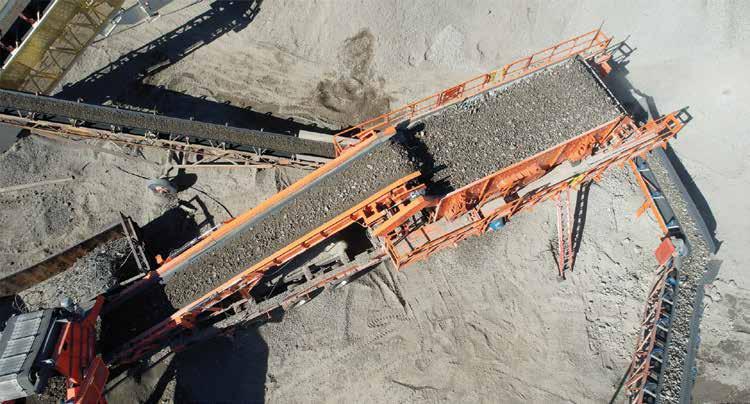
5 minute read
How to Make Your Plant More Efficient Right Now
Tips from conversations at recent meetings and shows
BY SANDY LENDER
Few hot-mix asphalt (HMA) producers in North America would’ve missed the call to further reduce greenhouse gas emissions (GHGs) at their facilities. While the asphalt industry has all the stats and facts to show how much it has lowered GHGs and particulate matter (PM) emissions over the years, our collective efforts must now focus on quantifying the proof of our environmental sustainability. This will be aided by environmental product declarations (EPDs) developed at multiple plants in every region of our nation; it will also be aided by good record-keeping and compliance with local regulations.
When a nearby “group” requests a Freedom of Information Act (FOIA) disclosure regarding your stack emissions test results, you want those numbers to be the best indication of your actual operation. You want the spring startup to go smoothly, cleanly and quietly for best air quality compliance, best neighbor relations and best environmental health.
At the recent National Asphalt Pavement Association (NAPA) annual meeting in Miami and CONEXPO-CON/AGG 2023 tradeshow and conference in Las Vegas, experts from industry shared thoughts for shoring up the asphalt plant and implementing some best practices to ensure all of the above. While a few of the ideas and products in the next few pages might be familiar to some readers, others may be new. They all combine to form a quick guidance for spring startup and summer production at your most environmentally sound production level.
Let’s start with the elephant in the room: lead times. If a plant owner needs to lower emissions right now to hit a neighbor-appeasing target number, he may not have the luxury of receiving new equipment for another three (or more) months. Trevor Wagoner, Astec product manager for sustainability, sat down with me at the company’s booth during CONEXPO-CON/AGG to share thoughts about environmental stewardship and strategies. He said there are operational improvements the savvy producer can introduce today while waiting for componentry to arrive tomorrow.
Wagoner shared that reducing emissions involves a combination of new equipment and operational efficiencies. For example, there’s a difference between using the Astec Generation 3 warm mix system to create a full-temperature mix that is easier for crews in the field to compact and using it to create a lower-temperature mix that reduces fuel consumption and potential for visible smoke emissions. The latter will assist in immediate environmental gains at the plant.
There are other examples of operational improvements. T.J. Young of T2ASCO LLC, shared with the NAPA audience that the three largest areas of energy consumption when operating the asphalt plant are drying and heating, storing liquid asphalt cement (AC) at target temperatures, and electrical energy use. If the savvy plant manager can operate more efficiently in these areas, he can reduce his carbon footprint.
When it comes to drying and heating, we naturally turn to stockpile management. Young shared, if you can reduce your aggregate moisture content by 1%, you can reduce your fuel consumption required for drying by 10%. Imagine the impact that has over a season of production.
While visiting with Wagoner, I asked him to elaborate on his views beyond stockpile management. After all, the “plant” section in Astec’s booth in the central hall highlighted 12 different features around the HMA plant where a producer can reduce emissions and/or increase efficiencies, such as the warm mix system, blue smoke controls and an alternate fuels burner display. Wagoner shared, while stockpile management is the first area a producer turns to realize emissions reductions, switching from waste oil or diesel to natural gas is the second easiest area to address. He stated that making the switch could realize a reduction of up to 27% in the plant’s carbon footprint.
Young shared reasoning behind the burner fuel discussion, as well. “Make sure your burner is efficient, but check your fuel,” he told the audience. “Alternate fuels save money and could burn more cleanly.”
Additional means of enhancing your production follow on the next few pages with equipment, software and services launched during—or near—CONEXPO-CON/AGG. While the guidance above and on the pages to follow isn’t exhaustive, it offers ideas to intrigue you and your plant managers. There’s more to come in the June “Lab & Binder” edition of AsphaltPro , where we’ll dive further into production tips.
Almix
ALmix , Ft. Wayne, Indiana, included a display of its new Insignia Control Suite during CONEXPO-CON/AGG. The entire suite of ALmix Insignia Control Suite (ICS) can be connected to the new Insignia Cloud, which is designed to give plant owners in-depth insight into plant operation.
ICS is a total plant control system for drum mix asphalt plants, offering command of the blending process and individual motor controls while allowing the operator to monitor, operate and report all plant functions. The system is designed with modern tailored graphics; a comprehensive primary operating display; built-in burner controls; clearly identified switches, meters and warnings; a series of operator-focused detail screens; detailed diagnostics; remote support; a point-andclick operating interface for timely loadout; and more.
For more information, visit www.almix.com/automation
Ammann
Ammann America Inc., Davie, Florida, included a model and video of its newest continuous plant offering during CONEXPO-CON/ AGG. The team shared that the counterflow, single-drum plant will see operating capacities ranging 200-600 TPH and recycled asphalt pavement (RAP) capabilities of 50-100%. They explained that they’re re-imagining the asphalt plant to fit in the paving process for the North American market with the North American contractor in mind. And now, it’s designed and built in America with Ammann’s new engineering and technical center in Orlando.
For more information, visit www.ammann.com.
Eagle Crusher
Eagle Crusher Company, Galion, Ohio, displayed two new plants at CONEXPO-CON/AGG 2023. The new UltraMax® 1600X-OC portable impactor plant is designed for larger-size aggregate operations and quarries and features the UltraMax 69X impactor with a 69inch x 51-inch feed opening to allow larger material into the impactor to increase throughput, up to 1,000 TPH.
The new 8x20 screen plant with integrated feed conveyor and blending gates offers multi-product screening. It is designed to produce up to four products simultaneously, three with absolute sizing, or return the oversized product for further reduction. The integrated 60-inch feed conveyor remains on for transport and eliminates the need for a separate conveyor, while each screen deck features four blending gates to allow for a wide range of custom product mixes to meet specific product needs.
Here are some specs for the 8x20 screen plant:
• 8X20, three-deck, triple-shaft screen
• Includes all-electric motors and electrical cords
• Hydraulic lift and leveling system
• 70-foot, 3-inch operating length
• 16-foot, 5-inch operating width
• 17-foot, 7-inch operating height
• 87,000-pound gross weight
• 36 inches, bottom screen deck cross conveyor width
• 36 inches, middle screen deck cross conveyor width
• 60 inches, under screen conveyor width
• 42 inches, retractable fines cross conveyor width
• 60 inches, plant feed conveyor width
For more information, visit www.eaglecrusher.com.
Gencor
The fully insulated Hy-Way Calibration Tank from Gencor, Orlando, offers a new feature to augment safety and efficiency for the asphalt producer. On display at the company’s booth during CONEXPO-CON/AGG, the Gencor team highlighted the new digital readout included on the calibration tank to give plant managers and truck drivers immediate information regarding tank levels. The large digital display is located at the top of the vertical, 1,000-gallon tank for easy visibility.
Calibration tanks also feature:
• 3-point loadcells
• Digital temperature readout
• Safety suction system
• 4-inch insulation
• Test weight platform
• 18-inch manway
• Access ladder
For more information, visit www.gencor.com.