
57 minute read
Corporate Profiles Showcase Offers a Look Inside
CORPORATE PROFILES SHOWCASE CORPORATE PROFILES SHOWCASE OFFERS A LOOK INSIDE OFFERS A LOOK INSIDE
BY ASPHALTPRO STAFF
Editor’s Note: The staff of AsphaltPro magazine is not responsible for the opinions expressed in the Corporate Profiles supplement. Statements made have not been verified, thus producers/contractors are still encouraged to use best practices when implementing new advice or making purchasing decisions.
The staff at AsphaltPro magazine sought a way to give original equipment manufacturers (OEMs) a chance to speak directly to asphalt professionals. We wanted to give the partners in our mission the chance to show you who they are and what they bring to the market to enhance your bottom line.
We posed a set of questions to those partners who support us, thus your operations, and left their answers raw and real. This special section to the July edition is our inaugural Corporate Profiles supplement and it represents an inside look at the OEMs who want to help you make the most of your business.
Companies like Hotmix Parts & Service®—co-located with Stansteel on page 46—shared basics that make sense for owners to consider: “From our favorable location, only minutes from United Parcel Service’s worldwide air hub, we can often ship items as late as 7 p.m. for delivery to your hot-mix asphalt plant facilities the next morning.”
But this supplement offers more than business basics. Herein, you’ll see company strategies among the mission statements shared with you.
The asphalt industry has its share of mergers and acquisitions among companies, such as those taking place under the Colas USA, CRH Cos. or Martin Marietta Materials Inc. umbrellas. Manufacturers supplying the equipment and services to enable operations have similar changes taking place.
For example, Command Alkon of Birmingham, Alabama, took Libra Systems Inc. and Ruckit Inc. into its family in November and December 2020 respectively. With this supplement to AsphaltPro magazine, Astec Industries Inc. spells out its mission with all its former subsidiaries folding into OneASTEC. Perhaps one of the more surprising acquisitions in Q4 2020 was that of Volvo CE divesting its North American Blaw-Knox paver business and associated assets to Gencor Industries, an asphalt plant equipment manufacturer.
Gencor’s spokesperson provided, “We offer highway-class pavers coupled with the most extensive line of screeds to the industry; all backed by a worldclass international service network.” Those pavers include performance features such as Blaw-Kontrol and the Blaw-Knox Ultimat screed platform, which is a double-width screed that doesn’t require bolt-on extensions.
Among the mergers and divestitures are workforce development initiatives. Hotmix Parts & Service spoke of its training, saying, “For a number of years, we have offered our Hotmix University courses to familiarize newer plant and management personnel with some of the intricacies of the hot-mix asphalt industry.” The team at Wirtgen devoted a great deal of its corporate profile explaining the nuances of its Center for Training and Technology (CTT), which has seen updates and expansions in the past few years.
You’ll see one of the areas in which we invited OEMs to share philosophies was that of environmental stewardship. OEMs are invested in helping conTOP: Gencor offers the proprietary “Blaw-Kote” on its Blaw-Knox pavers, which is an environmentally friendly pre-treat system designed to aide in asphalt cleanup. BOTTOM: Reliable Asphalt Products, on page 44, is the distributor for Vulcan burners.
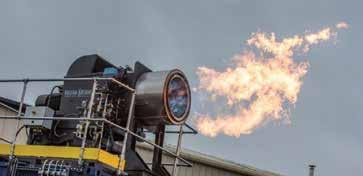
tractors and producers reach their net zero goals. It’s natural to think of the strides made toward zero emissions at the asphalt plant, but manufacturers are looking out for your best practices at the paving site as well.
Companies like TransTech Systems out of New York, while not eligible to participate in the supplement, still offer environmental “credit” to contractors. “Most people don’t realize that TransTech’s PQI 380 assists our customers in being good stewards of the environment,” the company shared. “Not only does the PQI 380 not emit any harmful nuclear radiation, but the primary benefits derive from its ability to help our customers build longer life roads with smoother surfaces, thereby enhancing fuel efficiency of all vehicles and reducing energy consumption.”
Also in the field, “Blaw-Knox is always looking for ways to improve performance while reducing the environmental effects normally associated with operating heavy machinery,” the company shared. They listed the example of their power-adaptive engine for reducing ambient noise pollution and improving fuel efficiency by lowering engine rpm.
These innovations and optimizations join the arsenal of product and service options available to our industry. AsphaltPro invites you to thumb through the profiles included herein for a look inside the companies bringing those options to you.
Founded: 1967 Our Mission: ADM began as Panco Corporation, a manufacturer of control panels, founded in 1967 by Wayne Boyd. By the 1970s, Panco evolved into a manufacturer of asphalt plants. In 1983, Panco became ADM, manufacturing asphalt plants exclusively, with the mission of providing the industry’s most extensive sales and service support anywhere.
ANTICIPATING OUR CUSTOMERS’ NEEDS
ADM’s personnel are extremely dedicated to anticipating customers’ needs to provide viable asphalt plant solutions and ongoing problem solving to ensure long-term customer success. As a family owned business that refuses to operate under layers of management and other personnel infrastructure, the company is highly positioned to provide uncompromising sales and service support.
ADM’s highly knowledgeable personnel devote as much time as it takes to listen and consult with customers and prospective customers in two-way collaborations to determine specifically what customers’ production goals are, specific plant-site concerns and needs, what the local environmental standards are, to which the producer must comply, and more to determine just the right plants for customers’ needs.
Engineers and sales personnel are dedicated to understanding customers’ businesses as whole operations. Within the framework of the four series of asphalt plants ADM manufactures, they custom design a plant from the most relevant series, outfitting it with just the right components to fulfill a producer’s specific needs.
Continuing with service well after the sale, ADM personnel assist with plant set-up to get the plant running and to keep it running throughout its life. For set-up, ADM service personnel help arrange and problem-solve plant transportation, determine the best on-site placement, offer technical set-up tips, as well as travel to the site. After set-up, this same service team helps producers troubleshoot as issues may arise, advise on maintenance, repairs, and quick-fix steps and procedures by phone and on-site.
When it comes to parts support, ADM maintains a large inventory of in-stock parts to allow quick and efficient delivery and avoid costly shutdowns.
Anticipating customers’ needs and providing the sales and service support to get customers just the right equipment and to keep it operating, is vital to the success of customers’ operations.

SUSTAINABILITY WITH ASPHALT
ADM prides itself on its commitment to asphalt sustainability, from reduce to reuse to recycle. The company’s commitment to sustainability greatly benefits the producers ADM serves.
Every plant ADM manufactures is designed to allow producers the use of RAP in their hot mix. Depending on the plant series purchased, producers may use up to 50% RAP. Recycled material in the mix significantly impacts producers’ bottom lines for higher returns on investment (ROI).
ADM asphalt plants fitted with baghouses go even further to improve ROI, since the baghouse allows fines to be reintroduced into the hot mix. In that way, baghouses also save producers in material costs along with reducing material itself.
ADM plants eliminate blue smoke and hydrocarbon emissions, allowing producers to meet strict environmental regulations, while ADM Warm-Mix Systems allow for the production of mix at reduced temperatures, thus allowing for a reduction in power and fuel.
Further demonstrating ADM’s reduce and reuse policies, the company’s engineers carefully spec the steel used in the manufacture of its asphalt plants and design the plants to use most of the steel purchased, with very little scrap, and highly reduced waste. What little scrap is left, is collected and stored on ADM’s lot until sufficient quantities are available to send out for recycling.
ADM also manufactures its plants and components using recycled steel that has been melted down for reuse in new-product manufacturing. The strength and durability of the steel used in ADM hot-mix asphalt plants is of such high quality, that with proper and ongoing plant maintenance, producers may rest assured of significant and long-lasting plant life.
MIXING IN A WINNING BID
With asphalt plants that can take up to 50% RAP and output up to 425 tph, depending on the particular plant, ADM enables producers increased capacities and maximum production to help them get the winning bid.
Winning bids are accomplished for producers in a variety of ways, starting with their ability to supply asphalt on a timely and consistent basis at pricing the market can afford. The greater a producer’s ability to keep operating costs low, the better their businesses are positioned to offer competitive asphalt pricing to the marketplace.
ADM helps producers keep their pricing competitive from the moment a producer purchases an ADM plant. That’s because ADM plants are more competitively priced than other brands on the market. Lower equipment prices help producers realize much faster returns on investment, which in turn, helps them more competitively price their own hot-mix asphalt product. By design, ADM operates under a lean business model, in order to offer producers more competitively priced equipment, and ultimately win bids.
ADM asphalt plants and components also help producers keep operating costs lower, and ROI higher, by providing equipment that is designed (or can be fitted) to use more RAP, reintroduce fines into the mix (saving on material costs), and use less fuel through warmmix production. All of this adds up to winning bids for the producers that ADM serves.
admasphaltplants.com 260-637-5729
Founded: 1952 Our Mission: We manufacture the most durably built and detailoriented line of asphalt plants and asphalt equipment on the market. Everything we make is designed from our customers’ perspective, fully customized for each operation and built to last.
ANTICIPATING OUR CUSTOMERS’ NEEDS
Our two most important products are the foundation on which our company is built: our drum mix asphalt plants and batch mix asphalt plants. ALmix manufactures a complete line of both styles of plants as well as a full line of auxiliary equipment and world-class control systems for each plant type. ALmix drum mix plants and batch mix plants are available in both relocatable and portable setups, and in a range of sizes designed to fit the production needs of any contractor.
Over the past several decades, we have continuously worked to make our plants stronger, safer, more efficient and more profitable for their owners. We understand that these plants are vital investments for our customer’s business—an investment that can be a game-changer for their future. That’s why we build these plants to fit their exact requirements, load them with the features that we’ve developed through the years from the perspective of our customers, and continue to stand by their side for ongoing service and support. Building the best asphalt plants and asphalt plant equipment is more than just a business to us—it’s in our DNA. That’s why we take the time to listen, to understand and to consult our customers through each plant purchase, ensuring that they get exactly what they need, every time.

SUSTAINABILITY WITH ASPHALT
At ALmix, we manufacture a variety of products designed to assist in our customer’s efforts to protect the environment, and to go above and beyond regulations as part of a good neighbor policy. We understand that what’s good for the sustainability of our resources and our environment is also good for business. These sustainability-focused products include our award-winning RAP equipment, blue smoke capture systems, reverse air baghouses, warm mix systems and more. We constantly strive to maximize efficiencies across every piece of equipment at the plant, leading to savings in power, fuel and plant emissions. At ALmix, we are focused on building plants that are better for our both our customers’ bottom line as well as the environments in which they operate.
MIXING IN A WINNING BID
Helping customers of all sizes find success is simple when you’ve been around for nearly 70 years. Being in the industry as long as we have, we’ve learned how to consult each of our customers individually through the strategic process plant ownership. Whether we are dealing with a first-time buyer or a seasoned, multiple-plant owner, we understand the unique challenges of their situation because chances are, we’ve been there before. Our knowledge of local regulations and ability to customize our equipment to fit any contractor’s needs results in our customers maximizing the value of their dollar. Our service after the sale and remote program support help to ensure that each plant is running in top shape so that our customers can focus on producing more tons.
Through the years we’ve learned that in order for our business to succeed, each and every plant we sell must be a successful investment for the owner. That’s why when you do business with ALmix, the relationship starts with careful listening and carries far beyond the sale of equipment. We see each customer as a lifelong partner in business.
almix.com 260-672-3004
Founded: 1869 Our Mission: Our company’s motto is “Productivity Partnership for a Lifetime.” Ammann works tirelessly to stay connected to customers as their needs (and businesses) evolve. Our broad range of roadbuilding products and services helps make this possible.
INDUSTRY-CHANGING INNOVATION
Ammann’s highly advanced approach to recycling was introduced to North America a few years ago.
Ammann’s recycling technology and processes are utilised in both BATCH and CONTINUOUS mixing plants. Ammann’s system enables production of high-quality mixes with recycling rates of 60%. This provides momentum for producers in several ways.
First, final mix quality is enhanced. This is because Ammann technology differs from conventional production methods. Virgin aggregates and RAP are heated separately. This enables temperature control that prevents overheating of the binder content in RAP. Dedicated mixers provide a homogenous combination of RAP, aggregates, binder and additives.
Second, virgin aggregates ARE NOT superheated when Ammann recycling processes are employed. That means dryers, mixers and other plant equipment is not exposed to excessive temperatures or complications caused by steam expansion.
Additionally, plants using Ammann’s system have high degrees of production flexibility because they are not limited to producing only high RAP mixes.
Ammann plants can produce 100% virgin mix, as well as incremental inclusion of RAP from 10% all the way up to 60%—and beyond, if so desired.
In the end, the plants provide momentum for producers to provide highly sustainable mixes without jeopardizing mix quality or adding process complexities to overcome conventional production methods.
Obviously, Ammann is deeply committed to recycling. That includes development of a High Recycling Technology (HRT) plant. The appearance of the Ammann ABP HRT Asphalt-Mixing Plant is unique. Its entire recycling system is arranged vertically, in direct line above the mixer. This allows materials to be dropped instead of conveyed, which minimizes wear and optimises transport of the hot RAP.
The HRT approach also means that there is enough room in the plant’s tower for additive feed components and for carrying out inspection and maintenance work.
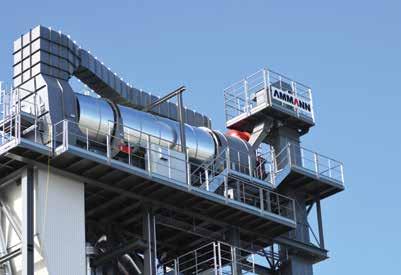
SUSTAINABILITY WITH ASPHALT
Sustainable and resilient pavements are a two-fold approach to environmental stewardship—and they go hand in hand. For example, with High Recycling Technology (HRT), producers are able to develop mixes with exceptional quality that include high RAP contents.
Much of the resistance to high RAP mixes can be easily overcome with HRT technology. It’s not a matter of magic, though. A proper understanding of how high RAP mixes are produced will dispel much of the doubt.
It comes back to the process of how the mix is made, how the ingredients are handled – and the superior, more sustainable and resilient pavement that results. Heating, mixing and controlling the plant go a long way in making sustainable mixes. The science behind how to make a sustainable mix really shines with HRT.
The HRT process makes sense when properly evaluated and analyzed. Still, it can take a little time to fully grasp and EMBRACE it.
MIXING IN A WINNING BID
As some pockets of the industry moved away from batch processing, Ammann invested in it, enhanced it and remained vigilant of who wants certain mixes and why.
At Ammann, we bill our proprietary as1 Control System as the brains of the plant. The system is plenty smart—which makes an enormous impact on our customers’ businesses.
A modern control system can have a significant effect on efficiency, and that cuts across many parts of the process. Improved efficiency will lessen fuel usage, emissions and material waste. And the as1 is the best in the business at doing exactly that.
The proprietary system provides statistical data that can help you uncover trends and identify areas of strength, areas where improvement is needed, and everything in between. Built-in statistical reports are presented in an easy-to-understand format. Data can be accessed through the internet.
And let’s not forget about production. There is a great deal of value provided when the system is running the plant. It provides fully automated mix production, plus the flexibility to work in safe manual mode.
The system offers a host of other benefits including the use of unlimited recipes, automatic burner control, dynamic in-flight correction abilities and full integration of electrically heated bitumen storage tanks.
A series of modules, which offers a specific area of focus, are available as well. These modules can help deliver even more value.
The as1 makes it easy for operators of all experience levels to succeed— and for production and quality goals to be met, too.
ammann.com/us-en/mix-masters 717-594-8437
Founded: 1972 Our Mission: Our Purpose is Built to Connect with a supporting Vision to connect people, processes and products, advancing innovative solutions from rock to road as OneASTEC. Astec was founded on innovation and a passion to help customers succeed. Innovation is in our DNA.
INDUSTRY-CHANGING INNOVATION
A few examples of products and improvements recently brought to market: Expanded Double Barrel Lineup: The Double Barrel drum dryer/mixer delivers guaranteed productivity and top-quality mixes while keeping operating costs per ton of mix low and meeting the most stringent environmental codes. The Double Barrel drum dryer/mixer revolutionized the market with its ability to handle RAP effectively and efficiently with a unique drum-within-a-drum style and an exclusive sequential mixing process.
Today’s Double Barrel drums still rely on sequential mixing to deliver high quality mix while continuing to advance mixing technology with the addition of patented V-Flights and the expansion of the Double Barrel product line with the Double Barrel X and the Double Barrel XHR, which can handle high RAP mixes of up to 70%. SB-3000 SHUTTLE BUGGY® MTV: Powerful and practical, the SB-3000 is a familiar yet entirely re-invented Shuttle Buggy. This Material Transfer Vehicle stores and transfers hot-mixed asphalt material from truck to paver for non-stop paving, while enhancing safety, comfort, and productivity.
The anti-segregation auger remixes material just before delivery to the paver and the 35-ton storage capacity allows trucks to unload HMA immediately. Engine, fluid checks, and other important daily maintenance items are at ground level for safe and easy maintenance access. Bright, LED lights illuminate the wheels, egress ladder, and operator platforms. The main operator is closer to the action while maintaining excellent site lines, and the ground operator is protected inside the structure of the machine. FT4250CC Mobile Impactor Plant: Astec announced the launch of its hybrid-powered FT4250CC mobile impactor plant, with an added pre-screen, at CONEXPO-CON/AGG 2020. The new, two-deck pre-screen minimizes the amount of undersized material that passes through the chamber, reducing wear costs and increasing the amount of final product by up to 30%. The hybrid power option allows producers to operate using either line power or diesel fuel.
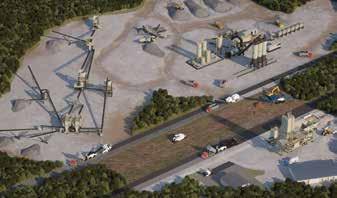
SAFETY IN THE INDUSTRY
Safety is the first of our core values (Safety, Integrity, Respect, Innovation and Devotion) embedded within our OneASTEC business model. We believe it is important to nurture a culture of safety with an unyielding desire to “Strive for Zero Harm.” It starts with our employees who are empowered to hold management and each other accountable with our Speak Up Listen Up program. We encourage our employees to point out concerns and make suggestions for improvement.
Safety data is tracked in real-time through a safety management software. The data translates into our safety KPIs which are discussed at all levels of the business from pre-shift huddles on the shop floor to our weekly executive meetings. Our safety managers also use the data to identify issues, develop solutions and share best practices which are also communicated to employees via a safety newsletter.
In addition, the company invests in personal protective equipment and regular training for our employees. New hires must first attend approximately 12 hours of training and pass proficiency tests before going to work. They also wear a red hat during the probationary period so that extra attention can be given to them as they learn on the job.
Our efforts are paying off with Liberty Mutual recently recognizing us with 6 silver and 2 gold safety awards for exceeding BLS industry rates. While we are proud, we know we can always do better. We regularly participate in third-party audits and seek out new ideas to improve our safety practices.
Lastly, we believe that our core value of safety extends to our families and the end-user of our products—this is our value chain of safety and our endless pursuit to Zero Harm.
MIXING IN A WINNING BID
With our many innovative products, proven by a century of work, Astec has a long history serving customers within the rock to road community and has made significant long-standing connections. Our commitment to helping our customer drove the decision to unify as one company.
Our organization’s former brands, including Astec Inc., Carlson, Heatec, KPI-JCI and Astec Mobile Screens, Peterson, and Roadtec, took on the Astec name and no longer operate as separate subsidiary companies. The unification makes it simpler to do business with Astec and allows us to better focus on customer success. Following the unification, we look forward to growing as a partner to the customers we serve in the asphalt mixing and road building sectors.
“We made the decision to unify to make it easier for our dealers and customers to do business with us. By coming together as one organization, we can offer greater customer service and drive innovation,” said Barry Ruffalo, president and CEO of Astec Industries Inc. “The rebrand enables us to build our strength together under one common name and purpose. We can better leverage our growth as one Astec team rather than individual brands.”
In addition, Astec has invested in a reinvigorated new product development process. From the beginning, Astec has emphasized innovation as a means to serve our customers. As we move forward as one unified company, we are accelerating our innovation journey with a focus on connectivity. As has always been the case, continuous input from our customers is included during all points in the innovation process.
astecindustries.com
Founded: 1957 Our Mission: Bopparder Maschinenbau-Gesellschaft, shortened to BOMAG, was founded in 1957 by Karl Heinz Schwamborn in Boppard, Germany, based on a new design model of a double vibratory roller. BOMAG Americas, owned by The Fayat Group, offers full range of products in Asphalt & Milling, soil/asphalt/ landfill Compaction, Recycling & Stabilization, & Landfill Management Equipment.

ANTICIPATING OUR CUSTOMERS’ NEEDS
We are the Global Leader in Road Construction solutions & recognized for the best application knowledge, technology, and service.
That is simply the BOMAG Americas motto. BOMAG Americas is not a full line construction OEM, but a specialized global leader in the road construction industry with laser precision. Our products do not serve dual purposes but are specifically designed and engineered for road building. Our engineers are wholly focused on machines designed for road building application with infrastructure crew inputs throughout product development. Our team members think, live, and breathe the road lifecycle. There are only road building products in our portfolio and that is our core and only business.
BOMAG Americas’ single-mindedness on road building and construction allows for concentrated emphasis on innovations in technology improvements. Our engineers and product development teams are the leaders in intelligent compaction, asphalt technology, hybrid & alternative fuel solutions across the globe with hundreds of patents.
SUSTAINABILITY WITH ASPHALT
BOMAP Connect is the leading solution for cloud-based, real-time intelligent compaction data. The app displays compaction progress on the operator’s own smartphone or tablet, reducing passes by up to 30% and cutting costs and CO2 emissions. In addition, BOMAP Connect is a cloud-based solution that offers networked control and documentation of all machines involved in compaction on the construction site. As well as several design advantages, the latest generation of BOMAG compactors is particularly impressive thanks to its higher efficiency, low operation costs, and even better driving comfort. The new hydrostatic travel system automatically ensures high efficiency, while ECOMODE and ECOSTOP reduce fuel consumption and wear.
The fully autonomous ROBOMAG tandem roller, developed by BOMAG in cooperation with the Technical University of Kaiserslautern as a technology study. In addition to other innovations, such as the BF 200 commercial paver and a digital maintenance concept called “Remote Service Assistant,” BOMAG was focusing primarily on alternative drive concepts. The BW 174 AP hybrid tandem roller combines a diesel engine, hydraulic accumulator and a compaction system into one highly efficient system solution that saves up to 20% fuel.
bomag.com/ww-en/machinery/categories/
Incorporated: 10/14/1982 Our Mission: To offer affordable asphalt plant controls that are dependable, logical and easy to learn as well as providing exceptional accuracy and the capability to meet the most stringent contract requirements.
ANTICIPATING OUR CUSTOMERS’ NEEDS
Reliability that instills the confidence to motivate more competitive bids and consequent contract awards.
Technical support and knowledge that goes beyond just our systems.
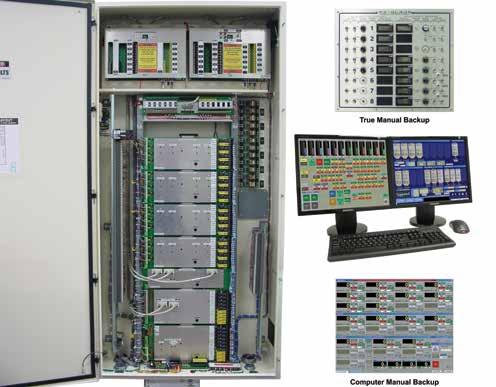
SAFETY IN THE INDUSTRY
Inherent in our designs are protection features such as dedicated built-in hardware “dead man timers” that detect computer failure and shut down the plant/process immediately as alternative for the disabled computer safety features.
MIXING IN A WINNING BID
By providing reliable asphalt plant controls with consistent operational real-time availability and unmatched accuracy by way of precise inject timing of all process materials during startup as well as during sequential on the fly mix changes.
bslight.com 918-342-1181
Founded: 1968 Our mission: We go the extra mile to provide exceptional asphalt equipment solutions and service.
ANTICIPATING OUR CUSTOMERS’ NEEDS
In the asphalt industry, the two most important products that CWMF provides to their customers are the Drum and Baghouse as a package. The entire plant as a whole, is important, but these two components are where production is made. Getting these components to run in harmony at optimal levels will yield high-end production rates at the lowest cost per ton achievable. With an efficient flighting design in the dryer, coupled with a VFD, the end-user is now capable of having complete control of their baghouse and mix temperatures.
In addition to equipment, service is the key to a successful result between the customer and OEM. CWMF strives to ensure we meet these expectations. We do this through good communication and follow-through. If you are clear about what you will be providing and follow through with it, the result should be nothing but positive.
Service and reliable, efficient equipment are vital to our customer’s success. The hot mix plant is just one entity of the road-building process. Unreliable equipment and delinquent service have no place in a successful outcome.
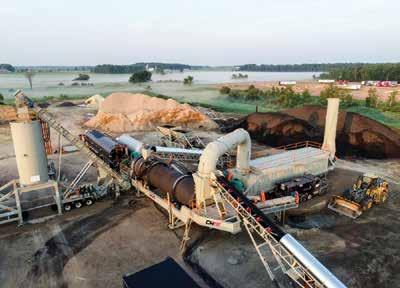
SUSTAINABILITY WITH ASPHALT
It is not a secret that asphalt is a recycled product. However, most people do not realize that asphalt is the number-one most recycled material in the world! This industry has also been very innovative in utilizing other foreign products into mix designs. These products may include seashells, crushed glass, roofing shingles, ground tire rubber, plastics, steel slag, and many others. Today, with the help of rejuvenators and additives, contractors can increase the amount of RAP that they use in a mix. CWMF has worked closely with its customer base to engineer its rotary drum, so it can be capable of handling higher amounts of RAP input. CWMF is proud to be working in an industry that is at the top of the list of recyclable products.
MIXING IN A WINNING BID
CWMF plays its part in the winning bid by continuing to educate our customers. Teaching our customers about where efficiencies are gained or lost is imperative in production. Often a simple spreadsheet to show potential financial gains/losses can be very effective in getting an operation to change a previous way of doing things or to adjust to a more efficient way of doing things. Also, we encourage all of our customers to follow a regular maintenance policy. Regardless of whose equipment our customers own, it needs to be maintained. Eliminating or reducing downtime will have a positive impact on the bottom line.
cwmfcorp.com 320-267-3805
Founded: 1968 Our Mission: Gencor Industries Inc. was formed by the merger of Mechtron Corporation with General Combustion Inc. and Genco Manufacturing Inc. in 1968: • To be the unquestionable technological and market share leader in the industries we serve. • To exceed customer expectations in all aspects. • To be a good neighbor and a positive influence in the lives of people in the community in which we live and work.

INDUSTRY-CHANGING INNOVATION
The new Gencor G-Series is the latest innovation in small portable hot mix plants providing contractors with all the features of Gencor’s award winning Ultraplant® in a smaller compact highly mobile plant that can be erected and operational virtually anywhere. Available in 150 and 200 U.S. tons per hour of hot mix asphalt.
Built around the unique patented counterflow Ultradrum® technology, proven in 100’s of applications around the globe for producing high quality hot mix without degradation, cleanly, and efficiently. The Ultradrum® flight design concept provides for the highest efficiency heat exchange between the aggregates and the combustion system making it the most efficient drum mixer in the industry. Each flight section is designed for maximum wear life, low maintenance and results in even drum loading.
The isolated mixing section is located behind the burner so there is no chance of liquid asphalt coming in contact with the burner flame. This means there is no oxidation of the asphalt, no degradation of the mix, and no asphalt vapors entering the exhaust gas stream.
The Astraflame burner achieves complete, efficient combustion without the use of refractory heads or combustion chambers. As a result, more of the BTU heating value of the available fuel applied directly to the drying process without unnecessary heat loss making it one of the most efficient burner applied to rotary aggregate dryers.
A standard 4-bin cold feed system, with variable speed independent feeders (VDF) and collector, provide accurate flow of aggregates to meet any mix specification. Features such as standard self-leveling telescopic legs and crank-down landing gear can accommodate any type of terrain and allows 180 degree arrangement to the screen.
The G Series also includes Gencor’s proven and highly portable silo that erects in minutes and provides an easy hot mix surge alternative without sacrificing storage capacity.
SUSTAINABILITY WITH ASPHALT
Gencor’s green products lead the industry in warm mix asphalt production and asphalt plant fuel savings. The Gencor Ultrafoam GX2™ warm mix system has a simple, robust and reliable method of injecting steam into the foaming process to produce warm mix asphalt. The Vector™ burner control is a fully automatic digital control system that minimizes fuel usage and gas emissions while maximizing production capacity. Gencor’s Ultraplant™ has taken top honors year after year for being the only hot mix plant with a positive volatile capture and recovery system that totally eliminates blue smoke and asphalt odors from the process and feeds them to the combustion process as fuel.
MIXING IN A WINNING BID
Gencor Ultradrum plants make HMA in a continuous operation and can store the asphalt in heated storage silos. Gencor’s Ultraplant™ concept is the most fuel efficient, environmentally clean and lowest maintenance design available to the hot mix industry. A totally integrated drum concept that allows high production continuous mix with high-volume, high moisture recycle and the optional flexibility of feeding a batch tower, all in a unitized drum design.
Gencor’s Ultraplant™ has taken top honors year after year for being the only hot mix plant with a positive volatile capture and recovery system that totally eliminates blue smoke and asphalt odors from the process and feeds them to the combustion process as fuel.
As a result, Gencor plants have been accepted in the most stringent and environmentally sensitive areas of the country, producing high quality polymer and Superpave mixes.
The Gencor Ultraplant™ combines simple design with the most advanced control technology and massive heavy construction unmatched in the industry.
Gencor Ultraplant™ helps contractors every year earn the most prestigious industry awards.
gencor.com (407) 290-6000
Founded: 1986 Our Mission: We also own Hamilton Tanks LLC, Inferno-therm (burners and tanks), and Construction Parts (wear parts). Our mission is to design, manufacture, and support the best asphalt equipment to the market. We continually aim to exceed our customers’ expectations in all we do. We desire a safe working environment to our employees and a profitable business to our shareholders.
INDUSTRY-CHANGING INNOVATION
Our company can be best described as the “home remodeler” for your asphalt plant. We help asphalt plant customers to improve efficiency through fuel saving, cost cutting, better methods or longer life products. Many times, we will provide turn-key solutions as more asphalt plants have minimized in-house talent to mechanically install or wire new equipment.
We have recently introduced a single clamshell 36" door opening on our hot mix storage silos. This is truly mass flow through the silo gates as more asphalt material is discharged through the gate without the “spraying” effect of smaller gate openings.
We are known for quality asphalt tanks and very fuel-efficient hot oil heaters. We manufacture asphalt tanks with cone bottoms to empty all the asphalt from the tanks. This is a relatively new design and is proving positive results with polymer modified asphalts and other blended liquid AC products. On our flat-bottomed tanks, we insulate the bottom of the tank, whereas most others have none leaving a space for heat to dissipate.
We have a patented RAP drying process that allows customers to increase their RAP to mixes. This coupled with our rejuvenator pump skids allow plants to increase RAP in mixes and to maintain quality products.

SAFETY IN THE INDUSTRY
Years ago, Meeker introduced the first asphalt tank valve control and tank monitoring system to the industry. We call it Liquid Vision. It is the original product designed to control all the asphalt valves on a plant tank farm and to monitor liquid levels in the tanks.
The valve control allows plant operators to stay away from the hot pipes and valves that go with a tank farm by having the valves automated. By having the valves controlled logically, this greatly minimizes the chance of using the wrong liquid in a mix or cross contaminating tanks with two different grades of liquid.
The tank monitoring allows operators and truck drivers to easily see levels in the tanks. This makes for more efficient ordering of liquid AC from the terminal and allows the person unloading the AC to make sure the correct liquid goes in the proper tank and allows the person to know how much space is left in the tank.
All of these tools in the Liquid Vision allow for a safer workplace for employees, customers, and visitors.
MIXING IN A WINNING BID
We strive to listen carefully to our customers. Each plant and each customer has its own unique set of circumstances. When one product works for one plant, it doesn’t necessarily work for another plant down the street. It’s up to us to learn what they are and help the customer implement products and/or methods to improve profitability.
Many plants have external pressures from neighbors and government agencies to help with quality-of-life issues. We understand these external pressures and work with customers to help asphalt plants with vapor recovery systems, tank venting systems, quiet burners with our Infern-o-therm line of products, and RAP systems to help profitability and environmental stewardship. reducing downtime will have a positive impact on the bottom line.
meekerequipment.com 717-667-6000 x 120
Founded: 2002 Our Mission: Reliable Asphalt Products Inc. was founded by Charles Grote III and Mike Mauzy in February of 2002. As the co-founders of a customer driven business, Charles and Mike developed the motto that “Every Company’s Greatest Asset is its Customers, Because Without Customers There is No Company.”
INDUSTRY-CHANGING INNOVATION
Even though Reliable Asphalt Products prides itself on supplying everything for an asphalt plant, MINDS asphalt plant automation and Vulcan burners have risen to the surface as highly sought-after plant upgrades. Reliable is the authorized dealer for these industry changing products. While providing front line support and the manual clean out panels for MINDS in the eastern half of the U.S., Reliable has supplied and installed over 100 systems in the past few years. Reliable has also coordinated and hosted annual MINDS user training schools that have been attended by 25-30 producer companies annually for the past 4 years. Vulcan burners have been a more recent addition to the Reliable product line. Originally invented and introduced to the hotmix plant market in England, the inventors of Vulcan burner decided to expand to the U.S. market. In 2019, Vulcan partnered with Reliable to install the first U.S. Vulcan burner at Sunbelt Paving in Auburn Georgia. Immediately, the burner exceeded expectations regarding fuel consumption and emissions. Since that initial installation, Reliable has sold and installed nearly a dozen more, and all are exceeding expectations. Meanwhile, Reliable has reached an agreement with Vulcan to be the sole distributor, manufacturer, and parts and maintenance supplier in the U.S. Much like with MINDS automation, the demand for the Vulcan burner indicates that this innovative product will soon be an industry standard.

SUSTAINABILITY WITH ASPHALT
Over the years, the asphalt industry has become increasingly more environmentally conscience, and Reliable Asphalt Products has developed many products to meet these eco-friendly improvements. Reliable is an industry leader in supplying and repurposing used and reconditioned asphalt plant equipment. Obviously, this reduces the need for new manufactured equipment. Asphalt is the world’s most recycled product, and Reliable offers a full line of equipment and innovations to increase usage of reclaimed asphalt into the final mix. As already mentioned, both MINDS plant automation and Vulcan burners improve production and efficiency of existing plants. Due to the precise calibrations of MINDS plant automation, waste in the process is minimized. The patented Vulcan burner is already an industry leader as a low NOx burner. The Vulcan burner typically requires less horsepower than the competition and is designed to efficiently burn multiple fuels. In addition to these environmentally friendly products, Reliable is in the late stages of research and development of a patented reclaimed asphalt dryer known as RAP Saver. Over the past 15 years, Reliable has been steadily working with the industry in developing an environmentally friendly system for extracting moisture from reclaimed asphalt. Reclaimed asphalt moisture causes severe production issues for an asphalt plant. As usage of reclaimed asphalt increases, fuel efficiency and production decrease in a conventional asphalt plant arrangement. Reliable’s efforts have focused on removing a portion of that moisture prior to injecting the reclaimed asphalt into the plant, thereby increasing plant production while decreasing fuel usage. Although Reliable has not brought this product to market yet, it is in the late stages of development and is currently operating on an existing high production asphalt plant. Reliable Asphalt plans to make this product another industry standard in the near future.
MIXING IN A WINNING BID
Asphalt plant downtime is one of the biggest concerns of the asphalt production industry. Reliable knows full well that a down plant with trucks waiting is an emergency that needs immediate attention. Reliable offers a full inventory of parts for immediate shipment with the focus on items that historically cause plant shutdowns. Reliable regularly ships parts overnight for next day installation and operation. MINDS automation is also a key combatant of plant down time. Remote plant diagnostics allows for immediate plant operation access regardless of the location of the Reliable service technician. Plant downtime is primarily due to a plant mechanical issue. MINDS automation taps into several monitoring devices on the plant to immediately diagnose the problematic mechanical issue. Minds offers an emergency kit with key replacement hardware parts for the system as well. The Vulcan burner also minimizes downtime due to the design simplicity. Reliable stocks all Vulcan burner replacement parts available for immediate shipment and encourages Vulcan burner owners to stock replacement parts as well. Reliable recently developed a PLC driven touch screen hot oil heater control panel that diagnoses the entire liquid AC and heating system. This panel is retrofittable to any manufactured hot oil heater and alerts the plant personnel in the event of any heating, tank level or flow issues that often cause plant downtime. Although this product was developed less than 2 years ago, Reliable has already installed over 40 panels and the demand is growing. Reliable offers 24-hour telephone access for all requests, including MINDS automation and plant diagnostics. All these measures are in place because Reliable realizes the importance of immediate customer service for minimizing down time.
reliableasphalt.com 866-647-1782
Founded: 2020 Our Mission: Sapphire's mission is to ensure natural gas delivery when pipeline infrastructure is constrained or unavailable. With over 60 years of experience in natural gas service and transportation, our management team provides turnkey CNG, LNG, and RNG solutions that promote safe, reliable, clean energy for our customers and communities.
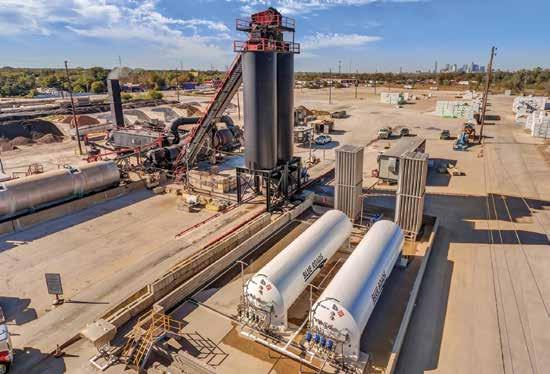
ANTICIPATING OUR CUSTOMERS' NEEDS
Sapphire's most important service is a complete turnkey solution for our asphalt customers with facilities or locations removed from pipeline infrastructure. Sapphire excels at creating and implementing CNG, LNG, or CNG/ LNG combination as a fuel source for power generation, heaters, burners, fleet vehicles, and heavy machinery fueling for customers with one or multiple locations.
SUSTAINABILITY WITH ASPHALT
Sapphire provides a complete solution to move our customers to clean-burning compressed or liquified natural gas. By replacing refined fuel oil (RFO) or waste oil with natural gas, cleaner fuel is burned, reducing carbon emissions, and increasing sustainability of plant operations.
MIXING IN A WINNING BID
The dense energy content of LNG or CNG allows large quantities of energy to be transported and stored on location, so it is ready to be used the instant tonnage is needed. Sapphire's modular equipment allows for flexible and transportable storage based on our customers' changing needs and demands.
sapphiregassolutions.com 214-433-1332
Founded: 1938 Our company motto is: “We make your plants run better.”
ANTICIPATING OUR CUSTOMERS’ NEEDS
Over the last 40+ years, Stansteel has innovated very advanced electronic control systems for hot mix asphalt plants. These products are a wide range and can be everything as comprehensive as the patented Accu-TrackTM Advantage control system down to an individual electronic device to help the plant either remotely monitor its operation or alert the plant operators even when they’re not present at the facility.
The Accu-Track Advantage is like an autopilot for the plant. Since the plant operator has scores of duties in keeping the operation and communications with the various customers and paving crews, this total-plant control system allows tracking of up to hundreds of points on the asphalt plant and relieves the operator from mundane duties. It can also track and alert for liquid asphalt deviation, material feed deviation and, due to the accumulated knowledge and experience of controlling plants, helps minimize waste on the part of the plant operation. With the Accu-Track Advantage, gone are the days when 10, 20 or 40 tons of mix must be wasted until it “gets right.” Another industry leading Stansteel product was specifically designed to help protect an asphalt plant’s most precious asset: the people who work there. Our Safe-T Station/AC Verification Station is a safe collection method for obtaining hot liquid AC samples from a pressurized line. Operators and QC/lab staff can easily and safely collect samples for testing. Once installed, the Safe-T Station immediately starts preventing burn injuries by enclosing the sample collection container before discharging the hot liquid AC. Large enough to enclose a one-gallon sample, the operator can view the fill level of the collection container through the sample station’s viewing glass door. The Stansteel Safe-T Station takes safety one step further by not allowing operation of the plug valve handle unless the enclosure door is securely shut tight in the closed position.
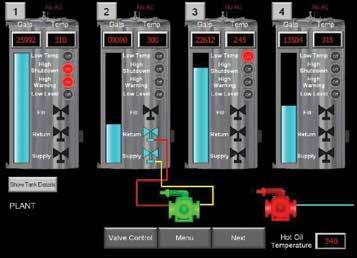
SUSTAINABILITY WITH ASPHALT
Since the hot mix asphalt industry is known for being the largest recycler of materials in North America, Stansteel helps bring that improved RAP utilization to the individual plant. Many important details need to be addressed for the integration of recycle, particularly to existing plants. For instance, there are different options on drum plants or batch plants to transform them from being able to run a minimal 10% or 15% RAP up to 50% or more. This can be done even on asphalt plants that are 50 years old.
By safely and sustainably upgrading these existing plants, the customer can often keep all their environmental permits in place and not further disrupt environmental concerns by modification, changing and removal and disposal of an older model plant just to buy new equipment. Stansteel has, over the last 20 years, introduced the Stansteel Green Line to the industry, which enables a series of products to help upgrade virtually any type of asphalt plant.
MIXING IN A WINNING BID
Integration and upgrading of customers’ existing plants is one of the specialties of Stansteel. By integration, we mean improving plant performance without expenditure of millions of dollars. Often, OEMs encourage hot mix producers to scrap everything you have and replace it with a new hot mix asphalt plant.
As plant equipment ages, it can put the company at a competitive disadvantage; for example, by not being able to run recycle, not being able to run high production rates, lack tons of storage of either hot mix asphalt or liquid asphalt or just suffer from the wear and inefficiency of old equipment such as dryers or slat conveyors.
By applying our extensive engineering experience and hundreds of years of accumulated knowledge and experience of plants, Stansteel assists contractors everywhere to upgrade their plants with custom new, used or reconditioned components and yield an extremely high return on investment through plant renovation, strategic upgrades and innovation.
stansteel.foleon.com/accu-track/brochure/home/ 502-245-1977
Founded: 1987 Our Mission: To design and manufacture operator friendly industrial controls and process automation that reliably addresses the needs of the asphalt industry and to provide lifetime service and “no excuses” support for those products.
ANTICIPATING OUR CUSTOMERS’ NEEDS
SYSTEMS’ ADP-100 has stood the test of time and is often called “Bomb Proof.” When you choose the ADP-100 you can do it with confidence knowing that it will outlast many products at the plant and that support will be available for years to come. As plants age and get replaced we have seen our controls get transferred and updated to the new plant continuing to make mix for many seasons. With continued development on an already “bomb-proof” platform the ADP-100 has become and will remain a leader in the asphalt industry.
Customer support starts with the design, and our products show that. We try to retain a backwards compatibility so that upgrades can be done without obsoleting the entire system. SYSTEMS offers support factory direct, through select OEMs and through service-based dealers. The people at SYSTEMS who develop and build our products are the ones you get to talk to for support. Their knowledge of our products is second to none. Along with SYSTEMS’ employees, our network of people have years of experience with total plant knowledge. We communicate with our OEMs and dealers to pool that knowledge and experience, striving to provide the best outcome for the customer. SYSTEMS offers “Real People with Real Solutions.”
Core Values: SYSTEMS’ Products Work. No Excuses • Make Promises Keep Promises • Relate to the Customer • Good Enough, Isn’t

SAFETY IN THE INDUSTRY
Knowing that equipment can fail, we believe in keeping the operator hands/eyes on and involved.
Errors and potential problems can be displayed on screens along with audible alarms for things like high silo and tank level alarms, no flow situations, motor amperages, equipment safety switches and nearly anything else that can provide us a signal.
We also offer products to keep plant personnel and truck drivers safe. With the use of stop and go lights, drivers know what scale to enter and when it is safe to do so. Audible horns for when the load is completed along with lights can give multiple indicators to when it is safe to move the truck. Our cameras can not only be used for truck identification but help to verify the truck position and making sure the scale is clear of hazards. Remote ticket printers and signature pads can keep drivers in their vehicles, thus reducing foot traffic in and around the plant. Our Remotely Operated Test weights keep plant personnel off of ladders and man-lifts eliminating the need to haul heavy weights onto scales for calibration checks. Easily programmed interlocks in our TSC Motors or Silo control prevents motors from being started or shutting down in the wrong sequence.
We strive to go above and beyond standards set by the NEC and UL. With everything from multiple ways of egress from structures to torqueing procedures for electrical connections we keep the customers safety in mind. Roomy well laid out control centers with large windows for operator visibility and high output LED scene/area lights, are the details that will keep the plant a safer environment for those on site. By offering a custom approach to control centers, owners/operators can help design and specify what fits their needs and concerns.
MIXING IN A WINNING BID
SYSTEMS can reduce down time with reliability, ease of troubleshooting and by stocking a large inventory of replacement parts for direct, fast shipping when needed.
While many problems “show up” on the screen it is not always SYSTEMS’ product that is faulty. Our people and our service-based dealers have total plant knowledge and the ability to find the problem that is causing errors and to help correct those problems, so that through preventative maintenance, the likelihood of them returning is reduced. User friendly easily learned controls give the plant owner the opportunity to cross-train employees so that backup is readily available if the primary operator is unavailable.
systemsequipment.com 563-568-6387
Our Mission: The WIRTGEN GROUP stands for more than 550 years of experience. We owe our success to the world leading brands, Wirtgen, Vögele, Hamm and Kleemann, as well as our amazing customers whose collaboration drives our desire to provide world class innovation. With a dealer network that covers North America coast to coast, we are “CLOSE TO OUR CUSTOMERS.”
ANTICIPATING OUR CUSTOMERS’ NEEDS
Ask any contractor what is at the top of their decision-making criteria and you will hear service and support. As the world market leader in road construction, WIRTGEN GROUP provides the best application support, technical training and parts support network in the world. Wirtgen America’s Center for Training and Technology (CTT) was built to support our customers, dealers, employees and the road construction industry. This 38,000-square-foot state-of-the-art facility located near Nashville, Tennessee, consists of 11 classrooms, 5 technology rooms, a 4-bay shop dedicated to training, and a 5-acre proving ground used exclusively for equipment operation training and demonstrations. At the CTT, we provide comprehensive road construction technical training. From guardrail to guardrail and 20 inches down, courses cover everything from aggregate production, to paving, compaction, and recycling of road materials. We offer unparalleled opportunities for high-quality training from industry experts, using a constantly evolving curriculum that keeps attendees in step with cutting-edge technology. CTT-educated technicians are trained to navigate job site challenges, maximizing machine efficiency and minimizing downtime. Our instructors put technical training in context, so service personnel understand not only how the machines work, but also how they work in different environments. This is the advantage our dealers and employees provide our customers every day. As Jim McEvoy, President of Wirtgen America said, “We call this a training center, but to me, this is a learning environment.”
Wirtgen America’s support network consisting of over 30 independent dealers, with 250 + locations across the US and Canada, covering our customers coast to coast. And because road construction takes place all hours of the day and night, they are available 24/7, 365 to provide parts and service. This is vital to the success of our customers and builds the trust necessary in any successful partnership. We commit to being “Close To Our Customers” with parts, service and application expertise.

SUSTAINABILITY WITH ASPHALT
To us, sustainability isn’t simply a trend, it’s an integral part of our corporate principles. The WIRTGEN GROUP incorporates sustainability into all of our business processes. Environmental considerations are a top priority from the development and design phase of our products and a central element in all stages of the production chain—right through to the use of the machines in projects around the world. We know that the future belongs to climate-friendly products, which we’re already manufacturing today.
WIRTGEN GROUP machines feature intelligent control systems and clever automatic functions to achieve maximum productivity with low fuel consumption and minimal emissions. Innovative technologies and machines proactively protect the environment—and our customers’ budgets.
Our high-quality products and technologies support environmentally friendly processes as well, like cold milling, asphalt recycling and surface mining. They’re not only green but create efficiencies for our customers through reduced trucking, recycling of existing materials and cut, crush and load operations, all reducing CO2 emissions and expenses.
WIRTGEN GROUP’s commitment to a better environment also extends to our production facilities. HAMM AG uses near-surface geothermal energy to heat and cool its office building. For this purpose, the company installed 48 geothermal probes under the employee parking lot that together generate a total of 600,000 kWh of heating energy—equivalent to around 15,850 gallons of oil—from renewable sources. And on hot summer days, the heat pump turns into a cooling unit that extracts heat from the building and “pumps” it back into the ground. This allows the company to “generate” another 200,000 kWh of additional cooling energy every year. Compared to conventional compression chillers, this reduces CO₂ emissions by up to 70%.
wirtgen-group.com
Founded: 1976 Our Mission: Our mantra is Together We Build Amazing. Command Alkon delivers a comprehensive portfolio of solutions and collaborative supply chain experience that ensures our customers’ success in the procurement, production and delivery of asphalt and execution of asphalt paving projects and operations around the globe.
INDUSTRY-CHANGING INNOVATION
Command Alkon addresses challenges for just-in-time scheduling of orders, automated reconciliation of material and haul tickets to invoices, and real-time job costing controls for trucking and material deliveries. With our cloud-based technology platform, CONNEX, our latest technologies can extract data from asphalt delivery tickets and invoices and instantly match those tickets with invoices to automate office and field processes. By fully connecting the materials supply chain with CONNEX-enabled solutions, we can digitize 100% of the paper tickets and invoices and eliminate the time-consuming work of keying in data into spreadsheets and disparate systems. With all of the data (from jobsite equipment, trucks, and plants) captured in real time, we can deliver CONNEX-powered operational and cost insights that empower smarter decisions to optimize the delivery of materials; when materials can be delivered cheaper by decreasing idle time and waste, everybody wins – asphalt suppliers, haulers, and contractors can improve their margins.
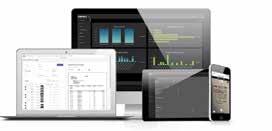
MIXING IN A WINNING BID
Command Alkon’s comprehensive suite of integrated solutions for the asphalt industry include Libra continuous drum mix automation, batch plant controls, silo loadout systems, and truck scale ticketing applications. Simple site automation technologies tie directly into these systems to keep operations flowing smoothly and put trucks on the road quickly. Enterprise service software enables central management of multiple facilities.
Dispatch and truck tracking software is available that is uniquely designed for asphalt producers, helping them to forecast, organize and manage job/truck scheduling to make the most efficient use of resources and thereby improve the bottom line. The dispatch software is integrated with the plant controls and self-service kiosks, so operators benefit by knowing the plant production requirements for the day, scheduled jobs, and when each truck will arrive, enabling them to boost efficiencies and get more loads out the door.
commandalkon.com 205-879-3282 ex. 3969
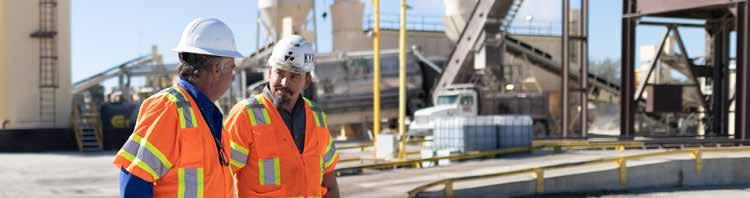
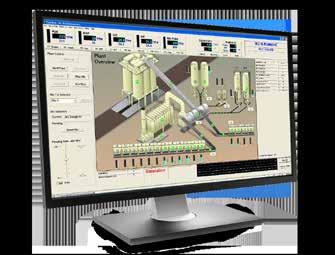

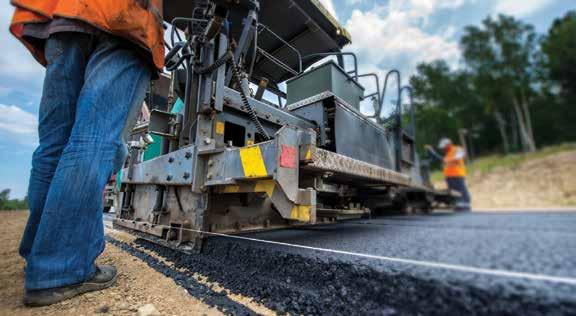
Founded: 2015 Our Mission: HaulHub is on a mission to accelerate the digital transformation of the construction industry by listening to, and engaging with, industry stakeholders to rapidly build and deploy digital tools that enhance the productivity, coordination and transparency of the industry.
iNDUSTRY-CHANGING INNOVATION
As the industry prepares to rebuild our nation’s aging infrastructure, HaulHub is proud to partner with contractors, materials producers, and Departments of Transportation across the country. The industry’s push towards digital project delivery lays the foundation to connect industry stakeholders in real-time to help all parties make better decisions and boost efficiency. With most state DOT’s looking to deploy digital construction methods like e-Ticketing and Digital As-Builts, driven in large part by Federal Highway’s Every Day Counts initiative, HaulHub serves as the premier industry partner to make this shift a reality. As the digital future unfolds, HaulHub is on the front lines listening to the needs of the industry and building the next generation of digital tools.
MIXING IN A WINNING BID
HaulHub’s suite of apps provides insights into every aspect of the construction materials supply chain. Our transportation management system provides analytics that enables a real-time assessment of bid vs. actual trucking costs. The easy-to-use tools provide field crews and management teams with actionable intel to improve operations immediately. HaulHub’s e-Ticketing solutions are revolutionizing the way materials producers, contractors, and project owners communicate. Unlocking the data associated with construction materials provides new ways of looking at customer behavior and trends and allows sales teams to operate more effectively in the marketplace. With the coming wave of infrastructure projects, the ability for management and crews to monitor and control the flow of materials onto the construction site in real-time will be a crucial differentiator for those who embrace the latest e-Construction tools.
haulhub.com 1.833.HAULHUB
Our Mission: Kenco Engineering specializes in solving wear problems that cause unnecessary equipment downtime. Our parts are engineered to save money by eliminating future replacement cycles of new parts, and to reduce labor costs.
INDUSTRY-CHANGING INNOVATION
Kenco Engineering has introduced a new line of Tungsten Carbide Impregnated (TCI), extra heavy-duty augers for the asphalt industry. Whether used as dust fines reject augers or asphalt transfer augers, Kenco’s use of our unique Tungsten Carbide Impregnation process will ensure your auger achieves the greatest possible wear life by maintaining the auger’s overall diameter for a much longer period than previously possible. Kenco’s TCI system will drastically reduce “diameter shrinkage” on the auger, thus enhancing efficiency along with wear life. Call us today for a quote!
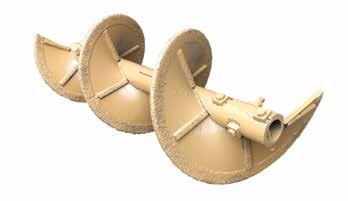
MIXING IN A WINNING BID
Asphalt producers make money by sending asphalt through the front gate. Kenco’s products, by reducing the amount of maintenance required and extending wear part life cycles, allow more “up time” for the plant and equipment. More “up time” means more days to produce or lay asphalt and more money straight to the bottom line.
kencoengineering.com 800-363-9859
Make It Last.
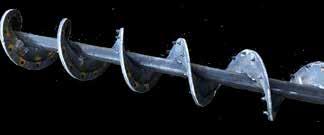
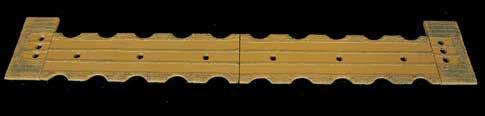
Protect your investment with Kenco wear parts.
Proudly manufactured in the USA since 1957, Kenco offers innovative products for the aggregate, asphalt and road building industries. Our products are designed to increase wearlife and reduce downtime on your plants and equipment.
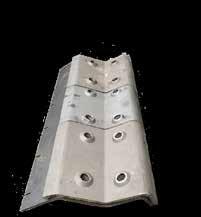
Kenco Engineering, Inc
www.kencoengineering.com 800-363-9859
Founded: 1947 Our Mission: Process Heating Company’s (PHCO’s) Lo-Density® Unitized Storage Tank Heaters, FuelOil Preheaters, Hot-Oil Heaters, and Distributor Truck Heaters provide unique electric heat benefits for asphalt plants, including lower operating costs, improved product quality, reduced maintenance, significantly longer heater life and enhanced sustainability.
ANTICIPATING OUR CUSTOMERS’ NEEDS
Lo-Density® drywell-style electric heaters offer 100% energy efficiency throughout the lifetime of the heater. This is because all energy is used to heat, compared to the inefficient burning of fossil fuels, which operate at only 85% efficiency when new — and that efficiency quickly drops to 50% to 65%. Our electric heaters typically last for more than 30 years, providing 100% efficient heat over their entire lifetime without incurring the cost of replacing fossil-fuel-fired heaters every 8 to 10 years.
Additionally, because these unique drywell-style heaters dissipate controlled heat as low as three watts per square inch on the heater’s sheath, they prevent coking or damaging of temperature-sensitive materials — eliminating the need to drain and clean tanks. Because the drywell elements are accessible from outside of the tank, they may be serviced without draining the tank. And since electric heat requires little maintenance, these heaters can reduce downtime even further.
SUSTAINABILITY WITH ASPHALT
Lo-Density® heaters provide unique environmental benefits that can help asphalt producers achieve sustainability goals. Electric heat is safe, consistent, and friendly to the environment because it heats without combustion or emissions, and it eliminates a source of fuel and material spills. Electric heat offers 100% energy efficiency because all of the energy is used to heat, when compared to the inefficient burning of fossil fuels. In addition, the efficiency will always be 100%, even after many years of operation, without costly maintenance. Electric heat also eliminates stacks that must be monitored for emissions, along with eliminating expensive air quality and boiler permits that must be pursued and maintained. Unitized Heaters can be interfaced and coordinated with other plant electrical equipment so that the load of the heaters can be reduced to base rates, thus preventing increased demand charges or peak-use rates and lowering consumption cost.
processheating.com 206-682-3414
TURN ON THE HEAT: REALIZE THE REWARDS
Lower Your Operating Costs Improve Your Product Quality Reduce Your Maintenance Needs Enjoy Decades of Trouble-Free Efficiency Improve Your Sustainability
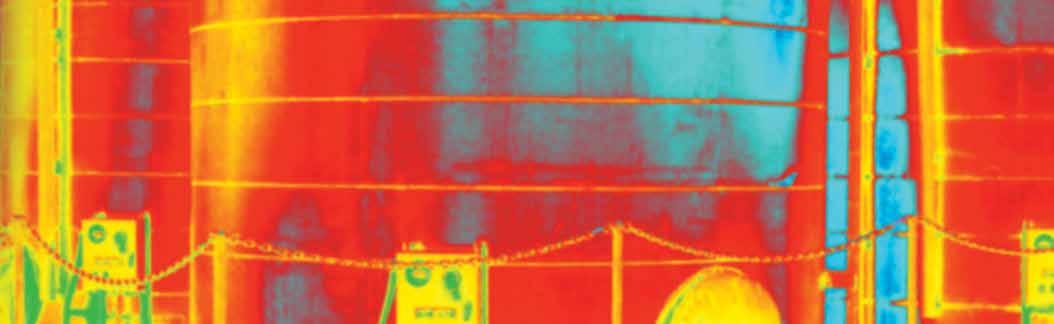
Lo-Density® Is Better!

Our 100%-efficient Lo-Density® drywell-style electric heaters provide safe, clean, reliable, and cost-effective heat — making them the best choice for heating your asphalt tanks, hot oil circulating systems, fuel oil preheaters, distributor trucks, and more.
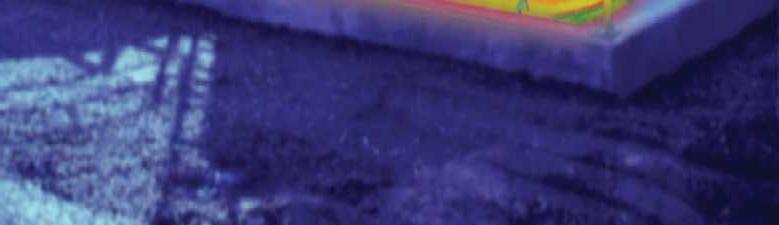
866-682-1582 info@processheating.com
PROCESS HEATING COMPANY www.processheating.com
Founded: 2006 Our Mission: Sripath Technologies® develops, manufactures, and markets innovative asphalt additives world-wide such as, rejuvenators, grade modifiers, oils, polymers, and anti-strips to enhance the performance of asphalt in paving and roofing applications. Our team of industry veterans have a track record for cutting edge innovation creating an excellent suite of sustainable solutions.
INDUSTRY-CHANGING INNOVATION
Sripath thrives on the challenge of confronting long-standing issues facing the asphalt industry by providing innovative, simple, and easy to use additive solutions.
Maximizing the RAP/RAS content in the asphalt mix has been one of the challenges Sripath has successfully addressed. Our veteran team of technologists developed the ReLIXER™ Asphalt Rejuvenator between 2011-2013, with early roadway trials in 2014, and initial sales in 2015. Now, with a 6-year track record of clearly showing the superior economic and performance results of paving with high RAP/RAS mixes containing ReLIXER, world-wide sales continue to increase dramatically. With ReLIXER, RAP use levels of 25-40% are common and 100% RAP use is viable, significantly reducing mix costs while meeting all specifications.
PGXpand® is another transformative polymer product that substantially boosts high temperature grade and improves rutting resistance without changing the low temperature performance. Unlike traditional polymers, it is easy-to-use, requiring only low shear mixing.
Sustainability with Asphalt
NuMIXER™ and ReLIXER™ are two environmentally friendly, bio-oil based blends providing sustainable solutions that reduce the carbon footprint thru longer lasting, higher performing asphalts and the increased use of RAP and RAS.
NuMIXER improves the low temperature grade of the asphalt, improves workability, and polymer compatibility.
ReLIXER is used for the rejuvenation of high RAP/RAS mixes, keeping reclaimed materials out of landfills. It rapidly penetrates and rejuvenates the old, aged asphalt, creating a reusable mix that can be easily applied. ReLIXER supports higher amounts of RAP/RAS in mixes, while maintaining key properties to meet specifications. It also contains no Volatile Organic Compounds (VOC) and is effective at low dosage levels. By reducing dependency on virgin asphalt and aggregate, ReLIXER makes Reducing, Reusing and Recycling RAP/RAS a cost-saving and easy process. With ReLIXER, the existing network of roadways becomes the next generation of mines and refineries.
sripath.com/profile 800-562-6276 (US/Canada) 201-721-7562 (Worldwide)
Make your RAP piles pay for themselves.
Use ReLIXER™ to maximize RAP content while meeting project specifications.
Engineered, high-performance rejuvenator for High RAP & RAS mixes
Rapidly penetrates and rejuvenates. Reduces the virgin asphalt requirements in the mix. Allows increased RAP & RAS content while aiding compaction Improves low temperature performance, fracture toughness, aging & fatigue 100% RAP mixes with no virgin AC added are viable with outstanding performance
ReLIXER™ • NuMIXER™ • ReNUBIT™ • PGXtend® • PGXpand® • SriCote™
1-800-562-6276 1-201-721-7562
Learn More At Sripath.com/piles
Make Asphalt Better

Founded: 2000 Our Mission: Tarmac International Inc.’s mission is to provide safe and complete hot mix asphalt plant systems at the highest quality and competitive prices with installation and maintenance service.
iNDUSTRY-CHANGING INNOVATION
Innovations to our hot mix asphalt systems include:
Improved maintenance features on dryers, baghouses, and drag slats.
PLC controls have been improved to allow for plant operational statistics to be available to the customer via our “Dashboard” screen. This feature is offered online giving real time data for a plant running and historical data including totals on each material run and fuel usage.
SUSTAINABILITY WITH ASPHALT
Tarmac rotary dryer systems are designed for lower fuel usage. Several details stand out: 1. Slower gas velocity within the dryer increases heat transfer to virgin aggregate and RAP. It additionally reduces fines discharge to air pollution control equipment. 2. Our shell insulation greatly reduces exterior shell heat loss thus lower burner fuel use. 3. Updated burners and burner controls reduce CO and NOX gases leaving the dryer. 4. Dryer flight design allows the burner flames to develop without material veiling into the flame. Tarmac flights allow for easy adjustments assuring proper and efficient veiling for both wet and dry aggregate. 5. Improved bag design and bag materials reduce particulate discharge from the baghouse.
Tarmac customers improve their bottom line and produce more tons by bringing new systems online in less time from date of order to final plant commissioning.
tarmacinc.com 816-220-0700
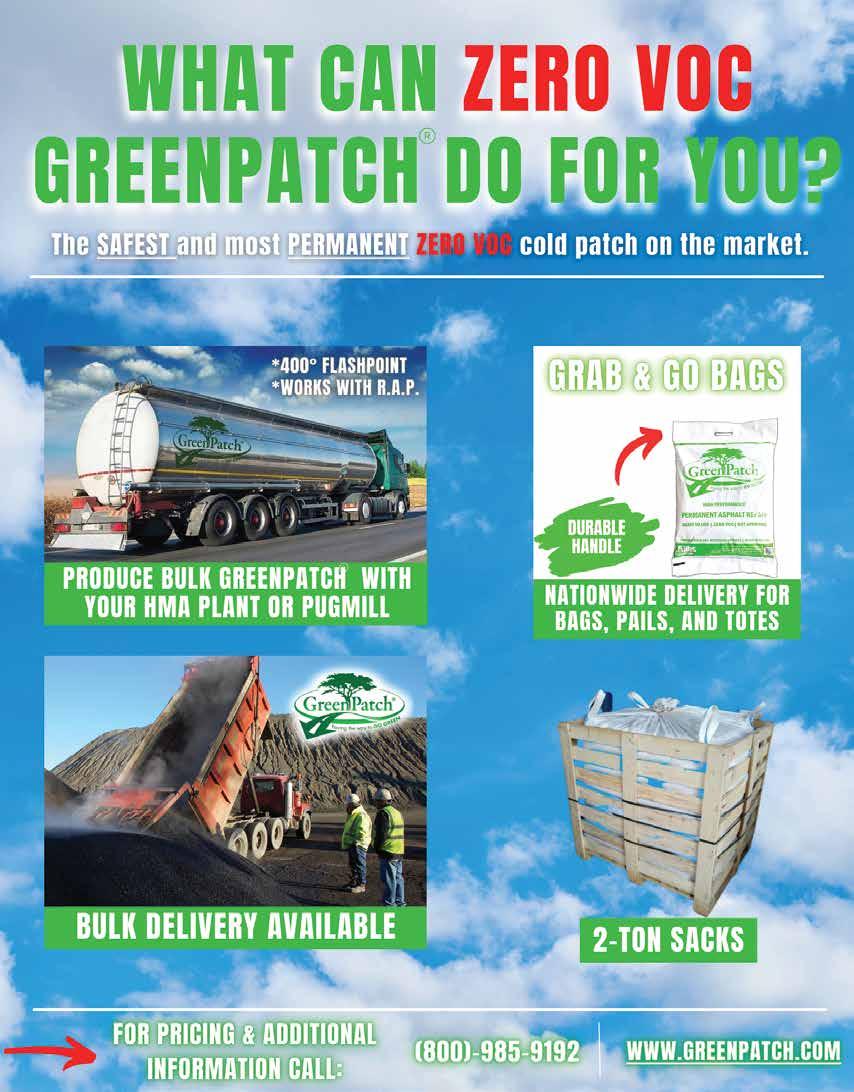