meet their capabilities,” Van Zyl said. “The logistics will be the bottleneck.” Logistics will require over a hundred trucks per day to deliver aggregate to the 600-ton silos. That’s right: a 2-acre site won’t accommodate multiple large stockpiles of virgin aggregate, so Astec supplied five aggregate silos over the cold feed bins, totaling 3,000 tons of capacity.
“The silos are 26-feet in diameter,” Van Zyl said. “With the truck dump hopper and conveyors, they cover about 200 feet. The aggregate is unloaded into a 30-ton truck dump hopper. Minimal dust is created as the hopper sits well below grade. The conveyors are all covered with aluminum dust covers and all aggregate transition points have water mist dampeners. The RAP screen is completely covered so that any dust created is mitigated.”
COLLECT DUST
Dust mitigation is one of the key factors that garnered the city’s Envision award. Under the category of air quality, the ISI stated: “As a project located in the South Coast Air Quality Management district, the project was required to meet stringent requirements to reduce particulate matter and other air pollutants. The new plant will be more efficient and provide significant improvements to air quality compacted to the previous plant that was designed in 1947.”
As Van Zyl mentioned, all conveyors and transfer points are covered. Astec supplied a 76,000-CFM pulse-jet baghouse for the project. Butler-Justice Inc. installed two insertable dust collectors along the RAP system to act as mini-baghouses at the Telsmith 4230 horizontal shaft impactor (HSI) and at the two 10-foot by 14-foot RAP bins.
“By utilizing material that would typically be sent to the landfill, this project is turning trash into a valuable material that is important for maintaining the city’s streets,” said Melissa Peneycad, ISI’s managing director. The award committee also noted that by using reclaimed aggregates from local resurfacing projects in the production of HMA, the city will avoid uncertainty in future mining and transportation costs.
To ensure the use of RAP is as environmentally friendly as possible, the project captures and re-uses its dust.
“By its very nature, the HSI will displace air, which causes dust to billow out,” Mike Butler of Butler-Justice said. “We collect the unruly dust created by the impactor and screen. The collector acts just like a vacuum cleaner; the 30 bags inside are like pillowcases. There are always 20 bags that are sucking particulate in. Every 10 seconds, a pulse goes off for a set of 10 of the bags. This is a constant rotation.
“We’re containing the unruly dust in the bag section. Then when the bag releases its
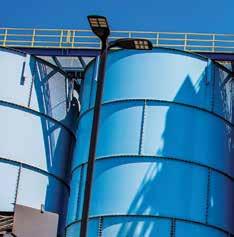
Notice the LED lighting for the plant has covers to focus and direct it.
dust cake onto the belt, the dust goes back into use.”
For the RAP material discussed here, special bags are required. “RAP wants to stick to bags,” Butler said. “But these bags balloon out when pulsed. The pores of the bag release the sticky dust.”
He explained that these small dust collectors—insertable baghouses—are gaining popularity with established plants where owners want additional dust control and want RAP dust to remain in the circuit. “In that 2-acre site, there’s not a lot of room for another stand-alone baghouse, plus conveyors and all the accoutrements that go with it.” He pointed out that capturing and storing RAP dust particulate could present additional environmental hoops for owners to jump through. Returning the dust to the system for immediate use makes sense. “We circumvent a problem we’d end up creating if we captured and stored the material,” Butler said. “Our whole job is to solve problems.”
COLLECT MIST
A potential problem Astec proactively solved is that of fugitive emissions at loadout. The company supplied three 300-ton storage silos and beneath them is an enclosed loading zone and a blue smoke control system with a kick. Van Zyl described it:
“The 18,000-CFM blue smoke control system includes a Fiberbed mist collector. The system prevents odorous fugitive emissions from the mix storage silos during filling and load-out operations. The truck loading zone is completely enclosed. The enclosure is outfitted with u-shaped collectors at each silo gate to capture emissions as mix is discharged. The enclosure is also outfitted with auxiliary intakes at each end to prevent emissions from escaping when trucks exit the scale.”
COLLECT AN AWARD
When it’s all said and done, the AP1 in downtown Los Angeles is now designed to showcase how sustainable the asphalt industry can be. Right down to reducing light pollution.
“Lighting needs were designed based on local guidelines that encourages strategies that minimize light glare and trespass,” the ISI press release reported. “In addition to incorporating LEDs, lighting controls adjust to the project’s needs based on availability of daylight.”
With the latest technology in place, the plant “is expected to exceed regulatory requirements, permit requirements, and industry guidelines for energy efficiency and emissions control, and meet the current BACT condition set forth by the SCAQMD (Air Board).”
Whether you wish to meet new air quality standards in your county or wish to apply for your own green ratings certification for your operations, the steps BSS took for its site are a primer for getting started.
RIGHTValve Valve RIGHT RIGHTPrice Now!Price Now!
Dependable, E conomical, Available …
Since 1892, Homestead continues to be the most reliable manufacturer of asphalt valves. With cast iron and ductile iron material options, we offer a complete source of valves for any liquid asphalt application. Our full line of hot-jacketed 2-way shutoff & 3-way diverter valves provide a ready solution to meet your flow requirements. Homestead’s cutting-edge actuation design allows you to easily add actuators to your existing Homestead valves, in-line, without modification. Our fully stocked warehouse of valves and actuators offers you security in knowing that the valve you need is only a phone call away.
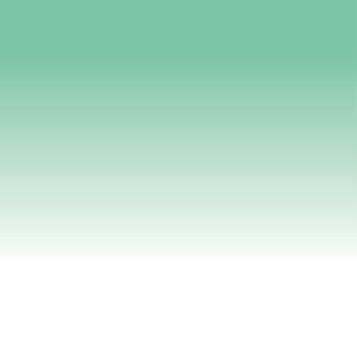
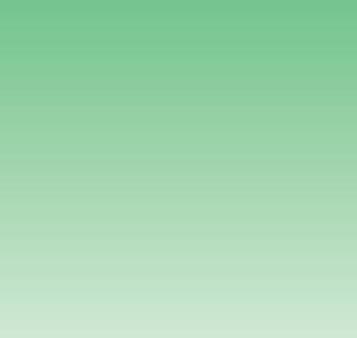
THE ASPHALT VALVE EXPERTS
Valve Types
■ Full Port – Standard Port ■ 2-Way Shutoff and 3-Way Diverter Patterns ■ 1"-8" Flanged and 1/2"- 4" Threaded ■ Steam/Hot Oil Jacketed ■ Transfl o Plug ■ Proportioning Plug
Valve Materials
■ Cast Iron – to 450° F ■ Ductile Iron – to 550° F ■ High Temperature Seals
Actuator Types
■ Pneumatic ■ Electric ■ Open-Close ■ Modulating
® 610-770-1100
asphaltvalves.com
Fax: 610-770-1108 sales@homesteadvalve.com
©2021 Olson Technologies, Inc.